再生器反应器
反应器、再生器检修施工方案
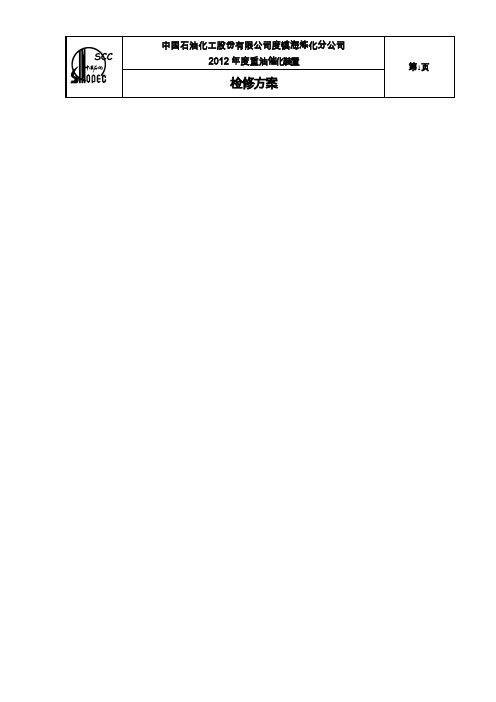
检修方案检修方案1.0工程概况1.1工程简介中国石化镇海炼化分公司炼油四部催化车间反应区的沉降器(T-201)、第二再生器(T-203)、外取热器(T-204)及其附属的项目检修是镇海炼化2012年度催化车间检修的关键项目。
本方案将重点阐述检修过程中的生产组织、施工程序、计划安排、质量控制、现场管理、安全措施以及施工机具和手段用料等内容。
1.2 工程特点本次检修施工时间紧,安装、吊装难度大,沉降器器、再生器、外取热器同时检修,由于施工作业空间狭小,给安装、吊装制造了极大的难度,施工时,大型吊车交叉作业多,各工种、工序、空间交叉施工较多,施工难度非常大。
为确保施工工期,前期预制工作要求在装置停气前进入施工现场并提前预制完毕。
1.3具体检修内容(根据镇海炼化炼油四部提供的资料)1.3.1沉降器(T-201)检修具体工作量1.3.2第二再生器(T-203)检修具体工作量序号名称材质规格(毫米)重量(吨)标高(米)备注序号名称材质规格(毫米)重量(吨)标高(米)备注1 开、封人孔和装卸孔2 ∮1100大油气线盲板装2次,拆1次3 ∮1100大油气线盲板法兰加碟璜.4 反再系统各人孔软梯安放固定5 DN1200提升管封头拆开6 提升管沉降器人孔、装卸孔档圈修理7 沉降器翼阀检查、更换8 汽提档板通气孔疏通9 提升管原料油进料喷嘴更换10 油桨进料喷嘴检查11 提升管中心环管,喷嘴加工更换12 DN1200提升管封头及法兰恢复13 底封头法兰拆开4对。
14 底部短节拆装(DN150)检修方案1 开、封人孔2 炉前瓦斯过滤短节拆装1只,DN803 F202火盆1只拆开,DN700,PN2.04 火盆连接软管拆除,DN80,DN40,DN15各1只5 配合火盆调试,油枪疏通,阀门拆装6 二再主风分布板检查,修补7 烧焦罐筒体钢板部分更换。
8 脱气罐锥体,再生立管部分更换。
9 大孔分布检查,耐磨喷嘴更换。
10 二再旋分检查3只,翼阀更换2只。
催化裂化装置工艺流程及设备简图
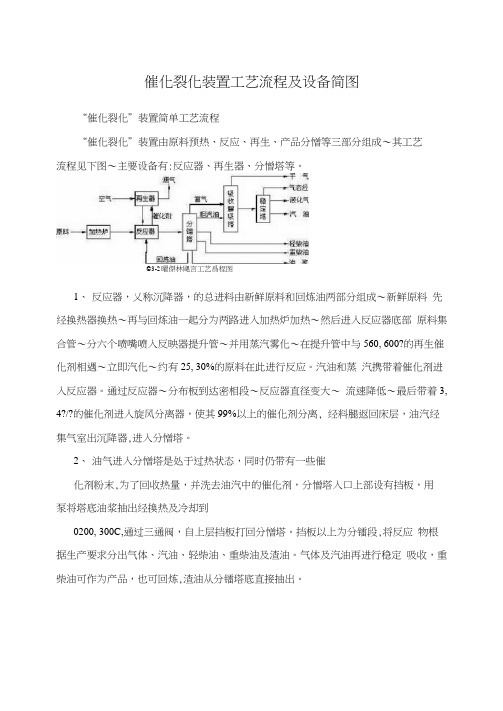
催化裂化装置工艺流程及设备简图“催化裂化”装置简单工艺流程“催化裂化”装置由原料预热、反应、再生、产品分憎等三部分组成〜其工艺流程见下图〜主要设备有:反应器、再生器、分憎塔等。
©3-2曜傑林飓言工艺爲程图1、反应器,乂称沉降器,的总进料由新鲜原料和回炼油两部分组成〜新鲜原料先经换热器换热〜再与回炼油一起分为两路进入加热炉加热〜然后进入反应器底部原料集合管〜分六个喷嘴喷入反映器提升管〜并用蒸汽雾化〜在提升管中与560, 600?的再生催化剂相遇〜立即汽化〜约有25, 30%的原料在此进行反应。
汽油和蒸汽携带着催化剂进入反应器。
通过反应器〜分布板到达密相段〜反应器直径变大〜流速降低〜最后带着3, 4?/?的催化剂进入旋风分离器,使其99%以上的催化剂分离, 经料腿返回床层,油汽经集气室出沉降器,进入分憎塔。
2、油气进入分憎塔是处于过热状态,同时仍带有一些催化剂粉末,为了回收热量,并洗去油汽中的催化剂,分憎塔入口上部设有挡板,用泵将塔底油浆抽出经换热及冷却到0200, 300C,通过三通阀,自上层挡板打回分憎塔。
挡板以上为分镭段,将反应物根据生产要求分出气体、汽油、轻柴油、重柴油及渣油。
气体及汽油再进行稳定吸收,重柴油可作为产品,也可回炼,渣油从分镭塔底直接抽出。
3、反应生焦后的待生催化剂沿密相段四壁向下流入汽提段。
此处用过热蒸汽提出催化剂,颗粒间及表面吸附着的可汽提桂类,沿再生管道通过单动滑阀到再生器提升管,最后随增压风进入再生器。
在再生器下部的辅助燃烧室吹入烧焦用的空气, 以保证床层处于流化状态。
再生过程中,生成的烟通过汽密相段进入稀相段。
再生催化剂不断从再生器进入溢流管,沿再生管经另一单动滑阀到沉降器提升管与原料油汽汇合。
4、山分镭塔顶油气分离出来的富气,经气压机增压,冷却后用凝缩油泵打入吸收脱吸塔,用汽油进行吸收,塔顶的贫气进入二级吸收塔用轻柴油再次吸收,二级吸收塔顶干气到管网,塔底吸收油压回分憎塔。
第六节催化裂化反应再生系统资料
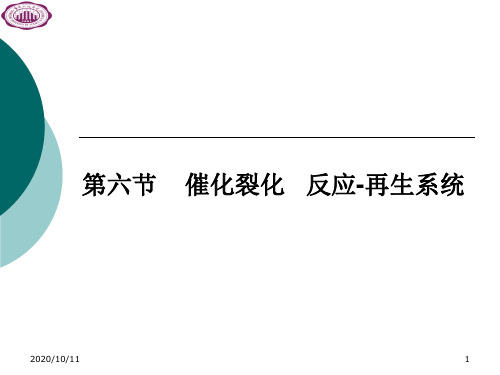
2020/10/11
19
c.快速床(循环流化床)再生 ➢气相转化成连续相,催化剂颗粒变为分散相,从而强化 了烧碳过程 ➢随着气速的提高,返混程度减小,中、上部接近于平推 流,也有利于烧碳强度的提高 ➢在快速流化床区域,必须有较大的固体循环量才能保持 较高的床层密度 ➢催化裂化装置的烧焦罐再生就是属于循环流化床的一种 再生方式
➢再生温度对烧碳反应速率的影响十分显著,提高再生温 度是提高烧碳速率的有效手段,在单段再生时,密相创层 的温度一般不超过730℃
➢工业上一般采用的空气线速为0.6~0.7m/s ➢工业装置采用的再生器压力在0.25~0.4MPa(绝)之间 ➢单段再生的主要问题是再生温度的提高受到限制和密相 床层的有效催化剂含炭量低
9
分段反应
➢不同的馏分需要不同的反应条件,理想选择是不同的 馏分在不同的场所和条件下进行反应 ➢两段提升管(Ⅰ型)催化裂化:
★第一段提升管只进新鲜原料,段间抽出柴油出装置 ★第二段提升管单独进循环油,显著改善产品分布 ★第二段提升管底部回炼汽油,降低汽油烯烃含量 ➢分段进料避免了新鲜原料和油浆的相互干扰
2020/10/11
18
b.两段再生 ➢两段再生是把烧碳过程分为两个阶段进行 ➢与单段相比,两段再生的主要优点是:
①对于全混床反应器,第一段出口的半再生剂的含碳量 高于再生剂的含碳量,从而提高了烧碳速率;
②在第二段再生时可以用新鲜空气和更高的温度,提高 了烧碳速率;
③第二段内的水气分压可以很低,减轻了催化剂的水热 老化;且第二段的催化剂藏量比单段再生器的催化剂藏量低, 停留时间较短。因此,第二段可采用较高的再生温度。
2020/10/11
20
2020/10/11
21
催化裂化装置反应器和再生器的技术改造
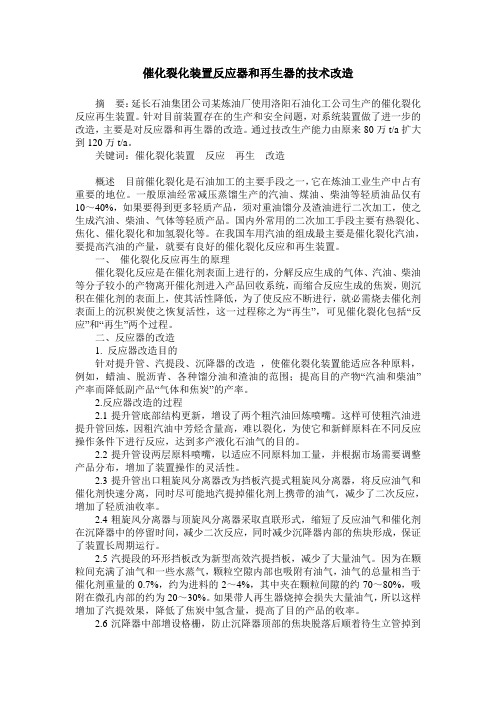
催化裂化装置反应器和再生器的技术改造摘要:延长石油集团公司某炼油厂使用洛阳石油化工公司生产的催化裂化反应再生装置。
针对目前装置存在的生产和安全问题,对系统装置做了进一步的改造,主要是对反应器和再生器的改造。
通过技改生产能力由原来80万t/a扩大到120万t/a。
关键词:催化裂化装置反应再生改造概述目前催化裂化是石油加工的主要手段之一,它在炼油工业生产中占有重要的地位。
一般原油经常减压蒸馏生产的汽油、煤油、柴油等轻质油品仅有10~40%,如果要得到更多轻质产品,须对重油馏分及渣油进行二次加工,使之生成汽油、柴油、气体等轻质产品。
国内外常用的二次加工手段主要有热裂化、焦化、催化裂化和加氢裂化等。
在我国车用汽油的组成最主要是催化裂化汽油,要提高汽油的产量,就要有良好的催化裂化反应和再生装置。
一、催化裂化反应再生的原理催化裂化反应是在催化剂表面上进行的,分解反应生成的气体、汽油、柴油等分子较小的产物离开催化剂进入产品回收系统,而缩合反应生成的焦炭,则沉积在催化剂的表面上,使其活性降低,为了使反应不断进行,就必需烧去催化剂表面上的沉积炭使之恢复活性,这一过程称之为“再生”,可见催化裂化包括“反应”和“再生”两个过程。
二、反应器的改造1. 反应器改造目的针对提升管、汽提段、沉降器的改造,使催化裂化装置能适应各种原料,例如,蜡油、脱沥青、各种馏分油和渣油的范围;提高目的产物“汽油和柴油”产率而降低副产品“气体和焦炭”的产率。
2.反应器改造的过程2.1提升管底部结构更新,增设了两个粗汽油回炼喷嘴。
这样可使粗汽油进提升管回炼,因粗汽油中芳烃含量高,难以裂化,为使它和新鲜原料在不同反应操作条件下进行反应,达到多产液化石油气的目的。
2.2提升管设两层原料喷嘴,以适应不同原料加工量,并根据市场需要调整产品分布,增加了装置操作的灵活性。
2.3提升管出口粗旋风分离器改为挡板汽提式粗旋风分离器,将反应油气和催化剂快速分离,同时尽可能地汽提掉催化剂上携带的油气,减少了二次反应,增加了轻质油收率。
探讨安装连续重整装置反应器及再生器内件的具体方法

探讨安装连续重整装置反应器及再生器内件的具体方法连续重整装置在芳烃联合装置中具有重要作用,该装置的原料包括加氢裂化重石脑油、直馏石脑油,可生产出高辛烷值汽油,副产含氢气体、戊烷、液化气、拔头油等产品。
该装置包括三个单元,分别为催化剂连续再生、连续重整、预处理三个环节。
本文主要分析连续重整装置反应器及再生器内件的具体安装方法,确保该装置应用的合理性与科学性。
标签:连续重整装置;再生器;反应器连续重整装置有4个反应器,布置方式为两两重叠。
催化剂再生器在其中具有重要作用,它可实现连续再生,利用催化剂管线,能够了解再生器与反应器。
第四反应器用过的催化剂受到氮气作用影响后,会输送至再生部分,催化剂会进至再生器,在重力作用影响下而移动,通过烧焦、氯化更新、干燥等环节后,可获取再生效果。
利用氢气可将催化剂(再生后)提升至反应器上部,催化器在加热条件下能够再还原,在重力作用下,催化剂会下移至第四反应器,在第四反应器中,被排除的催化剂可存至再生系统,从而将催化剂循环移动过程完成[1]。
1 连续重整装置分析在使用连续重整装置时,该装置内件易发生异常情况,其中反应器操作异常是最严重的异常现象。
在连续重整装置中,大多为重叠式反应器,包括多个组成部分,例如盖板、扇形筒、催化剂输送管、中心管等。
在装置正常运行时,可利用输送管将催化剂送至反应器中心管,在重力作用影响下,催化剂会向下流动,当达到反应器底部后,催化剂会经引导口,被送至另一反应器。
油气主要经反应器入口进至器壁,并流至催化剂床层,然后达到中心管内,流出于反应器出口,可使整个循环过程完成[2]。
反应器问题的产生受到很多因素的影响,最主要的因素在于催化生焦时存在焦粉累积现象,如果焦粉累积太多,就会缩小扇形区面积,对油气正常流通造成很大影响,易导致油气发生阻塞,出现短路的情况,增加了油气气压差。
在扇形筒中,如果积碳持续增加,则会出现扇形筒膨胀现象,若存在严重膨胀,可能引发扇形筒破裂,损坏内件[3]。
MTO反再系统设备培训

初的研究是基于二甲醚制烯烃,后来技术改进从甲醇开始,而从甲醇
开始的过程也包含甲醇转化为二甲醚,二甲醚转化烯烃的过程,故引 用double的意思;由于大连化物所地处大连,大部分人认为这个D是大
连的意思。
一、装置概述
MTO装置共计设备253台套,其中静设备148台,动设备90台,成套 设备4套,起重设备6台,炉类设备5台。 1、主要静设备包括:反应器-再生器系统设备、塔类设备、冷换类 设备及容器类。
二、反再系统设备-反应器和再生器
(五)催化剂汽提器 反应器下部设置催化剂蒸汽汽提设施,对待生 催化剂进行汽提力求减少待生催化剂携带的反应气
体量。
再生催化剂携带至反应器内的烟气量会对后部 产品分离带来许多不利影响。设计中在再生器下部
设置再生催化剂蒸汽汽提设施,对再生催化剂进行
汽提,力求减少再生催化剂携带的再生烟气量。 本装置采用LPEC多段格栅汽提技术并进行特
参数
最高工作温度:550℃ 最高工作压力0.2MPa 最高工作温度:720℃ 最高工作压力0.2MPa 最高工作温度:550℃ 工作压力0.11MPa 最高工作温度:700℃ 工作压力0.105MPa
介质
甲醇、油气、催化剂 油气/催剂 反应气/催化剂 烟气/催化剂
二、反应器和再生器
(一)反应器、再生器皆是关键设备,体积 大,结构复杂,设计温度较高,局部气速高,磨 损较严重。 1) 反应器设备外壳采用245R,内衬隔热耐磨衬 里材料,进料部分内件采用1Cr5Mo和 15CrMoR, 稀相旋分系统内件采用S32168 (06Cr18Ni11Ti); •2) 再生器外壳采用245R,内衬隔热耐磨衬里 材料,内件采用S30409 (07Cr19Ni10)0Cr18Ni9;
5催化裂化9-6反应再生系统

第六节 反应—再生系统 P365一、反应器P3661、床层反应器(在催化裂化中已淘汰)各段结构和作用:密相段、稀相段、汽提段。
ÈË×°½¹ÕôÆûÌáÕôÆûÔÁϺʹ߻¯¼Á´µÉ¨ÕôÓÍÆø½¹°åͼ¼òͼ2、提升管反应器气管旋风分离器速分离器降器升管反应器提段形挡板水斜管图6-56 提升管反应器及沉降器简图⑴型式及结构直立式:用于高低并列式装置 折叠式:用于同轴式装置提升管制成两段或三段不同直径,设两个进料口;下部为预提升段(气速>1.5m/s)。
沿提升管装有人孔、热电偶管、测压管、采样口等。
下进料口事故蒸汽人孔附图 提升管预提升段⑵直径和长度直径由气体线速度计算,长度由反应所需时间确定。
入口线速:4~7m/s; 出口线速:12~18m/s。
停留时间:τ=L/u平;u平=(u出-u入)/ln(u出/u入)一般停留时间2~4秒。
中止反应技术:P367图9-30⑶提升管出口设快速分离装置,油气与催化剂快速分离(a)伞帽:分离效率约60~70%(b)倒L型弯头:分离效率约70~80%(c)T型弯头:分离效率~85%(d)粗旋风分离器:分离效率可达98%以上(常用)(e)弹射式快速分离器:分离效率大于90%(f)垂直齿缝式快速分离器(a)(b)(c)(d)(e)(f)同时要缩短油气在高温下的停留时间,以减少二次反应(热裂化反应)。
重整技术问答004

342. YCLEMAX 催化剂再生部分有哪两大作用?下图是UOP CYCLEMAX 催化剂再生部分的流程简图。
该“催化剂再生部分”具有两大作用:催化剂再生和催化剂循环。
(1) 催化剂再生催化剂再生包括四大步骤。
头三步一烧焦、氯化/氧化和干燥在再生器中进行,第四步还原在反应器顶部的还原区中进行。
第五步催化剂冷却不包括在催化剂再生步骤内,但对催化剂良好的输送是必要的,这发生在再生器下部。
(2) 催化剂循环催化剂循环包括:将催化剂从重整反应器输送到再生部分以及催化剂从再生部分返回反应器。
图 UOP 连续重整CycleMax 流程简图 特殊弯头 粉尘收集分离料斗还原区反应器再生器氮封罐闭锁料斗氮气隔离阀 催化剂收集增压H 2提升L —阀组N 2提升气 催化剂添加料斗343. CYCLEMAX 再生器燃烧区/再加热区的工艺流程如何?有什么作用?再生部分燃烧区/再加热区的工艺流程如图所示。
催化剂上焦炭的燃烧,在再生器顶部的燃烧区中进行。
催化剂进入再生器后向下流动,进入一个垂直园柱形外部筛网和一个向内收缩的内部筛网之间。
带有低氧含量的高温再生气体在催化剂床层由外向内发散。
随着催化剂向下移动,烧焦不断进行。
当催化剂离开“燃烧区”时烧焦应完成。
高温燃烧气体同来自氯化段向上流动的气体相混合,该富氧的氯化气体为烧焦提供了氧气。
混合后气体流回到再生风机。
该风机使这些气体通过燃烧区管线回路再循环。
再生冷却器除去烧焦产生的热量。
如果管线中的热损大于燃烧热量,那么再生电加热器就用来加热气体达到合适的入口温度。
氧分析仪控制燃烧区入口的氧含量。
燃烧物在再生器入口排放,以便提供恒定的受控温度,气体排放到下游的氯化物洗涤设备。
待生催化剂风机直接密封气体冷却器排放 电加热器空气从氯化区来催化剂去氯化区再加热气 注:CycleMax 小装置在再加热气管上还有一个电加热器。
图 CYCLEMAX 再生器燃烧区/再加热区的工艺流程催化剂离开燃烧区,然后进入再加热区。
- 1、下载文档前请自行甄别文档内容的完整性,平台不提供额外的编辑、内容补充、找答案等附加服务。
- 2、"仅部分预览"的文档,不可在线预览部分如存在完整性等问题,可反馈申请退款(可完整预览的文档不适用该条件!)。
- 3、如文档侵犯您的权益,请联系客服反馈,我们会尽快为您处理(人工客服工作时间:9:00-18:30)。
3.2.4.4检查反映其内认字挡板、环形挡板、快分头即隔栅的固定、变形、磨损等情况。
3.2.4.5检查各油喷嘴、吹气管及喷水管的冲刷磨损,变形、堵塞和损坏情况。
3.2.4.6检查各开孔、接点等部位的磨损、堵塞、变形等情况。
3.2.4.7检查辅助燃烧炉的油气联合喷嘴,一次风分配器及炉上部合金钢陈套烧损情况。
2.2.5提升管及器内外等部件有无变形,冲蚀磨损、开裂。
2.2.6检查三级旋风分离器。
2.2.7检查内外取热系统。
2.2.8检查高温取热炉。
2.2.9检查膨胀节和烟道系统。
2.2.10检查辅助燃烧室系统。
3 检修与质量标准
3.1 检修前准备
3.1.1备齐所需的图纸、技术资料,并编制施工方案。
3.1.2备齐机具、量具、材料和劳动保护用品。
3.3.2.6料腿拉杆均应在靠近中心部位正下方开一个ø10㎜通气孔,各拉杆水平度偏差不的大于2㎜/m,料腿与拉筋不得强力组焊。
3.3.3翼阀
3.3.3.1翼阀应灵活,角度及肩闭符合要求,接触面应严密。翼阀的安装角必须经冷态试验后决定,其允许偏差为±0.5°。翼阀安装角的试验见附录A(参考件)。
3.3.3.2翼阀出口方向应按图纸要求进行施工安装。
3.3.8.2同一层上的人字挡板应在同一水平面上,其允许偏差为±5㎜。
3.3.8.3人字挡板的安装角度允许偏差为±2.5°,见图1。
图
图1 人字挡板安装示意图
α——设计安装角度
3.3.8.4环形挡板安装间距允许偏差为±5㎜,累计允许偏差为±10㎜。
3.3.8.5环形挡板内口与提升管外表面间隙、以及内环形挡板外寇语气提段内壁间隙的偏差应控制在10~20㎜。
3.3.6分布板、分布管
3.3.6.1再生器环形分布管安装水平堵在分布管上测量的水平偏差应不大于最外圈盘管中心直径的1‰,且不大于10㎜。
3.3.6.2环状分布管的支管与盘管安装前应进行预组装。
3.3.6.3环状分布管各盘管应同心,相邻两圈盘管中心距偏差为±10㎜。
3.3.6.4喷嘴与分布管焊接时应符合设计要求。
3.3.5.5进料弯管上的滑盘膨胀节,补偿板焊后应无翘曲,焊缝应磨平。
3.3.5.6滑盘膨胀节的滑动配合应保证严密,滑动灵活,在1/8周长上最大间隙不大于0.3㎜,其余应完全接触。
3.3.5.7膨胀节的安装方向应按介质流向或设计要求进行。
3.3.5.8安装波纹管膨胀节时,应设临时约束装置,且在系统交付使用前拆除。严禁利用波纹管膨胀节的变形来补偿安装偏差。
3.3.5.2跟换波形膨胀节时,应根据图纸要求进行预拉伸或压缩。
3.3.5.3波形膨胀节更换后,两端轴心同轴度允许偏差应符合表2规定值。
表2 波纹管膨胀节同心允许偏差 ㎜
波纹管直径 轴心允许偏移
≤400 ≤3
>400~1000 ≤6
>1000 ≤10
3.3.5.4膨胀节组装焊接时,应对膨胀节加以保护,防止电弧烧穿或焊接飞溅物落到膨胀节上。
3.3.1.6吊杆方位允许排偏差±5㎜,标高允许偏差±5㎜,垂直度不得大于1㎜;吊挂焊缝应饱满、平滑、无咬边,焊缝表面应进行100%渗透探伤检查,无裂纹。
3.3.2料腿
3.3.2.1料腿更换原则
a.料腿严重变形;Байду номын сангаас
b.料腿严重脱碳;
c.料腿壁厚减薄,不能安全使用到下一个检修周期。
3.3.2.2料腿检修更换应予组装并做好标记,不得强行组装。
1.2 编写修订依据
SHS 3504—2000 催化裂化装置反应再生系统设备施工及验收规范
SHS 3531—1999 隔热耐磨混凝土衬里技术规范
SHS 01004—2003 压力容器维护检修规程
GB 150—1998 刚制压力容器
国家质量技术监督检验检疫总局《特种设备安全检查条例》
国家质量技术监督检验检疫总局《压力容器安全技术监察规程》
3.3.6.5树枝状分布管的标高允许偏差为±5㎜。
3.3.6.6树枝状分布管更换后,单根支管水平渡河同一设备各族分布管水平度的允许偏差均应符合表3的要求。
表3 分布管水平度允许偏差 ㎜
设备直径 水平度允许偏差
≤ 1600 ≤3
> 1600~3200 ≤4
> 3200 ≤5
3.3.7取热器
3.3.7.1所有管子拼接长度不宜小于2500㎜,最短管段长度不小于500㎜。
3.1.3与两器连接管线应加盲板,内部必须清扫干净,施工现场必须符合有关安全规定。
3.2 检查内容
以外观检查为主,对“两栖”系统设备和部件的冲蚀、裂纹、古堡、乔奇、磨损、壁后减薄、脱落、堵塞、结焦等进行检查,必要时进行探伤、测厚或用0.5㎏小锤敲击检查;检查两器衬里的磨损、开裂、松动、鼓包和脱落等情况。
3.2.1检查两器壳体和受压元件变形、开裂、冲蚀磨损和过热等。
3.2.2两器内部构件的检查
3.2.2.1 检查旋风分离器的简体、锥体、灰斗、升气管、支耳的磨损和变形情况,旋风分离器出入口及其连接部位等处的变形、裂纹和磨损情况。
3.2.2.2 检查一级旋风分离器的地吊杆螺栓是否松动,吊挂焊缝有无裂纹,检修平台是否牢靠,测量吊杆螺母与支撑面的间隙。
3.2.2.3 检查粗旋出入口及出口盖板与支腿连接部位冲蚀磨损、变形。
3.2.2.4 检查料腿和料腿拉筋及灰斗下的耐磨短管的冲涮磨损、变形。
3.2.2.5 检查翼阀的灵活性、角度、磨损及接触面严密情况。
3.2.2.6 检查集气室环焊缝、生气管与集气室连接焊缝开裂和磨损情况。
3.2.2.7 检查防焦政气管的松动变形、冲蚀磨损、检查蒸汽孔是否堵塞、冲刷、磨损等。
3.3.4.5烟气入口中心管与箭体以及掉筒与筒体的同轴度允许偏差为三旋简体内径的1/1000。
3.3.4.6分离单管卸料盘应在设备其他内件安装完毕并彻底清扫内部后进行。
3.3.4.7三级旋风分离器内部膨胀节检修标准同本规程3.3.5节内容。
3.3.5膨胀结
3.3.5.1铰链式膨胀节铰链应于管道轴线平行,方位正确,链轴应在膨胀节全长正中位置,其回转平面应与出口管壁的主管及水平管的轴线所在平面一致。
3.3.4.3立管式三级旋风分离器上下隔板安装时方位允许偏差为5㎜(沿周向测量),上下隔板间对应管孔应同心,同轴度允许偏差为ø2㎜。
3.3.4.4卧管式三级旋风分离器分离单管的定位点应在同一水平面上,水平度允许误差为5㎜,相邻分离单管夹角允许偏差为±0.25°,分离单管与水平面的倾角允许偏差为±0.25°。
3.2.10.2检查旋风分离器衬里的磨损、开裂、松动、鼓包和脱落情况。
3.2.10.3检查所有烟道系统衬里的磨损、开裂、松动、鼓包和脱落情况。
3.2.10.4检查降压孔板室的变形、堵塞、冲蚀、开裂情况。
3.2.11检查结焦情况
3.2.11.1检查油气管线的结焦情况。
3.2.11.2检查沉降器集气室的结焦情况。
3.3.8.6人字挡板和环形挡板不得开裂和严重变形。
3.3.9窜气阻挡圈
3.3.9.1 窜气阻挡圈宽度允许偏差不大于2㎜,间距允许偏差不大于10㎜。
3.3.9.2 窜气阻挡圈高度应比隔热层低5㎜,允许偏差不大于2㎜。
3.3.9.3 反应器(一般沿轴向间隔为1000~1500㎜)及提升管、斜管、烟道(一般沿轴向为1800~2000㎜)衬里中均应设置窜气阻挡圈。
同轴度偏差 ≤
3
3
5
5
5
5
4
3.3.1.2与旋风分离器相连接各部位必须圆滑过渡。
3.3.1.3所有焊缝内表面应保持焊肉均匀、与母材平齐,其凸出部分应磨平。
3.3.1.4所有角焊缝采用连续焊,其焊角高度等于组焊件中较薄件的厚度。
3.3.1.5一级旋风分离器检修后,吊杆中心到旋风分离器本体主轴线距离的偏差不大于±3㎜,将吊杆螺母按图样规定松回,留出膨胀间隙。
3.3.2.3料腿下端与分布管(板)或其他零件的垂直距离允许偏差为±20㎜,料腿与旋风分离器接口及腿间接应开坡口,保证全焊透。
3.3.2.4材质为Cr5Mo的料腿焊接前,应对坡口进行着色检查,不得有裂纹,破口两侧10~20㎜内,其表面不得有油污、赃物和锈斑。
3.3.2.5料腿对口内错边量不超过管壁厚度的10%,且不大于1㎜,必须汗透。
5 维护…………………………………………………………(21)
附录A 翼阀冷态试验方法(参考件)…………………………
(22)
1 总则
1.1 主题内容与适用范围
1.1.1本规程规定了炼油厂催化裂化装置反应器(沉降器)、再生器(以下简称“两器”)的检修周期与内容、检修与质量标准、试验与验收、维护。
1.1.2本规程适用于炼油厂催化裂化装置“的两器”及所属附件的检修和维护。
3.2.2.8 检查提升管、再生斜管、待升斜管、密相提升管、烟道等的变形、磨损。
3.2.2.9 检查霜冻滑阀下游烟道锥体的护板、防冲板、拉筋及支撑的冲刷磨损、焊缝开裂情况。
3.2.3三级旋风分离器
3.2.3.1 检查单管及导向叶片冲刷、磨损、堵塞等情况。
3.2.3.2 检查连接螺栓有无松动。
3.2.3.3 检查壳体磨损、过热、裂纹等情况。
3.3.9.4 窜气阻挡圈与器壁的焊接,迎着气流方向为连续焊,另一方为断续焊。焊后应进行煤油试漏。中间不允许间断,但遇开孔接管时,把阻挡圈断开再与接管焊成整体。
1. 催化裂化反应器再生器
维护检修规程
SHS 02001—2004
目 次
1 总则……………………………………………………………(3)
2 检修周期与内容………………………………………………(3)
3 检修与质量标准………………………………………………(4)