再订货点与安全库存
某物流公司安全库存与订货计划

9 19 33 51 53
短期销售
制定/执行 订货计划
制定/执行 进口分货计划
物流中心运作
订
提高物流中心 内部管理
改善物流网络
建立物流组织结构
帮助和光集团变得更成功 第 1页
➢概述 ➢滚动订货计划 ➢安全库存 ➢订货频率
国内提货 22M 41 8.90 0.54M
平均库存下降 一次性库存资本下降 平均库存存置% 每年库存存置成本下降
第一年总成本下降 此后每年成本下降
HK提货 76M 122 2.99 0.62M
国内提货 22M 82 4.45 0.27M
0.45M 0.45M 68% 0.30M
0.75M 0.30M
短期销售 计划
制定/执行 订货计划
制定/执行 进口分货计划
物流中心运作
提高物流中心 内部管理
改善物流网络
订单配送
建立物流组织结构
图示:某型号12周滚动计划,该型号安全库存是100(假设:缺货订单不会取消)。
本周
销售预测 预计到达 预计库存 上周库存
采购量
10 11 12 13 14 15 16 17 18 19 20 21 22 100 100 100 100 100 100 100 100 100 100 100 100 20 20 20 20 20 500 100 100 100 100 100 100 20 (60) (140) (220) (300) 100 100 100 100 100 100 100
计划
订货计划
进口分货计划
提高物流中心
内部管理
为了满足日常销售而存放的平均周转库存。以IBM产品为例:
4.5连续检查订货策略库存模型

平均库存=
Q 2
z
STD
L
10
2单位订产货品费年存年储需费求Q用量*
2 KD h
D:平均需求量需求量分布的均值
9
l (R,Q)策略下库存水平变化情况
R+Q
Inventory position
Inventory level
R
Lead time
Safety stock
0
time
最低库存= z STD L
10
最大库存= Q z STD L
DS = DL/n
方差[DS] = 方差[DL]/n , 即σS = σL/√n
• Converting from Short to Long:
DL = n DS 方差[DL] = n 方差[DS] , 即 σL = √n σS
6
• 缺货概率α, CSL=1-α;缺货只可能发生在订货提前期内,即:
CSL 概率P(提前期内的需求量 R)
• 提前期内需求的分布(DL,σL)
DL D L, L LD
• 需求服从正态分布(D,σD)
7
(3)订货点R未知时安全库存的确定
ss F 1s(CSL) L Z L
= NORMSINV(CSL), 标准正态分布系数,安全因子
=1- CSL 缺货的概率
CSL (%) z
90 91 92 93 94% 95 96 97 98 99 99.9 1.29 1.34 1.41 1.48 1.56 1.65 1.75 1.88 2.05 2.33 3.08
8
(4)R和Q值的计算
l 再订货点 R= DL + ss
DL Z L D L Z LD
订货点采购与库存控制
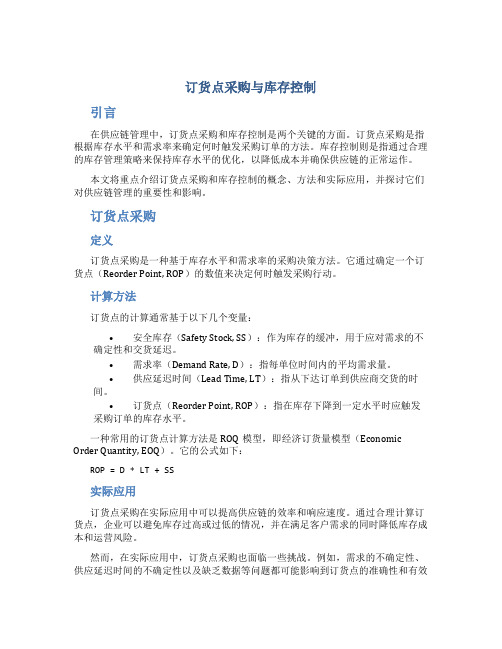
订货点采购与库存控制引言在供应链管理中,订货点采购和库存控制是两个关键的方面。
订货点采购是指根据库存水平和需求率来确定何时触发采购订单的方法。
库存控制则是指通过合理的库存管理策略来保持库存水平的优化,以降低成本并确保供应链的正常运作。
本文将重点介绍订货点采购和库存控制的概念、方法和实际应用,并探讨它们对供应链管理的重要性和影响。
订货点采购定义订货点采购是一种基于库存水平和需求率的采购决策方法。
它通过确定一个订货点(Reorder Point, ROP)的数值来决定何时触发采购行动。
计算方法订货点的计算通常基于以下几个变量:•安全库存(Safety Stock, SS):作为库存的缓冲,用于应对需求的不确定性和交货延迟。
•需求率(Demand Rate, D):指每单位时间内的平均需求量。
•供应延迟时间(Lead Time, LT):指从下达订单到供应商交货的时间。
•订货点(Reorder Point, ROP):指在库存下降到一定水平时应触发采购订单的库存水平。
一种常用的订货点计算方法是ROQ模型,即经济订货量模型(Economic Order Quantity, EOQ)。
它的公式如下:ROP = D * LT + SS实际应用订货点采购在实际应用中可以提高供应链的效率和响应速度。
通过合理计算订货点,企业可以避免库存过高或过低的情况,并在满足客户需求的同时降低库存成本和运营风险。
然而,在实际应用中,订货点采购也面临一些挑战。
例如,需求的不确定性、供应延迟时间的不确定性以及缺乏数据等问题都可能影响到订货点的准确性和有效性。
因此,企业需要建立有效的数据收集和分析系统,以支持订货点采购决策的优化。
库存控制定义库存控制是指通过合理的库存管理策略来优化和控制库存水平,以确保供应链的正常运作。
它包括库存的规划、监控和优化等环节。
方法和策略在库存控制中,有多种方法和策略可以帮助企业实现库存水平的控制和优化。
再订货点与安全库存
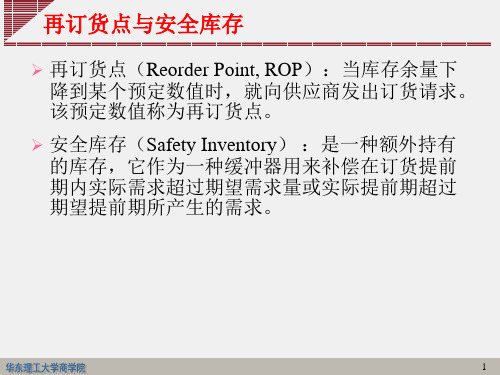
首先计算订货提前期内的标准差 σDLT=LT σ = 3 ×30=1.732×30=51.96
查正态分布表得 z(0.95)=1.64
因此安全库存SI=1.64×51.96≈ 85件
再订货点ROP=200×3+85=685件 订货批量可由一般经济订货批量模型确定。
10
降低安全库存的方法
缩短供应提前期 如果提前期缩短到原来的k倍,安全库存则降低为原 来的 k 倍。
=112 .7 SI=1.64×112.69≈185件 ROP=200×3+185=785件
13
多级库存管理
• 多级库存管理:管理整个渠道的库存而不只是 各自独立的存储点的库存。 • 基本逻辑:渠道中的每一级都按自己的库存水平 加上来自所有下游的库存来进行库存计划。也即, 每一级库存水平 的计划都不是仅仅考虑自己下 一级的需求信息,而是考虑最终客户的需求信息。
Q1 AIL1= + z× σ1 2
LTR
0.25= 61.38
= 311.8/2 +1.28×16.8 0.25= 166.65
17
零售商1
订货量,Q 再订货点,ROP 平均库存,AIL 订货周期(月) 312 61 167 1.54
零售商2
220 35 120 2.19
零售商3
381 87 202 1.26
1
需求与提前期都是常数时的再订货点
在库存持有量能够满足等待订货期间(即提 前期)的需求时下订单。
若需求与提前期都是常数,再订货点为:
ROP = d LT 其中: d —— 需求率; LT —— 提前期
Q*=93 ROP=?
2
需求与提前期变化时的再订货点
物料安全库存计算公式

物料安全库存计算公式在企业的生产和运营中,物料管理可是个至关重要的环节。
而物料安全库存的计算,就像是这场大“战役”中的一把利剑,能帮助我们在风云变幻的市场环境中站稳脚跟。
咱们先来说说啥是物料安全库存。
简单来讲,就是为了防止各种意外情况,比如供应商突然断货、生产需求突然增加、运输延误等等,而提前准备的那部分物料库存。
那这物料安全库存咋计算呢?这里就给您介绍几个常用的计算公式。
第一个公式是“再订货点 = 平均日需求量 ×平均交货期 + 安全库存”。
比如说,咱们厂里生产的某个产品,每天平均要用掉 100 个零件,供应商平均交货期是 5 天,为了保险起见,咱设定安全库存为 200 个零件。
那这再订货点就是 100×5 + 200 = 700 个零件。
也就是说,当库存降到 700 个零件的时候,就得赶紧补货啦。
再来看另一个公式,“安全库存= (预计最大日用量- 平均日用量)×平均提前期”。
我给您讲个事儿啊,之前我们厂新接了个大订单,生产线上预计每天要用 150 个某种特殊螺丝,可平常平均每天也就用 100 个。
供应商的平均提前期是 3 天。
那这安全库存就是(150 - 100)× 3= 150 个螺丝。
有了这个安全库存,就算生产需求突然增加,咱也能暂时顶一顶,不耽误生产进度。
不过您可别以为,拿着这些公式就能一劳永逸啦。
实际情况可比这复杂得多!像市场需求的波动、供应商的稳定性、库存成本等等,都会影响到安全库存的计算。
比如说,有一回我们厂的主要供应商出了点问题,交货期一下子延长了好多。
这可把我们急坏了,因为按照之前算的安全库存根本不够用。
那段时间,大家都忙得焦头烂额,一边到处找新的供应商,一边紧急调整生产计划,尽量减少对物料的需求。
经过这一遭,我们深刻认识到,不能只依赖固定的公式,还得时刻关注各种变化,灵活调整安全库存。
总之,物料安全库存的计算不是个简单的数学题,而是要综合考虑各种因素,不断摸索和调整。
库存控制的决策及其作用
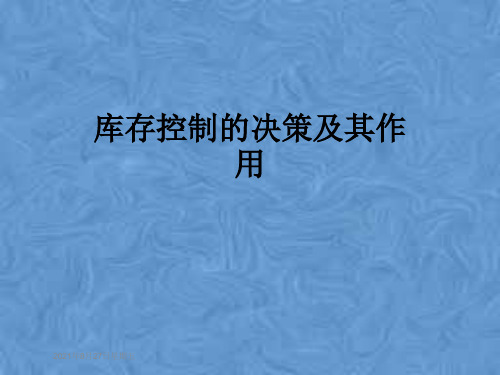
(二)边际分析法
公式: p(d) = ——C—u —
d<Q
Cu +C0
上式常称为损益转折概率, Cu 称为边际收益, C0 称为边 际损失。当累计概率刚大于或等于损益转折概率时,此时 的Q值就是最佳订货量。
例:某批发商准备订购一批圣诞树供圣诞节期间销售。该批
2、库存成本项目
(1)订货次数 = D / Q (2)订货费用 = (D / Q )S (3)平均库存 = Q / 2 (4)平均库存费用( 持有成本) = (Q / 2)H (5)库存物料成本 = P D 其中:D ----- 年需求量;
S ----- 一次订货费或调整准备费; H ----- 单位持有成本; P ----- 单位价格。
三、库存的种类
1、按库存在生产中的作用分类
①主要原材料;②辅助材料;③燃料和动力; ④修理用备件。
2、按库存物资存在的状态分类
①原材料库存;②成品库存;③部件库存; ④备件库存;⑤在制品库存。
3、按库存用途分类
①经常性库存;②保险性库存;③季节性库 存。
第二节 库存控制的决策
一、库存决策的内容
单周பைடு நூலகம்需求出现在下面两种情况:
①偶尔发生的某种物品的需求;
②经常发生的某种生命周期短的物品的不定量的需 求。
2、多周期需求:在足够长的时间里对某种物品的重 复的、连续的需求,其库存要不断地补充。
二、库存控制的基本方式
1、连续观测库存控制系统(固定量系统) 2、定期观测库存控制系统(固定间隔期
三、库存费用和库存控制的目标
(一)库存费用 1、随库存量增加而增加的费用 (1)资金成本 (2)仓储空间费用 (3)物品变质和陈旧 (4)税收和保险
精选安全库存

某产品周需求正态分布,d = 2,500/week; d = 500,满足需求的订单需要2周完成,(L = 2 周);当前订货策略是库存下降到6000台时订货10000台。(Q = 10,000; ROP = 6,000), 该产品平均库存量是多少?DL = dL = (2500)(2) = 5000ss = ROP - dL = 6000 - 5000 = 1000平均库存量 = Q/2+ ss = 5000 + 1000 = 6000库存周转期 = 平均库存量 / 出库率 = 6000/2500 = 2.4 周
补货策略 Replenishment Policies
补货策略: 决定何时再下订单,订单数量?库存的持续检查 Continuous review: 库存处于持续监控下,当库存水平达到再订货点(the reorder point) ROP时,下达订单订货批量Q------定量订货模型库存的定期检查Periodic review: 以固定周期检查库存水平,下达订单的订货批量需要达到一个预先确定的极限水平------定期订货模型
使用安全库存的定量订货模型
不确定提前期、 需求量固定不确定的需求、 不确定的提前期
使用安全库存的定量订货模型
不确定提前期、 需求量固定 化工厂每天消耗800吨酸性溶液,来自供应商的交货期服从正态分布,期望值14天,标准差4天。如果化工厂希望保证99% 的服务水平,那么再订货点应是多少?(z=2.33)不确定的需求、 不确定的提前期 一种工业用齿轮的需求服从正态分布,其均值是每天40单位,标准差是每天6单位。来自供应商的提前期也服从正态分布,均值是10天,标准差是5天,求95%服务水平下的再订货点。 (z=1.645)
再订购点策略

3.再订购点策略:是指针对物料的通用性比较高、需求比较稳定的物料,当物料库存水平下降到一定水平(补货点)时,自动触发采购订单下单的一种采购策略。
该采购策略使用于:(1)国网物料通用性比较好、用量比较稳定的物料;(2)低值易耗品(例如螺钉)和生产辅料。
再订购点采购模型示意图该模型若要在SAP系统中运行,要确定三个参数:安全库存S、再订购点(ROP)和订购批量。
◆再订购点计算公式错误!未找到引用源。
上式中:ROP:再订购点量;R:日均消耗量;L:采购提前期时间(天)S:安全库存数量;◆订货批量Q确定方法一:通过采用经济订货批量(Economic Order Quantity, EOQ)模型,将库存持有成本和订货成本的总成本最小化,可以确定最佳的订货批量。
EOQ可以采用如下的公式进行计算:其中:错误!未找到引用源。
=订货成本错误!未找到引用源。
=年需求量或产品的使用量(单位数)错误!未找到引用源。
=年库存持有成本(产品成本或价值的一个百分比) 错误!未找到引用源。
=每单位库存的平均成本或价值方法二:基于最高库存法计算对于体积大的物料可以根据库房最大容量限制计算其最大库存;对于体积小但占用资金大的物料可根据设定的最高库存周转天数和最大消耗速率计算。
Q=Q max -ROPQ Max − 最高库存量安全库存(S )计算公式情况一:对于日均消耗量波动,而采购提前期不变R S k δ=其中:S :安全库存;K :根据商品允许缺货率(即服务水平)而设置的安全系数,可根据概率统计理论推算,常用的K 值如下表[1]:表 服务水平与安全系数K 对应表L :采购提前期的平方根;R δ:单位时间消耗量的波动程度;情况二:日均消耗量和采购提前期都变化的情况S k =其中:LT :平均的补货周期D δ:日销售量的标准偏差(反映其波动情况)D :平均日销售量:采购提前期的标准偏差(反映其波动情况)LD再订购点采购策略试运行阶段性总结一、再订购点采购物料阶段性情况说明:10月21日-11月24日,实行调高最低库存、采购批量策略,库存水平迅速上升,缺料情况得到缓解,11月24日以来通过调低最低库存、采购批量的策略,以紧缩降低库存水平,但是由于原有在途订单交货不能立竿见影达到降低库存的效果,在紧缩控制库存的调控下,库存下降预计有15-20天左右的滞后性,库存将在12月31日控制在合理较低水平。
- 1、下载文档前请自行甄别文档内容的完整性,平台不提供额外的编辑、内容补充、找答案等附加服务。
- 2、"仅部分预览"的文档,不可在线预览部分如存在完整性等问题,可反馈申请退款(可完整预览的文档不适用该条件!)。
- 3、如文档侵犯您的权益,请联系客服反馈,我们会尽快为您处理(人工客服工作时间:9:00-18:30)。
2021/2/4
3
周期服务水平
服务水平(CSL)是衡量随机型库存系
统的一个重要指标,它反映的是补货周期 内不发生缺货的概率。
CSL=Prob(周期需求≤ROP)
服务水平可用以下指标衡量:
(1)整个周期内供货的数量/ 整个周期的需求量
(2)提前期内供货的数量/提前期的需求量
系数
2021/2/4
需求服从正 态分布时的
再订货点
服务水平 (无缺货概率)
无缺货概率
安全 库存
平均需求
再订货点
安全 系数
0
Z
6
给定采购补货策略下的服务水平衡量
服务水平(CSL)衡量公式:
CSL=Prob(周期需求≤ROP)
在需求服从正态分布的条件下,上式变为:
CSL=F( ROP,DLT ,σLT )
月
月
差
零售 218 188 225 217 176 187 221 212 210 203 188 商1
185 202. 16.8 5
零售 101 87 123 101 95 97 93 131 76 101 87 商2
114 100. 15.6 5
零售 268 296 321 312 301 294 285 305 289 303 324 商3
332 302. 18.0 5
总计 587 571 669 630 572 578 599 648 575 607 599
631 605. 32.4 5
产品在零售这一级的单位价值为10美元,在仓库的单位价值为5
美元。库存持有成本率为每年20%。零售商的补货订单处理成本
是40美元/订单,仓库的是75美元/订单。零售商的补货提前期是
再订货点与安全库存
需求与提前期都是常数时的再订货点
在库存持有量能够满足等待订货期间 (即提前期)的需求时下订单。 若需求与提前期都是常数,再订货点为:
ROP = d LT 其中: d —— 需求率; LT —— 提前期
Q*=93
ROP=?
2021/2/4
2
需求与提前期变化时的再订货点
➢ 一旦需求或提前期发生变化,实际需求就 有可能超过期望需求。因此,为了减少缺 货风险,应持有额外库存即安全库存。这 时,再订货点为:
2 用一个安全库存来保证变化下的服务水平
2021/2/4
安全库存与需求分布的方差有关 安全库存与服务水平有关
5
服务水平与安全库存的关系
在提前期内需求 近似服从正态分 布的情况下,如 果没有安全库存, 缺货的概率可达 50% 。增加安全 库存后,降低了 缺货风险,提高 了服务水平。
标准正态分 布中的安全
2021/2/4
17
订货量,Q 再订货点,ROP 平均库存,AIL 订货周期(月)
零售商1 312 61 167 1.54
零售商2 220 35 120 2.19
零售商3 381 87 202 1.26
仓库应持有多少库存?
2021/2/4
18
根据汇总的客户需求预测计算多级库存订货批量、 再订货点和平均库存
2021/2/4
11
需求和提前期都不确定条件下的再订货点
DLT=d×ALT
σDLT= LT2 d2L2T
ROP = DLT+ SI = DLT+ z× σDLT
2021/2/4
12
例4中,假设提前期均值为3天,标准差为0.5天。
σDLT= LT2 d2L2T = 330 220200.52
=112 .7 SI=1.64×112.69≈185件 ROP=200×3+185=785件
2021/2/4
13
多级库存管理
• 多级库存管理:管理整个渠道的库存而不只是 各自独立的存储点的库存。
• 基本逻辑:渠道中的每一级都按自己的库存水平 加上来自所有下游的库存来进行库存计划。也即, 每一级库存水平 的计划都不是仅仅考虑自己下 一级的需求信息,而是考虑最终客户的需 Φ( 600050)00= Φ(1.414) ≈ 0.92
707
2021/2/4
8
给定服务水平下的安全库存及订货点的确定
基本原理:
对方程CSL=Prob(周期需求≤ROP)逆向求
解得ROP,再根据SI = ROP-DLT求安全库存。
在需求服从正态分布的条件下,则为:
ROP =F-1( CSL, DLT , σDLT )
d=2500; σ=500;
LT=2周;
ROP=6000;
Q=10000
SI=ROP-DLT=6000-2500×2=1000 周期平均库存=Q/2+ SI =10000/2+1000=6000
库存周转时间=平均库存/平均周转速度
=6000/2500=2.4周
σDLT= LT σ= 2×500≈707
hP
0.2010
ROP1 = d1×LTR+ SI1 = d1×LTR + z× σDLT1
= d1×LTR + z× σ1
LT R
= 202.5×0.25 +1.28×16.8 0.2=561.38
平均库存水平
AIL1=
Q 2
1+
z×
σ1
LT R
= 311.8/2 +1.28×16.8 0.25= 166.65
一周(LTR=0.25月),仓库的补货提前期是两周(LTW=0.5月)。 零售商和仓库都保证提前期内90%的现货供应比率。零售商和仓
库的订货点和订货数量用再订货点法求出。问仓库需要多少库
存?
2021/2/4
16
根据客户需求预测计算各零售商的订货批量、 再订货点和平均库存
Q1=
2DS = 2(20.2512)40=311.8或312件
0 .5= 551.32
中心仓库的实际平均库存: 551-(167+120+202)=62(假设没有在途库存)
2021/2/4
20
汇报结束
谢谢大家! 请各位批评指正
来的 k 倍。
缩短供应提前期需要供应商付出努力,而减少的是采购 商的库存,因而需要设计相应的收益分享激励机制。
降低需求的不确定性,即标准差σ 安全库存与标准差保持同比例下降。 方法:采用更好的市场情报系统和更先进的需求预测方法。
对供应链管理来说,要降低需求的不确定性,就必须使各环 节的预测与最终顾客需求的数据相一致,协同预测(CPFR)。
库存、仓库订单上的库存和零售商订单上的库存减去已经出
售给最终客户但尚未从库存中扣除的部分的总和。当该多级
库存水平降至332件时,下一张1044件的订单给供应商。
2021/2/4
19
根据汇总的客户需求预测计算多级库存订货批量、 再订货点和平均库存
平均库存水平
AILW=
Q
+W
2
z×σW
LT W
= 1043.98/2 +1.28×32.4
QW=
2DS = 2(60.5512)75 =1043.98或1044件
hP
0.205
ROPW = dW×LTW+ SIW = dW×LTW + z× σDLTW
= dW×LTW + z× σW
LT W
= 605.5×0.5 +1.28×32.4 0 .5= 332.03
对多级库存进行监控,多级库存是各零售商库存、中心仓库
ROP
LT
DL=T Φ-1(
CSL
,
0,
1)
ROP = DLT+Φ-1( CSL , 0, 1)× σLT
SI =Φ-1( CSL , 0, 1)× σLT
2021/2/4
安全系数z
转化为标准正 态分布求解
9
例4:某大型服装零售商销售一款服装,每天平 均需求量为200件,标准差为30件,订货提前期 为3天。若该零售希望达到95%的周期服务水平, 则应如何确定安全库存和再订货点?
首先计算订货提前期内的标准差 σDLT=LT σ=3 ×30=1.732×30=51.96
查正态分布表得 z(0.95)=1.64
因此安全库存SI=1.64×51.96≈ 85件
再订货点ROP=200×3+85=685件
订货批量可由一般经济订货批量模型确定。
2021/2/4
10
降低安全库存的方法
缩短供应提前期 如果提前期缩短到原来的k倍,安全库存则降低为原
=Φ( ROP DLT, 0, 1) DLT
转化为标准正 态分布求解
2021/2/4
7
例3:假定联想电脑某款芯片的周需求符合正态分布,
均值为2500,标准差为500。供应商的供货提前期为两
周。目前联想的库存控制策略是连续盘点,当库存芯片
少于6000片时,订货10000片。试分析该芯片库存的均
值,安全库存和库存周转时间;并衡量周期服务水平。
(3)顾客订货得到完全满足的次数/ 订货发生的总次数
(4)不发生缺货的补充周期数/ 总补充周期数
(5)手头有货可供的时间/ 总服务时间
2021/2/4
4
如何处理不确定性需求?
• 如何表示需求变化?
σ = DLT LT σ
用标准方差 • 库存在不确定性需求下如何处理?
DLT=d×LT
1 用批量定货量与平均需求匹配
14
常见的多级库存渠道
仓库层级
仓库,
提前期,LTW
S
W
供应商
仓库
2021/2/4
R1 d1,σ1