SMT焊接工艺介绍
SMT(一)焊接工艺
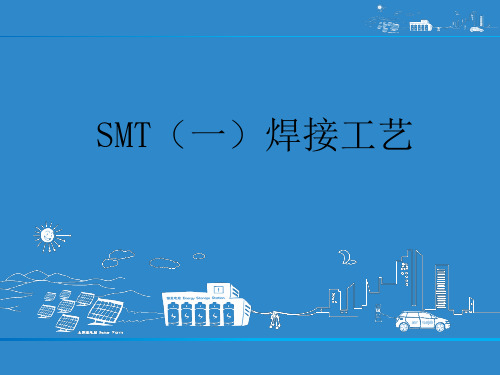
强制冷却,防止偏厚, 材质均匀,应力分散
冷热冲击试验后状态
(-40℃30分125℃30分)
材料组织破坏
爆米花效应及对策
爆米花效应又称炸锡. 产生原因:当锡膏中FLUX受到热冲击时快速挥发带出大量 的锡粉颗粒. 产生原因: 1. 锡膏过期或锡膏内添加稀释剂过量; 2. 锡膏回温不足,与空气接触后吸湿; 3. 温度曲线设置不当,升温速度过快; 4. PCB板子吸湿,加热过程出现吹气现象;
33
冷焊与葡萄球效应的区别
冷焊: 1.焊料内杂质含量太多 2.焊接前的不适当清洗 3.焊接过程温度不当
葡萄球产生原因: • 锡膏内助焊剂挥发过度,(钢网\PCB清洗时残留清洗剂)导
致锡膏中助焊剂局部失效,焊接过程中因失去助焊剂防氧 化作用,引起锡粉金属氧化,结成锡粉颗粒. • 物料电镀层金属氧化严重.焊接过程中造成金属颗粒化.
热
预 热
Flux
表面张力降低&助焊
表面清洁
促浸 进润
浸润 促進 表面清浄化
再氧化防止
母材材料 (电镀)
再氧化防止
熔 化
焊点 (Solder)
合 金 化
焊接不良 4要素不平衡状态时发生
热(回流炉槽温度) 无铅:240℃
锡膏材料組成
无铅:Sn3Ag0.5Cu
SMT焊接温度宽容度
Peak温度 230℃
有铅 (63SnPb)
25%
10%
15%
印刷机
钢网
锡膏
10%
贴片机
5%
电子零件
30% 焊点形成
回流
贴装精度极高 贴压微调整
理想的温度 曲线设定能力 温度偏差极小
高精度尺寸 贴装稳定性 零件耐温性 氧化
smt的两种生产工艺

smt的两种生产工艺
SMT(Surface Mount Technology)是现代电子产品制造中普
遍采用的一种电路组装技术。
它将电子元件直接粘贴到印刷电路板(PCB)上,而不是像传统的TH(Through-Hole)技术
那样通过插入孔进行连接。
以下是SMT的两种常见的生产工艺。
1. 贴片工艺
贴片工艺是SMT中最常用的一种工艺。
在贴片工艺中,电子
元件(如电阻、电容、二极管、集成电路等)通过粘贴或焊接方式固定在PCB上。
贴片电子元件通过自动化设备,如贴片机,根据PCB上的元件位置标记进行准确定位和精确贴装。
贴片工艺的优势在于其快速、高效、自动化的特点,可以大大提高生产效率和质量。
2. 焊接工艺
焊接工艺是SMT中另一种重要的生产工艺。
在SMT焊接中,焊接过程分为两个步骤:回流焊和波峰焊。
回流焊是通过加热整个PCB,使焊膏熔化并形成焊点。
这个过程中需要控制温
度和时间,以确保焊点的质量。
回流焊的主要优点是可以同时焊接多个焊点,缩短生产周期。
波峰焊则是将PCB的一侧浸
入熔化的焊料波峰中,使焊料通过离子化的方法与电路板实现焊接。
波峰焊适用于较大的电路板或需要更强的焊接强度的应用。
总结:这两种SMT生产工艺在电子产品制造中起到了至关重
要的作用。
贴片工艺使得电子元件的贴装速度更快、更准确,
提高了生产效率。
而焊接工艺则确保电子元件与PCB的可靠焊接,保证产品的质量和性能。
在实际制造中,通常会根据产品的需求和工艺要求来选择合适的工艺,以达到最佳的生产效果。
SMT工艺基础培训

SMT工艺基础培训1. 简介表面贴装技术(Surface Mount Technology,简称SMT)是一种常用于电子设备制造的工艺。
相较于传统的插针式组装技术,SMT工艺具有高效、高质量和成本较低的优势。
本文将介绍SMT工艺的基础知识和流程。
2. SMT工艺的基本原理SMT工艺的基本原理是将电子元器件直接焊接到印刷电路板(Printed Circuit Board,PCB)的表面上,通过高温熔化焊接剂,将元器件牢固地固定在PCB上。
SMT工艺主要由以下几个部分组成:贴装设备、焊接剂、PCB和元器件。
2.1 贴装设备SMT贴装设备主要包括贴片机、回流焊炉和波峰焊机。
贴片机用于自动将元器件精确地放置在PCB上,回流焊炉用于加热焊接剂使其熔化并与PCB和元器件形成可靠的焊点,波峰焊机则用于焊接插针式元器件。
2.2 焊接剂焊接剂是将元器件和PCB连接在一起的关键材料。
常用的焊接剂有无铅焊膏、铅锡焊膏和银浆焊膏。
焊接剂的选择应根据元器件和PCB 的要求来确定。
2.3 PCBPCB是SMT工艺的载体,通过电路设计将元器件连接在一起。
PCB 通常由铜箔、绝缘材料和防护层组成。
PCB的质量和设计对SMT工艺的成功与否至关重要。
2.4 元器件元器件是SMT工艺中的核心部件,包括电阻、电容、集成电路等。
元器件的选择应根据电路设计的要求来确定,同时需要考虑元器件的尺寸和焊接特性。
3. SMT工艺流程SMT工艺流程包括PCB板贴装、焊接和检测三个主要步骤。
3.1 PCB板贴装PCB板贴装是SMT工艺的第一步,主要包括元器件排列、元器件粘贴和元器件定位三个阶段。
在元器件排列阶段,根据电路设计,在PCB上规划元器件的位置。
在元器件粘贴阶段,使用贴片机将元器件精确地放置在PCB上。
在元器件定位阶段,通过视觉系统或传感器来检测并调整元器件的位置,保证其精确度。
3.2 焊接焊接是SMT工艺中的关键步骤,主要包括回流焊接和波峰焊接两种方法。
SMT工艺流程及各流程分析介绍
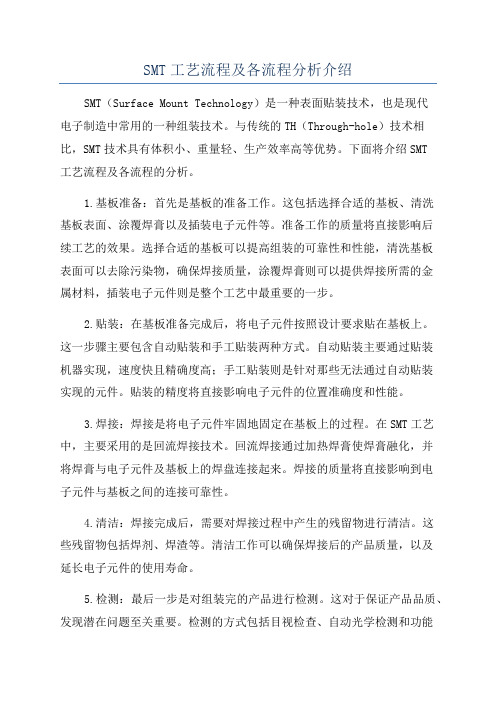
SMT工艺流程及各流程分析介绍SMT(Surface Mount Technology)是一种表面贴装技术,也是现代电子制造中常用的一种组装技术。
与传统的TH(Through-hole)技术相比,SMT技术具有体积小、重量轻、生产效率高等优势。
下面将介绍SMT工艺流程及各流程的分析。
1.基板准备:首先是基板的准备工作。
这包括选择合适的基板、清洗基板表面、涂覆焊膏以及插装电子元件等。
准备工作的质量将直接影响后续工艺的效果。
选择合适的基板可以提高组装的可靠性和性能,清洗基板表面可以去除污染物,确保焊接质量,涂覆焊膏则可以提供焊接所需的金属材料,插装电子元件则是整个工艺中最重要的一步。
2.贴装:在基板准备完成后,将电子元件按照设计要求贴在基板上。
这一步骤主要包含自动贴装和手工贴装两种方式。
自动贴装主要通过贴装机器实现,速度快且精确度高;手工贴装则是针对那些无法通过自动贴装实现的元件。
贴装的精度将直接影响电子元件的位置准确度和性能。
3.焊接:焊接是将电子元件牢固地固定在基板上的过程。
在SMT工艺中,主要采用的是回流焊接技术。
回流焊接通过加热焊膏使焊膏融化,并将焊膏与电子元件及基板上的焊盘连接起来。
焊接的质量将直接影响到电子元件与基板之间的连接可靠性。
4.清洁:焊接完成后,需要对焊接过程中产生的残留物进行清洁。
这些残留物包括焊剂、焊渣等。
清洁工作可以确保焊接后的产品质量,以及延长电子元件的使用寿命。
5.检测:最后一步是对组装完的产品进行检测。
这对于保证产品品质、发现潜在问题至关重要。
检测的方式包括目视检查、自动光学检测和功能性测试等。
通过检测可以及时发现问题并进行修复,避免对整个批量产品造成影响。
综上所述,SMT工艺流程包括基板准备、贴装、焊接、清洁和检测。
每个步骤都十分重要,对整个工艺流程的质量与效果有着直接影响。
合理的工艺流程可以提高生产效率、减少成本、提高产品质量,因此,企业在实施SMT工艺时应注重每个步骤的细节,确保每个环节的顺利进行。
电子产品焊接工艺

电子产品焊接工艺介绍电子产品焊接工艺是制造电子产品的关键环节之一。
焊接工艺的质量直接影响产品的可靠性和性能稳定性。
本文将介绍电子产品焊接工艺的基本概念和常见技术。
焊接方法表面贴装技术(SMT)表面贴装技术(Surface Mount Technology,简称SMT)是一种通过将电子元件直接粘贴或焊接到印刷电路板(PCB)表面上来实现电子组装的方法。
SMT在电子产品制造中广泛应用,因其具有高密度、小尺寸和高性能的优点而备受青睐。
SMT焊接的主要步骤包括:1.元件贴装:将元件按照设计要求粘贴或放置在PCB表面上。
2.固定:使用热熔胶或粘合剂固定元件,以防止元件在运输和使用过程中脱落。
3.焊接:通过热风炉或回流焊炉将元件和PCB表面焊接在一起。
4.检查:对焊接的元件进行目视检查或使用自动化检测设备进行检查,以确保焊接质量和正确性。
焊接贴装技术(THT)焊接贴装技术(Through-hole Technology,简称THT)是一种将元件插入PCB孔洞中,并通过焊接来固定元件的技术。
THT技术仍然在某些要求高可靠性的应用中使用,尤其是在大功率电子产品中。
THT焊接的主要步骤包括:1.元件插入:将元件通过孔洞插入PCB上。
2.电焊:使用焊锡丝和焊锡炉或手持焊接铁将元件与PCB焊接在一起。
3.修整:修整焊接的引脚,使之平整和均匀,以提高连接质量。
4.检查:对焊接的元件进行目视检查或使用自动化检测设备进行检查,以确保焊接质量和正确性。
焊接材料焊锡焊锡是一种常用的焊接材料,它通常是铅-锡合金。
焊锡的合金成分根据应用需求而不同,典型的焊锡合金包括63%锡和37%铅(Sn63Pb37)和无铅焊锡合金,如99.3%锡和0.7%铜(Sn99.3Cu0.7)。
焊剂焊剂是焊接过程中常用的辅助材料,它有助于焊接表面的清洁和氧化物的去除,提高焊接质量。
常见的焊剂类型包括酒精型焊剂和无铅焊剂。
焊接工艺控制为了确保焊接质量和一致性,焊接工艺需要严格控制。
SMT工艺流程及各工位操作规范

SMT工艺流程及各工位操作规范一、前言SMT(Surface Mount Technology)是一种基于表面贴装技术的电子元件贴装工艺。
本文将介绍SMT工艺的整体流程以及各工位操作的规范。
二、SMT工艺流程概述SMT工艺流程包括PCB板表面处理、贴片、回流焊等多个环节。
下面将详细介绍各个流程的操作规范。
1. PCB板表面处理在SMT工艺中,PCB板表面处理是非常重要的一环。
正确的表面处理可以确保元件的粘贴牢固,焊接质量良好。
•清洗:在表面处理之前,一定要对PCB板进行清洗,去除表面的污垢和氧化层。
•化学处理:可以通过化学方法对PCB板进行表面处理,增加元件与PCB板之间的黏附力。
2. 贴片在SMT工艺中,贴片是将各种电子元件粘贴到PCB板上的过程。
•手动贴片:对于一些小批量生产,可以采用手动贴片的方式,但需要保证操作人员的技术熟练度。
•自动贴片:对于大批量生产,通常会采用自动贴片机进行操作,提高生产效率。
3. 回流焊回流焊是SMT工艺中的最后一道工序,通过高温将电子元件焊接到PCB板上。
•控温控时间:在回流焊过程中,要严格控制温度和时间,确保焊接的质量。
三、各工位操作规范1. 贴片操作规范•在进行贴片操作时,要保证工作环境的清洁,避免灰尘和杂物影响粘贴效果。
•操作人员应熟练掌握贴片机的操作技巧,保证元件的精准贴合。
•贴片机的清洁和维护也是非常重要的,定期清洁贴片机,保持其良好运行状态。
2. 回流焊操作规范•操作人员要保证在回流焊过程中的安全,避免高温烫伤等意外发生。
•严格遵守回流焊的温度和时间要求,确保焊接的质量。
•在回流焊过程中,要及时检查焊接部位是否均匀,确保焊点完全熔合。
四、结论SMT工艺在电子生产制造中扮演着重要的角色,正确的操作规范可以提高生产效率,确保产品质量。
制定良好的工艺流程和操作规范对于SMT工艺的成功应用至关重要。
SMT整个工艺流程详细讲解
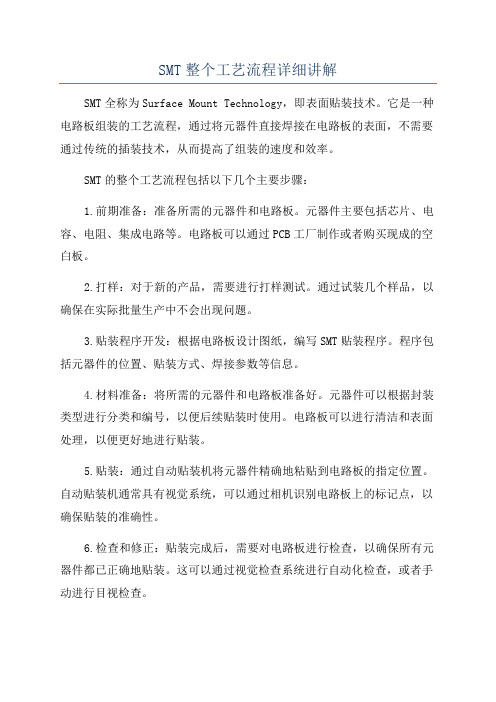
SMT整个工艺流程详细讲解SMT全称为Surface Mount Technology,即表面贴装技术。
它是一种电路板组装的工艺流程,通过将元器件直接焊接在电路板的表面,不需要通过传统的插装技术,从而提高了组装的速度和效率。
SMT的整个工艺流程包括以下几个主要步骤:1.前期准备:准备所需的元器件和电路板。
元器件主要包括芯片、电容、电阻、集成电路等。
电路板可以通过PCB工厂制作或者购买现成的空白板。
2.打样:对于新的产品,需要进行打样测试。
通过试装几个样品,以确保在实际批量生产中不会出现问题。
3.贴装程序开发:根据电路板设计图纸,编写SMT贴装程序。
程序包括元器件的位置、贴装方式、焊接参数等信息。
4.材料准备:将所需的元器件和电路板准备好。
元器件可以根据封装类型进行分类和编号,以便后续贴装时使用。
电路板可以进行清洁和表面处理,以便更好地进行贴装。
5.贴装:通过自动贴装机将元器件精确地粘贴到电路板的指定位置。
自动贴装机通常具有视觉系统,可以通过相机识别电路板上的标记点,以确保贴装的准确性。
6.检查和修正:贴装完成后,需要对电路板进行检查,以确保所有元器件都已正确地贴装。
这可以通过视觉检查系统进行自动化检查,或者手动进行目视检查。
7.固化焊接:将贴装后的电路板送入回流炉或波峰焊机进行焊接固化。
回流炉使用热风对整个电路板进行加热,使焊膏熔化并粘合元器件。
波峰焊机使用熔融的焊料波浪对电路板进行焊接。
8.清洗:焊接完成后,电路板需要进行清洗,以去除焊接过程中可能残留的焊膏或其他污染物。
清洗通常使用专门的清洗剂和设备。
9.测试:进行组装好的电路板的功能测试,确保其按照设计要求工作。
10.包装和出货:完成测试后,将电路板进行包装,并准备发货给客户。
在整个SMT工艺流程中,贴装是核心步骤。
贴装的准确性和质量直接影响到整个产品的性能和可靠性。
因此,SMT工艺流程中的其他步骤,如程序开发、材料准备、检查修正、焊接固化以及测试等,都需要高度的精确性和严谨性,以确保产品的质量和稳定性。
50条SMT工艺技术
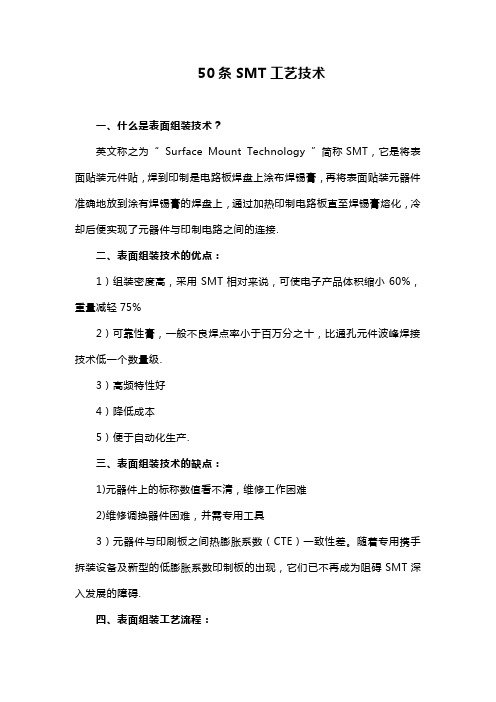
50条SMT工艺技术一、什么是表面组装技术?英文称之为“Surface Mount Technology ”简称SMT,它是将表面贴装元件贴,焊到印制是电路板焊盘上涂布焊锡膏,再将表面贴装元器件准确地放到涂有焊锡膏的焊盘上,通过加热印制电路板直至焊锡膏熔化,冷却后便实现了元器件与印制电路之间的连接.二、表面组装技术的优点:1)组装密度高,采用SMT相对来说,可使电子产品体积缩小60%,重量减轻75%2)可靠性膏,一般不良焊点率小于百万分之十,比通孔元件波峰焊接技术低一个数量级.3)高频特性好4)降低成本5)便于自动化生产.三、表面组装技术的缺点:1)元器件上的标称数值看不清,维修工作困难2)维修调换器件困难,并需专用工具3)元器件与印刷板之间热膨胀系数(CTE)一致性差。
随着专用携手拆装设备及新型的低膨胀系数印制板的出现,它们已不再成为阻碍SMT深入发展的障碍.四、表面组装工艺流程:SMT工艺有两类最基本的工艺流程,一类为锡膏回流焊工艺,另一类是贴片—波峰焊工艺.在实际生产中,应根据所用元器件和生产装备的类型以及产品的需求选择不同的工艺流程,现将基本的工艺流程图示如下:1)锡膏—回流焊工艺,该工艺流程的特点是简单,快捷,有利于产品体积的减小.2)贴片-波峰焊工艺,该工艺流程的特点是利用双面板空间,电子产品的体积可以进一步减小,且仍使用通孔元件,价格低廉,但设备要求增多,波峰焊过程中缺陷较多,难以实现高密度组装。
3)混合安装,该工艺流程特点是充分利用PCB板双面空间,是实现安装面积最小化的方法之一,并仍保留通孔元件价低的特点.4)双面均采用锡膏—回流焊工艺,该工艺流程的特点能充分利用PCB 空间,并实现安装面积最小化,工艺控制复杂,要求严格,常用于密集型或超小型电产品,移动电话是典型产品之一。
我们知道,在新型材料方面,焊膏和胶水都是触变性质流体,它们引起的缺陷占SMT总缺陷的60%,训练掌握这些材料知识才能保证SMT质量.SMT还涉及多种装联工艺,如印刷工艺,点胶工艺,贴放工艺,固化工艺,只要其中任一环节工艺参数漂移,就会导致不良品产生,SMT工艺人员必须具有丰富的工艺知识,随时监视工艺状况,预测发展动向。
- 1、下载文档前请自行甄别文档内容的完整性,平台不提供额外的编辑、内容补充、找答案等附加服务。
- 2、"仅部分预览"的文档,不可在线预览部分如存在完整性等问题,可反馈申请退款(可完整预览的文档不适用该条件!)。
- 3、如文档侵犯您的权益,请联系客服反馈,我们会尽快为您处理(人工客服工作时间:9:00-18:30)。
再做B面 点贴片胶 贴装元件 回流焊 翻转
插通孔元件后再过波峰焊 插通孔元件 波峰焊 清洗
双面混合安装工艺
多用于消费类电子三、焊锡膏与印刷技术介绍
3.1、锡膏 3.1.1、特性 a、锡膏:焊料粉末+糊状助焊剂,焊料粉末占90%左右,其余是化学 成分。
b、黏度:流体之间因流动或相对运动所产生的内摩擦阻力称为流体 的黏度。 c、锡膏的流变学行为:锡膏中混有一定量的触变剂,具有假塑性流 体性质,随着所受外力的增加,锡膏的黏度迅速下降,但下降到一 定程度后又开始稳定下来。这种性质在印刷锡膏时是非常有用。即 锡膏在印刷时,受到刮刀的推力作用,其黏度下降,当到达模板窗 口时,黏度达到最低,顺利通过窗口沉降到PCB焊盘上,随着外力的 停止,锡膏黏度又迅速回升,这们就不会出现印刷图形的塌落和漫 流,得到良好的印刷效果。
Page 7 of 24
三、焊锡膏与印刷技术介绍(附)
3.1、锡膏 3.1.1、特性 d、焊料粉末含量对黏度的影响:焊料粉末的增加可以有效地防止 印刷后及预热阶段的塌落,焊接后焊点饱满,有助于焊接质量的提 高。
黏度
粉含量%
Page 8 of 24
三、焊锡膏与印刷技术介绍(附)
3.1、锡膏 3.1.1、特性 e、焊料粉末粒度对黏度的影响(25-45um) f、温度对锡膏黏度的影响(20-26度)
g、转速对锡膏黏度的影响
黏度 粒度 T(度) 转速
Page 9 of 24
三、焊锡膏与印刷技术介绍(附)
3.2、锡膏的印刷技术 3.1.1、印刷模板 a、材料:铝合金+不锈钢; b、结构:刚-柔-刚 通常钢板上的图形离钢板的外边约50mm, 以供印刷机刮刀运行需要,丝网的宽度约30-40mm,以保证钢板在 使用中有一定的弹性;
b、安装并校正模板; c、印刷锡膏过程中应注意补充新锡膏,保持锡膏在印刷时能滚动前 进,环境质量:20-26度,无风、无尘,相对湿度<70%; d、完工/清洗模板:未用完的锡膏单独存放,用清洗剂和擦洗纸及 时清洗模板,不得使用坚硬的东西,防止模板变形。
Page 11 of 24
四、回流工艺温度曲线的建立与使用测温仪的注意事项 4..1 回流工艺温度曲线的建立 温度曲线是指SMA通过回流炉时,SMA上某一点的温度随时间变化的曲 线。温度曲线提供了一种直观的方法,来分析某个元件在整个回流焊 过程中的温度变化情况。这对于获得最佳的可焊性,避免由于超温而 对元件造成损坏,以及保证焊接质量都非常有用。以下从预热段开始 进行简要分析: 预热段: 该区域的目的是把室温的PCB尽快加热,以达到第二个特定目标,但 升温速率要控制在适当范围以内,如果过快,会产生热冲击,电路 板和元件都可能受损,过慢,则溶剂挥发不充分,影响焊接质量。 由于加热速度较快,在温区的后段SMA内的温差较大。为防止热冲击 对元件的损伤。一般规定最大速度为4℃/S。然而,通常上升速率设 定为1~3℃/S。典型的升温度速率为2℃/S。
目 录
一、回流技术产生背景与回流焊的发展阶段 二、回流焊工艺流程介绍 三、焊锡膏与印刷技术介绍 四、回流工艺温度曲线的建立与使用测温仪的注意事项 五、影响回流工艺主要原因的分析 六、回流工艺的发展趋势
Page 1 of 24
一、回流技术产生背景与回流焊的发展阶段 1.1 回流技术产生背景 由于电子产品PCB不断小型化的需要,出现了片状元件,传统的焊接方 法已不能适应需要。起先,只在混合集成电路板组装中采用了回流焊工 艺,组装焊接的元件多数为片状电容、片状电感,贴装型晶体管及二极 管等。随着SMT整个技术发展日趋完善,多种贴片元件(SMC)和贴装 器件(SMD)的出现,作为贴装技术一部分的回流焊工艺技术及设备也 得到相应的发展,其应用日趋广泛,几乎在所有电子产品领域都已得到 应用。
Page 2 of 24
一、回流技术产生背景与回流焊的发展阶段(附) 1.2 回流焊的发展阶段 根据产品的热传递效率和焊接的可靠性的不断提升,回流焊大致可分为 五个发展阶段:热板传导回流焊设备、红外热辐射回流焊设备、热风回 流焊设备、气相回流焊接系统、真空蒸汽冷凝焊接(真空汽相焊)系统。 a、热板传导回流焊设备:热传递效率最慢,5-30 W/m2K(不同材质的 加热效率不一样),有阴影效应。 b、红外热辐射回流焊设备:热传递效率慢,5-30W/m2K(不同材质的红 外辐射效率不一样),有阴影效应,元器件的颜色对吸热量有大的影响。 c、热风回流焊设备:热传递效率比较高,10-50 W/m2K,无阴影效应, 颜色对吸热量没有影响。 d、气相回流焊接系统:热传递效率高,200-300 W/m2K,无阴影效应, 焊接过程需要上下运动,冷却效果差。 e、真空蒸汽冷凝焊接(真空汽相焊)系统:密闭空间的无空洞焊接, 热传递效率最高,300 W-500W/m2K。焊接过程保持静止无震动。冷却效 果优秀,颜色对吸热量没有影响。
Page 3 of 24
二、回流焊工艺流程介绍
印刷锡膏
贴装元件
回流焊
单面回流焊工艺
简单,快捷
清洗
印刷锡膏
贴装元件
回流焊 翻转 插通孔元件
清洗 波峰焊
单面混装焊接工艺
价格低廉,但要求设备多,难以实现高密度组装
Page 4 of 24
二、回流焊工艺流程介绍(附)
通常先作B面 印刷锡膏 贴装元件 回流焊 翻转 再作A面
印刷锡膏
贴装元件
回流焊
翻转
双面回流焊工艺
清洗
A面布有IC、BGA等大型器件 B面以片式元件为主 充分利用 PCB空间,实现安装面积最小化,工艺控制复杂,要求严格 常用于密集型或超小型电子产品,如手机、手提电脑,上网卡等
Page 5 of 24
二、回流焊工艺流程介绍(附)
先做A面 印刷锡膏 贴装元件 回流焊 翻转
c、特性:坚固耐用,寿命长; d、规格:0.08、0.1、0.12、0.15、0.18、0.2mm等。
Page 10 of 24
三、焊锡膏与印刷技术介绍(附)
3.2、锡膏的印刷技术 3.2.2、锡膏印刷过程 a、回温、搅拌,从冰箱中取出,恢复到室温(约4H)后再打开,手 动或搅拌机自动搅拌3-4分钟;