激光加工陶瓷裂纹行为的理论分析及实验验证
陶瓷材料的微裂纹理论及其尺寸寸效应
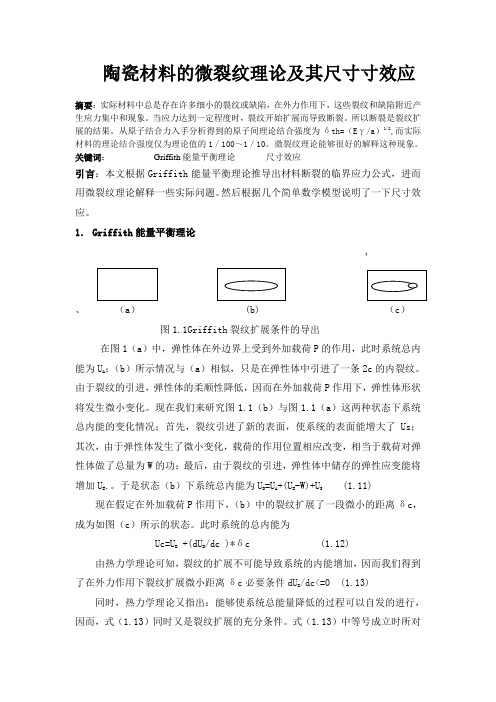
陶瓷材料的微裂纹理论及其尺寸寸效应摘要:实际材料中总是存在许多细小的裂纹或缺陷,在外力作用下,这些裂纹和缺陷附近产生应力集中和现象。
当应力达到一定程度时,裂纹开始扩展而导致断裂。
所以断裂是裂纹扩展的结果。
从原子结合力入手分析得到的原子间理论结合强度为δth=(Eγ/a)1/2,而实际材料的理论结合强度仅为理论值的1/100~1/10。
微裂纹理论能够很好的解释这种现象。
关键词:Griffith能量平衡理论尺寸效应引言:本文根据Griffith能量平衡理论推导出材料断裂的临界应力公式,进而用微裂纹理论解释一些实际问题。
然后根据几个简单数学模型说明了一下尺寸效应。
1.Griffith能量平衡理论,、(a) (b) (c)图1.1Griffith裂纹扩展条件的导出在图1(a)中,弹性体在外边界上受到外加载荷P的作用,此时系统总内能为UA;(b)所示情况与(a)相似,只是在弹性体中引进了一条2c的内裂纹。
由于裂纹的引进,弹性体的柔顺性降低,因而在外加载荷P作用下,弹性体形状将发生微小变化。
现在我们来研究图1.1(b)与图1.1(a)这两种状态下系统总内能的变化情况;首先,裂纹引进了新的表面,使系统的表面能增大了Us;其次,由于弹性体发生了微小变化,载荷的作用位置相应改变,相当于载荷对弹性体做了总量为W的功;最后,由于裂纹的引进,弹性体中储存的弹性应变能将增加UE .。
于是状态(b)下系统总内能为UB=UA+(UE-W)+US(1.11)现在假定在外加载荷P作用下,(b)中的裂纹扩展了一段微小的距离δc,成为如图(c)所示的状态。
此时系统的总内能为Uc=UB +(dUB/dc )*δc (1.12)由热力学理论可知,裂纹的扩展不可能导致系统的内能增加,因而我们得到了在外力作用下裂纹扩展微小距离δc必要条件dUB/dc<=0 (1.13) 同时,热力学理论又指出:能够使系统总能量降低的过程可以自发的进行,因而,式(1.13)同时又是裂纹扩展的充分条件。
激光打孔陶瓷微裂纹现象理论研究

参考文献
! &’()’ % *+,- &’(.’/ 0,1 2(3-(4 56 74(-83/ 9, 0 *0::.3, % 93(.,:.1 ;81.4 <83 =,:3)>(8, 5.:.?:(8,/ =@@@ A30,>0?:(8,> 8, B,8C4.1-. 0,1 50:0 @,-(,..3 (,-/ 2846 D/ E86 $/ F)4+ % G)-)>:/ !DDH6 " B6 =4-),/ *6 G6 *8330>/ 0,1 I6 G6 B.JJ.3.3/ &:0:. A30,>0?:(8, G,04+>(>K G I)4. % L0>.1 =,:3)>(8, 5.:.?:(8, GMM380?’/ =@@@ A30,>6 &8<:C03. @,-6/ 2846 "!/ ,86 N/ MM6 !OO % !DD/ ;036/ !DDP6 N6 &6 *6 &’(.’/ 0,1 2(3-(4 56 74(-83/ 0 *0::.3, % 93(.,:.1 =,:3)>(8, 5.:.?:(8, &+>:.J 0,1 =: Q > GMM4(?0:(8, *38?/ =@@@ &+JM6 I.>.03?’ (, &.?)3(:+ 0,1 *3(R0?+/ 90S40,1/ T04(<6/ MM6 N"H % N$"6 ;03 !DD!6 $ 张振国 6 一种基于规则的网络入侵检测系统 U F V 6 计算机科学/ "WW$6 D6
第"期 "WWY 年 " 月
陶瓷激光加工技术
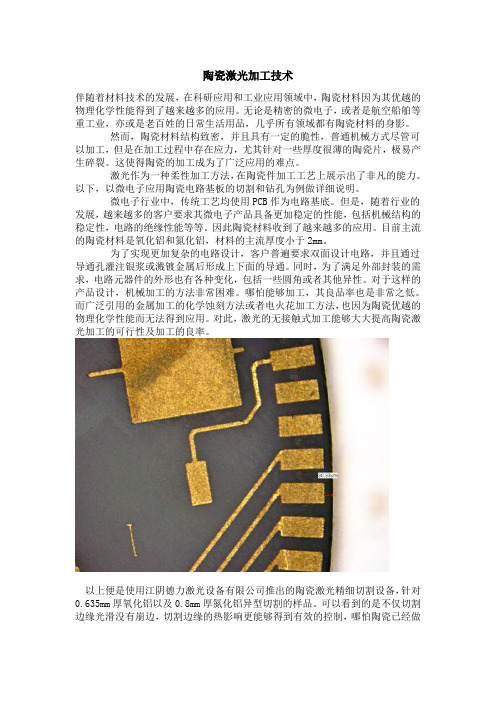
陶瓷激光加工技术伴随着材料技术的发展,在科研应用和工业应用领域中,陶瓷材料因为其优越的物理化学性能得到了越来越多的应用。
无论是精密的微电子,或者是航空船舶等重工业,亦或是老百姓的日常生活用品,几乎所有领域都有陶瓷材料的身影。
然而,陶瓷材料结构致密,并且具有一定的脆性,普通机械方式尽管可以加工,但是在加工过程中存在应力,尤其针对一些厚度很薄的陶瓷片,极易产生碎裂。
这使得陶瓷的加工成为了广泛应用的难点。
激光作为一种柔性加工方法,在陶瓷件加工工艺上展示出了非凡的能力。
以下,以微电子应用陶瓷电路基板的切割和钻孔为例做详细说明。
微电子行业中,传统工艺均使用PCB作为电路基底。
但是,随着行业的发展,越来越多的客户要求其微电子产品具备更加稳定的性能,包括机械结构的稳定性,电路的绝缘性能等等。
因此陶瓷材料收到了越来越多的应用。
目前主流的陶瓷材料是氧化铝和氮化铝,材料的主流厚度小于2mm。
为了实现更加复杂的电路设计,客户普遍要求双面设计电路,并且通过导通孔灌注银浆或溅镀金属后形成上下面的导通。
同时,为了满足外部封装的需求,电路元器件的外形也有各种变化,包括一些圆角或者其他异性。
对于这样的产品设计,机械加工的方法非常困难。
哪怕能够加工,其良品率也是非常之低。
而广泛引用的金属加工的化学蚀刻方法或者电火花加工方法,也因为陶瓷优越的物理化学性能而无法得到应用。
对此,激光的无接触式加工能够大大提高陶瓷激光加工的可行性及加工的良率。
以上便是使用江阴德力激光设备有限公司推出的陶瓷激光精细切割设备,针对0.635mm厚氧化铝以及0.8mm厚氮化铝异型切割的样品。
可以看到的是不仅切割边缘光滑没有崩边,切割边缘的热影响更能够得到有效的控制,哪怕陶瓷已经做好金属化,仍然能做到精准的切割而不伤到金属化部分。
当然,上世界七十年代,在美国已经出现陶瓷的激光直线划片加工。
但是可以看到的是,当今的陶瓷基板切割技术,已经得到了深远的发展。
传统的CO2高功率激光是目前在陶瓷直线切割应用中的传统工艺。
陶瓷材料的断裂行为与韧性评估研究
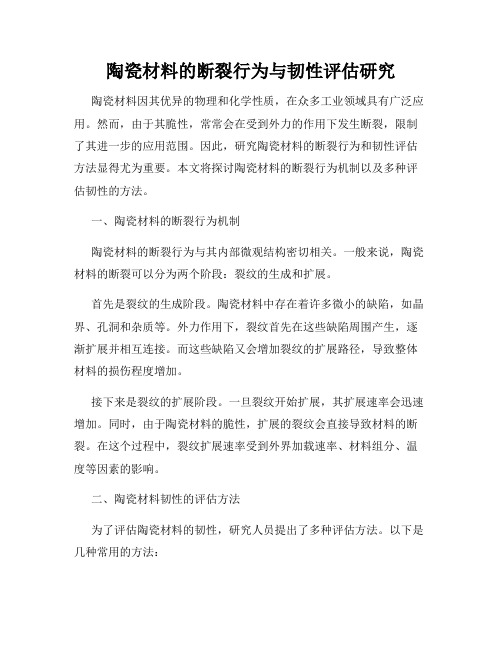
陶瓷材料的断裂行为与韧性评估研究陶瓷材料因其优异的物理和化学性质,在众多工业领域具有广泛应用。
然而,由于其脆性,常常会在受到外力的作用下发生断裂,限制了其进一步的应用范围。
因此,研究陶瓷材料的断裂行为和韧性评估方法显得尤为重要。
本文将探讨陶瓷材料的断裂行为机制以及多种评估韧性的方法。
一、陶瓷材料的断裂行为机制陶瓷材料的断裂行为与其内部微观结构密切相关。
一般来说,陶瓷材料的断裂可以分为两个阶段:裂纹的生成和扩展。
首先是裂纹的生成阶段。
陶瓷材料中存在着许多微小的缺陷,如晶界、孔洞和杂质等。
外力作用下,裂纹首先在这些缺陷周围产生,逐渐扩展并相互连接。
而这些缺陷又会增加裂纹的扩展路径,导致整体材料的损伤程度增加。
接下来是裂纹的扩展阶段。
一旦裂纹开始扩展,其扩展速率会迅速增加。
同时,由于陶瓷材料的脆性,扩展的裂纹会直接导致材料的断裂。
在这个过程中,裂纹扩展速率受到外界加载速率、材料组分、温度等因素的影响。
二、陶瓷材料韧性的评估方法为了评估陶瓷材料的韧性,研究人员提出了多种评估方法。
以下是几种常用的方法:1. 缺口尖头法(Notch-tip method):该方法通过在陶瓷试样上刻制一定尺寸的缺口,通过测量试样在外力作用下断裂前的弹性变形程度来评估其韧性。
缺口尖头法适用于评估较均匀结构的陶瓷材料。
2. 断裂韧度法(Fracture toughness method):该方法通过施加弯曲或拉伸等载荷,在断口上测量裂纹长度,并结合裂纹扩展力学理论计算出材料的断裂韧度。
断裂韧度法适用于评估较复杂结构的陶瓷材料。
3. 动态韧性评估方法:该方法基于陶瓷材料的断裂动力学过程,通过高速摄像技术等手段观察裂纹扩展的速率和路径,确定材料的韧性性能。
动态韧性评估方法对于评估陶瓷材料在高速冲击等极端环境下的性能十分重要。
三、陶瓷材料断裂行为与韧性评估的应用陶瓷材料的断裂行为和韧性评估不仅对于加工和制备工艺的优化具有重要意义,还对于实际应用中陶瓷材料的可靠性和安全性进行评估。
.激光加工陶瓷材料的研究

.激光加工陶瓷材料的研究激光是一种通过入射光子的激发使处于亚稳态的较高能级的原子、离子或分子跃迁到低能级时完成受激辐射所发出的光,它与引起这种受激辐射的入射光在相位、波长、频率和传播方向等几方面完全一致,因此激光除具有一般光源的共性之外,还具有亮度高、方向性好、单色性好和相干性好四大特性。
由于激光的单色性好和具有很小的发散角,因此在理论上可聚焦到尺寸与光波波长相近的小斑点上,温度可高至上万摄氏度,它是一种理想的切割热源,能使任何坚硬的材料如硬质合金、陶瓷、金刚石等,都将在瞬时 (<10-3s)被局部熔化和蒸发,并通过所产生的强烈冲击波被喷发出去。
因此,我们可以利用激光对各种材料进行切割等加工。
烧蚀或达到燃点,同时借与光束同轴的高速气流(即具有一定压力的辅助气体,常用气体有 N2、 O2、空气等,其主要作用是:在熔化切割时,依靠喷吹气体的压力把液态金属吹走形成切口;在氧气切割中,气体与切割金属反应放热,提供部分切割能量,同时又靠气体吹除反应物),吹除熔融物质,从而实现工件割开的一种热切割方法。
激光切割的原理激光切割系利用经聚焦的高功率密度激光束照射工件,使被照射处的材料迅即熔化、汽化、被割材料切割面激光切割的类型根据工件热物理特性和辅助气体的特性,激光切割可分为汽化切割、熔化切割、反应熔化切割和控制断裂切割四类。
其中激光汽化切割指在极高的激光功率密度(108W/cm2)的光束照射下,工件表面材料在极短时间内被加热到汽化点,并以气体或为气体冲击以液态、固态微粒形态逸出,形成割缝从而实现切割。
陶瓷的切割可采用汽化切割。
激光切割的主要特点(1)切割质量好由于激光的光斑小、能量密度高,切割速度又快,故能获得良好的切割质量。
①切缝窄,激光切割的割缝一般在0.10~ 0.20mm,节省材料。
②割缝边缘垂直度好,切割面光滑无毛刺,表面粗糙度一般控制在 Ra:12.5 以上。
③热影响区小:激光加工的激光割缝细、速度快、能量集中,因此传到被切割材料上的热量小,引起材料的变形也非常小,在某些场合,其热影响区宽度在 0.05mm 以下。
激光熔覆裂纹形成机理综述

Laser cladding with HA and functionally graded TiO2-HA precursors on Ti–6Al–4V alloy for enhancing bioactivity and cyto-compatibility 由于CaeP基生物陶瓷和Ti合金之间的弹性模量,热膨胀系数和硬度的大的不匹配,在涂层和基材之间产生了尖锐的界面。
即涂层和基材之间的微观结构没有逐渐变化。
这导致粘合强度和裂缝形成的降低。
为了控制裂缝并提高粘接强度,许多研究人员将一定比例的纯Ti粉末与CaP 基生物陶瓷混合,因为Ti的热膨胀系数与基材的热膨胀系数相似。
此外,为了增强界面处的冶金结合和涂层表面的生物活性,设计并使用激光熔覆制造功能梯度涂层。
如果包层材料或其中一种成分与基底材料匹配,则通常会增强冶金结合由于激光熔覆是一种热处理,其中涂层以及基底材料的一小部分以非常高的冷却速率熔化和固化。
通常,由于陡峭的温度梯度,凝固收缩和涂层与基材之间的热膨胀系数(CTE)差异所产生的应力,凝固过程中会产生裂缝HA,TiO和Ti-6Al-4 V的CTE 分别为13.3×10 -6/ K,9.4×10 -26/ K和8.6×10 -6/ K,分别为。
如Rodriguez等人报道的,相对于底物计算涂层和底物之间CTE的百分比差异。
因此,在100%HA包层中,涂层(HA)和基板(Ti-6Al-4V)之间的CTE百分比差异为54.6%。
由于这种巨大的百分比差异,在快速凝固的表面即涂层材料中产生压缩应力。
这引起了Ti-6Al-4V中的拉应力,这主要是裂纹产生和传播的原因。
由于激光模式的原因, 光斑中各处的温度分布是不均匀的, 这种因为温度梯度的存在而产生的熔池中表面张力的不均匀性,导致了凝固表面波纹的出现。
另一方面, 由于陶瓷材料与基体金属在结构上差异较大, 两者的润湿性和匹配性不好, 使涂层和基体的结合强度较差, 那么当残余应力或外力的作用大于涂层与基体的结合强度后, 涂层就会从基体上剥落。
紫外激光加工陶瓷的原理

紫外激光加工陶瓷的原理
紫外激光加工陶瓷的原理是利用紫外激光的高能量和特定波长来进行材料加工。
具体原理如下:
1.雕刻过程:紫外激光通过光学系统被聚焦到陶瓷表面,形成一个极小的光斑。
随着激光的照射,陶瓷表面被加热并迅速蒸发,形成气体和离子。
离子与激光相互作用,发生冲击电离等过程,导致材料的蒸发速率加快。
2.去除材料:随着激光的照射,陶瓷表面的蒸发和物质变化导致材料被去除。
激光的高能量和特定波长使它能够瞬间加热材料,导致单元结构的沉积物破裂,从而使材料脱离。
3.精细控制:紫外激光的波长通常在200-400纳米之间,较短的波长使得激光的光斑更小,能够精细控制加工效果。
此外,紫外激光的能量密度也可以进行调节,以适应不同的加工需求。
总体而言,紫外激光加工陶瓷的原理是通过激光的高能量和特定波长使陶瓷表面蒸发和物质变化,从而实现材料的去除和加工。
中文文献-激光熔覆陶瓷

激光熔覆陶瓷摘要:本论文提出了一种制造陶瓷部件的新型层压方法,即激光陶瓷熔覆。
这种方法是用激光束将陶瓷粉末熔覆使其联结在一起。
该过程包括五个步骤:将无机粘合剂和溶剂与陶瓷粉末混合以获得料浆;将料将铺在未烧结的基体块上;烘干并加强料浆薄层;用激光扫描未烧结的陶瓷层;从已熔覆的陶瓷工件上移除未熔覆的部分。
电子隧道显微镜图片展示了相邻的两陶瓷层熔覆的联结部分。
通过三点弯曲强度测试表明了其弯曲强度在3~12Mpa之间。
与其他层压方法相比,该方法是用激光直接熔覆未烧结的陶瓷体并得到陶瓷层而不需要传统的柱烧过程。
这种方法在制造更精密陶瓷部件方面具有很大的潜力。
关键词:精密;陶瓷部件;激光陶瓷熔覆;料浆;陶瓷层;弯曲强度1介绍现已有许多层压制造方法来制造陶瓷部件,它们大多数都是用聚合物粘合剂来联结陶瓷粉末。
由于陶瓷部件的强度取决于聚合物的强度,所以通过这些方法所获得的陶瓷部件、未烧结体的强度通常不能满足工业用途的要求,而其未烧结体的耐热性也因聚合物的存在受到限制。
因此,未烧结体必须在炉子中经后续的烧结来获得所需的强度和耐热性。
在烧结过程中会发生收缩,尤其是在制造复杂部件过程中会不可避免地产生扭曲变形。
本论文提出了一种制造陶瓷部件的新型层压方法,即激光陶瓷熔覆(CLF)。
这种方法是通过激光处理使陶瓷粉末熔覆并结合在一起。
2 激光陶瓷熔覆的原理如果将激光光束沿一直线照射在疏松的陶瓷粉上,陶瓷粉末将熔化,但是将会形成许多小球而不是我们所期望的直线状,这种现象叫做球化。
根据实验,如果陶瓷粉末在与其化学成分相同的固体底板上熔化,熔化的液体将完全润湿底板。
前述的底板或未烧结体可以通过烘干料浆来获得,料浆是由陶瓷粉、无机粘合剂及溶剂组成。
当激光光束照射在未烧结体上时,未烧结体的表面将熔化并粘附在未烧结体下面的部分。
可以通过这种方法制造出三维工件的二维搭接部分。
根据上述的激光熔覆原理出现了一种陶瓷部件的制造方法(美国专利,专利号:6217816B1)图1展示了这个方法的五个步骤。
- 1、下载文档前请自行甄别文档内容的完整性,平台不提供额外的编辑、内容补充、找答案等附加服务。
- 2、"仅部分预览"的文档,不可在线预览部分如存在完整性等问题,可反馈申请退款(可完整预览的文档不适用该条件!)。
- 3、如文档侵犯您的权益,请联系客服反馈,我们会尽快为您处理(人工客服工作时间:9:00-18:30)。
万方数据 万方数据9期同胤洲等:激光加工陶瓷裂纹行为的理论分析及实验验证国=吉丽≤‰宇×厂(3d2—9b2),3+(7b2d一5d3),.2+(3b4+19b2d2—8b3d)r+3b4d一5b2d3—8b3d2],(6)对应的应力趋势图如图2所示(为了简化计算,设≠生一T。
=1,6=o.1mm,d=10mm来观察应力1一卢趋势)。
图2热应力分布图Fig.2Thermal—stressfieldplot分别讨论式(6)中与激光加工参数有关的三个系数,ilp孑L径边缘温度Tm。
,孔半径6和热影响区半径d。
Tm。
对热应力的影响,如图3所示(为了简化计F算,设等丁。
=1,b=o.1mm,d=10mm来观察1一卢应力趋势)。
随着孔径边缘温度的提高,切向和径向的拉应力都有显著提高,将增加裂纹产生的可能。
因此要尽量降低孔径边缘温度接近熔化温度以减少材料中的拉应力,抑制裂纹的产生。
孔径大小b和热影响区大小d对应力分布的影响如图4所示。
当热影响区的大小减少时,两个方向的应力都有变小的趋势(如图4(a),(b),(c)所示);从图4(d)和(e)中可以看到,增大孔径也可以降低两个方向的拉应力;特别地,当热影响区的大小(d一6)不变,仅是增大孔径时也可以有效地降低打孑L的拉应力(如图4(f)和(g)所示)。
由(3)式可知在这种情况下温度场分布只是存在平移并不发生变化,即只要将温度场分布向外平移就可以降低热应力。
因此减少热影响区大小、增大打孔孔径或向外平移温度分布都可以抑制裂纹的产生。
切割的热应力分析由于切缝的存在而变得复杂,对于这种非轴对称的温度应力场的计算一般很难得到解析解,因此需要将切割过程的温度场以及应力分布在近似范围内进行合理简化。
切割过程图3温度对径向应力(a)和切向应力(b)的影响Fig.3Effectoftemperaturethermal-stressof(a)radialand(b)tangentdirection中,冷却气体对切缝的强冷却效果会导致切缝边缘具有温度较低的重凝层,因此可以将不在光斑覆盖范围内的切缝边缘看成是刚性的且一般切缝宽度很窄(o.1mm左右),又因为激光切割陶瓷一般采用脉冲方式,因此可以将脉冲激光切割近似为一系列打孔过程。
上述打孔热应力分析即可适用于脉冲激光切割,不同之处在于脉冲激光切割过程中脉冲间隔很近,会有热积累效应,即前一个脉冲作用的温度场会与后一个脉冲作用的温度场相叠加,导致加工处温度不断升高。
从图3中可知温度的升高会导致两个方向拉应力的显著提高,而增加裂纹的产生。
因此对脉冲切割的参数优化强度要高于打孔的参数优化,但基本思想还是:降低切缝边缘温度、减少热影响区以及增大切缝宽度。
2.2激光加工过程的裂纹行为预测从图2中可以看到,加工区域附近产生了很大的切向拉应力,这种应力的作用使得材料加工边缘的薄弱点成为裂纹的起点产生张开型裂纹,开裂的方向为径向,如图5中沿径向的裂纹处所示。
而图2中所示径向应力则在一定半径内迅速提高到拉应力的最大值,产生环行裂纹或是改变已扩展裂纹的传播方向。
图2所示应力较大的位置集中在距离加工处很近的一个环形区域,裂纹也将会在此区域出现,如图5中沿切向的裂纹处所示。
由于模型并没有针对某种特定的材料,所以无论对于何种材料,在 万方数据1404中国激光3i卷图4热影响区和孑L径对应力分布的影响曲线。
(a)热影响区半径d对径向成力的影响;(b)热影响Ⅸ半径d对切向应力的影响;(c)网4(b)中切向应力前端局部放大图;(d)孑L径大小b对径向脱力分布的影响;(e)孑L径大小b对切向应力分布的影响;(f)热影响区位置对径向应力分布的影响;(g)热影响区位置对切向应力分布的影响Fig.4Effectofheataffectedandholeradiusthermal—stress.(a)effectofheatafleetedradiusdthermal—ofradialdirection;(b)effectofheataffectedradiusdthermal—stressoftangentdirection:(c)anenlargefigureofFig.4(b)ontangentstressfount;(d)effectofholesradiusbthermal—stressofradialdirection;(e)effectofholesradiusbthermal—stressoftangentdirection;(f)effectofheataffectedpos;itionthermal—stressofradialdirection;(g)effectofheataffectedpositionthermal—stressoftangentdirection激光打孔过程中。
都会在其热影响区的一定范围内产生径向和切向拉应力,当拉应力超过材料的断裂阈值时将导致环形和径向裂纹的产生。
脉冲切割中每个脉冲产牛的热应力分布均应满万方数据9期同胤洲等:激光加工陶瓷裂纹行为的理论分析及实验验证1405图5裂纹形态趋势图Fig.5Sketchmapofcracksforms足(6)式,裂纹沿拉应力极大值进行扩展。
根据应力极大值的组合,将出现两类裂纹扩展方式——发散型和回归型。
发散型扩展方式如图6(a)所示。
由图2所示打孔应力分布可知:加工边缘处为以某一角度开裂而产生径向裂纹,随着光斑的移动裂纹尖端切向应力方向发生改变(图6(a)中所标半径方向),裂纹扩展的角度变大,引导裂纹进一步向远离加工区域的方向扩展,最后得到呈放射形状的裂纹。
回归型扩展方式如图6(b)所示,裂纹初始扩展与发散型裂纹扩展类似,但扩展到达径向应力最大处,裂纹在此处发生偏转,从径向扩展转为切向扩展;随着热影响区的继续移动,切向裂纹的扩展趋于与切缝平行,当裂纹尖端的速度小于切割速度时,切向裂纹扩展有向切缝位置扩展的趋势,则裂纹又偏转到径向方向,在切向应力和移动热影响区的共同作用下,裂纹将重新回归到切缝位置。
由于该类裂纹扩展距离有限,对材料加工质量的影响要小于发散型裂纹。
实际上两种裂纹初始的扩展过程是一致的,由于在径向应力最大处两个方向的应力相近,因此裂纹有两种近图6(a)发散型裂纹扩展方式;(b)回归型裂纹扩展方式Fig.6(a)Spreadmodeofemanativecracks;(b)spreadmodeofregressivecracks似等概率的扩展方向,该处裂纹不同的偏转现象形成了两种扩展类型。
3实验结果及讨论3.1实验装置及实验对象实验中采用峰值功率为3500W的SlabC0:激光器(德国Rofin公司)作为加工能量源,激光器光束模式为TEM。
模,激光输出方式可以为连续或脉冲,脉冲频率最高可达5kHz,配以六轴联动三维加工机床作为加工平台,加工精度可达0.01mm。
加工材料分别是厚度为4mm的致密氧化铝陶瓷(密度为3.73g/cm3)和厚度为0.48mm的单晶硅。
3.2实验结果对氧化铝陶瓷和单晶硅进行打孔实验,观察裂纹的基本形态,如图7所示。
从图7(a)中可以看到径向裂纹的扩展以及在径向拉应力作用下的偏转行为;从图7(b)中可以清晰看到在单晶硅中出现的环形裂纹,与理论预测两种打孔过程中的裂纹行为相吻合。
图7脉冲激光打孔过程中两种形态的裂纹。
(a)氧化铝陶瓷打孔的径向裂纹;(b)单晶硅H4L的环型裂纹Fig.7Twotypesofcracksformsduringpulsedlaserdrilling.(a)crackalongradialdirectionwithlaserdrillingalumina;(b)crackalongtangentdirectionwithlaserdrillingsingle-crystalsilicon使用相同工艺参数进行脉冲切割,观察了切割后的裂纹形态,如图8所示。
从图8(a)可以看到切割氧化铝陶瓷的发散型裂纹扩展;从图8(b)可以看到在单晶硅的切割过程中出现的回归型裂纹,这两 万方数据中国激光3j卷种脉冲激光切割中裂纹扩展的形式与理论预测的扩展方式基本一致。
图8脉冲激光切割中两种裂纹扩展方式。
(a)氧化铝陶瓷脉冲切割的发散型裂纹;(b)单晶硅脉冲切割的回归型裂纹Fig.8Twotypesofcrackspreadduringpulsedlasercutting.(a)anemanativecrackofpulsedlasercuttingalumina;(b)aregressivecrackofpulsedlasercuttingsingle-crystalsilicon从实验中可以看出,氧化铝陶瓷更容易产生径向裂纹以及发生发散型裂纹扩展,而单晶硅则更容易产生环形裂纹以及发生回归型裂纹扩展。
初步认为这是由于两种材料的微观结构不同导致的,多晶多相的氧化铝陶瓷对切向应力更为敏感,因而容易在切向应力的作用下形成裂纹并扩展;而单晶硅对径向应力更为敏感,因此容易在径向应力的作用下形成裂纹并扩展。
3.3激光加工参数优化的讨论及实验结果激光加工陶瓷中需要优化的参数涉及:峰值功率、占空比、焦点位置和辅助气体压力。
峰值功率、占空比和辅助气体压力会对加工边缘温度T。
产生影响,峰值功率与占空比的乘积表示为平均功率,平均功率描述激光注入材料中的热量,减少平均功率可以降低材料加工的温度。
但由于激光输出功率要达到熔化材料所需的阈值,所以峰值功率不能过低,因此只能降低占空比来实现降低平均功率的目的,而且占空比降低时每个脉冲作用的时间将减少,辅助气体可以更好地冷却,与连续激光相比町以降低注入到材料中的热量。
增大冷却气体压力可形成强对流效果,也降低加工材料处的温度。
因此降低孑L边缘温度L。
抑制裂纹产生的具体方法是通过降低占空比减少平均功率并增大冷却气体压力来实现的,在可能的情况下可通过进一步提高峰值功率并降低占空比n朝以减少激光对材料的热输入量;辅助气体压力还影响到热影响区大小,当提高气体压力时,冷却效果将提高,减少热影响区大小即减少热影响区半径d,实现降低热应力减少裂纹的产生;由于聚焦光斑的发散,焦点位置影响打孔孔径,通过离焦打孔的方法可实现增大孑L径减少热应力抑制裂纹产生的目的;特别地,由图4(f)和(g)可知在不增大冷却气压时,采用离焦打孔将热影响区向外平移,同样可以降低拉应力抑制裂纹产生,防止由于气压过大而产生机械力断裂的问题。
在脉冲切割过程中,由于脉冲间隔很小,所以会在加工处存在明显的热积累效应,易在切割过程中产生大的拉应力形成裂纹,因此要进一步地降低激光输出占空比、增大气体压力并进行离焦加工,最大限度地降低热应力以抑制裂纹的产生。