客车蒙皮的成型及安装工艺
铝合金车身客车蒙皮接缝处理工艺方法研究
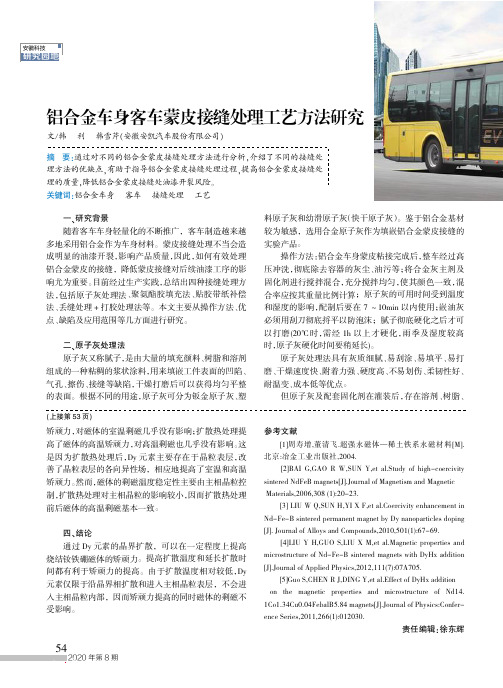
2020年第8期一、研究背景随着客车车身轻量化的不断推广,客车制造越来越多地采用铝合金作为车身材料。
蒙皮接缝处理不当会造成明显的油漆开裂,影响产品质量,因此,如何有效处理铝合金蒙皮的接缝,降低蒙皮接缝对后续油漆工序的影响尤为重要。
目前经过生产实践,总结出四种接缝处理方法,包括原子灰处理法、聚氨酯胶填充法、贴胶带纸补偿法、丢缝处理+打胶处理法等。
本文主要从操作方法、优点、缺陷及应用范围等几方面进行研究。
二、原子灰处理法原子灰又称腻子,是由大量的填充颜料、树脂和溶剂组成的一种粘稠的浆状涂料,用来填嵌工件表面的凹陷、气孔、擦伤、接缝等缺陷,干燥打磨后可以获得均匀平整的表面。
根据不同的用途,原子灰可分为钣金原子灰、塑料原子灰和幼滑原子灰(快干原子灰)。
鉴于铝合金基材较为敏感,选用合金原子灰作为填嵌铝合金蒙皮接缝的实验产品。
操作方法:铝合金车身蒙皮粘接完成后,整车经过高压冲洗,彻底除去容器的灰尘、油污等;将合金灰主剂及固化剂进行搅拌混合,充分搅拌均匀,使其颜色一致,混合率应按其重量比例计算;原子灰的可用时间受到温度和湿度的影响,配制后要在7~10min 以内使用;嵌油灰必须用刮刀彻底捋平以防泡沫;腻子彻底硬化之后才可以打磨(20℃时,需经1h 以上才硬化,雨季及湿度较高时,原子灰硬化时间要稍延长)。
原子灰处理法具有灰质细腻、易刮涂、易填平、易打磨、干燥速度快、附着力强、硬度高、不易划伤、柔韧性好、耐温变、成本低等优点。
但原子灰及配套固化剂在灌装后,存在溶剂、树脂、矫顽力,对磁体的室温剩磁几乎没有影响;扩散热处理提高了磁体的高温矫顽力,对高温剩磁也几乎没有影响。
这是因为扩散热处理后,Dy 元素主要存在于晶粒表层,改善了晶粒表层的各向异性场,相应地提高了室温和高温矫顽力。
然而,磁体的剩磁温度稳定性主要由主相晶粒控制,扩散热处理对主相晶粒的影响较小,因而扩散热处理前后磁体的高温剩磁基本一致。
四、结论通过Dy 元素的晶界扩散,可以在一定程度上提高烧结钕铁硼磁体的矫顽力。
客车蒙皮的成型及安装工艺
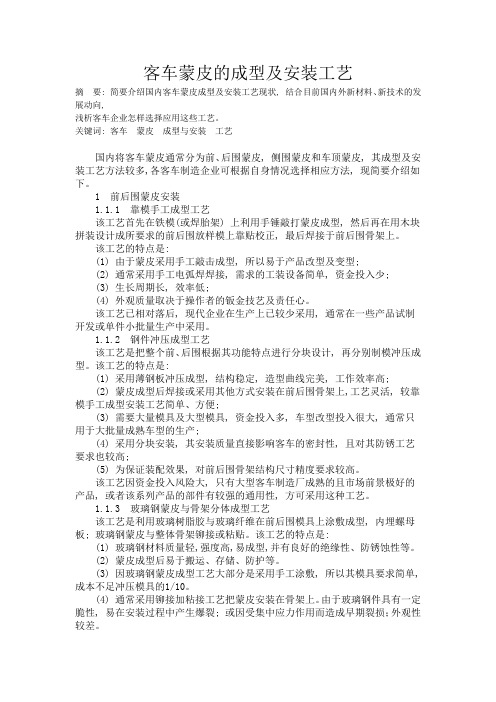
客车蒙皮的成型及安装工艺摘要: 简要介绍国内客车蒙皮成型及安装工艺现状, 结合目前国内外新材料、新技术的发展动向,浅析客车企业怎样选择应用这些工艺。
关键词: 客车蒙皮成型与安装工艺国内将客车蒙皮通常分为前、后围蒙皮, 侧围蒙皮和车顶蒙皮, 其成型及安装工艺方法较多,各客车制造企业可根据自身情况选择相应方法, 现简要介绍如下。
1前后围蒙皮安装1.1.1靠模手工成型工艺该工艺首先在铁模(或焊胎架) 上利用手锤敲打蒙皮成型, 然后再在用木块拼装设计成所要求的前后围放样模上靠贴校正, 最后焊接于前后围骨架上。
该工艺的特点是:(1) 由于蒙皮采用手工敲击成型, 所以易于产品改型及变型;(2) 通常采用手工电弧焊焊接, 需求的工装设备简单, 资金投入少;(3) 生长周期长, 效率低;(4) 外观质量取决于操作者的钣金技艺及责任心。
该工艺已相对落后, 现代企业在生产上已较少采用, 通常在一些产品试制开发或单件小批量生产中采用。
1.1.2钢件冲压成型工艺该工艺是把整个前、后围根据其功能特点进行分块设计, 再分别制模冲压成型。
该工艺的特点是:(1) 采用薄钢板冲压成型, 结构稳定, 造型曲线完美, 工作效率高;(2) 蒙皮成型后焊接或采用其他方式安装在前后围骨架上,工艺灵活, 较靠模手工成型安装工艺简单、方便;(3) 需要大量模具及大型模具, 资金投入多, 车型改型投入很大, 通常只用于大批量成熟车型的生产;(4) 采用分块安装, 其安装质量直接影响客车的密封性, 且对其防锈工艺要求也较高;(5) 为保证装配效果, 对前后围骨架结构尺寸精度要求较高。
该工艺因资金投入风险大, 只有大型客车制造厂成熟的且市场前景极好的产品, 或者该系列产品的部件有较强的通用性, 方可采用这种工艺。
1.1.3玻璃钢蒙皮与骨架分体成型工艺该工艺是利用玻璃树脂胶与玻璃纤维在前后围模具上涂敷成型, 内埋螺母板; 玻璃钢蒙皮与整体骨架铆接或粘贴。
大客车车身蒙皮及骨架检测修复要点分析

大客车车身蒙皮及骨架检测修复要点分析作者:赵扬来源:《中国新技术新产品》2016年第08期摘要:大客车是我国交通事业发展的重要工具,其在城市公共交通、城际间的交通等方面发挥着巨大的作用。
我国的大客车制造业自21世纪以来就步入了飞速发展期,已经形成了一整套的大客车整车制造、维修的完整体系,现今,各地都有我国自主设计、制造的大客车在运行。
大客车蒙皮是车辆中的重要组成部分,做好大客车蒙皮的制造、维修能够给大客车提供良好的外观和相应的保护。
本文将在分析大客车蒙皮外伤特点的基础上对如何做好大客车蒙皮与车辆骨架的修复进行分析阐述。
关键词:大客车;蒙皮;骨架;修复中图分类号:U463 文献标识码:A大客车蒙皮是大客车重要的围挡,其为大客车提供良好的外观和一定的防护。
大客车在使用的过程中难免会造成磕碰,从而造成大客车蒙皮出现损坏,通过对大客车蒙皮进行更换、修复在提升大客车外观美观的基础上确保大客车的防护性。
1 大客车外蒙皮局部修复要点大客车外蒙皮在使用的过程中正常出现的损伤多以裂纹、锈蚀等的现象为主。
做好大客车外蒙皮的修复主要以大客车蒙皮整型为主、制作为辅,通过对大客车外蒙皮进行修复,需要使得大客车外蒙皮的修复处与大客车原来型态相一致并做好对于修复处周边的搭配,在大客车外蒙皮修复的过程中要做到造型正确、线条分明、缝隙合理,确保大客车外蒙皮的修复质量。
对于大客车外蒙皮所出现的问题可以采取以下的修复措施:(1)对于大客车金属外蒙皮裂纹的修复可以使用CO2气体保护焊来进行焊接修复,而对于一些空间狭小且裂纹受力较大的部位,为提高焊接质量和焊接效果可以采用两面焊的焊接方法来进行处理,完成焊接后需要在焊缝的内侧使用铁垫进行垫衬并使用手锤等尖锐工具在金属蒙皮外焊缝的周边进行轻敲来去除焊缝所产生的残余应力,而后在使用锉刀、角磨机等工具打磨焊缝直至平整,完成喷漆即可。
(2)对于蒙皮局部锈蚀、损坏较为严重的部位,仅仅通过焊缝修复无法完成时,可以通过采用挖补或是贴补的方法来对金属蒙皮进行修复,如破损面积较大修复较为困难时则可以考虑直接更换整块蒙皮,提高修复的效率和降低成本。
浅谈对客车蒙皮技术的研究
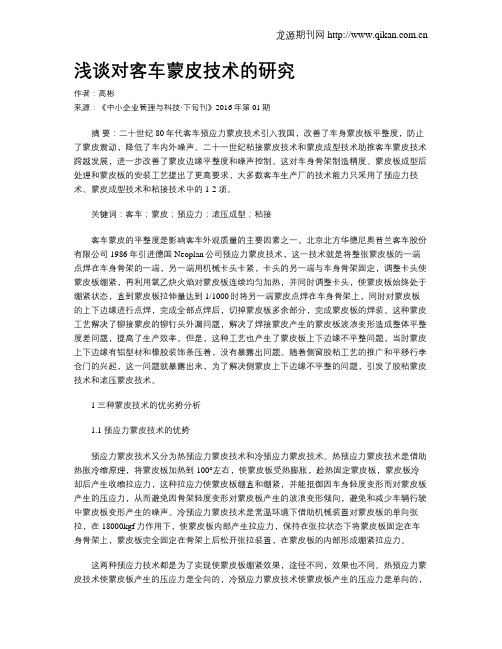
浅谈对客车蒙皮技术的研究作者:高彬来源:《中小企业管理与科技·下旬刊》2016年第01期摘要:二十世纪80年代客车预应力蒙皮技术引入我国,改善了车身蒙皮板平整度,防止了蒙皮震动,降低了车内外噪声。
二十一世纪粘接蒙皮技术和蒙皮成型技术助推客车蒙皮技术跨越发展,进一步改善了蒙皮边缘平整度和噪声控制。
这对车身骨架制造精度、蒙皮板成型后处理和蒙皮板的安装工艺提出了更高要求,大多数客车生产厂的技术能力只采用了预应力技术、蒙皮成型技术和粘接技术中的1-2项。
关键词:客车;蒙皮;预应力;滚压成型;粘接客车蒙皮的平整度是影响客车外观质量的主要因素之一,北京北方华德尼奥普兰客车股份有限公司1986年引进德国Neoplan公司预应力蒙皮技术,这一技术就是将整张蒙皮板的一端点焊在车身骨架的一端,另一端用机械卡头卡紧,卡头的另一端与车身骨架固定,调整卡头使蒙皮板绷紧,再利用氧乙炔火焰对蒙皮板连续均匀加热,并同时调整卡头,使蒙皮板始终处于绷紧状态,直到蒙皮板拉伸量达到1/1000时将另一端蒙皮点焊在车身骨架上,同时对蒙皮板的上下边缘进行点焊,完成全部点焊后,切掉蒙皮板多余部分,完成蒙皮板的焊装。
这种蒙皮工艺解决了铆接蒙皮的铆钉头外漏问题,解决了焊接蒙皮产生的蒙皮板波浪变形造成整体平整度差问题,提高了生产效率。
但是,这种工艺也产生了蒙皮板上下边缘不平整问题,当时蒙皮上下边缘有铝型材和橡胶装饰条压着,没有暴露出问题。
随着侧窗胶粘工艺的推广和平移行李仓门的兴起,这一问题就暴露出来,为了解决侧蒙皮上下边缘不平整的问题,引发了胶粘蒙皮技术和滚压蒙皮技术。
1 三种蒙皮技术的优劣势分析1.1 预应力蒙皮技术的优势预应力蒙皮技术又分为热预应力蒙皮技术和冷预应力蒙皮技术。
热预应力蒙皮技术是借助热胀冷缩原理,将蒙皮板加热到100°左右,使蒙皮板受热膨胀,趁热固定蒙皮板,蒙皮板冷却后产生收缩拉应力,这种拉应力使蒙皮板绷直和绷紧,并能抵御因车身轻度变形而对蒙皮板产生的压应力,从而避免因骨架轻度变形对蒙皮板产生的波浪变形倾向,避免和减少车辆行驶中蒙皮板变形产生的噪声。
汽车内饰蒙皮加工工艺

汽車內裝件的蒙皮加工法所謂蒙皮加工法是在汽車內裝件成形後,用其他工藝對最外層表面進行裝飾。
用這種方法可以對形狀複雜的汽車內裝件,實施高品位裝飾。
這幾年歐美和日本的著名汽車製造公司,廣泛應用以下各種蒙皮方法裝飾汽車內裝件。
熔融粉末裝飾法儘管這種方法在汽車行業中很早已經應用,因裝飾技術不斷改進而仍具有使用價值。
現在有許多高級轎車仍在用這種方法裝飾內裝件。
最新的技術是「雙熔融法」。
開發這種新技術的目的是為了改善內裝件的觸覺,以及減輕蒙皮的重量。
在用這種方法形成的裝飾層下面,是發泡PVC粉末的發泡體層。
它可以防止作為基體材料PUR發泡體向四處飛散。
除此之外該層還具有隔熱作用。
成形方法是將兩種不同性質的熔融粉末層,在一道工序中附著在處於高溫狀態的特殊模具型腔表面。
注射成形後即成為零部件的裝飾層。
這種裝飾層除了具有上述特點外,還可以使乘員的安全氣囊在-40℃條件下運作。
例如Audi A2型汽車內裝件的基體材料,是充填玻璃纖維的熱塑性注射材料。
在基體材料外面是半硬質發泡體,以及作為中間層的PVC發泡體。
最外面則是固體PVC 裝置層。
熱真空裝飾法這種裝飾方法是使PVC板在真空條件下發生熱變形,按照預先製作的模型形成可以對內裝件進行裝飾的殼體。
如果加熱PVC板按凸出形狀的陽模表面變形,稱為陽模正壓法。
反之加熱PVC板在真空條件下被吸附在凹入形狀的陰模表面,稱為陰模負壓法。
用正壓法裝飾的內裝件,耐擦刮性能較差。
用負壓法裝飾內裝件在-40℃溫度條件下也不會飛散,所以特別適合用於對車內氣囊覆蓋板進行裝飾。
PUR噴塗法這種方法的特點是,用單層就可以滿足使用要求。
現在賓士和大眾汽車公司的很多內裝件是用這種方法裝飾。
最近又開發了廣受用戶青睞的直接後發泡工藝。
這是在噴塗結束後,由第二機器人控制PUR 混合頭與半硬質發泡體相結合,可進一步提高內裝件的質量。
除了上面介紹的裝飾方法以外,還有PUR鑄造蒙皮、PUR反應注射、吹塑成形和雙蒙皮成形等方法,也都廣泛用於裝飾現代汽車的內裝件。
汽车内饰蒙皮加工工艺
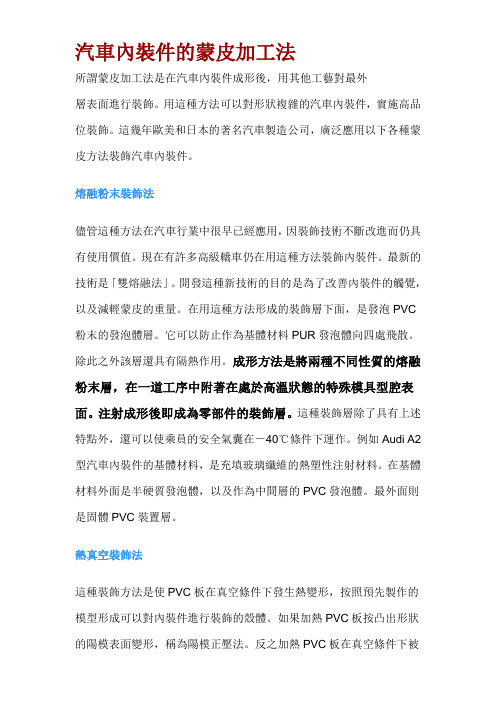
汽車內裝件的蒙皮加工法所謂蒙皮加工法是在汽車內裝件成形後,用其他工藝對最外層表面進行裝飾。
用這種方法可以對形狀複雜的汽車內裝件,實施高品位裝飾。
這幾年歐美和日本的著名汽車製造公司,廣泛應用以下各種蒙皮方法裝飾汽車內裝件。
熔融粉末裝飾法儘管這種方法在汽車行業中很早已經應用,因裝飾技術不斷改進而仍具有使用價值。
現在有許多高級轎車仍在用這種方法裝飾內裝件。
最新的技術是「雙熔融法」。
開發這種新技術的目的是為了改善內裝件的觸覺,以及減輕蒙皮的重量。
在用這種方法形成的裝飾層下面,是發泡PVC 粉末的發泡體層。
它可以防止作為基體材料PUR發泡體向四處飛散。
除此之外該層還具有隔熱作用。
成形方法是將兩種不同性質的熔融粉末層,在一道工序中附著在處於高溫狀態的特殊模具型腔表面。
注射成形後即成為零部件的裝飾層。
這種裝飾層除了具有上述特點外,還可以使乘員的安全氣囊在-40℃條件下運作。
例如Audi A2型汽車內裝件的基體材料,是充填玻璃纖維的熱塑性注射材料。
在基體材料外面是半硬質發泡體,以及作為中間層的PVC發泡體。
最外面則是固體PVC裝置層。
熱真空裝飾法這種裝飾方法是使PVC板在真空條件下發生熱變形,按照預先製作的模型形成可以對內裝件進行裝飾的殼體。
如果加熱PVC板按凸出形狀的陽模表面變形,稱為陽模正壓法。
反之加熱PVC板在真空條件下被吸附在凹入形狀的陰模表面,稱為陰模負壓法。
用正壓法裝飾的內裝件,耐擦刮性能較差。
用負壓法裝飾內裝件在-40℃溫度條件下也不會飛散,所以特別適合用於對車內氣囊覆蓋板進行裝飾。
PUR噴塗法這種方法的特點是,用單層就可以滿足使用要求。
現在賓士和大眾汽車公司的很多內裝件是用這種方法裝飾。
最近又開發了廣受用戶青睞的直接後發泡工藝。
這是在噴塗結束後,由第二機器人控制PUR 混合頭與半硬質發泡體相結合,可進一步提高內裝件的質量。
除了上面介紹的裝飾方法以外,還有PUR鑄造蒙皮、PUR反應注射、吹塑成形和雙蒙皮成形等方法,也都廣泛用於裝飾現代汽車的內裝件。
大客车蒙皮胶接工艺

卫生间小蒙皮胶接工艺规程1.领料及清理a.蒙皮用( )牌号镀锌板,尺寸1.0×900-1200×C;b.首先由蒙皮工段测量卫生间骨架垂直度,并把此角度书面通知下料工段相关责任人。
当骨架垂直度未达标时,镀锌板必须按照卫生间骨架实际角度下料(包括15mm折边宽度),并且按照骨架实际角度折弯;cd.卫生间小蒙皮折边端用砂轮切割机在圆弧部分每50mm开口一处,此法并非必须;e.蒙皮折边后要放置在车身上试装,小蒙皮要与大边蒙皮边缘吻合。
间隙小于0.5mm。
f.卫生间中间部分骨架(图中阴影部分)应稍许内凹1-2mm,让蒙皮能绷紧在骨架框体上,中间不致凸起;g.蒙皮用开卷机下料,开卷机刀盘的紧固技术是保证蒙皮下料之后边缘无毛刺,飞边,波浪的关键所在,另外开卷机压紧轴必须压紧;蒙皮下料后要保持平直,不应出现弧形弯曲;2.准备a.检查卫生间骨架,高出部分榔头敲平,用水平尺检测骨架,两端立柱应高出中间骨架1-2mm;把即将与蒙皮焊接的骨架部位用砂轮机打磨,露出金属光泽。
但使用导电漆的部位可不打磨,前提是导电漆喷涂厚度不超过25μm,导电漆厚度过大,将严重影响焊点强度;b.用清洁的抹布沾取埃塞克斯04604清洗剂(实际使用的是Betaclean7010清洗剂)擦拭骨架即将打胶部位,另取一块干净的抹布随即擦去清洗剂;注:车体骨架事先用PSC-003华阳恩赛金属清洗剂除油,除油在专门密闭的工房里进行,有独立的柴油燃烧机热风烘烤设备,除油后立即热风烘干并喷涂导电漆25μm,导电漆应不流挂,漏喷,随后向骨架小孔中用气动喷枪喷入防锈油并用塑料塞塞住孔口;c.骨架刷底涂清洗剂干燥后,用洁净抹布或者刷子刷涂埃塞克斯5061或者5402底涂(实际使用的是betawipe1707A+1707B,两种涂料混合后用泡沫塑料刷涂);d.骨架打胶底涂刷涂完毕开始计时,30分钟后打埃塞克斯7120黑胶,实际使用的是美国陶氏化学公司出品的betamate7120黑胶,胶体宽度×高度为12×10mm,勿多打。
客车侧围蒙皮张拉工艺

客车侧围蒙皮张拉工艺采用二次张拉工艺1:采用1mm厚的镀锌钢板(我厂使用传统的冷轧钢板),其耐蚀性为普通钢板的1倍以上,具有很好的拉延、折弯、焊接等机械性能。
2:下料尺寸为12000*1000,在宽度尺寸上下料时,应该在两侧均匀剪去多余部分,以保证两侧的机械性能相同,张拉时方能均匀伸长。
3:对蒙皮进行第一次张拉,要求超过其屈服极限,产生塑性变形为止。
具体对蒙皮施加张拉力为:F=195N/mm^2*1000mm^2=1.95*10^5N蒙皮伸长量为:弹性变形(195MPa/200GPa=0.1%+塑性变形0.2%(Q195在屈服强度(195MPa)下产生的塑性变形为0.2%)=0.3%12000*0.3%=36mm.由于厂里张拉机显示应力不准确,不能从压力表上读出实际张拉应力.第一次预张拉优点:(1)、由于金属在刚超过屈服变形时,产生不均匀屈服塑性变形,因而易使低碳钢冲压件边面产生皱*现象,所以在超过其屈服伸长两下预拉一次,可消除屈服现象,保证工件表面平整光洁。
(2)、在金属伸长过程中,当外力超过屈服强度之后,金属开始产生一种阻止继续塑性变形的抗力,就是应变硬化性能(形变强化)。
1)可使金属具有一定的抗偶然过载能力;2)和塑性变形适当配合可使金属进行均匀塑性变形。
所以应变硬化可以使蒙皮屈服极限得到提高,增强了抵抗变形的能力,而蒙皮硬化可以增加车身的整体刚度,提高整车的安全性能,同时可提高蒙皮的固有频率,有效降低蒙皮在行驶中产生的噪音。
4、蒙皮滚边加工,止口高度12mm,深度10mm,滚边同时在止口处打上塞焊孔,孔直径不大于6mm,间距为50mm。
5、蒙皮二次张拉:将蒙皮拉长其总长度的0.1%,在蒙皮绷紧状态下焊接。
由于蒙皮经过第一次预张拉,其屈服极限得到提高,大于其屈服强度195MPa,所以将蒙皮拉伸0.1%,蒙皮发生的是弹性变形,应力去除,则变形可完全消失。
可显著提高蒙皮张紧度,使蒙皮表面光滑平整。
- 1、下载文档前请自行甄别文档内容的完整性,平台不提供额外的编辑、内容补充、找答案等附加服务。
- 2、"仅部分预览"的文档,不可在线预览部分如存在完整性等问题,可反馈申请退款(可完整预览的文档不适用该条件!)。
- 3、如文档侵犯您的权益,请联系客服反馈,我们会尽快为您处理(人工客服工作时间:9:00-18:30)。
客车蒙皮的成型及安装工艺
摘要: 简要介绍国内客车蒙皮成型及安装工艺现状, 结合目前国内外新材料、新技术的发展动向,
浅析客车企业怎样选择应用这些工艺。
关键词: 客车蒙皮成型与安装工艺
国内将客车蒙皮通常分为前、后围蒙皮, 侧围蒙皮和车顶蒙皮, 其成型及安装工艺方法较多,各客车制造企业可根据自身情况选择相应方法, 现简要介绍如下。
1前后围蒙皮安装
1.1.1靠模手工成型工艺
该工艺首先在铁模(或焊胎架) 上利用手锤敲打蒙皮成型, 然后再在用木块拼装设计成所要求的前后围放样模上靠贴校正, 最后焊接于前后围骨架上。
该工艺的特点是:
(1) 由于蒙皮采用手工敲击成型, 所以易于产品改型及变型;
(2) 通常采用手工电弧焊焊接, 需求的工装设备简单, 资金投入少;
(3) 生长周期长, 效率低;
(4) 外观质量取决于操作者的钣金技艺及责任心。
该工艺已相对落后, 现代企业在生产上已较少采用, 通常在一些产品试制开发或单件小批量生产中采用。
1.1.2钢件冲压成型工艺
该工艺是把整个前、后围根据其功能特点进行分块设计, 再分别制模冲压成型。
该工艺的特点是:
(1) 采用薄钢板冲压成型, 结构稳定, 造型曲线完美, 工作效率高;
(2) 蒙皮成型后焊接或采用其他方式安装在前后围骨架上,工艺灵活, 较靠模手工成型安装工艺简单、方便;
(3) 需要大量模具及大型模具, 资金投入多, 车型改型投入很大, 通常只用于大批量成熟车型的生产;
(4) 采用分块安装, 其安装质量直接影响客车的密封性, 且对其防锈工艺要求也较高;
(5) 为保证装配效果, 对前后围骨架结构尺寸精度要求较高。
该工艺因资金投入风险大, 只有大型客车制造厂成熟的且市场前景极好的产品, 或者该系列产品的部件有较强的通用性, 方可采用这种工艺。
1.1.3玻璃钢蒙皮与骨架分体成型工艺
该工艺是利用玻璃树脂胶与玻璃纤维在前后围模具上涂敷成型, 内埋螺母板; 玻璃钢蒙皮与整体骨架铆接或粘贴。
该工艺的特点是:
(1) 玻璃钢材料质量轻,强度高,易成型,并有良好的绝缘性、防锈蚀性等。
(2) 蒙皮成型后易于搬运、存储、防护等。
(3) 因玻璃钢蒙皮成型工艺大部分是采用手工涂敷, 所以其模具要求简单, 成本不足冲压模具的1/10。
(4) 通常采用铆接加粘接工艺把蒙皮安装在骨架上。
由于玻璃钢件具有一定脆性, 易在安装过程中产生爆裂; 或因受集中应力作用而造成早期裂损;外观性较差。
(5) 蒙皮与预埋螺母板、骨架的连接处易脱裂。
1.1.4玻璃钢蒙皮与骨架一体成型工艺
该工艺是将前后围骨架总成置于前后围成型模中, 然后用玻璃纤维及玻璃树脂胶直接与玻璃钢蒙皮一起成型。
成型后将前后围整体与车身骨架中段
焊接。
该工艺的特点是:
(1) 除了具有1.1.3 节中提及的玻璃钢材料特性外, 还较易达到设计使用的强度和刚度;
(2) 简化了前后围蒙皮外包工艺, 节省了工时费用等;
(3) 能实现设计要求的任何曲面造型;
(4) 前后围与中段骨架采用专用夹具夹紧, 直接焊接, 既保证了强度, 又减少了焊接变形;
(5) 具有良好的密封性。
该工艺简单、效率高、制造成本低, 可大力推广使用。
前后围蒙皮造型直接影响客车外观性, 在市场中起着非常重要的作用。
所以采用何种生产工艺, 经济合理地开发生产出适应市场的客车, 是客车生产企业的决策重要内容。
2客车两侧蒙皮安装工艺
2.1.1分片铆接工艺
把单侧蒙皮分成3~ 5 片不等, 逐片采用专用夹具夹紧于车身骨架上, 钻孔拉铆安装。
该工艺的特点是:
(1) 简单方便, 需用的工具设备简单通用;
(2) 由于采用分片安装, 大大减轻了工作量;
(3) 要靠操作者的技艺及责任心来保证质量。
该工艺虽简单, 效率高, 但由于有外露的铆钉以及蒙皮未经张拉绷紧易凹凸不平而影响外观质量。
如改变蒙皮材料及结构(比如采用铝型材蒙皮及长条分块“之”形单边铆接结构) , 可消除这种现象。
如再辅以胶粘工艺, 可大大降低行车噪声及增强客车整体密封性等。
2.1.2机械应力张拉CO2 电铆焊工艺
该工艺是在蒙皮两端用专用夹具夹紧, 一端或两端同时手动机械收紧产生张拉力将蒙皮绷紧, 再用CO2 焊机进行塞焊, 将蒙皮焊于骨架上。
该工艺的特点是:
(1) 工装简易, 手工性强; 不需要特殊的加压装置, 电源功率较小, 焊接设备简单。
(2) 焊点强度比电阻点焊高。
(3) 对上、下板的装配精度要求不太严格。
(4) 抗锈能力强, 对焊件表面处理要求不高。
(5) 由于采用手工张拉, 蒙皮的张力不易均匀,且张力较小, 所以蒙皮在焊后产生的应力不易消除,而易造成蒙皮表面有凹凸现象, 修补费时。
该工艺易于实现, 焊接牢固, 安装的蒙皮有一定的外观性。
但对操作者的责任心要求较高, 安装外观质量不易保证。
电铆焊(或点焊) 工艺
2.1.3冷张拉蒙皮CO
2
该工艺是通过液压蒙皮张拉机预紧蒙皮, 并采用单面点焊或塞焊固定蒙皮。
该工艺的特点如下:
(1) 要求有较大型的张拉设备,且产品结构要形成系列化,有一定的通用性。
通常张拉为一整块蒙皮, 美观性好。
(2) 可采用塞焊技术, 即蒙皮张紧后, 紧贴于车身骨架上进行钻孔, 当蒙皮与骨架同时钻穿后, 再用CO2 焊机点焊填充孔。
该工艺只需用较简单的工装及设备, 且焊点牢固, 对车身制造材料要求不高。
因塞焊是先钻穿孔后再进行电铆焊的, 所以其前处理不影响其焊接强度, 对防腐、除锈等设备的要求也不高。
但采用CO2 气体保护焊存在蒙皮焊接变形严重、打磨工作量大、不易保证蒙皮的外观质量等不足;
(3) 可采用点焊技术, 即蒙皮张紧后, 紧贴于车身骨架上, 使用点焊机进行点焊安装。
该工艺效率高, 蒙皮外观质量好, 是大批量生产或高档车生产的好方法。
但其要求配备相关制造设备, 特别是在防腐方面, 要求配备大型的前处理池及喷磷设备等, 否则应采用镀锌管(板) 材料, 加大了制造成本。
2.1.4热张拉蒙皮粘贴工艺
该工艺利用粘接剂将蒙皮与车身骨架粘接安装, 并在蒙皮两端接通电极, 利用蒙皮自身导电耦合作用发热, 加速粘接剂的固化以实现蒙皮的安装。
该工艺对车身材料及工艺环境要求较高, 目前国内较少采用, 通常只停留在试验阶段。
3车顶蒙皮工艺
车顶外观质量标准通常定为C 面或D 面, 其外观性要求较低, 但因车顶通常需安装空调、顶窗、通气装置等, 而对其防漏、防锈及降噪要求较高。
车顶蒙皮可分高位及低位蒙皮工艺。
3.1.1高位蒙皮工艺
即车身五大片骨架焊装后, 通过升降台等在车顶安装蒙皮。
通常有直接铆接工艺和分片成型铆焊粘工艺。
(1) 直接铆接工艺。
直接将蒙皮放于顶盖骨架上用专用夹具夹紧后, 钻孔铆接。
铆接前要求将铆钉先涂胶。
由于车顶的防漏、防锈要求高, 所以在铆后, 还通常粘一饰条或涂一层胶以遮住外露铆钉。
该工艺简单, 因为手工控制, 其外观性较差, 质量难以控制,尤其是在车顶两侧处的弯弧曲线不易保证。
工作效率也不高。
(2) 分片成型铆焊粘工艺。
在车顶外两侧采用铝型材成型后(通常与导水槽一并成型) , 与中间蒙皮相搭接安装于顶骨架上。
安装时采用铆焊粘相结合:在两侧面尽量采用粘焊相结合, 而在车顶侧采用铆焊相结合。
另外, 可在车内顶进行局部点焊以减少行车噪声。
3.1.2低位蒙皮工艺
顶盖骨架焊好后, 在五大片组焊前, 在低位工装上将顶蒙皮安装于顶骨架上。
安装顶蒙皮后再将整个顶盖总成与车身骨架进行合装, 常采用分片成型铆焊粘工艺或张拉点焊安装等。
(1) 分片成型铆焊粘工艺与高位蒙皮工艺中的相同, 但因在低位作业, 所以大大降低了劳动强度,也易于控制产品质量。
该工艺对车身五大片骨架焊接质量要求较高, 还需配备五大片骨架组焊机。
(2) 张拉点焊安装工艺。
即采用配备液压张拉蒙皮机的低位顶蒙皮安装台架, 将蒙皮张拉紧于顶盖骨架上, 再进行点焊安装。
该工艺工作效率高, 蒙皮外观美观, 劳动强度低。
但同样需配备大型的工装设备, 且要求产品结构应有相对的稳定性和通用性;在防腐上与要求高的侧蒙皮点焊相同, 制造成本较高。
通常在侧蒙皮、顶蒙皮安装中, 在蒙皮内侧与骨架相接触部位, 要采用密封胶填充涂前喷涂发泡材料, 这可以大大提高客车降噪、隔热、防腐、耐候等性能, 而且其生产成本不高, 已被广泛应用。
另外, 对于一些豪华旅游车侧蒙皮中的
下裙蒙皮, 因有行李舱门、风栅门、检视门、空调机门等而常采用钎(挂) 板门工艺, 即用定位焊接门铰连接各门。
4结束语
客车蒙皮安装工艺方法很多, 但作为生产企业,要从实际出发, 根据产品市场预测及产品类型, 结合企业自身的工艺能力、特点及其经济性, 设计开发出合适的产品结构, 并选用合适的材料, 综合选用有关工艺方法, 而且在不同的阶段, 不同的市场区域, 应根据产品的不同特点, 相应改变生产工艺, 这样才能使企业在激烈的市场竞争中立于不败之地。