模具制造及产品设计的相关规范
模具设计规范

模具设计规范一、模具工程代号:PG—顺送PB—连续开料BK—外形CP—外形及孔PC—冲孔NC—缺口加工BR—抽牙BN—押曲UB—U曲VB—V曲LB—L曲RB—R曲ZB—Z曲WB—W曲CL—卷外弯加工CB—复合弯曲DB—面押CK—窝合模HB—冲台DR—拉伸CT—分断TP—攻牙VM—折床SW—碰焊AW—烧焊PL—电镀PT—喷油HT—热处理RK—校正LV—直平RV—窝钉TB—镏披锋DG—除油PK—包装SS—丝印OT—其它二、产品图及展开图的绘制:要把客户的产品转化为设计所需的产品图。
比如:尺寸公差的调整,形状的修正等。
1.所有产品图纸尺寸需与电子图文件核对一遍。
确认产品图纸与电子图文件正确无误。
2.所有公差尺寸在图纸上用颜色笔作好标记,以便于审查、校对,且有助于自我记忆。
3.所有图形尺寸的公差调整,按其产品图纸所需加工精度要求适当调整。
例如下表:4.折弯尺寸公差调整,如尺寸公差标注在外面时,其公差需放在凸模上,母模按其尺寸调整实数做;如尺寸公差标注在内面时,其公差需放在母模上,凸模按其尺寸调整实数做。
5.设计者对图面有疑问时,应及时做好标记、并呈报上级主管共同商讨其对策。
例如:冲压件的工艺极限,图面的图形、注解及其尺寸等问题不清或有疑问等等,可向上级呈报说明其详细情况后,通过提出打合书、检讨依赖书、要望申请书等书面形式与客户联络。
其方式可采用FAX或E-mail转送、答复。
我公司优先采用FAX方式联络。
三、排样图1、首先要确定产品的毛刺方向,压延方向;产品的毛刺方向一般情况下由客户下决定:产品的压延方向当客户有特殊要求时按客户的要求来做;当客户无特别要求时,对各向同性的材质(SECC、SPCC、SPCE)来讲,应以材料的利用率为优先考虑,其产品的加工难易程度及生产稳定性面不需要考虑压延方向;对各向异性的材质(如SUS、铜材等)来讲,首先要考虑材质的纤维方向不可与折弯方向相平行,其次才考虑带料的稳定性及加工的容易程度。
模具行位设计标准要求规范

模具行位设计标准要求规范模具行位设计标准要求规范主要包括以下几个方面:一、尺寸要求:模具行位的尺寸应符合国家标准或相关行业标准的要求。
包括行位的长度、宽度、高度、孔径等尺寸参数。
行位的尺寸应与相邻模具零件的尺寸保持一致,确保模具在装配的过程中能够正常配合、连接。
二、垂直度要求:模具行位的垂直度是指行位与模具的垂直度,也是指行位上下两个面的平行度。
行位的垂直度要求符合国家标准或相关行业标准的要求。
垂直度的要求主要是为了保证模具的精度和稳定性,使其在使用过程中不产生变形、偏斜等问题。
三、表面质量要求:行位的表面质量要求符合国家标准或相关行业标准的要求。
行位的表面应光滑、平整,不得有明显的裂纹、气孔、划痕等缺陷。
表面质量的要求主要是为了保证模具的精度和使用寿命,使其能够正常运行。
四、材料要求:模具行位的材料要求应符合国家标准或相关行业标准的要求。
行位的材料应具有一定的强度和耐磨性,能够承受模具在使用过程中的压力、冲击等力量。
材料的选择要根据具体的模具使用环境和工作条件来确定,确保模具的使用效果和寿命。
五、加工精度要求:模具行位的加工精度要求应符合国家标准或相关行业标准的要求。
行位的加工精度主要包括尺寸精度、形位公差、表面粗糙度等指标。
加工精度的要求主要是为了保证模具的精度和稳定性,使其能够满足产品的要求。
六、安装要求:模具行位的安装要求应符合国家标准或相关行业标准的要求。
行位的安装应牢固可靠,保证模具在使用过程中不会因为行位的松动而产生误差。
安装的过程中要注意行位与相邻模具零件的配合和对齐,确保模具的装配精度和稳定性。
以上是模具行位设计标准要求规范的一些主要内容,具体的标准要求还需要根据具体的模具类型、使用环境和产品要求来确定。
模具行位的设计标准要求规范能够保证模具的质量和性能,提高模具的使用效果和寿命。
同时,对于模具生产厂家和用户来说,严格按照标准进行设计和生产,有助于提高产品的竞争力和市场占有率。
第1章 模具制造工艺规程

第1章模具制造工艺规程1.1 模具制造工艺规程编制的基本概念1.1.1生产过程与工艺过程1.生产过程制造模具时,将原材料或半成品转变成为成品的各有关劳动过程的总和称为生产过程。
具体地讲,模具制造是在一定的工艺条件下,改变模具材料的形状、尺寸和性质,使之成为符合设计要求的模具零件,再经装配、试模和修整而得到整副模具产品的过程。
广义的模具生产制造过程还应包括生产技术准备、模具零件加工和模具装配等阶段。
(1)生产技术准备生产技术准备阶段的主要任务是分析模具图样,制订工艺规程;编制数控加工程序;设计和制造工装夹具;制定生产计划,制定并实施工具、材料、标准件等外购和零件外协加工计划。
各种生产服务活动如生产中原材料、半成品和工具的供应、运输、保管以及产品的包装和发运等。
(2)模具零件加工在模具零件加工中,加工的工艺方法非常多,基本可以概括为:1)传统的切削加工,如车、钳、刨、铣、磨等;2)非切削加工,如电加工加工、冷挤压、铸造等;3)数控加工,如数控铣削、加工中心加工等;4)焊接、热处理和其它表面处理等。
根据模具零件的分类加工对象可以分为两种:1)非成形零件加工,结构零件类零件加工。
这些零件大多具有国家或行业标准,部分实现了标准化批量生产。
在模具工艺规划中,根据设计的实际要求和企业的生产实际可选择外购或由本企业加工。
2)成形零件加工,型腔类零件的加工。
如注射模具的成形零件一般结构比较复杂,精度要求高,有些模具型腔表面要求有纹饰图案。
其加工过程主要由成形加工、热处理和表面加工等环节构成。
特种加工、数控加工在模具成形零件加工中应用非常普遍。
(3)模具装配模具装配是根据模具装配图样要求的质量和精度,将加工好的零件组合在一起构成一副完整模具的过程。
除此之外,装配阶段的任务还有清洗、修配模具零件,试模及修整等。
由上述过程可以看出,模具产品的生产过程是相当复杂的。
为了便于组织生产和提高劳动生产率,现代模具工业的发展趋势是自动化、专业化生产。
模具的设计与制作要求

模具的设计与制作要求1.准确的产品尺寸和形状:模具的设计要根据产品的准确尺寸和形状进行,这是保证产品质量和一致性的基础。
同时,也要考虑到产品的形状复杂性,进行合理布局和结构设计。
2.合理的材料选择:模具的工作环境要考虑到温度、压力、磨损等因素,所以在材料的选择上需要具有良好的耐磨性、耐腐蚀性和热稳定性。
一般常用的模具材料有铸钢、工具钢、硬质合金等。
3.可靠的结构设计:模具的结构设计要考虑到产品的工艺要求和承受的力,以确保模具在工作过程中不变形、不破裂,并有足够的刚度和强度。
另外,还要考虑到模具的分解性、装配性和可维修性,方便模具的更换和维护。
4.高效的冷却系统设计:模具的制作过程中会产生大量的热量,如果不能有效地散热,会导致模具温度过高,进而影响产品质量和模具寿命。
因此,模具的设计中要充分考虑冷却系统的设置,合理布置冷却通道和出水口,以提高散热效果。
5.精密的加工工艺:模具的制作一般采用数控机床进行精密加工,要求加工精度高,尺寸精确,表面光洁度好。
加工工艺包括铣削、钻孔、褶皱、车削、车削、划线等,要保证模具的加工质量和尺寸精度。
6.严格的质量控制:模具的设计与制作过程中,要进行严格的质量控制,包括原材料的采购、模具制作过程中的检测和验收,以及最终的模具出厂检验。
尤其对于关键部件和加工工艺要进行特别的把关。
7.合理的模具使用和维护:模具的使用和维护也非常重要,要按照操作规范进行使用,定期保养和维修,并且要妥善保管模具,以延长模具的使用寿命。
总之,模具的设计与制作是一个相对复杂和繁琐的工作,需要综合考虑产品的需求、材料的特性、工艺的要求以及工装设备的配合等多个因素,以实现高效、精确、持久的生产制造目的。
模具加工精度国标标准

模具加工精度国标标准模具作为制造业中的重要工具,其加工精度直接影响到产品的质量和生产效率。
为了规范模具加工行业,国家制定了一系列国标标准,以确保模具的精度和质量。
本文将对模具加工精度的国标标准进行简要介绍。
一、标准概述模具加工精度的国标标准是为了确保模具的制造和验收符合一定的精度要求而制定的。
这些标准涉及到模具的设计、制造、检测和维修等各个环节,为模具行业的健康发展提供了有力保障。
二、主要标准内容1. 设计阶段在模具设计阶段,国标标准规定了模具的基本结构、材料选择、热处理等方面的要求。
设计人员需要根据产品需求和生产工艺要求,合理选择模具结构,确保模具的强度、刚度和稳定性。
同时,还要考虑到模具的加工和维修便利性。
2. 制造阶段在模具制造阶段,国标标准对加工设备、工艺流程、加工精度等方面进行了详细规定。
加工设备需要满足一定的精度和稳定性要求,工艺流程需要合理安排,以保证模具各部分能够达到要求的精度。
此外,对于模具的关键部位,如型腔、浇口、冷却通道等,需要采用高精度的加工设备和技术,以确保其精度和质量。
3. 检测阶段在模具检测阶段,国标标准规定了检测方法、检测工具和检测标准。
检测方法可以分为非接触式和接触式两种,检测工具需要根据具体的检测项目进行选择。
检测标准包括尺寸精度、形位公差、表面粗糙度等方面的要求,检测人员需要根据标准要求对模具进行全面检测,确保其符合质量要求。
4. 维修阶段在模具维修阶段,国标标准规定了维修流程、维修标准和维修记录等方面的要求。
维修人员需要定期对模具进行检查和维护,及时发现并处理存在的问题,确保模具的正常运行和使用寿命。
同时,还需要建立完善的维修记录,以便对模具的使用和维护情况进行跟踪和管理。
总之,模具加工精度的国标标准是确保模具质量的重要保障。
通过遵循这些标准,可以有效地提高模具的制造和验收质量,降低生产成本,提高生产效率,为制造业的发展提供有力支持。
模具管理办法:模具制造质量标准
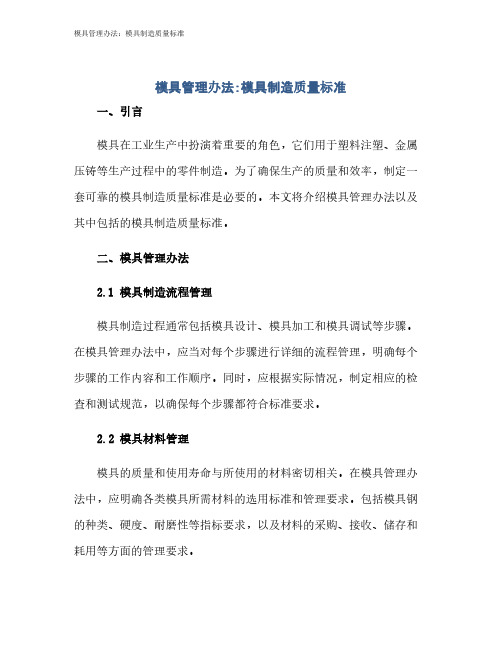
模具管理办法:模具制造质量标准一、引言模具在工业生产中扮演着重要的角色,它们用于塑料注塑、金属压铸等生产过程中的零件制造。
为了确保生产的质量和效率,制定一套可靠的模具制造质量标准是必要的。
本文将介绍模具管理办法以及其中包括的模具制造质量标准。
二、模具管理办法2.1 模具制造流程管理模具制造过程通常包括模具设计、模具加工和模具调试等步骤。
在模具管理办法中,应当对每个步骤进行详细的流程管理,明确每个步骤的工作内容和工作顺序。
同时,应根据实际情况,制定相应的检查和测试规范,以确保每个步骤都符合标准要求。
2.2 模具材料管理模具的质量和使用寿命与所使用的材料密切相关。
在模具管理办法中,应明确各类模具所需材料的选用标准和管理要求。
包括模具钢的种类、硬度、耐磨性等指标要求,以及材料的采购、接收、储存和耗用等方面的管理要求。
2.3 模具加工设备管理模具加工设备的精度和性能将直接影响模具的制造质量。
在模具管理办法中,应对加工设备的选型、保养、维修和检验等方面进行详细规定。
确保加工设备的正常运行,提高模具制造的精度和效率。
2.4 模具质量控制模具质量控制是模具制造过程中的重要环节。
在模具管理办法中,应对模具的制造过程中的质量控制进行详细规定。
包括对模具尺寸、外观、装配精度、性能和使用寿命等方面的检验标准和方法。
三、模具制造质量标准3.1 模具尺寸精度标准模具的尺寸精度直接影响着产品的制造质量。
在模具制造质量标准中,应规定模具各个零部件的尺寸精度标准。
这些标准可以参考国家相关标准,或根据企业的实际情况制定。
3.2 模具装配精度标准模具在使用过程中需要完成各种装配动作,因此模具的装配精度标准也是一个重要的考虑因素。
在模具制造质量标准中,应规定模具的装配精度标准,并根据实际需求制定相应的装配检验方法和标准。
3.3 模具性能和使用寿命标准模具的性能和使用寿命直接关系到产品的质量和生产效率。
在模具制造质量标准中,应规定模具的性能指标和使用寿命标准,并制定相应的测试方法和评估标准。
模具设计的标准

模具设计的标准1. 引言模具设计在工业制造中起着至关重要的作用,它们被广泛应用于金属加工、塑料注塑、汽车制造以及电子设备等领域。
一个优质的模具设计对于产品质量和生产效率有着重要的影响。
因此,制定模具设计的标准是必要的,可以确保设计师们具备相同的设计要求和目标。
2. 模具设计的基本原则模具设计的标准旨在优化设计过程、提高生产效率、确保模具质量和保证产品规格的一致性。
以下是模具设计的基本原则:2.1 简化设计模具设计应该尽量简化模具的结构和零件数量,以减少制造成本和加工时间。
简化的设计可以降低模具的重量,提高使用寿命,并且方便清洁和维护。
2.2 提高精度和可靠性模具应该具备高精度的加工能力,以确保产品的质量和准确性。
此外,模具设计还应考虑到材料的可靠性和耐用性,以便长时间使用而不损坏。
2.3 考虑制造和加工要求模具设计应充分考虑制造和加工过程中的要求,例如模具的可加工性、装配性和调试性等。
合理的设计可以减少制造过程中的错误和延误。
3. 模具设计的标准要素为了确保模具设计的一致性和可比性,以下标准要素应该包括在模具设计中:3.1 尺寸和公差模具设计中应明确规定产品的尺寸和公差要求。
尺寸和公差的标准化可以确保不同批次生产的产品具有相同的质量和功能。
3.2 材料选择在模具设计中,应根据产品的特性和使用环境选择合适的材料。
考虑因素包括高温、高压、腐蚀性和耐磨性等要求。
3.3 模具标准件模具设计中应尽量使用标准件,以减少设计和制造的复杂性。
标准件的使用可以降低制造成本和提高模具的可维护性。
3.4 塑料模具特殊要求在塑料模具设计中,考虑到流道设计、冷却系统、顶针和脱模机构等特殊要求。
这些要求对产品质量和生产效率的影响非常重要。
4. 模具设计的流程为了确保模具设计的一致性和规范性,一个典型的模具设计流程应包括以下步骤:4.1 分析和定义在模具设计之前,应进行产品的分析和定义。
了解产品的功能、样式和尺寸要求是设计一个合适的模具的基础。
模具设计制造及验收技术要求

技术协议附件三模具设计制造及验收技术要求1.大体技术条件1.1.模具设计的大体技术条件1.1.1.工法图设计和模具结构设计必需按用户确认的《钣金件模具设计标准》及提供的《冲压设备技术参数》和冲压生产布线要求。
用户将对冲压工艺方案、冲压设备选用情形、模具结构方案进行认可性会签。
1.1.2.所需卖方开发模具的零件:W=2490车身的驾驶室总成(包括仪表板总成和流水槽)、需要制作弯曲成形类模具的型材和前保险杠总成等与驾驶室同时过油漆线的零件。
1.1.3.按A级标准开发模具的钣金件是:全数外覆盖件(包括:左/右车门外板、前保险杠、顶盖、左/右后侧围外板、左/右前柱外板和后围外板等)、大型或复杂钣金件(包括:后围内板、左/右车门内板、左/右边围内板、地板鼓包等)、t≥的厚板料钣金件(包括:左/右前纵梁、左右后纵梁等);其余钣金件、滚压件和型材按B级标准开发模具。
1.1.4.卖方提供给用户的模具冲出制件的材料利用率必需达到车门为70%,地板为90%,平均为80%以上。
如卖方在冲压工艺要领图设计时,如有发觉材料利用率不能达到要求时,应进行CAE分析,提供出科学准确的材料利用率数据供用户确认。
1.1.5.模具工作部份的材料选用原那么及热处置要求:1.1.6.模具的安装应方便快捷,中大型模具采纳托杆快速定位,应能利用快速安装夹紧装置。
1.1.7.所有模具应考虑得手工操作的平安合理性(如:良好的视野,足够的操作空间和操作区域),便于操作、维修、搬运与寄存,坯件的送进掏出方便,坯件的定位靠得住,废料的排出平安通畅;模具的零部件应考虑防松、防崩、防脱落、防冲击等方法;活动零部件应有平安方法,应有行程限位器、寄存限位器、平安块、防护板、防护罩等。
1.1.8.模具的导柱均安装在下模座上,模具的起重和翻转应在设计时考虑。
1.1.9.模具的气动接头采纳快换接头,接头的安放位置及尺寸规格与压机匹配,并应备有堵塞和换向阀及调压阀;接头插座的顺序排列为定位装置升起、下降、托料装置升起、下降。
- 1、下载文档前请自行甄别文档内容的完整性,平台不提供额外的编辑、内容补充、找答案等附加服务。
- 2、"仅部分预览"的文档,不可在线预览部分如存在完整性等问题,可反馈申请退款(可完整预览的文档不适用该条件!)。
- 3、如文档侵犯您的权益,请联系客服反馈,我们会尽快为您处理(人工客服工作时间:9:00-18:30)。
模具制造及结构设计的相关设计规范一、行位系统涉及的结构设计规范二、斜顶系统涉及的结构设计规范三、进胶系统涉及的结构设计规范四、外观要求涉及的结构设计规范五、顶出机构涉及的结构设计规范六、注塑成型涉及的结构设计规范七、模具强度涉及的结构设计规范一、行位系统问题点1. 圆形隧道行位1.1设计圆形隧道行位,模具分型面到圆形镶件之间的钢料应保证 1.5MM以上A,行位镶件直径15毫米以下,模具分型面到圆形镶件之间的钢料厚度保证 1.8MM以上B,行位镶件直径15/30毫米,模具分型面到圆形镶件之间的钢料厚度保证 2.8MM以上备注;以上数据为模具量产的可靠值,防止隧道孔压变形、断裂导致内模重制,影响生产进度2. 方形及异形隧道行位2.1设计方形及异形隧道隧道行位时,模具分型面到行位镶件之间的钢料厚度应保证以下数据:A,宽度15毫米以下,厚度保证1.8以上B,宽度15/30毫米,厚度保证2.5以上C,宽度30/50毫米,厚度保证3.5以上备注;以上为模具量产的可靠值,防止隧道孔压变形导致内模重制,影响生产进度。
3. 隧道行位镶件碰穿内模薄铁3.1设计隧道行位,有时会出现行位镶件碰穿薄铁的现象,薄铁厚度应保证以下数据: A,薄铁高度15毫米以下,厚度保证3毫米以上备注;以上为模具量产的可靠值,防止薄铁变形断裂导致重制,影响生产进度4. 后模行位镶件碰穿内模薄铁4.1设计后模行位,有时会出现行位镶件碰后模薄铁的现象,厚度应保证以下数据:A,薄铁高度15毫米以下,薄铁厚度保证2MM以上B,薄铁高度15/20毫米,薄铁厚度保证3MM以上备注;以上数据为模具量产的可靠值,防止变形导致切割镶件重制薄铁位置,影响生产进度。
5. 后模行位镶件碰穿斜顶镶件5.1设计前模行位,有时会出现前模行位镶件碰穿后模斜顶现象,会出现以下风险: A,容易出现行位镶件和斜顶撞模,出现工件重制,甚至压模。
B,两个碰穿零件容易磨损,出现产品批峰导致烧焊或者重制镶件。
备注;以上情况产品结构请尽量避免,影响模具生产且修模频繁。
1、斜顶系统如图所示,两扣距离保证13mm以上,且扣位脱模深度在1mm以内,小于以上参数会出现以下问题。
A,两斜顶顶出行程不足,导致撞斜顶模。
B,斜顶只能做小到4毫米以下,强度不足易断裂,甚至断裂后撞坏前模外观,导致前模降面重新加工和斜顶重制如图所示,两扣距离保证10mm以上,小于以上参数会出现以下问题。
A,要保证两斜顶之间的模具强度。
也有利于后模顶针板斜顶挂台镶件的分布如图所示,此距离保证3mm以上,小于以上参数会出现以下问题A,存在薄铁,影响模具强度,生产容易断裂,修模率高,不利量产。
此种情况扣位距离保证19mm以上,且扣位脱模深度在1mm以内,小于以上参数会出现以下问题A,产品空间所限制斜顶只能做小,强度不足易断裂,甚至断裂后撞坏前模外观,导致前模降面重新加工和斜顶重制此种情况此距离保证20mm以上,且扣位脱模深度在1mm以内,小于以上参数会出现以下问题A,保证斜顶滑动空间和模具装配的可实现性。
备注;以上情况产品结构请避免,防止模具量产时有断斜顶风险,频繁修模,以上情况都是根据注塑生产修模反应出来的模具强度问题,修模多影响注塑生产三、进胶系统对结构设计和模具设计的要求1.细水口点进胶良好进胶案例大面积薄胶不良进胶案例A,特点:进胶速度快、开模水口自动脱落;B,缺陷:点胶口周围有少量气纹、水口拉断后有残留水口咼出(0.1〜0.2 )mm进胶速度快无缓冲空间在填充较小胶厚产品的模具型腔易产生气体导致困气;C,不良进胶案例说明:1.1,结构要求透明件产品正反面不能有胶口和顶针印痕,模具评审侧进胶流道拐角纵多会延缓走胶速度及压力要求前期结构改善增加弹力臂胶位宽度和厚度;评审结果结构要求参照样板设计在弹力臂底面点进胶直接入型腔(主型腔12.0X4.6X2.8mm胶厚、弹力臂胶厚0.8mm),点进胶在0.8mm薄胶处向厚2.8mm的型腔走胶产生困气导致顶面缩水存在(产品结构限制无法加工排气位置),后模具仍修改为大水口侧进胶但仍有轻微缩水印痕。
1.2,注塑面积及融胶量过大且有做高光外观产品,首要考虑注塑成型降低外观瑕疵和弯曲变形风险故采用在二次外观面上胶厚处点进胶,由于点进胶一侧存在(36X18X.6 ) mm大面积薄胶位注塑时从薄胶位置走胶过渡到厚胶过程中产生了注塑应力作用呈现出了凹凸不平影响到外观,后期模具要求加厚胶位改善了点胶口附近的凹凸不平综合上述点进胶特点及以往缺陷对结构设计和模具设计提出建议:1.3,建议产品设计首要考虑注塑采用点进胶来满足外观及变形控制, 预留点胶位不能在:薄胶顶面、薄胶附近、1.4,结构设计预留点胶口底部胶厚需满足 1.0mm以上厚度,如点胶口预留在厚以下不能满足注塑条件;1.5,外观要求镜面、高光面、细纹面产品模具建议结构设计前期优先采用点胶注塑并预留点胶位置;1.6,模具结构选用点胶注塑时事项:点胶口位置根据结构预留空间定位,口径大小根据产品注塑填充胶量定义口径;胶口位置及口径大小限制注塑速度、时间和压力,口径过大不易拉断、拉断后存在残留水口干涉主装;,唧嘴直接进胶A, 特点:直接走胶速度快、外观上无碰穿孔时不产生熔接线;B, 缺陷:增加了注塑完成后续水口加工;综合上述唧嘴直接进胶特点及缺陷对结构设计和模具设计提出建议:1. 非外观且注塑面积较大产品首要选择大水口注塑;2. 产品预留进胶口位置周圈胶厚不得薄于0.8mm胶口周圈薄胶宽度不得大于3. 镜面光和高光面产品可选择在遮蔽位置产品设计预留进胶位置,注塑完成后采用后续加工冲压或锣掉;3. 搭接侧进胶1.0mm 胶1.0mm;A,特点:走胶速度快,可满足丝印、电镀等后工艺辅助架框;(侧进胶类型:扇形进胶, 锥形进胶、平直进胶)B,缺陷:进胶口剪切后产品侧面存在疤痕和残留水口高出(0.15〜0.2 )mm喷油、电镀都无法遮蔽疤痕综合上述搭接侧进胶特点及缺陷对结构设计和模具设计提出建议1,镜片类及小配件产品结构设计前期可优先选择侧进胶注塑,方便产品后工艺加工;2,以注塑角度建议镜片类产品如:(15X25)mm面积的胶位设计厚度不能薄于0.7mm以满足注塑成型保证外观,以此类推注塑面积增大胶位同等比例加厚;3, 设计带裙边的透明产品模具建议裙边胶厚做到0.7mm以上并预留侧进胶位置裙边宽度不大于2.0mm。
不良注塑案例说明:主体直径5.0mm厚度2.2mm裙边厚度0.5mm注塑存在困气导致缩水且顶出困难,4, 普通产品设计预留侧进胶时裙边胶厚建议(厚0.7mm以上、宽度2.0mm以内);4. 搭底进胶,特点:走胶速度快,可满足丝印、电镀等后工艺辅助架框;(侧进胶类型:扇形进胶,锥形进胶、平直进胶)B,缺陷:进胶口剪切后产品地面存在疤痕和残留水口高出(0.15〜0.2 )mm主装存在干涉风险,残留水口需修剪平整;综合上述搭接搭底进胶特点及缺陷对结构设计和模具设计提出建议1.结构设计需电镀产品可优先选用搭底进胶,产品设计时考虑预留出残留水口对主装的干涉的避空空间;5. 潜伏顶针和骨位进胶A, 特点:潜伏牛角进胶产品外观上无胶口缺陷,注塑不需处理水口;B, 缺陷:进胶口顶面会存在气团影响外观,喷油等处理仍有轻微瑕疵,不适合镜面、细纹面和薄胶产品米用;综合上述特点及缺陷对结构及模具结构要求:1. 结构设计预留牛角进胶要考虑牛角进胶口顶面胶厚不得薄于 1.5mm,避免影响外观;2. 结构设计预留牛角进胶在内壁骨位时建议预留主装干涉避空位,因模具设计牛角进胶在产品骨位上时会在骨位上局部加大胶厚有干涉主装可能;进胶案例A, 特点:潜伏顶针或骨位进胶可以满足外观上无胶口缺陷;B, 缺陷:顶针进胶水口需后续剪切加工、剪切水口后存在残留水口高出(进胶骨位顶面会有轻微气纹;综合上述特点及缺陷对结构及模具结构要求:0.2 〜0.5 ) mm1. 产品设计预留顶针进胶的残留水口对主装干涉的空间;6. 牛角进胶四、产品外观对结构件要求:1.外观拔模需求:外观出模斜度产品外观高度(0.0mm) 脱模斜度光面/高光面/镜面纹面1.0 〜2.023.0 〜10 1.5避免出模后外观拖伤10以上 1.21.0 〜5.0纹板度数+仝1以益新纹板为准;例如:YS1281-A (1°) 5.0以上纹板度数+仝0.5产品出模要求单边拔模(1.5 〜2)度。
备注2.枕位、滑块和斜顶与前模插破拔模需求:类型 孑L 高度(0.0mm) 插(靠)破面斜度备注枕位/滑块、1.0〜 -3.03 小于拔模需求模具量产时易损坏,导致 3.0-5.0 2 重制5.0以上1.5 斜顶2.0以下 4 小于拔模需求模具量产中导致产品外观3.0〜 -5.0 3 拉伤线条,5.0以上 2六、注塑成型对结构设计要求A,结构设计时外观的刻字或花纹最细胶位不得窄于(0.25〜0.3 ) mn ,深度不得超出0.3mmB,结构设计时骨位厚度不得大于产品顶面及侧面胶的75%m否则存在缩水风险(例如:1.0mm胶位做0.6mm骨位);C.结构设计掏胶位根据产品面积大小做减胶,减胶所需面积越大深度要求越小;最深的掏胶不得超出顶面胶厚的20%,另外掏胶的口边倒R或斜坡顺接避免注塑存在厚薄胶应力印痕风险;产品顶面最厚位置胶厚0.9m m,掏胶面积过大占产品一半位置且顶面薄胶0.6mm,模具注塑薄胶区域产生困气难易满胶,增大注塑压力满胶后产品外观出现应力印痕及整体弯曲变形。
产品顶面胶厚2.2mm,薄胶厚度1.0mm,注塑时产品严重应力印痕且变形突出。
七、模具强度对结构设计的要求1. 产品胶位之间薄铁参照数值;备注小于模具要求量产时易损坏修模几率高: 断裂镶件重制,影响量产不能顺利进行;2. 产品设计中扣位的斜顶与骨位镶件、镶针之间大于 2.0mm 间距,反之模具无法保证强度会导致量产过程中修模几率过高;(前面斜顶系统已经说明)3. 产品设计必须保证斜顶退出方向扣位面与骨位、柱位表面不得小于7.0mm 距离,扣位设计预留斜 顶宽度方向不得窄于4.0mm一圆孔切点与PL 面不得小于1.5mm 薄铁;详细参考数值:直径 厂5.0mm 以内保持1.0mm (5.0〜10.0直径)以内保持2.0mmI方孔、椭圆或异型孔跨距 10mm 以下,PL 面下薄钢不得小于4. 隧道滑块与PL 面之间薄铁:* .(1.5〜1.8mm );方孔、椭圆及异型跨距(10〜50)mm 以内,PL 面下铁料厚度不得 j 小于 3.5mm ;模具部制2010-7-8类型薄铁深度范围(mm 最低薄铁厚度1.0〜 -3.0 0.5 〜0.7薄铁3.0-5.0 1.5 5.0〜 *10 2.5 10〜303.5。