煤化工工艺学课件6.1 费托合成
合集下载
化工工艺学煤化学加工PPT教案
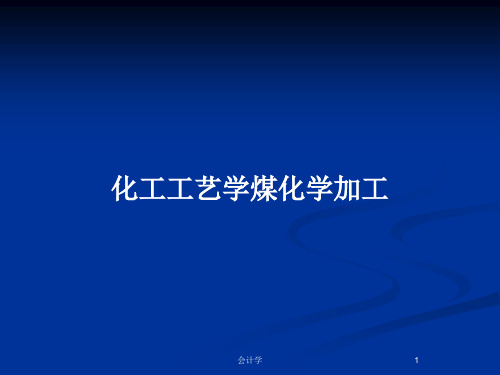
灰分和灰熔点:灰分越低越好,固态排渣炉要求 灰熔点高,气化温度不能超过灰熔点;而液态排 渣则需要灰熔点低,气化温度必须超过灰熔点。
挥发组分:容易挥发组分首先反应或者混入产生 的煤气中,影响煤气化过程和气化结果。总的来 说,挥发组分350~450ºC时就形成 胶质体,发生软化、熔融,有液相产物与煤粘在 一起,析出挥发物固化后形成块状焦炭。这种煤 气化时需要破粘措施。由于有粘结性,所以用它 作焦化气热值高。 过程:粒度5~30mm的煤间歇加入炉内,但炉
内布料器上存煤多,煤进入炉膛燃烧区是连续 的。炉内设有破粘装置。 煤气化压力约3MPa,水蒸气和氧气由转动炉箅 进入气化炉,生成的煤气由上部引出,灰渣经 下部灰箱排出。煤粒在炉内从上到下移动经过 干燥层、热解层、气化层、燃烧层。 鲁奇加压气化炉如图9.4. 鲁奇加压气化流程如图9.5.牛牛文档分享图 9.6 图 9.7
牛牛文档分享煤反应能力一个典型煤反应速率常数与温度关系如9.8.
通常情况下随温度升高反应速率是上升的。但是 在600~700ºC 之间有异常。其加热反应速率大约 为恒温600ºC的3倍,为700ºC的2倍。原因是反应 温度较高时热解反应剧烈有中间产物和ification of coal
概述
煤气化是煤与气化剂作用生成气体混合物的反应 过程。目的是将煤转化成可燃气体。煤气化过程 包含煤的热解、半焦的气化等过程。煤气的主要 组成为CO,CO2,H2,CH4,H2O.
1. 煤气分类及用途
还原气是指炼铁过程中产生的可燃性气体,要求其 中水蒸气和二氧化碳含量较少,较多时应将其除去。
(3)城市煤气
城市煤气要求含氢气和甲烷较多,硫含量少,以提对气化的影响
水分:水分较高时只适宜用固定床气化法,因为 这种方法床内温度高。
挥发组分:容易挥发组分首先反应或者混入产生 的煤气中,影响煤气化过程和气化结果。总的来 说,挥发组分350~450ºC时就形成 胶质体,发生软化、熔融,有液相产物与煤粘在 一起,析出挥发物固化后形成块状焦炭。这种煤 气化时需要破粘措施。由于有粘结性,所以用它 作焦化气热值高。 过程:粒度5~30mm的煤间歇加入炉内,但炉
内布料器上存煤多,煤进入炉膛燃烧区是连续 的。炉内设有破粘装置。 煤气化压力约3MPa,水蒸气和氧气由转动炉箅 进入气化炉,生成的煤气由上部引出,灰渣经 下部灰箱排出。煤粒在炉内从上到下移动经过 干燥层、热解层、气化层、燃烧层。 鲁奇加压气化炉如图9.4. 鲁奇加压气化流程如图9.5.牛牛文档分享图 9.6 图 9.7
牛牛文档分享煤反应能力一个典型煤反应速率常数与温度关系如9.8.
通常情况下随温度升高反应速率是上升的。但是 在600~700ºC 之间有异常。其加热反应速率大约 为恒温600ºC的3倍,为700ºC的2倍。原因是反应 温度较高时热解反应剧烈有中间产物和ification of coal
概述
煤气化是煤与气化剂作用生成气体混合物的反应 过程。目的是将煤转化成可燃气体。煤气化过程 包含煤的热解、半焦的气化等过程。煤气的主要 组成为CO,CO2,H2,CH4,H2O.
1. 煤气分类及用途
还原气是指炼铁过程中产生的可燃性气体,要求其 中水蒸气和二氧化碳含量较少,较多时应将其除去。
(3)城市煤气
城市煤气要求含氢气和甲烷较多,硫含量少,以提对气化的影响
水分:水分较高时只适宜用固定床气化法,因为 这种方法床内温度高。
费托合成 ppt课件
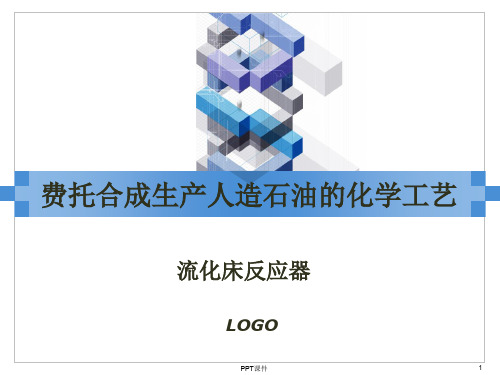
FFB反应器上方提供了足够的自由空间以分离出 大部分催化剂,剩余的部分催化剂则通过反应器 顶部的多孔金属过滤器被全部分离出并返回床层
由于催化剂颗粒被控制在反应器内,因而催化剂 回收系统可取消,除节省投资外,冷却更有效, 也增加了总的热效率
由于FFB反应器的直径可远大于CFB反应器,安 装冷却盘管的空间增加了50%以上,这使得转化 率更高,产能也得到提高
4000×104L/a
公司
1937 中压法FTS开发成功
1937 引进德国技术以钴催化剂为核心的FTS合成厂建成投产
日本与中国锦 州石油六厂
1944
中压法过程中采用合成气循环工艺技术,FTS合成油厂进一 步发展
德国
1945后 FTS受石油工业增长的影响,其工业化发展受到影响
1952 5×104t/a煤基FTS合成油和化学品3 工厂建成
②相对固定床反应器产量高
③在线装卸催化剂容易、装置运转时间长
④热效率高、压降低、反13 应器径向温差低
流化床反应器
固定流化床(FFB)
固定流化床反 应器是一个带有气 体分配器的塔,流 化床为催化剂,床 层内置冷却盘管, 配有从气相产品物 流中分离催化剂的 设备
14
PPT课件
流化床反应器
PPT课件
12
PPT课件
流化床反应器
PPT课件
原料气从反应器底部进入,与立管中经滑阀下 降的热催化剂流混合,将气体预热到反应温度, 进入反应区。大部分反应热由反应器内的两组 换热器带出,其余部分被原料气和产品气吸收。 催化剂在较宽的沉降漏斗中,经旋风分离器与 气体分离,由立管向下流动而继续使用。
循环流化床反应器特点 ①初级产物烯烃含量高
co在固体催化剂作用下非均相氢化生成不同链长的烃类混合物和含氧化合物的反应以煤为原料经过气化生成合成气然后经fts制取液体产品被称为煤的间接液化法fts反应作为煤炭间接液化过程中的重要反应近半个世纪来受到各国学者的广泛重视目前fts已成为煤间接液化制取各种烃类及含氧化合物的重要方法之一fts历史背景时间发展进程主要研究者1923发现co和h在铁类催化剂上发生非均相催化反应可合成直链烷烃和烯烃为主的化合物其后命名为ftsffischer和htropsch1936常压多级过程开发成功建成第一座以煤为原料的fts油厂400010德国鲁尔化学公司1937中压法fts开发成功1937引进德国技术以钴催化剂为核心的fts合成厂建成投产日本与中国锦州石油六厂1944中压法过程中采用合成气循环工艺技术fts合成油厂进一步发展德国1945后fts受石油工业增长的影响其工业化发展受到影响1952510ta煤基fts合成油和化学品工厂建成前苏联fts历史背景时间发展进程主要研究者19534500ta的铁催化剂流化床合成油中试装置建成中国科学院原大连石油研究所1955建立以煤为原料的大型fts合成厂采用arge固定床反应器中压法沉淀铁催化剂sasol公司1970提出fts合成在钴催化剂上最大程度上制备重质烃然后再在加氢裂解与异构化催化剂上转化为油品的概念荷兮shell公司1970浆态床反应器技术mtg工艺和zsm5催化剂开发成功美国mobil公司1980sasol建成投产中压法循环流化床反应器熔融铁催化剂sasol公司改进kelloggcfbfts历史背景时间发展进程主要研究者1982sasol建成投产中压法循环流化床反应器熔融铁催化剂sasol公司1982提出将传统的fts与沸石分子筛相结合的固定床两段合成工艺mft工艺中国科学院山西煤炭化学研究所1985新型钴基催化剂和重质烃转化催化剂开发成功荷兮shell公司1993采用smds中间馏分油合成工艺在马来西亚的bintulu建成以天然气为原料年产5010ta液体燃料包括中间馏分油和石蜡荷兮shell公司1994采用mft工艺及femn超细催化剂进行2000ta工业试验中国科学院山西煤炭化学研究所fts技术现状南非sasol公司的低温铁系催化剂固定床低温铁系催化剂浆态床高温铁系催化剂循环流化床高温铁系催化剂固定流化床和低温钴系催化剂浆态床费托合成技术
费托合成催化剂选择与处理—催化剂的装填与卸料(煤制油技术课件)

01
催化剂的装填
3 催化剂补充
对合成反应器内失活和流失催化剂的补充,这时合成反应器处 于正常操作阶段,合成反应器内的温度、压力都较高,催化剂的补充 加入量比较小。催化剂加入时需要注意保持合成反应器的操作平稳, 防止由于催化剂加入时产生液泛现象。在催化剂加入合成反应器前, 需要根据加入量提前将合成反应器的液位降低。保障在催化剂加入后 合成反应器操作液位的稳定。
还原反应器还原好的催化剂加入到合成反应器中,分合成反应 器开车加入和对合成反应器内流失、失活催化剂的补充两种方式。
01
催化剂的装填
2 开车加入
合成反应器内还没有催化剂,催化剂的加入需要时间较长,在 催化剂加入前,合成反应器的温度、压力维持在正常操作水平。在催 化剂全部加入结束前,需根据催化剂加入量控制进合成反应器的合成 气流量,注意保持合成反应器的操作平稳,催化剂加入速度可根据还 原反应器与合成反应器的压差调整。
02
催化剂的卸出
(1)紧急情况下还原反应器需要卸出催化剂时,首先还原反 应器系统降压,降至1.0MPa。
(2)确认渣蜡减压罐接收正常,调节压力调节阀开度,继续 给还原反应系统降压,待还原反应系统压力降到0.6~0.8MPa时, 关闭调节阀,还原反应器系统维持一定的压力。开启还原反应器卸 料口阀门,向渣蜡减压罐卸料。催化剂浆料卸出后,关闭催化剂卸 料阀。
煤间接液化 -催化剂的装填与卸出
目录
01 催化剂的装填 02 催化剂的卸出
01
催化剂的装填
费托合成采用浆态床反应器, 浆态床反应器的催化剂实行在线 补充加入,可以实现合成反应器 的连续操作运行。
01
催化剂的装填
1 催化剂装填
正常生产时,催化剂在还原反应器内还原后再补充到合成反应 器内。还原反应器催化剂装填采用程序控制加催化剂,还原反应器装 填重柴后,启动催化剂加料程序顺序控制。
费托合成催化剂选择与处理—催化剂还原工艺原理(煤制油技术课件)

01
铁基催化剂还原工艺原理
研究表明:不同还原气氛如纯H2、纯CO、H2+CO混合气体对催化剂活性的影响不同。 结果表明,使用富H2合成气、纯CO或富CO合成气还原低温沉淀铁催化剂,都可以获得令人 满意的催化活性。在研究不同还原气氛对负载Cu/K/Si 的Fe基催化剂费托合成性能影响时发 现,纯H2还原的催化剂能最快达到稳定状态,其次是(H2 +CO)还原的催化剂,而未还原 和纯CO还原的催化剂经过很长时间才能达到稳定状态。初始活性顺序为:(H2 +CO)还原 >H2还原>CO还原>未还原,而稳定活性顺序为:CO还原>(H2 +CO)还原>H2还原> 未还原。未还原和H2还原催化剂的甲烷选择性随反应时间的延长而增加,而CO还原和(H2 +CO)还原催化剂的甲烷选择性随反应时间的延长而降低。(H2 +CO)还原的催化剂甲烷选择 性最大, H2还原的催化剂起始甲烷选择性小于CO还原的催化剂,超过60h后甲烷选择性却 反超。
钴基催化剂组成不同,其最佳还原温度也不同,如对于负载SiO2/Al2O3 或负载ZrO2-SiO2-Al2O3的Co基催化剂,费托合成活性还原温度为350-450℃。
01
铁基催化剂还原工艺原理
铁基催化剂还原主要反应
3Fe2O3 + H2
2 Fe3O4 + H2O
Fe3O4 +4H2
3Fe+ 4H2O
3Fቤተ መጻሕፍቲ ባይዱ2O3 +CO
2 Fe3O4 +CO2
xFe3O4 +(4x+6)CO
3FexC+(4x+3)CO2
2CO
C+CO2
(3-1) (3-2) (3-3) (3-4) (3-5)
费托合成—影响费托合成反应的因素(煤制油技术课件)

钴催化剂在常压时就有足够活性,当表压介于0.1~0.5MPa时,其活性和寿命都比常压时高; 但当压力超过1.5MPa时,由于产物脱附严重受阻,导致烃类产物产率开始下降。同时,压力 增加,气相产物产率下降,碳原子数超过C18的重质烃明显增加,且烯烃对烷烃的比例下降。
06
空速的影响
空速增大,装置的生产能力或处理量也会增加,但同时会导致转化率下降,所以必须 通过优化合理地选择空速和转化率。使用铁基催化剂,空速在一定范围内增加,转化率 和烃类总产率下降不明显;使用钴基催化剂,空速增加,烃类产率明显下降,同时固体 石蜡减少、液态烃比例增加。
07
工艺参数的影响
增加反应温度、增加H2/CO比、降低铁催化剂的碱性、增加空速和降低压力有利于降低产品 中的碳原子数,即缩短碳链长度,反之则有利于增加碳链长度。
增加反应温度和提高H2/CO比,有利于增加支链烃或异构烃,反之有利于减少支链烃或异构 烃。
降低合成气中H2/CO比、提高空速、降低合成转化率和提高铁催化剂的碱性有利于增加烯烃 含量,反之不利于烯烃生成。
降低反应温度、降低H2/CO比、增加反应压力、提高空速、降低转化率和铁催化剂加碱,有 利于生成羟基和羰基化合物,反之羟基和羰基化合物的产率下降。
01
催化剂的影响
费托合成生产工艺应用的催化剂主要为铁基和钴基催化剂。铁基催化剂不但能催 化合成烃类反应,还能催化水煤气变换反应,因而对H2/CO比要求不高。在合成烃 类的催化性能方面,由于铁基催化剂的加氢活性不如钴基催化剂,其催化产物中烯 烃含量相对较高,CH4和长链烃产率较低。
02
反应器的影响
由于不同催化剂的催化机理不同,因此费托合成反应对H2/CO的比要求也不同。对生 成 烃 类 和 水 的 反 应 , H2/CO 的 化 学 计 量 比 为 2 :1 , 而 对 生 成 烃 类 和 CO2的 反 应 , 这 一 比 例为1:2。对同一催化剂,H2/CO比增加,石蜡产率下降,CH4产率增加。
06
空速的影响
空速增大,装置的生产能力或处理量也会增加,但同时会导致转化率下降,所以必须 通过优化合理地选择空速和转化率。使用铁基催化剂,空速在一定范围内增加,转化率 和烃类总产率下降不明显;使用钴基催化剂,空速增加,烃类产率明显下降,同时固体 石蜡减少、液态烃比例增加。
07
工艺参数的影响
增加反应温度、增加H2/CO比、降低铁催化剂的碱性、增加空速和降低压力有利于降低产品 中的碳原子数,即缩短碳链长度,反之则有利于增加碳链长度。
增加反应温度和提高H2/CO比,有利于增加支链烃或异构烃,反之有利于减少支链烃或异构 烃。
降低合成气中H2/CO比、提高空速、降低合成转化率和提高铁催化剂的碱性有利于增加烯烃 含量,反之不利于烯烃生成。
降低反应温度、降低H2/CO比、增加反应压力、提高空速、降低转化率和铁催化剂加碱,有 利于生成羟基和羰基化合物,反之羟基和羰基化合物的产率下降。
01
催化剂的影响
费托合成生产工艺应用的催化剂主要为铁基和钴基催化剂。铁基催化剂不但能催 化合成烃类反应,还能催化水煤气变换反应,因而对H2/CO比要求不高。在合成烃 类的催化性能方面,由于铁基催化剂的加氢活性不如钴基催化剂,其催化产物中烯 烃含量相对较高,CH4和长链烃产率较低。
02
反应器的影响
由于不同催化剂的催化机理不同,因此费托合成反应对H2/CO的比要求也不同。对生 成 烃 类 和 水 的 反 应 , H2/CO 的 化 学 计 量 比 为 2 :1 , 而 对 生 成 烃 类 和 CO2的 反 应 , 这 一 比 例为1:2。对同一催化剂,H2/CO比增加,石蜡产率下降,CH4产率增加。
煤化工工艺学课件ppt
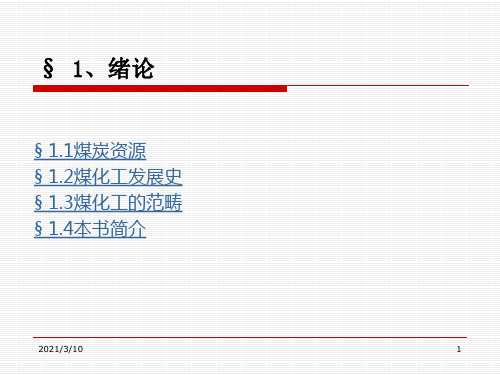
7
§ 1.4本书简介
1、绪论: 介绍煤炭资源、煤化工发展简史和煤化工范畴。
2、煤的低温干馏: 低温干馏主要原理、主要炉型、立式炉生产城市煤气以及固体 热载体干馏新工艺。
3、炼焦: 煤的成焦过程、配煤和焦炭、现代焦炉、炼焦新技术、燃烧和 传热以及流体力学。
4、炼焦化学产品的回收与精制:
粗煤气的分离、氨和粗苯的回收、粗苯精制、焦油蒸馏和沥青 加工、粗苯精制生产生产苯类产品、焦油分离精制生产酚类、 萘、蒽等。
只能处理块状煤料,干馏气态产物混入气态惰性气体热值低
2.托斯考(Toscoal)工艺
⑴原料:
非黏结性煤和弱黏结性煤(预先破黏)
⑵产品:
煤气:热值高(符合中热值城市煤气需求)
焦油:
(加氢可转化为合成原油)
半焦:有一定挥发分(可作发电厂燃料或制成无烟燃料)
2021/3/10
25
⑶托斯考干馏非黏洁性煤的流程(图2-7)
气体冷却系统
煤气
粉尘
焦油、中油
⑵ 鲁奇三段炉(固定床): ①原料:褐煤块、型煤,20~80mm,非粘结性煤
2021/3/10
21
②流程(图2—3): 三段:干燥段、干馏段和冷却段
煤
煤 槽
水
干馏炉 烟气
初冷器
电捕焦油器
冷却器
余
干
煤
燥 段
气
燃 空气
低
烧
温
室
干
气体燃料
馏
段
分离器
冷
焦油
水
却
段
焦
图2--3 气流内热式炉干馏流程
§ 1、绪论
§ 1.1煤炭资源 § 1.2煤化工发展史 § 1.3煤化工的范畴 § 1.4本书简介
§ 1.4本书简介
1、绪论: 介绍煤炭资源、煤化工发展简史和煤化工范畴。
2、煤的低温干馏: 低温干馏主要原理、主要炉型、立式炉生产城市煤气以及固体 热载体干馏新工艺。
3、炼焦: 煤的成焦过程、配煤和焦炭、现代焦炉、炼焦新技术、燃烧和 传热以及流体力学。
4、炼焦化学产品的回收与精制:
粗煤气的分离、氨和粗苯的回收、粗苯精制、焦油蒸馏和沥青 加工、粗苯精制生产生产苯类产品、焦油分离精制生产酚类、 萘、蒽等。
只能处理块状煤料,干馏气态产物混入气态惰性气体热值低
2.托斯考(Toscoal)工艺
⑴原料:
非黏结性煤和弱黏结性煤(预先破黏)
⑵产品:
煤气:热值高(符合中热值城市煤气需求)
焦油:
(加氢可转化为合成原油)
半焦:有一定挥发分(可作发电厂燃料或制成无烟燃料)
2021/3/10
25
⑶托斯考干馏非黏洁性煤的流程(图2-7)
气体冷却系统
煤气
粉尘
焦油、中油
⑵ 鲁奇三段炉(固定床): ①原料:褐煤块、型煤,20~80mm,非粘结性煤
2021/3/10
21
②流程(图2—3): 三段:干燥段、干馏段和冷却段
煤
煤 槽
水
干馏炉 烟气
初冷器
电捕焦油器
冷却器
余
干
煤
燥 段
气
燃 空气
低
烧
温
室
干
气体燃料
馏
段
分离器
冷
焦油
水
却
段
焦
图2--3 气流内热式炉干馏流程
§ 1、绪论
§ 1.1煤炭资源 § 1.2煤化工发展史 § 1.3煤化工的范畴 § 1.4本书简介
费托合成—费托合成工艺简介(煤制油技术课件)

04 铁基高温浆态床费托合成工艺特点
(1)采用铁催化剂,有利于实现大规模低成本的催化剂生产;
(2)有利于实现合成气转化过程中降低甲烷生产率、实现较高温度下合成重组分的目标,有利于提高过 程馏分油的产率; (3)催化剂的产油能力比低温浆态床大幅度提高,铁基催化剂消耗低,有利于降低合成成本和下游处理 成本,有利于实现清洁生产;
04 铁基高温浆态床费托合成工艺特点
(4)高温合成副产蒸汽压力等级高,彻底解决了低温浆态床费托合成技术的低位能过剩的问题,提高过 程的综合集成热效率; (5)浆态床反应器温度分布均匀,移热方便,容易控制,易于大型化;
(6)浆态床催化剂磨损小,可在线更换,操作周期长。
费托合成工艺简介
目录
01 费托合成工艺类型 02 费托合成工艺选择原则 03 铁基高温浆态床费托合成工艺 04 铁基高温浆型
根据使用的反应器与催化剂可将不同的费托合成工艺细分为四种典型的工艺: 铁基/钴基低温固定床费托合成技术 ; 铁基高温流化床费托合成技术 ; 铁基/钴基低温浆态床费托合成技术 ; 铁 基 高 温 浆 态 床 费 托 合 成 技 术 。
02
费托合成工艺选择原则
原则上讲,费托合成反应器系统工艺应综合考虑热力学及动力学两个方面的问 题,才能使过程达到最优化的设计。为此,集成一个有效的费托合成回路需要 根据具体过程需求,优化合理的工艺配置,在平衡各种消耗中寻找满足项目约 束条件的最佳设计参数。
03
铁基高温浆态床费托合成工艺
费托合成单元采用最新的铁基高温浆态床费托合成技术,铁基高温浆态床过程对 费托合成流程的集成就是在各种优化约束条件下,对催化剂体系重新塑造所产生的 合成工艺技术。
费托合成
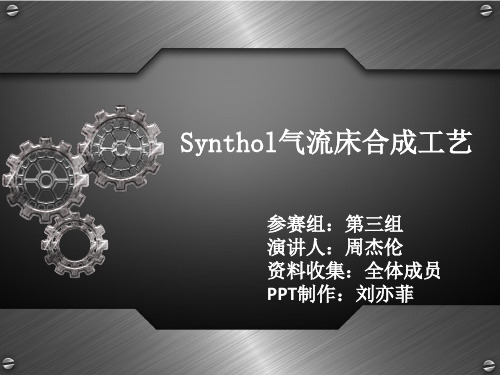
F-T合成原理
烷烃的 生成
烯烃的 生成
主要 反应
醛类的 生成
副反应
醇类的 生成
反应原理(方程式):
烷烃
烯烃
醇类
醛类
反应器
反应器
固定床反应器 流化床反应器
浆态床反应器
synthol气流床反应器
synthol反应器为循 环硫化床型。该反应 器直径为2.2米,反 用于固相加工过程或催化剂迅速失活的 循环流化床 应热由两个冷却段用 流体相加工过程。例如催化裂化过程。 循环油冷剂移出。催 化剂沉降室直径5米。 无固体物料连续进料和出料装置,用于固体 颗粒性状在相当长时间(如半年或一年)内, 固定流化床 有两个旋风分离器进 不发生明显变化的反应过程。 行分离。催化剂再经 调节阀进入合成器, 再次循环到反应器。。
Synthol气流床合成工艺
参赛组:第三组 演讲人:周杰伦 资料收集:全体成员 PPT制作:刘亦菲
目录
1 2
费托合成(总体把握) 费托合成反应器 synthol气流床反应器 工艺流程 煤液化发展前景,及个人心得
3
4 5
费托合成
费托合成是煤间接液化技术之一,是用 煤制合成气获得一氧化碳和氢气并在金属 催化剂上合成出脂肪烃和含氧化合物。 F-T合成技术包括高温F-T合成和低温F-T合 成两种。 高温F-T合成产品经加工可得到对环境友 好的汽油、柴油、溶剂油和烯烃。 低温F-T合成主产品石蜡可加工成特种蜡 或经加氢裂化/异构化生产优质柴油、润滑 油基础油,石脑油馏分还是理想的裂解原 料。
工艺流程图:
流程方块图:
合成气
反应器
竖管
催化剂沉降室 催化剂 余气
油洗塔
ቤተ መጻሕፍቲ ባይዱ
- 1、下载文档前请自行甄别文档内容的完整性,平台不提供额外的编辑、内容补充、找答案等附加服务。
- 2、"仅部分预览"的文档,不可在线预览部分如存在完整性等问题,可反馈申请退款(可完整预览的文档不适用该条件!)。
- 3、如文档侵犯您的权益,请联系客服反馈,我们会尽快为您处理(人工客服工作时间:9:00-18:30)。
合成气中的氢气与一氧化碳的摩尔比要求在2~2.5。 V(H2 )∕V(co)↗利于链烯烃、重产物及含氧物生成 ; V(H2 )∕V(co)↘利于饱和烃、轻产物及甲烷的生成;
②反应压力 P↗利于长链烃产物↗ (例:铁催化剂常压合成活性低,寿命短,一般0.7~3.0MP) ③温度 50~350℃,T↗利于甲烷等轻产物↗; (例:钴催化剂:170~210 ℃ ;铁催化剂:220~340 ℃ ) ④空速 空速增加,一般转化率低,产物变轻。 (例:钴催化剂:800~1200/h ;沉淀铁催化剂: 500~700/h;熔铁催化剂气流床: 500~1200/h ) ⑤催化剂
乙烯
乙烷 产 品 产 率 % 丙烯 丙烷
0.2
2.4 2.0 2.8
丁烯
丁烷 汽油C5~C12 柴油C13~C18
3.0
2.2 22.5 15.0
重 油
蜡
C19~C21
C22~C30
6.0
17.0 18.0 3.5
非酸性化合物
酸类
0.4
F-T合成反应器
②气流床反应器
(Synthol 反应器)
a:反应器特点: 熔铁催化剂随原料气一起 进入反应器,又随反应产物 排出反应器,催化剂在反应 器内不停地运动,循环于反 应器和催化剂沉降室之间。 是可以加入新催化剂,也可 以移走旧催化剂。 b:反应热的移出: 反应器上下两段设油冷却装 置,用以携出反应热(循环 流化床的反应段近乎处于等 温状态,催化剂床层的温差 一般小于2°C)。
2.8
3.0 2.2 22.5 15.0 6.0 17.0 18.0 3.5 0.4
2.0
8.0 1.0 39.0 5.0 1.0 3.0 2.0 6.0 1.0
F-T合成反应器
①固定床反应器(Arge 反应器) a:反应器特点: 管壳式,管内装填 沉淀铁催化剂;管 外为沸腾水. b:反应热的移出: 管外为沸腾水,通 过水的蒸发移走管 内的反应热,产生 蒸汽(为防止催化 剂失活和积碳).
c:固定床反应器的优点有: 易于操作;由于液体产品顺催化剂床层流下,催化剂 和液体产品分离容易,适于费托蜡生产。 d:固定床反应器也有不少缺点: 反应器制造昂贵。高气速流过催化剂床层所导致的高 压降和所要求的尾气循环,提高了气体压缩成本。反应 器放大昂贵。装填了催化剂的管子不能承受太大的操作 温度变化。需要定期更换铁基催化剂;所以需要特殊的 可拆卸的网格,从而使反应器设计十分复杂。重新装填 催化剂也是一个枯燥和费时的工作。 f:Arge固定床合成工艺流程
§ 6、煤间接液化
§ 6.1 费托合成
煤可以变成液体燃料吗?
汽油的成分是什么?通常是如何得到的? 费雪(F.Fischer)托普斯(H.Tropsch)的发明: 用一氧化碳和氢在金属催化剂上于常压下合成出脂肪烃 (F-T合成),除了能得到汽油之外,还能合成一些重 要的基本有机化工原料,例如,乙烯、丙烯、丁烯、
床层内催化剂颗粒处于湍流状态但整体保持静止不动。 和循环流化床相比,它们具有类似的选择性和更高的转化率。 固定流化床比循环流化床制造成本更低,这是因为它体积小 而且不需要昂贵的支承结构。 不需要定期的检查和维护。 SAS反应器中的压降较低,压缩成本也低。 积碳也不再是问题。SAS催化剂的用量大约是Synthol的50%。
320 2.2
新原料气,H2/CO比(分子)
循环比(分子) H2+CO转化率,%
1.7~2.5
1.5~2.5 60~68
2.4~2.8
2.0~3.0 79~85
新原料气流量,km3/h
反应器尺寸,直径×高,m
20~28
3×17
70~125
2.2×36
300~350
3×75
SASOL-Ⅰ 表 SASOL的FT合产品分布 Arge Synthol
g:优点: ⅰ:对原料气组成的适应性大。 即使用贫氢原料气也能正常生产,而前二种反应器在贫氢条 件下会因积碳和产生高分子蜡,破坏正常生产操作; ⅱ:产品灵活性大。 例如适当提高反应温度,减少催化剂中K2O含量,可以得到低 沸点烯烃为主要组分的产品,相反降低温度,增加K2O含量又可生 产以蜡为主的产品; ⅲ:反应器温度均匀。 冷却管内外均为液体,传热效果好,反应器温度均匀; ⅳ:反应器结构简单,投资省,热效率高,产品价格低。 ⅴ:浆态床的床层压降比固定床大大降低; ⅵ:可简易地实现催化剂的在线添加和移走;
F-T合成催化剂为多组分体系:100Ni-18ThO2-100硅胶; 100CO-5ThO2-3Mg-200硅胶
a:主金属
催化剂的活性组分,具有加氢作用、使一氧化碳的 碳氧键削弱或解离作用以及叠合作用。
b:催化剂的粒度
c:载体作用
载体不仅起到分散活性组分、提高表面积的作用, 而且可以起到提高选择性的作用。
SASOL-Ⅱ Synthol
甲烷
乙烯 乙烷 产 品 产 率 % 丙烯
5.0
0.2 2.4 2.0
10.1
4.0 6.0 12.0
11.0
7.5 13.0 11.0 37.0 11.0 3.0 0.5 6.0
丙烷
丁烯 丁烷 汽油C5~C12 柴油C13~C18 重油 蜡 非酸性化合物 酸类 C19~C21 C22~C30
c:气流床优点: 催化剂易于更新,产物很轻,生成汽油多。一台Synthol反应器相当于4~5 台Arge反应器。 d:气流床缺点: 操作复杂;从尾气中分离细小的催化剂颗粒比较困难。防止碳化铁颗粒所 引起的磨损要求使用陶瓷衬里来保护反应器壁。 f:流程
新原料气与循环气以1:2.4比例混合,加热到160℃以后进入反 应器的水平进气管,与循环热催化剂混合,进入提升管和反应器内反 应。 为了防止催化剂被蜡粘结在一起,采用较高的温度(320~340℃) 和富氢操作,合成气H2/CO=6,反应压力2.26~2.35MPa。 反应气体先在热油洗涤塔除去重质油和夹带的催化剂,塔顶温度 150℃,使塔顶产物不含重油,塔顶产物进入分离器分出轻油和水,大 部分尾气经循环压缩机返回反应器,余气再送入油吸收塔脱除C3和C4。
③水煤气变换反应: 反应①产物水汽很容易再发生反应:CO+H2O→H2+CO2 — Q
nH2+2nCO → CnH2n+nCO2 + Q
思考:如何得到高的转化率?
④醇类生成反应: 2nH2 + nCO = CnH2n+1OH + (n-1)H2O
(n+1)H2 + (2n-1)CO = CnH2n+1OH + (n-1)CO2 ⑵影响因素 ①原料气体组成 一般H2 + CO 含量高,反应速率大,转化率高。(一般要求 80%~85%)
合成反应
(燃料气)
产品分离
烃(基本化学原料, 乙烯,丙烯,丁烯,液化气) 烃(汽油,正烯烃) 烃(柴油、轻燃料油) 烃(石蜡基重油) 》 烃(固体蜡)
产品精制
水溶性含氧化合物(乙醇、丙酮等)
2.F-T合成的原理
★⑴化学反应
①烷烃生成反应: (2n+1)H2 + nCO → CnH2n+2 + nH2O + Q ① ②烯烃生成反应: 2nH2 + nCO → CnH2n + nH2O+ Q (n+1)H2+2nCO → CnH2n+2+nCO2 + Q
④浆态床反应器 SASOL的三相浆态床反应器(Slurry Phase Reactor): a:特点: 浆态床反应器属于三相流化床。床内液体是高沸点烃类油,催 化剂微粒悬浮其中,合成气以鼓泡形式通过,构成气液固三相流 化床; b:两项专利技术: SASOL浆态床技术的核心和创新是其拥有专利的蜡产物和催化 剂实现分离的工艺;此技术避免了传统反应器中昂贵的停车更换 催化剂步骤。反应器设计简单。 SASOL浆态床技术的另一专利技术是把反应器出口气体中所夹 带的“浆”有效地分离出来。
c:合成蜡与催化剂分离: 内置过滤器: (典型的浆态床反应器为了将合成蜡与催化剂分离,一般内置 2~3层的过滤器,每一层过滤器由若干过滤单元组成,每一组过 滤单元又由3~4根过滤棒组成。正常操作下,合成蜡穿过过滤棒 排出,而催化剂被过滤棒挡住留在反应器内。当过滤棒被细小的 催化剂颗粒堵塞时可以采用反冲洗的方法进行清洗。在正常工况 下一部分过滤单元在排蜡,另一部分在反冲洗,第三部分在备 用。) d:反应热移走: 反应器内设置换热盘管: (另为了将反应热移走,反应器内还设置2~3层的换热盘管,进 入管内的是锅炉给水,通过水的蒸发移走管内的反应热,产生蒸 汽。通过调节汽包的压力来控制反应温度。)
③固定流化床反应器((简称 为SAS)反应器) 名为SASOL Advanced Synthol(简称为SAS)反 应器。 a:固定流化床反应器由以下部 分组成: 气体分布器的容器; 催化剂流化床; 床层内的冷却管; 旋风分离器。 b:固定流化床反应器特点: 操作比较简单。 气体从反应器底部通过 分布器进入并通过流化床。
f:其操作过程如下: 合成气经过气体分配器在反应器截面上均匀分布,在向上流动 穿过由催化剂和合成蜡组成的浆料床层时,在催化剂作用下发生 FT合成反应。 生成的轻烃、水、CO2和未反应的气体一起由反应器上部的气 相出口排出,生成的蜡经过内置过滤器过滤后排出反应器,当过 滤器发生堵塞导致器内器外压差过大时,启动备用过滤器,对堵 赛的过滤器应切断排蜡阀门,而后打开反冲洗阀门进行发冲洗, 直至压差消失为止。 为了维持反应器内的催化剂活性,反应器还设置了一个新鲜 催化剂/蜡加入口和一个催化剂/蜡排出口。可以根据需要定期定 量将新鲜催化剂加入同时排出旧催化剂。
SASOL-Ⅰ
表 SASOL的FT合产品 分布 甲烷 Arge
5.0
煤气,经净化得H2/CO比 1.7的合成气,新鲜气与循环 气以1:2.3比例混合,混合 气被压缩到2.45MPa后,再被 换热器升温到150~180℃进 反应器进行合成反应。 反应产物先经分离器脱 去石腊烃,经换热器后再脱 去软石蜡,又经冷却器冷却 分离出烃类油,冷却器后的 余气部分循环,其余送油吸 收塔回收C3和C4烃类。 Arge反应器的产物较重, 含腊较多,见表。
②反应压力 P↗利于长链烃产物↗ (例:铁催化剂常压合成活性低,寿命短,一般0.7~3.0MP) ③温度 50~350℃,T↗利于甲烷等轻产物↗; (例:钴催化剂:170~210 ℃ ;铁催化剂:220~340 ℃ ) ④空速 空速增加,一般转化率低,产物变轻。 (例:钴催化剂:800~1200/h ;沉淀铁催化剂: 500~700/h;熔铁催化剂气流床: 500~1200/h ) ⑤催化剂
乙烯
乙烷 产 品 产 率 % 丙烯 丙烷
0.2
2.4 2.0 2.8
丁烯
丁烷 汽油C5~C12 柴油C13~C18
3.0
2.2 22.5 15.0
重 油
蜡
C19~C21
C22~C30
6.0
17.0 18.0 3.5
非酸性化合物
酸类
0.4
F-T合成反应器
②气流床反应器
(Synthol 反应器)
a:反应器特点: 熔铁催化剂随原料气一起 进入反应器,又随反应产物 排出反应器,催化剂在反应 器内不停地运动,循环于反 应器和催化剂沉降室之间。 是可以加入新催化剂,也可 以移走旧催化剂。 b:反应热的移出: 反应器上下两段设油冷却装 置,用以携出反应热(循环 流化床的反应段近乎处于等 温状态,催化剂床层的温差 一般小于2°C)。
2.8
3.0 2.2 22.5 15.0 6.0 17.0 18.0 3.5 0.4
2.0
8.0 1.0 39.0 5.0 1.0 3.0 2.0 6.0 1.0
F-T合成反应器
①固定床反应器(Arge 反应器) a:反应器特点: 管壳式,管内装填 沉淀铁催化剂;管 外为沸腾水. b:反应热的移出: 管外为沸腾水,通 过水的蒸发移走管 内的反应热,产生 蒸汽(为防止催化 剂失活和积碳).
c:固定床反应器的优点有: 易于操作;由于液体产品顺催化剂床层流下,催化剂 和液体产品分离容易,适于费托蜡生产。 d:固定床反应器也有不少缺点: 反应器制造昂贵。高气速流过催化剂床层所导致的高 压降和所要求的尾气循环,提高了气体压缩成本。反应 器放大昂贵。装填了催化剂的管子不能承受太大的操作 温度变化。需要定期更换铁基催化剂;所以需要特殊的 可拆卸的网格,从而使反应器设计十分复杂。重新装填 催化剂也是一个枯燥和费时的工作。 f:Arge固定床合成工艺流程
§ 6、煤间接液化
§ 6.1 费托合成
煤可以变成液体燃料吗?
汽油的成分是什么?通常是如何得到的? 费雪(F.Fischer)托普斯(H.Tropsch)的发明: 用一氧化碳和氢在金属催化剂上于常压下合成出脂肪烃 (F-T合成),除了能得到汽油之外,还能合成一些重 要的基本有机化工原料,例如,乙烯、丙烯、丁烯、
床层内催化剂颗粒处于湍流状态但整体保持静止不动。 和循环流化床相比,它们具有类似的选择性和更高的转化率。 固定流化床比循环流化床制造成本更低,这是因为它体积小 而且不需要昂贵的支承结构。 不需要定期的检查和维护。 SAS反应器中的压降较低,压缩成本也低。 积碳也不再是问题。SAS催化剂的用量大约是Synthol的50%。
320 2.2
新原料气,H2/CO比(分子)
循环比(分子) H2+CO转化率,%
1.7~2.5
1.5~2.5 60~68
2.4~2.8
2.0~3.0 79~85
新原料气流量,km3/h
反应器尺寸,直径×高,m
20~28
3×17
70~125
2.2×36
300~350
3×75
SASOL-Ⅰ 表 SASOL的FT合产品分布 Arge Synthol
g:优点: ⅰ:对原料气组成的适应性大。 即使用贫氢原料气也能正常生产,而前二种反应器在贫氢条 件下会因积碳和产生高分子蜡,破坏正常生产操作; ⅱ:产品灵活性大。 例如适当提高反应温度,减少催化剂中K2O含量,可以得到低 沸点烯烃为主要组分的产品,相反降低温度,增加K2O含量又可生 产以蜡为主的产品; ⅲ:反应器温度均匀。 冷却管内外均为液体,传热效果好,反应器温度均匀; ⅳ:反应器结构简单,投资省,热效率高,产品价格低。 ⅴ:浆态床的床层压降比固定床大大降低; ⅵ:可简易地实现催化剂的在线添加和移走;
F-T合成催化剂为多组分体系:100Ni-18ThO2-100硅胶; 100CO-5ThO2-3Mg-200硅胶
a:主金属
催化剂的活性组分,具有加氢作用、使一氧化碳的 碳氧键削弱或解离作用以及叠合作用。
b:催化剂的粒度
c:载体作用
载体不仅起到分散活性组分、提高表面积的作用, 而且可以起到提高选择性的作用。
SASOL-Ⅱ Synthol
甲烷
乙烯 乙烷 产 品 产 率 % 丙烯
5.0
0.2 2.4 2.0
10.1
4.0 6.0 12.0
11.0
7.5 13.0 11.0 37.0 11.0 3.0 0.5 6.0
丙烷
丁烯 丁烷 汽油C5~C12 柴油C13~C18 重油 蜡 非酸性化合物 酸类 C19~C21 C22~C30
c:气流床优点: 催化剂易于更新,产物很轻,生成汽油多。一台Synthol反应器相当于4~5 台Arge反应器。 d:气流床缺点: 操作复杂;从尾气中分离细小的催化剂颗粒比较困难。防止碳化铁颗粒所 引起的磨损要求使用陶瓷衬里来保护反应器壁。 f:流程
新原料气与循环气以1:2.4比例混合,加热到160℃以后进入反 应器的水平进气管,与循环热催化剂混合,进入提升管和反应器内反 应。 为了防止催化剂被蜡粘结在一起,采用较高的温度(320~340℃) 和富氢操作,合成气H2/CO=6,反应压力2.26~2.35MPa。 反应气体先在热油洗涤塔除去重质油和夹带的催化剂,塔顶温度 150℃,使塔顶产物不含重油,塔顶产物进入分离器分出轻油和水,大 部分尾气经循环压缩机返回反应器,余气再送入油吸收塔脱除C3和C4。
③水煤气变换反应: 反应①产物水汽很容易再发生反应:CO+H2O→H2+CO2 — Q
nH2+2nCO → CnH2n+nCO2 + Q
思考:如何得到高的转化率?
④醇类生成反应: 2nH2 + nCO = CnH2n+1OH + (n-1)H2O
(n+1)H2 + (2n-1)CO = CnH2n+1OH + (n-1)CO2 ⑵影响因素 ①原料气体组成 一般H2 + CO 含量高,反应速率大,转化率高。(一般要求 80%~85%)
合成反应
(燃料气)
产品分离
烃(基本化学原料, 乙烯,丙烯,丁烯,液化气) 烃(汽油,正烯烃) 烃(柴油、轻燃料油) 烃(石蜡基重油) 》 烃(固体蜡)
产品精制
水溶性含氧化合物(乙醇、丙酮等)
2.F-T合成的原理
★⑴化学反应
①烷烃生成反应: (2n+1)H2 + nCO → CnH2n+2 + nH2O + Q ① ②烯烃生成反应: 2nH2 + nCO → CnH2n + nH2O+ Q (n+1)H2+2nCO → CnH2n+2+nCO2 + Q
④浆态床反应器 SASOL的三相浆态床反应器(Slurry Phase Reactor): a:特点: 浆态床反应器属于三相流化床。床内液体是高沸点烃类油,催 化剂微粒悬浮其中,合成气以鼓泡形式通过,构成气液固三相流 化床; b:两项专利技术: SASOL浆态床技术的核心和创新是其拥有专利的蜡产物和催化 剂实现分离的工艺;此技术避免了传统反应器中昂贵的停车更换 催化剂步骤。反应器设计简单。 SASOL浆态床技术的另一专利技术是把反应器出口气体中所夹 带的“浆”有效地分离出来。
c:合成蜡与催化剂分离: 内置过滤器: (典型的浆态床反应器为了将合成蜡与催化剂分离,一般内置 2~3层的过滤器,每一层过滤器由若干过滤单元组成,每一组过 滤单元又由3~4根过滤棒组成。正常操作下,合成蜡穿过过滤棒 排出,而催化剂被过滤棒挡住留在反应器内。当过滤棒被细小的 催化剂颗粒堵塞时可以采用反冲洗的方法进行清洗。在正常工况 下一部分过滤单元在排蜡,另一部分在反冲洗,第三部分在备 用。) d:反应热移走: 反应器内设置换热盘管: (另为了将反应热移走,反应器内还设置2~3层的换热盘管,进 入管内的是锅炉给水,通过水的蒸发移走管内的反应热,产生蒸 汽。通过调节汽包的压力来控制反应温度。)
③固定流化床反应器((简称 为SAS)反应器) 名为SASOL Advanced Synthol(简称为SAS)反 应器。 a:固定流化床反应器由以下部 分组成: 气体分布器的容器; 催化剂流化床; 床层内的冷却管; 旋风分离器。 b:固定流化床反应器特点: 操作比较简单。 气体从反应器底部通过 分布器进入并通过流化床。
f:其操作过程如下: 合成气经过气体分配器在反应器截面上均匀分布,在向上流动 穿过由催化剂和合成蜡组成的浆料床层时,在催化剂作用下发生 FT合成反应。 生成的轻烃、水、CO2和未反应的气体一起由反应器上部的气 相出口排出,生成的蜡经过内置过滤器过滤后排出反应器,当过 滤器发生堵塞导致器内器外压差过大时,启动备用过滤器,对堵 赛的过滤器应切断排蜡阀门,而后打开反冲洗阀门进行发冲洗, 直至压差消失为止。 为了维持反应器内的催化剂活性,反应器还设置了一个新鲜 催化剂/蜡加入口和一个催化剂/蜡排出口。可以根据需要定期定 量将新鲜催化剂加入同时排出旧催化剂。
SASOL-Ⅰ
表 SASOL的FT合产品 分布 甲烷 Arge
5.0
煤气,经净化得H2/CO比 1.7的合成气,新鲜气与循环 气以1:2.3比例混合,混合 气被压缩到2.45MPa后,再被 换热器升温到150~180℃进 反应器进行合成反应。 反应产物先经分离器脱 去石腊烃,经换热器后再脱 去软石蜡,又经冷却器冷却 分离出烃类油,冷却器后的 余气部分循环,其余送油吸 收塔回收C3和C4烃类。 Arge反应器的产物较重, 含腊较多,见表。