热处理炉测试方案
热处理炉有效加热区测定方法

热处理炉有效加热区测定方法热处理炉有效加热区测定方法导言:热处理炉是一种被广泛应用于金属材料处理的设备,其主要功能是通过加热和冷却控制,对金属材料进行结构调整和物理性能改善。
在进行热处理过程中,确保炉内加热区能够达到有效加热是非常关键的。
本文将探讨热处理炉有效加热区的测定方法,以帮助读者更好地理解和掌握该技术。
一、有效加热区的定义在热处理炉中,有效加热区是指能够达到所需温度范围并实现均匀加热的区域。
一般来说,如果炉内的温度分布能够在一定的误差范围内保持均匀,那么该区域就可以被认定为有效加热区。
在实际应用中,有效加热区的确定对于炉内金属材料的均匀加热非常重要,它直接影响到处理效果的质量。
二、传统方法1. 温度测量法传统的热处理炉有效加热区测定方法之一是通过在炉内不同位置布置温度传感器,测量这些位置处的温度值。
根据温度分布图来确定加热区的范围。
这种方法简单直接,可以提供炉内温度的整体情况。
然而,由于传感器的布置可能存在问题,比如不均匀或数量不足,因此可能会导致测量结果的不准确。
2. 金属试块法另一种常用的方法是使用金属试块来评估有效加热区的范围。
在炉内放置一系列具有相同材料和尺寸的金属试块,然后根据试块的质量变化来判断加热区的位置。
这种方法相对简单,但仍然存在一些局限性,比如试块的分布和数量问题,以及在实际加热过程中试块与工件之间的传热差异等。
三、改进方法为了克服传统方法存在的问题,近年来,一些新的测定方法被提出并得到了广泛应用。
下面介绍几种改进的方法:1. 热像仪法热像仪是一种能够显示物体表面温度分布的设备,通过红外线探测技术来测量物体的辐射能量并将其转化为图像。
热像仪可以将炉内的温度分布直观地展示出来,并能够在实时监测中提供精确的温度数据。
通过分析热图,可以快速确定有效加热区的位置和范围。
这种方法不仅操作简便,而且具有较高的测量精度,因此在炉内温度分布调整和优化过程中得到了广泛的应用。
2. 数值模拟法数值模拟方法是一种通过计算机仿真来预测热处理过程中加热区温度分布的技术。
热处理炉炉温均匀性检测方法

热处理炉炉温均匀性检测方法炉温均匀性测量:在热稳定前和热稳定后,用校准过的现场测试仪表对炉子的有效工作区进行炉温均匀性测量以确定工艺设备内的温度分布状况的一种测试方法。
常见炉温均匀性检测依据的标准:GB/T 9452-2012《热处理炉有效加热区测定方法》、GB/T30824-2014《燃气热处理炉温度均匀性测试方法》、GB/T 30825-2014《热处理温度测量》、API Spec 6A《井口装置和采油设备规范》、AMS 2750G《高温测量》、AIAG CQI-9 《热处理系统评审》、ASTM A991/A991M- 17《钢制品热处理炉温度均匀性测量标准试验方法》、GJB 904A-1999《锻造工艺质量控制要求》、GJB 509B-2008 《热处理工艺质量控制》、BAC 5621《波音工艺规范-材料处理温度控制》、HB 5354-1994《热处理工艺质量控制》、HB 5425-2012 《航空制件热处理炉有效加热区测定方法》。
炉温均匀性检测需要依据热处理炉的有效加热区尺寸、精度等级、炉型确定需要多少个测温点:热处理炉精度等级划分和TUS测试周期:炉温均匀性检测权威机构:江苏东方航天校准检测有限公司(简称OACT)位于江苏省苏州工业园区,是一家集校准、检测、培训及技术服务为一体的综合性第三方服务机构。
OACT成立于2010年3月,是航天科技集团公司下属空间技术研究院(航天五院)下属北京东方计量测试研究所投资设立。
2011年4月获得CNA检测和校准实验室能力认可,认可编号CNAS L5056。
目前通过CNAS认可的检测和校准项目涉及电磁、无线电、时间频率、几何量、热工、力学、化学等七个计量专业领域。
OACT秉承严谨、专业、精确、先进的计量理念,信守“质量为本、客户至上、科学公正、止于至善”的质量承诺,利用先进的仪器设备和精湛的测试技术,竭诚为每一位客户提供高水平的校准检测服务和整体解决方案。
热处理炉测试方案
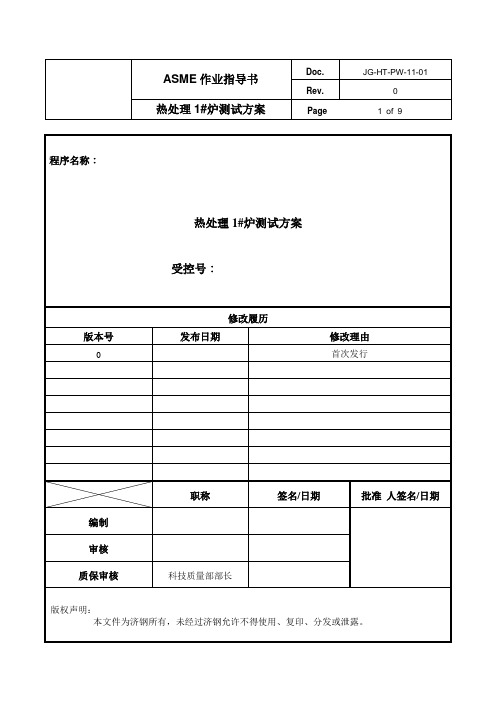
6.9热处理炉各区温度稳定后开始进行测试,开启送料按钮,将钢板送入热处理炉内,热处理炉二级系统自动计算钢板再炉内的运行速度,并记录钢板再炉内各个区域的气氛温度。在钢板出炉后并冷却到适宜温度,将自动温度记录仪取出、关闭。此时记录仪记录了从开启到关闭阶段的温度、时间。并将外接热电偶从钢管中抽出,整理测试设备。
注:热处理炉示意图见附录A
8.2各测试点通过各区时同截面最大偏差以及测试最终标准
Zone
Preheating Zone(T01~T08)
Heating Zone(T T09~T16)
温区
预热区(T01~T08)
加热区(T09~T16)
range
偏差
148.5℃
69℃
Zone
温区
Soaking Zone(T17~T20)
2.2 GB/T 9452-2003热处理炉有效加热区测定方法
3.定义和缩写
3.1 T1为内置热电偶。固定在炉内,该热电偶只为监测钢板出炉温度,不做温度控制。编号为:T1
3.2 T01~T20为内置热电偶。固定在炉内,用于监测和控制热处理炉内各区气氛的温度。编号为:T01~T20
3.3 T21~T26为外接热电偶,用于测量作业过程中,钢板的实际温度。编号为:T21~T26
程序名称:
热处理1#炉测试方案
受控号:
修改履历
版本号
发布日期
修改理由
0
首次发行
职称
签名/日期
批准人签名/日期
编制
审核
质保审核
科技质量部部长
版权声明:
本文件为济钢所有,未经过济钢允许不得使用、复印、分发或泄露。
热处理炉有效加热区测定方法
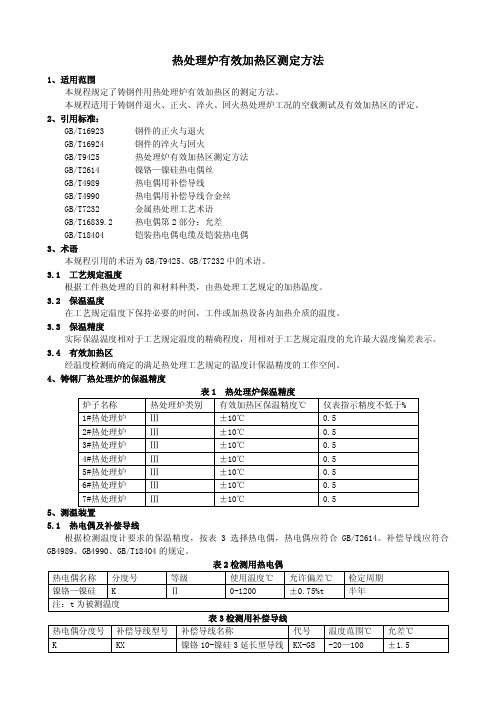
热处理炉有效加热区测定方法1、适用范围本规程规定了铸钢件用热处理炉有效加热区的测定方法。
本规程适用于铸钢件退火、正火、淬火、回火热处理炉工况的空载测试及有效加热区的评定。
2、引用标准:GB/T16923 钢件的正火与退火GB/T16924 钢件的淬火与回火GB/T9425 热处理炉有效加热区测定方法GB/T2614 镍铬—镍硅热电偶丝GB/T4989 热电偶用补偿导线GB/T4990 热电偶用补偿导线合金丝GB/T7232 金属热处理工艺术语GB/T16839.2 热电偶第2部分:允差GB/T18404 铠装热电偶电缆及铠装热电偶3、术语本规程引用的术语为GB/T9425、GB/T7232中的术语。
3.1 工艺规定温度根据工件热处理的目的和材料种类,由热处理工艺规定的加热温度。
3.2 保温温度在工艺规定温度下保持必要的时间,工件或加热设备内加热介质的温度。
3.3 保温精度实际保温温度相对于工艺规定温度的精确程度,用相对于工艺规定温度的允许最大温度偏差表示。
3.4 有效加热区经温度检测而确定的满足热处理工艺规定的温度计保温精度的工作空间。
4、铸钢厂热处理炉的保温精度表1 热处理炉保温精度炉子名称 热处理炉类别 有效加热区保温精度℃ 仪表指示精度不低于%1#热处理炉 Ⅲ ±10℃ 0.52#热处理炉 Ⅲ ±10℃ 0.53#热处理炉 Ⅲ ±10℃ 0.54#热处理炉 Ⅲ ±10℃ 0.55#热处理炉 Ⅲ ±10℃ 0.56#热处理炉 Ⅲ ±10℃ 0.57#热处理炉 Ⅲ ±10℃ 0.55、测温装置5.1 热电偶及补偿导线根据检测温度计要求的保温精度,按表3选择热电偶,热电偶应符合GB/T2614。
补偿导线应符合GB4989、GB4990、GB/T18404的规定。
表2检测用热电偶热电偶名称 分度号 等级 使用温度℃ 允许偏差℃ 检定周期镍铬—镍硅 K Ⅱ 0-1200 ±0.75%t 半年注:t为被测温度表3检测用补偿导线热电偶分度号 补偿导线型号 补偿导线名称 代号 温度范围℃ 允差℃K KX 镍铬10-镍硅3延长型导线 KX-GS -20—100 ±1.55.2 检测仪器检测仪器用精度不低于0.5级,使用有纸记录仪—富士PHA88004-EA0YV 记录仪。
热处理炉炉温均匀性检测操作规程

7.相关记录
炉温均匀性检测计划表 《RCLL-001》
炉温均性检测记录表 《RCLL-002》
编制
日期
审核
日期
批准
日期
标记
处数
更改文件号
签字
日期
炉温均匀性测量记录表
炉子名称
设备 编号 设备 型号
车间
检测日期
假定有效加热区尺寸 /mm
装载量及气氛
设定温度/℃
测量结果
时间
温度传感器真实温度/℃ 1# 2# 3# 4# 5# 6# 7# 8# 9# 10#
实施条件
最大值 最小值 最大偏差 结论 检测者 备注
审核者
批准者
6.3.5 准备 TUS 炉温均匀性检测表按照热电偶排布进行排列记录,进行准备。
编ቤተ መጻሕፍቲ ባይዱ 审核 批准
日期 日期 日期
标记 处数
更改文件号
签字
日期
热处理炉温均匀性测试作业规程
共2页
第2页
6.3.6 准备工作就绪,依据产品的热处理工艺设置仪表的工作参数,热处理炉开始工作,当控温仪仪表或 TUS 热电偶中任意一个测量 点温度达到测试温度公差下限前,数字记录仪开始记录数据,每 5 分钟记录一 次,所有热电偶测量的数据(测量间隔最大不超过 5 分钟),应至少连续记录 6 组数据。数字记录仪的数据记 录格式如附件炉温均匀性检测记录表。
实施条件
编号:
最大值
最小值
最大偏差
结论
合格
检测者
备注
标准(偏差): ±10℃
审核者
批准者
炉温均匀性测量记录表
编号:
炉子名称
炉子 编号 设备 型号
车间
炉温均匀性测试作业指导书
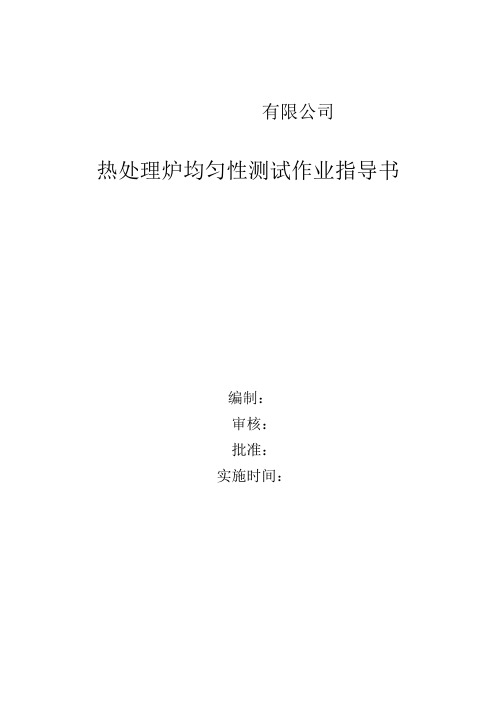
有限公司热处理炉均匀性测试作业指导书编制:审核:批准:实施时间:1、目的:生产中使用的热处理炉TUS(温度均匀性)和使用仪表及热电偶满足公司生产需要以及符合客户需求特制定本作业指导书。
2、范围:本作业指导书适用于公司热处理炉产品所使用的热处理炉温度均匀性测试。
3、职责4.1 公司热处理工程师根据客户要求负责热处理工艺编制和最终确认。
4.2 技术部与生产部门按照产品热处理工艺选择需要的热处理设备,设备的仪表类型也必须经过国家法定检定机构校检并符合客户要求。
4.3由公司热处理工程师主持相关技术人员对热处理炉进行TUS测试。
4、热处理温度均匀性热处理炉内工作区温度达到稳定化后相对于设定点温度的变化,工作区内任两点的温度偏差不应超过热处理工艺对温均匀性的要求(一般情况下用于正火的热处理炉温度均匀性:±14℃,回火热处理炉温度均匀性±8℃)。
热处理炉等级与温度均匀性范围要求:5、温度均匀性测试(TUS)进行TUS时,如果客户没有特别指出热处理炉的装载状态,一般情况下在满载情况下进行测试,装载的产品必须是依据公司工艺文件进行热处理的产品。
当下一次进行TUS时也必须是和前一次测试时的装载状态且产品与上一次相同。
5.2 温度均匀性测试(TUS)步骤5.2.1通常情况下,在进行TUS时热处理炉必须是室温状态下;如果热处理炉刚进行过生产有一定温度(例如:此时炉内温度是500℃),则下一次进行TUS测试也必须和此次情况相同(500℃)。
5.2.2 热电偶(传感器)的处理。
TUS测试进行之前,热电偶测量端必须用直径不超过13mm(0.5英寸)并且不超过待热处理产品的最薄处、与产品材料一致的长60mm,内部加工出与热电偶直径一样大小深40mm圆孔的圆棒,置于热电偶测量端进行保护。
5.2.3 测量点的选择与位置图5.2.3.1测量点及热电偶的选择本公司热处理炉温度均匀性测试,采用10点进行测量,9 TUS+1控温热电偶。
热处理炉炉温均匀性检测操作规程

实施条件
最大值 最小值 最大偏差 结论 检测者 备注
审核者
批准者
公司
热处理炉炉温均匀性测试作业规程
共2页
第1页
1. 目的: 为了确保使用的热处理炉 TUS(炉温均匀性测试)和使用仪表及热电偶满足公司生产需要,并保 证其稳定性,特制定此作业规程。
2. 编制依据 编制本工艺规程的依据为 GB/T9452-2012 热处理炉有效加热区测定方法。
3. 基本要求 3.1 热处理工必须经过技术培训,考核合格,持证上岗。 3.2 热处理设备状态良好。 3.3 热处理环境整洁,热处理炉温设定符合产品技术条件要求。 3.4 热处理现场须有放置检测热电偶支架。 4. 职责
1
多通道巡点记录仪
2
K 型铠装热电偶
3
炉温均匀性检测支架
6. 作业程序
6.1 TUS 炉温均匀性测试一般于每年的 12 月份之前制定下一年度测试计划。
6.2 用于 TUS 炉温均匀性测试所使用的设备及仪器,应每年定期对其精度进行校验,确保其符合要求。
6.3 温度均匀性测试( TUS )步骤
6.3.1 通常情况下, 在进行 TUS 时热处理炉必须是室温状态下,检测温度设定为工件热处理温度。
实施条件
编号:
最大值
最小值
最大偏差
结论
合格
检测者
备注
标准(偏差): ±10℃
审核者
批准者
炉温均匀性测量记录表
编号:
炉子名称
炉子 编号 设备 型号
车间
检测日期
冲压车间
假定有效加热区尺寸 /mm
装载量及气氛
空载
设定温度/℃
250
测量结果
时间
热处理炉有效加热区测定方法
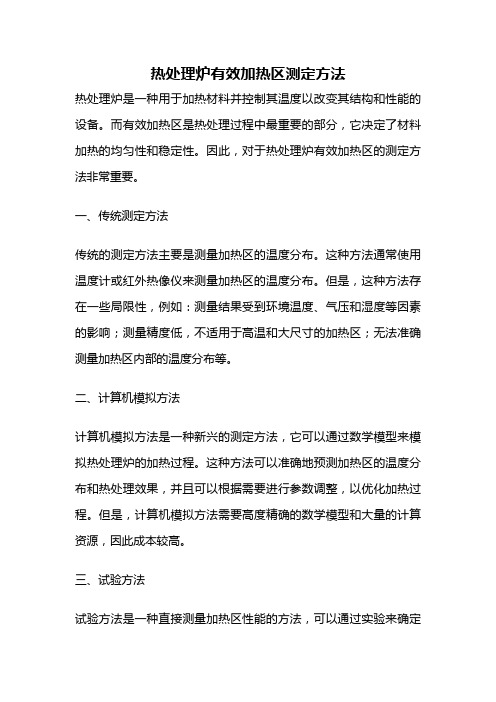
热处理炉有效加热区测定方法热处理炉是一种用于加热材料并控制其温度以改变其结构和性能的设备。
而有效加热区是热处理过程中最重要的部分,它决定了材料加热的均匀性和稳定性。
因此,对于热处理炉有效加热区的测定方法非常重要。
一、传统测定方法传统的测定方法主要是测量加热区的温度分布。
这种方法通常使用温度计或红外热像仪来测量加热区的温度分布。
但是,这种方法存在一些局限性,例如:测量结果受到环境温度、气压和湿度等因素的影响;测量精度低,不适用于高温和大尺寸的加热区;无法准确测量加热区内部的温度分布等。
二、计算机模拟方法计算机模拟方法是一种新兴的测定方法,它可以通过数学模型来模拟热处理炉的加热过程。
这种方法可以准确地预测加热区的温度分布和热处理效果,并且可以根据需要进行参数调整,以优化加热过程。
但是,计算机模拟方法需要高度精确的数学模型和大量的计算资源,因此成本较高。
三、试验方法试验方法是一种直接测量加热区性能的方法,可以通过实验来确定加热区的有效加热区域和温度分布。
这种方法可以准确地测量加热区的性能,但是需要大量的试验数据和实验设备,并且需要耗费大量的时间和金钱。
四、综合方法综合方法是一种将传统测定方法、计算机模拟方法和试验方法综合使用的方法。
通过综合使用这些方法,可以更准确地测量加热区的性能,并且可以根据需要进行参数调整,以优化加热过程。
综合方法可以克服传统方法和计算机模拟方法的局限性,同时也可以克服试验方法的成本和时间限制。
热处理炉有效加热区的测定方法是一个复杂的问题,需要综合考虑多种因素。
根据具体情况选择合适的测定方法,可以有效地提高热处理的效果和质量。
- 1、下载文档前请自行甄别文档内容的完整性,平台不提供额外的编辑、内容补充、找答案等附加服务。
- 2、"仅部分预览"的文档,不可在线预览部分如存在完整性等问题,可反馈申请退款(可完整预览的文档不适用该条件!)。
- 3、如文档侵犯您的权益,请联系客服反馈,我们会尽快为您处理(人工客服工作时间:9:00-18:30)。
目录
1. 目的和范围…….…………………………………….………………………3/9
2. 参考文件…….…………………………………………………….…………3/9
3. 定义和缩写…….…………………….………………………………………3/9
4. 职责和权限…….………………………………….…………………………3/9
5. 要求.…………………….…………………….…………………….………..3/9
6. 检验程序.…………………….…………………….…………….…………..3/9
7. 测试过程数据以及结论.………………….……………………..…………..5/9 8.附表…. ……………………………………………………………………...8/9
ASME作业指导书
Rev. 0
热处理1#炉测试方案Page 5 of 9
7. 测试过程数据以及结论
根据热处理炉的设计要求,钢板在加热温度900℃的情况,采用的加热系数为1.5并且保温10min,钢板在出料炉门处的温度均匀性在±10℃。
可以计算出钢板总共在炉时间为1.5*25+10=45min 通过自动温度纪录仪记录的温度曲线如图7.1所示。
7.1 钢板正过程的温度曲线
7.1 预热阶段:根据自动温度纪录仪开启11min48s时钢板开始如炉,根据钢板运行速度,可以计算出钢板进入加热阶段的时间是17min30s,也就是预热阶段在温度纪录仪中记录的时间为11min48s~29min18s。
根据自动温度纪录仪中记录的温度,可以发现预热阶段最大温度偏差为148.5℃。
ASME作业指导书
Rev. 0
热处理1#炉测试方案Page 6 of 9
7.2 加热阶段:根据钢板运行速度,可以计算出钢板在加热阶段的时间为29min18s~46min48s。
根据自动温度纪录仪中记录的温度,可以看出钢板在进入加热段时最大温度偏差为99℃。
在加热段结束时的钢板最大温度偏差为6℃。
自动温度纪录仪记录的数据如图7.2.1所示。
图7.2.1 加热段结束时钢板温度
ASME作业指导书
Rev. 0
热处理1#炉测试方案Page 7 of 9
7.3 保温阶段:根据钢板运行速度,可以计算出钢板在加热阶段的时间为46min48s~56min48s。
根据自动温度纪录仪中记录的温度,可以看出钢板在保温阶段的最大温差为8℃。
自动温度纪录仪记录的数据如图7.3.1所示。
图7.3.1 保温结束时钢板温度
7.4结论:根据热处理炉设计要求的加热系数以及保温时间下,钢板的出炉温度的最大偏差在±4℃,在设计的±10℃范围内。
Sample Form(样表)8-1。