一、液态金属成形过程及其控制
液态金属成形过程及控制
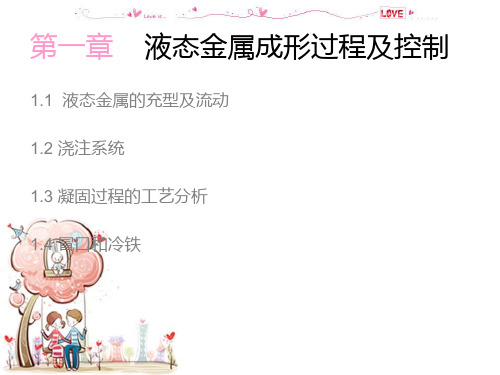
冒口。
冒口补缩原理
二、选择冒口位置的原则
1.冒口应就近设在铸件热节(hot spot)的上方或侧 旁; 2.冒口应尽量设在铸件最高、最厚的部位; 3.冒口不应设在铸件重要的、受力大的部位; 4.冒口不应选在应力集中处; 5.应尽量用一个冒口补缩几个热节或铸件; 6.冒口不应在加工面上。
金属液过滤器安放位置
泡沫陶瓷过滤器过滤机理
• • 1.“滤饼”机制 复杂的泡沫陶瓷结构,可以高效率 地机械挡渣,当金属液通过结构复 杂的泡沫陶瓷过滤器时,通过过滤 介质的机械分离作用,把大于过滤 器表面孔眼的夹杂物滤除,并使之 沉积在过滤器液态金属流入端,成 为过滤器的一个组成部分。随着夹 杂物在过滤器表面上堆积数量的增 多,逐渐形成了一层“滤饼”,使 金属液流道进一步变细,因而新增 的过滤介质表面可以滤除更为细小 的夹杂物。与此同时,介质内部也 有过滤作用,在贯穿于陶瓷体的众 多小孔中,有的呈现微小狭缝,有 的存在死角,这些变化不同的区域 都是截获夹杂物的可能位置。
第一章
液态金属成形过程及控制
1.1 液态金属的充型及流动 1.2 浇注系统 1.3 凝固过程的工艺分析 1.4 冒口和冷铁
1.1液态金属的充型及流动
• 概述:充型+凝固→铸造成形→质量 一、液态金属充型的水力学特征及在浇注系统中的流动 水力学特征: ①粘性流动←粘度→合金成分,温度,结晶 ②流动的不稳定性 ③散体材料的“多孔管流动”
铸件
1.位置(4)-阶梯式
a)多直浇道式 b)用塞球法控制式 c)控制各 组元比例式 d)带缓冲直浇道 e)带反直浇道式
2.按各单元断面积的比例
• 收缩式:A直﹥ A横﹥ A内 • 扩张式: A直﹤ A横﹤ A内 • 半扩张式: A直﹤ A横﹥ A内
液态金属简介
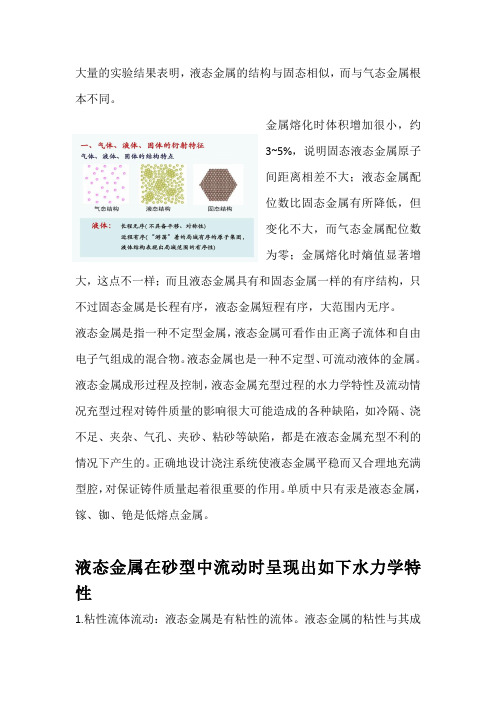
大量的实验结果表明,液态金属的结构与固态相似,而与气态金属根本不同。
金属熔化时体积增加很小,约3~5%,说明固态液态金属原子间距离相差不大;液态金属配位数比固态金属有所降低,但变化不大,而气态金属配位数为零;金属熔化时熵值显著增大,这点不一样;而且液态金属具有和固态金属一样的有序结构,只不过固态金属是长程有序,液态金属短程有序,大范围内无序。
液态金属是指一种不定型金属,液态金属可看作由正离子流体和自由电子气组成的混合物。
液态金属也是一种不定型、可流动液体的金属。
液态金属成形过程及控制,液态金属充型过程的水力学特性及流动情况充型过程对铸件质量的影响很大可能造成的各种缺陷,如冷隔、浇不足、夹杂、气孔、夹砂、粘砂等缺陷,都是在液态金属充型不利的情况下产生的。
正确地设计浇注系统使液态金属平稳而又合理地充满型腔,对保证铸件质量起着很重要的作用。
单质中只有汞是液态金属,镓、铷、铯是低熔点金属。
液态金属在砂型中流动时呈现出如下水力学特性1.粘性流体流动:液态金属是有粘性的流体。
液态金属的粘性与其成分有关,在流动过程中又随液态金属温度的降低而不断增大,当液态金属中出现晶体时,液体的粘度急剧增加,其流速和流态也会发生急剧变化。
2.不稳定流动:在充型过程中液态金属温度不断降低而铸型温度不断增高,两者之间的热交换呈不稳定状态。
随着液流温度下降,粘度增加,流动阻力也随之增加;加之充型过程中液流的压头增加或和减少,液态金属的流速和流态也不断变化,导致液态金属在充填铸型过程中的不稳定流动。
3.多孔管中流动:由于砂型具有一定的孔隙,可以把砂型中的浇注系统和型腔看作是多孔的管道和容器。
液态金属在“多孔管”中流动时,往往不能很好地贴附于管壁,此时可能将外界气体卷入液流,形成气孔或引起金属液的氧化而形成氧化夹渣。
4.紊流流动:生产实践中的测试和计算证明,液态金属在浇注系统中流动时,其雷诺数Re大于临界雷诺数Re临,属于紊流流动。
例如ZL104合金在670℃浇注时,液流在直径为20mm的直浇道中以50cm/s 的速度流动时,其雷诺数为25000,远大于2300的临界雷诺数。
金属液态成形工艺概述

铸造产品称为: 铸件、铸锭、铸坯、铸带等
一、金属液态成形工艺特点
1. 适应性强
铸件重量:几克 ~ 几百吨 铸件壁厚:0.5 毫米 ~ 1 米 铸件长度:几毫米 ~ 十几米 铸件材质:铁碳合金(鋳铁、鋳钢)、铝合金、铜合金、
镁合金、锌合金、钛合金、复合材料等
速箱体(灰口铸铁)
精密铸造件(不锈钢)
水轮机铸件(铜合金)
箱体(铝合金)
叶轮(钛合金)
一、金属液态成形工艺特点
1. 适应性强
铸件重量:几克 ~ 几百吨 铸件壁厚:0.5 毫米 ~ 1 米 铸件长度:几毫米 ~ 十几米 铸件材质:铁碳合金(鋳铁、鋳钢)、铝合金、铜合金、
镁合金、锌合金、钛合金、复合材料等
铸造方法几乎不受零件大小、形状和结构复杂程度的限制。
轧辊
异型件
装饰件
工艺品
一、金属液态成形工艺特点
2. 尺寸精度高
铸件比锻件、焊接件的尺寸精度高,更接近于零件的尺 寸,可节约大量的金属材料和机械加工工时。
一、金属液态成形工艺特点
2. 尺寸精度高
铸件比锻件、焊接件的尺寸精度高,更接近于零件的尺 寸,可节约大量的金属材料和机械加工工时。
形成的先进铸造技术
精密、优质化
精密成形与加工 近无缺陷成形
数字、网络化
数字造型 虚拟制造
网络制造
精确铸造成形 金属熔体的纯净化、致密化
铸造工艺CAD,铸造模具CAD/CAM一体化 铸造过程宏观模拟及工艺优化 铸件组织微观模拟及性能预测 分散网络化铸造系统
高效、智能化
快速制造 自动化制造系统
智能制造
快速原形及快速制模 铸造过程自动检测与控制,铸造机器人的应用
液态金属凝固成形的方法
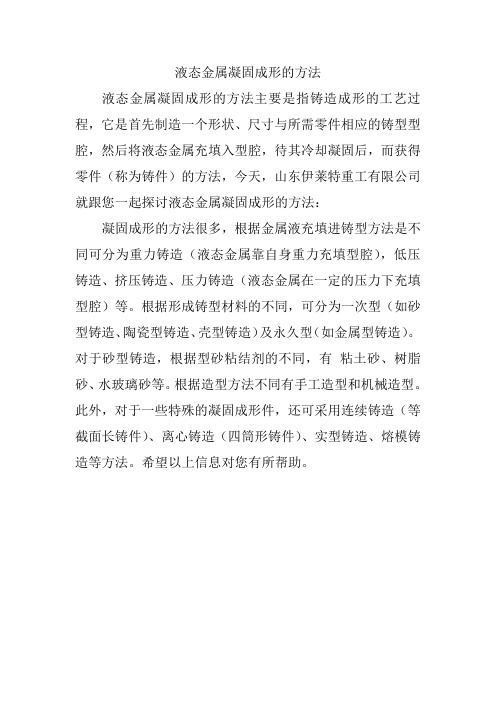
液态金属凝固成形的方法
液态金属凝固成形的方法主要是指铸造成形的工艺过程,它是首先制造一个形状、尺寸与所需零件相应的铸型型腔,然后将液态金属充填入型腔,待其冷却凝固后,而获得零件(称为铸件)的方法,今天,山东伊莱特重工有限公司就跟您一起探讨液态金属凝固成形的方法:
凝固成形的方法很多,根据金属液充填进铸型方法是不同可分为重力铸造(液态金属靠自身重力充填型腔),低压铸造、挤压铸造、压力铸造(液态金属在一定的压力下充填型腔)等。
根据形成铸型材料的不同,可分为一次型(如砂型铸造、陶瓷型铸造、壳型铸造)及永久型(如金属型铸造)。
对于砂型铸造,根据型砂粘结剂的不同,有粘土砂、树脂砂、水玻璃砂等。
根据造型方法不同有手工造型和机械造型。
此外,对于一些特殊的凝固成形件,还可采用连续铸造(等截面长铸件)、离心铸造(四筒形铸件)、实型铸造、熔模铸造等方法。
希望以上信息对您有所帮助。
液态金属加工中的凝固控制

液态金属加工中的凝固控制是一个重要环节,因为它对产品的质量和性能有着显著的影响。
通过控制凝固过程,可以确保金属材料得到充分凝固,形成良好的组织和性能。
下面将从三个方面详细介绍液态金属加工中的凝固控制。
一、温度控制在液态金属加工中,温度是影响凝固过程的关键因素之一。
为了确保金属材料充分凝固,需要对加工过程中的温度进行精确控制。
通常,通过使用水冷装置或热管理系统来调节和控制温度。
在加工过程中,温度的波动可能会对金属材料的组织和性能产生不利影响。
因此,需要定期检查冷却系统的运行状况,确保其正常工作。
二、速度控制液态金属加工中的速度控制也是至关重要的。
在金属凝固过程中,过快的加工速度可能会导致金属材料变形或产生裂纹。
因此,需要根据金属材料的性质和加工设备的性能,合理设置加工速度。
同时,在加工过程中还需要密切关注金属材料的流动情况,避免过热或过冷现象的发生。
三、冷却速率控制冷却速率是影响金属材料凝固速度和组织结构的重要因素之一。
通过控制冷却速率,可以调整金属材料的凝固过程,使其达到最佳的性能和组织。
在液态金属加工中,通常使用水冷或空气冷却等方式来控制冷却速率。
通过调节冷却水的流量或空气的压力,可以实现对冷却速率的有效控制。
此外,还可以通过调整模具的结构和形状来改变金属材料的凝固过程,以达到最佳的凝固效果。
总之,液态金属加工中的凝固控制是一个综合性的过程,需要从温度、速度和冷却速率等多个方面进行考虑和控制。
通过精确控制这些因素,可以确保金属材料得到充分凝固,形成良好的组织和性能,从而提高产品的质量和性能。
这需要操作人员具备丰富的经验和专业知识,以及对设备和材料的深入了解。
金属的液态成型

• 2. 球墨铸铁(简称球铁)
• ① 球墨铸铁球化、孕育处理 球铁是用灰口铸铁 成份的铁水经球化、孕育处理后制成的。为保证 球铁质量,生产中应注意下列几点:
• 球墨铸铁的化学成分选择 原铁水成分与灰口铸铁 原则上相同,但要求严格。
• 球化剂和孕育剂
• ②球墨铸铁的铸造性能和工艺特点
• 3.可锻铸铁
• 合理选择铸造合金
• 合理选用凝固原则
显微缩松
顺序凝固原则
阀体铸造方案
同时凝固原则
• (2)铸造内应力、变形和裂纹的形成和控制 • 铸件在凝固后继续冷却时,若在固态收缩阶段受
到阻碍,则将产生应力,此应力称为 铸造内应力。 它是铸件产生变形、裂纹等缺陷的主要原因。 • ① 铸造内应力形成过程 铸造内应力按其产生原 因,可分为热应力和机械应力两种。 • 热应力 铸件在凝固和冷却过程中,由于不同部位 不均衡的收缩而引起的应力称为热应力。 • 机械应力 铸件在固态收缩时因受到机械阻碍而形 成的应力,称为机械应力,也称收缩应力。 • ②铸件的变形与裂纹 当铸件中存有内应力时, 会使其处于不稳定状态。 • ③铸件变形、裂纹的控制 所有减少铸造内应力 的措施都有肋于控制铸件的变形和裂纹。
• ①金属型应保持合理的工作温度。
• ②为保护型腔和减缓铸型的传热速度,型腔表面和浇冒口 中要涂以厚度为0.2~1.0 mm的耐火涂料,以使金属液和 铸型隔开。
• ③因金属型无退让性,故应掌握好适宜的开型时间。
• ④为防止铸铁件产生白口组织,其壁厚一般应大于15 mm ,并控制铁水中碳、硅的质量分数不小于6%。
6.1.3 合金的偏析和吸气性
• 1.偏析 • 在铸件中出现化学成分不均匀的现象称为偏析。偏析使铸
件性能不均匀,严重时会造成废品。偏析分为晶内偏析和 区域偏析两类。 • 晶内偏析(又称枝晶偏析)是指晶粒内各部分化学成分不均 匀的现象。采用扩散退火可消除晶内偏析。 • 区域偏析是指铸件上、下部分化学成分不均匀的现象。为 防止区域偏析,在浇注时应充分搅拌或加速合金液冷却。 • 2.吸气性 • 合金在熔炼和浇注时吸收气体的性能称为合金的吸气性。
第七章 金属的液态成形

缩松:分散在铸件内部分散而细小的缩孔,大多分布在 铸件中心轴线处、冒口根部、内浇口附近或缩孔下方。形成 的原因与缩孔基本相同。 缩孔及缩松使铸件力学性能下降,防止其发生的主要 措施是“定向凝固”,通过增设冒口、冷铁等一些工艺措施 ,使凝固顺序形成向着冒口方向进行,如下图。远离冒口的 部位先凝固,冒口最后凝固,使缩松和缩孔产生在冒口处。 或在铸件厚大部位增设冷铁,以加快该处的凝固速度。
第七章 金属的液态成形
什么是金属的液态成形: 即将液态金属浇入与零件形状相适应的铸型空腔 中,待其冷却凝固,以获得毛坯或零件的工艺方法,亦 称铸造. 金属的液态成形的作用: 金属的液态成形是制造毛坯、零件的重要方法之一。 按铸型材料的不同,金属液态成形可分为砂型铸造和特 种铸造(包括压力铸造、金属型铸造等)。 其中砂型铸 造产品成本最低,应用最普遍,所生产的铸件要占铸件 总量的80%以上。但工艺过程较复杂不易控制,,铸件内 部常有缩孔、夹渣、气孔、裂纹等缺陷产生,导致铸件 力学性能,特别是冲击性能较低。
• (2) 浇注温度 • 浇注温度越高,液态合金的流动性越好,若过高,铸 件易产生缩松、粘沙等缺陷。一般浇注温度控制在:铸钢 1520~1620℃;铸铁1230~1450℃;铝合金680~780℃。 • (3)铸型填充条件 • 内浇道横截面小、型腔表面粗糙、型砂透气性差都会增加 液态合金的流动阻力;铸型材料的导热性过大,使液体金 属凝固快,同样会降低流动性。
f) 挖砂造型
活块造型是在制模时将铸件上的妨碍起模的小凸台,肋 条等这些部分作成活动的(即活块)。起模时,先起出 主体模样,然后再从侧面取出活块。其造型费时,工人 技术水平要求高。主要用于单件、小批生产带有突出部 分、难以起模的铸件。
活块造型
三箱造型的铸型由上、中、下三型构成。中型高度 需与铸件两个分型面的间距相适应。三箱造型操作 费工。主要适用于具有两个分型面的单件、小批生 产的铸件。
金属液态成形

材料成形技术基础第一章 金属液态成形金属液态成形(铸造):将液态金属在重力或外力作用下充填到型腔中,待其凝固冷却后,获得所需形状和尺寸的毛坯或零件的方法。
液态成形的优点:(1)适应性广,工艺灵活性大(材料、大小、形状几乎不受限制)(2)最适合形状复杂的箱体、机架、阀体、泵体、缸体等(3)成本较低(铸件与最终零件的形状相似、尺寸相近)主要问题:组织疏松、晶粒粗大,铸件内部常有缩孔、缩松、气孔等缺陷产生,导致铸件力学性能,特别是冲击性能较低。
分类:铸造从造型方法来分,可分为砂型铸造和特种铸造两大类。
其中砂型铸造工艺如图1-1所示。
图1-1 砂型铸造工艺流程图第一节金属液态成形工艺基础一、熔融合金的流动性及充型液态合金充满型腔是获得形状完整、轮廓清晰合格铸件的保证,铸件的很多缺陷都是在此阶段形成的。
(一)熔融合金的流动性1.流动性 液态合金充满型腔,形成轮廓清晰、形状和尺寸符合要求的优质铸件的能力,称为液态合金的流动性。
流动性差:铸件易产生浇不到、冷隔、气孔和夹杂等缺陷。
流动性好:易于充满型腔,有利于气体和非金属夹杂物上浮和对铸件进行补缩。
螺旋形流动性试样衡量合金流动性,如图1-2所示。
在常用铸造合金中,灰铸铁、硅黄铜的流动性最好,铸钢的流动性最差。
常用合金的流动性数值见表1-1。
表1-1 常用合金的流动性(砂型,试样截面8㎜×8㎜)2. 影响合金流动性的因素(1) 化学成份 纯金属和共晶成分的合金,由于是在恒温下进行结晶,液态合金从表层逐渐向中心凝固,固液界面比较光滑,对液态合金的流动阻力较小,同时,共晶成分合金的凝固温度最低,可获得较大的过热度,推迟了合金的凝固,故流动性最好;其它成分的合金是在一定温度范围内结晶的,由于初生树枝状晶体与液体金属两相共存,粗糙的固液界面使合金的流动阻力加大,合金的流动性大大下降,合金的结晶温度区间越宽,流动性越差。
Fe-C合金的流动性与含碳量之间的关系如图1-3所示。