抽油机井举升工艺方案设计方法研究
油井高效举升配套工艺与合理匹配探究

油井高效举升配套工艺与合理匹配探究随着油田勘探开发的不断深入,油井产量的提高成为油田开发中的一个重要环节。
而油井的高效举升是影响产量的重要因素之一。
为了实现油井高效举升,需要配备合适的工艺与设备,并进行合理匹配。
本文将从油井高效举升的概念入手,探讨油井高效举升配套工艺与合理匹配的关键问题。
一、油井高效举升的概念油井高效举升是指通过合理的工艺与设备,将地下油气输送到地面进行处理和加工的过程。
高效举升要求能够提高油井的产量和提高采油效率,最大限度地利用油田资源。
高效举升还要求在保证安全的前提下,实现节能减排,降低开采成本,提高经济效益。
1. 油层地质条件:不同的油层地质条件对油井的举升效果会产生重要影响。
比如油层的压力、渗透率、黏度等因素都会影响油井的产量和举升难度。
2. 举升设备和工艺:举升设备和工艺的选用对油井的举升效果至关重要。
包括泵及其类型、管道输送系统、控制系统等设备,以及举升操作流程、油井作业计划等工艺。
3. 油井状态管理:油井的状态管理包括油井的维护、检修、保养等方面。
合理的油井状态管理可以确保油井的正常运转,保证举升的高效进行。
4. 油井管理人员技术水平:油井管理人员的技术水平和管理经验也会直接影响油井的举升效果。
只有具备丰富的实践经验和专业知识的管理人员,才能有效应对各种复杂情况,确保油井的高效举升。
1. 泵类型的选择:油井举升设备中最为关键的部分是泵。
根据油井的地质条件和产量要求,选择合适类型的泵是至关重要的。
比如对于高产量油井,常采用离心泵;对于低产量油井,常采用柱塞泵。
还需考虑泵的材质、耐磨性、耐腐蚀性等因素。
2. 管道输送系统:管道输送系统的设计和布置对油井举升效率有着直接的影响。
合理的管道布局和优化的输送系统可以减少泵功耗,减少油品损耗,提高举升效率。
3. 控制系统和监测系统:举升过程中的控制和监测系统必须具备高度的可靠性和精度。
只有通过科学的控制和实时监测,才能保证油井的安全和稳定的运行。
油井举升工艺技术

• 根据所选择的设备和生产需要,确定设备的 工作参数。
举升工艺技术-2009
几种举升方式适用条件
-14-
项目 排量 (m3/d) 泵深
井况
其它
条件 正常工作范围 目前最大排量 正常工作范围 目前最大泵深 小井眼多层完
井 斜井及弯曲井
高油气比
高粘油
含砂
有杆泵 1~200
-32-
沉砂式防砂泵
●砂粒可通过沉砂外管沉入泵下 尾管中。
●泵筒上部装有挡砂滑块,停泵 时可防止砂粒进入泵筒与柱塞之 间造成卡泵。
●规格:φ38、φ44、φ57 。
举升工艺技术-2009
长柱塞防砂泵
●采用长柱塞、短泵筒结构, 长柱塞的搅动防止砂粒沉积 。
●柱塞上阀罩始终处于泵筒 外,防止砂粒进入泵筒与柱塞 间隙。
qo
1 0.2
pwf pr
0.8
pwf pr
2
qo max
c.根据给定的流压及计算的相应产量绘制IPR曲线
举升工艺技术-2009
单相流与两相流的结合(PI-IPR)方法
-12-
当油藏压力和井底流压 高于饱合压力时,油流入 曲线在Pr和饱合压力Pb之 间为一直线,当Pwf<Pb时 ,流入动态曲线为二次曲 线。描述这种油藏的油井 流入,用PI-IPR曲线法.
500 〈3000 限
环空排气,气锚效 果一般
可用稠油泵抽,系 统较好
易卡泵可用砂锚一 般
电潜泵 80~905
8744 3000 4572
均不适
小斜度适宜,弯曲 受限
对气敏感,分气效 果一般
油井举升方式优化调整探索与实践

一、油田举升设备存在问题1.产能足与设备举升能力不匹配通过现场生产数据统计,部分井其设备无法满足生产。
(1)螺杆泵井方面。
调查2016年底数据,有145口大泵型(1200以上泵型)且高产的螺杆泵井存有上产空间,平均日产液130t,动液面356m,平均转速95.9r/min。
其中有6口井,平均日产液大于190t,螺杆泵举升设备已无法满足生产需求,可更换电泵设备。
2)抽油机井方面。
有64口井机型、泵型、参数已经匹配到极限,但该井具有产能足、液面浅等特点,有一定的上产空间。
2.举升设备使用效率低(1)电泵井效率低,目前采用掺液的方式维持生产。
经统计,有8口低产能电泵井,平均单井日产液81t,日耗电858kWh,是同产量抽油机井、螺杆泵井耗电量的4倍多。
2)抽油机井使用效率低,一般情况下14型抽油机应匹配83mm 或95mm的抽油泵,但统计了200口14型抽油机井,其中有127口井由于产液低,匹配了57mm和70mm的抽油泵,由此造成设备使用的资源浪费。
二、举升方式设计原则及技术解决方案1.抽油机机型设计目前抽油机井泵效一般最大按60%设计。
结合产液情况,选择57、70、83、95m m抽油泵。
根据实际情况,产液Q≤60t/d的井采用57mm泵,60t/ d<Q≤90t/d的井采用70mm泵,90t/d <Q≤115t/d的井采用83mm泵,产液Q>115t/d的井采用95mm泵。
根据产液量、泵型,参照抽油机的承载标准(载荷利用率小于或等于95%或扭矩利用率小于或等于90%)设计机型。
2.螺杆泵设计根据螺杆泵排量进行设计。
由于目前大泵型螺杆泵存在反转的安全隐患,故现场一般使用800以下的泵型。
3.电泵设计根据电泵排量进行设计。
4.方案设计在以往的举升方式“双转”的过程中,更换下来的地面设备、井下杆管会被暂时存放,以备他用,一定程度上造成不必要的浪费;为此,方案设计要结合检泵时机与地质预产。
以“泵效最高,设备吨液单耗最低”为匹配原则,利用原井管柱及机组,同步开展举升方式互换调整以及检泵作业,最大限度地降低成本投入,盘活资产。
桩西油田大斜度井井筒举升工艺研究与应用

沦下入深度的桩5 、7 . t 2 4 8 块深抽直井采取 “ , 杆柱扶 正 、配合 油管锚 定 和底部 J重技 术”减轻弹性弯曲造成的管杆 偏磨 ②对超过 D J u 级杆 理 沦下入深度油井和偏磨严重 、屡次断脱 井 , 用 “ 应 连续杆 、高强度 杆” ,提高杆 自身强度 ,I时采片油管锚锚 定 , 油杆扶 正等措施避 司 j 抽 免泵上油管受 压弯曲使 管 杆磨损 。
片, { 然而 ,在开发这些区块的过程q ,也陆续 面临着 新的大斜 度井开 J 发的难题 ,井斜角越来越大 、 斜点越 来越浅 、井身轨迹也越来越复 造
杂
器,把抽 ig. 的偏磨点转移到扶正. 上 ;二是实现均 匀磨损的技 l f 柱上 j 器 术 ,主要 是指旋转抽 油杆和旋转油管装置等 ;三是降低杆柱偏磨速度 的技 术 ,主要是指 采用经表面 处理的油管 、抽油杆和耐磨接箍以及缓 蚀 剂技术 桩 西采油厂结合现场实际情况 ,经过 多年室内研究和现场 试验 ,形 成了一 系列的防偏磨技术 系列. 、
23 常规排量油井的防偏 磨技 术 . 对于常规排量油井的杆管偏磨主要I 素有 : 机械磨损:由于井 ①
身 质量 原凶( 井斜 、挠 曲J 以及抽油杆在轴 向载荷作用下的弯 曲,造 成 抽油杆与油管直接接触 ,在抽油秆上 、下往复运动过 程中产生机械磨
损. ②磨料磨损 :油管内充满了流体 ,这种来 自 层的流体 含有 不I 地 州 性质的岩眉 , 这些岩屑的存在 使得抽 油杆 与油管之 『 的磨损 成为磨料 H J
在进行 偏磨治理的 l时 ,也配套了相关的技术进一步减缓油井偏 - j 磨 ,主要是针对防腐的配套技 术。 ( ) 用阴极 保护器 防腐 。通过在 泵下 尾管上接阴极 保护 器的 1应
油井高效举升配套工艺与合理匹配探究

油井高效举升配套工艺与合理匹配探究随着石油工业的发展,油田开采已经成为了能源行业的重要组成部分。
在油田开采的过程中,油井高效举升配套工艺和合理匹配是非常重要的一环。
本文将就油井高效举升配套工艺与合理匹配进行探究,从而为油田开采提供更好的技术保障和支持。
一、油井高效举升配套工艺在油田开采的过程中,油井高效举升配套工艺是非常重要的一部分。
油井高效举升配套工艺主要包括以下几个方面:1. 举升系统设计:举升系统是油井开采的关键设备之一,其设计要根据具体油井的情况来确定,包括油井的深度、产量、地质条件等因素。
要保证举升系统设计合理,能够有效提高油井开采效率,降低成本。
2. 举升设备选型:举升设备的选型也是非常重要的一环,要根据油井的具体情况来选择合适的设备,包括泵浦、泵杆、吊卡等。
要考虑设备的性能、可靠性、经济性等因素,从而保证举升设备的正常运行。
3. 举升工艺优化:举升工艺的优化对于提高油井开采效率也非常重要。
可以通过优化举升参数、提高油井产量、降低能耗等方式进行工艺优化,从而达到高效举升的目的。
二、合理匹配探究在油井高效举升的过程中,合理匹配也是非常重要的一环。
合理匹配涉及到举升设备、工艺参数、油井的特性等多个方面,要保证各个方面的匹配能够达到最佳效果。
1. 设备与工艺的匹配:举升设备与工艺的匹配非常重要,要根据油井的特性来选择合适的设备,并确定合理的工艺参数,从而保证设备与工艺之间的匹配能够达到最佳效果。
2. 工艺参数的调整:工艺参数的调整对于油井高效举升也非常重要。
要根据具体油井的特性来调整工艺参数,包括举升速度、液面控制、油井稳定性等参数,从而保证高效举升。
3. 资源的合理配置:在油井的运营过程中,资源的合理配置也非常重要。
要合理配置人力、物力、财力等资源,从而保证油井的高效开采。
油井高效举升配套工艺与合理匹配的意义是非常重大的,它关系到油井开采的效率、成本、安全等多个方面。
1. 提高开采效率:油井高效举升能够提高油井的开采效率,从而提高石油产量,降低成本,增加经济效益。
油井高效举升配套工艺与合理匹配探究
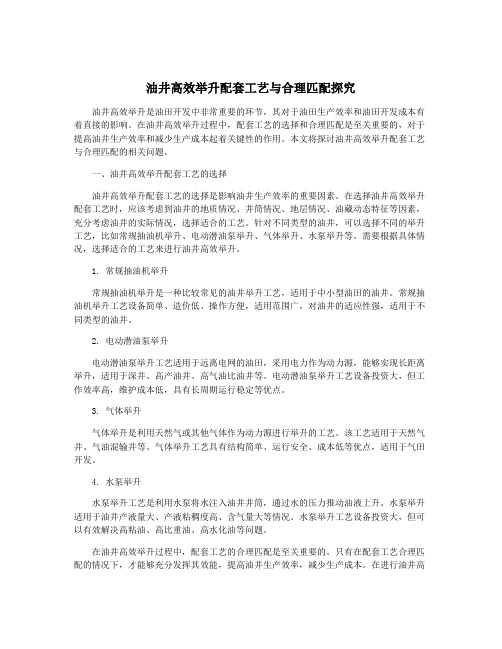
油井高效举升配套工艺与合理匹配探究油井高效举升是油田开发中非常重要的环节,其对于油田生产效率和油田开发成本有着直接的影响。
在油井高效举升过程中,配套工艺的选择和合理匹配是至关重要的,对于提高油井生产效率和减少生产成本起着关键性的作用。
本文将探讨油井高效举升配套工艺与合理匹配的相关问题。
一、油井高效举升配套工艺的选择油井高效举升配套工艺的选择是影响油井生产效率的重要因素。
在选择油井高效举升配套工艺时,应该考虑到油井的地质情况、井筒情况、地层情况、油藏动态特征等因素,充分考虑油井的实际情况,选择适合的工艺。
针对不同类型的油井,可以选择不同的举升工艺,比如常规抽油机举升、电动潜油泵举升、气体举升、水泵举升等。
需要根据具体情况,选择适合的工艺来进行油井高效举升。
1. 常规抽油机举升常规抽油机举升是一种比较常见的油井举升工艺,适用于中小型油田的油井。
常规抽油机举升工艺设备简单、造价低、操作方便,适用范围广,对油井的适应性强,适用于不同类型的油井。
2. 电动潜油泵举升电动潜油泵举升工艺适用于远离电网的油田,采用电力作为动力源,能够实现长距离举升,适用于深井、高产油井、高气油比油井等。
电动潜油泵举升工艺设备投资大,但工作效率高,维护成本低,具有长周期运行稳定等优点。
3. 气体举升气体举升是利用天然气或其他气体作为动力源进行举升的工艺。
该工艺适用于天然气井、气油混输井等。
气体举升工艺具有结构简单、运行安全、成本低等优点,适用于气田开发。
4. 水泵举升水泵举升工艺是利用水泵将水注入油井井筒,通过水的压力推动油液上升。
水泵举升适用于油井产液量大、产液粘稠度高、含气量大等情况。
水泵举升工艺设备投资大,但可以有效解决高粘油、高比重油、高水化油等问题。
在油井高效举升过程中,配套工艺的合理匹配是至关重要的。
只有在配套工艺合理匹配的情况下,才能够充分发挥其效能,提高油井生产效率,减少生产成本。
在进行油井高效举升时,需要从油井的地质情况、井筒情况、地层情况、油藏动态特征等方面出发,选取适合的举升工艺,并做好相应的配套工艺的合理匹配。
抽油机井举升工艺方案设计方法研究

抽油机井举升工艺方案设计方法研究目前,我国的科技发展十分想迅速,为了保证抽油机举升工艺系统满足生产要求、提高整个系统运行的稳定性、延长设备的整体寿命,需要对抽油机举升工艺系统进行优化设计。
根据举升工艺方案设计思路,对每一项设计内容的预测方法进行归纳汇总,并对应用中的注意事项及局限性进行分析,对抽油机井举升工艺方案设计起到积极地指导作用。
标签:抽油机;举升工艺;方案;设计方法0 引言如今我国对油田资源的开发开始进入后期阶段,当前因为针对聚合物驱油技术的开发手段与运用技术都在不断完善,我厂实践所汇集的数据也显示抽油机井检泵率指标指数也节节攀升,从举升工艺“硬件”潜力看,基本上达到了极限。
今后降低其检泵率的重要举措是,从举升工艺的管理方面出发,研究也进入了后期阶段,通过完善相关的工作制度,保证抽油机井的合理运行,除此之外,还希望达成抽油机稳定、长期的生产,这对油田开发经济效益的提高有着十分重要的作用。
1 抽油机井举升工艺适应性分析系统动态控制图和参数1.1 抽油机井地面设备动态控制图1)参数的选择能够反映抽油机井地面设备运转的主要特性参数有悬点载荷、曲柄轴输出扭矩、电机实耗功率。
2)驴头悬点载荷驴头悬点载荷是反映抽油机井的工作能力的重要参数之一,也是选型的主要依据,当抽油机工作时,驴头悬点主要承受以下五种载荷,即:(1)抽油杆杆柱重;(2)油管内活塞以上液柱重;(3)抽油杆柱和液柱在运转时所产生的惯性载荷;(4)抽油杆柱和液柱在运转时所产生的振动载荷;(5)活塞与泵筒、抽油杆与油管内壁的摩擦,以及抽油杆与液柱、液流与油管内壁的摩擦等。
若不考虑摩擦载荷的影响,抽油机井悬点最大载荷Pmax和最小载荷Pmin:Pmax=Wl+Wr(1+SN2/1790)Pmax——抽油机井悬点最大载荷,单位(N);Wl——柱塞以上液体的重力,单位(N);Wr——杆柱在空气中的重力,单位(N);SN2/1790——无因次动载荷系数;Pmin=Wrl-Wr×SN2/1790Wrl——杆柱在液体中的重力,单位(N);抽油机井负载利用率f:f=P实际/P铭牌×100%P实际——抽油机现场实测载荷,单位(KN);P铭牌——抽油机铭牌允许最大载荷,单位(KN);3)减速箱曲柄轴输出扭矩减速箱曲柄轴输出扭矩是衡量抽油机运转的重要技术参数,其经验公式M 实际:M实际=30S-0.236S×(Pmax-Pmin)抽油机井减速箱曲柄轴输出扭矩利用率M:M=M实际/M铭牌×100%M实际——抽油机减速箱曲柄轴实测输出扭矩,单位(KNm);M铭牌——抽油机减速箱曲柄轴铭牌输出最大扭矩,单位(KNm).1.2 抽油机井地面设备适应性动态控制图的绘制此时若是将期减速箱扭矩利用率转变成为X轴的情况下,那么可以把负载利用率当做四Y轴,再构建相应的直角坐标系,此时绘制出的控制图能够检验抽油机的运转中液量和泵径,之间的具体运行是否完全匹配,如果电机功率的利用率为X轴,那么可以Y轴的负载利用率具体来描绘出相关的适应性动态控制图,这个绘制的图片能够具体检验液量与电机相互间是否完全匹配。
油井高效举升工艺与优化匹配技术

技术与检测Һ㊀油井高效举升工艺与优化匹配技术曾立国摘㊀要:采用配套工艺既能充分发挥和协调油层的供液潜力及抽油设备的排液能力ꎬ又可以解决杆管失稳弯曲造成的杆柱冲程损失及偏磨问题ꎬ实现了抽油泵连续高效举升ꎮ现场应用表明ꎬ采用配套工艺ꎬ抽油泵平均泵效提高18%ꎬ免修期延长ꎬ收到良好应用效果ꎮ关键词:油井ꎻ高效举升ꎻ优化匹配一㊁技术研究(一)小直径抽油泵小直径抽油泵改变了抽油泵的进排油方式ꎬ将游动阀组设计在泵筒外ꎬ固定在泵筒的下端ꎬ使其阀球直径不受泵径限制ꎬ可增大阀球直径ꎬ加大油流通道ꎮ此外ꎬ阀球质量的增加使得阀球关闭及时ꎬ工作灵活ꎬ增加了抽油泵的可靠性ꎮ小直径抽油泵主要由柱塞㊁泵简㊁加长筒㊁进油阀组和出油阀组等组成ꎬ上冲程时ꎬ抽油杆柱带动柱塞上行ꎬ柱塞下部的空腔体积增大ꎬ其腔内的压力下降ꎬ进油阀打开ꎬ井内原油经进油阀和出油阀的侧面通道进入柱塞下部的空腔内ꎮ下冲程时ꎬ柱塞下部的空腔体积减小ꎬ其腔内的压力上升ꎬ进油阀关闭ꎬ空腔内的原油经出油阀的侧面通道向下流动ꎬ再从出油阀的中部向上打开出油阀排至油管ꎬ然后被排到地面ꎮ(二)抽油杆防失稳技术低产油井大都供液不足ꎬ需要深抽ꎬ而下部抽油杆柱失稳弯曲是造成杆柱冲程损失及杆管偏磨的直接原因ꎮ克服抽油杆下行阻力ꎬ消除振动载荷的影响ꎬ要从抽油杆集中加重和抽油杆缓冲补偿两方面入手ꎬ才能有效解决抽油杆失稳的问题ꎮ1.抽油杆集中加重技术有杆泵在抽油过程中ꎬ抽油泵活塞下行过程中由于受阻力的影响ꎬ导致下部抽油杆柱失稳弯曲ꎬ造成杆管偏磨ꎬ摩擦阻力增加ꎮ抽油杆集中加重技术就是在抽油杆底部采用防偏磨加重抽油杆ꎬ降低中和点的位置ꎬ以解决抽油杆失稳问题ꎮ防偏磨加重抽油杆主要由中心杆㊁加重外管和防磨滑套等组成ꎬ加重外管套装在中心杆外ꎬ防磨滑套套装在加重外管外ꎮ防偏磨加重抽油杆位于杆柱的最下端ꎬ抽油时ꎬ中心杆承受载荷ꎬ外管起到加重的作用ꎬ中心杆受拉扶正外管ꎬ提高了杆柱的稳定性ꎮ同时外管的重力通过上管压下管的方式向下传递ꎬ集中加到抽油泵活塞上ꎬ使抽油杆柱的中和点下移ꎬ以解决抽油泵活塞下行阻力造成的下部抽油杆柱失稳弯曲及杆管偏磨问题ꎮ2.抽油杆缓冲补偿技术抽油杆缓冲补偿技术主要是采用抽油杆补偿器来解决振动载荷造成的杆柱失稳弯曲及杆管偏磨问题ꎮ抽油杆补偿器主要由上接头㊁中心杆㊁外筒和下接头组成ꎮ上接头与中心杆连接ꎬ外筒套装在中心杆外ꎬ外筒与中心杆之间可以相对滑动ꎮ抽油杆补偿器连接在抽油杆柱的失稳部位ꎬ抽油杆失稳弯曲之前ꎬ外筒与中心杆之间相对滑动ꎬ抽油杆柱的弹性势能通过抽油杆补偿器转化为抽油杆柱的重力势能ꎬ使抽油杆失稳弯曲的弹性力得到释放ꎬ进而提高抽油杆柱的稳定性ꎮ同时在液体阻尼的作用下ꎬ抽油杆柱上的振动载荷快速衰减ꎬ抽油杆柱不会失稳ꎬ抽油杆与油管之间也不会产生接触压力ꎬ从而防止抽油杆与油管之间的偏磨ꎮ(三)杆管减磨接箍技术低产油井中ꎬ除了抽油杆应用常规抗磨副减轻本体偏磨外ꎬ油管端部㊁抽油杆接箍磨损也比较突出ꎮ因此ꎬ研制了抽油杆㊁油管减磨接箍ꎬ解决了因油管㊁抽油杆接箍磨损造成的管杆失效问题ꎮ1.抽油杆减磨接箍抽油杆减磨接箍是在普通抽油杆接箍表面熔结高强度非金属材料ꎬ该材料主要由高强度碳纤维及石墨等材料熔结而成ꎬ具有强度高㊁耐腐蚀和摩擦因数低的特点ꎬ与普通油管配套使用ꎬ能有效保护油管免受磨损ꎮ2.油管减磨接箍针对油管端部磕碰磨损问题ꎬ对油管接箍内表面结构进行了圆滑过渡设计ꎬ内孔尺寸设计为硒lmmꎬ并对内表面进行了硬化光洁处理ꎮ当抽油杆接箍经过油管端部时ꎬ因有油管减磨接箍的扶正和圆滑过渡设计ꎬ能有效消除抽油杆接箍与油管端部的碰撞和切屑磨损ꎬ大大减缓杆管接箍的磨损ꎮ(四)低产井优化设计技术低产井液面低㊁泵挂深ꎬ杆柱承受载荷加大ꎬ抽油杆断脱和生产故障率增加ꎮ据统计ꎬ油田近三年因杆柱断脱造成检泵326井次ꎮ为此ꎬ研制了低产井有杆泵优化软件ꎮ在油井产能分析的基础上ꎬ进行举升工艺设备适应性分析和生产参数的优化设计ꎬ具有油井不动管杆柱的抽汲参数调整和新井或措施井抽油设备选择与抽汲参数设计2大计算功能ꎬ并实现了加重杆㊁补偿器和减磨接箍安装位置的优化设计ꎬ具体程序框图见图1ꎮ图1 低产井优化流程框图二㊁关键技术(一)小直径抽油泵技术改变抽油泵的进排油方式ꎬ将游动阀组设计在泵筒外ꎬ固定在泵筒的下端ꎬ其阀球直径不受泵径限制ꎬ在增大阀球直径㊁加大油流通道的同时ꎬ可形成更小直径抽油泵ꎬ进一步加深泵挂ꎬ对低产井有更好的适应性ꎮ(二)抽油杆防失稳技术防偏磨加重抽油杆和抽油杆补偿器综合应用ꎬ克服了抽油杆柱下行阻力ꎬ改善了杆柱的受力状况ꎬ减轻杆柱的失稳弯曲ꎬ消除振动的影响ꎬ有效地解决了抽油杆柱失稳的问题ꎮ(三)防偏减磨技术抽油杆减磨接箍无活塞叠加效应ꎬ摩擦因数小ꎬ不增加下行阻力ꎮ油管减磨接箍最小内径为61mmꎬ表面镍磷镀精化处理后抗磨防腐ꎮ杆管减磨接箍的配套应用ꎬ使抽油杆与油管从本体与连接处更大限度地限制了偏磨ꎮ三㊁结论(1)采用低产井有杆泵高效举升配套工艺技术既解决了 大马拉小车 的问题ꎬ又充分利用了能源ꎬ达到了节能降耗和防偏减磨的目的ꎬ促进了采收率的提高ꎮ(2)该配套工艺技术在低产井中应用良好ꎬ在加深泵挂的同时ꎬ采取有效的防偏磨油井治理措施ꎬ提高了泵效ꎬ延长了油井免修期ꎮ(3)该配套工艺技术实现了低产井的有杆泵小排量连续举升ꎬ充分发挥和协调了油层的供液潜力及抽油设备的排液能力ꎬ满足低产井高效举升的要求ꎬ拓展了有杆泵的应用范围ꎮ参考文献:[1]郝忠献ꎬ耿莉ꎬ吕增烈ꎬ等.高温采油泵举升技术试验研究[J].石油矿场机械ꎬ2016(1).作者简介:曾立国ꎬ胜利油田分公司纯梁采油厂工艺研究所ꎮ351。
- 1、下载文档前请自行甄别文档内容的完整性,平台不提供额外的编辑、内容补充、找答案等附加服务。
- 2、"仅部分预览"的文档,不可在线预览部分如存在完整性等问题,可反馈申请退款(可完整预览的文档不适用该条件!)。
- 3、如文档侵犯您的权益,请联系客服反馈,我们会尽快为您处理(人工客服工作时间:9:00-18:30)。
抽油机井举升工艺方案设计方法研究
作者:张华先潘晨虞小卫蔡旭东
来源:《E动时尚·科学工程技术》2019年第05期
摘要:目前,我国的科技发展十分想迅速,为了保证抽油机举升工艺系统满足生产要求、提高整个系统运行的稳定性、延长设备的整体寿命,需要对抽油机举升工艺系统进行优化设计。
根据举升工艺方案设计思路,对每一项设计内容的预测方法进行归纳汇总,并对应用中的注意事项及局限性进行分析,对抽油机井举升工艺方案设计起到积极地指导作用。
关键词:抽油机;举升工艺;方案;设计方法
0 引言
如今我国对油田资源的开发开始进入后期阶段,当前因为针对聚合物驱油技术的开发手段与运用技术都在不断完善,我厂实践所汇集的数据也显示抽油机井检泵率指标指数也节节攀升,从举升工艺“硬件”潜力看,基本上达到了极限。
今后降低其检泵率的重要举措是,从举升工艺的管理方面出发,研究也进入了后期阶段,通过完善相关的工作制度,保证抽油机井的合理运行,除此之外,还希望达成抽油机稳定、长期的生产,这对油田开发经济效益的提高有着十分重要的作用。
1 抽油机井举升工艺适应性分析系统动态控制图和参数
1.1 抽油机井地面设备动态控制图
1)参数的选择能够反映抽油机井地面设备运转的主要特性参数有悬点载荷、曲柄轴输出扭矩、电机实耗功率。
2)驴头悬点载荷驴头悬点载荷是反映抽油机井的工作能力的重要参数之一,也是选型的主要依据,当抽油机工作时,驴头悬点主要承受以下五种载荷,即:(1)抽油杆杆柱重;(2)油管内活塞以上液柱重;(3)抽油杆柱和液柱在运转时所产生的惯性载荷;(4)抽油杆柱和液柱在运转时所产生的振动载荷;(5)活塞与泵筒、抽油杆与油管内壁的摩擦,以及抽油杆与液柱、液流与油管内壁的摩擦等。
若不考虑摩擦载荷的影响,抽油机井悬点最大载荷Pmax和最小载荷Pmin:Pmax=Wl+Wr(1+SN2/1790)Pmax——抽油机井悬点最大载荷,单位(N);Wl——柱塞以上液体的重力,单位(N);Wr——杆柱在空气中的重力,单位(N);SN2/1790——无因次动载荷系数;Pmin=Wrl-Wr×SN2/1790Wrl——杆柱在液体中的重力,单位(N);抽油机井负载利用率f:f=P实际/P铭牌×100%P实际——抽油机现场实测载荷,单位(KN);P铭牌——抽油机铭牌允许最大载荷,单位(KN);3)减速箱曲柄轴输出扭矩减速箱曲柄轴输出扭矩是衡量抽油机运转的重要技术参数,其经验公式M实际:M实际
=30S-0.236S×(Pmax-Pmin)抽油机井减速箱曲柄轴输出扭矩利用率M:M=M实际/M铭牌
×100%M实际——抽油机减速箱曲柄轴实测输出扭矩,单位(KNm);M铭牌——抽油机减速箱曲柄轴铭牌输出最大扭矩,单位(KNm).
1.2 抽油机井地面设备适应性动态控制图的绘制
此时若是将期减速箱扭矩利用率转变成为X轴的情况下,那么可以把负载利用率当做四Y轴,再构建相应的直角坐标系,此时绘制出的控制图能够检验抽油机的运转中液量和泵径,之间的具体运行是否完全匹配,如果电机功率的利用率为X轴,那么可以Y轴的负载利用率具体来描绘出相关的适应性动态控制图,这个绘制的图片能够具体检验液量与电机相互间是否完全匹配。
1.3 抽油泵设计
(1)下泵深度的确定抽油泵的作用是将不低于预测产液量的流体举升至地面。
产液量和井底流压决定泵的下入深度。
常用的下泵深度预测方法有经验公式法和供排协调点法。
经验公式(3)依据井筒多相流压力分布特点,用于下泵深度估算。
式中:Hp—下泵深度,m;Hz—油层中部,m;Pfs—井底流压,MPa;Pλ—泵吸入口压力,MPa;γo—混合液密度,g/cm3。
应用设计软件绘制IPR曲线和不同下泵深度的流出曲线,得出多个协调点处的井底流压和产量,选取满足产能预测要求的协调点,对应的下泵深度即为投产初期抽油泵的下泵深度。
1.4 抽油泵适应性动态控制图
抽油机井生产过程是油层生产能力和深井泵工况相互影响、协调的过程。
抽油机井动态控制图是在平面坐标图中描述井底流压与抽油泵泵效之间的关系,是地层供液能力同抽油泵排液能力有机结合。
由于目前流压是通过泵吸入压力和油层中深到泵吸入口液柱压力计算得到的。
在套压合理的条件下,应用沉没率(沉没度/泵深×100%)替代流压,相比更直观反映油层供液能力。
抽油泵动态控制图的绘制横坐标为泵效,纵坐标为沉没率;如图2-3所示。
低效区:泵效0-20%,沉没率0-40%;泵效20%-30%,沉没率0-30%。
分析原因:单井供液能力差。
检泵区:泵效0-20%,沉没率40%-100%;泵效20%-30%,沉没率70%-100%。
分析原因:由于断脱、漏失等原因异常。
下调参数区:泵效30%-70%,沉没率0-20%。
分析原因:工作制度不合理,参数偏大。
上调参数区:泵效30%-80%,沉没率70%-100%。
分析原因:工作制度不合理,参数偏小。
待落实区:泵效80%以上,沉没率0-50%;泵效70%-80%,沉没率0%-30%。
分析原因:选值资料不准,需核实。
自喷区:泵效80%以上,沉没率50%-100%。
分析原因:参数偏小,供液能力大。
2 抽油杆和抽油机的确定
根据《采油工程手册》中的计算公式,结合下泵深度、泵径预测结果,预测设计井的最大载荷、最小载荷、扭矩、抽油杆折算应力。
参考抽油杆使用安全系数和抽油机选型要求,进行抽油杆组合的选配和抽油机选型。
大庆油田抽油杆工作安全系数为1.2;抽油机的载荷利用率小
于90%、扭矩利用率小于90%。
抽油机选型时要参考相似区块的已投产井示功图载荷对计算公式进行修正。
3 抽油机井举升工艺适应性分析系统的现场应用情况
抽油机井举升工艺适应性動态控制图是抽油机井总井数根据单月数据统计的。
相对时间而言是静态的。
为了连续观测抽油机单井举升工艺适应性变化情况,引入抽油机单井措施跟踪图表,提高适应性动态控制图的监测和措施后的跟踪功能,加强了措施的针对性和可靠性,完善了适应性控制图“动态”的含义。
4 结语
(1)抽油机井动态控制图根据目前的研究发现,其还有待进一步的优化设计,但是不可忽视的是,该工艺的适应性分析体系应用价值非常高,也能够很大程度上让追踪的数据更加精确,提高工作人员的工作效率。
(2)通过在抽油机井上的应用情况分析可知,其中还是存在着一些不足之处,有必要采取一定的策略和方法来加以完善,使其提供的维护和治理效果达到最佳状态。
(3)结合具体的计算机辅助工作和实践应用数据可以提高整个抽油机井的数据收集正确率与使用效率,这从根本上满足了整个油田日后发展的要求。
参考文献
[1]王俊愧,王春瑞,方亮.采油井合理井底压力界限的确定方法[J].大庆石油地质与开发,1999,18(5):21-22.
[2]林玉秋,王树华.采油井合理流动压力的界限[J].石油勘探与开发,1995,22(6):51-53.。