如何提高装配车间生产能力报告
生产车间产能提高措施

生产车间产能提高措施一、前言随着市场竞争的加剧,提高生产车间产能成为企业降低成本、提升竞争力的重要手段。
本文档旨在分析当前生产车间的产能现状,并提出相应的提高措施,以期实现生产效率的提升。
二、产能现状分析1. 设备及人员配置:评估现有设备的技术水平、运行状态以及人员配置情况,分析其对产能的影响。
2. 生产流程:分析现有的生产流程是否存在瓶颈,如生产流程不合理、生产计划不科学等。
3. 质量控制:分析生产过程中的质量控制环节,是否存在质量问题导致生产线停滞或返工。
4. 物料管理:评估物料供应、库存以及物料流动环节是否存在问题,如物料供应不及时、库存过高或过低等。
三、提高产能措施1. 设备及人员优化- 引进先进设备,提高生产效率。
- 定期进行设备维护和保养,确保设备稳定运行。
- 加强人员培训,提高员工技能水平和工作效率。
2. 生产流程优化- 分析并优化生产流程,消除瓶颈环节。
- 制定合理的生产计划,确保生产任务的高效完成。
3. 质量控制优化- 加强质量控制环节,减少生产线停滞和返工。
- 采用先进质量管理方法,提高产品质量。
4. 物料管理优化- 优化物料供应流程,确保物料及时供应。
- 实施有效的库存管理,降低库存成本。
- 优化物料流动环节,减少物料损耗。
四、实施计划1. 制定详细的实施计划,明确各项措施的负责人、完成时间等。
2. 对实施过程进行监控,确保各项措施按计划进行。
3. 定期对实施效果进行评估,并根据实际情况进行调整。
五、总结提高生产车间产能是提升企业竞争力的重要途径。
通过分析产能现状,采取设备及人员优化、生产流程优化、质量控制优化和物料管理优化等措施,有望实现生产效率的提升。
同时,制定详细的实施计划并进行过程监控和效果评估,有助于确保各项措施的顺利实施和取得预期效果。
如何提高工厂的生产能力
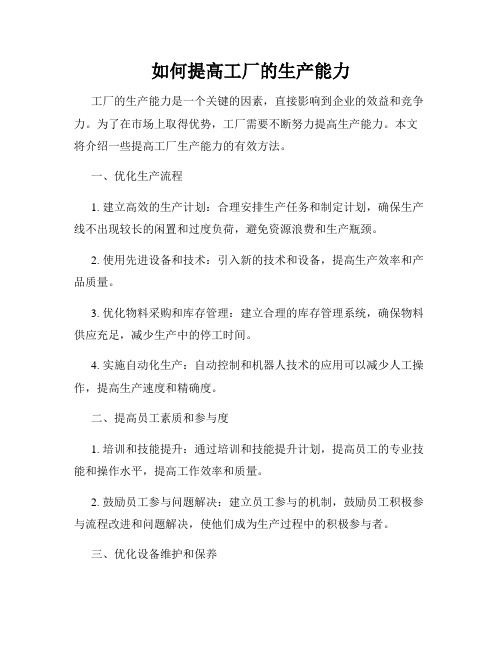
如何提高工厂的生产能力工厂的生产能力是一个关键的因素,直接影响到企业的效益和竞争力。
为了在市场上取得优势,工厂需要不断努力提高生产能力。
本文将介绍一些提高工厂生产能力的有效方法。
一、优化生产流程1. 建立高效的生产计划:合理安排生产任务和制定计划,确保生产线不出现较长的闲置和过度负荷,避免资源浪费和生产瓶颈。
2. 使用先进设备和技术:引入新的技术和设备,提高生产效率和产品质量。
3. 优化物料采购和库存管理:建立合理的库存管理系统,确保物料供应充足,减少生产中的停工时间。
4. 实施自动化生产:自动控制和机器人技术的应用可以减少人工操作,提高生产速度和精确度。
二、提高员工素质和参与度1. 培训和技能提升:通过培训和技能提升计划,提高员工的专业技能和操作水平,提高工作效率和质量。
2. 鼓励员工参与问题解决:建立员工参与的机制,鼓励员工积极参与流程改进和问题解决,使他们成为生产过程中的积极参与者。
三、优化设备维护和保养1. 定期和预防性维护:制定设备维护计划,进行定期的设备检修,减少设备故障和停机时间。
2. 清洁和润滑:保持设备的清洁和润滑,以减少磨损和故障。
四、实施供应链管理1. 供应商优化:选择可靠的供应商,确保物料的及时供应和质量稳定。
2. 供应链流程优化:与供应商密切合作,优化供应链的流程和交付时间,减少等待时间和库存量。
总结:通过优化生产流程、提高员工素质、优化设备维护和实施供应链管理,工厂可以有效提高生产能力。
这些方法需要管理团队的积极引导和员工的参与,同时也需要持续的监测和改进。
只有不断地提高生产能力,工厂才能在激烈的市场竞争中保持优势。
装配车间员工个人工作总结范文7篇

装配车间员工个人工作总结范文7篇篇1一、引言作为装配车间的一名员工,我深感责任重大。
在过去的一年里,我始终秉持着公司的发展理念,以高度的责任心和敬业精神,认真履行自己的工作职责。
在此,我对过去一年的工作进行全面的回顾和总结。
二、工作内容及成果1. 生产线装配工作在过去的一年里,我主要从事装配车间的生产线装配工作。
我严格按照生产流程,认真完成每一道工序,确保产品质量。
同时,我也积极参与生产线的优化工作,提出合理化建议,提高生产效率。
2. 技术学习与提升为了提高自身的技术水平,我积极参加公司组织的各类培训,学习先进的装配技术和理念。
同时,我也自主学习,通过阅读相关书籍和资料,不断提高自己的专业技能。
3. 团队协作与沟通在车间工作中,我始终注重团队协作,与同事们保持良好的沟通。
我积极参与团队讨论,为车间管理提出建设性意见。
同时,我也乐于帮助同事,共同解决工作中遇到的问题。
4. 安全生产与设备维护我深知安全生产的重要性,始终严格按照安全操作规程进行工作。
同时,我也积极参与设备的日常维护和保养,确保设备的正常运行。
三、工作收获与成长1. 专业技能提升通过一年的工作和学习,我在装配技术方面取得了显著的进步,能够独立完成复杂的装配任务。
2. 团队协作能力增强在团队协作中,我学会了如何与同事有效沟通,共同解决问题。
我也更加明白团队协作的重要性,懂得为团队利益着想。
3. 责任心与敬业精神增强通过一年的工作,我更加明白责任心和敬业精神对工作的重要性。
我始终尽职尽责,为公司的发展贡献自己的力量。
四、工作不足与改进1. 创新能力不足虽然我在工作中取得了一些成绩,但在创新方面还有待提高。
今后,我将更加积极地思考,提出更多的创新建议。
2. 应对压力能力有待提高在工作中,有时会遇到一些压力较大的情况,我需要提高自己的应对压力能力。
今后,我将学习更多的压力管理技巧,提高自己的心理素质。
五、未来展望在新的一年里,我将继续提高自己的专业技能和团队协作能力,为公司的发展贡献更多的力量。
提高生产车间产能的措施

提高生产车间产能的措施目标我们的目标是提高生产车间的产能,以满足市场需求并提高公司的竞争力。
1. 优化生产流程- 分析生产流程,找出瓶颈环节,并采取措施解决瓶颈问题,以提高整体生产效率。
- 引入先进的生产设备和技术,自动化生产过程,减少人工操作时间和错误率。
- 制定详细的生产计划和排程,确保资源的合理配置和生产任务的高效完成。
2. 增加设备运行时间- 定期进行设备维护和保养,提高设备的可靠性和使用寿命。
- 优化设备的启停时间,减少停机和转换时间,提高设备的运行效率。
- 采用智能化设备监控系统,实时监测设备运行状态,及时发现并解决潜在问题。
3. 提高员工技能和培训- 定期组织员工培训,提高员工的专业技能和操作水平。
- 鼓励员工研究和分享经验,促进团队合作,提高整体生产效率。
- 设立奖励制度,激励员工提高工作效率和质量。
4. 优化物料管理- 建立完善的物料管理系统,确保物料供应的及时性和准确性。
- 优化物料采购流程,降低物料库存成本,减少废品和报废率。
- 与供应商建立良好的合作关系,确保物料质量和供应稳定性。
5. 引入质量管理体系- 建立完善的质量管理体系,包括质量检测、质量控制和质量改进等环节。
- 引入先进的质量检测设备和方法,提高产品的质量稳定性和一致性。
- 鼓励员工参与质量改进活动,持续提升产品质量和客户满意度。
6. 数据分析和改进- 收集和分析生产数据,找出问题和改进的机会。
- 制定改进措施并跟踪实施效果,持续优化生产流程和方法。
- 建立良好的反馈机制,及时反馈问题并采取纠正措施。
总结通过优化生产流程、增加设备运行时间、提高员工技能和培训、优化物料管理、引入质量管理体系以及数据分析和改进等措施,我们可以有效提高生产车间的产能,提高公司的竞争力和市场份额。
装配车间产能分析报告

装配车间产能分析报告1. 引言本报告旨在对某装配车间的产能进行详细分析,以帮助车间管理人员了解当前产能状况和潜在瓶颈,为提升效率和优化生产提供参考意见。
2. 数据收集与整理为了进行产能分析,我们收集并整理了以下数据:•车间工人数量和各岗位的工作时间;•装配生产线的生产能力和总运行时间;•原材料供应情况,包括供应商交货时间和质量;•不良品数量和相关原因;•装配过程中的平均生产周期。
3. 产能计算方法为了准确计算装配车间的产能,我们使用以下公式:产能 = 工作时间 × 生产线运行时间 × 良品率•工作时间:车间工人的实际工作时间,不包括休息、换班和其他非生产时间;•生产线运行时间:装配生产线实际运行的时间,不包括停机、维修和故障排除时间;•良品率:装配生产线生产的良品数量占总产量的比例。
4. 产能分析结果根据我们的数据分析和计算,得出以下产能分析结果:•车间工人数量:共有60名工人,包括装配工、检验工和包装工;•各岗位工作时间:装配工每人工作8小时,检验工每人工作4小时,包装工每人工作8小时;•生产线运行时间:装配生产线每天运行16小时;•原材料供应:原材料供应稳定,供应商交货时间为每周两次,质量良好;•不良品数量:平均每天产生30个不良品,主要原因是操作失误和设备故障;•平均生产周期:每个产品的平均生产周期为2天。
根据以上数据,我们进行产能计算如下:•车间工人总工作时间 = 60人 × 8小时 = 480小时/天•良品率 = (总产量 - 不良品数量) / 总产量 = (480 - 30) / 480 ≈ 0.9375因此,装配车间的实际产能为:产能= 480 × 16 × 0.9375 ≈ 7224 件/天5. 产能瓶颈分析及建议根据产能分析结果,我们发现当前装配车间的产能为7224件/天。
然而,由于不良品的产生和一些操作失误,实际产出数量较理论产能有所下降。
提高装配效率的措施
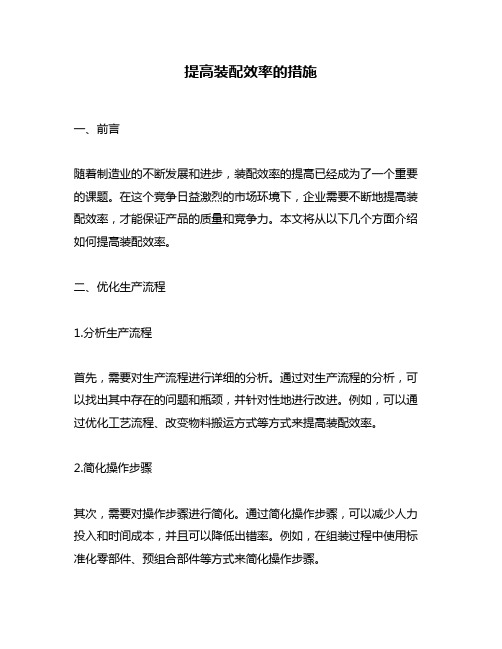
提高装配效率的措施一、前言随着制造业的不断发展和进步,装配效率的提高已经成为了一个重要的课题。
在这个竞争日益激烈的市场环境下,企业需要不断地提高装配效率,才能保证产品的质量和竞争力。
本文将从以下几个方面介绍如何提高装配效率。
二、优化生产流程1.分析生产流程首先,需要对生产流程进行详细的分析。
通过对生产流程的分析,可以找出其中存在的问题和瓶颈,并针对性地进行改进。
例如,可以通过优化工艺流程、改变物料搬运方式等方式来提高装配效率。
2.简化操作步骤其次,需要对操作步骤进行简化。
通过简化操作步骤,可以减少人力投入和时间成本,并且可以降低出错率。
例如,在组装过程中使用标准化零部件、预组合部件等方式来简化操作步骤。
3.优化物料供应链此外,还需要优化物料供应链。
通过优化物料供应链,可以确保物料及时到位,并且减少因为缺失物料而导致的停工现象。
例如,在与供应商对接时要求其按时交货,建立物料库存管理系统等方式来优化物料供应链。
三、提高员工技能1.培训员工员工是企业的重要资源,他们的技能水平直接影响到企业的生产效率和质量。
因此,需要通过培训来提高员工的技能水平。
例如,可以开展专业技术培训、安全生产培训、岗位职责培训等方式来提高员工技能。
2.激励员工除了培训之外,还需要通过激励机制来激发员工的积极性和创造力。
例如,可以通过设立奖金、晋升机制等方式来激励员工。
四、采用先进设备1.引进先进设备在现代化制造业中,先进设备是提高装配效率的关键因素之一。
因此,需要引进先进设备,并根据实际情况进行定制化改造。
例如,在自动化装配线上使用机器人等智能化设备。
2.维护保养设备除了引进先进设备之外,还需要及时维护保养现有设备。
通过定期检查和维护保养,可以确保设备始终处于最佳状态,并且延长其使用寿命。
五、优化管理模式1.建立科学的管理体系建立科学的管理体系是提高装配效率的关键。
通过建立科学的管理体系,可以实现生产过程的标准化和流程化,从而提高生产效率。
装配工作总结:提高生产效率
装配工作总结:提高生产效率2023年装配生产总结在2023年,我公司针对装配生产的相应工作进行了总结,并着重思考了如何提高生产效率的问题。
首先,我们发现提高生产效率是一个系统的工程,需要从多个方面入手。
具体来说,可以从以下三个方面进行改善:一、制定科学合理的计划为了提高生产效率,我们需要在制定计划时更加科学合理。
在做好各项准备工作之后,制定一个具有有效性和可操作性的生产计划,考虑到材料的充足性、生产周期及各个工序之间的时间关系等,以避免出现生产过程中的错误等影响生产进度的变化情况。
同时,我们需要提高对制定计划的准确性和可行性的认识,找出问题并及时解决。
二、提高生产技术水平为了提高生产效率,我们需要在提升生产技术水平方面下功夫。
在这个方面,我们需要注重技术创新的培养和推广。
通过培训、学习,我们可以积极学习新的生产技术、生产工艺,并将其运用到自己的装配生产过程中。
这样不仅仅可以提高工人操作技能,还能加强对设备控制的理解,提高机器设备的利用效率,突破技术瓶颈,提高生产效率。
三、优化管理方式为了提高生产效率,我们需要在工厂管理方面进行优化升级。
在这个方面,我们需要更加注重事前规划、事中沟通与协调、事后评估、事后反馈等各项工程,打高效切实的管理战争。
同时,加强设备检查、定期维护,实行严格的设备管理制度和日常生产管理制度,以及问题的准确归纳、分析和解决等手段,确保生产能够实现正常运行,提高了生产效率和质量。
总之,在2023年的装配生产领域中,提高生产效率是一个任务繁重的工作。
从多方面入手,制定科学合理的计划、提高生产技术水平、优化管理方式,三者互为支撑,共同推动装配生产工作的顺利实施。
我们相信,不断总结优化的装配生产工作将能够为公司的未来繁荣做出积极贡献。
提高装配效率的措施
提高装配效率的措施一、引言在现代制造业中,装配是一个非常重要的环节。
装配效率的高低直接影响到企业的生产能力和产品质量。
提高装配效率是企业提高竞争力、降低成本的关键一环。
本文将探讨一些提高装配效率的措施,以帮助企业实现生产效率的增长。
二、流程优化2.1 详细流程分析在提高装配效率之前,首先需要对装配流程进行详细的分析。
通过对整个装配过程的梳理,找出每个环节中存在的问题和瓶颈,以及可能的改进点。
2.2 标准化操作制定标准化操作流程是提高装配效率的关键。
通过统一的操作流程,可以减少工人的操作错误和浪费,提高装配的一致性和效率。
在制定标准化操作流程时,应充分考虑工人的实际操作情况,并进行实地测试和改进。
2.3 制定时间目标为了提高装配效率,可以制定时间目标。
通过设定合理的时间目标,可以激励工人加快工作速度,提高效率。
同时,可以将时间目标与绩效考核挂钩,进一步激发工人的工作动力。
三、设备改进3.1 自动化设备引入自动化设备是提高装配效率的关键一步。
自动化设备可以实现自动化装配、检测和调整,大大提高装配的速度和准确性。
同时,还可以减少对人力的依赖,降低劳动成本。
3.2 智能化设备在装配过程中,可以引入一些智能化设备。
例如,智能化拧紧工具可以根据不同的螺丝规格自动调整扭矩和角度,提高装配的准确度和速度。
智能化设备还可以通过传感器和算法,实现实时监控和调整,提高装配的稳定性和一致性。
3.3 设备维护和保养为了保证设备的正常运行和稳定性,需要进行定期的设备维护和保养。
定期的设备维护和保养可以延长设备的使用寿命,避免设备故障对装配效率的影响。
同时,还可以通过维护保养,及时发现设备存在的问题,并做好记录和改进。
四、人员管理4.1 培训和培养为了提高装配效率,需要对工人进行系统的培训和培养。
培训可以提高工人的操作技能和知识水平,使其能够更好地适应装配工作的要求。
同时,还应注重培养工人的团队合作能力和问题解决能力,以提高整体的工作效率。
车间产能提升报告(共5篇)
车间产能提升报告(共5篇):产能车间提升报告车间产能提升方案关注车间每天的产能如何提高车间产能篇一:提升产能报告1220关于制造系统提升产能报告为完成公司2012年经营指标,销售保证3.2亿,力争3.7亿,确保利润4000万,根据所得2010年、2011年1---9月份部分统计数字,提出以下产能提升报告:一、各车间提升产能需求:1、人员2010年共销售17100 万元,总销售收入14630万元,工业总产值11115万元,一线结构、机加、装配三个车间共出勤人数1521人,月均出勤127人,人均工业总产值87.69万元。
2011年1—9月份共销售13500 万元,总销售收入11500万元,工业总产值8775万元,一线结构、机加、装配三个车间共出勤人数1293人,月均出勤143人,人均工业总产值81.44万元。
2012年经营目标销售32000万元,销售收入27400万元,工业总产值20800万元,根据10年、11年最高人均工业总产值为87.69万元,推算出一线结构、为完成明年经营指标,经车间多次核算,11月份在岗员工175人,计划增加需求53人,明年总人数达228人,较推算237人,尚欠缺9人。
2、设备车间现有主要加工设备(机加、下料、焊接,不含电器、行车等辅助设备)合计99台,计划增加25台,总计达到124台。
现在设备利用率主要欠缺在机加工车间,现有设备约80 台,去除刨床及一台老50车床,剩余78台有效机加设备,白班设备利用率基本为100%,中班开机设备23 台,设备利用率为30% ,两班累计利用率为130%,综合平均利用率为65% ,对应1—9月份工业总产值共8775万元,自制销售各类产品1183 台,月平均销售131台,月平均工业总产值975万元,如(两班制)设备利用率增至100% ,即中班全开,则相对应可达到年工业总产值18000 万元,年销售自制产品2427 台,月平均工业总产值1500万元,月平均销售自制产品202台,台机销售额230万元。
提高组装车间生产效率的途径和方法
提高组装车间生产效率的途径和方法第一篇:提高组装车间生产效率的途径和方法提高组装车间生产效率的途径和方法摘要:通过分析某组装车间生产效率低的现状,找出了制约生产效率提高的原因,并根据实际情况,提出了有效的途径和方法,为车间生产效率的提高指明了方向。
Abstract: Through the analysis of the status of a workshop low production efficiency, this paper finds out the reason of restricting efficiency, and according to the actual situation proposes the effective ways and methods for improving the efficiency of production workshop.关键词:车间;生产效率;提高Key words: workshop;production efficiency;raise0引言随着科学技术的迅速发展和社会经济的快速增长,制造业的竞争日益激烈,再加上消费者的需求日新月异的变化,这给制造业带来了很大的机遇和挑战。
对制造业而言,每个企业都面临着持续多变、不可预测的全球化市场竞争,为了在日益激烈的市场竞争中生存下去,企业必须快速适应市场的变化并做出相应的产品结构调整,高效率、低成本已成为当今制造企业生存和发展的基本保障。
本文分析了影响组装车间效率的主要原因,并提出了相应的提高生产效率的有效措施。
1影响车间生产效率的因素分析某泵生产企业,由于所生产的产品适用范围广、质量好,从而销量较好,订单较多,但是由于一些车间,尤其是组装车间的生产效率较低,导致经常不能按期交付订单,从而影响了公司的信誉和收入。
经现场调查发现,影响因素主要有以下几个方面:1.1 工作量分配不合理在组装流水线上,各工位的工作量各不相同,有的工位工作量较小,而有的工位则较大,但是在每个工位都只分配一个工人,且工资待遇都相同,这就给干活多的人造成心理上的不平衡,影响工作积极性,从而不认真对待工作,进而影响生产效率和产品质量。
- 1、下载文档前请自行甄别文档内容的完整性,平台不提供额外的编辑、内容补充、找答案等附加服务。
- 2、"仅部分预览"的文档,不可在线预览部分如存在完整性等问题,可反馈申请退款(可完整预览的文档不适用该条件!)。
- 3、如文档侵犯您的权益,请联系客服反馈,我们会尽快为您处理(人工客服工作时间:9:00-18:30)。
关于实现400台套产能报告
在这120多天的车间管理过程中,让我更进一步了解到周密的工作计划对
工作指导的重要性。
为了全面完成400/月台套以上的产量及各项工作指标,实
现轻伤以上事故为零;根据我们农机目前的生产情况,我主要从以下几个方面
分析问题:
一、数字分析。
1、各部装现场实测产量记录表I
2、部装实际操作分析
①割台部装:共有25 个零件需要装配,其中4LBA02-0331001左调节盒、
4LBA02-0349300防草圈焊件、4LBA02-0310000机壳总成、4LBA02-0333002梳
脱带等需要打磨装配;平均每台打磨耗费时间大概为62 分钟。
②分禾器部装:共有37 个零件需要装配,主要部件4LBA02-04091208支杆焊件I、连接板与送
禾轮间隙不符合图纸要求需要打磨装配;平均每台套打磨耗费时间大概为30分钟。
③操作架体:共有90 多个零件需要装配,其中4LBA02-0752000g面板焊件与
4LBA02-0750008h操作台前罩、4LBA02-0762000f座位支架与4LBA02-0760002e座椅罩子等需要打磨配装;平均每台打磨耗费时间大概为24分钟。
3、岗位工位器具、工具、工装等满足不了工作需要。
如割头部装标准件有17 种,其中有42 颗螺钉需要拧紧如果用气动板手装配速度会提高原来的2倍以上;某些零部件需要专用的工位器具来存放如提升螺旋、出谷螺旋、二次脱粒滚筒等。
二、现场生产情况
1、本岗位装配人员的技术知识不够硬,装配工艺不完善,缺少岗位作业指导书,无法统一装配工序标准。
2、生产连续性和节奏性差,不论外协还是内部提供都缺乏成套作业,若某一环节出了问题就会造成停工形成内部物流的堵塞,在相同时间间隔内不能提供生产数量相同的产品,不能均衡地完成生产,经常出现时松时紧或某一环节松散现象。
3、生产节奏太慢,主要是整机无法定型,工艺不够明确,精准,造成产量居下不上。
4、员工的积极性和主动性比较消极,主要是车间生产计划执行力度不够,整体规划缺乏周密,要一样做一样,想要什么就下什么,导致操作人员工作心情烦躁。
5、生产链不能实现一环扣一环,部门对接经常脱节,主要是生产环节控制监督不力。
6、车间没有真正实现流水线作业,造成员工容易钻空子;员工缺少专业培训。
8、职责不分明,一个人不可能实现无边界作业,一个公司有可能实施无边界化管理,但这种管理方式就会使一些人过于依赖另一个人来完成自己的职责,没有明确的分工就不会有正规化的管理,弄得一些人飞不飞,落不落,自己的事情没有处理好,相关的事情又出现了。
9、配送物料不按时,导致安排的工作易混乱,白天活少,晚上还得加班。
三、自身管理问题。
我总是急急忙忙地处理一些日常性的杂事以及别的组别或部门的生产协调工作。
在车间管理方面我不得不承认我是一个失败者,因为:1、车间管理实际上注重一个“检”字,多“检查、监督”,其关键在于动态管理。
随时了解各车间生产进度和完成情况,当时我只注重现场零件装配问题的处理。
2、生产安排没有严密的计划性和监督性,使带班人员不知道自己的工作量和完成时间。
车间管理混乱分析其原因和结果,其责任主要在我的身上,因为几个月以来我对生产管理就有所松懈,对其他管理人员存在一种依赖,觉得安排好工作和反馈一些意见就可以了,从而导致被动的局面。
3、差不多用了三个月时间来处理人际关系,使得车间管理人员彻底服从我的安排;导致前面工作非常被动,工作又无法做好。
针对以上情况,我认为要想真正实现月产量400台套以上必须切实抓好以
下工作,确保全年生产经营任务的完成:
一、车间基础管理工作方面:
1、继续发扬职工强烈的责任意识、系统思考意识、拼搏奉献意识和创新意识,
用先进的理念统一全车间职工的思想,在“严细实”上下功夫,做到高标准、
严要求、行动快。
车间要做到这一点必须有一套完整的产品质量检验标准。
2、进一步完善优胜劣汰,完善竞争激励机制,在分配制度上拉开档次,对贡献大、特别是在某项指标上有所突破的人进行重奖。
要做到“下一道工序就上一道工
序的顾客”,其意思就是阐述了生产现场上下工序的衔接的重要性,每个岗位的工作内容不同,与之对应的岗位职责就不尽相同。
车间要做到这一点必须有一
套完整的作业指导书、实现工时或计件工资及相应的考核制度。
3、车间人员定额:方案一,按目前的生产状况由现场实测产量记录表I分析;如割台2人一组平均每台套需要4个小时,即是每天上班时间按11小时计算就有每组:11/4=2.7台/天,那么割台部装要达到15台套/天;还要补充6人。
由此推算装配车间还要增加20人,共79人执行两班制。
方案二,实现计算机化管理,完善生产网络流程、工艺流程和设备,建立了高效快捷的生产流水线,实现三分钟一台,装配车间应达到200人左右。
4、岗位配套设施:
5、成立配送中心。
在车间建立了配送中心,按时按量按需按台供应配件,畅通了工厂内部物流系统,减少了因配件供应问题而产生的时间损耗、推诿扯皮等现象,提高生产效率。
6、上班执行打卡制度,建全车间组织机构;做到事事有人管,日事日清的管理。
7、每月进行1-2次员工作业指导标准化知识培训,由质量部和工艺部负责。
8、严控不合格零件流入装配岗位和监督生产进度及控制,做到每天一小报每周一例会,随时把握生产进度。
5、起动现有的车间生产流水线作业来提高装配效率。
6、车间主任应有人事提拔和降职的权力。
二、质量工作方面:
1、坚持做好“人人都是质检员”,通过全员在线产品质量控制逐步减少缺陷产品,特别是对公司形象、品牌形象影响较坏的质量问题,进行认真整改。
2、开展质量优胜机组评比活动,稳步提高在线质量管理水平和质量控制水平。
3、加强学习,进一步强化装配工艺意识,坚定不渝的把质量工作摆在管理和生产工作的首位。
加强对工作责任的理解,将智能劳动应用到工作中的每一件事情上,学习质量控制的相关办法,提高对质量缺陷的判定能力。
4、强化在线产品质量控制办法和方案,落实岗位自检频率及自检力度。
进一步观察质量监控点上存在的问题,透过现场的生产工作寻找问题原因的根本,不断分析总结,不断整改完善。
5、加强岗位人员之间的沟通,注重岗位人员的协调配合。
注重员工技能水平的提高和良好操作习惯的形成,为保证产品质量打下坚实的基础。
三、完善作业流程标准。
总体说来,在这四个多月的工作和学习中,使我清楚的认识到公司管理人员、技术人员的岗位责任制的重要性。