电源功率器件散热器计算
电动汽车散热器计算

电动汽车散热器计算
电动汽车的散热器计算是为了确保电动汽车在工作过程中能够保持正常的温度,从而提高电池和电动机等重要部件的使用寿命。
散热器计算一般包括以下几个方面:
1. 散热功率计算:根据电动汽车各个部件的功率和热损耗来计算散热器需要处理的热量。
例如,电池组的功率损耗、电动机的功率损耗、电子控制器的功率损耗等。
2. 散热器面积计算:根据散热功率和散热器的换热能力来计算所需的散热器面积。
根据不同的散热器类型,可以使用不同的换热能力公式来计算。
3. 散热器材料选择:根据散热器工作条件和要求,选择合适的散热器材料,例如铝合金、镀锌板等。
4. 散热风扇选择:根据电动汽车散热器的设计和工作条件,选择合适的散热风扇,保证散热器能够正常工作。
需要注意的是,不同类型的电动汽车可能有不同的散热器计算要求。
因此,在进行散热器计算时,应根据具体的电动汽车型号和要求进行计算和设计。
同时,还需要考虑电动汽车在不同工况下的散热需求,例如高速行驶、低速行驶、急加速等。
功率器件热设计及散热器的优化设计

功率器件热设计及散热器的优化设计1 表征功率器件热性能的主要参数功率器件应用时所受到的热应力可能来自器件内部,也可能来自器件外部。
器件工作时所耗散的功率要通过发热形式耗散出去。
若器件的散热能力有限,则功率的耗散就会造成器件内部芯片有源区温度上升及结温升高,使得器件可靠性降低,无法安全正常工作。
表征功率器件热能力的参数主要有结温和热阻。
一般将功率器件有源区称为结,器件的有源区温度称为结温。
这些器件的有源区可以是结型器件(如晶体管)的pn结区、场效应器件的沟道区,也可以是集成电路的扩散电阻或薄膜电阻等。
当结温T j高于周围环境温度Ta时,热量通过温差形成扩散热流,由芯片通过管壳向外散发,散发出的热量随着温差(Tj-T a)的增大而增大。
为了保证器件能够长期正常工作,必须规定一个最高允许结温 Tjmax。
Tjmax的大小是根据器件的芯片材料、封装材料和可靠性要求确定的。
功率器件的散热能力通常用热阻表征,记为 RT。
热阻越大,则散热能力越差。
热阻又分为内热阻和外热阻,内热阻是器件自身固有的热阻,与管芯、外壳材料的导热率、厚度和截面积以及加工工艺等有关;外热阻则与管壳封装的形式有关。
一般来说,管壳面积越大,则外热阻越小,金属管壳的外热阻就明显低于塑封管壳的外热阻。
当功率器件的功率耗散达到一定程度时,器件的结温升高,系统的可靠性降低,为了提高可靠性,应进行功率器件的热设计。
2 功率器件热设计功率器件热设计是要防止器件出现过热或温度交变引起的热失效,可分为器件内部芯片的热设计、封装的热设计和管壳的热设计以及功率器件实际使用中的热设计。
其主要关系如图1所示。
对于一般的功率器件,在生产工艺阶段,就要充分考虑器件内部、封装和管壳的热设计,当功率器件功耗较大时,依靠器件本身的散热(芯片、封装及管壳的热设计)并不能够满足散热要求。
功率器件结温可能会超出安全结温,此时需要安装合适的散热器,通过散热器有效散热,保证器件结温在安全结温之内且能长期正常可靠的工作。
MOSFET功率开关器件的散热计算
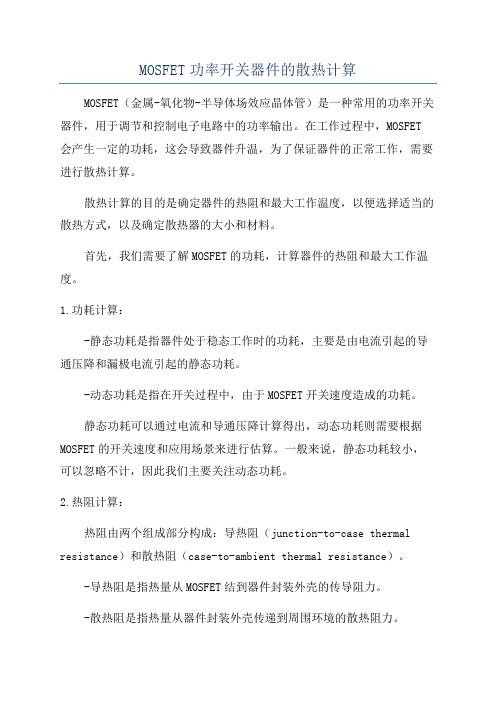
MOSFET功率开关器件的散热计算MOSFET(金属-氧化物-半导体场效应晶体管)是一种常用的功率开关器件,用于调节和控制电子电路中的功率输出。
在工作过程中,MOSFET 会产生一定的功耗,这会导致器件升温,为了保证器件的正常工作,需要进行散热计算。
散热计算的目的是确定器件的热阻和最大工作温度,以便选择适当的散热方式,以及确定散热器的大小和材料。
首先,我们需要了解MOSFET的功耗,计算器件的热阻和最大工作温度。
1.功耗计算:-静态功耗是指器件处于稳态工作时的功耗,主要是由电流引起的导通压降和漏极电流引起的静态功耗。
-动态功耗是指在开关过程中,由于MOSFET开关速度造成的功耗。
静态功耗可以通过电流和导通压降计算得出,动态功耗则需要根据MOSFET的开关速度和应用场景来进行估算。
一般来说,静态功耗较小,可以忽略不计,因此我们主要关注动态功耗。
2.热阻计算:热阻由两个组成部分构成:导热阻(junction-to-case thermal resistance)和散热阻(case-to-ambient thermal resistance)。
-导热阻是指热量从MOSFET结到器件封装外壳的传导阻力。
-散热阻是指热量从器件封装外壳传递到周围环境的散热阻力。
导热阻可以通过器件手册或厂商提供的数据手册来获得,散热阻可以通过热量传导理论和计算公式来估算。
3.最大工作温度:最大工作温度可以通过器件手册或厂商提供的数据手册来获得。
有了以上的基础知识,我们可以按照以下步骤进行MOSFET的散热计算:1.根据应用场景和数据手册提供的参数,计算出MOSFET的功耗。
2.根据功耗计算出MOSFET的热阻(包括导热阻和散热阻)。
3.确定最大工作温度,通常根据数据手册提供的温度参数来确定。
4.根据最大工作温度和热阻,计算出器件离开环境的温度差。
5.根据热耗的温度差和功耗,计算出散热器的尺寸和材料。
需要注意的是,散热计算是一个非常复杂的过程,涉及到多方面的因素,包括器件的封装类型、散热器的设计和材料选择等。
散热器尺寸设计计算方法

散热器尺寸设计计算方法1.散热器面积计算:散热器的面积是散热效果的关键因素之一、根据散热器的材料、形状和工况要求,可以计算出散热器需要的面积。
常用的计算公式如下:A=Q/(U*ΔT)其中,A为散热器面积(m^2),Q为需要散热的功率(热量,W),U为散热器的总传热系数(J/(m^2·s·K)),ΔT为散热器的温差(K)。
2.散热器尺寸计算:散热器的尺寸也是影响散热效果的重要参数。
常用的尺寸设计计算方法有以下几种:(1)翅片间距计算:翅片间距是翅片散热器的一个重要参数,影响散热器的散热面积。
一般情况下,翅片间距需要与相邻的翅片高度相等,以确保散热面积充分利用。
翅片间距计算公式如下:S=H/(N+1)其中,S为翅片间距(m),H为散热器的高度(m),N为翅片数量。
(2)翅片厚度计算:翅片厚度会影响散热器的散热效果和机械强度,一般情况下,翅片厚度越小,散热效果越好。
根据散热器的散热面积和翅片的数量,可以计算出翅片的厚度。
翅片厚度计算公式如下:T=A/(N*L)其中,T为翅片厚度(m),A为散热器的面积(m^2),N为翅片数量,L为散热器的长度(m)。
(3)散热管直径计算:散热管的直径也是散热器的一个重要尺寸参数。
直径越大,散热效果越好,但同时也会增加材料成本。
根据散热器的总传热系数和散热管的数量,可以计算出散热管的直径。
D=sqrt((4Q)/(P*π*N))其中,D为散热管的直径(m),Q为需要散热的功率(W),P为散热管的壁厚(m),N为散热管的数量。
除了上面介绍的计算方法,根据具体的散热要求和特殊情况,也可以采用一些其他的尺寸设计计算方法。
需要根据实际情况选择合适的计算方法,确保散热器的散热效果和稳定性。
散热器的计算
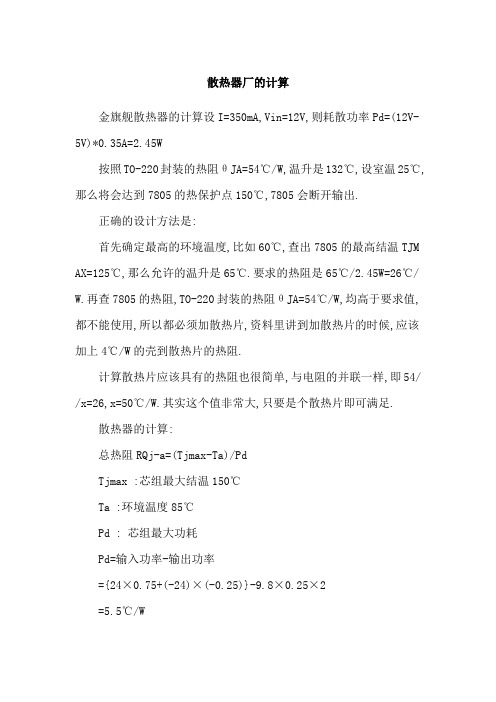
散热器厂的计算金旗舰散热器的计算设I=350mA,Vin=12V,则耗散功率Pd=(12V-5V)*0.35A=2.45W按照TO-220封装的热阻θJA=54℃/W,温升是132℃,设室温25℃,那么将会达到7805的热保护点150℃,7805会断开输出.正确的设计方法是:首先确定最高的环境温度,比如60℃,查出7805的最高结温TJM AX=125℃,那么允许的温升是65℃.要求的热阻是65℃/2.45W=26℃/ W.再查7805的热阻,TO-220封装的热阻θJA=54℃/W,均高于要求值,都不能使用,所以都必须加散热片,资料里讲到加散热片的时候,应该加上4℃/W的壳到散热片的热阻.计算散热片应该具有的热阻也很简单,与电阻的并联一样,即54/ /x=26,x=50℃/W.其实这个值非常大,只要是个散热片即可满足.散热器的计算:总热阻RQj-a=(Tjmax-Ta)/PdTjmax :芯组最大结温150℃Ta :环境温度85℃Pd : 芯组最大功耗Pd=输入功率-输出功率={24×0.75+(-24)×(-0.25)}-9.8×0.25×2=5.5℃/W总热阻由两部分构成,其一是管芯到环境的热阻RQj-a,其中包括结壳热阻RQj-C和管壳到环境的热阻RQC-a.其二是散热器热阻RQd-a,两者并联构成总热阻.管芯到环境的热阻经查手册知 RQj-C=1.0 R QC-a=36 那么散热器热阻RQd-a应<6.4. 散热器热阻RQd-a=[(10/kd) 1/2+650/A]C其中k:导热率铝为2.08d:散热器厚度cmA:散热器面积cm2C:修正因子取1按现有散热器考虑,d=1.0 A=17.6×7+17.6×1×13算得散热器热阻RQd-a=4.1℃/W,散热器选择及散热计算目前的电子产品主要采用贴片式封装器件,但大功率器件及一些功率模块仍然有不少用穿孔式封装,这主要是可方便地安装在散热器上,便于散热。
功率器件的散热计算及散热器选择

司产 品)作 低频 功 放 ,其 电路如 图 1 所
器件 为 8引脚 T 3 属外 壳 封装 O一 金 0 1  ̄ W ;若 器件 底 面 不绝 缘 需 示 。 ~0 2C/ 器 件 丁作 条 件 如 要 另 外 加 云 母 片 绝 器 件上 还 采用 流动 冷水 冷却 板 , 它有 更 下 作 电压 ±V 工 s 缘 , 其 R 可达 1 则 一 ℃/ 好 的散 热效 果 。 为 ±1 V 8 ;负 载 阻 W P 为 实 际的最 大 。 散 热 计 算 就 是 在 一 定 的 _作 条件 r 抗 R 为 4 Q, T 损 耗 功 率 ,可 根 据 不 下 , 过 计算 来 确 定 合适 的散 措 施及 通 作 频 率 直 流 条 件 同器 件 的工 作 条件 计
R ≤ o P r T )/ 一
割成 一 定 长度 而制成 非 标准 的散热 器
散 热 器 的 表 面处 理有 电 泳 涂 漆 或
可靠 地 r 作
则 计算 最 夫 允许 的 散 热 器 到 环 境 黑 色 氧极 化 处 理 , 口的是 提 高散 热 敢 其
温度 的 热 阻 R 为 一
率 及 绝 缘 性 能 :在 自然 冷 却 下 可 提 高 1 ~1 % , 0 5 在通 风 冷却 下 可提 高 3 , % 电
泳涂 漆 可 耐压 5 0 0 v 0  ̄8 0
散 热计 算
任何器件在 1作时都有 一 耗 定 的 损 大部 分 的损 耗 变成 热 量 。小功 率 器
’ r
计 算 实例
一
常 用 的 就 是 将 功 率 器 件 安 装 在 散 热 器
利 用散 热器 将 热 量散 到 刷 隔 空 间 , 必 要 时 冉加 上散 热 风 扇 , 一定 的风速 加 强 冷却 散 热 = 某些 大 型设 备 的 功率 在
dcdc热计算

dcdc热计算DC/DC热计算是指在直流电源中,对DC/DC变换器的热特性进行计算和分析,以确保变换器在工作过程中能够正常工作并避免过热导致故障。
热计算是设计和优化变换器的重要环节,可以帮助工程师选取合适的散热方案、确定合适的元器件等。
一、热计算的基本原理DC/DC热计算主要是通过计算各个元器件的功率损耗来得到整个变换器的热功率,然后再根据散热系统的特性来计算温度分布。
常见的元器件包括开关管、二极管、电感、电容等。
在计算功率损耗时,需要考虑元器件的导通和关断功耗,以及开关过程中的损耗。
二、热计算的步骤1.确定输入和输出电压:根据设计需求,确定变换器的输入和输出电压,以确定变换器的电流大小。
2.计算输入功率:根据输入电压和电流大小,计算出输入电路的功率。
3.计算输出功率:根据输出电压和电流大小,计算出输出电路的功率。
4.计算开关管功耗:开关管的功耗主要来自于导通和关断过程中的损耗。
通过计算开关管导通时间和关断时间,结合开关管的电流和电压,可以计算出开关管的功耗。
5.计算二极管功耗:二极管的功耗主要来自于导通过程中的正向电压降和反向电流。
通过计算二极管导通时间和二极管的电流和电压,可以计算出二极管的功耗。
6.计算电感功耗:电感的功耗主要来自于电流的涨落引起的损耗。
通过计算电感的电流大小,以及电感的电阻和电感系数,可以计算出电感的功耗。
7.计算电容功耗:电容的功耗主要来自于电流的涨落引起的损耗。
通过计算电容的电流大小,以及电容的电阻和电容系数,可以计算出电容的功耗。
8.计算散热器的热阻:根据散热器的材料和结构,可以计算出散热器的热阻。
同时需要根据散热器的面积和空气流速等因素,确定散热器的热导率。
9.计算变换器的温度分布:根据计算得到的功率损耗,结合散热器的热阻和热导率,可以计算出变换器的温度分布。
通过温度分布的计算,可以判断是否需要增加散热器、增加风扇、改进散热系统等。
三、热计算的应用DC/DC热计算广泛应用在工业控制、电源设计、电动机控制和通信等领域。
功率器件的散热计算及散热器选择
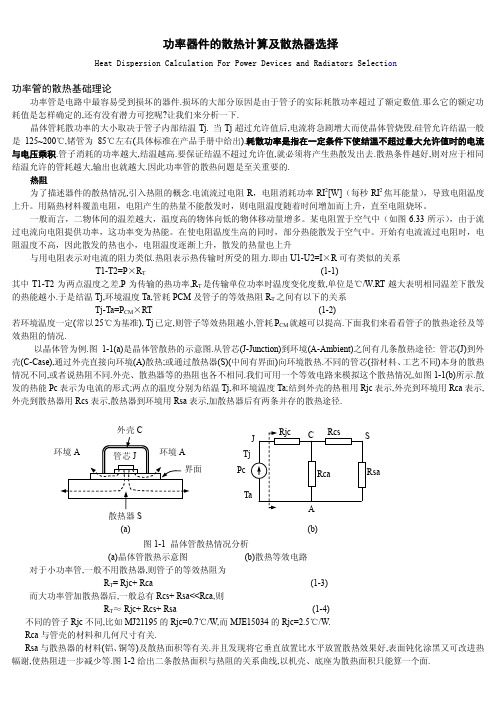
不同的管子 Rjc 不同,比如 MJ21195 的 Rjc=0.7℃/W,而 MJE15034 的 Rjc=2.5℃/W.
Rca 与管壳的材料和几何尺寸有关.
Rsa 与散热器的材料(铝、铜等)及散热面积等有关.并且发现将它垂直放置比水平放置散热效果好,表面钝化涂黑又可改进热
幅谢,使热阻进一步减少等.图 1-2 给出二条散热面积与热阻的关系曲线,以机壳、底座为散热面积只能算一个面.
其中 T1-T2 为两点温度之差,P 为传输的热功率,RT 是传输单位功率时温度变化度数,单位是℃/W.RT 越大表明相同温差下散发
的热能越小.于是结温 Tj,环境温度 Ta,管耗 PCM 及管子的等效热阻 RT 之间有以下的关系
Tj-Ta=PCM×RT
(1-2)
若环境温度一定(常以 25℃为基准), Tj 已定,则管子等效热阻越小,管耗 PCM 就越可以提高.下面我们来看看管子的散热途径及等
量散到周围空间。若没有风扇以一定风速冷却,这称为自然冷却或自然对流散热。 热量在传递过程有一定热阻。由器件管芯传到器件管壳的热阻为 Rjc,器件管壳与散热器之间的热阻为 Rcs,散热器将热
量散到周围空间的热阻为 Rsa,总的热阻 Rja=Rjc+R cs+R sa。若器件的最大功率损耗为 PD,并已知器件允许的结温为 Tj、环 境温度为 TA,可以按下式求出允许的总热阻 Rja。
Rcs 是管壳与散热器界面的热阻.可分为接触热阻和绝缘层热阻.接触热阻取决于接触面的情况,如面积大小、压紧程度等. 若在界面涂导热性能较好的硅脂可减少热阻.当需要与散热器绝缘时(如利用外壳、底座进行散热的情况),垫入绝缘层也会形成 热阻.绝缘层可以是 0.05~0.1mm 厚的云母片或采用阳极氧化法在表面形成的绝缘层.
- 1、下载文档前请自行甄别文档内容的完整性,平台不提供额外的编辑、内容补充、找答案等附加服务。
- 2、"仅部分预览"的文档,不可在线预览部分如存在完整性等问题,可反馈申请退款(可完整预览的文档不适用该条件!)。
- 3、如文档侵犯您的权益,请联系客服反馈,我们会尽快为您处理(人工客服工作时间:9:00-18:30)。
电源功率器件散热器计算
一、7805 设计事例
设I=350mA,Vin=12V,则耗散功率
Pd=(12V-5V)*0.35A=2.45W。
按照TO-220
封装的热阻θJA=54℃/W,温升是132℃,设室温25℃,那么
将会达到7805 的
热保护点150℃,7805 会断开输出。
二、正确的设计方法是:
首先确定最高的环境温度,比如60℃,查出民品7805 的最高结
温
Tj(max)=125℃,那么允许的温升是65℃。
要求的热阻是
65℃/2.45W=26℃/W。
再查7805 的热阻,TO-220 封装的热阻θJA=54℃/W,
TO-3 封装(也就是大家说的“铁壳”)的热阻θJA=39℃/W,均
高于要求值,都不能使用(虽然达不到热保护点,但是超指标使用还
是不对的),所以不论那种封装都必须加散热片。
资料里讲到加散热片
的时候,应该加上4℃/W 的壳到散热片的热阻。
计算散热片应该具有的热阻也很简单,与电阻的并联一样,即
54//x=26,
x=50℃/W。
其实这个值非常大,只要是个散热片即可满足。
三、散热片尺寸设计
散热片计算很麻烦的,而且是半经验性的,或说是人家的实测结果。
基本的计算方法是:
1.最大总热阻θja =(器件芯的最高允许温度TJ -最高环境
温度
TA )/ 最大耗散功率
其中,对硅半导体,TJ 可高到125℃,但一般不应取那么高,温度太高会降
低可靠性和寿命。
最高环境温度TA 是使用中机箱内的温度,比气温会高。
最大耗散功率见器件手册。
2.总热阻θja=芯到壳的热阻θjc +壳到散热片的θcs +散热片到环
境的θsa
其中,θjc 在大功率器件的DateSheet 中都有,例如3---5
θcs对TO220 封装,用2 左右,对TO3 封装,用3 左右,加导热硅脂后,
该值会小一点,加云母绝缘后,该值会大一点。
散热片到环境的热阻θsa 跟散热片的材料、表面积、厚度都有关系,作为
参考,给出一组数据例子。
a.对于厚2mm 的铝板,表面积(平方厘米)和热阻(℃/W)的对应关系是:
中间的数据可以估计了。
b.对于TO220,不加散热片时,热阻θsa 约60--70 ℃/W。
可以看出,当表
面积够大到一定程度后,一味的增大表面积,作用已经不大了。
据称,厚度
从 2 mm 加到 4 mm 后,热阻只降到0.9 倍,而不是0.5 倍。
可见一味的加
厚作用不大。
表面黑化,θsa 会小一点,注意,表面积是指的铝板二面的面积之和,但紧贴电路板的面积不应该计入。
对于型材做的散热片,按表面积算出的θsa 应该打点折扣……
说到底,散热片的计算没有很严格的方法,也不必要严格计算。
实际中,
是按理论做个估算,然后满功率试试看,试验时间足够长后,根据器件表面
温度,再对散热片做必要的更改。
国产散热器厂家其实就是把铝型材做出来,然后把表面弄黑。
热阻这种
最基本的参数他们恐怕从来就没有听说过。
如果只考虑散热功率芯片的输入输出电压差X 电流是芯片的功耗,这就是散热片的散热功率。