切削用量的选择 1
切削用量及选择
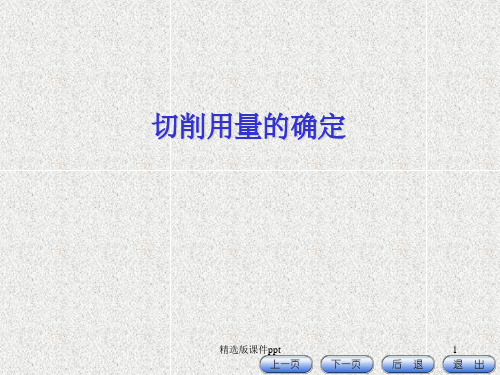
精选版课件ppt
14
3、切削用量对刀具耐用度的影响
(3) 进给量f与刀具耐用度的关系
当增大进给量后,切屑厚度增大,由切屑带着走的热量增 多,同时切屑与前刀面的接触长度增加,散热面积增大。 通过测试得知,切削温度随进给量的增加而升高,但温度 的升高幅度不及切削速度显著。
(4 )背吃刀量ap与刀具耐用度的关系
下课件ppt
33
4.分段切削背吃刀量
如果牙型较深,螺距较大,可分几次进给。每次进给 背吃刀量用螺纹深度减精加工背吃刀量所得的差按递减规 律分配。
螺纹分段切削示意图
常用螺纹切削进给次数与背吃刀量可参考表3-7~表3-9
精选版课件ppt
34
总结
1. 切削用量确定的步骤
背吃刀量的选择 →进给量的选择→切削速度的确定→校验 2. 提高切削用量的途径
13
3、 切削用量对刀具耐用度的影响 (1)刀具耐用度 所谓刀具耐用度,是指一把新刀从开始切削直到磨损量 达到磨损标准为止,在这期间所使用的总的切削时间, 用T表示。
(2) 切削速度vc与刀具耐用度的关系
切削速度是影响刀具耐用度的主要因素,其原因是当提高 切削速度时,单位时间的金属去除率会成正比例增加,刀 具与工件间的摩擦加剧,消耗于金属变形和摩擦的无用功 增加,因而产生过多的热量。因此,提高切削速度的结果 是:摩擦热大量的积聚在切屑底层而来不及传导出去,从 而使切削温度急剧升高,使刀具的耐用度大大降低。
精选版课件ppt
16
切削用量的选择:基本原则
选择切削用量的基本原则是首先选取尽可能大的背吃刀量; 其次要在机床动力和刚度允许的范围内,同时又满足已加 工表面粗糙度的要求的情况下,选取尽可能大的进给量, 最后利用《切削用量手册》选取或用公式计算确定最佳切 削速度。
简述切削用量的选择原则
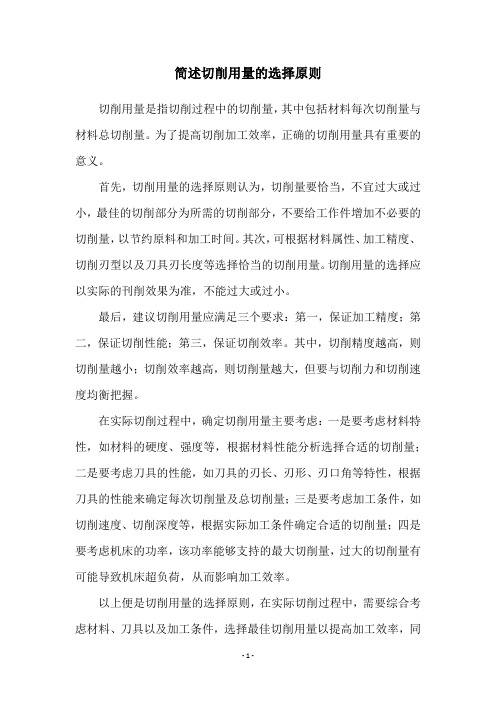
简述切削用量的选择原则
切削用量是指切削过程中的切削量,其中包括材料每次切削量与材料总切削量。
为了提高切削加工效率,正确的切削用量具有重要的意义。
首先,切削用量的选择原则认为,切削量要恰当,不宜过大或过小,最佳的切削部分为所需的切削部分,不要给工作件增加不必要的切削量,以节约原料和加工时间。
其次,可根据材料属性、加工精度、切削刃型以及刀具刃长度等选择恰当的切削用量。
切削用量的选择应以实际的刊削效果为准,不能过大或过小。
最后,建议切削用量应满足三个要求:第一,保证加工精度;第二,保证切削性能;第三,保证切削效率。
其中,切削精度越高,则切削量越小;切削效率越高,则切削量越大,但要与切削力和切削速度均衡把握。
在实际切削过程中,确定切削用量主要考虑:一是要考虑材料特性,如材料的硬度、强度等,根据材料性能分析选择合适的切削量;二是要考虑刀具的性能,如刀具的刃长、刃形、刃口角等特性,根据刀具的性能来确定每次切削量及总切削量;三是要考虑加工条件,如切削速度、切削深度等,根据实际加工条件确定合适的切削量;四是要考虑机床的功率,该功率能够支持的最大切削量,过大的切削量有可能导致机床超负荷,从而影响加工效率。
以上便是切削用量的选择原则,在实际切削过程中,需要综合考虑材料、刀具以及加工条件,选择最佳切削用量以提高加工效率,同
时节约切削原料,以降低切削成本。
数控加工的切削用量

数控加工的切削用量2009-6-11 9:42:00 来源:作者:余英良,于辉阅读:1418次我要收藏1 切削用量选择1.1 数控加工花键轴的切削用量为了保证零件的加工精度,零件分为粗车加工和精车加工。
在粗、精车零件装夹方式与刀具选择的基础上,选定零件数控加工的切削参数如下:在数控精车车削加工中,零件轮廓轨迹的加工余量为0.8÷2=0.4 mm。
主轴转速、背吃刀量等的选择参见表1。
表1 数控加工花键轴工序卡及切削用量1.2 数控加工轴承座的切削用量为了保证零件的加工精度,零件分为粗车加工和精车加工。
在粗、精车零件装夹方式与刀具选择的基础上,选定零件数控加工的切削参数如下:在数控精车车削加工中,零件轮廓轨迹的加工余量为0.8÷2=0.4 mm。
主轴转速、背吃刀量等的选择参见表2。
表2 数控加工轴承座工序卡及切削用量2 相关内容概述金属切削加工的目的,就是用各种类型的金属切削刀具把J:件毛坯上的多余部分从毛坯上剥离开来,得到图样所要求的零件形状和尺寸。
图1 车削加工中切削用量nextpage 2.1 切削用量切削用量是指机床在切削加工时的状态参数。
切削用量包括切削速度、进给速度和背吃刀量。
参见图1。
2.1.1 切削速度切削刃上的切削点相对于工件运动的瞬时速度称为切削速度。
切削速度的单位为m/min。
切削速度与机床主轴转速之问进行转换的关系为:(1)2.1.2 进给速度是刀具在单位时间内沿进给方向上相对于工件的位移量,单位为mm/min。
2.1.3 背吃刀量己加工表面和待加工表面之问的垂直距离。
背吃刀量的计算公式为:(2)式(1)、式(2)中n为主轴(工件)转速,d为工件直径,dω、dm见图1。
在切削加工中,切削速度、进给速度和背吃刀量3个参数是相互关联的。
粗加工中,为提高效率,一般采用较大的背吃刀量。
此时切削速度和进给速度相对较小;在半精加工和精加工阶段,一般采用较大的切削速度、较小的进给量和背吃刀量,以获得较好的加工质量。
切削 用量的合理选择
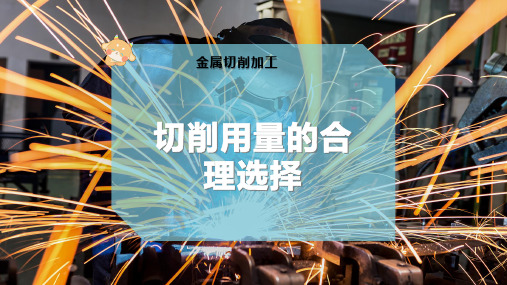
2)根据机床说明书,取机床实际进给量 =0.51mm/r。 3)检验机床进给机构允许的进给量。参考CA6140车床说 明书,查出机床进给机构允许的最大进给抗力为:FMfmax= 3528N。 计算切削时进给力为:
统、工件刚度以及精加工时表面粗糙度要求,确定进给量。
3)根据刀具寿命,确定切削速度。 4)所选定的切削用量应该是机床功率所允许的。
1.2切削用量的合理选择方法
1.背吃刀量的合理选择
背吃刀量一般是根据加工余量来确定。 粗加工(表面粗糙度Ra=50~12.5μm)时,尽可能一 次走刀即切除全部余量,在中等功率的机床上加工,取 ap=8~10mm;加工余量太大或余量不均匀、工艺系统刚性 不足或者断续切削时,可分几次走刀。 半精加工(Ra=6.3~3.2μm)时,取ap=0.5~2mm。 精加工(Ra=1.6~0.8μm)时,取ap=0.1~0.4mm。
1.5切削用量的优化概念
切削用量的优化是指在一定的预定目标及约束条件下, 选择最佳的切削用量。
在实际生产中,由于各种条件(加工零件、机床、刀 具、夹具等)都在变化,很难确定出一组最合理的切削用 量数值。
利用切削用量优化的方法,在确定加工条件下,综合 考虑各个因素,通过计算机辅助设计,能找出满足高效、 低成本、高利润和达到表面质量要求的一组最佳的切削用 量参数。实际切削用量的优化过程就是建立优化目标的数 学模型,用计算机求极值。主要目标函数有三个。
床功率是否允许。 在实际生产中,切削用量的合理选择,既可参照有关 手册的推荐数据,也可凭经验根据选择原则确定。
1.3车削用量的合理选择例题
切削用量的选择和计算公式

切削用量的选择和计算公式切削用量的选择和计算是机械加工中非常重要的一环,它直接影响到加工效率、加工质量和工具的使用寿命。
正确选择和计算切削用量可以使加工过程更加稳定和高效。
本文将介绍切削用量的选择和计算公式,并探讨其在机械加工中的应用。
切削用量的选择。
切削用量是指在切削加工过程中,刀具与工件之间的相对运动距离。
切削用量的选择需要考虑到工件材料、刀具材料、切削速度、进给速度等因素。
一般来说,切削用量越大,切削效率越高,但是过大的切削用量会导致刀具磨损加剧,甚至损坏刀具。
因此,在选择切削用量时需要在保证加工效率的前提下,尽量减小刀具的磨损。
切削用量的计算公式。
切削用量的计算公式通常包括切削速度、进给速度和刀具的切削刃数。
切削速度是指刀具在工件表面的相对运动速度,通常用Vc表示,单位为m/min。
进给速度是指刀具在工件表面的进给速度,通常用f表示,单位为mm/r。
刀具的切削刃数是指刀具上切削刃的数量,通常用z表示。
根据切削速度、进给速度和刀具的切削刃数,切削用量的计算公式可以表示为:切削用量 = 切削速度×进给速度×刀具切削刃数。
在实际应用中,切削用量的计算公式可以根据具体的加工情况进行调整,以满足加工的要求。
切削用量的应用。
切削用量的选择和计算在机械加工中具有重要的应用价值。
正确选择切削用量可以提高加工效率,降低成本,提高产品质量。
同时,合理的切削用量还可以延长刀具的使用寿命,减少刀具的更换次数,降低加工成本。
在实际加工中,切削用量的选择和计算需要结合具体的加工情况进行调整。
例如,在加工硬质材料时,可以适当增大切削用量,以提高加工效率;在加工精密零件时,可以适当减小切削用量,以保证加工精度。
此外,切削用量的选择还需要考虑到刀具的类型、刀具的磨损情况、工件的材料和形状等因素。
总之,切削用量的选择和计算是机械加工中非常重要的一环。
正确选择和计算切削用量可以提高加工效率、降低成本、提高产品质量。
车削加工切削用量的选择

数控机床加生产效率为主,但也应考 率加工成本;半精加工和精加工的切削用量应以保证加工质量 为前提,并兼顾切削效率和加工成本。粗车和半精车切削用量 的具体选择方法介绍如下: (1)粗车切削用量选择
数控机床加工的切削用量
2)进给量f
当背吃刀量确定后,再选出进给量f ,就能计算切削力。 该力作用在工件、机床和刀具上,应为它们的刚度和强度所 允许。也就是说,应在不损坏刀片和刀杆、不损坏机床进给 机构、不顶弯工件和不产生振动的条件下,选取一个最大的 进给量f 值。或者利用确定的和f ,求出主切削力Fz,来校验 刀片和刀杆的强度;根据计算出的切深抗力Fy来校验工件的 刚度;根据计算出的进给抗力Fx来校验机床进给机构薄弱环 节的强度等。
数控机床编程与操作
半精车和精车的背吃刀量较小,产生的切削力不大,所
以增大进给量主要受到表面粗糙度限制。在已知的切削速度v
(预先假设)和刀尖圆弧半径条件下,根据加工要求达到的 表面粗糙度,可利用计算的方法或手册资料确定进给量。
数控机床加工的切削用量
3)切削速度Vc
半精车、精车的背吃刀量和进给量f 较小,切削力对工艺系 统强度和刚度影响较小,消耗功率较少,故切削速度Vc主要受 刀具耐用度限制。需要注意的是,交流变频调速的数控车床低 速输出力矩较小,因此切削速度不能太低。
按上述原则,可利用计算的方法或查手册资料来确定进 给量f 值。 3)切削速度v
在背吃刀量和进给量选定后,根据规定达到的合理耐用度 值,就可确定切削速度v。
数控机床加工的切削用量
1.切削用量选择原则
a 要提高生产效率应尽量增大背吃刀量 p、进给量f 和切
削速度 v 。事实上,在提高切削用量时会受到切削力、切削
切削用量的合理选择
表7-5 硬质合金车刀及高速钢车刀粗车外圆和端面时的进给量
3)切削速度 切削速度vc是根据刀具耐用度T确定的。在背吃刀量ap和进给量f
确定后,根据规定的刀具耐用度T,计算刀具耐用度T所允许的切削n计,再选取机床主轴实际转速n,最后由机床主轴实 际转速n计算实际切削速度vc。
对切削加工实际生产来 说,较方便的是根据切 削用量手册查表确定切 削用量。切削用量手册 中的数据是在积累了大 量的生产经验及试验研 究工作的基础上,经过 科学的数据处理后制定 出来的。查表确定切削 用量后,还可根据具体 生产条件适当调整。
把各公式的计算结果绘 制成各种图表,直接从 其上选择切削用量。针 对具体机床制成的切削 用量图表,更适合于生 产现场使用。
3)切削速度 c 半精加工和精加工的切削速度
也是受刀具耐用度的限制,因此,
切削速度与粗加工时的计算方法相同。但由于半精加工和精加工切削条
件较好,刀具耐用度比粗加工时规定得大,所以半精加工和精加工时的
切削速度一般比粗加工时高。
1.3 提高切削用量的途径
提高切削用量的途径很多,可归纳为以下几个方面: (1)采用切削性能更好的新型刀具材料。 (2)改善工件材料的加工性。 (3)改进刀具结构和选用合理刀具几何参数。 (4)提高刀具的制造和刃磨质量。 (5)采用新型的、性能优良的切削液和高效率的冷却方法。
(7-1)
若加工余量A太大或加工工艺系统刚性比较差,则加工余量A
可经二次或更多次走刀去除。若分二次走刀,则它们的背吃刀量
的表达式分别为
ap1=(3/4~2/3)A ap2=(1/3~1/4)A
(7-2) (7-3)
2)进给量 当背吃刀量确定后,根据加工工艺系统允许的切削力,进一步确定
切削用量的选择
切削用量的选择一、引言切削用量的选择是机械加工中非常重要的一项工作,它直接影响到加工质量、生产效率和设备寿命等方面。
因此,正确选择切削用量是保证机械加工质量和效率的关键。
二、切削用量的定义切削用量是指在机械加工过程中,钻头、铣刀或其他刀具每次进给或每分钟进给的长度或数量。
通常包括进给速度、转速和切深等。
三、影响切削用量的因素1.材料硬度:材料硬度越高,所需的切削力就越大,因此需要减小切削用量。
2.材料性质:不同材料具有不同的物理性质和化学性质,在选择切削用量时需要考虑这些因素。
3.加工精度:如果要求高精度加工,则需要降低切削用量以减少误差。
4.设备能力:设备本身也有其最大可承受的进给速度、转速等限制,需要根据设备能力进行选择。
5.加工方式:不同的加工方式对于所需的切削用量也有影响,例如铣削和车削的切削用量选择不同。
四、切削用量的选择方法1.根据材料硬度选择切削用量:一般来说,材料硬度越高,所需的切削力就越大,因此需要减小切削用量。
但是也需要注意,如果切削用量过小,则会导致加工时间过长、工具磨损严重等问题。
2.根据加工精度选择切削用量:如果要求高精度加工,则需要降低切削用量以减少误差。
此时可以通过增加进给次数或减小每次进给长度来实现。
3.根据设备能力选择切削用量:设备本身也有其最大可承受的进给速度、转速等限制,需要根据设备能力进行选择。
如果超过了设备能力,则会导致设备故障或者加工效率下降。
4.根据材料性质选择切削用量:不同材料具有不同的物理性质和化学性质,在选择切削用量时需要考虑这些因素。
例如对于易碎材料,应该采取小进给、低转速的方式进行加工。
5.根据加工方式选择切削用量:不同的加工方式对于所需的切削用量也有影响,例如铣削和车削的切削用量选择不同。
一般来说,铣削时需要较大的切削用量,而车削时则需要较小的切削用量。
五、切削用量的优化1.合理选择刀具:不同类型的刀具适用于不同材料和加工方式,在选择刀具时需要考虑这些因素。
切削用量的选择与计算
切削用量的选择与计算正确的切削用量,对于保证产品质量、提高切削效率和经济效益,具有重要意义。
切削用量的选择主要依据工件材料、加工精度和表面粗糙度的要求,还应考虑刀具合理的耐用度、工艺系统刚性及机床效率等条件。
由于切削速度V c对刀具寿命影响最大,其次为进给量f,影响最小的是背吃刀量a p,因此,选择切削用量的步骤是先确定背吃刀量a p,再选择进给量f,最后再确定切削速度V c,必要时应校验机床功率是否允许。
所以,其基本原则是:首先应选择一个尽可能大的背吃刀量a p,其次选择一个较大的进给量f,最后,在刀具耐用度和机床功率允许的情况下选择一个合理的切削速度V c。
4.1轴外圆的切削用量4.1.1确定粗车时的切削用量ap1)背吃刀量的a p的选择:工件下料为45号钢棒料,大小为62mm×90mm,粗车至Φ60mm,表面有硬化层、氧化皮或硬杂质等,但在加工余量(指半径方向上)不多并比较均匀,且加工工艺系统刚性足够,应使背吃刀量一次性切除余量A,即:a p=A,查《简明机械加工工艺手册》表11-1可知A=(50-46)/2=2mm,单边留1mm做半精车、精车余量,取粗车背吃刀量a p=1mm。
2)确定进给量f:查查《简明机械加工工艺手册》表11-1可知,f=0.4~0.5mm/r,根据机床说明书,初步选定f=0.45mm/r.3)确定切削速度V c:查查《简明机械加工工艺手册》表11-5可知,V c=2.17~2.667m/s,考虑到进给量较大取V c=2m/s。
4)确定主轴转速n,由公式:n=1000v/πd=(1000×2)/(3.14×60)=10.62r/s 根据机床说明书,取n=12.5r/s。
此时切削速度为:V c=πdn/1000=(3.14×60×12.5)/1000=2.36m/s 此速度小于预得切削速度,故可用。
5)校验机床效率:查《简明机械加工工艺手册》表11-6~11-9可求得切削力的公式及相关数据。
切削用量及加工余量的合理选择
削用量及加工余量的合理选择切削用量的选择,主要根据刀具耐用度和加工表面粗糟度,加工精度的要求。
切削用量愈大,刀具耐用度愈低。
切削速度Vc,进给量f和切削深度Ap刀具耐用度的影响不同,切削速度影响最大,进给量次之,切削深度影响最小。
(1)切削深度的选择切削深度应根据加工余量确定。
1)粗加工时,在留有精加工及半精加工的余量后,应尽可能一次走刀切除全部粗加工余量。
若粗切余量过大,不能一次切除,这时,应将第一次走刀的切削深度取大些,可占全部余量的2/3~3/4,以使精加工工序获得较小的表面粗糙度值及较高的加工精度。
2)切削零件表层有硬皮的铸、锻件或不锈钢等冷硬较严重的材料时,应使切削深度超过硬皮或冷硬层,以避免使切削刃在硬皮或冷硬层上切削。
(硬皮深度可达0.07~0.5mm)3)当冲击载荷较大(如断续切削)或工艺系统刚性较差时,应适当减小切削深度。
4)一般精切( 1.6!~ 0.8)时,可取=0.05~0.8mm;半精切( 6.3~ 3.2)时,可取=1.0~3.0mm.(2)进给量F的选择1)粗加工时,进给量主要受刀杆、刀具、机床、工件等的强度、刚度所能承受的切削力的限制,一般是根据刚度来选取。
2)精加工时,进给量主要受表面粗糙度要求的限制。
要求表面粗糙度小,应选取较小的F。
但F过小,切削厚度过薄,表面粗糙度反而大,而且刀具磨损加剧。
3)当刀具的副角较大,刀尖圆弧半径较大时,F可选较大值。
(3)切削速度的选择在保证刀具的经济耐用度及切削负荷不超过机床的额定功率的情况下选定切削速度。
1)粗车时,背后吃刀量和进给量均较大,故选较低的切削速度,精车时,则选较高的切削速度。
2)加工材料的加工性差时,切削速度选得低些。
如加工灰铸铁的切削速度比加工中碳钢低;而加工铝合金和铜合金的切削速度比加工中碳钢要高得多。
3)刀具材料的切削性能越好时,切削速度也可以越高。
如涂层硬质合金、陶瓷、金刚石和立方氮化硼刀具的切削速度。
- 1、下载文档前请自行甄别文档内容的完整性,平台不提供额外的编辑、内容补充、找答案等附加服务。
- 2、"仅部分预览"的文档,不可在线预览部分如存在完整性等问题,可反馈申请退款(可完整预览的文档不适用该条件!)。
- 3、如文档侵犯您的权益,请联系客服反馈,我们会尽快为您处理(人工客服工作时间:9:00-18:30)。
切削用量的选择
选择合理的切削用量,要综合考虑生产率、加工质量和加工成本。
一般地,粗加工时,由于要尽量保证较高的金属切除率和必要的刀具耐用度,应优先选择大的背吃刀量,其次选择较大的进给量。
最后根据刀具耐用度,确定合适的切削速度。
精加工时,由于要保证工件的加工质量,应选用较小的进给量和背吃刀量,并尽可能选用较高的切削速度。
(1)背吃刀量的选择
粗加工的背吃刀量应根据工件的加工余量确定,在保留半精加工余量的前提下,应尽量用一次走刀就切除全部粗加工余量;当加工余量过大或工艺系统刚性过差时,可分二次走刀。
第一次走刀的背吃刀量,一般为总加工余量的2/3—3/4。
在加工铸、锻件时,应尽量使背吃刀量大于硬皮层的厚度,以保护刀尖。
半精、精加工的切削余量较小,其背吃刀量通常都是一次走刀切除全部余量。
(2)进给量的选择
粗加工时,进给量的选择主要受切削力的限制。
在工艺系统刚度和强度良好的情况下,可选用较大的进给量值。
表1.4 为粗车时进给量的参考值。
由于进给量对工件的已加工表面粗糙度值影响很大,一般在半精加工和精加工时,进给量取得都较小。
通常按照工件加工表面粗糙度值的要求,根据工件材料、刀尖圆弧半径、切削速度等条
件来选择合理的进给量。
当切削速度提高,刀尖圆弧半径增大,或刀具磨有修光刃时,可以选择较大的进给量,以提高生产率。
表 1.4 硬质合金及高速钢车刀粗车外圆和端面时的进给量
注:1.加工断续表面及有冲击的加工时,表内的进给量应乘系数K=0.75~0.85。
2.加工耐热钢及其合金时,不采用大于1.0 mm/r 的进给量。
3.加工淬硬钢时,表内进给量应乘系数K=0.8(当材料硬度为44~56HRC)或K=0.5(当硬度为57~62HRC时)。
(3)切削速度的选择
在背吃刀量和进给量选定以后,可在保证刀具合理耐用度的条件下,确定合适的切削速度。
粗加工时,背吃刀量和进给量都较大,切削速度受刀具耐用度和机床功率的限制,一般较低。
精加工时,背吃刀量和进给量都取得较小,切削速度主要受加工质量和刀具耐用度的限制,一般较高。
选择切削速度时,还应考虑工件材料的强度和硬度以及切削加工性等因素。
表1.5 为车削外圆时切削速度的参考值
1.5 硬质合金外圆车刀切削速度参考值
注:切削钢及灰铸铁时刀具耐用度约为 60~90min。