第三章_玻璃的熔制及成型
3 玻璃的熔制及熔(1)讲解

(5)玻璃液冷却阶段 将清澄和均化了的玻璃液均匀降温,使玻璃 液具有成型所需的黏度; 在冷却阶段应不破坏玻璃液的质量; 浮法玻璃冷却阶段结束的温度在1100~ 1050℃左右。
3.1.1 配合料的熔化
(1)配合料的加热及初熔 (2)各种反应简介 多晶转变 盐类分解 水分的逸出 (3)成分的挥发 R2O的挥发 由纯碱引入时:引入量×0.032% 由芒硝引入时:引入量×0.06%
3.1.3 澄清
(1)目的 消除玻璃液中的气泡 (2)玻璃液中的气泡形态和种类 形态:可见气泡、溶解气泡、化学结合的气 体。还有熔体表面上的气体。 种类: CO2、SO2、SO3、N2、O2、H2O、H2
(3) 排泡与去气 澄清是排出玻璃液中的可见气泡; 去气是全部排除玻璃液中的气体,包括化学 结合的气体。
B.二次气泡(灰泡,直径小于0.1mm) ①硫酸盐和其他盐类的继续分解; ②溶解气体的析出; ③耐火材料气泡 ④玻璃液流股间的化学反应; ⑤电化学反应
r=1mm时, 2σ/r =0.6kPa; r<0.01mm时, 2σ/r > 0.06MPa; R= 0.001mm时, 2σ/r= 0.6MPa。 可以看出,表面张力对大气泡的影响可以忽 略,对小气泡的影响则是巨大的。 玻璃液中存在的微小气泡,在温度降低时, 内部的压力急剧增大,使气泡内的气体分压 明显大于玻璃液中气体的分压,从而溶解于 玻璃液中;温度升高时,气泡又会析出。
B.新气泡的产生 澄清好的玻璃液一般不能再次产生气泡。 原因是: 新生气泡的半径r≈0,需要克服的
2σ/r≈∞。
(8)影响澄清的因素
A.配合料中的气体率 一般15~20% B.澄清温度 温度高,黏度小,有利于澄清;熔窑温度受 耐火材料的限制。 C.窑压 微正延长澄清时间 B.提高澄清温度 C.搅拌 D.鼓泡 E .加澄清剂(最常用)
玻璃的熔制过程
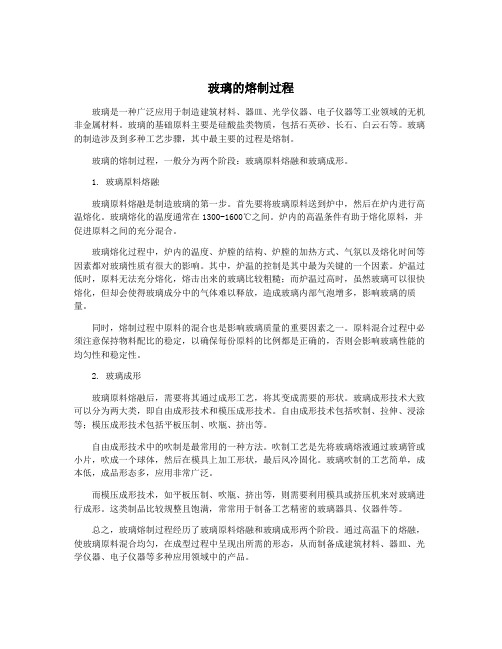
玻璃的熔制过程玻璃是一种广泛应用于制造建筑材料、器皿、光学仪器、电子仪器等工业领域的无机非金属材料。
玻璃的基础原料主要是硅酸盐类物质,包括石英砂、长石、白云石等。
玻璃的制造涉及到多种工艺步骤,其中最主要的过程是熔制。
玻璃的熔制过程,一般分为两个阶段:玻璃原料熔融和玻璃成形。
1. 玻璃原料熔融玻璃原料熔融是制造玻璃的第一步。
首先要将玻璃原料送到炉中,然后在炉内进行高温熔化。
玻璃熔化的温度通常在1300-1600℃之间。
炉内的高温条件有助于熔化原料,并促进原料之间的充分混合。
玻璃熔化过程中,炉内的温度、炉膛的结构、炉膛的加热方式、气氛以及熔化时间等因素都对玻璃性质有很大的影响。
其中,炉温的控制是其中最为关键的一个因素。
炉温过低时,原料无法充分熔化,熔击出来的玻璃比较粗糙;而炉温过高时,虽然玻璃可以很快熔化,但却会使得玻璃成分中的气体难以释放,造成玻璃内部气泡增多,影响玻璃的质量。
同时,熔制过程中原料的混合也是影响玻璃质量的重要因素之一。
原料混合过程中必须注意保持物料配比的稳定,以确保每份原料的比例都是正确的,否则会影响玻璃性能的均匀性和稳定性。
2. 玻璃成形玻璃原料熔融后,需要将其通过成形工艺,将其变成需要的形状。
玻璃成形技术大致可以分为两大类,即自由成形技术和模压成形技术。
自由成形技术包括吹制、拉伸、浸涂等;模压成形技术包括平板压制、吹瓶、挤出等。
自由成形技术中的吹制是最常用的一种方法。
吹制工艺是先将玻璃熔液通过玻璃管或小片,吹成一个球体,然后在模具上加工形状,最后风冷固化。
玻璃吹制的工艺简单,成本低,成品形态多,应用非常广泛。
而模压成形技术,如平板压制、吹瓶、挤出等,则需要利用模具或挤压机来对玻璃进行成形。
这类制品比较规整且饱满,常常用于制备工艺精密的玻璃器具、仪器件等。
总之,玻璃熔制过程经历了玻璃原料熔融和玻璃成形两个阶段。
通过高温下的熔融,使玻璃原料混合均匀,在成型过程中呈现出所需的形态,从而制备成建筑材料、器皿、光学仪器、电子仪器等多种应用领域中的产品。
玻璃生产过程(3篇)

第1篇一、引言玻璃是一种具有广泛应用领域的无机非金属材料,广泛应用于建筑、汽车、电子、光学、化工等领域。
玻璃的生产历史悠久,技术不断进步,如今已成为现代化工业的重要组成部分。
本文将详细介绍玻璃生产的过程,包括原料选择、熔化、成型、退火、检验等环节。
二、原料选择1. 纯碱(Na2CO3):纯碱是玻璃生产的主要原料之一,其主要作用是降低熔化温度,提高熔化速度,改善玻璃的化学稳定性。
2. 石灰石(CaCO3):石灰石在玻璃生产中起到稳定熔融玻璃的作用,可以减少玻璃中的铁、镁等有害成分,提高玻璃的透明度。
3. 硅砂(SiO2):硅砂是玻璃生产的主要原料,其含量决定了玻璃的化学成分,对玻璃的物理性能有重要影响。
4. 镁砂(MgO):镁砂可以提高玻璃的化学稳定性,降低热膨胀系数,提高玻璃的耐热冲击性能。
5. 铝土矿(Al2O3):铝土矿可以提高玻璃的化学稳定性,降低玻璃的软化温度,提高玻璃的耐热冲击性能。
6. 硼砂(B2O3):硼砂可以提高玻璃的化学稳定性,降低玻璃的热膨胀系数,提高玻璃的耐热冲击性能。
三、熔化1. 熔炉选择:根据玻璃的种类和生产规模,选择合适的熔炉。
常见的熔炉有池炉、窑炉、熔窑等。
2. 熔化过程:将选好的原料按照一定的比例进行混合,放入熔炉中加热熔化。
熔化过程中,熔炉内的温度控制在1200℃-1500℃之间,使原料充分熔化。
3. 混合:在熔化过程中,通过搅拌使熔融的玻璃充分混合,达到均匀的化学成分。
四、成型1. 拉丝法:将熔融的玻璃拉成细丝,经过冷却、拉伸、退火等工序,制成玻璃纤维。
2. 拉管法:将熔融的玻璃拉成管状,经过冷却、切割等工序,制成玻璃管。
3. 压延法:将熔融的玻璃压延成薄片,经过冷却、切割等工序,制成玻璃板。
4. 拉伸法:将熔融的玻璃拉伸成薄片,经过冷却、切割等工序,制成玻璃丝。
五、退火1. 退火目的:退火是为了消除玻璃内部的应力,提高玻璃的物理性能,如强度、耐热冲击性能等。
玻璃制造工艺(3篇)

第1篇一、引言玻璃是一种常见的无机非金属材料,具有透明、坚硬、耐高温、化学稳定性好等特点。
随着科技的不断发展,玻璃在建筑、汽车、电子、光学等领域得到了广泛应用。
本文将介绍玻璃制造工艺,包括原料的选择、熔制、成型、退火、切割、磨光、清洗等环节。
二、原料选择玻璃制造的原材料主要包括石英砂、纯碱、石灰石、长石等。
这些原料经过破碎、筛选、混合等过程,制备成合格的玻璃原料。
1. 石英砂:石英砂是玻璃制造的主要原料,占原料总量的70%左右。
它主要来源于天然的石英岩、石英砂岩等。
石英砂的化学成分主要是SiO2,具有较高的熔点和良好的化学稳定性。
2. 纯碱:纯碱是玻璃制造中的一种助熔剂,其主要成分是Na2CO3。
纯碱在玻璃制造过程中起到降低熔点和改善玻璃性质的作用。
3. 石灰石:石灰石是玻璃制造中的一种助熔剂,其主要成分是CaCO3。
石灰石在玻璃制造过程中起到降低熔点和提高玻璃化学稳定性的作用。
4. 长石:长石是玻璃制造中的一种原料,其主要成分是K2O和Na2O。
长石在玻璃制造过程中起到提高玻璃的化学稳定性和改善玻璃性质的作用。
三、熔制熔制是玻璃制造工艺中的关键环节,主要包括以下步骤:1. 加热:将原料放入玻璃熔炉中,通过加热使原料熔化。
熔炉类型有电熔炉、燃油熔炉、燃气熔炉等。
2. 熔化:加热至一定温度后,原料开始熔化。
熔化过程中,原料中的杂质会逐渐析出,形成熔渣。
3. 混合:熔化过程中,通过搅拌使熔融的玻璃均匀混合,确保玻璃成分均匀。
4. 调节:根据玻璃成分和性能要求,对熔融玻璃进行成分和温度的调节。
四、成型成型是将熔融玻璃制成所需形状和尺寸的过程。
常用的成型方法有:1. 浇注成型:将熔融玻璃倒入模具中,冷却固化后取出。
适用于制造平板玻璃、瓶罐玻璃等。
2. 拉制成型:将熔融玻璃通过拉丝机拉制成细长的玻璃丝。
适用于制造玻璃纤维、玻璃丝等。
3. 挤压成型:将熔融玻璃通过模具挤压成所需形状。
适用于制造玻璃管、玻璃棒等。
玻璃熔制及熔窑---玻璃熔制过程剖析

玻璃的形成
2.石英颗粒的尺寸: τ---形成玻璃的时间
k1r03
石英颗粒越小,反应时间越短。注:过小,结团而成为大颗 粒,反而不宜熔化。 3.熔体温度: τ---形成玻璃的时间
aebt
b、t与玻璃成分、原料颗粒度等相关的常数
玻璃的形成
4.配合料及投料质量 a.原料的颗粒级配 难熔的小一些、易熔的大一些;密度小的 粗一些,密度大的细一些。 b.配合料质量 均匀性与水分含量 c.投料方式 薄层投料、均匀投料 d、碎玻璃
玻璃形成的动力学: 1.玻璃成分:τ---熔化速度常数,表示玻璃相对难熔的特征。
τ是一经验常数, 要综合各种因
一般工业玻璃:
SiO2
Al 2 O3
素后确定熔化 温度。
Na2O K 2O
硼酸盐玻璃:
SiO2 Al2O3
Na2O
K2O
1 2
B2O3
铅酸盐玻璃:
SiO2 Al2O3
Na2O K 2O 0.125 PbO
O2与N2:一般情况下以物理溶解为主,溶解度很小
玻璃液的澄清
(4)几种气体在玻璃液中的性质
CO2:物理溶解度随着T升高,过饱和程度的增加而降低;玻璃液 的吸收能力随碱性氧化物浓度增加而增加。化学溶解为主 SO2:低于1200℃时玻璃液的吸收能力随着T升高而增大,超1200℃ 时,溶解量迅速减少。化学溶解为主
500℃左右开始分解;白云石700 ℃左右MgCO3(先)分解 完全,CaCO3(后)分解很少;硝酸钠350 ℃左右开始分解。
c.脱水:结晶水、结构水、化学结合水
d.熔融:固态转变为液态
硅酸盐的形成阶段
3.各组分之间(多组分)的加热反应
a.固相反应:
玻璃的熔制及成型
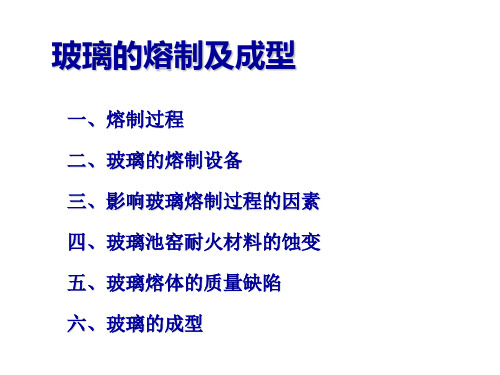
4. 玻璃液的均化
澄清后的玻璃液中存在着条纹及其它不均匀体,需经过 均化过程才能获得化学组成均匀一致的玻璃液。 均化过程就是不均匀体在玻璃液中溶解、扩散的过程。 改善玻璃液均化效果的措施主要有:
保证原料和配合料质量,对配合料进行粒化、烧结等预处理;
3. 原料
原料的种类
原料的挥发
原料的粒度
4. 配合料的质量
配合料中水份、碎玻璃均起到了促进玻璃融化的作用;
配合料的气体率大小,不仅影响玻璃的得率,更重要得是
影响玻璃的澄清过程; 配合料的成分均匀性是确保玻璃液成分均匀的重要前提。
5. 熔制作业制度
合理的作业制度是正常生产的保证,也是获得高产量
(1)侵蚀介质的种类
配合料组分与耐火材料发生低共熔作用;
玻璃液渗透到耐火材料孔隙中,与之发生交代反应, 加剧耐火材料的蚀变; 配合料和玻璃液的挥发物,与耐火材料表面反应,或 渗入耐火材料气孔形成冷凝物,侵蚀耐火材料; 重金属,极易沉入玻璃池窑底部,与池底耐火材料发 生低共熔作用而侵蚀耐火材料。
不变。 (1)硅质耐火材料的蚀变
(2)电熔锆刚玉(AZS)耐火材料的蚀变
(3)格子砖的蚀变
(1)硅质耐火材料的蚀变
硅质耐火材料在日用玻璃池窑上用做大碹及胸墙等的
耐火材料。因此主要承受碱性挥发物的侵蚀。在正常使用 情况下,窑温不高于1600oC时,硅质是很耐侵蚀的。
表面蚀变
内部蚀变 多晶蚀变
进行人工均化(如机械搅拌、池底鼓泡等),加强扩散;
采用先进的熔制技术(如电熔窑可减少挥发); 对挥发量大的玻璃液可采用密封和液面挡料、撇料、定期池底
人教版高中化学选修一课件第三章第三节玻璃
现代玻璃工业发展迅速,新型玻璃材 料不断涌现,应用领域不断拓展。
随着科技的发展,人们逐渐掌握了玻 璃的制造技术,生产出各种不同类型 的玻璃。
玻璃分类及用途
01
02
03
按成分分类
主要包括硅酸盐玻璃、硼 酸盐玻璃、磷酸盐玻璃等 。
按功能分类
可分为普通平板玻璃、钢 化玻璃、夹层玻璃、中空 玻璃等。
按应用领域分类
玻璃概述与分类
BIG DATA EMPOWERS TO CREATE A NEW
ERA
玻璃定义及特点
玻璃是一种非晶态固 体材料,由硅酸盐、 氧化物等主要成分组 成。
玻璃不透气、不透水 ,具有良好的隔离性 能。
玻璃具有透明度高、 化学稳定性好、机械 强度高等特点。
玻璃历史与发展
玻璃的起源可以追溯到古代,最早是 由天然矿物和植物灰烬混合制成的。
从而提高玻璃的强度和耐候性。
03
玻璃制备工艺与设备
BIG DATA EMPOWERS TO CREATE A NEW
ERA
原料选择与预处理
原料种类
玻璃制备的主要原料包括石英砂 、纯碱、石灰石等。
原料质量
原料的质量对玻璃的性质有很大影 响,如石英砂的粒度、纯碱的纯度 等。
预处理
原料在使用前需要进行破碎、筛分 、洗涤、烘干等预处理,以去除杂 质和水分,保证玻璃的质量。
高性能化
智能化
新型玻璃材料将继续追求更高的性能,如 更高的强度、更好的耐磨性、更优异的透 光性等。
随着科技的发展,智能玻璃的应用范围将 进一步扩大,如智能调光玻璃、智能加热 玻璃等。
当前面临挑战及解决策略探讨
技术挑战
新型玻璃材料的研发和生产需要较高的技术水平,如何突破技术瓶颈是当前面临的主要挑 战之一。解决策略包括加强科研投入、引进先进技术、培养专业人才等。
玻璃的熔制过程及玻璃的形成
玻璃的熔制过程及玻璃的形成玻璃是一种非晶态物质,在固体状态下具有高度的无序性。
与晶体不同,玻璃的原子或分子没有规则的排列方式,而是呈现出一种类似液体的结构。
玻璃的制作过程通常涉及以下几个步骤:原料的准备、混合、熔融、成型和退火。
首先,玻璃的原料通常包括硅酸盐、碳酸盐、氟化物、氧化物等。
这些原料需要经过精细的筛选和准备,以确保最终的玻璃制品具有高质量和一致性。
接下来,原料会被混合在一起。
这个过程中,可以添加一些助熔剂来降低玻璃的熔点,并提高其流动性。
同时,还可以添加一些颜料或着色剂,使玻璃获得不同的颜色。
然后,混合后的原料会被放置在熔炉中进行加热熔化。
熔化温度通常在1000℃-1600℃之间,具体取决于玻璃的成分。
在熔化过程中,原料中的化合物会逐渐分解并混合在一起,形成一个均匀的、粘稠的玻璃熔体。
当玻璃熔体达到适当的粘度后,可以进行成型。
一种常见的方法是通过将玻璃熔体倒入预先设计好的模具中,并迅速冷却,使得玻璃凝固成所需的形状。
也可以使用玻璃纤维或吹塑技术来制作不同形状的玻璃制品。
最后,将成型后的玻璃进行退火处理。
退火是将玻璃制品加热至较低的温度,然后缓慢冷却。
这个过程有助于减少玻璃内部的残余应力,增强玻璃的强度和稳定性。
关于玻璃形成的机制,有几种理论被提出。
其中最常被引用的是针对硅酸盐玻璃的聚集-聚合-凝胶理论。
根据这个理论,玻璃形成过程中的原子或分子聚集在一起形成聚集体,然后通过聚合反应形成更大的聚合体,并最终凝胶化形成玻璃。
除此之外,还有一些其他的理论,如液体-液体相分离理论和无限长寿命理论。
这些理论试图解释玻璃形成过程中原子或分子的排列和结构。
总的来说,玻璃的熔制过程包括原料的准备、混合、熔融、成型和退火。
而玻璃的形成机制仍然存在一定的争议,但聚集-聚合-凝胶理论是目前被广泛接受和引用的解释之一。
热熔玻璃工艺(3篇)
第1篇一、热熔玻璃工艺原理热熔玻璃工艺的核心是玻璃的热塑性能。
玻璃是一种非晶态固体,具有可塑性。
当玻璃加热到一定温度时,其分子间的相互作用力减弱,玻璃逐渐软化,此时可以进行塑形、切割、焊接等操作。
热熔玻璃工艺的温度范围一般在600℃至800℃之间,具体温度根据玻璃种类和厚度而定。
热熔玻璃工艺原理主要包括以下几个方面:1. 玻璃软化:玻璃在加热过程中,分子运动加剧,分子间的相互作用力减弱,导致玻璃软化。
2. 塑形:在玻璃软化过程中,通过模具、手工等手段对玻璃进行塑形,形成所需形状。
3. 切割:在玻璃软化过程中,利用切割工具将玻璃切割成所需尺寸。
4. 焊接:将两块或多块玻璃加热至软化状态,使其熔接在一起,形成整体。
二、热熔玻璃工艺流程热熔玻璃工艺流程主要包括以下步骤:1. 玻璃原料准备:根据产品需求,选择合适的玻璃原料,如石英砂、硼砂、硼酸等。
2. 玻璃熔制:将玻璃原料放入炉中熔化,形成玻璃液。
3. 玻璃成型:将熔融的玻璃液倒入模具中,冷却后形成玻璃板。
4. 玻璃切割:将玻璃板切割成所需尺寸。
5. 玻璃软化:将切割好的玻璃加热至软化状态。
6. 玻璃塑形:在软化状态下,通过模具、手工等手段对玻璃进行塑形。
7. 玻璃切割:将塑形后的玻璃切割成所需尺寸。
8. 玻璃焊接:将两块或多块玻璃加热至软化状态,使其熔接在一起。
9. 玻璃冷却:将焊接好的玻璃冷却至室温,形成最终产品。
三、热熔玻璃工艺应用领域热熔玻璃工艺具有独特的艺术性和实用性,广泛应用于以下领域:1. 建筑领域:热熔玻璃工艺可用于制作玻璃幕墙、玻璃窗、玻璃门、玻璃屋顶等建筑玻璃制品。
2. 家居领域:热熔玻璃工艺可用于制作玻璃家具、玻璃餐具、玻璃工艺品等家居用品。
3. 装饰领域:热熔玻璃工艺可用于制作玻璃壁画、玻璃挂件、玻璃饰品等装饰品。
4. 艺术领域:热熔玻璃工艺可用于制作玻璃雕塑、玻璃装置等艺术作品。
5. 照明领域:热熔玻璃工艺可用于制作玻璃灯具、玻璃装饰灯等照明产品。
第三节 玻璃的熔制
在熔制无色瓶罐玻璃的普通纯碱配合料时,必须保 持氧化气氛。 熔制以碳粉作还原剂的纯碱-芒硝配合料时,为保持碳 粉在加料口不被氧化,须还原气氛;最后又必须将碳粉完 全烧尽,须氧化气氛。
三、玻璃体的缺陷
玻璃体内由于存在各种夹杂物,引起玻璃体均匀性 的破坏,称为玻璃的缺陷。 通常所说的缺陷主要是指气泡、条纹和结石三大缺 陷。他们分别是均匀玻璃中的气态、玻璃态和固态夹杂 物。 1、气泡 2、条纹、 线道、结瘤 3、结石
化学过程
1. 固相反应 2. 盐类分解 3. 水化物分解 4. 结晶水分解 5. 硅酸盐形成 与相互作用
物理化学过程
1. 低共熔物形成 2. 固态溶解,液态互溶
3. 玻璃液、炉气、气泡间
的相互作用 4. 玻璃液与耐火材料作用
2、玻璃的熔制过程
掌握
玻璃熔制
硅酸盐形 成阶段
玻璃形成 阶段
玻璃液澄 清阶段
D. 玻璃液的对流 玻璃液的对流有利于均化,但对耐火材料侵蚀加大; E. 气泡的上升 澄清过程,带动玻璃液均化。
玻璃液的冷却:1100 ~1200℃ 将玻璃液的温度降低200-300℃; 玻璃液具有成型必须的粘度。
定义
冷却是将玻璃液均匀冷却到 成型温度的过程。
注意!!
整个冷却过程应力求平稳 进行,以保证玻璃液的热均 匀性,并防止出现温度波动, 以免引起二次气泡。
澄清时间 通常延长澄清时间利于排除气泡。但硫 酸盐玻璃不然。 机械搅拌、超声波作用 使玻璃液沸腾搅拌。压力与气氛。窑内 必须保持微正压或微负压,负压过大,使冷 气吸入窑内,玻璃液产生大量气泡;相反正 压过大,不利于气体排除。
- 1、下载文档前请自行甄别文档内容的完整性,平台不提供额外的编辑、内容补充、找答案等附加服务。
- 2、"仅部分预览"的文档,不可在线预览部分如存在完整性等问题,可反馈申请退款(可完整预览的文档不适用该条件!)。
- 3、如文档侵犯您的权益,请联系客服反馈,我们会尽快为您处理(人工客服工作时间:9:00-18:30)。
③④ 气泡中分离出来的气体,进入炉气或溶解在玻璃中; ⑤ 气体从炉气进入到玻璃液中。
(4)澄清过程
通常所说的玻璃液的澄清过程是指排除玻璃液中可见
气泡中的气体。根据以上所述的气体平衡关系,要消除可
见气泡,有两种途径:
使可见气泡上浮到液面破裂,气体进入炉气中;
使可见气泡中的气体溶解到玻璃液中。 通常不可行
使玻璃液中溶解的气体渗入气泡,使之增大。
澄清剂原理:
澄清剂是指在玻璃熔化高温阶段释放出气体,促进玻璃
液中已有的可见气泡长大,并加速上浮,玻璃液的澄清过程 因而明显加速的物质。 作用过程: 硝酸盐分解(500℃以下开始) ↓ 400-1300 ℃ >1300 ℃ As2O5 O2↑ + As2O3 As2O3+O2↑
τ=
SiO2+Al2O3 Na2O+K2O
对于含硼硅酸盐玻璃,
τ=
SiO2+Al2O3 Na2O+K2O+0.5 B2O3 SiO2+Al2O3 Na2O+0.5 B2O3+0.125 PbO
对于含铅硅酸盐玻璃,
τ=
其中:氧化物—各氧化物在玻璃中的重量百分数; —表示玻璃相对难熔的特征值;
与值相应的熔化温度
(1)侵蚀介质的种类
配合料组分与耐火材料发生低共熔作用;
玻璃液渗透到耐火材料孔隙中,与之发生交代反应, 加剧耐火材料的蚀变; 配合料和玻璃液的挥发物,与耐火材料表面反应,或 渗入耐火材料气孔形成冷凝物,侵蚀耐火材料; 重金属,极易沉入玻璃池窑底部,与池底耐火材料发 生低共熔作用而侵蚀耐火材料。
(3) 澄清过程
(1)气体的来源
配合料中原料的分解; 部分组分的挥发;
组分间化学反应产生的气体;
配合料粉体空隙中夹带的气体; 玻璃液与耐火材料相互作用产生的气体; 玻璃液从窑炉火焰空间中吸收、溶解的气体。
(2)气体种类
随着玻璃组成、原料种类、窑炉气氛、压力、温度等的 变化,存在于玻璃液中的气体的种类也不尽相同。常见的有
的成品率和生产成本。 1. 气泡 2. 结石 3. 条纹、线道、结瘤
1. 烧结体的形成 (硅酸盐形成阶段)
质量合乎要求的配合料加入玻璃窑炉中,在高温作用下,
发生一系列物理、化学反应,形成不透明烧结物。
物 理 变 化 配合料加热升温 固相反应 化学变化
配合料脱水
各组分的熔化
碳酸盐、硫酸盐、硝酸盐的分解
气氛的影响
液面制度
玻璃液面附近耐火材料的侵蚀过程 (左:产生熔融层 中:熔融层移去 右:玻璃液渗透)
2. 常见耐火材料的蚀变
变代反应——指在气化-热液的作用下,耐火材料的物质
或组份发生带入或带出,以至使原物质被新 物质取代。 特点:原结构的破坏和新结构的形成是同时发生的。整个
过程是在有溶液参与的固态下进行的。变代反应前后体积
不变。 (1)硅质耐火材料的蚀变
(2)电熔锆刚玉(AZS)耐火材料的蚀变
(3)格子砖的蚀变
(1)硅质耐火材料的蚀变
硅质耐火材料在日用玻璃池窑上用做大碹及胸墙等的
耐火材料。因此主要承受碱性挥发物的侵蚀。在正常使用 情况下,窑温不高于1600oC时,硅质是很耐侵蚀的。
表面蚀变
内部蚀变 多晶蚀变
格子砖还应考虑高温作用下的荷重作用破坏。
1. 气泡
按大小分为:大泡、小泡、针尖泡; 按形成原因分为:一次气泡、二次气泡、耐火材料气泡等。 二次气泡 澄清好的玻璃液中重新析出的气泡。造成二次气泡有 物理、化学两方面原因: 物理原因:
降温后玻璃液又一次升温超过一定限度
化学原因: 与玻璃的化学组成和使用的原料有关。(含钡玻璃) BaO + O2
3. 原料
原料的种类
原料的挥发
原料的粒度
4. 配合料的质量
配合料中水份、碎玻璃均起到了促进玻璃融化的作用;
配合料的气体率大小,不仅影响玻璃的得率,更重要得是
影响玻璃的澄清过程; 配合料的成分均匀性是确保玻璃液成分均匀的重要前提。
5. 熔制作业制度
合理的作业制度是正常生产的保证,也是获得高产量
热稳定性,甚至会使制品自行破裂。 按其成因可分为: 配合料结石 耐火材料结石 析晶结石
3. 条纹、线道、结瘤
定义:玻璃主体内存在的异类玻璃态夹杂物。 特点:属于一种比较普遍的玻璃不均匀性方面的缺陷。 化学组成上、物理性质上(折射率、密度、粘度、 表面张力、热膨胀、机械强度、颜色)与玻璃的 主体不同。 形成原因: 配合料混合不均匀 某些组分的挥发 耐火材料蚀变形成
用,从而受到侵蚀。这种侵蚀一方面导致窑炉寿命的缩短,
另一方面还影响到玻璃制品的质量。 1. 影响耐火材料蚀变的因素 2. 常见耐火材料的蚀变
五、玻璃熔体的质量缺陷
通常所说的缺陷主要是指气泡、条纹和结石三大缺陷, 他们分别是均匀玻璃中的气态、玻璃态和固态夹杂物。这
些缺陷的存在直接影响到玻璃液的质量,关系到玻璃生产
AZS砖的蚀变主要是: 玻璃相结合物被溶解;
刚玉与碱性氧化物发生变代反应,生成β-Al2O3和霞石。
(3)格子砖的蚀变
由于配合料及玻璃液的挥发物,燃料燃烧废气中某些
成分(如SO3)等随烟气进入蓄热室,在格子砖的表面侵 蚀形成腐蚀性冷凝液,形成对耐火材料的侵蚀。 此外,热作用也是格子砖易损的原因之一。对于下层
(2)电熔锆刚玉(AZS)耐火材料的蚀变
AZS砖具有较强的抗侵蚀能力,用于池窑的高温和玻璃液
直接接触部位的部位。 AZS砖标号越高,ZrO2含量越高,斜锆
石相越多,抗侵蚀性能越好。此外,AZS砖中玻璃相受蚀后常 生成含ZrO2的高粘度长石质玻璃,这层高粘度的玻璃液滞留在 砖表面,保护了砖体的进一步蚀变。
高温
BaO2
低温
BaO + O2
2. 结石
结石是玻璃液中的晶态(固态)夹杂物。它是玻璃熔体 缺陷中破坏性最大的缺陷,因而也是限制最严的缺陷。它不 仅破坏了玻璃制品的外观和光学均一性,而且降低了玻璃制 品的使用价值。结石与它周围玻璃的膨胀系数相差愈大,产
生的局部应力也就愈大。这就大大降低了制品的机械强度和
4. 玻璃液的均化
澄清后的玻璃液中存在着条纹及其它不均匀体,需经过 均化过程才能获得化学组成均匀一致的玻璃液。 均化过程就是不均匀体在玻璃液中溶解、扩散的过程。 改善玻璃液均化效果的措施主要有:
保证原料和配合料质量,对配合料进行粒化、烧结等预处理;
进行人工均化(如机械搅拌、池底鼓泡等),加强扩散;
需要指出的,玻璃熔制过程的五个阶段,在实际生产中,
是难以完全分开的,有时甚至是同步发生的。
池窑中玻璃熔融过程模型图
二、玻璃的熔制设备
工业上用于玻璃熔制的设备有坩锅窑和池窑。前者产量 低、耗能大,主要用于手工生产小批量的玻璃制品;后者用 于玻璃产品的工业化大规模的连续生产。 池窑的分类 1. 按使用热源分 (1)火焰窑 以燃料燃烧为热能来源。燃料可以是煤气,
配合料经高温加热熔融最终转变为复合成型要求的玻璃液 的过程是极其复杂的,所有与这一过程有关联的因素都将影响
玻璃熔制的质量。
1. 玻璃组成 2. 玻璃液的黏度、表面张力的影响
3. 原料
4. 配合料的质量 5. 熔化作业制度的影响 6. 加速玻璃熔化的辅助手段
四、玻璃池窑耐火材料的蚀变
在玻璃生产过程中,耐火材料因与高温玻璃液、配合料 和玻璃液的挥发物以及燃料中某些组份及其燃烧产物相互作
重油和水;
(2)电热窑 以电能作为热量来源; (3)火焰-电热窑 以燃料为主要热源,电能为辅助热源。
2. 按窑内火焰流动的方向分 (1) 横焰窑 窑内火焰作横向流动、与玻璃液流动 方向垂直; (2) 马蹄焰窑 窑内火焰呈马蹄形流动; (3) 纵焰窑 窑内火焰作纵向流动、与玻璃液流动 方向相平行。
三、影响玻璃熔化过程的因素
(3)搅拌与鼓泡
在池窑上增设搅拌与鼓泡装置可提高玻璃液的澄清和均化
速度。搅拌装置通常设置在池窑的卡脖、供料道等处,鼓泡通 常设在熔化池的料堆区和热点区。 (4)电助熔 (5)富氧燃烧 (6)高压与真空熔炼
1. 影响耐火材料蚀变的因素
(1)侵蚀介质的种类
(2)耐火材料的性能 (3)池窑作业的工艺制度
3. 玻璃液的澄清
玻璃液的澄清是指气体夹杂物从玻璃液中消除的过程。 在玻璃熔制过程中,硅酸盐的形成阶段将放出玻璃配合料 重量的18%左右的气体,其中大部分可以通过配合料间的缝隙
排出,剩余的部分将被包裹在此阶段生成的液相和玻璃形成阶
段生成的玻璃相中。 (1)气体的来源 (2)气体的种类
(3)存在形式
水化物的分解
晶相转变
个别组分的挥发
化学结合水的分解
硅酸盐的形成与相互作用
对于普通钠-钙硅酸盐玻璃而言,这一阶段结束后,配合料 转变为由硅酸盐和残余石英颗粒组成的烧结体。
2. 玻璃液的形成(玻璃的形成)
烧结物进一步加热后开始熔融,并相互熔融、扩散,并
最终由不透明体变为透明玻璃液。 但此时的玻璃液含有大量可见气泡,且玻璃液的化学成分 很不均匀,这需要澄清和均化过程去完成。
对于第一种方式,可见气泡从玻璃液中上浮过程符合 Stocks 9η
r----气泡的半径 v----气泡上浮速度
g----重力加速度
d、 d` ----玻璃液和气泡的密度 η----熔融玻璃液的粘度
在等温等压下,使气泡变大的两个因素: 使多个小气泡汇集合成一个大气泡;但实际上气泡 间距远,加之玻液表面张力大,难以实现。
N2、O2、CO2、H2O、CO、SOx、NOx等。
(3)存在形式
残留在玻璃液中的气体存在三种形式:
可见气泡 物理溶解
化学结合