OMEGA用户手册 (15)
Omega 产品用户指南说明书
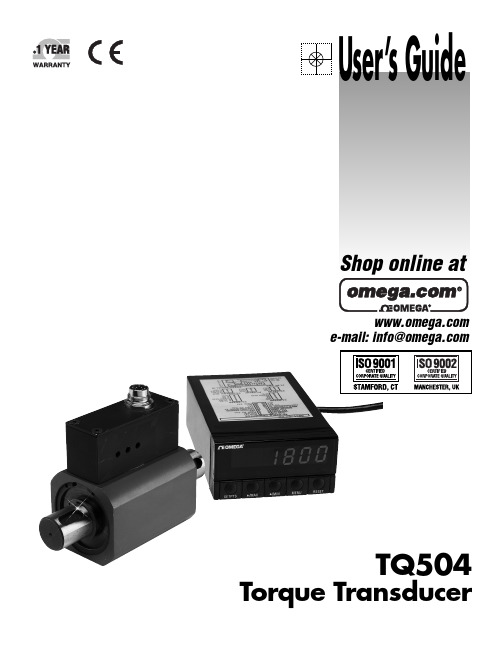
e-mail:**************User’s GuideTQ504Torque TransducerShop online atINDEX1.Applications and typical attributes ...............................................Page 12.Description of the measurement system ......................................Page 12.1Mechanical design .................................................................Page 12.2Electrical design .....................................................................Page 22.3Angle-of-rotation transducer ...............................................Page 33.Electrical connection of the torque transducer ............................Page 43.1Connector pin assignments ..................................................Page 53.1.1Signals, angle outputs ...........................................................Page 63.2Laying of the output signal cables ......................................Page 63.3Placement of conductors in cable ........................................Page 64.Mechanical installation of the torque transducer........................Page 84.1Suggestions for installation ..................................................Page 85.Mechanical calibration .....................................................................Page 95.1Assembly of a simple calibrating setup............................Page 105.2Sample calculation of lever arm length.............................Page 105.3Electrical calibration.............................................................Page 116.Maintenance......................................................................................Page 117.Troubleshooting guide for transducer shaft...............................Page 12See Data Sheet for technical specificationsi1.Applications and typical attributes• Torque transducer with inductive angular position measurement system.• Measurement of constant and variable torques.• Torque measurement on a rotating shaft.• For laboratory, production and quality assurance applications.• Built- in instrument amplifier.• Built- in angle-of-rotation transducer.2.Description of the measurement system2.1Mechanical design• The transducer consists of a stator through which a bearing-mounted shaft passes.• A certain length of the shaft is utilized to convert the torque into a proportional torsional angle.• This torsional angle or angle of twist is measured between the two ends of this shaft length by an inductive (wave-form) angular position measurement system.• The inductive angular position measurement system converts the angle of twist into a proportional electrical signal.1• The electrical power for operation of the inductive angular positionmeasurement system, which rotates along with the shaft, is provided by meansof a rotary transformer.• The electrical output signal, which is proportional to the torque, is transferredto the stator by a second rotary transformer.• The connection box on the stator contains the electronics, the power supplyunit, and the instrument amplifier.2.2Electrical designThe built-in electronics comprise the following functional groups:• Oscillator for generation of the AC input voltage• Preamplifier for the output signal• Phase-sensitive rectifier for conversion of the AC output signal into a DCvoltage• Output amplifier22.3Angle-of-rotation transducer1.Rotating shaft2.Encoder disk3.Double-arm photoelectric barrier4.Open-collector output (external pull-up resistor required)*Features:• 360 slots in the encoder disk• Two double-arm photoelectric barriers 90°apart.• Number of pulses generated proportional to angle of rotation.* The ohmic value of the resistor depends on the maximum speed of rotation andthe cable length (e.g. 1500 rpm and a 4 m cable, R=3.3kΩ).33. Electrical connection of the torque transducer• Cable type: at least 12 conductors, e.g. LIYCY12 x 0.14• Max. cable length: 15 m43.1 Connector pin assignmentsDescription of interface for Type, art.-no.: 7203Angle outputs: open collector outputs with internal 10k Ωpull-up to +Vop Built in connector: Binder Series 680, type 09-0331-80-12 or equivalent Cable diagram with plugs on both sides5Top view of connector on transducer3.1.1Signals, angle outputs3.2Laying of the output signal cables-Note on safety-• Do not lay together with control lines or lines carrying a high current.• Do not lay close to strong electromagnetic fields, e.g. those of transformers,welding equipment, contactors, motors, etc.• If the above is unavoidable, the cables must be laid in grounded heavygage steel conduit.• At the transducer, lay the cables in a sling in order to prevent vibration-induced damage to them.3.3Placement of conducters in cableIn order to prevent the measurement signal being distorted by the angle pulses,the corresponding conductors should be separated within the cable.6The cable length has virtually no influence on the measurement signal, but in the case of the angle outputs the external pull-up resistances must be properly adjusted.74.Mechanical installation of the torque transducerTransducer with fixed stator:2 holes are provided in the transducer housing for this purpose.• Use displaceable couplings as both shaft ends that are capable of accommodating angular, radial and axial misalignment.• Good results have been obtained with miniature couplings stiff against torsion such as those described in data sheet 8303.At torques of 50 Nm or greater, it is also possible to install the transducer without fixed stator:• In this case, use flexible couplings at both ends.Caution:during installation no impermissibly high torques may beallowed to arise between the two ends of the torque transducer shaft.4.1Suggestions for installationTransducer with fixed stator and couplings able to accommodate angular, radial and axial misalignment at both ends.8This type of installation is possible at torques of 50 Nm and greater.5.Mechanical calibrationTo perform this, a calibration setup with lever arm and weights is needed tocreate a torque.Steps for calibration:a)Apply the rated torque to the transducer, then remove the load again.b)Precisely adjust the transducer to the zero point.c) Apply a known torque to the transducer.d) Set the indicator to the proper value.Recording of a calibration curve:a) Calibrate the transducer as described above.b) Progressively apply greater torques to the transducer in steps of 1/10 up tothe full rated torque. Then gradually remove the torque in the same way. Ateach step, wait at least 30 seconds for the torque reading to stabilize, and thenrecord.95.1A simple calibrating setup5.2Sample calculation of lever arm length10eg. m = 1 kg. Mt = 10 NmL =10Nm sec 21 kg _ 9.80665= 1,0197 m5.3Electrical calibrationA calibration control facility is integrated in the transducer to permit electrical calibration.Procedure for electrical calibration:• Remove all mechanical loads from the transducer (no torque).• Apply the calibration voltage Vc to pin K referenced to pin E.• An output signal corresponding to the rated torque will be emitted.6.Maintenance• Type IE transducers require virtually no maintenance.• The service life expectancy of the bearings within the rated temperature range is approx. 20,000 hours.• The service life expectancy of the bearing within the operating temperature range is approx. 10,000 hours.• The bearings can only be replaced in the factory.• For high-precision applications: recalibrate the transducer once annually (calibration at the factory or using an appropriate calibration setup).• Once a month, check the cable connectors to make sure that they are securely seated.• Check the cables for damage once a month.117.Troubleshooting guide for transducer shaft12ProblemProbable causesRemedial actionShaft does not rotate Bearings are defective due to:freelya) Torsional or flexional vibrations b) Excessive axial or radial loads Return to factoryc) Old or soiled bearings d) Bent shaft Zero point displacement Rotational vibration Readjust zero point on ≤2 %Shock forcesinstrument amplifier Zero offset between 2%Transducer has been overloaded The zero point can be and 5% of range Shock forcesrecalibrated once at Rotational vibrationthe instrument amplifier Transducer has Transducer has been overloaded hysteresis between by changing loads or rotational Return to factoryclockwise and counter-Rotation vibrationclockwise torqueNOTES: 13WARRANTY/DISCLAIMEROMEGA ENGINEERING, INC. warrants this unit to be free of defects in materials and workmanship for a period of 13 months from date of purchase. OMEGA’s WARRANTY adds an additional one (1) month grace period to the normal one (1) year product warranty to cover handling and shipping time. This ensures that OMEGA’s customers receive maximum coverage on each product.If the unit malfunctions, it must be returned to the factory for evaluation. OMEGA’s Customer Service Department will issue an Authorized Return (AR) number immediately upon phone or written request. Upon examination by OMEGA, if the unit is found to be defective, it will be repaired or replaced at no charge. OMEGA’s WARRANTY does not apply to defects resulting from any action of the purchaser, including but not limited to mishandling, improper interfacing, operation outside of design limits, improper repair, or unauthorized modification. This WARRANTY is VOID if the unit shows evidence of having been tampered with or shows evidence of having been damaged as a result of excessive corrosion; or current, heat, moisture or vibration; improper specification; misapplication; misuse or other operating conditions outside of OMEGA’s control. Components which wear are not warranted, including but not limited to contact points, fuses, and triacs.OMEGA is pleased to offer suggestions on the use of its various products. However, OMEGA neither assumes responsibility for any omissions or errors nor assumes liability for any damages that result from the use of its products in accordance with information provided by OMEGA, either verbal or written. OMEGA warrants only that the parts manufactured by it will be as specified and free of defects. OMEGA MAKES NO OTHER W ARRANTIES OR REPRESENTATIONS OF ANY KIND WHATSOEVER, EXPRESS OR IMPLIED, EXCEPT THAT OF TITLE, AND ALL IMPLIED WARRANTIES INCLUDING ANY WARRANTY OF MERCHANTABILITY AND FITNESS FOR A PARTICULAR PURPOSE ARE HEREBY DISCLAIMED. LIMITATION OF LIABILITY: The remedies of purchaser set forth herein are exclusive, and the total liability of OMEGA with respect to this order, whether based on contract, warranty, negligence, indemnification, strict liability or otherwise, shall not exceed the purchase price of the component upon which liability is based. In no event shall OMEGA be liable for consequential, incidental or special damages.CONDITIONS: Equipment sold by OMEGA is not intended to be used, nor shall it be used: (1) as a “Basic Component” under 10 CFR 21 (NRC), used in or with any nuclear installation or activity; or (2) in medical applications or used on humans. Should any Product(s) be used in or with any nuclear installation or activity, medical application, used on humans, or misused in any way, OMEGA assumes no responsibility as set forth in our basic WARRANTY/DISCLAIMER language, and, additionally, purchaser will indemnify OMEGA and hold OMEGA harmless from any liability or damage whatsoever arising out of the use of the Product(s) in such a manner.RETURN REQUESTS/INQUIRIESDirect all warranty and repair requests/inquiries to the OMEGA Customer Service Department. BEFORE RETU RNING ANY PRODU CT(S) TO OMEGA, PU RCHASER MU ST OBTAIN AN AU THORIZED RETU RN (AR) NU MBER FROM OMEGA’S CU STOMER SERVICE DEPARTMENT (IN ORDER TO AVOID PROCESSING DELAYS). The assigned AR number should then be marked on the outside of the return package and on any correspondence.The purchaser is responsible for shipping charges, freight, insurance and proper packaging to prevent breakage in transit.FOR WARRANTY RETURNS, please have the following information available BEFORE contacting OMEGA:1.Purchase Order number under which the productwas PURCHASED,2.Model and serial number of the product underwarranty, and3.Repair instructions and/or specific problemsrelative to the product.FOR NON-WARRANTY REPAIRS,consult OMEGA for current repair charges. Have the following information available BEFORE contacting OMEGA: 1. Purchase Order number to cover the COSTof the repair,2.Model and serial number of the product, and3.Repair instructions and/or specific problemsrelative to the product.OMEGA’s policy is to make running changes, not model changes, whenever an improvement is possible. This affords our customers the latest in technology and engineering.OMEGA is a registered trademark of OMEGA ENGINEERING, INC.© Copyright 2002 OMEGA ENGINEERING, INC. All rights reserved. This document may not be copied, photocopied, reproduced, translated, or reduced to any electronic medium or machine-readable form, in whole or in part, without the prior written consent of OMEGA ENGINEERING, INC.Where Do I Find Everything I Need for Process Measurement and Control?OMEGA…Of Course!Shop online at TEMPERATUREⅪߜThermocouple, RTD & Thermistor Probes, Connectors, Panels & AssembliesⅪߜWire: Thermocouple, RTD & ThermistorⅪߜCalibrators & Ice Point ReferencesⅪߜRecorders, Controllers & Process MonitorsⅪߜInfrared PyrometersPRESSURE, STRAIN AND FORCEⅪߜTransducers & Strain GagesⅪߜLoad Cells & Pressure GagesⅪߜDisplacement TransducersⅪߜInstrumentation & AccessoriesFLOW/LEVELⅪߜRotameters, Gas Mass Flowmeters & Flow ComputersⅪߜAir Velocity IndicatorsⅪߜTurbine/Paddlewheel SystemsⅪߜTotalizers & Batch ControllerspH/CONDUCTIVITYⅪߜpH Electrodes, Testers & AccessoriesⅪߜBenchtop/Laboratory MetersⅪߜControllers, Calibrators, Simulators & PumpsⅪߜIndustrial pH & Conductivity EquipmentDATA ACQUISITIONⅪߜData Acquisition & Engineering SoftwareⅪߜCommunications-Based Acquisition SystemsⅪߜPlug-in Cards for Apple, IBM & CompatiblesⅪߜDatalogging SystemsⅪߜRecorders, Printers & PlottersHEATERSⅪߜHeating CableⅪߜCartridge & Strip HeatersⅪߜImmersion & Band HeatersⅪߜFlexible HeatersⅪߜLaboratory HeatersENVIRONMENTALMONITORING AND CONTROLⅪߜMetering & Control InstrumentationⅪߜRefractometersⅪߜPumps & TubingⅪߜAir, Soil & Water MonitorsⅪߜIndustrial Water & Wastewater TreatmentⅪߜpH, Conductivity & Dissolved Oxygen InstrumentsM2958/0602。
OMEGA 产品说明书.pdf_1718692831.469412

It is the policy of OMEGA worldwide safety and EMC/EMI regulations that apply. OMEGA is constantly pursuing certification of its products to OMEGA will add the CE mark to These products are not designed for use in, and should not be used The information contained in this document is believed to be correct but OMEGA Engineering, Inc. accepts no liability for any errors it contains, and reserves the right This device is marked with the international caution symbol. It is important to read the Setup Guide before installing or commissioning this device as it contains important information relating to safety and EMC.until the controller displays.For complete product manual:/manuals/manualpdf/M1MENU until thePress ᮣT/mV to display r.2 =f or r.2 =c(temperature unit of F or C).Press ᮡ/pH to select the desired temperature unit.Press MENU to select the calibration. The unit displays.Proceed with Calibration depending on Temperature Compensation Setting:If you choose OFF, go to “To Perform Calibration” section.Connect the pH Electrode1.Secure the pH electrode to the pH input BNC connector on the back of the controller.2.If you are using automatic temperature compensation (ATC), connect the RTD as shown below.apply Power1.Apply ac power to the unit.The unit initializes, flashing the following messages: rst , ph , init . Then a pH value appears.2.Verify that a value appears. If not:•Remove ac power.•Verify the TB1 power connections.•Check your power source.•Apply ac power again.234Using This Quick Start Manua lUse this Quick Start manual to set up your pHController and begin operation. Information is provided on how to:•Mount the controller •Connect ac Power•Connect a pH electrode•Calibrate the controller prior to useFor complete information on this controller, refer to the Operator’s Manual.Before You BeginIn addition to the meter and the related parts, you will need the following items to set up your meter:•ac power, as listed on meter’s ID/Power Label •pH electrode (with BNC input connector)•1⁄8” flat blade screwdriverMount the Unit1.Cut a panel opening using the dimen s ions shown to the right.2.Position the unit in the open i ng, making sure the front bezel gasket is flush to the panel.3.Slide on mounting bracket to secure.Connect ~ac PowerWarning: Do not connect AC power to your device until you have completed all input and output connections. This device must only be installed by a specially trained electrician with corresponding qualifications. Failure to follow all instructions and warnings may result in injury!1.Remove the panel at the back of the unit.2.Locate the TB1 connector.3.Insert the correct wire in each terminal as shown in the following figure and tighten the lockdown screws.4.Tug gently on the wires to verify the connections.MANU = the controller uses a manually entered value for temperature compensation.METR = the controller uses the RTD input for automatic temperature compensation.to select the temperaturecompensation setting shown. The controller To Set The Decimal Point Position:If it’s not already shown, press MENU until the controller displays Press ᮣT/mV . The controller displays:to move the decimal point to the desired location. The choices are ff.ff , fff.f , orffff .。
Omega产品支持信息书说明书
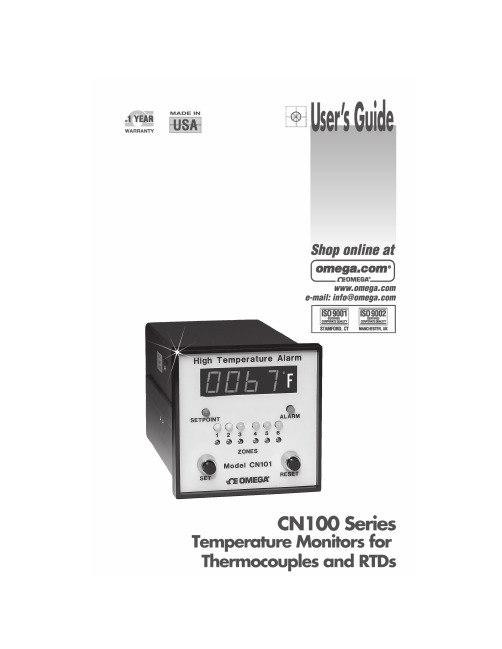
TABLE OF CONTENTSCNIOO SERIES TEMPERATURE MONITORSSECTION PAGESECTION 1 INTRODUCTION1 1.1General Description1 1.2Available Models1SECTION 2 INSTALLATION3 2.1Unpacking3 2.2Controller Location3 2.3Mounting3 2.4Wiring Power Circuit4 2.5Sensor Placement4 2.8Setup Procedure5SECTION 3 OPERATION63.1Operation6 3.1.1Controls and Indicators6 3.1.2Relay Output7 3.2Adjusting Setpoints7 3.3Adjusting Scan Time7 SECTION 4 SERVICE INFORMATION74.1Maintenance7 4.2Test Procedure7 4.2.1Visual Inspection7 4.2.2Functional Observation7 4.2.3Calibration Temperature9 4.2.4Calibration Alarm10 4.2.5Zone Crosstalk10 4.3Troubleshooting11SECTION 5 SPECIFICATIONS125.1Thermocouple12 5.2RTD13 5.3Parts List14 5.4Calibration Charts17 5.4.1Calibration Table 0-20000F-Type K18 5.4.2Calibration Table 0-5000F-Type K19 5.4.3Calibration Table 0-2500C-RTD20 5.5Component Layouts21 5.8Schematic231SECTION 1 INTRODUCTION1.1GENERAL DESCRIPTIONThe OMEGA® CN100 Series temperature monitor is a tempera-ture indicator with either high or low alarms. The six input channels accept independent thermocouple inputs, and there is an individual setpoint for each channel. In operation, the CN100will scan each channel for 4 to 12 seconds (via side adjustment),and the display will indicate the temperature measured by the individual thermocouples. A red LED indicates an alarm condi-tion; in the event of an alarm, scanning is halted and the relay de-energizes, until the manual reset button is depressed. The CN101 models are high temperature alarms, while the CN102units will alarm on low temperatures.The CN102 models also feature a built-in cold start alarm suppression. When the “START UP” LED is lit, the alarm action is suspended until the temperatures of each input reach their respective setpoints. Power failures for less than 30 minutes do not affect the start-up operation.1.2AVAILABLE MODELSCN101(*)-(**) HIGH ALARMCN102(*)-(**) LOW ALARMRTD#2SECTION 2 INSTALLATION2.1UNPACKINGRemove the packing list and verify that all equipment has beenreceived. If there are any questions about the shipment, pleasecall OMEGA Customer Service Department.Upon receipt of shipment, Inspect the container and equip-ment for any signs of damage. Take particular note of anyevidence of rough handling in transit. Immediately report anydamage to the shipping agent.NOTEThe carrier will not honor any claims unless allshipping materiel is saved for their examination.After examining and removing contents, savepacking material and carton in the event reship-ment is necessary.2.2CONTROLLER LOCATIONSelect a location for the controller that is free from excessiveshock, vibration, dirt, moisture, and oil. The ambient tem-perature should be between 30° and 130°F(-1° and 54°C).2.3MOUNTINGMount the controller into a 3 5/8” (92mm) square cutout. Referto Figure 2-1 for the cutout and case dimensions. The plug-in controller does not have to be removed from its housing formounting.Remove the two screws that hold the mounting slides; thenremove the slides. Insert the case into the cutout from thefront side of the panel and reinstall the two slides and twoscrews. The length of the slides must be reduced if the con-troller is to be mounted in an extra thick panel. If the control-ler has been unplugged from its housing, the top of the hous-ing can be determined by the serial tag.3.4Figure 2-1. Outline Dimensions2.4WIRING POWER CIRCUITThe controller operates on either 120 or 240 VAC, 50 to 60Hz line voltage when connected to the proper terminals.Incoming power lines should be properly fused. Refer to Figure 2-2.NOTE Fuse incoming high side of line with fast blow fuse of appropriate rating. Shorted heater or wiring will destroy the relay or output Triac.2.5SENSOR PLACEMENTProper sensor placement is essential. It can eliminate many problems in the total system. The probe should be placed so that it can detect any temperature change with little thermal lag. In a process that requires fairly constant heat output, the probe should be placed close to the heater.In processes where the heat demand is variable, the probe should be close to the work area. Experimenting with probe location can often provide optimum results.In an ice bath process, the addition of a stirrer will help to eliminate lags. Some RTD’s are shock sensitive andrequire care in handling and installation.2.2SET UP PROCEDUREWire the instrument as shown in Figure 2-2. Observe polarity(on the thermocouples red is always negative, on RTDs blackis negative) and short all the unused zone inputs (do not shortthe analog output). Turn all the setpoints fully CW on CN101models and CCW on the CN102 models. Power up theinstrument. If any zone alarms, check for open thermo-couples or setpoints turned the opposite way. Correct theproblem and push the RESET button. Observe the scanningrate and readjust if needed at the side of the instrument. Pushthe SET button and release. The green light should appear forabout 10 seconds and the display indicates the setpoint Adjustthe setpoint of the indicated zone to the desired alarm tem-perature. If more time Is needed, push the SET button to getan additional 10 seconds. Wait for the green light to disappearand repeat the procedure for all used zones. For unusedzones, leave the setpoints fully CW for CN101 models andfully CCW for CN102 models.Figure 2-2. Wiring Diagram56SECTION 3 OPERATION3.1OPERATIONThe typical control system contains the sensor, controller and the process. The thermocouple sensor produces a small voltage change proportional to the measured temperature of the process. An RTD produces a change in resistance proportional to the measured temperature of the process.This is linearized in a unique active circuit, and amplified by the controller, where it is compared with setpoint temperature. If the temperature of the sensor is above setpoint, the output circuitry will be actuated. This is indicated by means of an LED light. The digital meter displays the sensor’s process tem-perature, and when switched, displays the alarm setpoints.Six zones share common amplifier and display.3.1.1Controls and Indicators (Refer to Figure 3-1)1.LED Display (temperature or setpoint)2.Setpoint (displayed by green LED)3.Start Up button—cold start (CN102 only)4.Alarm Light (red LED)5.Zone Light (yellow LED)6.Setpoint Control7.Setpoint Enable8.Manual Alarm Reset9.Scan Time Adjust 10.Calibration LO and HI potentiometers3.1.2RELAY OUTPUTThe output relay has SPDT contacts rated 5 amps at 120Vand 3 amps at 240 VAC. These contacts can be wired toprovide power to the alarm. This is a latching relay.3.2ADJUSTING SETPOINTSSix setpoint adjustments are located on the faceplate. Theseare 15-turn potentiometers with slotted shafts. A small screw-driver is required.3.3ADJUSTING SCAN TIMEThis adjustment is located on the side of the instrument. It is a15-tum potentiometer with slotted shaft CW rotation in-creases the scan time.SECTION 4 SERVICE INFORMATION4.1MAINTENANCESome simple preventative maintenance will keep thecontroller operating properly:1. Keep the controller clean and protected from dirt, oil andcorrosion.2.Periodically recheck all electrical connections.4.2TEST PROCEDURE4.2.1Visual Inspection1.Inspect the instrument for mechanical damage.2.Make sure that all screws are tight.3.Make sure all switches and lights are properly installed.4. Make sure all labels are properly and correctly attached. 4.2.2Functional Observation1.Short the thermocouple or RTD inputs to each zone.2.Attach cord and plug to 120 VAC line terminals.3.Attach ohmmeter to C and NO relay terminals.4.Insert the power cord to 120 VAC line outlet.5.Observe that ohmmeter reads near zero ohms.6.Observe that digital display is “on” and all the digits areworking properly.77.Observe that only one scan light is on.8.Observe that digital display reading is more than zero andless than 1000F (or 0C).9.Adjust LO calibration potentiometer on the side of theinstrument until the display reads 75 ±50F (25 ±50C). Refer to Figure 4.1.10.Turn all setpoint controls 10 turns clockwise.11.If the alarm light (red) is on, push the RESET button andremove the alarm.12.Observe that zone light scans sequentially from zone tozone without skipping any zones.13.Turn the scan time control fully CW (about 20 turns) andobserve that the scan rate is more than 12 seconds.14.Turn the scan time control fully CCW and observe that thescan rate is between 2-5 seconds.15.Set the scan time at 5 seconds ±1 second.16.When the scan light comes to zone 1, push the set switchand observe that the green setpoint light comes on. Ob-serve that the light stays on for 7-15 seconds and the zone scan light stays on zone 1 as long as green light is on. 17.Push the SET button and turn the setpoint control fullyCCW; observe that indication goes to 0000 -0 +2.18.Observe that the alarm light comes on and ohmmeterresistance measures HI (open).19.Push the SET button and turn the setpoint control fully CW.Observe that the display rises gradually from 0 to full range of the instrument.20.Push the RESET button and observe that the RESET lightis off and the instrument resumes scanning.21.Repeat steps 17 through 20 for other channels.22.Switch the power on and off several times and observe thatthe unit does not go to alarm condition.23.Disconnect the thermocouple short from zone 1 andobserve that when the scan light comes to zone 1, theinstrument indicates alarm, the meter reeds full scale, and the scanning has stopped.84.2.3 Calibration Temperature1. After the instrument has been warmed up for 15minutes,attach proper thermocouple or RTD wire to zone 1.2.Connect the other end of the wire to the thermocouplesignal generator. Select proper cold junction compensa-tion. Refer to Figure 4-2. For RTD version use precisiondecade resistance box.3.Bring the instrument to alarm condition by setting themillivolt or resistance signal higher than the range of theinstrument. This will stop the scanning and keep theinstrument latched to the zone being calibrated.4.Set the millivolt source or decade resistance box to lowcalibration point as indicated on the calibration tables.5.Adjust the LO calibration potentiometer on the side ofthe instrument to read the proper typical value ±10F or±10C.6.Set the millivolt source or decade resistance box to highcalibration point as indicated on the calibration tables.7.Adjust the Hi calibration potentiometer on the side of theinstrument to read the proper typical value ±1 0F or±10C.8.If large adjustments are made on HI calibration potenti-ometer, repeat steps 4 through 7 until all errors areeliminated.9.Check all calibration points on the table to be within±.25% of the typical calibration.10.Measure that the DC voltage output corresponds to thecalibration table. For RTD version, check resistanceoutput.910Figure 4-2. Thermocouple Calibration4.2.4Calibration Alarm1. Push the SET button and adjust zone 1 setpoint to mid-range.2. Set the temperature input to .25% of range below the setpoint.3.Push the RESET button and allow the scan light to go to zone2.4.Set the input to zone 1 to .25% of range above the setpoint.5.Observe that when the zone light comes to zone 1, the unit goes into alarm condition within 4 seconds.4.2.5Zone Crosstalk1.Set zone 1 setpoint to full range.2.Set zone 1 temperature to 90% of its range.3.Set zone 2 setpoint to .25% of range above its shorted thermocouple temperature.4.Reset alarm if necessary and allow the unit to scan.5.Observe that zone 2 does not alarm.SYMPTOM1. instrument isinactive2.Display reads fullrange unit inalarm no scanning 3.No output, unit inalarm4.Reading is zero5.Reads ambient6.Alarm does notreset7.Does not readsetpoints8.Erratic indication9.Cannot reachrange10.Cannot adjustscan rateCORRECTIVE ACTIONCheck line voltageReplace fuseClean terminalReplace power trans-former.Check probeReplaceCheck relay.Clean or replaceCheck and correct.Check and correct.Check and replace.Tighten or replace.Check cable.Check ±12V regulators.Check 5.03V ±.02;adjust if necessary.Replace potentiometer PROBABLE CAUSENo line voltageBlown fuseDirty screw terminalOpen transformerprimaryOpen thermocoupleprobe or RTD probeBurned input l.C.Relay contacts orrelay coilReversed thermo-couple leadsShorted thermocoupleBroken or jammedreset switchBroken or looseswitchLoose ribbon cable.Power supply faulty5V ReferenceBroken potentiometer11SECTION 5 SPECIFICATIONS 5.1THERMOCOUPLEALARM TYPEACCURACY:INPUTS:NO. OF SETPOINTS:SCANNING RATE:RELAY:ANALOG OUTPUT:ALARM OPERATION:RESET:MAX. VOLTAGE BETWEEN INPUTS: POWER:POWER LOSS:DISPLAY:AMBIENT OPERATING RANGE: DIMENSIONS:PANEL CUTOUT:DEPTH BEHIND PANEL: TERMINALS:CN1O1 models-high alarm; CN1O2 models-low alarm±1% of range6, thermocouple6, independent for each input4 to 12 seconds per channel, side adjustmentSPDT Mechanical, rated 5A at120 VAC, 3A at 240 VAC latching 0 to 5 VDC, scans sequentially from zone to zone (non-isolated)Relay de-energized. ALARM ON LED indicator on, scan hold until reset Manual, front pushbutton10 VDC or 6 VRMS120/240 VAC, 50/60 HzUnit returns to ready state4-digit LED, 0.6”32 to 1350F3.56”H x 3.56”W x 6.25”D1/4 DIN, 3.622” x 3.622”6.25”Type 6-32 screws125.2RTDACCURACY:INPUTS:NO. OF SETPOINTS:OPEN SENSOR INDICATION: SCANNING RATE:RELAY:ANALOG OUTPUT:ALARM OPERATION:RESET:MAX. VOLTAGE BETWEEN INPUTS: POWER:POWER LOSS:RESOLUTION:DISPLAY:AMBIENT OPERATING RANGE: DIMENSIONS:PANEL CUTOUT:DEPTH BEHIND PANEL: TERMINALS:Greater than 0.5% range ±1RTD 100 ohm Platinum (European)—2 wire “Top” input connector—common to all 6 channels (negative wire). “Bottom” input connector—single inputs to each channel (positive wire)6, independent for each input Treated as alarm4 to 12s per channel, side adjustment Mechanical, rate 5A @ 120 Vac(24 Vdc), 3A @ 240 Vac (48 Vdc); SPDT type0 to 5 Vdc, non-isolatedRelay de-energized, ALARM ON LED indicator on, scan hold until reset Manual, front pushbutton10 Vdc or 6Vrms120/240 Vac, 50/60 HzUnit returns to ready state after power resumption104-digit LED, 0.6”32 to 1350F3.56” H x 3.56”W x 7” D¼ DIN, 3.622” x 3.622”6.25”Type 6-32 screws135.3PARTS LISTP.C. Board-ARESISTORS 1/4 WATT1-220 ohm (R26)2-1K (R6, R22)4- 1.5K (R9, R10, R11, R12)1- 2.2K (R17)1- 2.7K (R16)6- 4.7K (R4, R7, R8, R24, R29, R30)7-10K (R2, R3, R5, R13.2, R14. R15, R23) 1-8.2K (R27)1-18K (R28)1-33K(R1)1-66K (R19)1-lOOK (R20)1-470K (R25)PRECISION RESISTORS:1 ‘ 400K(R18)POTS:1-2K (P3) (89PR)2-1OOK (P1, P2) (89PR)CAPACITORS:1-68pF (C3)1-220pF (C2)1-4700 pF(C4)3-0.01uF (Mylar) (C5, C8, near Q14)1- 2.2/50V (C7)1-10/25V(C6)2-10/50V (C9. C10)1-100/25V (C1)2-100/50V (C13. C1411-1000/16V (C12)DiODES:9-1N4148 (D1, D2, D3, D4, D5, D6, D7, D8, D9) 4-1N4004 (D0, D11, D1Z, D13, D14)TRANSISTORS:7-2N4424(Q2,Q3, Q4, Q5, Q7, Q23, Q24) CRYSTAL:1 ‘ 3.579514INTEGRATED CIRCUITS:1-741 (Q19)1-311 (Q18)3-4518(Q 8,Q12, Q13)2-4028 (Q1, Q16)2-4040(Q11, Qi4)2-4052(Q9, Q10)1-4066(Q17)1-4011 (Q6)VOLTAGE REGULATORS:1.317LZ (Q22)1-7812(Q20)1-7819(Q21)RELAYS:1- 5 AMP Relay MS64-932TRANSFORMER:1-830957HEADERS:1-4161-14-03-P1 (Straight)1-4162-22-06-P1SOCKETS:2-16 Pin MEGA 16MPCONNECTOR:1-4002-14-00-P5P.C. Board-BPRECISION RESISTOR 1%:11K (R52)1-250K (R53)1-174K(NearP10)POTS:1-200 ohm (P10) 89PR7-10K (P4, P5, P6, P7, P8, P9, P11) 89PR15CAPACITORS:1- 2.2/50 (C25)1- 4.7/50V (C22)4-22/50 (C15, C16, C19, C23)RESISTORS 1/4 WATT6-100 ohm (R76, R77, R78, R79, R80, R81)7-1K (R29, R49, R56, R57, R58, R62, R63)1- 1.5K (R72)1- 2.2K (R64)2- 4.7 (R74, R83)5-10K (R27, R51, R59, R67, R69)17-33K (R32, R33, R34, R37, R38, R39, R40, R45, R47, R48, R50, R54, R55, R60, R61, R68, R70)3-100K (R28, R46, R91)1-220K(R35)-330K (R30)2- 1 Meg. (R36, R41)1- 1.5 Meg. (R42)2-10 Meg. (R65, R66)DIODES:6-1N4148 (D15, D16, D18, D19, D20, D23)6-1N751, 1N753 or 1N754 (Z2, Z3, Z4, Z5, Z6, Z7) TRANSISTORS:1- 2N4424 (Q29)INTEGRATED CIRCUITS:3-4051(Q24,Q30,Q31)2-uA339 (Q25,Q26)1-4066(Q27)I-0P20 (Q28)HEADERS:1-14 PIn #4161-14-03-Pi (Straight)SWITCHES:2-C&K8168(S1,S2)2-BIackCaps80252-Metal Guards G-12A2-WashersBARRIER CONNECTOR:1-A204207NLR501-A20720NLR5316CONNECTOR:1-4002-14-00-P51- Cable #455-240-14PC Board-CRESISTOR 1/4 W:7-47ohmLED’s:1-Red (MV5754)1-Green (MV5454)6-Yellow(MV5354)DISPLAY MODULE:2-MAN6740HARDWARE:1-Case1-Backplate1-Bezel1-Face Plate (Metal)1-Face Plate (Plastic)1-SprIng4-3/8” x 5/32” F/HD Screws4-3/8” x 5/32” R/MD Screws2-5/32 Nuts1-Red Lens5.4CALIBRATION CHARTSThe following charts are sample calibration charts for theranges 0-5000FJ, and 0-20000FK. For models other than theseranges,it is advisable to calibrate the units at 10% and 90% FS.1718CN101(*)-(**)5.4.1CALIBRATION TABLE 0-2000°F-TYPE-KRANGE COMPONENTSR13.4-10K R18-400K 1%R62- 1.5K R63- 2.2K R64- 1.3K R73-43K R84-13.3K R85-27K R86-110K 1%195.4.3CALIBRATION TABLE 0-500°F-TYPE JRANGE COMPONENTSR13.2-10K R18-400K 1%R62-1K R63-1K R64- 2.2K R73-33K R84-OUT R85-10K R86-350K 1%20NOTES Actual temperature rounded off to whole digit (no decimal point). Accuracy better than 0.5% of 250C-2250C range.Recommended lead wire distances to obtain stated accuracy with proper calibration. Use copper wire. Based on ambient temperature.AWG Distance 14150ft 2050ft 2425ft5.4.3CALIBRATION TABLE 0-250°C-RTD275.5COMPONENT LAYOUT-P .C. Board A1.Select nearest standard range resistor (e.g. 800° = R13.3).2.Set setpoint pot full CW (maximum).3.Adjust P2 for required range readout.4.Reduce R18 If range cannot be reached.5.5COMPONENT LAYOUT-P.C. Board B5.6SCHEMATICM0666/0702。
Omega 产品说明书

e-mail:**************For latest product manuals:Shop online atUser’s Guidey = mx+bA Guide to Calibration and Unit ConversionOMB-457-0949 rev 1.0System Calibration & Engineering Units Conversion Using mx + b In many data acquisition software programs, the mx + b application is a powerful tool, which can be used to adjust displayed readings and/or values obtained from stored data. Using this software computational feature, it is possible to convert voltage readings to any more useful or appropriate engineering units, and simultaneously accomplish channel calibration to reduce or eliminate offset and gain errors. The following examples demonstrate how either or both objectives are accomplished for:•Engineering Units Conversion (1 example)•System Channel Calibration (2 examples)•Combined System Channel Calibration and Engineering Units Conversion (1 example) Engineering Units ConversionA pressure transducer with a 0-600 psi range has a 4-20mA output and is connected in a closed loop to drop 1-5 volts across a 250-ohm resistor. The theoretical nameplate relationship establishes that 1 V = 0 psi and 5 volts = 600 psi.A units conversion equation can be written in the following form:Desired Reading = m(Available Reading) + bWrite a pair of equations, representing the two known points.0 = m(1) + b (1)600 = m(5) + b (2)Solve for m by multiplying equation (1) by -1 and adding to equation (2).0 = m(1) - b600 = m(5) + b600 = m(5 - 1) (3)m = 600/(5 - 1) (4)m = 150Substitute the value for m into equation (1) to determine the value for b.0 = 150(1) + b (5)b = -150Write the correction equation using the previously determined values for m and b.Desired Reading in psi = 150(Available Reading in volts) - 150Check the result with the two original voltage readings.Correct Reading for 600 = 150(5) - 150= 600.00Correct Reading for 0 = 150(1) - 150= 0.00Any readings in the region between these two points provide the proportional psi reading as provided by the transducer.y = mx + b September 2002457-0949, rev 1.0 - 1 -System Channel Calibration(Example 1 of 2)A DBK9 and a DaqBook are connected to a precision 100.0 ohm resistor and read 0.2 °C; However, in this instance we know that 0.0 °C is the correct value. When connected to a 350.1 ohm resistor, the channel reads 719 °C. In this second instance we know that 716 °C is the correct value. From these two “points,” a correction [or calibration] equation can be derived. The equation has the mx + b form of:Correct Reading = m(Erroneous Reading) + bWrite a pair of equations, representing the two known points.0 = m(0.2) + b (1)716 = m(719) + b (2)Solve for m by multiplying equation (1) by -1 and adding to equation (2).0 = m(-0.2) - b716 = m(719) + b716 = m(719 - 0.2) (3)m = 716/(719 - 0.2) (4)m = 0.9961Substitute the value for m into equation (1) to determine the value for b.0 = 0.9961(0.2) + b (5)b = -0.1992Write the correction equation using the previously determined values for m and b.Correct Reading = 0.9961(Erroneous Reading) - 0.1992Check the result with the two original erroneous values.Correct Reading for 716 = 0.9961(719) - 0.1992= 715.99Correct Reading for 0 = 0.9961(0.2) - 0.1992= 0.00002Any readings in the region of these two points should be much more accurate after being adjusted by the correction equation. -2- 457-0949, rev 1.0September 2002y = mx + bSystem Channel Calibration(Example 2 of 2)A DBK8 and a DaqBook are configured for a 50 volt range. Shorting the inputs together delivers a reading of 0.022 volts and applying a DC calibrator set at 47.5 volts produces a reading of 48.3 volts. From these two “points” a correction or calibration equation can be derived which has the form:Correct Reading = m(Erroneous Reading) + bWrite a pair of equations, representing the two known points.0 = m(0.022) + b (1)47.5 = m(48.3) + b (2)Solve for m by multiplying equation (1) by -1 and adding to equation (2).0 = m(-0.022) - b47.5= m(48.3) + b47.5 = m(48.3 - 0.022) (3)m = 47.5/(48.3 - 0.022) (4)m = 0.9839Substitute the value for m into equation (1) to determine the value for b.0 = 0.9839(0.022) + b (5)b = -0.0216Write the correction equation using the previously determined values for m and b.Correct Reading = 0.9839(Erroneous Reading) - 0.0216Check the result with the two original erroneous values.Correct Reading for 47.5 = 0.9839(48.3) - 0.0216= 47.501Correct Reading for 0 = 0.9839(0.022) - 0.0216= 0.00004Any readings in the region of these two points should be much more accurate after being adjusted by the correction equation. y = mx + b09-13-023Combined System Channel Calibration and Engineering Units Conversion A DBK15 and a DaqBook are connected to a string pot to measure the open position of a vertical bay door. When the door is closed, the voltage reading given by the DaqBook is 0.175 volts. When the door is raised to a height of 12 feet, the voltage reading provided by the DaqBook is 4.572 volts. From these two “points” a correction [or calibration] equation can be derived which has the form:Correct Reading = m(Erroneous Reading) + bWrite a pair of equations, representing the two known points.0 = m(0.175) + b (1)12 = m(4.572) + b (2)Solve for m by multiplying equation (1) by -1 and adding to equation (2).0 = m(-0.175) - b12 = m(4.572) + b12 = m(4.572 - 0.175) (3)m = 12/(4.572 - 0.175) (4)m = 2.729Substitute the value for m into equation (1) to determine the value for b.0 = 2.729 (0.175) + b (5)b = -0.478Write the correction equation using the previously determined values for m and b.Correct Reading = 2.729(Erroneous Reading) - 0.478Check the result with the two original erroneous values.Correct Reading for 12 = 2.729(4.572) - 0.478= 12.00Correct Reading for 0 = 2.729(0.175) - 0.478= 0.00Any readings in the region of these two points should be much more accurate after being adjusted by the correction equation. -4- 457-0949, rev 1.0September 2002y = mx + bWARRANTY/DISCLAIMEROMEGA ENGINEERING, INC. warrants this unit to be free of defects in materials and workmanship for a period of 13 months from date of purchase. OMEGA’s WARRANTY adds an additional one (1) month grace period to the normal one (1) year product warranty to cover handling and shipping time. This ensures that OMEGA’s customers receive maximum coverage on each product.If the unit malfunctions, it must be returned to the factory for evaluation. OMEGA’s Customer Service Department will issue an Authorized Return (AR) number immediately upon phone or written request. Upon examination by OMEGA, if the unit is found to be defective, it will be repaired or replaced at no charge. OMEGA’s WARRANTY does not apply to defects resulting from any action of the purchaser, including but not limited to mishandling, improper interfacing, operation outside of design limits, improper repair, or unauthorized modification. This WARRANTY is VOID if the unit shows evidence of having been tampered with or shows evidence of having been damaged as a result of excessive corrosion; or current, heat, moisture or vibration; improper specification; misapplication; misuse or other operating conditions outside of OMEGA’s control. Components in which wear is not warranted, include but are not limited to contact points, fuses, and triacs.OMEGA is pleased to offer suggestions on the use of its various products. However, OMEGA neither assumes responsibility for any omissions or errors nor assumes liability for any damages that result from the use of its products in accordance with information provided by OMEGA, either verbal or written. OMEGA warrants only that the parts manufactured by the company will be as specified and free of defects. OMEGA MAKES NO OTHER WARRANTIES OR REPRESENTATIONS OF ANY KIND WHATSOEVER, EXPRESSED OR IMPLIED, EXCEPT THAT OF TITLE, AND ALL IMPLIED WARRANTIES INCLUDING ANY WARRANTY OF MERCHANTABILITY AND FITNESS FOR A PARTICULAR PURPOSE ARE HEREBY DISCLAIMED. LIMITATION OF LIABILITY: The remedies of purchaser set forth herein are exclusive, and the total liability of OMEGA with respect to this order, whether based on contract, warranty, negligence, indemnification, strict liability or otherwise, shall not exceed the purchase price of the component upon which liability is based. In no event shall OMEGA be liable for consequential, incidental or special damages.CONDITIONS: Equipment sold by OMEGA is not intended to be used, nor shall it be used: (1) as a “Basic Component” under 10 CFR 21 (NRC), used in or with any nuclear installation or activity; or (2) in medical applications or used on humans. Should any Product(s) be used in or with any nuclear installation or activity, medical application, used on humans, or misused in any way, OMEGA assumes no responsibility as set forth in our basic WARRANTY/DISCLAIMER language, and, additionally, purchaser will indemnify OMEGA and hold OMEGA harmless from any liability or damage whatsoever arising out of the use of the Product(s) in such a manner.RETURN REQUESTS/INQUIRIESDirect all warranty and repair requests/inquiries to the OMEGA Customer Service Department. BEFORE RETURNING ANY PRODUCT(S) TO OMEGA, PURCHASER MUST OBTAIN AN AUTHORIZED RETURN (AR) NUMBER FROM OMEGA’S CUSTOMER SERVICE DEPARTMENT (IN ORDER TO AVOID PROCESSING DELAYS). The assigned AR number should then be marked on the outside of the return package and on any correspondence.The purchaser is responsible for shipping charges, freight, insurance and proper packaging to prevent breakage in transit.FOR WARRANTY RETURNS, please have the following information available BEFORE contacting OMEGA:1.Purchase Order number under which the productwas PURCHASED,2.Model and serial number of the product underwarranty, and3.Repair instructions and/or specific problemsrelative to the product.FOR NON-WARRANTY REPAIRS,consult OMEGA for current repair charges. Have the following information available BEFORE contacting OMEGA: 1. Purchase Order number to cover the COSTof the repair,2.Model and serial number of the product, and3.Repair instructions and/or specific problemsrelative to the product.OMEGA’s policy is to make running changes, not model changes, whenever an improvement is possible. This affords our customers the latest in technology and engineering.OMEGA is a registered trademark of OMEGA ENGINEERING, INC.© Copyright 2006OMEGA ENGINEERING, INC. All rights reserved. This document may not be copied, photocopied, reproduced, translated, or reduced to any electronic medium or machine-readable form, in whole or in part, without the prior written consent of OMEGA ENGINEERING, INC.Where Do I Find Everything I Need for Process Measurement and Control?OMEGA…Of Course!Shop online at TEMPERATUREⅪߜThermocouple, RTD & Thermistor Probes, Connectors, Panels & AssembliesⅪߜWire: Thermocouple, RTD & ThermistorⅪߜCalibrators & Ice Point ReferencesⅪߜRecorders, Controllers & Process MonitorsⅪߜInfrared PyrometersPRESSURE, STRAIN AND FORCEⅪߜTransducers & Strain GagesⅪߜLoad Cells & Pressure GagesⅪߜDisplacement TransducersⅪߜInstrumentation & AccessoriesFLOW/LEVELⅪߜRotameters, Gas Mass Flowmeters & Flow ComputersⅪߜAir Velocity IndicatorsⅪߜTurbine/Paddlewheel SystemsⅪߜTotalizers & Batch ControllerspH/CONDUCTIVITYⅪߜpH Electrodes, Testers & AccessoriesⅪߜBenchtop/Laboratory MetersⅪߜControllers, Calibrators, Simulators & PumpsⅪߜIndustrial pH & Conductivity EquipmentDATA ACQUISITIONⅪߜData Acquisition & Engineering SoftwareⅪߜCommunications-Based Acquisition SystemsⅪߜPlug-in Cards for Apple, IBM & CompatiblesⅪߜDatalogging SystemsⅪߜRecorders, Printers & PlottersHEATERSⅪߜHeating CableⅪߜCartridge & Strip HeatersⅪߜImmersion & Band HeatersⅪߜFlexible HeatersⅪߜLaboratory HeatersENVIRONMENTALMONITORING AND CONTROLⅪߜMetering & Control InstrumentationⅪߜRefractometersⅪߜPumps & TubingⅪߜAir, Soil & Water MonitorsⅪߜIndustrial Water & Wastewater TreatmentⅪߜpH, Conductivity & Dissolved Oxygen InstrumentsM4347/0606。
欧米茄表使用说明书
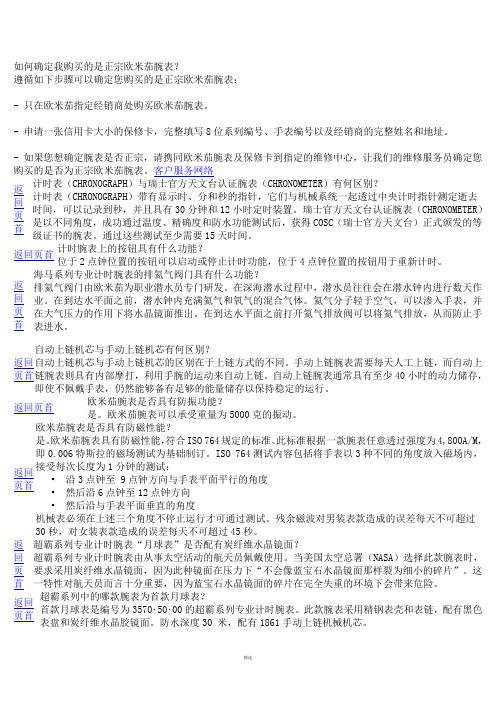
如何确定我购买的是正宗欧米茄腕表?遵循如下步骤可以确定您购买的是正宗欧米茄腕表:- 只在欧米茄指定经销商处购买欧米茄腕表。
- 申请一张信用卡大小的保修卡,完整填写8位系列编号、手表编号以及经销商的完整姓名和地址。
- 如果您想确定腕表是否正宗,请携同欧米茄腕表及保修卡到指定的维修中心,让我们的维修服务员确定您购买的是否为正宗欧米茄腕表。
客户服务网络返回页首计时表(CHRONOGRAPH)与瑞士官方天文台认证腕表(CHRONOMETER)有何区别?计时表(CHRONOGRAPH)带有显示时、分和秒的指针,它们与机械系统一起透过中央计时指针测定逝去时间,可以记录到秒,并且具有30分钟和12小时定时装置。
瑞士官方天文台认证腕表(CHRONOMETER)是以不同角度,成功通过温度、精确度和防水功能测试后,获得COSC(瑞士官方天文台)正式颁发的等级证书的腕表。
通过这些测试至少需要15天时间。
返回页首计时腕表上的按钮具有什么功能?位于2点钟位置的按钮可以启动或停止计时功能,位于4点钟位置的按钮用于重新计时。
返回页首海马系列专业计时腕表的排氦气阀门具有什么功能?排氦气阀门由欧米茄为职业潜水员专门研发。
在深海潜水过程中,潜水员往往会在潜水钟内进行数天作业。
在到达水平面之前,潜水钟内充满氦气和氧气的混合气体。
氦气分子轻于空气,可以渗入手表,并在大气压力的作用下将水晶镜面推出。
在到达水平面之前打开氦气排放阀可以将氦气排放,从而防止手表进水。
返回页首自动上链机芯与手动上链机芯有何区别?自动上链机芯与手动上链机芯的区别在于上链方式的不同。
手动上链腕表需要每天人工上链,而自动上链腕表则具有内部摩打,利用手腕的运动来自动上链。
自动上链腕表通常具有至少40小时的动力储存,即使不佩戴手表,仍然能够备有足够的能量储存以保持稳定的运行。
返回页首欧米茄腕表是否具有防振功能?是。
欧米茄腕表可以承受重量为5000克的振动。
返回页首欧米茄腕表是否具有防磁性能?是。
Omega HX15高温相对湿度传感器用户指南说明书

HX15High Temperature Relative Humidity/Temperature®e-mail:**************For latest product manuals:Shop online at®User’sGuideRoHS 2 CompliantIt is the policy of OMEGA Engineering, Inc. to comply with all worldwide safety and EMC/EMI regulations that apply. OMEGA is constantly pursuing certification of its products to the European New Approach Directives. OMEGA will add the mark to every appropriate device upon certification.The information contained in this document is believed to be correct, but OMEGA accepts no liability for anyTABLE OF CONTENTSA. General Description 1.B. Unpacking 1.C. Theory of Operation 2.D. Terminal Connections 3.E. Wiring Example 3.F. Mounting 4.G. Calculations 5.H. R H Calibration 6.I. Temp. Calibration 7.J. Maintenance 7.K. Specifications 8.A. GENERAL DESCRIPTIONThe stainless steel probe provides relative humidity as well astemperature out puts. A thin film polymer capacitor senses relative humidity, while temperature is monitored by a 1000 Ohm platinum RTD. The sensors are protected by a stainless steel filter cap easily removed for cleaning. The probe is connected to an electronicsenclosure with a 40 inch (1m) Teflon cable. The enclosure contains the calibration trimmers, signal and power connections via twoterminal blocks. The probe is available in two configurations, as a2.5” (64 mm) probe with a wall mounting clip, and as an 8.5” (216mm) probe with an adjustable duct flange.B. UNPACKINGVerify that the following parts have been received.1.Remove probe with cable and electronics enclosure.2.Instruction manual.3.Wall mounting clip [for 2.5” (64 mm) probe].4. 2 piece duct flange, with o-ring, (3) screws, and a gasket.[for 8.5” (216 mm) probe]C. THEORY OF OPERATIONA 4 to 20 milliamp loop is a series current loop in which atransmitter will vary the current flow depending upon the parameter being measured (Relative Humidity or Temperature). Advantages ofa current output over a voltage output is that is less susceptible tonoise interference and allows the connection of more than one meter or recorder to the loop as long as the maximum resistance is notexceeded.The typical current loop will consist of a power supply, transmitter, and a meter to measure the current flow. The loop resistance is the sum of the impedance of the meter(s) and the lead wire. Themaximum allowable loop impedance of the probe is found by the Formula:Rmax = (power supply voltage-7 volts) /.02 ampsExample: when using a 24 VDC power supply:Rmax= (24-7) /.02=850 ohms (for total wire length to andfrom the transmitter).AWG WIRE SIZE RESISTANCE PER 1000 FEETIf the meter or recorder being used accepts only voltage, convert the current to voltage by installing a 250 ohm resistor across the input terminals of the recorder to obtain a 1 to 5 volts input.D. TERMINAL CONNECTIONS AND TRIM POTSE. WIRING EXAMPLESTYPICAL CURRENT HOOKUP Wires R1 and R2 can be combined into one single wire with a jumper at pins (4) and (2). This will result in 3 wires instead of 4. TRIMPOTS TYPE A. RH GAIN B. RH ZERO C. RH OFFSET D. TEMP GAIN E. TEMP ZEROPROBE INSTALLATIONF. MOUNTINGA.DUCT MOUNTINGSTEPS1.Slide flange holder onto probe with countersinkhole facing front of probe as shown.2.Position o-ring on probe at desired position (for depth intoduct).3.Slide duct flange onto probe as shown.4.Fasten with (3) 6/32 screws and tighten evenly until secure.5.Position gasket between duct flange and duct wall and fastenassembly to duct with (4) #6 sheet metal screws (notincluded).6.Loosening the 6/32 screws allows for repositioning orremoval of the probe without having to remove the ductflange from the wall.The d uct wall requires a 11/16” (.684” or 17.5 mm) hole forprobe, with (4) mounting holes (for #6 sheet metal screws)evenly spaced on a 2.0” (51 mm) circle. Use duct flange astemplate.B.WALL MOUNTING1.Fasten metal clip to wall.2.Snap probe into clip.G. RH AND TEMPERATURE CALCULATIONS1.Maximum current loop impedance for RH or temperature.Rmax = (V supply – 7 volts) /.02 amps2.RH current output (i = current output in milliamperes)3.Temperature current output.oC = (i-4) x 220/16) – 40 iC = (oC + 40) x (16/220) + 4oF = (i-4) x (396/16) – 40 iF = (oF + 40) x (16/396) + 4The upper limit of the humidity measurement range decreases based on temperature. The humidity measurement limit decreases as follows:2.20% per °C from 95 to 120°C (1.11% per °F from 203 to 248°F)1.00% per °C from 120 to 140°C (0.56% per °F from 248 to 284°F) 0.50% per °C from 140 to 160°C (0.28% per °F from 284 to 320°F) 0.25% per °C from 160 to 180°C (0.14% per °F from 320 to 356°F)For example, at 120°C the upper humidity limit decreases to about 45% ((120-95)(2.20%) = 55% decrease which is 45%), at 180°C it is reduced to about 10%.To calculate the RH accuracy, we’ll use the accuracy specs given in the specifications section:+/-2%RH at 25°C and -40° to 150°C at 0.05 % RH/°C.To clarify lets take an example,RH accuracy at 120°C,=+/- (2% + (120-25)0.05%) = +/- (2% + 4.75%)=+/-6.75%So the accuracy at 120°C is +/- 6.75% and the upper humidity measurement limit is 45% RH.H. RH CALIBRATIONRefer to Section D for the location of trim pots A and B.Note: The HX92-CAL Relative Humidity Calibration Kit is for providing the “low” and “high” RH environments for this procedure. The salt solutions in this kit are prepared according to ASTM standard E104-85 to provide 11.3% and 75.3% relative humidity environments. The containers provided in the kit are designed to fit with these instruments.1.Turn the span (trim pot A) all the way up (clockwise).2.Turn the zero (trim pot B) all the way down (counter-clockwise).3.Place the sensor in the low (11.3%) RH environment. Allowat least one hour for stabilization or until the output stopschanging.4.Verify the output is 4 +/-.02 mA. If it is not, return the unitto Omega for evaluation and repair.5.Adjust the zero (trim pot B) to the point where it just starts tocause a change in the output.6.Place the sensor in the high (75.3%) RH environment. Allowat least one hour for stabilization or until the output stopschanging.7.Adjust the span (trim pot A) so the output is equivalent tothe difference between low and high RH environments.Example: 75.3%-11.3% = 64% which is equivalent to 14.24mA.8.Adjust the sensor in the low RH environment and allow atleast one hour for stabilization or until the output stopschanging. Verify the output is equivalent to the low RHenvironment. Example: 11.3% is equivalent to 5.81 mA.I. TEMPERATURE CALIBRATIONTemperature is factory calibrated only, and does not requireany further calibrations.J. MAINTENANCEIf the probe is operated in a dusty environment, theprotective sensor filter, if clogged, may be removed for cleaning.Unscrew filter and gently blow compressed air through screen.If necessary, use a soft brush to remove lint from sensors.If the sensors are subjected to 100% condensation, they must bedried to obtain correct readings. There is no permanentcalibration shift, nor is recalibration necessary if 100%condensation occurs.The instrument should not be exposed to highConcentrations of ammonia or alcohol vapors. However,any environment that is breathable under normal HVACapplications should not affect the sensors. To maintain originalspecifications, it is generally recommended that the RH sensorbe recalibrated on an annual basis depending upon operatingconditions. The temperature sensor does not require calibration.K. SPECIFICATIONS1.Relative Humidity: Thin film polymer capacitor.Input Voltage Range: 7 to 30 VDC (polarity protected).Range, Accuracy: 3% RH to 95% RH (@-40 to 95°C)*, ±2%RH at 25°CTypical Temp. Characteristics: -40°C to 150°C at .05%RH/°COutput: 4 to 20 mA. For 0%RH to 100%RH.Time Constant: Under 30 seconds, 90% response at 25°C in 1M/sec air.* See RH and Temperature Calculations section for full range.2.Temperature: Thin film 1000 ohm platinum RTD.Input Voltage Range: 7 to 30 VDC (polarity protected).Range, Accuracy: -40°C to 180°C (-40°F to 356°F), ±0.5°C (±1°F)Output: 4 to 20 ma. For -40°C to 180°C (-40°F to 356°F)Time Constant: Under 4 seconds, 60% response in 1m/sec air.3.MechanicalStandard Probe: Stainless steel, 2.5” (64 mm) x .625” (16 mm)diameter. 40” (1m) Teflon cable, metal wall mounting clip.Duct Probe: Stainless steel, 8.5” (216 mm) x .625” (16 mm)diameter. 40” (1m) Teflon cable.Duct Flange: 2.75” (70mm) dia., duct hole 11/16 (.684”,17.5 mm) dia. With 4 mounting holes .156(4 mm)diameter (for #6 sheet metal screws), on 2.00”(51mm) circle.Electronics: Operating temp. -20°C to 70°C(-4°F to 158°F)ABS housing 4.72” (120mm) x 3.14” (80 mm) x2.16” (55 mm) H meets NEMA 1,2,3,4,4X,5,12and 13 specifications.Connectors: Liquid-tight with neoprene gland for .09” to .265”diameter cable.4-pin plug in screw terminal block for output connections.5-pin screw terminal block for cable wire inputconnections, accepts #14 to #22 AWG wires.Weight: 2.5” (64 mm) probe with housing 14 oz. (397 grams).8.5” (216 mm) probe with housing and flange 20 oz. (567grams).WARRANTY/DISCLAIMEROMEGA ENGINEERING, INC. warrants this unit to be free of defects in materials and workmanship for a period of 37 months from date of purchase. OMEGA’s WARRANTY adds an additional one (1) month grace period to the normal three (3) year product warranty to cover handling and shipping time. This ensures that OMEGA’s customers receive maximum coverage on each product.If the unit malfunctions, it must be returned to the factory for evaluation. OMEGA’s Customer Service Department will issue an Authorized Return (AR) number immediately upon phone or written request. Upon examination by OMEGA, if the unit is found to be defective, it will be repaired or replaced at no charge. OMEGA’s WARRANTY does not apply to defects resulting from any action of the purchaser, including but not limited to mishandling, improper interfacing, operation outside of design limits, improper repair, or unauthorized modification.This WARRANTY is VOID if the unit shows evidence of having been tampered with or shows evidence of having been damaged as a result of excessive corrosion; or current, heat, moisture or vibration; improper specification; misapplication; misuse or other operating conditions outside of OMEGA’s control. Components in which wear is not warranted, include but are not limited to contact points, fuses, and triacs.OMEGA is pleased to offer suggestions on the use of its various products. However, OMEGA neither assumes responsibility for any omissions or errors nor assumes liability for any damages that result from the use of its products in accordance with information provided by OMEGA, either verbal or written. OMEGA warrants only that the parts manufactured by the company will be as specified and free of defects. OMEGA MAKES NO OTHER WARRANTIES OR REPRESENTATIONS OF ANY KIND WHATSOEVER, EXPRESSED OR IMPLIED, EXCEPT THAT OF TITLE, AND ALL IMPLIED WARRANTIES INCLUDING ANY WARRANTY OF MERCHANTABILITY AND FITNESS FOR A PARTICULAR PURPOSE ARE HEREBY DISCLAIMED. LIMITATION OF LIABILITY: The remedies of purchaser set forth herein are exclusive, and the total liability of OMEGA with respect to this order, whether based on contract, warranty,negligence, indemnification, strict liability or otherwise, shall not exceed the purchase price of the component upon which liability is based. In no event shall OMEGA be liable for consequential, incidental or special damages.CONDITIONS: Equipment sold by OMEGA is not intended to be used, nor shall it be used: (1)as a “Basic Component” under 10 CFR 21 (NRC), used in or with any nuclear installation or activity; or (2) in medical applications or used on humans. Should any Product(s) be used in or with any nuclear installation or activity, medical application, used on humans, or misused in any way, OMEGA assumes no responsibility as set forth in our basic WARRANTY/ DISCLAIMER language, and, additionally, purchaser will indemnify OMEGA and hold OMEGA harmless from any liability or damage whatsoever arising out of the use of the Product(s) in such a manner.RETURN REQUESTS/INQUIRIESDirect all warranty and repair requests/inquiries to the OMEGA Customer Service Department.BEFORE RETURNING ANY PRODUCT(S) TO OMEGA, PURCHASER MUST OBTAIN AN AUTHORIZED RETURN (AR) NUMBER FROM OMEGA’S CUSTOMER SERVICE DEPARTMENT (IN ORDER TO AVOID PROCESSING DELAYS). The assigned AR number should then be marked on the outside of the return package and on any correspondence.The purchaser is responsible for shipping charges, freight, insurance and proper packaging to prevent breakage in transit.FOR WARRANTY RETURNS, please havethe following information available BEFOREcontacting OMEGA:1.Purchase Order number under whichthe product was PURCHASED,2.Model and serial number of the productunder warranty, and3.Repair instructions and/or specificproblems relative to the product.FOR NON-WARRANTY REPAIRS,consult OMEGA for current repair charges. Have the following information available BEFORE contacting OMEGA:1. Purchase Order number to cover the COST of the repair,2.Model and serial number of theproduct, and 3.Repair instructions and/or specific problemsrelative to the product.OMEGA’s policy is to make running changes, not model changes, whenever an improvement is possible. This affords our customers the latest in technology and engineering.OMEGA is a registered trademark of OMEGA ENGINEERING, INC.© Copyright 2013 OMEGA ENGINEERING, INC. All rights reserved. This document may not be copied, photocopied,reproduced, translated, or reduced to any electronic medium or machine-readable form, in whole or in part, withoutthe prior written consent of OMEGA ENGINEERING, INC.Where Do I Find Everything I Need for Process Measurement and Control?OMEGA…Of Course!Shop online at SMTEMPERATUREⅪߜThermocouple, RTD & Thermistor Probes, Connectors, Panels & AssembliesⅪߜWire: Thermocouple, RTD & ThermistorⅪߜCalibrators & Ice Point ReferencesⅪߜRecorders, Controllers & Process MonitorsⅪߜInfrared PyrometersPRESSURE, STRAIN AND FORCEⅪߜTransducers & Strain GagesⅪߜLoad Cells & Pressure GagesⅪߜDisplacement TransducersⅪߜInstrumentation & AccessoriesFLOW/LEVELⅪߜRotameters, Gas Mass Flowmeters & Flow ComputersⅪߜAir Velocity IndicatorsⅪߜTurbine/Paddlewheel SystemsⅪߜTotalizers & Batch ControllerspH/CONDUCTIVITYⅪߜpH Electrodes, Testers & AccessoriesⅪߜBenchtop/Laboratory MetersⅪߜControllers, Calibrators, Simulators & PumpsⅪߜIndustrial pH & Conductivity EquipmentDATA ACQUISITIONⅪߜData Acquisition & Engineering SoftwareⅪߜCommunications-Based Acquisition SystemsⅪߜPlug-in Cards for Apple, IBM & CompatiblesⅪߜData Logging SystemsⅪߜRecorders, Printers & PlottersHEATERSⅪߜHeating CableⅪߜCartridge & Strip HeatersⅪߜImmersion & Band HeatersⅪߜFlexible HeatersⅪߜLaboratory HeatersENVIRONMENTALMONITORING AND CONTROLⅪߜMetering & Control InstrumentationⅪߜRefractometersⅪߜPumps & TubingⅪߜAir, Soil & Water MonitorsⅪߜIndustrial Water & Wastewater TreatmentⅪߜpH, Conductivity & Dissolved Oxygen Instruments M3199/0313。
Omega 一体化测量与控制手册说明书
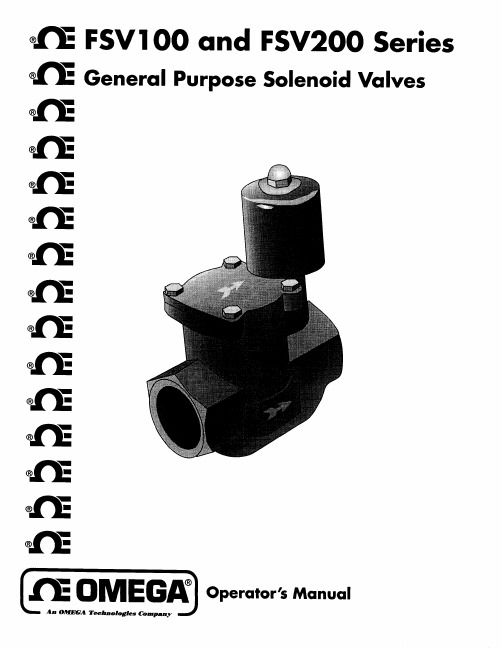
Servicing Europe: United Kingdom Sales and Distribution Center
25 Swannington Road, Broughton Astley, Leicestershire LE9 6TU, England
Telephone: 44 (1455) 285520 FAX: 44 (1455) 283912
1
1.3 Fea t u r es ..................................................................................................................
2
1.4 Ava il ab le M ode ls .........................................................................................................
NOTE The carrier will not honor any claims unless all shipping material is saved for inspection. After examining and removing contents, save packing material and carton in the event reshipment is necessary.
General Purpose Solenoid Valve
(1)
Operators’Manual (1)
If you have any questions about the shipment, please call OMEGA Customer Service Department. When you receive the shipment, inspect the container and equipment for signs of damage. Note any evidence of rough handling in transit. Immediately report any damage to the shipping agent.
OmegaT用户手册
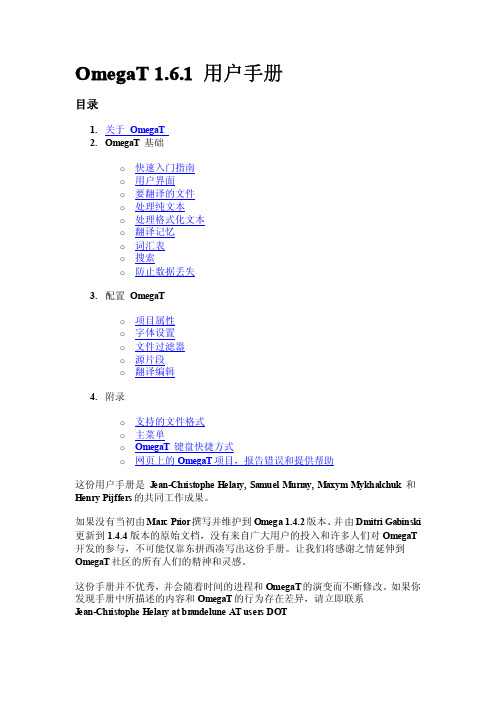
II. 如何使用 OmegaT 翻译
这份手册并不优秀,并会随着时间的进程和 OmegaT的演变而不断修改。如果你 发现手册中所描述的内容和 OmegaT 的行为存在差异,请立即联系 Jean-Christophe Helary at brandelune AT users DOT
关于 OmegaT
OmegaT 是一种免费的多平台计算机辅助翻译工具。
b. 逐段翻译
当你定义好项目以及要翻译的文件之后,OmegaT 将会在编辑器中打开第一个源 文件。第一个片段将以绿色高亮度显示,在下方 “目标区域”将会显示一段源文本 的拷贝。(此时,目标区域之外的所有文本都受到保护无法修改)你必须在标记 < segment 0001>和<end segment>之间输入你的翻译,并覆盖源文本。
快速入门指南
(五分钟内学会使用 OmegaT )
这份快 速入门指 南只覆 盖了非常 基础的 内容。理 论上,所 有的用户 应该这 份用 户手册来熟悉 OmegaT 所能提供的一切。
内容
5. OmegaT 的简要工作机制 6. 如何使用 OmegaT 翻译
o 创建并打开一个新的项目 o 逐段翻译 o 使用翻译记忆和词汇表匹配
翻译过程
假如你不得不对一个充斥着子目录和文件的目录中所有内容进行翻译。而这些文 件又由各种不同的格式组成。你只需告诉 OmegaT 你想翻译哪些文件,它就会 使用文件过滤规则在其中查找所支持的文件,将文本部分识别出来 ,并按照分段 规则对最大的文本组进行分割,最后将片段逐段显示出来以便你进行翻译。
- 1、下载文档前请自行甄别文档内容的完整性,平台不提供额外的编辑、内容补充、找答案等附加服务。
- 2、"仅部分预览"的文档,不可在线预览部分如存在完整性等问题,可反馈申请退款(可完整预览的文档不适用该条件!)。
- 3、如文档侵犯您的权益,请联系客服反馈,我们会尽快为您处理(人工客服工作时间:9:00-18:30)。
To Set the Decimal Point
1.
If it's not already shown, press MENU until the unit displays DEC.P
2.
Press ᮣ/DEV to show the current decimal point location.
3.
Press ᮡ/MAX to move the decimal point to the desired location. The choices are FFFF or FFF.F .
4.
Press MENU to store the value.
5.Press RESET twice to display the current temperature.
To Select Temperature Unit
(Fahrenheit or Celsius):1.
Press MENU until the display shows RD.CF
2.
Press ᮣ/DEV to display the current temperature unit.
3.
Press ᮡ/MAX to select between °F and °C.
4.
Press MENU to store the value.
5.
Press RE SE Ttwice to display the current temperature.
To Enter Setpoints:
1.
Press SETPTS to display the current setpoint. The leftmost digit will flash.
2.
Press ᮣ/DEV to select the digit you want to change.
3.
Press ᮡ/MAX to increase the value of the flashing digit.
4.
Press SETPTS to store the
setpoint.
5.
Repeat steps 1 through 4 to enter the next setpoint.
DP25-TC and DP25B-TC
PROGRAMMABLE DIGITAL
THERMOCOUPLE CONTROLLER
It is the policy of OMEGA to comply with all worldwide safety and EMC/EMI regulations that apply. OMEGA is constantly pursuing certification of its products to the European
New Approach Directives. OMEGA will add the CE mark to every appropriate device upon certification.
The information contained in this document is believed to be correct but
OMEGA Engineering, Inc. accepts no liability for any errors it contains, and reserves the right to alter specifications without notice.
TRADEMARK NOTICE:
®
®, and
,
are trademarks of OMEGA Engineering, Inc.
®
WARNING:These products are not designed for use in, and should not be used for, patient connected applications.
MQS3732/1205
5
6
START HERE
Using This Quick Start Manual
Use this Quick Start Manual with your controller to make
changes to the thermocouple type, decimal point, units, and to change the setpoints.
Before You Begin
In addition to the meter and the related parts, you will need the following items to set up your meter:•ac power, as listed on meter’s ID/Power Label •Thermocouple
•
1/8” flat blade screwdriver
Mount the Unit
1.Cut a panel opening using the dimensions shown to the right.
2.Position the unit in the opening, making sure the front bezel is flush with the panel.
3.Install retaining clip on the meter and tighten against the panel.
AC Powered Unit Connections
Time-delay, UL 248-14 listed Time-lag, IEC 127-3 recognized 175 mA (115 Vac line)125 mA (115 Vac line)80 mA (230 Vac line)
63 mA (230 Vac line)
Pollution Degree.
The instrument is a panel mount device protected in
accordance with EN61010-1 (Safety requirements for electrical equipment for measurement, control, and laboratory standard).Remember that the unit has no power-on switch. Building
installation should include a switch or circuit-breaker that must be compliant to IEC 947-1 and 947-3.SAFETY:
•Do not exceed voltage rating on the label located on the top of the instrument housing.
•Always disconnect power before changing signal and power connections.
•Do not use this instrument on a work bench without its case for safety reasons.
•Do not operate this instrument in flammable or explosive atmospheres.
•Do not expose this instrument to rain or moisture.EMC:•Whenever EMC is an issue, always use shielded cables. •Never run signal and power wires in the same conduit.•Use signal wire connections with twisted-pair cables.
•
Install Ferrite Bead(s) on signal wire close to the instrument if EMC problems persist.
DC Powered Unit Connections
Using the Menus
To Change the Thermocouple Type:1.Press MENU until the display
shows INPT
2.
Press ᮣ/DEV to show current thermocouple type:
3.
Press ᮡ/MAX to select the setting from J, K, Tor DJ.T C.
4.Press MENU to store the value.
5.Press RE SE Ttwice to display the current temperature.。