模具标准零件加工工艺
模具标准零件加工工艺

模具标准零件加工工艺模具标准零件加工工艺是指对模具标准零件进行加工的技术和方法,主要是针对金属材料的机械加工过程。
模具标准零件是模具加工中最基本的部件之一,它们直接影响着模具的加工质量和使用寿命,因此模具标准零件的加工工艺显得尤为重要。
模具标准零件加工工艺需要遵循的一些基本原则和技术要点:1. 熟练掌握加工工艺和加工设备的基本知识,对于加工途中可能出现的问题,需要能够及时的进行判断和应对。
2. 考虑加工工艺的整体性,从加工序列、加工工艺、加工设备及所需工具、夹具等方面进行全面规划,保证整个加工过程的顺畅和高效。
3. 严格控制零件加工的质量和精度,特别需要注意加工零件的尺寸和端面平行度,因为它们对模具加工的精度直接决定。
4. 对于不同材质的模具标准零件,需要选择不同的切削工具,以保障加工效率,同时还要考虑材质硬度及加工性等因素。
在进行模具标准零件的加工过程中,还需要注意以下方面1. 材料的选择与加工要求:材料的选择与零件加工后要求的表面加工精度和粗糙度有关,对于不同的工艺要求可能需要不同材质的切削工具,以确保完成最终的加工要求。
2. 加工前准备与机床设置:加工前首先需要对该零件的加工阶段进行划分、方案设计以及机床设计;接着需要根据加工零件的材料、形状、大小、加工要求等进行不同机床的选择,并对其进行技术参数的设置。
3. 切削工具的选择和修复:切削工具的合理选用对零件的加工精度直接影响较大。
刀具的磨损情况对于工件表面质量也有直接影响,因此要及时检查、维护切削工具的磨损情况,若有问题要及时修复或更换。
4. 机床操作流程:在进行原始加工前,需要事先进行一次系统的单件检查,并完成自认划分和机床设置工序,完成机床基本参数的输入,先进行试加工。
然后,进行设备调试,将设备调整到最佳状态,调整的关键是精调床身,定具及杆上定位孔的位置及容度,以保证零件尺寸和几何精度的稳定和一致性。
综上所述,模具标准零件加工工艺需要严格的操作流程和质量控制,才能保证零件的加工质量和精度。
模具加工工艺流程
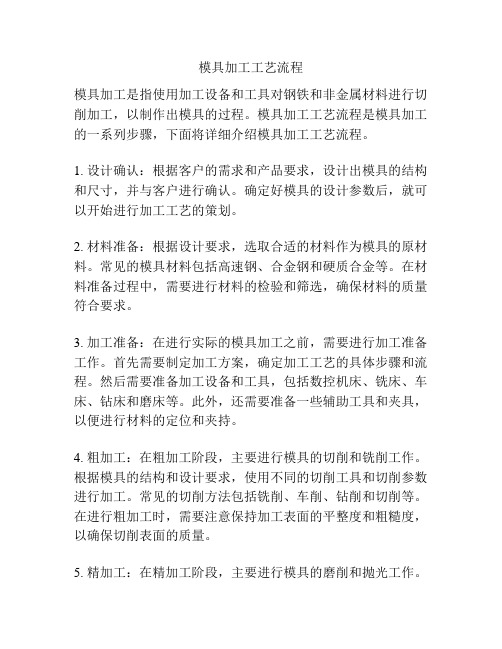
模具加工工艺流程模具加工是指使用加工设备和工具对钢铁和非金属材料进行切削加工,以制作出模具的过程。
模具加工工艺流程是模具加工的一系列步骤,下面将详细介绍模具加工工艺流程。
1. 设计确认:根据客户的需求和产品要求,设计出模具的结构和尺寸,并与客户进行确认。
确定好模具的设计参数后,就可以开始进行加工工艺的策划。
2. 材料准备:根据设计要求,选取合适的材料作为模具的原材料。
常见的模具材料包括高速钢、合金钢和硬质合金等。
在材料准备过程中,需要进行材料的检验和筛选,确保材料的质量符合要求。
3. 加工准备:在进行实际的模具加工之前,需要进行加工准备工作。
首先需要制定加工方案,确定加工工艺的具体步骤和流程。
然后需要准备加工设备和工具,包括数控机床、铣床、车床、钻床和磨床等。
此外,还需要准备一些辅助工具和夹具,以便进行材料的定位和夹持。
4. 粗加工:在粗加工阶段,主要进行模具的切削和铣削工作。
根据模具的结构和设计要求,使用不同的切削工具和切削参数进行加工。
常见的切削方法包括铣削、车削、钻削和切削等。
在进行粗加工时,需要注意保持加工表面的平整度和粗糙度,以确保切削表面的质量。
5. 精加工:在精加工阶段,主要进行模具的磨削和抛光工作。
磨削可以通过磨床或手工进行,以提高模具的精度和表面质量。
在进行抛光时,可以使用研磨机或抛光机进行,以获得光滑的表面和高光泽度。
6. 零件装配:在模具加工完成后,需要进行零件的装配工作。
根据模具的结构和设计要求,将不同的零件进行拼装和组装。
在装配过程中,需要进行零部件的调整和校正,以保证装配的精度和稳定性。
7. 调试和试模:在模具装配完成后,需要进行调试和试模的工作。
通过调整模具的位置和结构,使其在使用过程中达到最佳的工作效果。
在试模过程中,需要使用一些样品或原料进行试模操作,以评估模具的功能和使用性能。
8. 模具加工完成后,还需要对模具进行保养和维护,以延长其使用寿命和性能。
对于长期使用的模具,还需要定期进行检修和维修工作,以恢复其正常的功能和精度。
模具加工工艺标准
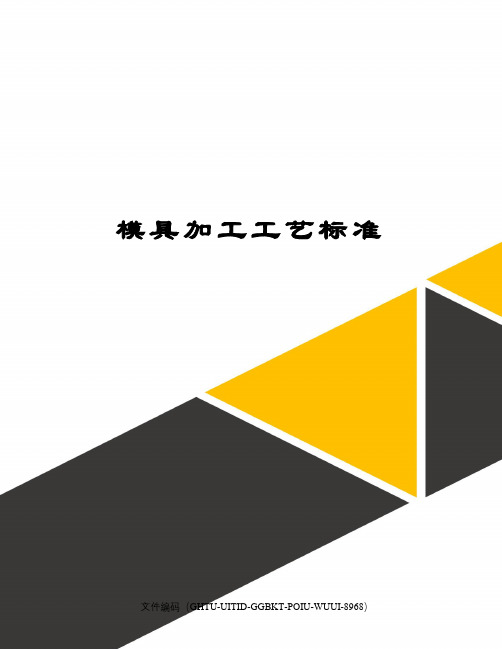
模具加工工艺标准文件编码(GHTU-UITID-GGBKT-POIU-WUUI-8968)模具加工工艺标准1.目的和适用范围为保证模具制作加工工艺的合理性、一致性,优化加工工艺,提高模具制作的进度,特制定本标准。
2.模具加工工艺标准工艺员编工艺卡时要在工艺卡中详细注明加工预留量、预留量的方位、粗糙度要求及注意事项。
加工工艺流程卡编写原则:在能保证精度、质量的前提下,优先采用加工效率高的设备。
铣床、CNC、磨床的加工效率比线切割、电脉冲要快,尤其是电脉冲加工效率最慢。
图纸上的尺寸不能随意更改(只有技术员能改),加工预留量原则:需要热处理加工的工件,热处理前外形备料尺寸单边加0.25mm的磨床余量,模仁、镶件需要CNC粗加工的部分,单边预留余量0.2mm,钳工铣床粗铣外形单边预留余量-0.5mm,线割后需要磨床加工的工件,成型部位单边预留0.05mm,外形开粗单边预留0.1mm的磨削余量; CNC精加工、电脉冲后要镜面抛光,单边留0.03mm的抛光余量。
加工精度要求:模具尺寸的制造精度应在~0.02mm范围内;垂直度要求在~0.02mm范围内;同轴度要求在~0.03mm范围内;动、定模分型面的上、下两平面的平行度要求在~0.03mm范围内。
合模后,分型面之间的间隙小于所成型塑料的溢边值。
其余模板配合面的平行度要求在~0.02mm范围内;固定部分的配合精度一般选用~0.02mm范围内;小芯子如果无对插要求或对尺寸影响不大可取双边~0.02mm的间隙配合;滑动部分的配合精度一般选用H7/e6、H7/f7、H7/g6三种。
注意:镜面上如有做了挂靠台阶的镶件,配合不能太紧,否则在镶件从正面往后退敲打时,用来敲打的工具易碰坏镜面,如不影响产品尺寸,可取双边~0.02mm的间隙配合。
CNC拆电极的原则:模具型腔型芯应先拆外观主体电极,再拆其他主体电极,最后拆局部电极;定模外观电极要考虑整体加工,对CNC清角不到的地方,采用线切割清角,以便定模外观面完整,无接痕;动模深度相差不大的加强筋、筋片、柱子能一起加工的尽量做在一个电极上;比较深的筋片要做镶件,要单独做电极侧打,以防电脉冲时积碳;动模电极尽量不要CNC铣好之后还要线切割清角,如要,应将电极分解拆开或直接采用线切割;动模的筋部和筋位或者柱子的间隔超过35mm,应当分开做,节约铜料。
模具零件加工工艺流程
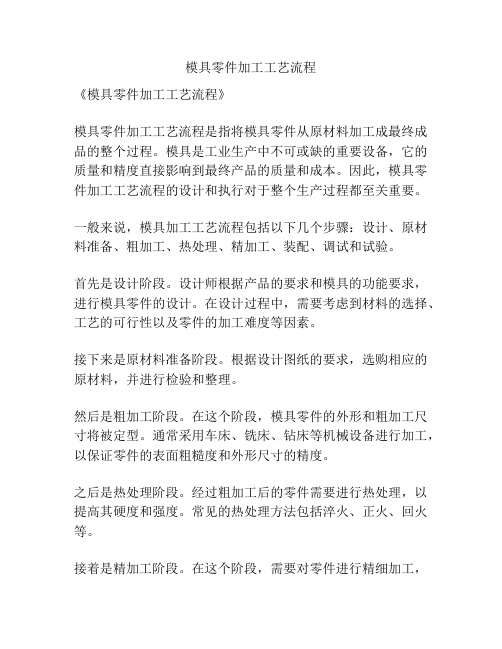
模具零件加工工艺流程《模具零件加工工艺流程》模具零件加工工艺流程是指将模具零件从原材料加工成最终成品的整个过程。
模具是工业生产中不可或缺的重要设备,它的质量和精度直接影响到最终产品的质量和成本。
因此,模具零件加工工艺流程的设计和执行对于整个生产过程都至关重要。
一般来说,模具加工工艺流程包括以下几个步骤:设计、原材料准备、粗加工、热处理、精加工、装配、调试和试验。
首先是设计阶段。
设计师根据产品的要求和模具的功能要求,进行模具零件的设计。
在设计过程中,需要考虑到材料的选择、工艺的可行性以及零件的加工难度等因素。
接下来是原材料准备阶段。
根据设计图纸的要求,选购相应的原材料,并进行检验和整理。
然后是粗加工阶段。
在这个阶段,模具零件的外形和粗加工尺寸将被定型。
通常采用车床、铣床、钻床等机械设备进行加工,以保证零件的表面粗糙度和外形尺寸的精度。
之后是热处理阶段。
经过粗加工后的零件需要进行热处理,以提高其硬度和强度。
常见的热处理方法包括淬火、正火、回火等。
接着是精加工阶段。
在这个阶段,需要对零件进行精细加工,以达到设计要求的形状和精度。
一般采用磨削、拉削、钻孔、铣削等工艺进行加工。
然后是装配阶段。
将经过精加工的各个零件组装到一起,形成一个完整的模具。
最后是调试和试验阶段。
经过装配的模具需要进行调试和试验,以验证其性能和精度是否符合设计要求。
总的来说,模具零件加工工艺流程是一个综合性的过程,需要设计、原材料准备、加工、装配、调试和试验等多个步骤有机地结合在一起,确保最终的模具零件能够满足产品的要求。
模具加工工艺标准

结构简单:模 具设计应尽量 简单、明了, 方便操作和维 护。
0
0
0
0
1
2
3
4
模具设计的工艺性分析
模具材料的选用:根据产品要求和生产条件选择合适的模具材料,确保模具的耐磨性、 耐腐蚀性和热稳定性。
模具结构的合理性:模具结构设计应简单、紧凑,便于制造、装配、调试和使用,同时 要充分考虑模具的强度和刚性。
热处理工艺流程:预热、加热、保温、冷却和后处理等步骤
热处理工艺参数:加热温度、保温时间、冷却速度等参数对热处理效果的影响
04
模具设计的工艺要求
模具设计的原则
符合产品要求: 模具设计应满 足产品形状、 尺寸和性能的 要求。
加工方便:模 具设计应便于 制造、装配、 检测和维修, 降低制造成本。
寿命长:模具 设计应保证模 具的使用寿命, 提高模具的可 靠性和稳定性。
根据模具材料选择合适的刀 具类型和刀片材质
考虑刀具的寿命和耐用度, 合理使用刀具补偿功能
掌握刀具的安装与拆卸方法, 确保安全操作
切削参数的优化
切削速度:根据材料和刀具选 择合适的切削速度,以提高加 工效率和降低表面粗糙度。
进给量:适当调整进给量可以 提高切削效率,同时保证加工 质量。
切削深度:合理选择切削深度 可以减少刀具磨损和加工时间, 提高加工精度。
模具加工的重要性
模具加工的精度和稳定性直 接关系到产品的质量和生产 效率,是实现产品批量生产 的关键因素。
模具加工是制造业的重要环节, 对产品生产的质量和效率具有 决ቤተ መጻሕፍቲ ባይዱ性影响。
模具加工技术的发展和应用, 能够推动制造业的技术进步 和产业升级,提高生产效率
和产品质量。
标准模具 外发加工品质要求及工艺标准
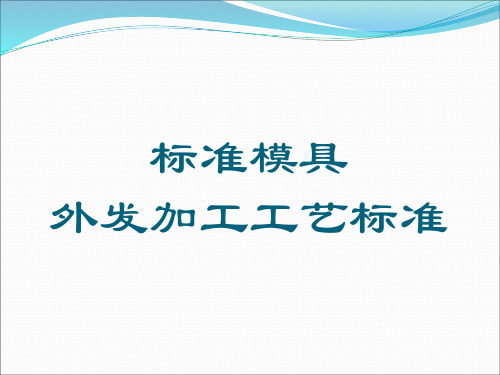
工件取数基准
任何镶件(包括排位镶件),都必 须在2D图上有取数基准的明显标 识,以免各工序使用不同的边取数
第一部分
第二部分
工件取数标准
工件防变形
工件防变形
在加工大型工件时需要严格按我们提供的加工工艺来加工, 1。 先粗加工正面留余量,下机冷却24小时以上,有些工件甚至 需要更长时间来释放工件的加工时产生的应力,在冷却完成 后,需要检查工件是否变形,工件周边是否直角(如下图)
提醒:
在加工的时候,一定要认真仔细的去看我们提供的 2D图纸上所标注的取数要求,不要报着一个我以为 就是这样取数加工的,以这样的心态去做事,十次 就会有九次出错
工件防变形
2。 对于又细又高的工件,顶部订料时订高35mm左右,NC开粗 时底面和顶面都留脚仔,既方便NC加工,又可防工件变形。 光刀时最后光顶面,光顶面之前先将顶部脚仔用快走丝割掉。 (注:开粗时要多留些余量)
工件防变形
3。 对于较大的中间为通槽的推方,开粗时内圈要适当多留些余 量,以防淬火后变形。
工件取数基准
5。 工件一个方向,但不在工件中心,实际工件需要在 单边取数加工(如图)
下面图片工件外形尺寸是207*207*86,工件XY方向是碰单边取 数再为“0”很多时候大家都会直接四面分中加工,造成偏位
工件取数基准
碰数边的高度设计5mm以上
标准模具 外发加工工艺标准
第一部分
工件取数标准
第二部分
工件防变形
工件取数基准 1。下面基准标示是不能做取数依据的
此位是模具基准角,不能做取数基准
工件取数基准 2。工件单边取数
单边取数基准“0”位
工件取数基准 3。工件单边取数,取数边不在工件最大边, 需要碰边移进去为“0”
模具加工流程中工艺标准及要求【详尽版】
模具加工流程中工艺标准及要求【详尽版】内容来源网络,由“深圳机械展(11万㎡,1100多家展商,超10万观众)”收集整理!更多cnc加工中心、车铣磨钻床、线切割、数控刀具工具、工业机器人、非标自动化、数字化无人工厂、精密测量、数控系统、3D打印、激光切割、钣金冲压折弯、精密零件加工等展示,就在深圳机械展一、范围:本标准规定了注塑模具的加工标准和要求。
二、引用标准:《模具设计标准》《一般模具设计参照标准》《热嘴设计标准》《模具设计规范》三、模具外观:1.铭牌内容打印模具编号、模具重量(Kg)、模具外形尺寸(mm),字符均用1/4英寸的字码打上,字符清晰、排列整齐,铭牌厚度1mm铝片。
2.铭牌固定在模腿上靠近后模板和基准角的地方(离两边各有15mm的距离),用四个柳钉固定,固定可靠,不易剥落。
3.冷却水嘴用塑料块插水嘴Ф10管,规格可为G1/8″、G1/4″、G3/8″。
如合同有特殊要求,按合同。
4.冷却水嘴原则上不伸出模架表面(客户另有要求除外),水嘴头部凹进外表面不超过3mm。
5.冷却水嘴避空孔直径为Ф25×30、Ф30×30、Ф35×30三种规格,孔外沿有倒角,倒角大于1.5×45,倒角一致。
6.冷却水嘴有进出标记,进水为IN,出水为OUT,IN、OUT后加顺序号,如:IN01、02,OUT01、02,要求用8~12mm字码打上。
7.进出油嘴、进出气嘴在IN、OUT前空一个字符加G(气)、O(油),字码相同。
8.模具安装柱下方有支撑腿加以保护。
9.模架上各模板有基准符号,大写英文DATUM,字高5/16″,位置在离边10mm处,字迹清晰、美观、整齐、间距均匀(或按模架厂统一)。
10.各模板有零件编号,编号在基准角符号正下方离底面10mm处,要求同9号,模号打在基准角的对边。
11.模具配件影响模具的吊装和存放,如安装时下方有外漏的油缸、水嘴、先复位机构等,应有支撑腿保护(同8号)。
标准模具模肉加工工艺标准
14、藏哥位R角避空工艺
周围R角:离开R边5—10mm, 避空0.5mm再倒R
避空0.5mm
模肉加工要求(排气加工标准)
模肉加工要求(排气加工标准) 一.平面大排气:(用专用排气刀加工)
模肉加工要求(排气加工标准) 二.曲面大排气:(用球刀加工)
用球刀加大曲 面排气,提高模 具表面光洁度
检测镶件槽 及圆孔直径
在封型面及碰 穿面做试刀程式
检测方法:下机前必须装配面相 应位置做试刀程式,要保证测试 符合,镶件槽检测应用标准塞件. 较表.分中棒等工具测量与图纸 相符,圆孔检测应用标准圆柱紧 配,编程师要在程式单上标识相 关有需检测数据.
图档优化及加工要求(如何优化图档)
当分型面为曲面时,排气槽必须 设计为“U”型,直接用球刀加工。
分型面为曲面,排气不可以设计为方 槽没法加工刀位,模具表面不美观.
5、落位加工方法
落位周围都有倒角,但底部经常起级. 解决方案:编程师做一条独立程式,底部 优先光一刀,并注明可低于平面0.02mm
封胶口必须要用新刀加工
模肉加工要求(封胶口外锣避空标准)
四、分型面要锣避空0.05~0.1mm
锣避空面不要用新刀加工
模肉加工要求(封胶口精加工标准) • 三.结合工件形状:
封胶口请新 刀光刀
注:所有光刀一定要 测量刀具
模肉加工要求(封胶口外锣避空标准)
四、分型面要锣避空0.05~0.1mm
模肉加工要求(排气加工标准) 四.平面小排气:
模肉加工要求(排气加工标准) 三.平面小排气:
模肉加工要求(排气加工标准) 五.曲面小排气(编程时必须独立程式加工)
模肉加工要求(排气加工标准) 三.曲面小排气:
模具加工工艺及流程
模具加工工艺及流程模具加工工艺及流程模具加工是指设计、制作、组装、加工、试模等一系列工序,最终得到能够生产出理想产品的模具。
模具是现代工业生产过程中不可缺少的生产工具,因此模具加工技术的发展对于提高生产效率、降低成本、保证产品质量等方面都具有重要作用。
下面将介绍模具加工的工艺及流程。
一、设计模具制作的第一步是根据产品的要求进行模具设计。
设计人员需要结合产品的形态特征、使用要求、生产工艺等因素进行综合分析和考虑,制定出合理的模具结构。
设计注意事项:1.要按照零件原理、标准规范进行设计。
2.设计前要对所需材料进行详细的了解和分析,选择合适的材料。
3.在设计过程中要注意加工和使用的方便性,以提高加工效率和降低失败率。
4.设计完成后要结合实际情况仔细斟酌,进行模具设计优化和改进。
二、制模制模是模具加工的主要环节之一,它的精准度和成功率直接关系到整个加工过程的成败。
制模工序包含模具主体加工、零部件加工、元件制作、组装调试等环节。
1. 模具主体加工:模具主体是模具的主体结构,包含了模腔壳体、模心、导柱等。
在模具设计合格后,需要进行主体加工。
2. 零部件加工:零部件主要包括模具底板、卡板、顶板、定位销等,这些零部件需要与主体进行组合而形成完整的模具。
零件加工过程中需要注重加工精度。
3. 元件制作:元件主要包括弹簧、卡簧、顶针、定位圈等,这些元件起到了对模具加工过程中防止伤害和保护作用。
4. 组装调试:在模具中应用到的零件必须进行预装和调试,避免出现安装过程中的不匹配问题,确保模具的高效运行。
三、加工精度控制对模具加工的加工精度进行控制非常重要。
通过引入计算机数控加工技术能够实现更精确的加工精度,提高了模具生产的效率和精度。
加工精度控制主要包括以下几个方面:1. 高精度加工设备的选择和应用:数控机床、电火花加工机、线切割加工机等具有较高加工精度,能够保证模具的高精度加工。
2. 加工刀具的选择:高精度加工刀具精度高,寿命长,性能稳定可靠。
模具加工工艺流程
模具加工工艺流程
模具加工工艺流程
一、总体安排
在模具加工工艺流程中,应根据模具设计要求进行材料选择、制备和焊接,模具由设计、机加工、抛光、喷涂及装配组装等环节构成,具体工艺流程如下:
二、材料切割、制备
1、制作模具图样:首先,根据产品图纸要求对模具进行设计,完善技术要求及制作工艺细节,编制模具图样;
2、切割材料:根据模具图样的要求,将工件零件材料切割成所需尺寸;
3、检查切割尺寸:切割完成后需要进行尺寸检查,检查合格后方可进行下一步工序,不合格的材料需要重新切割;
4、机加工:根据材料尺寸要求,进行工件零件的机加工,保证工件零件在加工后的精度。
三、焊接、装配
1、焊接:在焊接前,要进行焊接工艺设计、焊接工具的熔接模型选择以及焊接操作的准备,焊接要求熔接接口部位的焊痕不得超出规定尺寸和要求,熔接接头自然变形要求不超过规定值;
2、装配:完成焊接后,要对焊接接头进行磨光,清理表面杂质、检查尺寸等;之后将所有模具零件装配成完整的模具,安装各个零部件;
3、抛光、喷涂:安装完毕后,要进行抛光和喷涂;抛光要求所有表面完美无缺,处理后的模具表面光滑平整,以满足微抛光和美观的要求;喷涂要求可耐磨拉伸、腐蚀等负荷。
四、模具装配
1、模具模板:模具模板主要由护板、槽洞模板、锁模件等组成,它们在模具开模过程中起着重要作用。
2、模具模块:模具模块是模具的核心部分,它包括凸出部件、分离部件、弹性部件等,用以把工件零件设计成产品图形;
3、模具模座:模具模座用以固定模具模型,是模具的重要部分,一般由底座、支撑等组成。
五、模具检测
在模具加工完成后,需要对其进行合格检验,涉及的检测项目有尺寸精度、表面质量检测、尺寸公差等,确保模具加工工艺及质量达到要求。
- 1、下载文档前请自行甄别文档内容的完整性,平台不提供额外的编辑、内容补充、找答案等附加服务。
- 2、"仅部分预览"的文档,不可在线预览部分如存在完整性等问题,可反馈申请退款(可完整预览的文档不适用该条件!)。
- 3、如文档侵犯您的权益,请联系客服反馈,我们会尽快为您处理(人工客服工作时间:9:00-18:30)。
标准零件加工工艺1、目的:
有效地控制异常,提高效率,提高品质。
2、范围:
适用标准零件的加工。
3、职责:
无
4、定义:
无
5、内容:
5.1 油板(耐磨板):(如图)
5.1.1工艺路线:铣床组→磨床组→锯床→铣床组→磨床组→铣床组→热处理→磨床组
→铣床组→品检;
5.1.2 铣床加工零件长宽方向的正四面体,单边留余量0.5mm;
5.1.3 磨床见光零件长宽方向的正四面体,加工直角后送铣床;
5.1.4 锯床加工零件Z方向的厚度,留余量1mm-2mm;
5.1.5 铣床用飞刀加工零件Z方向的厚度,留余量0.5mm-0.6mm;
5.1.6 送磨床加工Z方向的平面,留余量0.3mm-0.4mm;
5.1.7 铣床加工平头螺丝扩孔及杯头;
5.1.8 铣床倒角,去毛刺后送品检检测;
5.1.9 送热处理加硬,硬度 52℃±2°;
5.1.10 磨床精磨至图纸尺寸;
5.1.11 铣床加工油槽;
5.1.12 送品检检测;
5.2 压块(斜顶座耐磨板);
5.2.1工艺路线:铣床组→磨床组→锯床→铣床组→磨床组→铣床组→品管组→热处理
→磨床组→铣床组→品检
5.2.2 铣床加工零件长宽方向的正四面体,单边留余量0.5mm;
5.2.3 磨床见光零件长宽方向的正四面体,加工直角后送铣床;
5.2.4 锯床加工零件Z方向的厚度,留余量1mm-2mm;
5.2.5 铣床用飞刀加工零件Z方向的厚度,留余量0.5mm-0.6mm;
5.2.6 送磨床加工Z方向的平面,留余量0.3mm-0.4mm;
5.2.7 铣床加工螺丝底孔,并倒角攻牙;
5.2.8 品检检测后送热处理,HRC52℃±2°;
5.2.9 磨床精磨至图纸要求尺寸;
5.2.10 铣床加工油槽;
5.2.11送品检检测;
5.3 斜顶座:
5.3.1工艺路线:磨床→铣床→磨床组→线切割→品检
5.3.2 磨床开料Z、宽方向的正四面体并精磨到图纸要求尺寸;
5.3.3 铣床开粗T形台阶,A、B尺寸留余量0.15mm-0.25mm;
5.3.4 磨床精磨T形台阶B尺寸,尺寸公差为±0.01mm;
5.3.5 磨床精磨A尺寸,尺寸公差为±0.02mm;
5.3.6 送慢走丝加工长方向的尺寸及导向槽,导向槽尺寸公差要求+0.015mm至+0.01mm;
5.3.7 送品检检测;
5.4 运输板:
5.4.1工艺路线:铣床组→磨床组→锯床→铣床组→磨床组→品检;
5.4.2 铣床开粗长宽方向的正四面体,长宽尺寸留余量0.4mm-0.5mm;
5.4.3 磨床加工长宽尺寸至要求尺寸,公差为±0.5mm;
5.4.4 送锯床加工Z方向的厚度,留余量1mm-1.5mm;
5.4.5 铣床加工Z方向的厚度,留余量0.3mm-0.4mm;
5.4.6 铣床加工螺丝扩孔和螺丝槽公差标准为-0.3mm至+0.1mm;
5.4.7 铣床倒C角;
5.4.8 送磨床精磨至图纸尺寸公差标准为±0.5mm;
5.4.9 送品检检测;
5.5 压线板:
5.5.1工艺路线:铣床组→磨床组→锯床→铣床组→磨床组→品管
5.5.2 铣床开粗长宽方向的正四面体,长宽尺寸留余量0.4mm-0.5mm;
5.5.3 磨床加工长宽尺寸至要求尺寸,公差为±0.5mm;
5.5.4 送锯床加工Z方向的厚度,留余量1mm-1.5mm;
5.5.5 铣床加工Z方向的厚度,留余量0.3mm-0.4mm;
5.5.6 铣床加工平头螺丝扩孔和平头螺丝杯头;
5.5.7 铣床倒C角;
5.5.8 送磨床精磨至图纸尺寸公差标准为±0.5mm;
5.5.9 送品检检测;
5.6 摆杆:
5.6.1工艺路线:铣床组→磨床组→锯床→铣床组→磨床组→铣床组→品检
5.6.2 铣床加工长宽方向的正四面体,留余量0.4mm-0.5mm;
5.6.3 磨床加工至图纸尺寸,公差为长宽方向+0.03mm至+0.05mm;
5.6.4 锯床锯Z方向的厚度,留余量1mm-1.5mm,;
5.6.5 铣床加工Z方向的厚度,留余量0.3mm,并加工A尺寸,留余量0.2mm;
5.6.6 磨床精磨Z方向和A尺寸的厚度至图纸尺寸,公差±0.1mm;
5.6.7 铣床加工螺丝扩孔和螺丝杯头孔;
5.6.8 铣床用分度转盘加工图示R位置;
5.6.9 铣床将各部位倒角;
5.6.10送品检检测;
5.7 击杆导正块:
5.7.1工艺路线:铣床组→磨床组→锯床→铣床组→磨床组→铣床组→品检
5.7.2 铣床开粗长宽方向的正四面体,留余量0.3mm-0.5mm;
5.7.3 磨床加工长宽方向的尺寸至图纸尺寸,公差为+0.00mm至+0.03mm;
5.7.4 锯床加工Z方向的厚度,留余量1mm至1.5mm;
5.7.5 铣床加工Z方向尺寸及A、B尺寸,留余量0.3mm;
5.7.6 铣床钻螺丝扩孔及螺丝杯头孔后加工斜面至图纸要求尺寸;
5.7.7 磨床加工Z方向尺寸及A尺寸,公差为±0.2mm,磨床精磨B尺寸,公差为±0.02mm;
5.7.8 铣床倒角;
5.7.9 送品检检测;
5.8 急回击杆;
5.8.1工艺路线;铣床组→磨床组→品检
5.8.2 铣床领精料;
5.8.3 铣床组钻螺丝扩孔及销钉孔并倒角;
5.8.4 铣床加工斜面至图纸尺寸,公差±0.2mm;
5.8.5 铣床倒角后送磨床;
5.8.6 磨床精磨宽尺寸,公差为±0.02mm;
5.8.7 送品检检测;
5.9 行位座
5.9.1工艺路线:铣床组→磨床组→锯床→铣床组→磨床组→铣床组→磨床组→品检
5.9.2 铣床领精料并加工T槽各部位尺寸,留余量0.3mm;
5.9.3 磨床精磨T槽各位尺寸,公差见公差标准;
5.9.4 锯床切断长方向的尺寸,留余量1mm-1.5mm;
5.9.5 铣床加工长度尺寸,留余量0.3mm-0.5mm;
5.9.6 磨床精磨长度尺寸,公差±0.1mm;
5.9.7 送铣床加工斜面、斜孔及镶件挂台槽,斜面留余量0.5mm-0.6mm,斜孔公差为
+0.2mm至0.5mm,镶件挂台槽留余量0.2mm-0.3mm;
5.9.8 磨床精磨斜面,留余量0.3mm,精磨镶件挂台槽,公差见公差标准;
5.9.9 送品检检测;
5.10 铲基:
5.10.1工艺路线:铣床组→磨床组→锯床→铣床组→磨床组→铣床组→磨床组→品检
5.10.2 铣床领精料;
5.10.3 铣床加工A及螺丝孔,A尺寸留余量0.3mm-0.5mm;
5.10.4 送磨床精磨A尺寸,公差为+0mm至+0.02mm;
5.10.5 锯床切断长度方向尺寸,留余量1mm-1.5mm;
5.10.6 铣床加工长度方向尺寸,留余量0.2mm-0.4mm;
5.10.7 磨床精磨长度尺寸,公差为-0.1mm至-0.3mm;
5.10.8 铣床粗加工斜面,留余量0.3mm;
5.10.9 磨床精磨斜面,留余量0.15mm钳工Fit模;
5.10.10 送品检检测;
6、相关文件:
6.1 标准图纸;
7、相关表格:
7.1 «零件加工控制表»;
7.2 «零件\铜公交接表»。