催化剂预硫化
浅谈加氢装置开工前的催化剂预硫化

浅谈加氢装置开工前的催化剂预硫化一前言目前,大多数加氢催化剂的钨、钼、钴等活性金属组分,使用前都是以氧化物的状态分散在载体表面。
根据生产经验和理论研究,加氢催化剂的活性只有呈硫化物的形态才有较高的活性。
因此,当催化剂装入反应器后,加氢催化剂使用前必须先进行预硫化。
预硫化是提高加氢催化剂活性和延长其使用寿命的重要步骤。
二加氢催化剂的预硫化技术(1)加氢催化剂的预硫化方法及选择虽然氧化态催化剂可通过在使用过程中由原料油中含有的硫化物反应生成硫化氢对其硫化,但一方面由于原料中的硫化物需要在较高的温度条件下才能反应生成硫化氢,从而导致一部分金属氧化物还原,使催化剂的硫化达不到正常水平。
因此,对这类加氢催化剂,多采用外加硫化剂预硫化的方法,将金属氧化物在进原料油反应之前转化为硫化态。
目前,工业装置最常见的预硫化方法有干法硫化和湿法硫化两种。
所谓干法硫化,即在循环氢气存在下,注入硫化剂进行硫化;湿法硫化,即在循环氢气存在下,以低氮煤油或轻柴油为硫化油,携带硫化剂注入反应系统进行硫化。
在实际生产中,究竟选择哪种预硫化方法,应视工厂及加氢催化剂的具体情况而定。
一般来说,对以无定型硅铝为载体的加氢精制催化剂多采用湿法硫化;而对于含分子筛的加氢裂化催化剂则多采用干法硫化。
因为沸石分子筛酸性较强,如果用湿法硫化,可能会因硫化油发生裂解反应而导致催化剂床层超温,并产生积炭而使催化剂活性下降。
(2) 预硫化过程的化学反应在氢存在的条件下,预硫化过程中的化学反应包括硫化剂的分解反应及金属氧化物还原和硫化的竞争反应。
理想的预硫化反应如下:CS2+4H2=2H2S+CH4MoO3+2H2S+H2=MoS2+3H2O9CoO+8H2S+H2=Co9S8+9H2O3NiO+2H2S+H2=Ni3S2+3H2OWO3+2H2S+H2=WS2+3H2O催化剂预硫化反应十分复杂,金属氧化物的还原和硫化反应互相竞争,主要取决于硫化反应的各种条件。
催化剂硫化的主要步骤

催化剂硫化的主要步骤催化剂硫化是制备硫化催化剂的重要工艺步骤之一。
硫化催化剂具有催化剂活性高、稳定性好等优点,广泛应用于化工领域中的各种催化反应中。
下面将介绍催化剂硫化的主要步骤。
步骤一:催化剂的选择催化剂硫化的第一步是选择合适的催化剂。
催化剂的选择应根据具体的反应要求来确定。
常见的催化剂包括金属催化剂、氧化物催化剂、酸碱催化剂等。
在选择催化剂时,需要考虑催化剂的活性、选择性、稳定性以及成本等因素。
步骤二:催化剂的预处理在催化剂硫化之前,需要对催化剂进行预处理。
预处理的目的是去除催化剂表面的杂质和不稳定物质,提高催化剂的活性和稳定性。
常见的预处理方法包括洗涤、焙烧、还原等。
步骤三:硫化剂的选择硫化剂是催化剂硫化的关键步骤。
硫化剂可以是硫化氢、硫醇、硫酸等。
根据具体的反应要求和催化剂的特性,选择合适的硫化剂进行硫化。
硫化剂的选择应考虑硫化速率、硫化效率以及对催化剂活性的影响等因素。
步骤四:硫化条件的控制硫化过程中,硫化条件的控制非常重要。
硫化温度、硫化时间、硫化压力等条件的选择应根据催化剂和硫化剂的性质来确定。
硫化温度过高或过低都会影响硫化效果,硫化时间过长或过短也会导致催化剂的质量下降。
步骤五:催化剂的活化催化剂硫化完成后,还需要对催化剂进行活化处理。
活化的目的是进一步提高催化剂的活性和稳定性。
常见的活化方法包括还原、氧化、钝化等。
活化过程中需要控制好活化剂的浓度、温度和时间等参数,以保证活化效果的良好。
步骤六:催化剂的测试和评价催化剂硫化完成后,需要对催化剂进行测试和评价。
测试的目的是评估催化剂的催化性能和稳定性。
常见的测试方法包括催化活性测试、选择性测试、寿命测试等。
评价的目的是确定催化剂的优缺点,为后续的催化反应提供依据。
催化剂硫化的主要步骤包括催化剂的选择、催化剂的预处理、硫化剂的选择、硫化条件的控制、催化剂的活化以及催化剂的测试和评价。
这些步骤的正确进行可以保证催化剂的质量和活性,从而提高催化反应的效果和产率。
催化剂的器外预硫化

用温度探针测量试样和惰性参比样的温差,经处理转换
成相应的△H,表征试样的相对放热强度;该设备十分
类似于一个加氢处理反应器,在实验室可用于模拟工业
装置预硫化催化剂活化时的放热情况。
• 同一类型Co/Mo 催化剂三种预 硫化样品,用 DSC测试的结果 见图13-4-4所示。
图 13-4-4
三种样品 DSC 测试结果
整个过程发生在28℃ (82℉)附近一个很窄的温度范围内。
• 元素硫预硫化催化剂在243℃ (470℉)左右引发反应,其
放热峰值更高,其峰宽狭窄,放热量最集中。这些表征
放热情况的“峰高”与工业装置中所观测到的温升成正 比,actiCAT预硫化催化剂活化时放热缓慢,在相同的
开工条件下,有助于减少床层温升。
得到有效的应用(见下表)。
•
SULFICAT预硫化催化剂的工业应用 丁烷加氢 烯烃加氢 苯加氢 芳烃加氢 直馏石脑油加氢 焦化石脑油加氢 煤油加氢 中间馏分油加氢 柴油加氢 轻瓦斯油加氢 加氢裂化 石蜡加氢 润滑油加氢 减压瓦斯油加氢 FCC原料加氢 缓和加氢裂化 加氢裂化原料 加氢脱金 渣油加氢
再经钝化处理后装入加氢装置的反应器中,用氢气或者
氢气和油循环升温到一定的温度条件下,换进原料油。
催化剂器外预硫化的优点
• 开工时间大大缩短;
• 预硫化催化剂含有适量的硫,开工过程中不需要再准备 催化剂硫化所需的化学品。
• 开工阶段不用注硫泵,注硫泵因不常用而往往失修,注 硫设备维修会延误开工时间; • 可相对减少对所在地社区的环境污染; • 开工简便,actiCAT、Tricat预硫化催化剂,开工比较 容易,开工条件相对宽松; • 可靠性好,装置使用的“ 每一粒 ”催化剂都经过充分 预硫化处理,反应器催化剂床层截面的物流和温度分布 均匀。
加氢催化剂预硫化方案

1. 引言加氢催化剂是广泛应用于石化工业领域的关键催化剂之一。
为了提高加氢催化剂的活性和稳定性,预硫化技术被广泛应用。
本文将从预硫化的原理、影响因素以及常见的预硫化方案等方面进行探讨。
2. 预硫化的原理预硫化是指在加氢催化剂使用之前,使用硫化物溶液进行处理,使其表面形成一层硫化物膜。
这一膜可以防止催化剂表面被氧化物或其他不活性物质占据,从而提高催化剂的活性和稳定性。
预硫化的原理可以归结为两个方面:•活性金属硫化物的形成:活性金属如镍、钼等能够与硫化物反应形成硫化物,这种硫化物能够促进加氢反应的进行,提高催化剂的反应活性。
•表面硫化膜的形成:硫化物膜可以阻隔外界氧气和不活性物质的侵蚀,减少催化剂的表面被氧化的机会,提高催化剂的稳定性。
3. 预硫化的影响因素预硫化的效果受到多种因素的影响,下面列举了一些主要的影响因素:3.1 硫化剂的选择预硫化过程中使用的硫化剂对催化剂的性能起着至关重要的作用。
常用的硫化剂包括硫化氢(H2S)、二硫化碳(CS2)等。
不同的硫化剂在反应中会产生不同的硫化物,并对催化剂表面的化学状态产生影响。
3.2 预硫化温度和时间预硫化温度和时间是影响预硫化效果的关键因素。
一般来说,高温和长时间的预硫化会使硫化剂更充分地与催化剂发生反应,生成更完善的硫化物膜。
然而,过高的温度可能会导致催化剂的部分活性成分被分解或损失,因此需要根据具体情况选择合适的预硫化温度和时间。
3.3 氛围条件预硫化过程中的气氛条件也会对催化剂的预硫化效果产生影响。
一般情况下,加氢环境中的氢气浓度越高,硫化剂与催化剂的反应速度越快,硫化物膜形成的效果也越好。
4. 常见的预硫化方案4.1 H2S气体预硫化H2S气体预硫化是一种常用的预硫化方式。
预硫化过程中,将催化剂放入加热炉中,通入含有H2S气体的加硫气体。
通过控制炉内温度和气氛浓度,使硫化剂与催化剂表面反应生成硫化物。
4.2 溶液浸泡预硫化溶液浸泡预硫化是另一种常见的预硫化方式。
催化剂预硫化操作简版

1.1.催化剂预硫化1.1.1.预硫化的准备工作1)变换催化剂升温脱水已完成,变换炉床层温度达200~220℃。
2)硫化剂已拉至现场(35t),考虑到催化剂硫化过程中损失等因素,硫化剂的准备量应为理论耗量的1.5倍。
3)21V009硫化剂罐已储存硫化剂;预硫化过程中当界位低于30%时应及时补充硫化剂。
4)联系调度引开工氢气至装置界区前备用。
开工氢气规格:压力≦1.0MPa(G),不含烯烃,氧气含量小于0.05%(V);开工氢气采样分析合格。
5)检查确认21E005、21E008、21E009已建立正常液位。
6)按岗位操作法投用工艺凝液汽提系统,工艺凝液汽提系统具备接收预硫化产生的含硫污水。
1.1.2.预硫化的注意事项1)预硫化过程中,严格按硫化曲线操作,控制好硫化温度、循环气中硫化氢及氢气浓度。
2)硫化氢未穿透催化剂床层时,催化剂床层任意温度不能大于280℃。
3)若催化剂床层温升超过30℃,则停止升温或降低注硫量,并且保持变换炉进口温度不变直至温升降至小于30℃。
4)硫化剂的加入应采取连续少量的原则加入,防止超温。
5)硫化过程中,定期检测循环气中的硫化氢浓度。
6)预硫化过程中,视采样分析结果,调整开工氢气补入量,将循环系统氢含量维持在10%~25%(V),以控制20%(V)为宜。
预硫化期间要始终保持H2含量在10%(V)以上,保证硫化剂加入后能完全氢解。
7)催化剂硫化产生的污水应密闭排往工艺凝液汽提系统。
8)若电加热器故障长时间停运:应停配氢气、停止注硫、停21K001,系统保温保压,必要时引氮气置换以降低系统内氢气浓度。
故障排除后按岗位操作法启动21K001、21E001进行硫化。
9)若注硫泵21P003不上量:催化剂停止提温,停止配氢气,尽快处理好注硫系统的故障并向催化剂注硫,重新配氢气以维持循环氢中氢浓度在指标范围内。
若注硫无法恢复正常,应监控循环气中硫化氢浓度,提高氮气补入量,以降低循环气中氢气浓度。
为什么加氢催化剂使用前必须进行预硫化
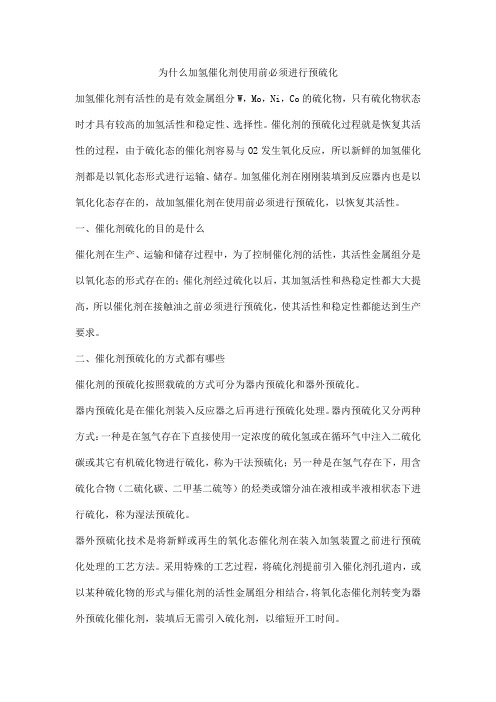
为什么加氢催化剂使用前必须进行预硫化加氢催化剂有活性的是有效金属组分W,Mo,Ni,Co的硫化物,只有硫化物状态时才具有较高的加氢活性和稳定性、选择性。
催化剂的预硫化过程就是恢复其活性的过程,由于硫化态的催化剂容易与O2发生氧化反应,所以新鲜的加氢催化剂都是以氧化态形式进行运输、储存。
加氢催化剂在刚刚装填到反应器内也是以氧化化态存在的,故加氢催化剂在使用前必须进行预硫化,以恢复其活性。
一、催化剂硫化的目的是什么催化剂在生产、运输和储存过程中,为了控制催化剂的活性,其活性金属组分是以氧化态的形式存在的;催化剂经过硫化以后,其加氢活性和热稳定性都大大提高,所以催化剂在接触油之前必须进行预硫化,使其活性和稳定性都能达到生产要求。
二、催化剂预硫化的方式都有哪些催化剂的预硫化按照载硫的方式可分为器内预硫化和器外预硫化。
器内预硫化是在催化剂装入反应器之后再进行预硫化处理。
器内预硫化又分两种方式:一种是在氢气存在下直接使用一定浓度的硫化氢或在循环气中注入二硫化碳或其它有机硫化物进行硫化,称为干法预硫化;另一种是在氢气存在下,用含硫化合物(二硫化碳、二甲基二硫等)的烃类或馏分油在液相或半液相状态下进行硫化,称为湿法预硫化。
器外预硫化技术是将新鲜或再生的氧化态催化剂在装入加氢装置之前进行预硫化处理的工艺方法。
采用特殊的工艺过程,将硫化剂提前引入催化剂孔道内,或以某种硫化物的形式与催化剂的活性金属组分相结合,将氧化态催化剂转变为器外预硫化催化剂,装填后无需引入硫化剂,以缩短开工时间。
三、常用的硫化剂都有哪些硫化剂的作用是在硫化过程中提供H2S与金属氧化物反应,为此,硫化剂的选用原则是在硫化过程中能在较低温度下分解为H2S,保证催化剂硫化的顺利进行,提高硫化效果。
经综合考虑使用效果、价格、分解温度、安全环保等因素,器内预硫化剂主要包括二硫化碳(CS2)、二甲基二硫化物(DMDS)、正丁硫醇(NBM)、二甲基硫化物(DMS)、甲硫醚等,目前,工业上普遍采用的硫化剂是CS2和DMDS。
加氢裂化催化剂预硫化操作规程

加氢裂化催化剂预硫化操作规程一、催化剂预硫化的目的加氢裂化催化剂的活性金属组分主要是Mo、Ni、Co和W,同其它新催化剂或再生后的催化剂一样,其所含的活性金属组分(Mo、Ni、Co、W)都是以氧化态的形式存在。
大量的研究和工业实践证明,催化剂经过硫化,活性金属组分由氧化态转化为硫化态,具有良好的加氢活性和热稳定性。
因此,在加氢催化剂接触原料油汽之前,先进行预硫化,将催化剂活性金属组分由氧化态转化为硫化态。
本装置使用的FZC系列保护剂为Mo-Ni系活性金属氧化物,FF-20精制催化剂活性金属为W-Mo-Ni系金属氧化物,FC-14裂化催化剂的活性金属为W-Ni系金属氧化物,予硫化能使MoO3、WO3和NiO转变为具有较高活性的MoS2、WS2和Ni3S2金属硫化物。
催化剂硫化一般分为湿法硫化和干法硫化两种,湿化硫化为在氢气存在下,采用硫化物或馏分油在液相或半液相状态下的预硫化;干法硫化为在氢气存在下,直接用含有一定浓度的H2S或直接向循环氢中注入有机硫化物进行的预硫化。
湿法硫化分为两种:一种为催化剂硫化过程所需要的硫油外部加入的硫化物而来,一种为依靠硫化油自身的硫进行预硫化。
本装置预硫化工艺为干法气相硫化。
使用二甲基二硫化物C2H6S2(DMDS)作为硫化剂。
二、催化剂预硫化的原理催化剂预硫化是基于硫化剂(DMDS)临氢分解生成硫化氢(H2S),H2S与催化剂活性金属氧化态反应转化成相应金属硫化态的反应。
其相关的硫化反应如下:(CH3)2S2+3H2→ 2H2S+2CH4MoO3 + 2H2S + H2→ MoS2 + 3H2O3NiO + 2H2S + H2→ Ni3S2 + 3H2OWO3 + 2H2S + H2→ WS2 + 3H2O三、具备条件(1)经过气密检验和紧急泄压试验,确认系统严密性和联锁系统性能安全可靠。
(2)供氢系统确保稳定可靠,1401-K-101及1401-K-102运转正常。
催化剂预硫化
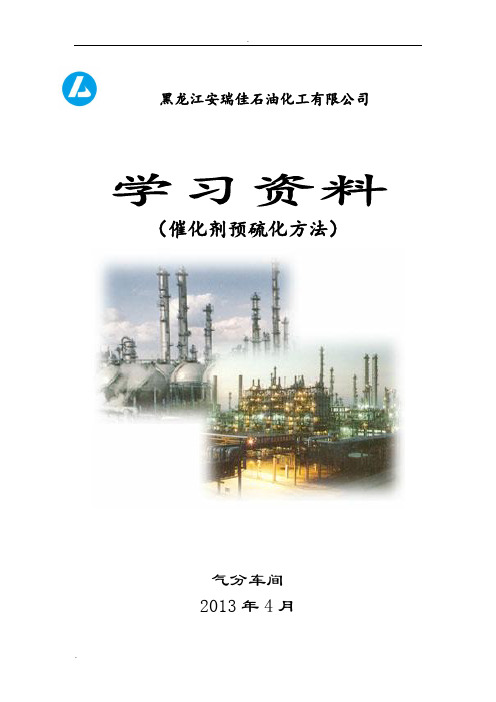
黑龙江安瑞佳石油化工有限公司学习资料(催化剂预硫化方法)气分车间2013年4月催化剂的预硫化催化剂的预硫化有两种方法:一是干法预硫化,亦称气相预硫化,即在循环氢或氢氮混合气或氢气与丙烷或氢气与丁烷混合气存在下注入硫化剂进行硫化;二是湿法预硫化,亦称液相预硫化,即在循环氢存在下以轻油等为硫化油携带硫化剂注入反应系统进行硫化。
催化剂硫化的基本原理催化剂硫化是基于硫化剂(CS2或二甲基二硫DMDS)临氢分解生成的H2S,将催化剂活性金属氧化态转化为相应的硫化态的反应。
干法硫化反应:用氢气作载体,硫化氢为硫化剂。
MoO3 + 2H2S + H2MoS2 + 3H2O9CoO + 8H2S + H2Co9S8 + 9H2O3NiO + 2H2S + H2Ni3S2 + 3H2O湿法硫化反应:用氢气作载体,CS2为硫化剂。
CS2 + 4H22H2S + CH4MoO3 + CS2 + 5H2MoS2 + 3H2O + CH4MoO3 + CS2 + 3H2 MoS2 + 3H2O + C9CoO + 4CS2 + 17H2Co9S8 + 9H2O + CH49CoO + 4CS2 + 9H2Co9S8 + 9H2O + 4C3NiO + 2CS2 + 5H2Ni3S2 + 3H2O + CH4基于上述硫化反应式和加氢催化剂的装量及相关金属含量可估算出催化剂硫化剂的理论需要量。
其硫化剂的备用量(采购量)一般按催化剂硫化理论需硫量的1.25倍考虑即可。
硫化剂和硫化油的选择实际上催化剂硫化时是H2S在起作用,所以所选用的硫化剂在临氢和催化剂存在的条件下,能在较低反应温度下分解生成H2S,以有利于催化剂硫化的顺利进行,提高硫化效果,同时硫化剂中的硫含量应较高,以减少硫化剂的用量,避免其它元素对硫化过程的不利影响,另外硫化剂价格便宜、毒性小、使用安全。
常用硫化剂的理化性质见表4。
表4 常用硫化剂的理化性质催化剂湿法硫化时需要硫化油,硫化油一般采用含链烷烃的直馏煤油或轻柴油,其指标见表5。
- 1、下载文档前请自行甄别文档内容的完整性,平台不提供额外的编辑、内容补充、找答案等附加服务。
- 2、"仅部分预览"的文档,不可在线预览部分如存在完整性等问题,可反馈申请退款(可完整预览的文档不适用该条件!)。
- 3、如文档侵犯您的权益,请联系客服反馈,我们会尽快为您处理(人工客服工作时间:9:00-18:30)。
黑龙江安瑞佳石油化工有限公司学习资料(催化剂预硫化方法)气分车间2013年4月催化剂的预硫化催化剂的预硫化有两种方法:一是干法预硫化,亦称气相预硫化,即在循环氢或氢氮混合气或氢气与丙烷或氢气与丁烷混合气存在下注入硫化剂进行硫化;二是湿法预硫化,亦称液相预硫化,即在循环氢存在下以轻油等为硫化油携带硫化剂注入反应系统进行硫化。
催化剂硫化的基本原理催化剂硫化是基于硫化剂(CS2或二甲基二硫DMDS )临氢分解生成的H2S, 将催化剂活性金属氧化态转化为相应的硫化态的反应。
干法硫化反应:用氢气作载体,硫化氢为硫化剂。
M O O3 + 2H2S + H2 ----------- ► M0S2 + 3H2O9CoO + 8H2S + H2 --------- ► C09S8 + 9H2O3NiO + 2H2S + H2 ________ . M3S2 + 3出0湿法硫化反应:用氢气作载体,CS2为硫化剂。
CS2 + 4H2 ----------- ► 2H2S + CH4M O O3 + CS2 + 5H2 --------------- k M0S2 + 3H20 + CH4M O O3 + CS2 + 3H2 ---------------- ► M0S2 + 3H2O + C9C O O + 4CS2 + 17H2 -------------- 09S8 + 9H20 + CH49C O O + 4CS? + 9H2 ----------- k C09S8 + 9H2O + 4C3Ni0 + 2CS2 + 5H2 ------------ ► M3S2 + 3出0 + CH4基于上述硫化反应式和加氢催化剂的装量及相关金属含量可估算出催化剂硫化剂的理论需要量。
其硫化剂的备用量(采购量)一般按催化剂硫化理论需硫量的1.25倍考虑即可。
硫化剂和硫化油的选择实际上催化剂硫化时是H2S在起作用,所以所选用的硫化剂在临氢和催化剂存在的条件下,能在较低反应温度下分解生成 H2S,以有利于催化剂硫化的顺利进行,提高硫化效果,同时硫化剂中的硫含量应较高,以减少硫化剂的用量,避免其它元素对硫化过程的不利影响,另外硫化剂价格便宜、毒性小、使用安全常用硫化剂的理化性质见表4。
表4常用硫化剂的理化性质催化剂湿法硫化时需要硫化油,硫化油一般采用含链烷烃的直馏煤油或轻柴油,其指标见表5。
表5硫化油性质指标催化剂干法预硫化在反应系统有氢气或氢氮混合气或氢气与丙烷或氢气与丁烷混合气循环,压力在1.5〜2.0MPaG,床层温度在175C以上,使用H2S气体做硫化剂进行预硫化,将催化剂的氧化态活性金属转化为相应的流化态活性金属。
催化剂干法预硫化通常是在装置操作压力不小于1.5 MPaG、循环压缩机全量循环的条件下进行的。
硫化步骤如下:•脱氧过程完成后,重新往循环氢压缩机入口注入 N2,开启循环氢压缩机,建立起气体循环,使系统的压力达到I.OMPaG,然后停止注入N2, 往系统中注入H2,使系统的压力达到1.6MPaG。
•氢氮混合气的循环流程为:依次通过循环氢压缩机入口分液罐 V1103、循环氢压缩机C11O1A/B、换热器E1101、E1102和加热炉F1101,然后进入反应器R1101,再经过换热器E1102,再经过跨线进换热器E1101 (不必经过E1207A/B),再经过空冷器 A1101,然后进入汽液分离罐V1102,再进入循环氢压缩机入口分液罐 V1103,再进入循环氢压缩机。
在此过程中将不相关的阀门关闭。
•开启加热炉F1101,对循环气进行加热,以20C/h〜30r/h的速度,将催化剂床层的温度升高到175°C时恒温。
•将硫化氢钢瓶连接到循环氢压缩机入口的注硫线上,开始注入硫化氢气体,注入速度为 90Kg/h。
•注入硫化氢60分钟后,取循环H2样品分析其中的硫化氢含量,每隔1小时取样分析一次,当连续两个样的硫化氢含量超过 5000 ppm时,停止硫化氢的注入。
注意床层温升,如果温升过高,需减少H2S的注入速度,同时及时从高分罐 V1102的脱水包中切水。
•床层继续升温,升到 200C时恒温,此过程的升温速度为 30 C /h。
继续每隔1小时取循环H2样品进行分析,如果硫化氢含量下降,继续以90Kg/h的速度向系统中注入硫化氢,直到连续取两个样的硫化氢含量大于5000ppm 时,停止硫化氢的注入。
注意床层温升,如果温升过高,需减少H2S的注入速度,同时及时从高分罐 V1102的脱水包中切水。
在此过程中,对所有高温法兰的螺栓重新把紧,防止系统泄漏。
-床层继续升温,升到 230C时恒温,此过程的升温速度为 30 C /h。
继续每隔1小时取循环H2样品进行分析,如果硫化氢含量下降,继续以 90Kg/h的速度向系统中注入硫化氢,直到连续取两个样的硫化氢含量大于5000ppm时,停止硫化氢的注入。
此阶段的恒温时间不得小于8 小时,并且注意床层温升,如果温升过高,需减少H2S 的注入速度,同时及时从高分罐 V1102 的脱水包中切水。
•床层继续升温,升到290C恒温,此过程的升温速度为20C /h〜30 C /h。
继续每隔1小时取循环H2样品进行分析,如果硫化氢含量下降,则继续以90Kg/h 的速度向系统中注入硫化氢,直到连续取两个样的硫化氢含量大于5000ppm时,停止硫化氢的注入。
注意床层温升,如果温升过高,需减少H2S的注入速度,同时及时从高分罐 V1102的脱水包中切水。
-290C恒温硫化结束后,调整循环氢中 H2S浓度至1.0〜2.0V%,提高反应器入口温度,此过程的升温速度为20C /h〜30C /h0当催化剂床层温度升至320C左右时,再恒温硫化一段时间。
及时从高分罐V1102 的脱水包中切水。
此后若满足以下条件,即可确认催化剂硫化结束。
a. 硫化剂的注入量已达到催化剂硫化理论需硫量的100〜120%;b. 催化剂床层基本无温升;c. 高分罐 V1102 的切水量无明显增加。
•催化剂预硫化最多需要大约 2000Kg的硫化氢,耗氢量大约10000Nm3。
预硫化完毕后,计算一下实际用的硫化氢的量,并与设计值相比较,如果相差很大,需要查明原因,并将少注入的硫化氢全部注入系统。
•催化剂硫化结束后,以每小时不超过30 C的速度将催化剂床层的温度降至160C,以备进料开车。
在降温过程中应停止注硫化氢或少量的注入,但任何时候循环氢中 H2S 含量不得低于 1000ppm。
催化剂干法预硫化期间注意的问题•系统升温到200C以上时需要进行装置试密,该重新紧固的螺栓必须重新紧固。
•催化剂预硫化一段时间后,必须定期从分离罐 V1102 和 V1103 底部脱水,结束硫化后必须全部将水排放干净。
对排放的含硫、酸性水称重计量并取样分析其硫含量,必要时应作催化剂硫化的硫平衡估算,评估催化剂的硫化效果。
•在H2S穿透催化剂之前,即循环氢中 H2S含量没有达到1000ppm之前,催化剂床层温度不得超过230 Eo•如因故中断硫化剂注入时,应将催化剂床层温度降至230E以下,若硫化剂注入中断时间较长,而循环氢中H2S 浓度又不能维持在1000ppm以上,则应将催化剂床层温度降至 175C。
催化剂湿法预硫化在反应系统有氢气循环,压力在 2.5MPaG,床层温度在230C以上,使用含链烷烃的直馏煤油或轻柴油为硫化油携带 CS2或DMDS硫化剂对催化剂进行预硫化,将催化剂的氧化态活性金属转化为相应的硫化态活性金属。
硫化步骤如下:•采购硫化油(含链烷烃的直馏煤油或轻柴油) ,采购数量需几乎充满整个系统。
然后注入进料缓冲罐 V1101,需要时通过反应进料泵P101A/B 输送到系统中。
•采购硫化剂(CS2或DMDS ),如果使用CS2采购数量大约2200Kg,若使用DMDS采购数量大约3000Kg。
然后注入专用储罐中,并且需要设置一台进料泵以便将其输送到系统中。
•脱氧过程完成后,停止注入N2,往系统中注入H2,开启循环氢压缩机,建立起气体循环,使系统的压力达到 2.5MPaG o•开启加热炉F1101,对循环气进行加热,以20 E /h〜30 E /h的速度,将催化剂床层的温度升高到150〜160Eo•开启进料泵P101A/B往系统中注硫化油(含链烷烃的直馏煤油或轻柴油),注入速度为55〜60吨/小时。
•建立油和气的循环。
气相的循环为:依次通过循环氢压缩机入口分液罐V1103、循环氢压缩机C1101A/B、换热器E1101、E1102和加热炉F1101, 然后进入反应器 R1101,再经过换热器 E1102,再经过跨线进换热器E1101 (不必经过E1207A/B),再经过空冷器 A1101,然后进入汽液分离罐V1102,再进入循环氢压缩机入口分液罐 V1103,再进入循环氢压缩机。
在此过程中将不相关的阀门关闭。
油的循环为:依次通过进料缓冲罐V1101、进料泵P101A/B、再经过跨线与循环气汇合进换热器 E1101(不必经过T1101)、E1102和加热炉F1101,然后进入反应器R1101, 再经过换热器 E1102, 再经过跨线进换热器 E1101(不必经过E1207A/B),再经过空冷器A1101,然后进入汽液高压分离罐V1102, 然后通过压力差由汽液高压分离罐V1102 液位控制返回到进料缓冲罐 V1101。
在此过程中将不相关的阀门关闭,打开相关的盲板和阀门。
•开启硫化剂进料泵往系统中注硫化剂(CS2或DMDS ),注入速度为90〜1 00Kg/h 。
•保持150〜160C恒温润湿催化剂2小时。
•待反应器催化剂床层温度稳定后,以20 C /h〜30 C /h的速度缓慢提升反应器入口温度,继续注入硫化剂,并取样检测循环H2中的H2S含量,在检测出H2S之前,催化剂床层任何一点温度不得超过230C o•继续注入硫化剂,每隔 1 小时取循环 H2 样品进行分析,当循环氢中的 H2S 含量达到1000ppm后,将催化剂床层温度调整到 230C。
然后每隔1 小时取循环 H2 样品进行分析,如果硫化氢含量下降,则继续以90〜100Kg/h 的速度向系统中注入硫化剂,直到连续取两个样的硫化氢含量大于5000ppm时,停止硫化剂的注入。
在230 C条件下,恒温至少8小时。
注意床层温升,如果温升过高,需减少硫化剂的注入速度,同时及时从高分罐V1102的脱水包中切水。
-床层继续升温,升到290C恒温,此过程的升温速度为 20C/h〜30C/h o 继续每隔1小时取循环H2样品进行分析,如果硫化氢含量下降,则继续以90〜100Kg/h的速度向系统中注入硫化剂,直到连续取两个样的硫化氢含量大于5000ppm时,停止硫化剂的注入。