镀锌常见质量问题及其解决方法
镀锌产品质量缺陷和判级标准全面解析

锌起伏
缺陷特征:在镀锌钢带表面呈现无规律波浪凸 起。(如下图) 产生原因:
1)锌液温度低于规定温度。 2)锌液中含铝量高,使锌层局部超厚。 3)气刀角度偏高。 4)气刀压力偏低,速度缓慢。
夹杂
缺陷特征:夹杂有明显的点状、块状、长条状或柳叶 状。(如下图)点状、小黑条状夹杂易与氧化铁皮细 孔、脏物压入混淆。 产生原因:
残留有氧化物; 3、退火炉内保护气体氧含量或露点偏高,导致钢
带还原不充分; 4、机组速度过快,退火不完全,钢带入锌锅温度
较低。
锌花不均
缺陷特征:肉眼观察带钢表面锌花局部出现大小不等(如下 图)。
产生原因: 1、原料上下板面或局部粗糙度不均匀; 2、脱脂不良,钢带清洁度差; 3、镀锌时上下板面冷却速度不同、气刀刀唇到带钢上下板面 的距离不一致、上下板面气刀的风速和风量不同等都会造成 上下板面锌花大小不均; 4、板面覆盖氧化铁皮沿带钢成规律型波动、带钢划伤或炉辊 结瘤等,这些缺陷会增加锌花的结晶点,使镀层表面锌花较 小且不均匀; 5、当气刀与带钢不平行,出现夹角时,易产生带钢横断面上 的锌花不均匀;当沉没辊、稳定辊出现轴振动或带钢存在浪 形时,较易出现该问题;另外连续退火炉采用区温控制时, 或辐射管使用不对称时,带钢的温度易产生波动,会产生带 钢低温区锌花小、高温区锌花大的现象; 6、带钢入锌锅温度、锌液温度、镀后冷却温度的影响。
1)气刀的缝隙发生了局部堵塞。 2)气刀局部缺口或损坏。 3)板形不好。
气刀刮伤
缺陷特征:钢带上的锌层被气刀嘴刮伤,在板面上 留下沿轧制线方向的痕迹或沟痕,连续或断续,刮 痕条数、轻重程度不等,轻者形成印痕,重者形成 沟痕,露出钢板基体,锌层破坏。 产生原因:
1)钢带规格薄,板形不好。 2)钢带张力小,运行时出现摆动。 3)钢带距离喷嘴太近。 4)稳定辊未起稳定作用。
锌酸盐镀锌工艺的故障原因与处理方法
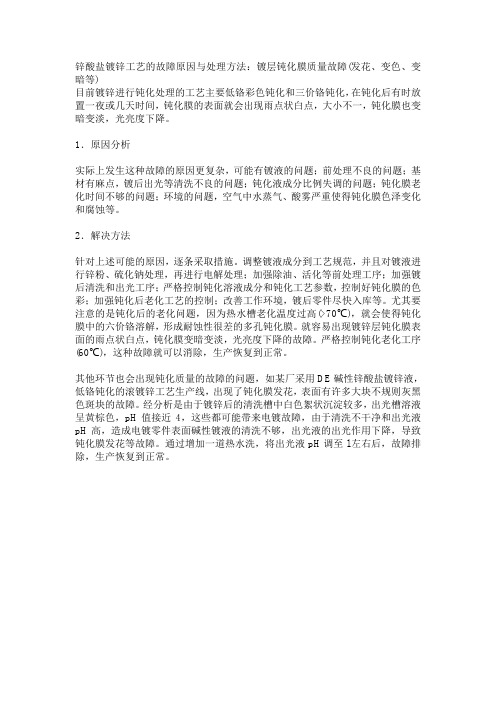
锌酸盐镀锌工艺的故障原因与处理方法:镀层钝化膜质量故障(发花、变色、变暗等)目前镀锌进行钝化处理的工艺主要低铬彩色钝化和三价铬钝化,在钝化后有时放置一夜或几天时间,钝化膜的表面就会出现雨点状白点,大小不一,钝化膜也变暗变淡,光亮度下降。
1.原因分析实际上发生这种故障的原因更复杂,可能有镀液的问题;前处理不良的问题;基材有麻点,镀后出光等清洗不良的问题;钝化液成分比例失调的问题;钝化膜老化时间不够的问题;环境的问题,空气中水蒸气、酸雾严重使得钝化膜色泽变化和腐蚀等。
2.解决方法针对上述可能的原因,逐条采取措施。
调整镀液成分到工艺规范,并且对镀液进行锌粉、硫化钠处理,再进行电解处理;加强除油、活化等前处理工序;加强镀后清洗和出光工序;严格控制钝化溶液成分和钝化工艺参数,控制好钝化膜的色彩;加强钝化后老化工艺的控制;改善工作环境,镀后零件尽快入库等。
尤其要注意的是钝化后的老化问题,因为热水槽老化温度过高(>70℃),就会使得钝化膜中的六价铬溶解,形成耐蚀性很差的多孔钝化膜。
就容易出现镀锌层钝化膜表面的雨点状白点,钝化膜变暗变淡,光亮度下降的故障。
严格控制钝化老化工序(60℃),这种故障就可以消除,生产恢复到正常。
其他环节也会出现钝化质量的故障的问题,如某厂采用DE碱性锌酸盐镀锌液,低铬钝化的滚镀锌工艺生产线,出现了钝化膜发花,表面有许多大块不规则灰黑色斑块的故障。
经分析是由于镀锌后的清洗槽中白色絮状沉淀较多,出光槽溶液呈黄棕色,pH值接近4,这些都可能带来电镀故障,由于清洗不干净和出光液pH高,造成电镀零件表面碱性镀液的清洗不够,出光液的出光作用下降,导致钝化膜发花等故障。
通过增加一道热水洗,将出光液pH调至l左右后,故障排除,生产恢复到正常。
常见13种氯化钾镀锌故障处理分析告诉你标准答案

A'常见13 种氯化钾镀锌故障分析告诉你答案本篇汇总了氯化钾镀锌的常见故障,包括镀层不光亮、发雾、结合力差、烧焦、黑色条纹、厚度不均、脆性、沉积速度慢、分散能力差、镀液浑浊等。
介绍了这些疵病的产生原因及其处理方法。
提出了应加强工艺管理、认真做好镀液维护、定期进行净化等措施,以期避免或减少故障发生。
氯化钾镀锌是由最早的无氰氯化铵镀液发展而来的一种无铵弱酸性光亮镀锌工艺。
其优点是:(1) 镀液导电性好,槽压低,节省电能;(2) 镀层结晶细致、光亮、平整;(3) 电流效率高,沉积速度快;(4) 镀液分散能力好;(5) 适用于铸件直接电镀;(6) 废水处理简便,解决了环境污染的问题。
因此,氯化钾镀锌在工业上得到了广泛应用。
但是,在日常生产中难免会发生质量故障,主要原因在于镀液维护不力,组分失调或受到有害杂质干扰,以及工件前处理不良。
本篇拟就氯化钾镀锌中常见故障的产生原因及其处理方法进行汇总和介绍。
各种常见故障的产生原因及其处理方法1. 镀层不光亮产生原因:(1) 镀液浓度过低(即氯化锌、氯化钾和硼酸的含量均低);(2) 光亮剂不足;(3) pH 过高;(4) 镀液温度过高;(5) 阴极电流密度小;(6) 金属铁杂质多;(7) 有机杂质多。
处理方法:(1) 通过分析,补加氯化锌、氯化钾和硼酸至工艺规范;(2) 适当添加光亮剂;(3) 用稀盐酸溶液调节pH 至工艺规范;(4) 降低镀液温度至工艺规范;(5) 适当提高阴极电流密度;(6) 加入0.5 ~ 2 mL/L的双氧水(w = 30%),充分搅拌后,用w = 5% 的氢氧化钠调节pH 至 6.2,沉淀、过滤后可除去氢氧化铁;(7) 在镀液温度为45 °C 时加入 1 ~ 3 g/L 活性炭,搅拌约30 min 后过滤;或采用高锰酸钾法处理, 即先用稀盐酸调低pH 至3 ~ 4, 然后在搅拌的情况下将溶有0.5 ~ 1 g/L 高锰酸钾的热水均匀加入镀液中,再继续搅拌30 min ,然后静置过滤,可除去有机物。
电镀常见的问题及解决方案

电镀常见的问题及解决方案
电镀过程中可能出现的问题及其解决方案如下:
1.针孔或麻点:这是由于前处理不良、有金属杂质、硼酸含量太少、镀液温度太低等原因造成的。
可以使用润湿剂来减小影响,并严格控制镀液维护及流程。
2.结合力低:如果铜镀层未经活化去氧化层,铜和镍之间的附着力就差,会产生镀层剥落现象。
因此,在电镀前应对基材进行适当的预处理,如酸洗、活化等。
3.镀层脆、可焊性差:这通常是由于有机物或重金属物质污染造成的。
添加剂过多会使镀层中夹带的有机物和分解产物增多,此时可以用活性炭处理或电解等方法除去重金属杂质。
4.镀层发暗和色泽不均匀:有金属污染可能是造成这一问题的原因。
应尽量减少挂具所沾的铜溶液,并在发现污染时立即处理。
5.镀层烧伤:这可能是由于硼酸不足、金属盐的浓度低、工作温度太低、电流密度太高、PH值太高或搅拌不充分等原因造成的。
需要检查并调整相关工艺参数,确保其处于合适的范围。
6.沉积速率低:PH值低或电流密度低都可能导致沉积速率低。
应检查并调整镀液的PH值和电流密度,以优化沉积速率。
7.其他问题:如辅助阳极的铜条未与生产板长度一致或已发粗,不允许再使用。
全板及图形镀后板需在24小时内制作下工序。
图形镀上板戴细纱手套,下板戴棕胶手套,全板上板戴橡胶手套,下板戴干燥的粗纱手套。
在处理电镀问题时,需要综合考虑多个因素,包括镀液成分、设备状况、操作条件等。
如遇到难以解决的问题,建议寻求专业人士的帮助。
镀锌线常见缺陷原因及对策
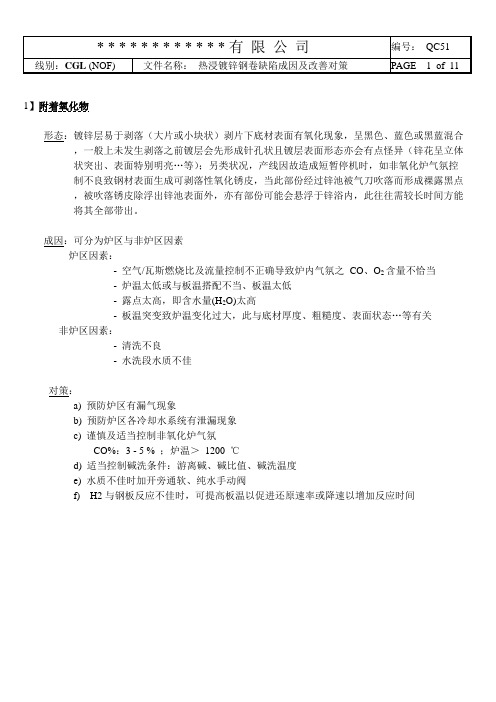
1】附着氧化物形态:镀锌层易于剥落(大片或小块状)剥片下底材表面有氧化现象,呈黑色、蓝色或黑蓝混合,一般上未发生剥落之前镀层会先形成针孔状且镀层表面形态亦会有点怪异(锌花呈立体状突出、表面特别明亮…等);另类状况,产线因故造成短暂停机时,如非氧化炉气氛控制不良致钢材表面生成可剥落性氧化锈皮,当此部份经过锌池被气刀吹落而形成裸露黑点,被吹落锈皮除浮出锌池表面外,亦有部份可能会悬浮于锌浴内,此往往需较长时间方能将其全部带出。
成因:可分为炉区与非炉区因素炉区因素:- 空气/瓦斯燃烧比及流量控制不正确导致炉内气氛之CO、O2含量不恰当- 炉温太低或与板温搭配不当、板温太低- 露点太高,即含水量(H2O)太高- 板温突变致炉温变化过大,此与底材厚度、粗糙度、表面状态…等有关非炉区因素:- 清洗不良- 水洗段水质不佳对策:a) 预防炉区有漏气现象b) 预防炉区各冷却水系统有泄漏现象c) 谨慎及适当控制非氧化炉气氛CO%:3 - 5 % ;炉温>1200 ℃d) 适当控制碱洗条件:游离碱、碱比值、碱洗温度e) 水质不佳时加开旁通软、纯水手动阀f) H2与钢板反应不佳时,可提高板温以促进还原速率或降速以增加反应时间2】表面积碳形态:镀层易于剥落,表面附有黑色粉状,底材有时也会有蓝化现象,黑色粉物有可能为氧化物,亦有可能为炭(C)粉,所以需先做实验或以经验来观察判断(多数出现于头尾端处)。
成因:- 炉区气氛控制不当(CO %太高)对策:a) 适当控制炉区气氛:CO % : 2 – 3 %3】锌渣过多形态:一种为块状(氧化剥落片之渣);另一种为颗粒状(金属间化合物)其可分为两种-顶浮渣及底渣。
这些渣物会造成钢板表面粗糙(分布于钢板全面或两侧边缘),严重的话收卷后易形成翘边。
成因:- 锌池温度变化过大,尤其是在沉放大锌锭时浸入过快易造成其周围温度变化- AL含量过高,若Al含量过低易生成底渣,故Al含量应控制于0.18 – 0.22 %为佳- 停机缺陷或其它因素造成的氧化物剥片- 底材表面缺陷易造成锌渣附着对策:a) 尽量维持锌池温度稳定。
镀锌件常见问题和解决方法
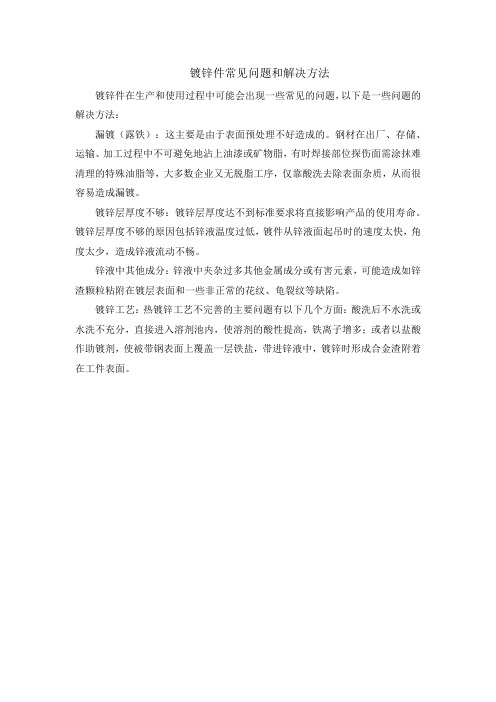
镀锌件常见问题和解决方法
镀锌件在生产和使用过程中可能会出现一些常见的问题,以下是一些问题的解决方法:
漏镀(露铁):这主要是由于表面预处理不好造成的。
钢材在出厂、存储、运输、加工过程中不可避免地沾上油漆或矿物脂,有时焊接部位探伤面需涂抹难清理的特殊油脂等,大多数企业又无脱脂工序,仅靠酸洗去除表面杂质,从而很容易造成漏镀。
镀锌层厚度不够:镀锌层厚度达不到标准要求将直接影响产品的使用寿命。
镀锌层厚度不够的原因包括锌液温度过低,镀件从锌液面起吊时的速度太快,角度太少,造成锌液流动不畅。
锌液中其他成分:锌液中夹杂过多其他金属成分或有害元素,可能造成如锌渣颗粒粘附在镀层表面和一些非正常的花纹、龟裂纹等缺陷。
镀锌工艺:热镀锌工艺不完善的主要问题有以下几个方面:酸洗后不水洗或水洗不充分,直接进入溶剂池内,使溶剂的酸性提高,铁离子增多;或者以盐酸作助镀剂,使被带钢表面上覆盖一层铁盐,带进锌液中,镀锌时形成合金渣附着在工件表面。
常见13种氯化钾镀锌 故障分析告诉你答案

常见13种氯化钾镀锌故障分析告诉你答案本篇汇总了氯化钾镀锌的常见故障,包括镀层不光亮、发雾、结合力差、烧焦、黑色条纹、厚度不均、脆性、沉积速度慢、分散能力差、镀液浑浊等。
介绍了这些疵病的产生原因及其处理方法。
提出了应加强工艺管理、认真做好镀液维护、定期进行净化等措施,以期避免或减少故障发生。
氯化钾镀锌是由最早的无氰氯化铵镀液发展而来的一种无铵弱酸性光亮镀锌工艺。
其优点是:(1)镀液导电性好,槽压低,节省电能;(2)镀层结晶细致、光亮、平整;(3)电流效率高,沉积速度快;(4)镀液分散能力好;(5)适用于铸件直接电镀;(6)废水处理简便,解决了环境污染的问题。
因此,氯化钾镀锌在工业上得到了广泛应用。
但是,在日常生产中难免会发生质量故障,主要原因在于镀液维护不力,组分失调或受到有害杂质干扰,以及工件前处理不良。
本篇拟就氯化钾镀锌中常见故障的产生原因及其处理方法进行汇总和介绍。
各种常见故障的产生原因及其处理方法1.镀层不光亮产生原因:(1) 镀液浓度过低(即氯化锌、氯化钾和硼酸的含量均低);(2) 光亮剂不足;(3) pH 过高;(4) 镀液温度过高;(5) 阴极电流密度小;(6) 金属铁杂质多;(7) 有机杂质多。
处理方法:(1) 通过分析,补加氯化锌、氯化钾和硼酸至工艺规范;(2) 适当添加光亮剂;(3) 用稀盐酸溶液调节pH 至工艺规范;(4) 降低镀液温度至工艺规范;(5) 适当提高阴极电流密度;(6) 加入~ 2 mL/L 的双氧水(w = 30%),充分搅拌后,用w = 5% 的氢氧化钠调节pH 至,沉淀、过滤后可除去氢氧化铁;(7) 在镀液温度为45 °C 时加入1 ~ 3 g/L 活性炭,搅拌约30 min 后过滤;或采用高锰酸钾法处理,即先用稀盐酸调低pH 至3 ~ 4,然后在搅拌的情况下将溶有~ 1 g/L 高锰酸钾的热水均匀加入镀液中,再继续搅拌30 min ,然后静置过滤,可除去有机物。
热镀锌缺陷及事故处理
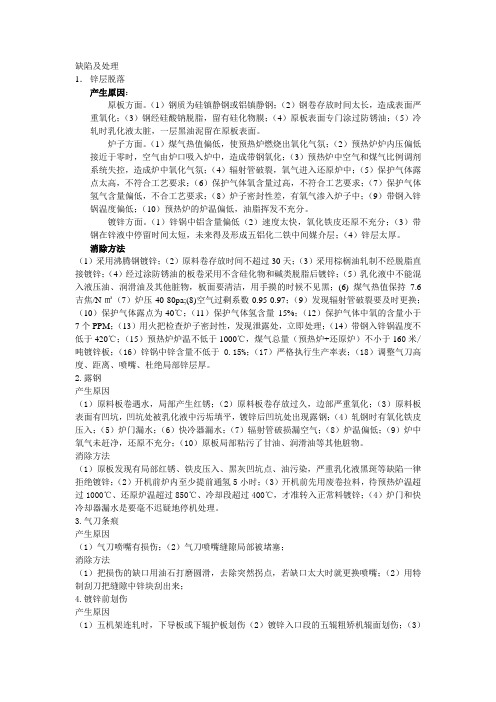
缺陷及处理1.锌层脱落产生原因:原板方面。
(1)钢质为硅镇静钢或铝镇静钢;(2)钢卷存放时间太长,造成表面严重氧化;(3)钢经硅酸钠脱脂,留有硅化物膜;(4)原板表面专门涂过防锈油;(5)冷轧时乳化液太脏,一层黑油泥留在原板表面。
炉子方面。
(1)煤气热值偏低,使预热炉燃烧出氧化气氛;(2)预热炉炉内压偏低接近于零时,空气由炉口吸入炉中,造成带钢氧化;(3)预热炉中空气和煤气比例调剂系统失控,造成炉中氧化气氛;(4)辐射管破裂,氧气进入还原炉中;(5)保护气体露点太高,不符合工艺要求;(6)保护气体氧含量过高,不符合工艺要求;(7)保护气体氢气含量偏低,不合工艺要求;(8)炉子密封性差,有氧气渗入炉子中;(9)带钢入锌锅温度偏低;(10)预热炉的炉温偏低,油脂挥发不充分。
镀锌方面。
(1)锌锅中铝含量偏低(2)速度太快,氧化铁皮还原不充分;(3)带钢在锌液中停留时间太短,未来得及形成五铝化二铁中间媒介层;(4)锌层太厚。
消除方法(1)采用沸腾钢镀锌;(2)原料卷存放时间不超过30天;(3)采用棕榈油轧制不经脱脂直接镀锌;(4)经过涂防锈油的板卷采用不含硅化物和碱类脱脂后镀锌;(5)乳化液中不能混入液压油、润滑油及其他脏物,板面要清洁,用手摸的时候不见黑;(6) 煤气热值保持7.6吉焦/N㎡(7)炉压40-80pa;(8)空气过剩系数0.95-0.97;(9)发现辐射管破裂要及时更换;(10)保护气体露点为-40℃;(11)保护气体氢含量15%;(12)保护气体中氧的含量小于7个PPM;(13)用火把检查炉子密封性,发现泄露处,立即处理;(14)带钢入锌锅温度不低于420℃;(15)预热炉炉温不低于1000℃,煤气总量(预热炉+还原炉)不小于160米/吨镀锌板;(16)锌锅中锌含量不低于0.15%;(17)严格执行生产率表;(18)调整气刀高度、距离、喷嘴、杜绝局部锌层厚。
2.露钢产生原因(1)原料板卷遇水,局部产生红锈;(2)原料板卷存放过久,边部严重氧化;(3)原料板表面有凹坑,凹坑处被乳化液中污垢填平,镀锌后凹坑处出现露钢;(4)轧钢时有氧化铁皮压入;(5)炉门漏水;(6)快冷器漏水;(7)辐射管破损漏空气;(8)炉温偏低;(9)炉中氧气未赶净,还原不充分;(10)原板局部粘污了甘油、润滑油等其他脏物。
- 1、下载文档前请自行甄别文档内容的完整性,平台不提供额外的编辑、内容补充、找答案等附加服务。
- 2、"仅部分预览"的文档,不可在线预览部分如存在完整性等问题,可反馈申请退款(可完整预览的文档不适用该条件!)。
- 3、如文档侵犯您的权益,请联系客服反馈,我们会尽快为您处理(人工客服工作时间:9:00-18:30)。
11
• 六、板面点块状露钢 • 常见原因:1、炉内局部气氛不合要求:炉区 常见原因: 、炉内局部气氛不合要求: 漏气、漏水或开机前吹扫不干净。 2、炉区 漏气、漏水或开机前吹扫不干净。 、 NOF段造成板面氧化。3、进炉前的板存在锈 段造成板面氧化。 、 段造成板面氧化 蚀或是板面有水、油等其它污染物。 、 蚀或是板面有水、油等其它污染物。4、若JC 快冷风机处有较多锌灰或锈皮, 快冷风机处有较多锌灰或锈皮,则启用快冷风 机后也容易露钢。 机后也容易露钢。
13
• 八、锌渣痕带露钢:带钢板面附有锌渣 锌渣痕带露钢: 条状、片状), ),其中又有针孔状露钢 (条状、片状),其中又有针孔状露钢 或块状露钢,多出现在下表面, 或块状露钢,多出现在下表面,呈不规 律的线条状居多,有时某个局部稍多, 律的线条状居多,有时某个局部稍多, 侧或D侧 目前原因尚不清楚。( 。(从 如O侧或 侧。目前原因尚不清楚。(从 侧或 沉辊划伤会造成露钢的情况看, 沉辊划伤会造成露钢的情况看,下表面 锌渣痕露钢是否为钢板在炉内造成比如热张力辊)
14
• • • • • • • • • •
锌层脱落
– 缺陷特征
由于锌层粘附性能不好,在进行机械咬合或球冲试验时, 由于锌层粘附性能不好,在进行机械咬合或球冲试验时,带钢表面 出现的严重锌层与钢基分离的现象称锌层脱落。 出现的严重锌层与钢基分离的现象称锌层脱落。在生产线上也可以直接 看到锌层局部呈块状与钢基分离、锌层掉落的现象。 看到锌层局部呈块状与钢基分离、锌层掉落的现象。 2、产生原因 、 原板存在擦、划伤、锈蚀等缺陷; 原板存在擦、划伤、锈蚀等缺陷; 轧机乳化液太脏,带钢表面残留物偏高; 轧机乳化液太脏,带钢表面残留物偏高; NOF炉温偏低,不能有效的灼烧掉带钢表面的残留物; 炉温偏低, 炉温偏低 不能有效的灼烧掉带钢表面的残留物; NOF空燃比设定不合理 或烧嘴变形), 空燃比设定不合理(或烧嘴变形),NOF呈强氧化气氛; 呈强氧化气氛; 空燃比设定不合理 或烧嘴变形), 呈强氧化气氛 H2掉或机组恢复生产时 掉或机组恢复生产时HN置换时间不够; 置换时间不够; 掉或机组恢复生产时 置换时间不够 炉压偏低,炉门吸风; 炉压偏低,炉门吸风; 炉子密封状况不好; 炉子密封状况不好;
9
• 2、原料钢卷边部较脏(有油或其它脏物),清洗不 原料钢卷边部较脏(有油或其它脏物),清洗不 原料钢卷边部较脏 ), 干净,也容易造成侧缘露钢。 干净,也容易造成侧缘露钢。 • 3、a.炉区非氧化直火燃烧段(NOF段)烧嘴变形致 炉区非氧化直火燃烧段( 、 炉区非氧化直火燃烧段 段 火焰直接烧于钢板,致带钢边部氧化。 烧嘴火焰调 火焰直接烧于钢板,致带钢边部氧化。b.烧嘴火焰调 的不好直接烧于钢板,致带钢边部氧化(空燃比不正确 的不好直接烧于钢板,致带钢边部氧化 空燃比不正确 或烧嘴变形后致LPG、AIR混合不好)。更换或维修 混合不好)。 或烧嘴变形后致 、 混合不好)。更换或维修 好变形烧嘴,调节好火焰(空燃比)即可。炉区NOF 好变形烧嘴,调节好火焰(空燃比)即可。炉区 烧嘴空燃比范围: 均可, 烧嘴空燃比范围:0.92~0.98均可,在保证质量的 ~ 均可 情况下,空燃比应尽量按偏大控制。 情况下,空燃比应尽量按偏大控制。日本内外炉推荐 空燃比为0.965。 空燃比为 。
4
• 一般以气刀为分界线,将划伤分为镀前划伤或镀后划伤。镀后划 一般以气刀为分界线,将划伤分为镀前划伤或镀后划伤。 伤会发亮。 伤会发亮。 • 划伤原因:1、线上辊轮不转或转动不同步。2、线上设备变形 划伤原因: 、线上辊轮不转或转动不同步。 、线上设备变形/ 损坏后接触带钢或带钢晃动碰触设备。3、产线掉入其它异物造 损坏后接触带钢或带钢晃动碰触设备。 、 成划伤。(如高塔水平冷却风机处塞满锌皮) 。(如高塔水平冷却风机处塞满锌皮 成划伤。(如高塔水平冷却风机处塞满锌皮) • 内部检查人员判断划伤是镀前或镀后,划伤是间断还是连续,有 内部检查人员判断划伤是镀前或镀后,划伤是间断还是连续, 利于快速查找划伤原因。 利于快速查找划伤原因。 • 生产线上容易产生划伤的地方:1、前处理辊轮及设备。2、沉 生产线上容易产生划伤的地方: 、前处理辊轮及设备。 、 没辊。 、移动风机上方小夹棍。 、高塔冷却风机( 没辊。3、移动风机上方小夹棍。4、高塔冷却风机(带钢晃动 碰触或掉满锌皮)。 )。5、淬水槽沉浸辊。 、光整机防皱辊、 碰触或掉满锌皮)。 、淬水槽沉浸辊。6、光整机防皱辊、防 撞辊、挤干辊。7、铬酸槽辊轮。8、红外炉(一般为灯管损 撞辊、挤干辊。 、铬酸槽辊轮。 、红外炉( 坏)。
7
• 沉辊刮渣原则及方法: 沉辊刮渣原则及方法: • 捞锌池面渣原则及方法: 捞锌池面渣原则及方法:
8
• 一、露钢:即漏镀缺陷,钢板表面没有镀上铝锌镀层,直接露出 露钢:即漏镀缺陷,钢板表面没有镀上铝锌镀层, 钢基。 钢基。 • 二、露钢类别(按表现形式分):侧缘露钢、板面针孔状露钢、 露钢类别(按表现形式分):侧缘露钢、板面针孔状露钢、 ):侧缘露钢 板面点块状露钢、板面条状或线状露钢、锌渣痕带露钢等。 板面点块状露钢、板面条状或线状露钢、锌渣痕带露钢等。 • 三、露钢的表现形式往往与形成露钢的原因有一定联系。处理露 露钢的表现形式往往与形成露钢的原因有一定联系。 钢的基本原则: 、根据露钢的表现形式判断露钢的原因。 、 钢的基本原则:1、根据露钢的表现形式判断露钢的原因。2、 减速、升温、改善炉内气氛(特别是在原因不确定的情况下)。 减速、升温、改善炉内气氛(特别是在原因不确定的情况下)。 3、观察退火炉口的板面有无生锈或有无污染物,以确定露钢原 、观察退火炉口的板面有无生锈或有无污染物, 因是炉前因素或炉区/锌池因素 锌池因素。 因是炉前因素或炉区 锌池因素。 • 四、侧缘露钢:带钢侧缘未镀上锌铝,露出钢基,卷取后钢卷侧 侧缘露钢:带钢侧缘未镀上锌铝,露出钢基, 面呈黑色。原因:1、钢卷放置时间长,侧缘被氧化生锈,在退 面呈黑色。原因: 、钢卷放置时间长,侧缘被氧化生锈, 火炉内还原不好导致镀不上铝锌。 火炉内还原不好导致镀不上铝锌。一般用打磨机打磨原料侧缘可 减少或消除。 减少或消除。
5
• 锌渣粘附在板面上,经光整整平后变成黑色的亮痕。 锌渣粘附在板面上,经光整整平后变成黑色的亮痕。 有圆点状的、线条状的。一般上表面较多。 有圆点状的、线条状的。一般上表面较多。 • 点状锌渣痕:沉辊粘渣、锌液中悬浮渣较多、面渣较 点状锌渣痕:沉辊粘渣、锌液中悬浮渣较多、 炉鼻处(锌液浸泡部分) 多、炉鼻处(锌液浸泡部分)粘渣等因素均可造成板 面点状锌渣痕。解决思路: 、 面点状锌渣痕。解决思路:1、掌握正确的刮渣方法 和捞面渣方法。 、定期清理底渣。 、 和捞面渣方法。2、定期清理底渣。3、清除炉鼻处粘 渣。4、有时更换沉辊即可消除点状锌渣痕,具体原 、有时更换沉辊即可消除点状锌渣痕, 因仍有待探讨。(与沉辊沟槽有何联系? 。(与沉辊沟槽有何联系 因仍有待探讨。(与沉辊沟槽有何联系?与沉辊转动 是否同步有无联系?是否锌液中悬浮渣较多?) 是否同步有无联系?是否锌液中悬浮渣较多?)
3
• 沉辊不转或转动与带钢不同步造成带钢划伤,有时划 沉辊不转或转动与带钢不同步造成带钢划伤, 伤部位会出现锌渣痕或露钢。 伤部位会出现锌渣痕或露钢。 • 应对措施:1、减速。 2、改变张力:选择合适的张 应对措施: 、减速。 、改变张力: 有时减小、有时增大),可能原因分析: ),可能原因分析 力(有时减小、有时增大),可能原因分析:张力大 时造成轴承处卡死,张力小时摩擦系数不够。 、 时造成轴承处卡死,张力小时摩擦系数不够。 3、更 换规格:比如生产 比如生产0.28mm出现划伤时,换0.33mm可 出现划伤时, 换规格 比如生产 出现划伤时 可 能会正常;生产0.43mm出现划伤时,换0.28mm可 出现划伤时, 能会正常;生产 出现划伤时 可 能会正常。 、沉辊辊面摩擦系数的改变: 能会正常。 4、沉辊辊面摩擦系数的改变:如是否有 沟槽,辊面是否结渣等。 、沉辊整修的影响( 沟槽,辊面是否结渣等。 5、沉辊整修的影响(整修 组补充): 组补充): •
1
• 跟锌浪的形成原因类似,板面呈现圆形小凹坑,直径0.3跟锌浪的形成原因类似,板面呈现圆形小凹坑,直径 1.5mm不等(附图)。 不等( 不等 附图)。 • 影响出现小凹点的因素: 影响出现小凹点的因素: • 1、锌液温度:锌液温度较高时容易出现小凹点,比如锌液温度 、锌液温度:锌液温度较高时容易出现小凹点, 620℃以上。现锌池温度规定按605±2℃控制。 ℃以上。现锌池温度规定按 ± ℃控制。 • 2、带钢入锌池板温:入锌池板温偏高时易出现小凹点,比如入 、带钢入锌池板温:入锌池板温偏高时易出现小凹点, 锌池板温610℃以上时。现入锌池板温规定按560~580℃控制。 锌池板温610℃以上时。现入锌池板温规定按560~580℃控制。 • 3、气刀参数:a.气刀角度:为了消除小凹点,气刀角度应调整 气刀角度: 、气刀参数: 气刀角度 为了消除小凹点, 成较大的负角度(即向下)。 气刀距离 气刀距离: 成较大的负角度(即向下)。 b.气刀距离:气刀距离带钢较远 容易产生小凹点。 气刀高度 在允许范围内, 气刀高度: 时,容易产生小凹点。 c.气刀高度:在允许范围内,气刀高度 对小凹点的形成无明显影响。高度调整原则:速度快、 对小凹点的形成无明显影响。高度调整原则:速度快、气刀压力 大时,气刀高度适当升高;速度低、气刀压力小时, 大时,气刀高度适当升高;速度低、气刀压力小时,气刀高度适 当降低。 气刀压力的影响 气刀压力的影响: 当降低。 d.气刀压力的影响:
10
• 五、针孔状露钢:一般为整个板面或大 针孔状露钢: 部分板面,位置特点不明显, 部分板面,位置特点不明显,有时可能 为板面一定区域。主要原因: 、 为板面一定区域。主要原因:1、炉内 整体气氛不合要求:氧含量或露点偏高、 整体气氛不合要求:氧含量或露点偏高、 氢气比例不合要求等。 、 氢气比例不合要求等。2、炉温或板温 偏低,造成板面清洁及还原效果较差。 偏低,造成板面清洁及还原效果较差。