制造电机定转子铁芯零件的现代冲压技术
铁芯冲压工艺步骤

铁芯冲压工艺步骤
铁芯冲压工艺是一种将金属板材加工成各种形状和尺寸的工艺技术,广泛应用于电机、变压器、电磁铁等电子和电力设备中。
铁芯冲压工艺步骤如下:
1.准备材料:首先需要准备一定数量的金属板材,通常采用硅钢片、铁片或
铜片,根据具体要求选择不同规格和厚度的材料。
2.剪裁和切边:将金属板材按照所需尺寸进行剪裁和切边,以便后续的冲压
加工。
3.模具设计:根据所需形状和尺寸设计模具,模具的质量直接影响到最终产
品的质量和生产效率。
4.冲压加工:将剪裁和切边后的金属板材放入模具中进行冲压加工,通过冲
压机的压力将金属板材加工成所需形状和尺寸。
5.质量检测:对冲压加工后的产品进行质量检测,检查产品的尺寸、形状、
表面质量等方面是否符合要求。
6.整理和包装:对合格的产品进行整理和包装,以便运输和储存。
铁芯冲压工艺需要使用高精度的冲压机和模具,同时对操作人员的技能和经验要求较高。
在生产过程中,还需要注意安全问题,如操作冲压机时要注意防止手部受伤等。
Y210—2型电动机定子铁芯冲压模具设计

Y210—2型电动机定子铁芯冲压模具设计一、产品零件的工艺分析零件简图该电动机定子铁芯的材料为电工硅钢片D21,钢板厚度0.50mm,具有良好的冲裁性能。
零件形状简单,对称,是由圆弧和直线组成。
对于冲小孔Φ5,冲复杂圆孔Φ80,按照冲压手册一般冲孔模对该材料(钢 <400MPa)可以冲压的最小的孔径为d≧t=0.5mm,因而小孔符合工艺要求。
最小孔边距为b=3.5mm≧t,因而符合孔边距工艺要求,以上分析均符合冲裁工艺要求。
由表1、2 查出冲裁件内外所能达到的经济精度为IT11,孔中心与边缘距离尺寸公差为±0.6,对于孔心距公差为±0.1,将以上精度与零件简图中所标注的尺寸公差相比较,可认为该零件的精度要求能够在冲裁加工中得到保证,其他尺寸标准、生产批量等情况,也均符合冲裁的工艺要求,故决定采用冲孔落料复合冲裁模进行加工,且一次成形。
表1 冲裁件内外形所能达到的经济精度二、模具类型的确定常见的模具形式可分为单工序模、复合模和级进模三种。
确定模具形式,应以冲裁工件的要求、生产批量、模具加工条件为主要依据。
冲压生产批量与合理模具形式见表3 ,单工序模、级进模和复合模的比较见表4通过以上关系比较,此工件是大批量生产,故采用冲孔落料复合冲裁模进行加工,且一次冲压成行。
所谓复合模具结构,就是在冲床的一次行程内,完成两道以上的冲压工序。
在完成这些工序过程中,冲件材料无需进给移动。
复合模具结构的优点(1)制件精度高。
由于是在冲床的一次行程内,完成数道冲压工序。
因而不存在累积定位误差。
使冲出的制件内外形相对位置及各件的尺寸一致性非常好,制件平直。
适宜冲制薄料和脆性或软质材料。
(2)生产效率高。
(3)模具结构紧凑,面积较小。
复合模具结构的选用原则:只有当制件精度要求高,生产批量大,表面要求平整时,才选用复合模具结构。
三、冲裁间隙的选用在冲裁模的设计中,凸凹模间隙的合理选取,是保证模具正常工作、提高冲片质量、延长模具寿命的一个关键因素。
简要分析小型电机定转子铁芯冲压级进式模具

微特电机SMALL & SPECIALELECTRICAL MACHINES1999年第27卷第1期vol.27no.1 1999简要分析小型电机定转子铁芯冲压级进式模具顾飞跃【摘要】通过对日本小型电机定转子铁芯生产技术及设备的简要分析,希望国内同行引进此种设备时得到一点借鉴,避免盲目引进,从而提高市场的竞争能力。
【关键词】小电机定转子铁芯冲压级进式冲压模具1 概述定转子铁芯级进式冲压模是一种冲制定转子冲片并把定转子冲片直接叠压成定子和转子铁芯的模具,这样可以省去定子铁芯的铆压或焊接工序及转子铁芯的齐片扭槽工序,并且定转子铁芯的长度及转子斜槽的角度可以通过调节模具中的控制器来改变。
该模具使得定转子铁芯单件制造工时短,生产批量大,制造成本低,并且生产出来的定转子铁芯尺寸精度高、电气性能好。
日本的电机生产厂与生产电机工装及设备的制造厂基本上是独立分开的,也就是讲,引进此设备前,对电机某零件部的质量要求及对方能达到什么要求必须了解清楚,做到知已知彼才能确保引进的设备接近时代的先进水平。
2 定转子铁芯生产技术日本小型电机定转子铁芯都是以带状卷料形式的硅钢片送料,通过级进式模具冲压而成的,定转子铁芯通过自身的扣片产生的毛刺和在模具高压缸中产生的变形力扣紧的,转子斜槽也是在级进模中完成的,转子的扭槽装置可以在上模完成也可以在下模完成,两种结构比较起来以上模扭槽结构为好,它生产的转子铁芯质量稳定性要高一些,扭槽可以达到的精度见图1,定转子铁芯厚度及转子扭槽角度均可调。
t—齿距;K—比例系数图 12.1 对硅钢片的技术要求以厚度δ0.5为例:δ=0.5±0.05,月亮弯≤0.5/m,毛刺≤0.05,材料宽度公差≤0.2。
2.2 对定转子冲片扣片形式的选择由于定转子铁芯的扣紧力是由本身扣片产生的,转子一般要求斜槽,转子铁芯铸铝,因此定转子铁芯对扣片产生扣紧力的要求是不同的,不同形状的机片形式产生的扣紧力也不同。
汽车驱动电机铁芯冲压工艺-概述说明以及解释
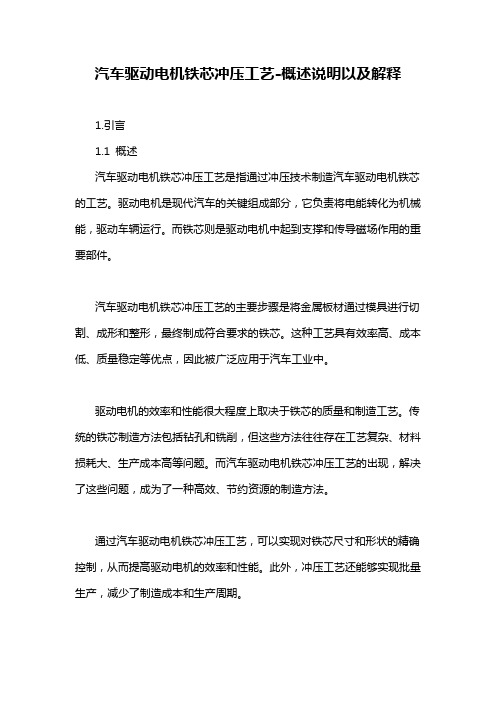
汽车驱动电机铁芯冲压工艺-概述说明以及解释1.引言1.1 概述汽车驱动电机铁芯冲压工艺是指通过冲压技术制造汽车驱动电机铁芯的工艺。
驱动电机是现代汽车的关键组成部分,它负责将电能转化为机械能,驱动车辆运行。
而铁芯则是驱动电机中起到支撑和传导磁场作用的重要部件。
汽车驱动电机铁芯冲压工艺的主要步骤是将金属板材通过模具进行切割、成形和整形,最终制成符合要求的铁芯。
这种工艺具有效率高、成本低、质量稳定等优点,因此被广泛应用于汽车工业中。
驱动电机的效率和性能很大程度上取决于铁芯的质量和制造工艺。
传统的铁芯制造方法包括钻孔和铣削,但这些方法往往存在工艺复杂、材料损耗大、生产成本高等问题。
而汽车驱动电机铁芯冲压工艺的出现,解决了这些问题,成为了一种高效、节约资源的制造方法。
通过汽车驱动电机铁芯冲压工艺,可以实现对铁芯尺寸和形状的精确控制,从而提高驱动电机的效率和性能。
此外,冲压工艺还能够实现批量生产,减少了制造成本和生产周期。
随着新能源汽车行业的迅速发展,对驱动电机的要求也越来越高。
而汽车驱动电机铁芯冲压工艺的应用将进一步推动驱动电机的技术进步和产业发展。
未来,随着冲压工艺的不断创新和完善,相信汽车驱动电机铁芯冲压工艺将发挥更大的作用,促进整个汽车工业的可持续发展。
文章结构部分的内容可以描述文章整体的构架和逻辑,以及各个章节的主要内容和目标。
可以按以下方式编写1.2文章结构部分的内容:本文将以《汽车驱动电机铁芯冲压工艺》为题,结构分为引言、正文和结论三个部分。
在引言部分,我们将首先对汽车驱动电机铁芯冲压工艺进行概述,简要介绍其背景和重要性。
其次,我们将介绍本文的结构和各个章节的安排,为读者提供整体的文章框架。
最后,我们将阐述本文的目的,即通过对汽车驱动电机铁芯冲压工艺的深入研究,探讨其优点和发展前景。
在正文部分,将详细展开对汽车驱动电机铁芯冲压工艺的概述,包括其原理、工艺流程、相关技术以及应用领域等内容。
特别关注汽车驱动电机铁芯冲压工艺的优点,探究其在提高动力系统效率、降低噪音和振动、提高产品可靠性等方面的优势。
钢板电机外壳冲压生产工艺研究

钢板电机外壳冲压生产工艺研究钢板电机外壳是电机的重要组成部分,起到保护电机内部零部件和外界环境隔离的作用。
冲压生产工艺是生产钢板电机外壳的常用工艺之一,本文将对钢板电机外壳冲压生产工艺进行研究和探讨。
一、引言钢板电机外壳是电机的外部保护罩,其质量和工艺直接关系到电机的性能和使用寿命。
冲压生产工艺是一种高效、精确的制造方法,可以快速、准确地生产出复杂形状的钢板件。
本文将以钢板电机外壳冲压生产工艺为研究对象,探讨其工艺流程、工艺参数以及工艺优化方法。
二、钢板电机外壳冲压工艺流程钢板电机外壳冲压工艺流程包括模具设计、钢板切割、冲孔、折弯、涂装等多个环节。
首先,根据钢板电机外壳的形状和尺寸要求,设计模具,包括上下模、顶针、导向柱等,以确保冲压过程中的准确性和稳定性。
然后,将钢板按照外壳的形状进行切割,得到初始的工件。
接下来,通过模具和冲压机的协同作用,对钢板进行冲孔,形成外壳的孔洞结构。
冲孔后,根据外壳的设计要求,采用专用的折弯机对钢板进行折弯,形成外壳的立体结构。
最后,对外壳进行清洗、喷涂等表面处理,提高外壳的美观性和防腐性。
三、钢板电机外壳冲压工艺参数钢板电机外壳冲压工艺参数包括冲压力、冲压速度、冲模间隙、冲模润滑、冲头形状等。
冲压力是指冲头对钢板施加的压力,需要根据钢板材料的硬度和厚度来确定,以确保冲孔的质量和效率。
冲压速度是指冲头下压的速度,过快或过慢都会影响冲孔的质量和冲压机的寿命。
冲模间隙是指上下模之间的间隙,需要根据钢板材料的厚度和型号来确定,以确保冲孔的准确性和一致性。
冲模润滑是为了减少冲压过程中的摩擦和磨损,可以采用润滑油或润滑脂进行润滑。
冲头形状也是影响冲孔质量的重要因素,常见的冲头形状有圆形、方形、椭圆形等,选择合适的冲头形状可以提高冲孔的效率和质量。
四、钢板电机外壳冲压工艺优化方法为了提高钢板电机外壳冲压工艺的效率和质量,可以采取以下优化方法。
首先,优化模具设计,减少冲压工序,降低生产成本。
电机定转子片冲压工艺及模具设计讲解
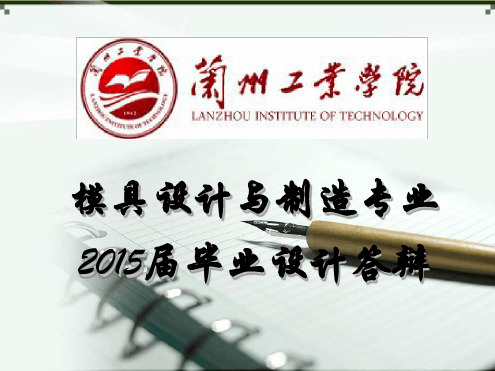
三、模具设计及主要的尺寸计算
1—下模座; 2、15—销钉; 3—凹模; 4—套;5—导柱; 6—导套; 7—上模座; 8—卸料 板9—橡胶; 10—凸模固定板; 11 —垫板; 12—卸料螺钉; 13—凸模; 14—模柄; 16、 17—螺钉
冲裁模典型结构与模具总体设计尺寸关系图
1.模具类型的选择
复合冲压是在压力机滑块的一次 行程中,在同一位置上,使材料顺 序完成几个冲压工序的方法,如落 料—冲孔、落料—拉深、落料—拉 深—冲孔、冲孔—翻边等复合工序, 该类模具称为复合模。生产现场应 用较多的有落料—冲孔复合模、落 料—拉深复合模和落料—拉深—冲 孔复合模等。
1)复合冲裁模的结构形式 复合冲裁模有倒装、顺装两种
结构形式。 倒装式复合模结构简单,使用
方便,应用较为广泛。 2)落料—拉深复合模
落料—拉深—冲孔复合模 3)带浮动模柄的落料—冲孔复合模
4)翻边复合冲模
2.工作部分的结构和尺寸的确定
工件的外形落料凹模采用整体 结构,直刃口形式。这种刃口强度 较好,孔口尺寸不随刃口的刃磨而 增大,适于形状复杂、精度高的工 件向上顶出的要求。
电机定、转子冲片工艺方案的种类
在冲裁工艺分析和技术经济分 析的基础上根据冲裁件的特点确定 冲裁工艺方案。冲裁工艺方案可分 为单工序冲裁、复合冲裁、级进冲 裁。
单工序冲裁是在压力机一次行 程,在模具单一的工位中完成单一 工序的冲压;复合冲裁是在压力机
一次行程中,在模具的同一工作位 置同时完成两个或两个以上的冲压 工序;级进冲裁是把冲裁件的若干 个冲压工序,排列成一定的顺序, 在压力机一次行程中条料在冲模的 不同工序位置上,分别完成工件所 要求的工序,在完成所有要求的工 序后,以后每次冲程都可以得到一 个完善的冲裁件,组合的冲裁工序 比单工序冲裁生产效率高,获得的
用于制造串激电机铁芯冲片的高速冲压连续模

用于制造串激电机铁芯冲片的高速冲压连续模引言随着现代电力工业的发展,电机的种类和工作要求越来越多样化。
其中,串激电机被广泛应用于家电、汽车、工业等领域。
铁芯冲片作为串激电机的关键部件之一,制造精度和质量对电机的使用寿命和性能都有着至关重要的影响。
为了提高铁芯冲片的制造效率和精度,高速冲压连续模应用于铁芯冲片的制造中,成为了当今冲压技术领域的一项重要技术。
冲压技术高速冲压技术是一种高效的铁芯冲片制造技术,其以精密连续模具为基础,通过快速的连续模冲击钢板,形成所需要的模具图形。
相对于常规冲压技术,其特点是速度快、效率高、精度高、成本低,因此得到了广泛的应用。
在现代工业制造中,高速冲压技术已成为了铁芯冲片制造的主要方式之一。
连续模连续模作为高速冲压技术中的关键技术之一,与铁芯冲片制造的质量和效率密切相关。
连续模是由多个模块组成的模具,通过连续模块之间的衔接和运动,在短时间内就能完成多次冲压动作,从而大大提高模具的使用效率。
具有连续模的高速冲压设备可以在高速运转的同时,可以快速完成各种异形、复杂模具的加工,达到了高效率、高精度、高稳定性的要求。
应用应用高速连续模进行铁芯冲片制造,可以达到以下好处:•提高生产效率:高速连续模的使用,可以减少冲压间隙,缩短制造周期,大大提高生产效率;•提高精度:连续模具的高精度制造,使得冲压过程中,铁芯成形的精度得到了保障,提高了产品质量;•降低成本:高速连续模具的使用能够提高冲压次数,减小铁芯冲片宽度,这样就能够减少废料的产生,从而降低了成本。
串激电机铁芯冲片制造中,高速冲压连续模应用是必不可少的。
通过这种先进的制造技术,可以大大提高电机的使用性能和寿命,实现高效、节能、可靠的工业生产。
电机铁心定转子片复合冲压工艺及模具设计
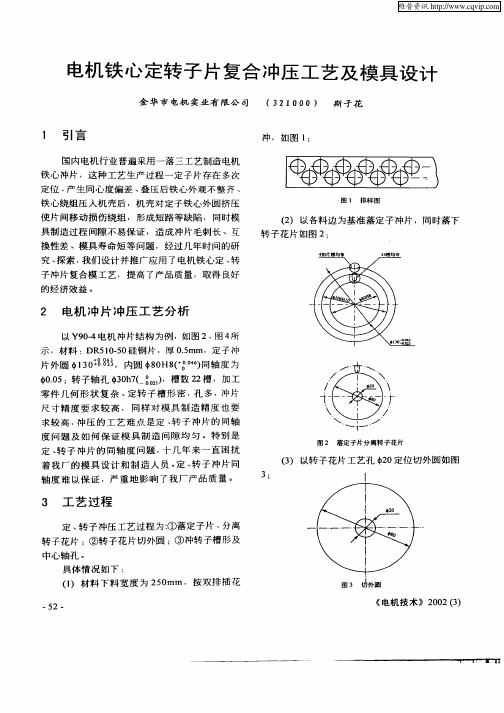
冲 ,如 图 1
铁 心 绕 组 压 入 机 壳 后 ,机 壳 对 定 子 铁 心 外 圆 挤 压 使 片 间 移 动 损 伤 绕 组 ,形 成 短 路 等 缺 陷 ,同 时 模 具 制 造 过 程 间隙 不 易 保 证 ,造 成 冲 片毛 刺 长 、互
出 ) 冲 裁 过 程 定 子 片 由弹 脱 料 装 置 采用 上 出料 方 ,
5 凸 凹模 l J 6 橡 胶 7 脱 料 板 8 定 子 脱 料 板 1 9 脱 料 板 1 凸 凹 摸 I 0 2J 1 下模 座 1
式 ,而 转 子 花 片 则 采 用 刚 性 打 料 在 冲床 上 行 时 通 过料杆 1 、打 料 板 2、脱 料 板 7打 落 ,并 由安 装在
中心轴孔 。 具体情况 如下 : () 材 料 下 料 宽 度 为 2 0 1 5 mm ,按 双 排 插 花
.
图 3
外 圆
52 .
《 电机 技 术 》2 0 3 0 2()
维普资讯
() 以转 子 片 工 艺 孔 定 位 冲 槽 形 及 中心 轴 孔 4
。
巾 . ;转子轴孔  ̄0 7一 ∞) 05 0 3h( : . ,槽数 2 槽 ,加工 2
零 件 几何 形状 复 杂 、 定转 子槽 形 密 , 多 , 片 孔 冲
尺 寸 精 度 要 求 较 高 , 同 样 对 模 具 制 造 精 度 也 要 求 较 高 , 压 的 工 艺 难 点 是 定 、 子 冲 片 的 同 轴 冲 转 度 问 题 及 如 何 保 证 模 具 制 造 间 隙 均 匀 。特 别 是 定 、 子 冲 片 的 同 轴 度 问 题 , 几 年 来 一 直 困 扰 转 十 着 我 厂 的 模 具 设 计 和 制 造 人 员 。 、 子 冲 片 同 定 转 轴 度 难 以 保 证 ,严 重 地 影 响 了 我 厂 产 品 质 量 。
- 1、下载文档前请自行甄别文档内容的完整性,平台不提供额外的编辑、内容补充、找答案等附加服务。
- 2、"仅部分预览"的文档,不可在线预览部分如存在完整性等问题,可反馈申请退款(可完整预览的文档不适用该条件!)。
- 3、如文档侵犯您的权益,请联系客服反馈,我们会尽快为您处理(人工客服工作时间:9:00-18:30)。
电机定转子铁芯零件的现代冲压技术邓卫国( 常州机电职业技术学院江苏常州213022 )[摘要]:介绍在制造电机定转子铁芯零件方面采用高精度、高效率、高寿命模具的现代冲压技术,配合高速冲床,实现高速自动化作业,提高了冲制铁芯零件的尺寸精度和生产效率,在大批量制造电机定转子铁芯零件方面有着非常现实的意义。
[关键词]:定子铁芯转子铁芯自动叠片带回转和扭斜自动冲压高速精密级进模Modern Stamping Technology Into The Motor LaminationDengWeiGuo( Tempel (Changzhou) Precision Metal Products Co., Limited Jiangsu Changzhou 213022 ) AbstractThis thesis introduces the modern stamping technology on producing the motor laminations, utilizing the dies with high precision, great efficiency and long life, the high speed presses, which has realized high-speed automatization, increased the precision and efficiency of the motor lamination parts, and the technology plays a practical action during volume-producing the motor lamination parts.Keywords:stator stack lam rotor stack lam auto-lamination indexing and skew auto-pressing high-speed precision progressive die1.引言现代冲压技术是集设备、模具、材料和工艺等多种技术于一体的高新技术。
高速冲压技术是近20年发展起来的先进成形加工技术。
电机定转子铁芯零件的现代冲压技术是用高精度、高效率、长寿命、集各工序于一副模具的多工位级进模在高速冲床上进行自动化冲制,其冲制过程是冲制条料从卷料上出来后,先经过校平机进行校平,再通过自动送料装置进行自动送料,然后条料进入模具,可以连续完成冲裁、成形、精整、切边、铁芯自动叠片、带扭斜叠片落料、带回转叠片落料等工序的冲制,到铁芯零件成品从模具中输送出来,整个冲图1 高速冲床冲制过程制过程都是在高速冲床上自动完成的,如图1所示。
随着电机制造工艺不断发展,现代冲压技术引用到制造电机铁芯方面的工艺方法,现在越来越多地被制造电机厂家所接受,制造电机铁芯的加工手段也越来越先进。
在国外,一般先进制造电机厂家,都采用现代冲压技术来冲制铁芯零件。
在国内,用现代冲压技术来冲制铁芯零件的加工方法正在进一步发展起来,而且这项高新制造技术日趋成熟,在电机制造行业中,这项制造电机工艺的优势已被许多制造电机厂家所重视。
用现代冲压技术来冲制铁芯零件与原来用普通模具及设备冲制铁芯零件相比较,具有冲制铁芯零件自动化程度高、尺寸精度高、模具使用寿命长等特点,适合于冲制件的大批量生产。
由于多工位级进模是集众多加工工艺于一副模具上的冲制,减少了电机的制造工序过程,提高了制造电机的生产效率。
2.现代高速冲压设备现代高速冲压的精密模具离不开高速冲床的配合,目前国内外现代冲压技术的发展趋势是单机自动化、机械化、自动送料、自动卸料、自动出成品,高速冲压技术目前在国内外得到了普遍发展。
电机定转子铁芯级进模的冲压速度一般为200~400次/min,多半是在中速冲压范围之内进行工作的。
冲制电机定转子铁芯带自动叠片的精密级进模对高速精密冲床技术要求是,冲床的滑块在下死点精度要求较高,因为影响到定转子冲片在模具內自动叠片形成铁芯过程的质量问题。
现在精密冲压设备正在向着高速度、高精度、稳定性好的方向发展,特别是近年来精密高速冲床发展很快,在提高冲制件生产效率方面发挥了重大的作用。
高速精密冲床在设计结构方面比较先进,制造精度又高,适合于多工位硬质合金级进模的高速冲压,可以大大提高级进模的使用寿命。
级进模所冲制材料是卷料形式,因此现代冲压设备都带有开卷机、矫平机等辅助装置,自动送料装置有:辊式、凸轮、机械无级调节式、齿轮式、数控无级调节式送料机等结构形式,分别与相适应的现代冲压设备配套使用。
由于现代冲压设备的自动化冲制程度高,且速度快,为充分保证模具在冲制过程中的安全性,现代冲压设备都配备有在发生失误情况下的电气控制系统,如模具在冲制过程中发生故障情况,则失误信号就会立即传送到电气控制系统,电器控制系统就会发出信号使冲床立即停止工作。
目前用于冲制电机定转子铁芯零件方面的现代冲压设备主要有:日本有:AIDA高速冲床、DOBBY 高速冲床、ISIS高速冲床,美国有:MINSTER高速冲床,台湾有:瑛瑜高速冲床等。
这些精密高速冲床,具有高的送料精度、冲压精度和机器的刚度、可靠的机器安全系统,其冲压速度一般多在200~600次/min范围,适合于冲制电机定转子铁芯的自动叠片和带扭斜、回转自动叠铆片的结构零件。
3.电机定转子铁芯的现代冲模技术3.1 电机定转子铁芯级进模概述在电机行业中,定、转子铁芯是电机上的重要零部件之一,它的质量好坏直接影响到电机的技术性能。
传统制作铁芯方法是用一般普通模具冲制出定、转子冲片(散片),经过齐片,再用铆钉铆接、扣片或氩弧焊等工艺过程制成铁芯,对于交流电机转子铁芯还需用手工进行扭转出斜槽,步进电机要求定、转子铁芯磁性能和厚度方向均匀,定子铁芯和转子铁芯冲片之间分别要求旋转一定的角度,如用传统方法制作,效率低,精度很难达到技术要求。
现在随着高速冲压技术的迅速发展,在电机、电器等领域,已广泛采用高速冲压多工位级进模制造自动叠片式的结构铁芯,其中定、转子铁芯还可以带扭转叠斜槽、冲片之间带大角度回转叠铆结构等,与普通冲模相比,多工位级进模具有冲制精度高、生产效率高、使用寿命长、所冲制铁芯尺寸精度一致性好、容易实现自动化、适合大批量生产等优点,是电机行业精密模具发展的方向。
定、转子自动叠铆级进模具有制造精度高、结构先进、带有技术性要求高的回转机构、计数分离机构及安全机构等,铁芯自动叠铆、转子带扭斜叠铆、大角度回转叠铆的冲制工步都是放在定、转子冲片落料工位上完成的。
级进模上的主要零件凸模、凹模都采用硬质合金材料,每磨一次刃口可冲150万次以上,模具总寿命在1.2亿次以上。
3.2电机定转子铁芯自动叠铆技术级进模上带自动叠铆技术就是要把原来传统制作铁芯的工艺过程(冲出散片-齐片-铆合)放在一副模具内完成,即在级进模的基础上增加了新的冲压工艺技术,除了冲定、转子上的轴孔、槽孔等冲片形状要求外,增设了定、转子铁芯叠铆需要的叠铆点及起叠铆点分离作用的计数孔的冲压工位,并将原来定、转子的落料工位改变成先起落料作用,然后使各冲片再形成叠铆过程和叠片计数分离过程(以确保铁芯厚度)的叠铆工位,如定、转子铁芯需要带扭转、回转叠铆功能的,在级进模转子或定子落料工位的下模上要带有扭转机构或回转机构,由叠铆点在冲片上不断改变或转动位置而实现这一功能的,从而满足在一副模具内自动完成冲片的叠铆和回转叠铆的技术要求。
3.2.1 铁芯自动叠片形成的过程是:在定、转子冲片适当部位上冲出一定几何形状的叠铆点,叠铆点的形式如图2所示,上部是凹陷形孔,下部是凸起的,然后将同一名义尺寸的上 一冲片凸起部分嵌入到下一冲片的凹陷形孔时,在模具中落料凹模收紧圈内自然形成“过盈”,达到紧固连接的目的,如图3所示。
在模具内铁芯形成的过程是,在冲片落料工位上使上一 片叠铆点的凸起部位正确地与下面一片的叠铆点凹形孔部位重合在一起,当上面一片受到落料凸模压力作用时,下面一片借助其外形与凹模壁摩擦所产生的反作用力使两片产生叠铆。
这样,通过高速自动冲床连续不断的冲制,就可以得到一片挨着一片排列、毛刺是同一方向而且具有一定叠厚的整齐铁芯。
3.2.2 铁芯叠片厚度的控制方法是,在铁芯预定的片数时,把最后一片冲片上的叠铆点冲穿,使铁芯按预定的片数分离,如图4所示。
在模具结构上设置有自动叠片计数分离装置,如图5所示。
在计数凸模上面有一个抽板机构,抽板由气缸带动,气缸动作由电磁阀控制,电磁阀根据控制箱发出的指令而动作。
冲床每一次行程信号都输入到控制箱里,当冲到所设定片数时,控制箱会发出信号,通过电磁阀和气缸,使抽板动作,从而使计数凸模达到计数分离的目的,即在冲片的叠铆点上达到计量孔被冲穿和不冲计量孔的目的。
铁芯的叠片厚度可以自行设定。
另外,有的转子铁芯的轴孔因支承结构的需要,要求冲制成有2段或3段台肩沉孔,如图6所示,级进模上要同时完成冲制这种有台肩孔工序要求的铁芯,可采用上述相类似的结构原理,模具结构如图7所示。
图2 冲片叠铆点结构 图3 铁芯自动叠片结构 图4 叠铆铁芯分离情况图5 铁芯叠片计数分离机构 1. 气缸、电磁阀 2.计数凸模 3. 抽板图6 转子铁芯台肩沉孔结构图7 冲制大小轴孔计数分离机构1.气缸、电磁阀2.计数轴孔凸模3. 抽板4. 上下移动凸模垫板3.2.3 铁芯叠铆结构形式有两种:第一种是密叠式,即叠铆成组的铁芯不需要在模具外再加压,出模即可达到铁芯叠铆的结合力。
第二种是半密叠式,出模时已叠铆的铁芯冲片之间有间隙,还需要再加压才能保证结合力。
3.2.4 铁芯叠铆的设置及数量的确定:铁芯叠铆点位置的选择应根据冲片的几何形状确定,同时考虑到电机的电磁性能及使用要求,模具上应考虑叠铆点的凸模、凹模镶块位置是否有干涉现象及落料凸模相应叠铆顶杆孔位置离边上距离的强度问题。
叠铆点在铁芯上分布应对称和均匀,叠铆点的数量及大小应根据铁芯冲片之间要求的结合力大小来确定,同时必须考虑到模具的制造工艺性。
如铁芯冲片之间带有大角度回转叠铆的,还要考虑叠铆点的等分要求等。
如图8所示。
图8 铁芯叠铆点分布图图10 叠铆点过盈量示意图图9 叠铆点几何形状3.2.5 铁芯叠铆点的几何形状有:(a)圆柱形叠铆点,适用于铁芯的密叠式结构;(b)V型叠铆点,该叠铆点的特点是铁芯冲片之间的连接强度大,适用于铁芯的密叠式结构和半密叠式结构;(c)L型叠铆点,该叠铆点形状一般用于交流电机转子铁芯的扭斜叠铆,适用于铁芯的密叠式结构;(d)梯形叠铆点,该叠铆点有园梯形和长梯形叠铆点结构之分,两者都适用于铁芯的密叠式结构,如图9所示。
3.2.6 叠铆点的过盈量:铁芯叠铆的结合力大小与叠铆点的过盈量有关,如图10所示,叠铆点凸台的外径D与内经d的尺寸差(即过盈量),由冲制叠铆点凸模与凹模的刃口间隙确定,所以选取合适的间隙是保证铁芯叠铆强度以及叠铆难易程度情况的一个重要部分。