典型轴类零件加工工艺分析修订版
轴类零件的加工工艺及技术要求
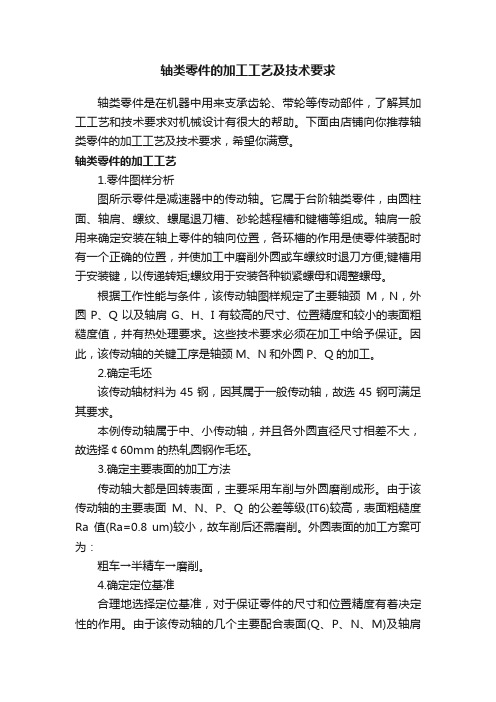
轴类零件的加工工艺及技术要求轴类零件是在机器中用来支承齿轮、带轮等传动部件,了解其加工工艺和技术要求对机械设计有很大的帮助。
下面由店铺向你推荐轴类零件的加工工艺及技术要求,希望你满意。
轴类零件的加工工艺1.零件图样分析图所示零件是减速器中的传动轴。
它属于台阶轴类零件,由圆柱面、轴肩、螺纹、螺尾退刀槽、砂轮越程槽和键槽等组成。
轴肩一般用来确定安装在轴上零件的轴向位置,各环槽的作用是使零件装配时有一个正确的位置,并使加工中磨削外圆或车螺纹时退刀方便;键槽用于安装键,以传递转矩;螺纹用于安装各种锁紧螺母和调整螺母。
根据工作性能与条件,该传动轴图样规定了主要轴颈M,N,外圆P、Q以及轴肩G、H、I有较高的尺寸、位置精度和较小的表面粗糙度值,并有热处理要求。
这些技术要求必须在加工中给予保证。
因此,该传动轴的关键工序是轴颈M、N和外圆P、Q的加工。
2.确定毛坯该传动轴材料为45钢,因其属于一般传动轴,故选45钢可满足其要求。
本例传动轴属于中、小传动轴,并且各外圆直径尺寸相差不大,故选择¢60mm的热轧圆钢作毛坯。
3.确定主要表面的加工方法传动轴大都是回转表面,主要采用车削与外圆磨削成形。
由于该传动轴的主要表面M、N、P、Q的公差等级(IT6)较高,表面粗糙度Ra值(Ra=0.8 um)较小,故车削后还需磨削。
外圆表面的加工方案可为:粗车→半精车→磨削。
4.确定定位基准合理地选择定位基准,对于保证零件的尺寸和位置精度有着决定性的作用。
由于该传动轴的几个主要配合表面(Q、P、N、M)及轴肩面(H、G)对基准轴线A-B均有径向圆跳动和端面圆跳动的要求,它又是实心轴,所以应选择两端中心孔为基准,采用双顶尖装夹方法,以保证零件的技术要求。
粗基准采用热轧圆钢的毛坯外圆。
中心孔加工采用三爪自定心卡盘装夹热轧圆钢的毛坯外圆,车端面、钻中心孔。
但必须注意,一般不能用毛坯外圆装夹两次钻两端中心孔,而应该以毛坯外圆作粗基准,先加工一个端面,钻中心孔,车出一端外圆;然后以已车过的外圆作基准,用三爪自定心卡盘装夹(有时在上工步已车外圆处搭中心架),车另一端面,钻中心孔。
典型零件加工工艺分析

套筒类零件的安装
§6.2.3 套类零件孔的加工方法
套类零件的孔加工方法常用的有:钻孔、扩孔、 镗孔、车孔、铰孔、磨孔、拉孔、珩孔、研磨孔 及孔表面滚压加工。其中钻孔、扩孔、镗孔、车 孔常作为粗加工与半精加工;而铰孔、磨孔、拉 孔、珩孔、研磨孔及孔表面滚压加工作为精加工 方法。
1. 磨孔 内圆磨削具有以下特点:
(1) 孔与外圆的精度要求。 (2) 几何形状精度要求。 (3) 相互位置精度要求。
3、套筒类零件的材料及毛坯
材料 套类零件一般用钢、铸铁、青铜、黄铜制成。有 些滑动轴承可选用双金属结构,对一些强度和硬度要求 较高的套类零件(如镗床主轴套筒、伺服阀套),可选用 优质合金钢(38CrMoALA、18CrNiWA)。
深孔钻削
深孔镗削
浮动镗孔
深孔加工
精细镗孔 珩磨内孔 内孔研磨 滚压孔
精加工
§6.3 齿轮加工
§6.3.1 概述
齿轮的功用
圆柱齿轮是机械传动中的重要零件,其功用是按规 定的传动比传递运动和动力。它具有传动比准确、 传动力大、效率高、结构紧凑、可靠性好等优点, 广泛应用于各种现代机器和仪表中。
圆柱齿轮的结构与分类
• 圆柱齿轮可以看成由齿圈和轮体两部分所构成,
在轮圈上切出直齿、斜齿或人字齿(图6-9)等就 形成了齿轮。 • 按齿形曲线性质可分为渐开线、摆线、鼓形和圆 弧等。 • 齿轮的结构分类常以轮体结构的形状为依据,即 可分为单联齿轮、双联齿轮、三联齿轮、连轴齿轮、 内齿轮、装配齿轮、齿条及扇形齿轮等(图6-10)
图c) • 4 以顶尖孔安装——顶尖孔定心、定位。图d)
图6-12 齿形加工安装实例
• 二 齿坯的加工方式 • 1 内孔安装 控制端面跳动与内径公差。
轴类零件的数控加工工艺编制及分析
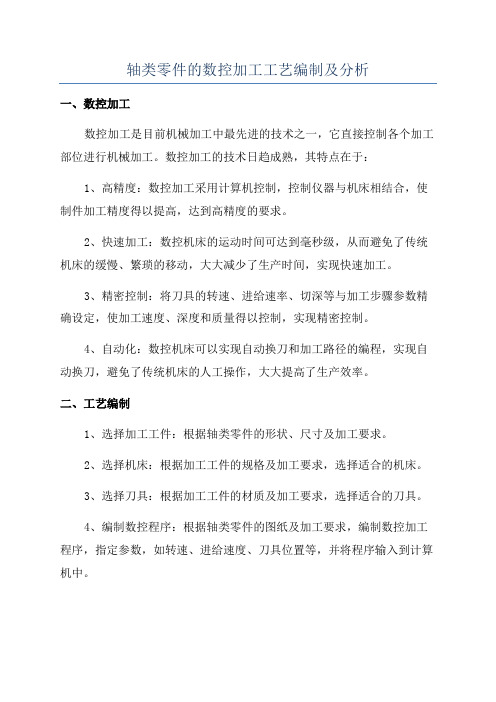
轴类零件的数控加工工艺编制及分析
一、数控加工
数控加工是目前机械加工中最先进的技术之一,它直接控制各个加工部位进行机械加工。
数控加工的技术日趋成熟,其特点在于:
1、高精度:数控加工采用计算机控制,控制仪器与机床相结合,使制件加工精度得以提高,达到高精度的要求。
2、快速加工:数控机床的运动时间可达到毫秒级,从而避免了传统机床的缓慢、繁琐的移动,大大减少了生产时间,实现快速加工。
3、精密控制:将刀具的转速、进给速率、切深等与加工步骤参数精确设定,使加工速度、深度和质量得以控制,实现精密控制。
4、自动化:数控机床可以实现自动换刀和加工路径的编程,实现自动换刀,避免了传统机床的人工操作,大大提高了生产效率。
二、工艺编制
1、选择加工工件:根据轴类零件的形状、尺寸及加工要求。
2、选择机床:根据加工工件的规格及加工要求,选择适合的机床。
3、选择刀具:根据加工工件的材质及加工要求,选择适合的刀具。
4、编制数控程序:根据轴类零件的图纸及加工要求,编制数控加工程序,指定参数,如转速、进给速度、刀具位置等,并将程序输入到计算机中。
典型轴类零件图纸工艺分析及数控车加工艺制订

典型轴类零件图纸工艺分析及数控车加工艺制订典型轴类零件如图所示,零件材料为45钢,无热处理和硬度要求,试对该零件进行数控车削工艺分析。
(1)零件图工艺分析该零件表面由圆柱、圆锥、顺圆弧、逆圆弧及螺纹等表面组成。
其中多个直径尺寸有较严的尺寸精度和表面粗糙度等要求;球面Sφ50㎜的尺寸公差还兼有控制该球面形状(线轮廓)误差的作用。
尺寸标注完整,轮廓描述清楚。
零件材料为45钢,无热处理和硬度要求。
通过上述分析,可采用以下几点工艺措施。
①对图样上给定的几个精度要求较高的尺寸,因其公差数值较小,故编程时不必取平均值,而全部取其基本尺寸即可。
②在轮廓曲线上,有三处为圆弧,其中两处为既过象限又改变进给方向的轮廓曲线,因此在加工时应进行机械间隙补偿,以保证轮廓曲线的准确性。
③为便于装夹,坯件左端应预先车出夹持部分(双点画线部分),右端面也应先粗车出并钻好中心孔。
毛坯选φ60㎜棒料。
(2)选择设备根据被加工零件的外形和材料等条件,选用TND360数控车床。
(3)确定零件的定位基准和装夹方式①定位基准确定坯料轴线和左端大端面(设计基准)为定位基准。
②装夹方法左端采用三爪自定心卡盘定心夹紧,右端采用活动顶尖支承的装夹方式。
(4)确定加工顺序及进给路线加工顺序按由粗到精、由近到远(由右到左)的原则确定。
即先从右到左进行粗车(留0.25㎜精车余量),然后从右到左进行精车,最后车削螺纹。
TND360数控车床具有粗车循环和车螺纹循环功能,只要正确使用编程指令,机床数控系统就会自动确定其进给路线,因此,该零件的粗车循环和车螺纹循环不需要人为确定其进给路线(但精车的进给路线需要人为确定)。
该零件从右到左沿零件表面轮廓精车进给,如所示。
5)刀具选择①选用φ5㎜中心钻钻削中心孔。
②粗车及平端面选用900硬质合金右偏刀,为防止副后刀面与工件轮廓干涉(可用作图法检验),副偏角不宜太小,选κ=350。
③精车选用900硬质合金右偏刀,车螺纹选用硬质合金600外螺纹车刀,刀尖圆弧半径应小于轮廓最小圆角半径,取rε=0.15~0.2㎜。
典型轴类零件加工实用工艺分析报告
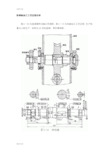
阶梯轴加工工艺过程分析图6—34为减速箱传动轴工作图样。
表6—13为该轴加工工艺过程。
生产批量为小批生产。
材料为45热轧圆钢。
零件需调质。
(一)结构及技术条件分析该轴为没有中心通孔的多阶梯轴。
根据该零件工作图,其轴颈M、N,外圆P,Q及轴肩G、H、I有较高的尺寸精度和形状位置精度,并有较小的表面粗糙度值,该轴有调质热处理要求。
(二)加工工艺过程分析1.确定主要表面加工方法和加工方案。
传动轴大多是回转表面,主要是采用车削和外圆磨削。
由于该轴主要表面M,N,P,Q的公差等级较高(IT6),表面粗糙度值较小(Ra0.8μm),最终加工应采用磨削。
其加工方案可参考表3-14。
2.划分加工阶段该轴加工划分为三个加工阶段,即粗车(粗车外圆、钻中心孔),半精车(半精车各处外圆、台肩和修研中心孔等),粗精磨各处外圆。
各加工阶段大致以热处理为界。
3.选择定位基准轴类零件的定位基面,最常用的是两中心孔。
因为轴类零件各外圆表面、螺纹表面的同轴度及端面对轴线的垂直度是相互位置精度的主要项目,而这些表面的设计基准一般都是轴的中心线,采用两中心孔定位就能符合基准重合原则。
而且由于多数工序都采用中心孔作为定位基面,能最大限度地加工出多个外圆和端面,这也符合基准统一原则。
但下列情况不能用两中心孔作为定位基面:(1)粗加工外圆时,为提高工件刚度,则采用轴外圆表面为定位基面,或以外圆和中心孔同作定位基面,即一夹一顶。
(2)当轴为通孔零件时,在加工过程中,作为定位基面的中心孔因钻出通孔而消失。
为了在通孔加工后还能用中心孔作为定位基面,工艺上常采用三种方法。
①当中心通孔直径较小时,可直接在孔口倒出宽度不大于2mm的60o内锥面来代替中心孔;②当轴有圆柱孔时,可采用图6—35a所示的锥堵,取1∶500锥度;当轴孔锥度较小时,取锥堵锥度与工件两端定位孔锥度相同;③当轴通孔的锥度较大时,可采用带锥堵的心轴,简称锥堵心轴,如图6—35b所示。
典型轴类零件的数控加工工艺设计(doc 29页)

典型轴类零件的数控加工工艺设计(doc 29页)摘要数控技术是用数字信息对机械运动和工作过程进行控制的技术,数控装备是以数控技术为代表的新技术对传统制造产业和新兴制造的渗透形成的机电一体化产品,即所谓的数字化装备。
本次设计就是进行数控加工工艺设计典型轴类零件,主要侧重于该零件的数控加工工艺和编程,包括完成该零件的工艺规程,主要工序工装设计,并绘制零件图、夹具图等。
通过本次毕业设计,对典型轴类零件的设计又有了深的认识。
从而达到了巩固、扩大、深化所学知识的目的,培养和提高了综合分析问题和解决问题的能力以及培养了科学的研究和创新能力。
关键词:数控技术典型轴类零件加工工艺毕业设计1.引言数控技术集传统的机械制造技术、计算机技术、成组技术与现代控制技术、传感检测技术、信息处理技术、网络通讯技术、液压气动技术、光机电技术于一体,是现代先进制造技术的基础和核心。
数控车床己经成为现代企业的必需品。
随着数控技术的不断成熟和发展及市场日益繁荣,其竞争也越来越激烈,人们对数控车床选择也有了更加广阔的范围,对数控机床技术的掌握也越来越高。
随着社会经济的快速发展,人们对生活用品的要求也越来越高,企业对生产效率也有相应的提高。
数控机床的出现实现了广大人们的这一愿望。
数控车削加工工艺是实现产品设计、保证产品的质量、保证零件的精度,节约能源、降低消耗的重要手段。
是企业进行生产准备、计划调度、加工操作、安全生产、技术检测和健全劳动组织的重要依据。
也是企业对高品质、高品种、高水平,加速产品更新,提高经济效益的技术保证。
这不但满足了广大消费者的目的,即实现了产品多样化、产品高质量、更新速度快的要求,同时推动了企业的快速发展,提高了企业的生产效率。
数控工艺规程的编制是直接指导产品或零件制造工艺过程和操作方法的工艺文件,它将直接影响企业产品质量、效益、竞争能力。
本文通过对典型轴类零件数控加工工艺的分析,对零件进行编程加工,给出了对于典型零件数控加工工艺分析的方法,对于提高制造质量、实际生产具有一定的意义。
轴类零件的加工工艺
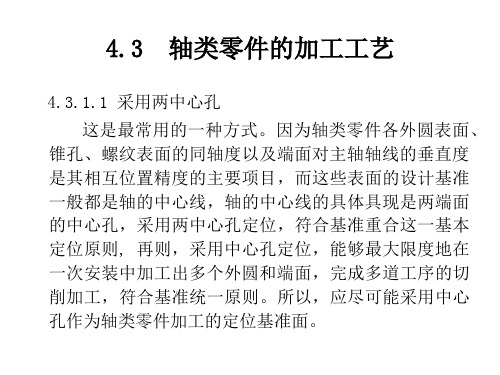
4.3.1.1 采用两中心孔 这是最常用的一种方式。因为轴类零件各外圆表面、
锥孔、螺纹表面的同轴度以及端面对主轴轴线的垂直度 是其相互位置精度的主要项目,而这些表面的设计基准 一般都是轴的中心线,轴的中心线的具体具现是两端面 的中心孔,采用两中心孔定位,符合基准重合这一基本 定位原则, 再则,采用中心孔定位,能够最大限度地在 一次安装中加工出多个外圆和端面,完成多道工序的切 削加工,符合基准统一原则。所以,应尽可能采用中心 孔作为轴类零件加工的定位基准面。
4.3 轴类零件的加工工艺
4.3.1.2 采用外圆表面 当加工较粗、较长的轴类零件 ,或为了在粗加工
阶段实现强力切削,则采用轴的外圆表面作为定位基准 面,或是以外圆和中心孔同时作为定位基准面,其目的 是为了提高工件刚度和加工生产率。 4.3.1.3 采用锥堵或锥堵心轴
当工件为通孔轴类零件时,工艺上采用带有中心孔 的锥堵(闷头)或锥堵心轴定位,如图4-34所示。当轴 孔的锥度比较小时,(如某车床的主轴锥孔分别为1: 20和莫氏6号锥度),可使用锥堵;当锥孔的锥度较大 或圆柱孔时,则用带锥堵的锥堵心轴。
4.3 轴类零件的加工工艺
⑴ 用右、左偏刀(90º主偏角)车削端面 右偏刀适于车削带有台阶和端面的工件,如一般的 轴和直径较小的端面。通常情况下,偏刀由外向中心走 刀车端面时,是由副刀刃进行切削的,如果背吃刀量较 大,向里的切削力会使车刀扎入工件,而形成凹面,如 图4-36(a)所示。当然也可反向切削,从中心向外走 刀,利用主切削刃进行切削,则不易产生凹面,如图436(b)所示。切削余量较大时,可用如图4-36(c)所 示的端面车刀车削。 在精车端面时,一般用偏刀由外向中心进刀(背吃 刀量要很小),因为这时切屑是流向待加工表面的,故
数控加工工艺大作业典型轴类零件的数控加工工艺设计.doc

目录1.零件图工艺分析2设备选择3确定零件的定位基准和装夹方式4确定加工顺序及进给路线5刀具的选择6确定切削用量7填写数控加工工艺文件轴类零件的数控加工工艺的编制及加工图1.零件图工艺分析零件车削工艺分析如图1-1所示,零件材料处理为:45钢,下面对该零件进行数控车削工艺分析。
零件如图:图1-1 零件图1.1数控加工工艺基本特点数控机床加工工艺与普通机床加工原则上基本相同,但数控机床是自动进行加工,因而有如下特点:①数控加工的工序内容比普通机床的加工内容复杂,加工的精度高,加工的表面质量高,加工的内容较丰富。
②数控机床加工程序的编制比普通机床工艺编制要复杂些。
这是因为数控机床加工存在对刀、换刀以及退刀等特点,这都无一例外的变成程序内容,正是由于这个特点,促使对加工程序正确性和合理性要求极高,不能有丝毫的差错。
否则加工不出合格的零件。
在编程前我们一定要对零件进行工艺分析,这是必不可少的一步,如图1-1我要对该零件进行精度分析,选择加工方法、拟定加工方案、选择合理的刀具、确定切削用量。
该零件由螺纹、圆柱、圆锥、圆弧等表面组成。
可控制球面形状精度、30°的锥度等要求。
经上面的分析,我可以采用以下工艺措施:(1)为便于装夹,为了保证工件的定位准确、稳定,夹紧方面可靠,支撑面积较大,零件的左端是最大直径圆柱ф85mm,中段的圆柱ф80mm。
右端是螺纹,应先装夹毛坯加工出左端圆弧及圆柱ф85mm、ф80mm调头装夹ф80mm的圆柱加工右端螺纹、圆柱及锥面,毛坯选ф85×350mm。
1.2设备选择根据该零件的外形是轴类零件,只有在数控车床上加工才能保证其加工的尺寸精度和表面质量。
我选择在本校的数控机床HNC-CK6140加工该零件。
1.3确定零件的定位基准和装夹方式1.3.1粗基准选择原则(1)为了保证不加工表面与加工表面之间的位置要求,应选不加工表面作粗基准。
(2)合理分配各加工表面的余量,应选择毛坯外圆作粗基准。
- 1、下载文档前请自行甄别文档内容的完整性,平台不提供额外的编辑、内容补充、找答案等附加服务。
- 2、"仅部分预览"的文档,不可在线预览部分如存在完整性等问题,可反馈申请退款(可完整预览的文档不适用该条件!)。
- 3、如文档侵犯您的权益,请联系客服反馈,我们会尽快为您处理(人工客服工作时间:9:00-18:30)。
典型轴类零件加工工艺分析集团标准化小组:[VVOPPT-JOPP28-JPPTL98-LOPPNN]阶梯轴加工工艺过程分析图6—34为减速箱传动轴工作图样。
表6—13为该轴加工工艺过程。
生产批量为小批生产。
材料为45热轧圆钢。
零件需调质。
(一)结构及技术条件分析该轴为没有中心通孔的多阶梯轴。
根据该零件工作图,其轴颈M、N,外圆P,Q及轴肩G、H、I有较高的尺寸精度和形状位置精度,并有较小的表面粗糙度值,该轴有调质热处理要求。
(二)加工工艺过程分析1.确定主要表面加工方法和加工方案。
传动轴大多是回转表面,主要是采用车削和外圆磨削。
由于该轴主要表面M,N,P,Q的公差等级较高(IT6),表面粗糙度值较小(Ra0.8μm),最终加工应采用磨削。
其加工方案可参考表3-14。
2.划分加工阶段该轴加工划分为三个加工阶段,即粗车(粗车外圆、钻中心孔),半精车(半精车各处外圆、台肩和修研中心孔等),粗精磨各处外圆。
各加工阶段大致以热处理为界。
3.选择定位基准轴类零件的定位基面,最常用的是两中心孔。
因为轴类零件各外圆表面、螺纹表面的同轴度及端面对轴线的垂直度是相互位置精度的主要项目,而这些表面的设计基准一般都是轴的中心线,采用两中心孔定位就能符合基准重合原则。
而且由于多数工序都采用中心孔作为定位基面,能最大限度地加工出多个外圆和端面,这也符合基准统一原则。
但下列情况不能用两中心孔作为定位基面:(1)粗加工外圆时,为提高工件刚度,则采用轴外圆表面为定位基面,或以外圆和中心孔同作定位基面,即一夹一顶。
(2)当轴为通孔零件时,在加工过程中,作为定位基面的中心孔因钻出通孔而消失。
为了在通孔加工后还能用中心孔作为定位基面,工艺上常采用三种方法。
①当中心通孔直径较小时,可直接在孔口倒出宽度不大于2mm的60o内锥面来代替中心孔;②当轴有圆柱孔时,可采用图6—35a所示的锥堵,取1∶500锥度;当轴孔锥度较小时,取锥堵锥度与工件两端定位孔锥度相同;③当轴通孔的锥度较大时,可采用带锥堵的心轴,简称锥堵心轴,如图6—35b所示。
使用锥堵或锥堵心轴时应注意,一般中途不得更换或拆卸,直到精加工完各处加工面,不再使用中心孔时方能拆卸。
4.热处理工序的安排该轴需进行调质处理。
它应放在粗加工后,半精加工前进行。
如采用锻件毛坯,必须首先安排退火或正火处理。
该轴毛坯为热轧钢,可不必进行正火处理。
5.加工顺序安排除了应遵循加工顺序安排的一般原则,如先粗后精、先主后次等,还应注意:(1)外圆表面加工顺序应为,先加工大直径外圆,然后再加工小直径外圆,以免一开始就降低了工件的刚度。
(2)轴上的花键、键槽等表面的加工应在外圆精车或粗磨之后,精磨外圆之前。
轴上矩形花键的加工,通常采用铣削和磨削加工,产量大时常用花键滚刀在花键铣床上加工。
以外径定心的花键轴,通常只磨削外径,而内径铣出后不必进行磨削,但如经过淬火而使花键扭曲变形过大时,也要对侧面进行磨削加工。
以内径定心的花键,其内径和键侧均需进行磨削加工。
(3)轴上的螺纹一般有较高的精度,如安排在局部淬火之前进行加工,则淬火后产生的变形会影响螺纹的精度。
因此螺纹加工宜安排在工件局部淬火之后进行。
二、带轮轴加工工艺过程分析图 6 — 36 为带轮轴工作图样。
带轮轴中的主要技术条件有两项:一为渗碳层深度,应控制在 1.2— 1.5 mm 范围内;二为外圆¢ 22 f 7 需经渗碳淬火,其硬度为 HRC58 ~ 63 。
可以看出只有¢ 22 f 7 处需渗碳处理,其余部分均不可渗碳。
零件上不需渗碳的部分,可用加大余量待渗碳后车去渗碳层或在不需渗碳处涂防渗材料。
加工余量应单面略大于渗碳深度,故右端直径取¢ 25 mm ,单面去碳余量为 2.5 mm ,总长两端也应放去渗碳余量各 3 mm 。
在磨外圆前由于已经过淬火工序,两端中心孔在淬火时易产生氧化皮及变形,故增加一道研磨中心孔的工序。
表 6 — 14 为带轮轴的加工工艺过程。
三、细长轴加工工艺特点(一)细长轴车削的工艺特点1 .细长轴刚性很差,车削时装夹不当,很容易因切削力及重力的作用而发生弯曲变形,产生振动,从而影响加工精度和表面粗糙度。
2 .细长轴的热扩散性能差,在切削热作用下,会产生相当大的线膨胀。
如果轴的两端为固定支承,则工件会因伸长而顶弯。
3 .由于轴较长,一次走刀时间长,刀具磨损大,从而影响零件的几何形状精度。
4 .车细长轴时由于使用跟刀架,若支承工件的两个支承块对零件压力不适当,会影响加工精度。
若压力过小或不接触,就不起作用,不能提高零件的刚度;若压力过大,零件被压向车刀,切削深度增加,车出的直径就小,当跟刀架继续移动后,支承块支承在小直径外圆处,支承块与工件脱离,切削力使工件向外让开,切削深度减小,车出的直径变大,以后跟刀架又跟到大直径圆上,又把工件压向车刀,使车出的直径变小,这样连续有规律的变化,就会把细长的工件车成“竹节”形,如图 6 — 37 所示。
(二)细长轴的先进车削法——反向走刀车削法图 6––38 为反向走刀车削法示意图,这种方法的特点是:1 .细长轴左端缠有一圈钢丝,利用三爪自定心卡盘夹紧,减小接触面积,使工件在卡盘内能自由地调节其位置,避免夹紧时形成弯曲力矩,在切削过程中发生的变形也不会因卡盘夹死而产生内应力。
2 .尾座顶尖改成弹性顶尖,当工件因切削热发生线膨胀伸长时,顶尖能自动后退,可避免热膨胀引起的弯曲变形。
3 .采用三个支承块跟刀架,以提高工件刚性和轴线的稳定性,避免“竹节”形。
4 .改变走刀方向,使床鞍由主轴箱向尾座移动,使工件受拉,不易产生弹性弯曲变形。
轴类零件加工工艺传动轴机械加工工艺实例轴类零件是常见的典型零件之一。
按轴类零件结构形式不同,一般可分为光轴、阶梯轴和异形轴三类;或分为实心轴、空心轴等。
它们在机器中用来支承齿轮、带轮等传动零件,以传递转矩或运动。
台阶轴的加工工艺较为典型,反映了轴类零件加工的大部分内容与基本规律。
下面就以减速箱中的传动轴为例,介绍一般台阶轴的加工工艺。
1.零件图样分析图A-1 传动轴图A-1所示零件是减速器中的传动轴。
它属于台阶轴类零件,由圆柱面、轴肩、螺纹、螺尾退刀槽、砂轮越程槽和键槽等组成。
轴肩一般用来确定安装在轴上零件的轴向位置,各环槽的作用是使零件装配时有一个正确的位置,并使加工中磨削外圆或车螺纹时退刀方便;键槽用于安装键,以传递转矩;螺纹用于安装各种锁紧螺母和调整螺母。
根据工作性能与条件,该传动轴图样(图A-1)规定了主要轴颈M,N,外圆P、Q以及轴肩G、H、I有较高的尺寸、位置精度和较小的表面粗糙度值,并有热处理要求。
这些技术要求必须在加工中给予保证。
因此,该传动轴的关键工序是轴颈M、N和外圆P、Q的加工。
2.确定毛坯该传动轴材料为45钢,因其属于一般传动轴,故选45钢可满足其要求。
本例传动轴属于中、小传动轴,并且各外圆直径尺寸相差不大,故选择¢60mm的热轧圆钢作毛坯。
3.确定主要表面的加工方法传动轴大都是回转表面,主要采用车削与外圆磨削成形。
由于该传动轴的主要表面M、N、P、Q的公差等级(IT6)较高,表面粗糙度Ra值(Ra=0.8 um)较小,故车削后还需磨削。
外圆表面的加工方案(参考表A-3)可为:粗车→半精车→磨削。
4.确定定位基准合理地选择定位基准,对于保证零件的尺寸和位置精度有着决定性的作用。
由于该传动轴的几个主要配合表面(Q、P、N、M)及轴肩面(H、G)对基准轴线A-B均有径向圆跳动和端面圆跳动的要求,它又是实心轴,所以应选择两端中心孔为基准,采用双顶尖装夹方法,以保证零件的技术要求。
粗基准采用热轧圆钢的毛坯外圆。
中心孔加工采用三爪自定心卡盘装夹热轧圆钢的毛坯外圆,车端面、钻中心孔。
但必须注意,一般不能用毛坯外圆装夹两次钻两端中心孔,而应该以毛坯外圆作粗基准,先加工一个端面,钻中心孔,车出一端外圆;然后以已车过的外圆作基准,用三爪自定心卡盘装夹(有时在上工步已车外圆处搭中心架),车另一端面,钻中心孔。
如此加工中心孔,才能保证两中心孔同轴。
5.划分阶段对精度要求较高的零件,其粗、精加工应分开,以保证零件的质量。
该传动轴加工划分为三个阶段:粗车(粗车外圆、钻中心孔等),半精车(半精车各处外圆、台阶和修研中心孔及次要表面等),粗、精磨(粗、精磨各处外圆)。
各阶段划分大致以热处理为界。
6.热处理工序安排轴的热处理要根据其材料和使用要求确定。
对于传动轴,正火、调质和表面淬火用得较多。
该轴要求调质处理,并安排在粗车各外圆之后,半精车各外圆之前。
综合上述分析,传动轴的工艺路线如下:下料→车两端面,钻中心孔→粗车各外圆→调质→修研中心孔→半精车各外圆,车槽,倒角→车螺纹→划键槽加工线→铣键槽→修研中心孔→磨削→检验。
7.加工尺寸和切削用量传动轴磨削余量可取0.5mm,半精车余量可选用1.5mm。
加工尺寸可由此而定,见该轴加工工艺卡的工序内容。
车削用量的选择,单件、小批量生产时,可根据加工情况由工人确定;一般可由《机械加工工艺手册》或《切削用量手册》中选取。
8.拟定工艺过程定位精基准面中心孔应在粗加工之前加工,在调质之后和磨削之前各需安排一次修研中心孔的工序。
调质之后修研中心孔为消除中心孔的热处理变形和氧化皮,磨削之前修研中心孔是为提高定位精基准面的精度和减小锥面的表面粗糙度值。
拟定传动轴的工艺过程时,在考虑主要表面加工的同时,还要考虑次要表面的加工。
在半精加工¢52mm、¢44mm及M24mm外圆时,应车到图样规定的尺寸,同时加工出各退刀槽、倒角和螺纹;三个键槽应在半精车后以及磨削之前铣削加工出来,这样可保证铣键槽时有较精确的定位基准,又可避免在精磨后铣键槽时破坏已精加工的外圆表面。
在拟定工艺过程时,应考虑检验工序的安排、检查项目及检验方法的确定。
综上所述,所确定的该传动轴加工工艺过程见表A-1。