铸铁发动机缸体曲轴孔的精加工方案
发动机缸体试制曲轴孔加工工艺创新

发动机缸体试制曲轴孔加工工艺创新发布时间:2021-06-09T15:30:27.973Z 来源:《基层建设》2021年第5期作者:任辉斌杨立平[导读] 摘要:随着经济的发展,人们生活水平的提高,对汽车的需求量也在逐年增多。
长城汽车动力事业部天津 300000摘要:随着经济的发展,人们生活水平的提高,对汽车的需求量也在逐年增多。
发动机作为汽车的动力核心部件,始终制约着我国的经济发展。
发动机缸体作为发动机核心的部件之一,直接影响着发动机的性能。
发动机缸体属于典型的多面多孔的箱体类零件,主要加工特征是平面和孔系,加工工艺复杂。
曲轴孔作为发动机骨架缸体上的重要孔系,它的加工质量好坏直接影响发动机的装配精度和整机性能,需要依靠设备精度、工装夹具的可靠性和加工工艺的合理性等来保证。
本文就发动机缸体试制曲轴孔加工工艺创新展开探讨。
关键词:发动机;缸体曲轴孔;加工工艺分析引言缸体曲轴孔精加工工序是缸体三道关键工序之一,其涉及到的各项尺寸与形位精度都将直接影响发动机的品质与寿命,进而决定汽车的性能。
高的曲轴孔尺寸精度、形位精度及小的表面粗糙度值能有效地提高曲轴外圆与曲轴孔的配合精度,从而提升曲轴的旋转精度;高的曲轴孔的孔与孔之间的同轴度能降低装配难度,降低磨损,改善曲轴旋转状况,提高曲轴使用寿命,从而提升发动机的品质与寿命。
因此,为使缸体曲轴孔达到使用要求,缸体曲轴孔的各项精度须达到技术要求。
而合理的加工工艺、高精度的加工设备以及高性能的刀具是曲轴孔能达到设计技术要求的主要保障。
1动机缸体加工的特点发动机缸体加工具有以下特点:(1)需要采用的加工工艺多,包括金属切削、珩磨、气密检测及清洗。
(2)加工的部位多,几乎六个面都需要进行加工。
(3)发动机缸体加工的特征虽然只有两个,即孔与面,面的平面度要求高,孔的数量多、种类多。
按孔的性质分,可分为光孔、螺纹孔两类,其中光孔有沉孔、通孔、斜孔与深孔,光孔的加工方法主要有钻、扩、铰与珩磨等。
发动机缸体顶面缸孔及止口精加工组合机床的精度保证分析

发动机缸体顶面缸孔及止口精加工组合机床的精度保证分析发动机是汽车的心脏,而发动机缸体顶面缸孔及止口的精加工是发动机制造中非常重要的一环。
在发动机的工作过程中,缸体顶面缸孔及止口的精加工质量对发动机的性能、经济和可靠性都有着重要的影响。
为了保证发动机缸体顶面缸孔及止口的精度,需要使用专门的组合机床进行加工,同时也需要对机床的精度进行保障分析。
一、发动机缸体顶面缸孔及止口的精加工要求1.精度要求发动机缸体顶面缸孔及止口的精加工需要满足高精度的要求,主要体现在以下几个方面:(1)孔径精度:对于缸孔而言,其内径的精度和表面质量将直接影响到气缸的气密性和工作效率;(2)表面粗糙度:缸孔及止口的表面粗糙度需要控制在一定范围内,以保证气缸气密性和机械配合;(3)孔位精度:缸孔及止口的位置精度需要满足装配要求,确保各个部件的配合精度。
2.加工工艺要求(1)如果缸孔和止口采用同一机床进行加工,需要确保加工过程中的切削力和切削温度对工件的影响尽量减小;(2)保证加工过程中的冷却润滑条件,以确保切削润滑效果和工件表面质量;(3)在加工过程中对加工刀具的工艺参数要求严格,如进给速度、切削深度、切削速度等。
1.选择合适的机床对于缸体顶面缸孔及止口的精加工,通常需要选择数控组合机床。
这种机床具有多种加工功能,可同时进行多种加工操作,包括钻孔、铰孔、镗孔、攻丝、刀具更换等,能够大大提高加工效率和精度。
2.机床精度要求(1)数控系统精度:数控系统是影响机床精度的重要因素之一,需要保证数控系统具有高精度的控制能力,能够精确控制加工过程中的各种参数。
(2)机床传动系统精度:机床传动系统包括主轴传动系统、进给传动系统等,需要具有一定的转动精度和位置精度,以保证加工过程中的稳定性和精度。
(3)加工台面精度:加工台面是机床上工件进行加工的基准平面,其精度直接影响到工件的加工精度和位置精度,需要保证加工台面的平整度和平行度。
3.机床刚性和稳定性机床刚性和稳定性对于保证加工精度具有重要的影响,尤其是在高速加工和深孔加工中,刚性和稳定性的要求更加严格。
33张图详解发动机缸体加工的33道工序

33张图详解发动机缸体加⼯的33道⼯序☞这是⾦属加⼯(mw1950pub)发布的第12110篇⽂章编者按汽车主要零部件组成中,汽缸盖、汽缸体、曲轴等部分形位复杂,加⼯难度最⼤。
今天我们来看下缸体加⼯有哪些难点,以及如何解决的。
汽缸体主要加⼯⾯1.曲轴孔半圆⾯粗加⼯(铸铁件)2.曲轴孔半精加⼯镗削(铝合⾦件)3.曲轴孔精镗(铸铁件)4.曲轴孔精镗·确定轴向宽度加⼯(铸铁件)5.决定轴颈部位宽度的两侧边铣削(铸铁件)6. 决定轴颈部位宽度的两侧边铣削(铝合⾦件)7. 决定轴颈部位宽度的两侧⾯加⼯⽤铣⼑(铸铁件)8.第3轴承⾯精镗(铸铁件)9. 第3轴承⾯精加⼯(铸铁件)10.轴承⾯油槽加⼯(铸铁件)11.轴承⾯油槽加⼯(铸铁件)12.缸孔粗镗13.缸孔粗镗14.缸孔精镗15.缸孔精镗16.缸孔内倒⾓加⼯(铝合⾦件)17.上下⾯粗铣(铝合⾦件)18.上下⾯粗铣(铝合⾦件)19.上下⾯精铣(铝合⾦件)20.上下⾯精铣(铝合⾦件)21.前后⾯精铣(铝合⾦件)22.前后⾯精铣(铝合⾦件)23.搬送⽤基准⾯铣削(铝合⾦件)24.轴承盖座粗铣(铸铁件)25.轴承盖座精铣(铸铁件)26.上下⾯粗铣(铸铁件)27.上下⾯精铣(铸铁件)28.下⾯精铣(铸铁件)29.前后⾯粗铣(铸铁件)30.前后⾯精铣(铸铁件)31.前后⾯精铣(铸铁件)32.搬送⽤基准⾯铣削(铸铁件)33.各种孔加⼯看了上⾯这些⼯艺,下⾯⼩编给您介绍⼀下⼯艺的创新点:1. 合理利⽤复合⼑具组合式镗⼑被应⽤于主轴承孔中,阶梯形钻头和钻扩复合⼑具分别⽤于结合⾯螺栓孔以及定位销孔的加⼯当中,在⼑具⼀次⼯作以及⼯件⼀次装夹整个流程中,由于使⽤了复合⼑具,因此能够⼀次性实现多道⼯序的⽣产加⼯,在重复定位⼑具和⼯件时,⼆者之间的误差能够被消除,促使精度有效提升,在这⼀过程中所消耗的辅助时间相对较少,整个测量过程得到了简化,因此加⼯效率极⾼。
2. ⼑具在线监测与补偿要想顺利进⾏⾦属切削加⼯,就必须严密监视⼑具状态,在实际加⼯中综合应⽤多传感器监测系统,能够促使⼑具在加⼯过程中的状态得到在线监测和补偿,在对⼑具运⾏中产⽣的⼏何参量进⾏读取的基础上,可以⾼效测量⼑形轮廓和⼑具预调初始点,从⽽对不同接触点实施补偿。
汽车发动机曲轴机械加工技术

汽车发动机曲轴机械加工技术精选文档TTMS system office room 【TTMS16H-TTMS2A-TTMS8Q8-汽车发动机曲轴机械加工技术2007-7-9 9:11:07来源: 汽车工业信息网编辑:zc目前,世界汽车工业发达国家对发动机曲轴的加工十分重视,并不断改进曲轴加工工艺。
随着中国加入WTO,国内曲轴生产厂家已经意识到形势的紧迫性,为了提高产品的整体竞争力,引进了为数不少的先进设备和技术,提高了曲轴的制造技术水平。
1曲轴用材料目前,车用发动机曲轴材质有球墨铸铁和钢两类。
由于球墨铸铁的切削性能良好,可获得较理想的结构形状,并且和钢质曲轴一样可以进行各种热处理和表面强化处理来提高曲轴的抗疲劳强度、硬度和耐磨性。
球墨铸铁曲轴成本只有调质钢曲轴成本的1/3左右,所以球墨铸铁曲轴在国内外得到了广泛应用。
据统计资料表明,车用发动机曲轴采用球墨铸铁材料的比例:美国为90%、英国为85%、日本为60%,此外德国、比利时等国家也已经大批量采用球墨铸铁材料。
国内采用球墨铸铁曲轴的趋势则更加明显,85%以上的中、小型功率的发动机曲轴均采用球墨铸铁材料。
就大功率车用柴油机曲轴而言,锻钢曲轴具有较高的综合机械性能。
许多高强化的中高速大功率四冲程柴油机都无一例外地采用锻钢曲轴。
排量在1.6 L以上的发动机也都采用钢质模锻曲轴。
2曲轴的机械加工技术目前,国内较陈旧的曲轴生产线多数由普通机床和专用机床组成,生产效率和自动化程度相对较低。
粗加工设备多采用多刀车床车削曲轴主轴颈及连杆轴颈,工序的质量稳定性差,容易产生较大的内应力,难以达到合理的加工余量。
一般精加工采用曲轴磨床,通常靠手工操作,加工质量不稳定,尺寸的一致性差。
老式生产线的主要特点是普通设备多,一条生产线有35~60台设备,导致产品生产周期长、场地占用面积大,且完全是靠多台设备分解工序和余量来提高生产效率。
随着贸易全球化的到来,各厂家已意识到形势的严峻性,纷纷进行技术改造,全力提升企业的竞争力,近年来引进了许多先进的曲轴加工设备和技术,其曲轴机械加工工艺大体上可分为欧美型工艺方案和日本丰田型工艺方案。
发动机缸体缸孔曲轴孔及顶面的精加工工艺技术
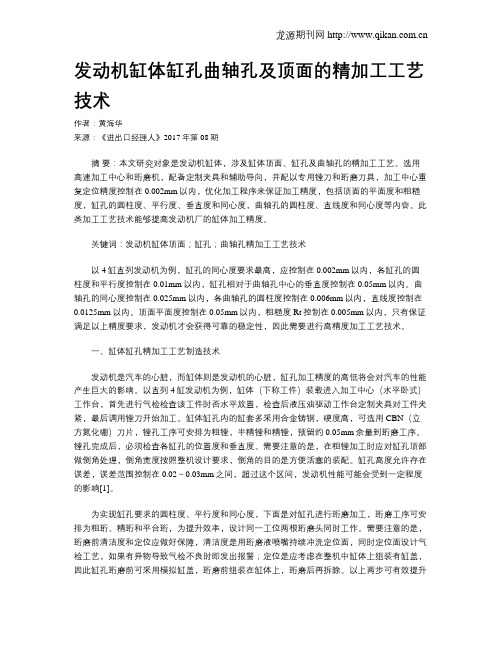
发动机缸体缸孔曲轴孔及顶面的精加工工艺技术作者:黄海华来源:《进出口经理人》2017年第08期摘要:本文研究对象是发动机缸体,涉及缸体顶面、缸孔及曲轴孔的精加工工艺。
选用高速加工中心和珩磨机,配备定制夹具和辅助导向,并配以专用镗刀和珩磨刀具,加工中心重复定位精度控制在0.002mm以内,优化加工程序来保证加工精度,包括顶面的平面度和粗糙度,缸孔的圆柱度、平行度、垂直度和同心度,曲轴孔的圆柱度、直线度和同心度等内容。
此类加工工艺技术能够提高发动机厂的缸体加工精度。
关键词:发动机缸体顶面;缸孔;曲轴孔精加工工艺技术以4缸直列发动机为例,缸孔的同心度要求最高,应控制在0.002mm以内,各缸孔的圆柱度和平行度控制在0.01mm以内,缸孔相对于曲轴孔中心的垂直度控制在0.05mm以内。
曲轴孔的同心度控制在0.025mm以内,各曲轴孔的圆柱度控制在0.006mm以内,直线度控制在0.0125mm以内。
顶面平面度控制在0.05mm以内,粗糙度Rt控制在0.005mm以内,只有保证满足以上精度要求,发动机才会获得可靠的稳定性,因此需要进行高精度加工工艺技术。
一、缸体缸孔精加工工艺制造技术发动机是汽车的心脏,而缸体则是发动机的心脏,缸孔加工精度的高低将会对汽车的性能产生巨大的影响。
以直列4缸发动机为例,缸体(下称工件)装载进入加工中心(水平卧式)工作台,首先进行气检检查该工件时否水平放置,检查后液压油驱动工作台定制夹具对工件夹紧,最后调用镗刀开始加工。
缸体缸孔内的缸套多采用合金铸钢,硬度高,可选用CBN(立方氮化硼)刀片,镗孔工序可安排为粗镗,半精镗和精镗,预留约0.05mm余量到珩磨工序。
镗孔完成后,必须检查各缸孔的位置度和垂直度。
需要注意的是,在粗镗加工时应对缸孔顶部做倒角处理,倒角宽度按照整机设计要求,倒角的目的是方便活塞的装配。
缸孔高度允许存在误差,误差范围控制在0.02~0.03mm之间,超过这个区间,发动机性能可能会受到一定程度的影响[1]。
发动机缸体双金属曲轴孔半精镗及精镗加工工艺

L UO J i n g  ̄
XI AO T i e z h o n g ②
,
。
G O N G We n j u n ①, Y U A N C h u n y i n g ③
② Me c h a n i c a l a n d E l e c t r o n i c E n g i n e e i r n g D e p a r t m e n t , S i c h u a n E n g i n e e r i n g
Te c hn i c a l Co l l e g e,De y a ng 61 8 0 0,CHN ;
达到 或超 过设 计 要求 , 成 功地在 重 庆某 机械 制造 企 业投产 。 关键 词 : 缸体 曲轴 孔 中 图分 类号 : T G5 3 9 镗 削 工艺 文献 标识 码 : A
Se mi - i n t e n s i v e a n d f i n e b o r i n g p r o c e s s i n g o f d u a l - me t a l
f (  ̄K e y L a b o r a t o r y o f M a n u f a c t u r e T e c h n i q u e s f o r A u t o m o b i l e P a r t s M i n i s t r y
o f Ed u c a t i o n,Ch o n g q i n g Un i v e r s i t y o f Te c h n o l o g y,Ch o n g q i n g 40 0 0 5 4, CHN;
球墨铸铁汽车曲轴的加工工艺

球墨铸铁汽车曲轴的加工工艺学院机电工程学院专业机械类年级班别创新实验班12(1)学号 3112010453 3112010454 3112010455 3112010462 学生姓名罗毓健骆智伟马欣华冼文飞指导教师王成勇2014年 6 月摘要球墨铸铁具有优良的机械性能,已经大量用于制造强度、韧性、耐磨性要求较高的零件。
球墨铸铁大量地应用于汽车发动机曲轴的加工生产,结合球墨铸铁的特性,本文讲述了球墨铸铁应用于曲轴的切削与磨削加工机理及其加工工艺,介绍了聚晶立方氮化硼(PCBN)刀具切削加工等温淬火球墨铸铁(ADI)时的特征。
介绍了奇瑞公司曲轴的加工工艺以及几款相关的曲轴专用加工机床。
关键词:球墨铸铁,曲轴,ADI,PCBN目录1球墨铸铁基本性质与应用 (1)1.1 球墨铸铁的成分与组织结构 (1)1.2 球墨铸铁的机械、物理、力学性能 (1)1.3 典型零件、应用场合 (2)1.4 球墨铸铁曲轴加工批量和加工质量要求 (2)1.5 小结 (2)2球墨铸铁切削与磨削加工机理 (2)2.1 等温淬火球墨铸铁(ADI)的切削与磨削可加工性简述 (3)2.2 铸铁应用于曲轴的主要切削、磨削去除过程 (3)2.3 球墨铸铁的切削加工过程特征 (4)2.4 加工等温淬火球墨铸铁常用刀具 (5)2.5 曲轴加工工艺 (6)3曲轴加工专用机床 (12)3.1 曲轴质量定心机 (13)3.2 数控车-车拉机床 (13)3.3 曲轴圆角滚压机床 (13)3.4 绿色粗磨“扒皮”机床 (13)参考文献 (14)球墨铸铁汽车曲轴的加工工艺1球墨铸铁基本性质与应用1.1球墨铸铁的成分与组织结构根据铸铁中石墨形态的不同,铸铁可分为以下四类:(1)普通灰铸铁。
石墨呈曲片状存在于铸铁中,简称灰铸铁或灰铁,是目前应用最广的一种铸铁。
(2)可锻铸铁。
由一定成分的白口铸铁经过石墨化退火而获得。
石墨呈团絮状存在于铸铁中,有较高的韧性和一定的塑性。
球墨铸铁曲轴工艺路线

球墨铸铁曲轴的制造工艺路线通常包括以下几个步骤:
1.原材料准备:根据曲轴的设计要求,选用高质量的球墨铸铁材料,同时准备加工所需的机床、刀具等工具。
2.初步加工:首先对原材料进行初步加工,例如锯断、车削、铣削等工艺操作,以便后续的精加工。
3.热处理:将初步加工好的曲轴进行热处理,一般采用正火+回火的工艺,以提高材料的硬度和强度。
4.精加工:在热处理后,对曲轴进行精加工,包括车削、磨削、钻孔等工艺操作,以便获得更高的精度和表面质量。
5.检验:对加工好的曲轴进行各项检验,包括外观质量、尺寸精度、表面质量等指标,确保产品符合设计要求。
6.包装出厂:对通过检验的曲轴进行清洁、包装、标识等工艺操作,以便出厂交付客户。
以上是球墨铸铁曲轴的一般制造工艺路线,具体的工艺流程和操作细节会根据不同的产品和生产工艺而有所差异。
- 1、下载文档前请自行甄别文档内容的完整性,平台不提供额外的编辑、内容补充、找答案等附加服务。
- 2、"仅部分预览"的文档,不可在线预览部分如存在完整性等问题,可反馈申请退款(可完整预览的文档不适用该条件!)。
- 3、如文档侵犯您的权益,请联系客服反馈,我们会尽快为您处理(人工客服工作时间:9:00-18:30)。
铸铁发动机缸体曲轴孔的精加工方案
曲轴孔的加工质量对发动机的工作性能具有重大影响,奇瑞公司发动机事业部根据实际加工情况,对铸铁发动机缸体曲轴孔的精加工方案不断进行研究和持续改进,收效显著,使加工质量和效率都得到了有效提升。
缸体是发动机重要的基础件,其主要功用是将各机构、各系统组装成一体,而发动机最主要的运动部件——曲轴、活塞和连杆都与缸体有着非常密切的关系。
图1为曲柄连杆机构示意图。
目前,我们常见的汽油发动机最高转速达6 000r/min以上,曲轴在发动机缸体的曲轴孔中与轴瓦之间形成油膜,以滑动轴承的方式支撑和润滑高速运转的曲轴,这就对曲轴孔的精加工提出了较高的工艺要求。
由于曲轴孔的加工质量对发动机的工作性能具有极大的影响,所以我们对发动机曲轴孔工艺的要求一般比较严格,包括直径、位置度、圆度、各档曲轴孔中心的直线度及表面粗糙度等。
为了满足这些要求苛刻的工艺指标,精加工一般采用精镗或铰珩两种加工方式。
精镗加工方式分析
精镗方式精加工曲轴孔相对于铰珩方式而言,初期投入成本较低,可在加工中心或专机上与其他部位的精加工共同安排在一道工序。
因考虑到特殊的工艺要求,目前我们采用的精镗方案是两把精镗刀组合,第一把精镗刀进行引导镗1、2档曲轴孔(见图2),第二把精镗刀在1、2档曲轴孔的支撑下精镗剩余的各档曲轴孔(见图3)。
由于曲轴孔各档之间需要保持较高的
同轴度,所以精加工时必须在同一个方向进刀加工,但这么长的曲轴孔镗刀在加工第1档曲轴孔时会出现因缺少支撑而跳动过大的情况,所以采用一长一短两把精镗刀组合的方式精加工曲轴孔。
图2 加工1、2档曲轴孔的精镗刀
图3 加工最后几档曲轴孔的精镗刀
目前,精镗曲轴孔的镗刀一般采用硬质合金或CBN材质的刀片。
硬质合金的刀片成本较低,但加工工件的表面粗糙度不好,且刀片的耐用度较低。
针对这一问题,我们协同刀具供应商共同收集了业内较为普遍的刀片涂层材料以及在刀片切削角度上的经验技术,对16款硬质合金刀片进行切削实验,并尝试了对各种合适的加工参数进行优化,具体的粗糙度波动情况如图4所示。
通过大量验证,硬质合金刀片在满足粗糙度等工艺要求的前提下最好的实验结果为一次性加工80件,仍不能满足大批量生产的要求。
图4 测试的硬质合金刀片中满足要求的部分刀片粗糙度波动
随后,我们对精镗刀的刀片材质进行了另外一种方案的验证,即更换现有的硬质合金刀片材料为CBN刀片材料。
我们依靠刀具供应商开发出了10多款不同的CBN刀片对曲轴孔进行切削验证,测试结果显示:在粗糙度的控制方面,CBN刀片明显优于硬质合金刀片,加工寿命能够突破200件。
但同时也产生了一些新的问题:用CBN材质的刀片加工约150件时,开始在孔侧出现轻微毛刺,严重时将会出现翻边现象。
此处的毛刺甚至翻边成为影响发动机性能的质量隐患,严重时会造成轴瓦划伤及曲轴抱死等质量事故。
在曲轴孔毛刺问题的处理方面,我们增加了曲轴孔的毛刷,在一定程度上缓解了毛刺的存在,但仍存在较大的质量风险。
此外,曲轴孔精镗方案的质量稳定性相对铰珩而言较差,且因为换刀频繁会极大地增加质量控制的风险。
精镗刀加工出的工件表面粗糙度变化趋势随刀具耐用度的减少而下降较快,精镗曲轴孔采用CBN刀片加工的工件表面粗糙度对比如图5、6所示。
图5 镗刀加工首件的表面粗糙度报告
图6 镗刀加工200件时的表面粗糙度报告
铰珩加工方式分析
对镗削精加工的曲轴孔方案我们做了大量的探索工作,并开发出多种新型刀片进行加工验证,但仍然未达到理想的加工效果,因此我们再次考虑曲轴孔铰珩方案。
从成本方面考虑,曲轴孔铰珩的一次性投入较大,德国某知名珩磨机厂商的初步报价为40万欧元(因配置要求不同,价格会有差异),但后期加工成本比精镗低很多,且加工质量稳定。
曲轴孔铰珩方案
的具体实施如图7所示。
图7 曲轴孔铰珩方案的实施
曲轴孔的铰珩采用卧式珩磨机进行加工,因为卧式珩磨机的工作行程较长,适用于像曲轴孔这类的深孔珩磨,深度最大可达3 000mm。
在加工过程中,珩磨头的油石在胀缩机构作用下作径向进给,把工件逐步加工到所需尺寸。
珩磨头外周镶有2~10根长度约为孔长1/3~3/4的油石,在珩孔时既旋转运动又往返运动,同时通过珩磨头中的弹簧或液压控制而均匀外涨,所以与孔表面的接触面积较大,加工效率较高。
珩磨余量一般不超过0.2mm。
对铸铁或有色金属进行加工,珩磨的圆周速度可达50m/min以上;珩磨的往复速度不宜超过15~20m/min。
油石对孔壁的压力一般为0.3~0.5MPa,粗珩时可达1 MPa左右,精珩可小于0.1 MPa。
由于珩磨时油石与工件是面接触,每颗磨粒对工件表面的垂直压力只有磨削时的1/50~1/100,加上珩磨速度低,故切削区的温度可保持在50℃~150℃范围内,有利于减小加工表面的残余应力,提高表面质量。
为了冲刷切屑,避免堵塞油石,同时降低切削区的温度和表面粗糙度,珩磨时采用的切削液要有一定的工作压力并经过过滤。
切削液大都采用煤油或煤油加锭子油,也可采用极压乳化液。
从图8粗糙度测量报告数据的波动趋势来分析,其铰珩的加工稳定性非常高,并且珩磨头一次更换砂条的耐用度可加工1万余件,生产效率大幅提高。
采用CBN刀片的精镗加工方式,每200件需要换刀一次,平均每次换刀和首件检测需要42min。
如果将频繁换刀所花费的时间折算到每个工件上,将损失12.6s/件。
按照现有某生产线的加工节拍为120s/件,生产纲领为16万件/年来计算,全年将损失加工时间201.6万s,利用这段时间每年可以多加工出1.68万件。
图8 连续20天实施铰珩方案的首检件粗糙度测量报告
表为曲轴孔不同精加工方式所产生的刀具损耗成本对比,从表可以分析出,单件的刀具成本差距较为明显。
按照理论分析计算,当生产103万件工件时,铰珩方案相对于CBN精镗方案的刀具损耗节约381.1万元左右,略同于铰珩设备的价格,并且铰珩方案的质量控制难度和风险都小得多。
曲轴孔不同精加工方式所产生的刀具损耗成本(单位:元)两种方案的对比
经过大量的实验和生产实践,我们认为铰珩方式与镗削方式各有优势,具体归纳如下:
1. 成本投入
镗削方式成本投入较少,只需定制专用刀具,与精加工其他部位共用机床即可;铰珩方式一次性投入较高,但可考虑与缸孔珩磨共用珩磨机,以适当减少投资。
2. 占地面积
采用镗削方式不需要单独新增设备;采用铰珩方式需要单独的区域布置铰珩设备,如果与缸孔珩磨共用设备需要增加珩磨机占地面积。
3. 加工质量
镗削方式能够满足加工质量的要求,但稳定性相对较差;而铰珩方式不仅能满足加工质量的要求,且质量稳定性较好。
4. 生产效率
虽然镗削方式的切削效率不低,但频繁换刀造成时间的损失较大;铰珩设备一次调整好后,可持续稳定加工,生产效率较高。
5. 单件刀具成本
由于工艺要求高且刀片耐用度低,使得镗削方式的单件刀具成本较高;采用铰珩方式,由于铰珩设备的珩磨头砂条耐用度高,单件刀具成本也较低。
综上所述,虽然目前这两种方式在各企业的曲轴孔精加工中都有较大范围的应用,但根据各自的优缺点分析,精镗方式更适合产量较小时使用;如果产量大、质量要求高,建议还是采用曲轴孔铰珩的方式进行加工,以提高产品的加工效率和质量稳定性,降低发动机的加工成本。
行业概况:
北京抛丽斯科技有限公司甘健先生认为:供求关系是一个行业能否快速发展的前提。
目前来看,市场需求是很大的,而供应方面却略显不足,尤其是拥有核心知识产权,产品质量过硬的企业并不多,行业整体缺乏品牌效应。
在需求旺盛的阶段,行业需求巨大,发展前景好,这是毋庸置疑的。
但如何保持行业的健康,稳定且可持续发展,需要业内企业的共同努力,尤其需要发挥吃毛求疵的研发精神,进一步提高生产工艺,降低成本,真正解决客户的实际困难,严把质量关,提供最可靠的产品。