铝阳极氧化与染色技术 之二 阳极化处理
铝合金阳极氧化与表面处理技术

铝合金阳极氧化与表面处理技术铝合金阳极氧化作为表面处理技术,可以极大地改善材料的物理和化学性能,提高其耐腐蚀性、抗冲击性和耐磨性等性能,是现代工业技术中一个重要的处理过程。
本文重点介绍了铝合金阳极氧化及其表面处理技术,并讨论了阳极氧化的实验与制备及其应用在工业上的相关研究。
铝合金阳极氧化是一种通过电化学方法在铝合金表面形成氧化膜的表面处理技术。
它将铝合金物理结构改变为氧化物,形成多层致密氧化膜,具有良好的耐腐蚀性、抗冲击性和耐磨性等性能。
铝合金阳极氧化主要是采用化学阳极技术,通过给铝合金涂覆特定种类的化学药剂来形成氧化膜的表面处理技术。
阳极氧化技术中的化学药剂包括氯离子、碳酸钠、氢氟酸,可以分别发挥不同的作用。
在铝合金阳极氧化实验中,首先需要对材料表面进行清洁,以确保表面可以以最佳效果氧化。
擦洗是铝合金阳极氧化前必须完成的一个关键环节,其目的是去除污垢、油污等,这样可以确保氧化过程中表面不被受到有害影响。
接下来,铝合金要经过酸浸或电解清洗,以充分去除表面的腐蚀物,然后才能进行阳极氧化。
擦洗后的表面必须完全干燥,铝合金放入阳极氧化槽中,溶液温度一般维持在比常温稍高一些的温度,在无氧、无腐蚀性气体的情况下,通过专门的电解装置将电流从阳极传入到铝合金的表面。
氧化过程中,也会加入一定量的药液,以增加氧化膜的硬度、厚度和耐腐蚀性等性能。
氧化完成后,铝合金表面的氧化膜具有不同的硬度、耐磨性和耐腐蚀性等特性,可以满足一定的应用要求。
此外,需要注意,氧化过程本身也可能会对铝合金的机械性能、力学性能和结构稳定性产生影响,因此,在进行阳极氧化前,需要对这些性能进行充分研究。
本文简要介绍了铝合金阳极氧化与表面处理技术,从处理过程、实验及制备方面讨论了氧化技术的研究和应用。
可以看出,铝合金阳极氧化是一种提升铝合金性能的重要技术,将在未来受到越来越多的关注和应用。
实验二铝的阳极氧化和电解着色
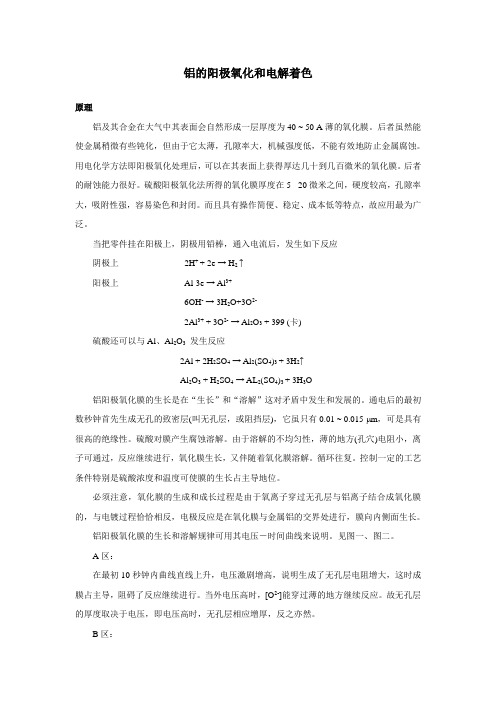
铝的阳极氧化和电解着色原理铝及其合金在大气中其表面会自然形成一层厚度为40 ~ 50 A薄的氧化膜。
后者虽然能使金属稍微有些钝化,但由于它太薄,孔隙率大,机械强度低,不能有效地防止金属腐蚀。
用电化学方法即阳极氧化处理后,可以在其表面上获得厚达几十到几百微米的氧化膜。
后者的耐蚀能力很好。
硫酸阳极氧化法所得的氧化膜厚度在5 - 20微米之间,硬度较高,孔隙率大,吸附性强,容易染色和封闭。
而且具有操作简便、稳定、成本低等特点,故应用最为广泛。
当把零件挂在阳极上,阴极用铅棒,通入电流后,发生如下反应阴极上2H+ + 2e → H2 ↑阳极上Al-3e → Al3+6OH-→ 3H2O+3O2-2Al3+ + 3O2-→ Al2O3 + 399 (卡)硫酸还可以与Al、Al2O3发生反应2Al + 2H2SO4→ Al2(SO4)3 + 3H2↑Al2O3 + H2SO4→ AL2(SO4)3 + 3H3O铝阳极氧化膜的生长是在“生长”和“溶解”这对矛盾中发生和发展的。
通电后的最初数秒钟首先生成无孔的致密层(叫无孔层,或阻挡层),它虽只有0.01 ~ 0.015 m,可是具有很高的绝缘性。
硫酸对膜产生腐蚀溶解。
由于溶解的不均匀性,薄的地方(孔穴)电阻小,离子可通过,反应继续进行,氧化膜生长,又伴随着氧化膜溶解。
循环往复。
控制一定的工艺条件特别是硫酸浓度和温度可使膜的生长占主导地位。
必须注意,氧化膜的生成和成长过程是由于氧离子穿过无孔层与铝离子结合成氧化膜的,与电镀过程恰恰相反,电极反应是在氧化膜与金属铝的交界处进行,膜向内侧面生长。
铝阳极氧化膜的生长和溶解规律可用其电压-时间曲线来说明。
见图一、图二。
A区:在最初10秒钟内曲线直线上升,电压激剧增高,说明生成了无孔层电阻增大,这时成膜占主导,阻碍了反应继续进行。
当外电压高时,[O2-]能穿过薄的地方继续反应。
故无孔层的厚度取决于电压,即电压高时,无孔层相应增厚,反之亦然。
铝合金阳极氧化膜与着色技术-实验二

表面技术概论实验指导书之一实验一铝阳极氧化膜与着色技术实验一、实验目的1.了解转化膜与着色技术的实际意义。
2.了解铝的阳极氧化和着色的原理。
3.掌握铝阳极氧化膜与着色技术工艺方法。
二、实验原理表面转化膜与着色技术是材料表面工程技术中的重要分支之一,应用非常广泛。
转化膜技术是通过化学或电化学方法,使金属表面形成稳定的化合物膜层而不改变其金属外观的一类技术,其形成方法是:将金属工件浸渍于处理溶液中,通过化学或电化学反应,使被处理金属表面发生溶解并与处理溶液发生反应,在金属表面上形成一层难溶的化合物膜层。
转化膜以“基体金属发生溶解、参与反应”,形成的是“难溶的化合物膜层”及“不改变金属外观”区别于电镀层、化学镀层或有机涂层等其它表面处理层。
(一)铝的阳极氧化轻金属材料的阳极氧化属于表面转化膜技术中的分支之一。
轻金属材料重量轻、导电导热性好,但这些材料耐腐蚀性差,容易产生晶间腐蚀,耐磨性比较低。
通过阳极氧化处理,可在其表面生成一层厚度达几十到数百微米的氧化膜。
根据不同用途,阳极氧化膜可赋予表面防护、装饰性、耐磨性、绝缘、隔热、光学性能等。
铝在大气中会自然形成非晶态的氧化铝膜,厚度为4~5μm。
这层膜不致密,耐腐蚀性差。
人工形成阳极氧化膜是在一定的电解池中进行的。
将铝制件作为阳极,其它材料(如铅、铝等)作为阴极置于电解池(如以硫酸溶液作为电解液)中,通上直流电,这时可以观察到在阳极上和阴极上都有气体析出。
阳极析出氧气,阴极析出氢气。
而阳极上析出的氧大部分与铝作用生成了Al203(氧化膜) (见图1)。
氧化膜的生成是两个不同过程同时进行的结果:一个是电化学过程,它产生氧并与铝作用生成从Al203,另一个是化学过程,生成的Al203膜被电解液溶解成为多孔层。
没有溶解过程,Al203膜就不能导电,反应不能继续。
其次,氧化膜的生成速度必须大于溶解速度,否则膜层不能增厚。
铝阳极氧化过程的电极反应可简单地描述如下:硫酸对金属铝和氧化膜的溶解作用为阳极氧化一开始,铝表面立即生成一层致密的氧化膜。
铝表面阳极氧化处理方法

铝表面阳极氧化处理方法(一)一、表面预处理无论采用何种方法加工得铝材及制品,表面上都会不同程度地存在着污垢与缺陷,如灰尘、金属氧化物(天然得或高温下形成得氧化铝薄膜)、残留油污、沥青标志、人工搬运手印(主要成分就是脂肪酸与含氮得化合物)、焊接熔剂以及腐蚀盐类、金属毛刺、轻微得划擦伤等。
因此在氧化处理之前,用化学与物理得方法对制品表面进行必要得清洗,使其裸露纯净得金属基体,以利氧化着色顺利进行,从而获得与基体结合牢固、色泽与厚度都满足要求且具有最佳耐蚀、耐磨、耐侯等良好性能得人工膜、(一)脱脂铝及铝合金表面脱脂有有机溶剂脱脂、表面活性剂脱脂、碱性溶液脱脂、酸性溶液脱脂、电解脱脂、乳化脱脂。
几种脱脂方法及主要工艺列于表—1。
在这些方法中,以碱性溶液特别就是热氢氧化钠溶液得脱脂最为有效。
表—1 脱脂及主要工艺脱脂方法溶液组成用量g/L 温度/度时间min 后处理备注有机溶剂汽油、四氯化碳、三氯乙烯等适量常温或蒸汽适当无浸蚀表面活性剂肥皂、合成洗涤剂适量常温-80适当。
水清洗无浸蚀碱性溶液 NaOH 50-200 40—80 0。
5—3水洗后用100—500g/L硝酸溶液中与及除挂灰脱脂兼腐蚀除去自然氧化,硝酸可用稀硫酸+铬酸代替十二水磷酸钠NaOH硅酸钠40—608-1225—30 60—70 3—5水清洗 NaOH可用40—50g/L碳酸钠代替,总碱度按NaOH计算为1.6%—2。
5%多聚磷酸钠碳酸钠磷酸钠一水硼酸钠葡萄糖酸液体润湿剂15、64。
84、84、80.3ml0。
1ml 60 12-15 水清洗使用前搅拌4个小时十二水磷酸钠硅酸钠液体肥皂 50-7025-353—5 75—85 3-5 水清洗碳酸钠磷酸钠 25-4025-40 75—85 适当水清洗磷酸钠碳酸钠NaOH 20106 45-65 3—5 水清洗强碱阻化除油剂40-60 70 5 水清洗除油不净可延长处理时间酸性溶液硫酸 50—300 60-80 1-3 水清洗硝酸 162-354 常温 3—5 水清洗松化处理磷酸硫酸表面活性剂307550-605-6水清洗磷酸(85%)丁醇异丙醇水 100%40%30%20% 常温5-10 水清洗溶液组成以体积记电解溶液阳极氧化用电解质常温适当交流电或阴极电流电解NaOH 100-200常温0、5-3 水清洗后中与铝制品为阴极,电流密度为4—8A/dm2乳化溶液石蜡三乙醇胺油酸松油水 8、0%0.25%0、5%2.25%89%常温适当水清洗溶液组成以体积记有机溶剂就是利用油脂易溶于有机溶剂得特点进行脱脂,常用得溶剂有汽油、煤油、乙醇、乙酸异戊脂、丙酮、四氯化碳、三氯乙烯等。
实验一-铝阳极氧化及着色

实验一铝阳极氧化与染色技术一、表面预处理无论采用何种方法加工的铝材及制品,表面上都会不同程度地存在着污垢和缺陷,如灰尘、金属氧化物(天然的或高温下形成的氧化铝薄膜)、残留油污、沥青标志、人工搬运手印(主要成分是脂肪酸和含氮的化合物)、焊接熔剂以及腐蚀盐类、金属毛刺、轻微的划擦伤等。
因此在氧化处理之前,用化学和物理的方法对制品表面进行必要的清洗,使其裸露纯净的金属基体,以利氧化着色顺利进行,从而获得与基体结合牢固、色泽和厚度都满足要求且具有最佳耐蚀、耐磨、耐侯等良好性能的人工膜。
(一)脱脂铝及铝合金表面脱脂有有机溶剂脱脂、表面活性剂脱脂、碱性溶液脱脂、酸性溶液脱脂、电解脱脂、乳化脱脂。
几种脱脂方法及主要工艺列于表-1。
在这些方法中,以碱性溶液特别是热氢氧化钠溶液的脱脂最为有效。
表-1 脱脂及主要工艺有机溶剂是利用油脂易溶于有机溶剂的特点进行脱脂,常用的溶剂有汽油、煤油、乙醇、乙酸异戊脂、丙酮、四氯化碳、三氯乙烯等。
有机溶剂仅用于小批量小型的或极污秽的制品脱脂处理。
表面活性剂是一些在很低的浓度下,能显著降低液体表面张力的物质。
常用于脱脂的表面活性剂有肥皂、合成洗涤剂、十二烷基硫酸钠、十二烷基苯磺酸钠等。
碱性脱脂溶液的配方非常多,传统工艺采用磷酸钠、氢氧化钠和硅酸钠,其中磷酸钠和硅酸钠有缓蚀、润湿、稳定作用,溶液加热和搅拌有助于获得最好的脱脂效果。
油脂在酸的存在下也能进行水解反应生成甘油和相应的高级脂肪酸。
电解脱脂可用阳极电流、阴极电流或交流电。
在碱性溶液中阴极电流脱脂,阳极最好为镀镍钢板。
其在铝及铝合金表面处理中不常用。
乳化脱脂所用的溶液为互不溶解的水与有机溶剂组成的两相或多相溶液,并添加有降低表面张力及对各相均有亲和力的去污剂。
(二)碱蚀剂碱蚀剂是铝制品在添加或不添加其他物质的氢氧化钠溶液中进行表面清洗的过程,通常也称为碱腐蚀或碱洗。
其作用是作为制品经某些脱脂方法脱脂后的补充处理,以便进一步清理表面附着的油污赃物;清除制品表面的自然氧化膜及轻微的划擦伤。
铝阳极氧化与染色技术

75-85
3月5日
水清洗
硅酸钠
25-35
液体肥皂 碳酸钠
3月5日 25-40
磷酸钠 磷酸钠
25-40 20
碳酸钠
10
NaOH
强碱阻化除 油剂
6 40-60
酸性溶液
硫酸 硝酸 磷酸
50-300 162-354
30
硫酸
7
表面活性剂 磷酸(85%)
5 100%
丁醇
40%
异丙醇
30%
电解溶液
水
阳极氧化用 电解质 NaOH
铝制品蚀洗后表面附着的灰色或黑色挂灰在冷的或热的清水洗中都不溶解,但却能溶 于酸性溶液中,所以经热碱溶液蚀洗的制品都得进行旨在除去挂灰和残留碱液,以露出光亮基 本金属表面的酸浸清洗,这种过程称为中和、光泽或出光处理。其工艺过程是制品在300400g/L硝酸(1420kg/立方米)溶液中,室温下浸洗,浸洗时间随金属组成的不同而有差异,一 般浸洗时间3-5分钟。含硅或锰的铝合金制品上的挂灰,可用硝酸和氢氟酸体积比为3:1的混合 液,于室温下处理5-15秒。中和处理还可以在含硝酸300-400g/L和氧化铬5-15g/L的溶液或氧化 铬100g/L加硫酸(1840kg/立方米)10ml/L溶液中于室温下进行。各道工序间的水清洗,目的在 于彻底除去制品表面的残留液和可溶于水的反应产物,使下道工序槽液免遭污染,确保处理效 率和质量。清洗大多采用一次冷水清洗。但碱蚀后的制品普遍采用热水紧接着是冷水的二重清 洗。热水的温度为40-60度。中和处理后的制品经水清洗就可以进行氧化处理,所以这道清洗应 特别认真,以防止清洁的表面受污染。否则前几道工序的有效处理可能会因最后的清洗不当而 前功尽弃。经中和、水清洗后的制品应与上进行氧化处理。在空气中停留的时间不宜过长,如 停留30-40分钟,制品就需要重新蚀洗和中和。
铝件导电氧化和阳极氧化

铝件导电氧化和阳极氧化铝是一种常见的金属材料,因其轻质、强度高、耐腐蚀等特点,广泛应用于电子、汽车、航空航天、建筑等行业中。
然而,铝面临的一个问题是,其表面容易氧化,导致其导电性变差,从而影响其使用效果。
因此,铝件的导电氧化和阳极氧化技术得到了广泛的研究和应用。
本文将介绍铝件的导电氧化和阳极氧化过程及其应用。
一、导电氧化技术导电氧化技术是通过在铝材表面形成一层氧化膜,使其具有较好的导电性能,从而实现对铝件表面的防腐蚀和增强其结构性能的目的。
目前常用的导电氧化工艺有紫外线辐射法、微波辐射法、脉冲电解法、电化学氧化法等。
1.紫外线辐射法紫外线辐射法是一种新兴的导电氧化技术,其主要原理是在紫外光照射下,铝材表面形成自组织氧化膜。
它的优点在于加工时间短、工艺简单、能耗低、成本较低,同时所形成的氧化膜均匀、致密,具有较好的导电性能。
2.微波辐射法微波辐射是在高频电场的作用下,利用铝与氧化还原剂反应得到氧化膜的方法。
其优势在于导电性能优异,且氧化膜表面平整光洁,粗糙度低,表面孔洞少,防腐蚀性能较好。
另外,微波辐射法的工艺稳定,操作简单,但其成本较高。
3.脉冲电化学氧化法脉冲电化学氧化法是一种新型的导电氧化技术,其主要原理是在铝材表面施加脉冲电流,由于脉冲电流存在间歇性,因此能够形成致密均匀的氧化膜,且导电性能好。
脉冲电化学氧化法对处理铝材的厚度、形状、大小、数量等几乎没有限制,优点在于工艺可控性好,操作简单,加工速度快。
4.电化学氧化法电化学氧化法是较常见的一种导电氧化技术,其通过电解处理,在铝材表面生成含Al2O3的氧化膜,从而实现防腐蚀和导电的目的。
电化学氧化法具有操作简单、成本低、处理效果好等优点。
但其缺点在于钝化剂、电压、电解质的选择必须谨慎,并且加工时间较长。
二、阳极氧化技术阳极氧化技术是一种特殊的电化学氧化技术,它通过加强电压,使氧化膜生成速度大幅提高,从而得到更厚、更硬的氧化膜。
相比于导电氧化技术,阳极氧化技术所形成的氧化膜硬度高,耐用性好,防腐蚀性强。
铝表面阳极氧化处理方法

铝表面阳极氧化处理方法一、表面预处理无论采用何种方法加工的铝材及制品,表面上都会不同程度地存在着污垢和缺陷,如灰尘、金属氧化物(天然的或高温下形成的氧化铝薄膜)、残留油污、沥青标志、人工搬运手印(主要成分是脂肪酸和含氮的化合物)、焊接熔剂以及腐蚀盐类、金属毛刺、轻微的划擦伤等。
因此在氧化处理之前,用化学和物理的方法对制品表面进行必要的清洗,使其裸露纯净的金属基体,以利氧化着色顺利进行,从而获得与基体结合牢固、色泽和厚度都满足要求且具有最佳耐蚀、耐磨、耐侯等良好性能的人工膜。
(一)脱脂铝及铝合金表面脱脂有有机溶剂脱脂、表面活性剂脱脂、碱性溶液脱脂、酸性溶液脱脂、电解脱脂、乳化脱脂。
几种脱脂方法及主要工艺列于表-1。
在这些方法中,以碱性溶液特别是热氢氧化钠溶液的脱脂最为有效。
表-1 脱脂及主要工艺脱脂方法溶液组成用量g/L 温度/度时间min 后处理备注有机溶剂汽油、四氯化碳、三氯乙烯等适量常温或蒸汽适当无浸蚀表面活性剂肥皂、合成洗涤剂适量常温-80 适当. 水清洗无浸蚀碱性溶液NaOH 50-200 40-80 0.5-3 水洗后用100-500g/L硝酸溶液中和及除挂灰脱脂兼腐蚀除去自然氧化,硝酸可用稀硫酸+铬酸代替十二水磷酸钠NaOH硅酸钠40-608-1225-30 60-70 3-5 水清洗NaOH可用40-50g/L 碳酸钠代替,总碱度按NaOH计算为1.6%-2.5%多聚磷酸钠碳酸钠磷酸钠一水硼酸钠葡萄糖酸液体润湿剂15.64.84.84.80.3ml0.1ml 60 12-15 水清洗使用前搅拌4个小时十二水磷酸钠硅酸钠液体肥皂50-7025-353-5 75-85 3-5 水清洗碳酸钠磷酸钠25-4025-40 75-85 适当水清洗磷酸钠碳酸钠NaOH 20106 45-65 3-5 水清洗强碱阻化除油剂40-60 70 5 水清洗除油不净可延长处理时间酸性溶液硫酸50-300 60-80 1-3 水清洗硝酸162-354 常温3-5 水清洗松化处理磷酸硫酸表面活性剂3075 50-60 5-6 水清洗磷酸(85%)丁醇异丙醇水100%40%30%20% 常温5-10 水清洗溶液组成以体积记电解溶液阳极氧化用电解质常温适当交流电或阴极电流电解NaOH 100-200 常温0.5-3 水清洗后中和铝制品为阴极,电流密度为4-8A/dm2乳化溶液石蜡三乙醇胺油酸松油水8.0%0.25%0.5%2.25%89% 常温适当水清洗溶液组成以体积记有机溶剂是利用油脂易溶于有机溶剂的特点进行脱脂,常用的溶剂有汽油、煤油、乙醇、乙酸异戊脂、丙酮、四氯化碳、三氯乙烯等。
- 1、下载文档前请自行甄别文档内容的完整性,平台不提供额外的编辑、内容补充、找答案等附加服务。
- 2、"仅部分预览"的文档,不可在线预览部分如存在完整性等问题,可反馈申请退款(可完整预览的文档不适用该条件!)。
- 3、如文档侵犯您的权益,请联系客服反馈,我们会尽快为您处理(人工客服工作时间:9:00-18:30)。
表面阳极化surface anodizing金属材料在电解质溶液中,通过外施阳极电流使其表面形成氧化膜的一种材料保护技术。
又称表面阳极氧化。
金属材料或制品经过表面阳极化处理后,其耐蚀性、硬度、耐磨性、绝缘性、耐热性等均有大幅度提高。
实施阳极化处理最多的金属材料是铝。
铝的阳极氧化一般在酸性电解液中进行,以铝为阳极。
在电解过程中,氧的阴离子与铝作用产生氧化膜。
这种膜初形成时不够细密,虽有一定电阻,但电解液中的负氧离子仍能到达铝表面继续形成氧化膜。
随着膜厚度增大,电阻也变大,从而电解电流变小。
这时,与电解液接触的外层氧化膜发生化学溶解。
当铝表面形成氧化物的速度逐渐与化学溶解的速度平衡时,这一氧化膜便可达到这一电解参数下的最大厚度。
铝的阳极氧化膜外层多孔,容易吸附染料和有色物质,因而可进行染色,提高其装饰性。
氧化膜再经热水、高温水蒸气或镍盐封闭处理后,还能进一步提高其耐蚀性和耐磨性。
除铝外,工业上采用表面阳极化处理的金属还有镁合金、铜和铜合金、锌和锌合金、钢、镉、钽、锆等。
铝阳极氧化与染色技术之二阳极化处理铝制品表面的自然氧化铝既软又薄,耐蚀性差,不能成为有效防护层更不适合着色。
人工制氧化膜主要是应用化学氧化和阳极氧化。
化学氧化就是铝制品在弱碱性或弱酸性溶液中,部分基体金属发生反应,使其表面的自然氧化膜增厚或产生其他一些钝化膜的处理过程,常用的化学氧化膜有铬酸膜和磷酸膜,它们既薄吸附性又好,可进行着色和封孔处理,表-3介绍了铝制品化学氧化工艺。
化学氧化膜与阳极氧化膜相比,膜薄得多,抗蚀性和硬度比较低,而且不易着色,着色后的耐光性差,所以金属铝着色与配色仅介绍阳极化处理。
表-3 铝制品化学氧化工艺(一)阳极氧化处理的一般概念1、阳极氧化膜生成的一般原理以铝或铝合金制品为阳极置于电解质溶液中,利用电解作用,使其表面形成氧化铝薄膜的过程,称为铝及铝合金的阳极氧化处理。
其装置中阴极为在电解溶液中化学稳定性高的材料,如铅、不锈钢、铝等。
铝阳极氧化的原理实质上就是水电解的原理。
当电流通过时,在阴极上,放出氢气;在阳极上,析出的氧不仅是分子态的氧,还包括原子氧(O)和离子氧,通常在反应中以分子氧表示。
作为阳极的铝被其上析出的氧所氧化,形成无水的氧化铝膜,生成的氧并不是全部与铝作用,一部分以气态的形式析出。
2、阳极氧化电解溶液的选择阳极氧化膜生长的一个先决条件是,电解液对氧化膜应有溶解作用。
但这并非说在所有存在溶解作用的电解液中阳极氧化都能生成氧化膜或生成的氧化膜性质相同。
适用于阳极氧化处理的酸性电解液见表-4。
表-4 氧化处理的酸性电解液3、阳极氧化的种类阳极氧化按电流形式分为:直流电阳极氧化,交流电阳极氧化,脉冲电流阳极氧化。
按电解液分有:硫酸、草酸、铬酸、混合酸和以磺基有机酸为主溶液的自然着色阳极氧化。
按膜层性子分有:普通膜、硬质膜(厚膜)、瓷质膜、光亮修饰层、半导体作用的阻挡层等阳极氧化。
铝及铝合金常用阳极氧化方法和工艺条件见表-5。
其中以直流电硫酸阳极氧化法的应用最为普遍。
表-5 铝及铝合金常用阳极氧化方法4、阳极氧化膜结构、性质阳极氧化膜由两层组成,多孔的厚的外层是在具有介电性质的致密的内层上上成长起来的,后者称为阻挡层(也称活性层)。
用电子显微镜观察研究,膜层的纵横面几乎全都呈现与金属表面垂直的管状孔,它们贯穿膜外层直至氧化膜与金属界面的阻挡层。
以各孔隙为主轴周围是致密的氧化铝构成一个蜂窝六棱体,称为晶胞,整个膜层是又无数个这样的晶胞组成。
阻挡层是又无水的氧化铝所组成,薄而致密,具有高的硬度和阻止电流通过的作用。
阻挡层厚约0.03-0.05μm,为总膜后的0.5%-2.0%。
氧化膜多孔的外层主要是又非晶型的氧化铝及小量的水合氧化铝所组成,此外还含有电解液的阳离子。
当电解液为硫酸时,膜层中硫酸盐含量在正常情况下为13%-17%。
氧化膜的大部分优良特性都是由多孔外层的厚度及孔隙率所觉决定的,它们都与阳极氧化条件密切相关。
(二)直流电硫酸阳极氧化1、氧化膜成长机理在硫酸电解液中阳极氧化,作为阳极的铝制品,在阳极化初始的短暂时间内,其表面受到均匀氧化,生成极薄而有非常致密的膜,由于硫酸溶液的作用,膜的最弱点(如晶界,杂质密集点,晶格缺陷或结构变形处)发生局部溶解,而出现大量孔隙,即原生氧化中心,使基体金属能与进入孔隙的电解液接触,电流也因此得以继续传导,新生成的氧离子则用来氧化新的金属,并以孔底为中心而展开,最后汇合,在旧膜与金属之间形成一层新膜,使得局部溶解的旧膜如同得到“修补”似的。
随着氧化时间的延长,膜的不断溶解或修补,氧化反应得以向纵深发展,从而使制品表面生成又薄而致密的内层和厚而多孔的外层所组成的氧化膜。
其内层(阻挡层、介电层、活性层)厚度至氧化结束基本都不变,位置却不断向深处推移;而外早一定的氧化时间内随时间而增厚。
2、氧化膜厚度计算阳极氧化生成的氧化膜厚度从理论上可按法拉第第二定律推导的公式进行计算。
σ= Kit式中σ为阳极氧化膜厚度(μm),I为电流密度(A/dm2),t 为氧化时间(min),K为系数(当氧化铝密度γ=kg/立方米则K=0.309)。
上述公式计算的前提是以认为通过的电量全用于氧化铝析出,同时也把氧化铝及膜的密度视为纯净的氧化铝密集的值。
但实际情况并非完全如此,为了使K值更切合实际,应将电流效率和在这种工艺条件下所生成膜的密度或孔隙度考虑在内,即:K = 1.57η/γ式中η为电流效率(电极上实际析出的物质量与又总电量换算出的析出物质量之比)。
K实值各国取值大小各异,美国有取0.328、0.285-0.355,日本有取0.352、0.364、0.25,中国、俄罗斯取0.25。
3、影响氧化膜生长和质量的因素当电解液的温度从 20度上升到30度,膜的溶解速度约增加3倍。
随电流密度的增加,制品被养护的金属量、表面生成的铝氧化膜厚度都随着增加。
硫酸浓度对氧化膜厚度的影响不大,为获得中等厚度、多孔而易于着色和封闭、抗蚀性较高的膜层,浓度最好为15%-20%;溶液用去离子水要求氯离子<15mg/L、铁离子<1mg/L、硫酸根离子<30mg/L,电阻率为5×10的5-6次方Ω·cm;溶液中杂质允许的最大含量铝离子20g/L,铜离子 2g/L,铁离子 5g/L,氯离子 0.1g/L。
随着阳极氧化时间的延长,氧化膜的厚度增加,到一定厚度后,由于膜厚电阻增加、导电能力下降,膜的生长速度减慢,有的合金即使延长氧化时间,膜的厚度也不会再增加。
不同的铝合金的阳极氧化膜有不同的色彩,纯铝上的膜无色透明,使金属的光泽完全保持下来;高纯铝添加少量的镁,膜色不会因氧化时间的延长而改变,当镁的含量超过2%,膜变暗浊色;铝硅合金阳极氧化时,硅不会被氧化或溶解,部分进入膜层使膜呈暗灰色。
含硅量大时,阳极氧化前先用氢氟酸浸泡,膜色会有所好转,一般含硅5%以上的合金不适合做光亮着色制品,含量达13%就难于进行阳极化处理;含铜的合金,当含量较少时,膜呈绿色,随铜含量的增加,膜薄,色调深暗。
某些变形铝合金的阳极氧化处理见表-6。
铝合金在硫酸溶液中阳极氧化,由于氧化膜在表面上形成、生长和溶解,引起电阻的变化,使过程中的电流、槽端电压及电流密度都随之发生变化。
实际操作中电压升高不宜太快,否则会使生成的膜不均匀。
表-6 某些铝合金阳极氧化处理效果注:1—优良;2—良好;3—尚好;4—可以;5—不适合;6—只适合于暗的颜色。
4、建筑铝型材阳极氧化工艺建筑铝材是目前阳极氧化处理的主要产品,其中75%-85%是用常规硫酸法处理。
中国建筑型材标准规定氧化膜的厚度大于10μm。
建筑铝材阳极氧化工艺的最佳工艺参数为电解液硫酸15%±2%,铝离子含量小于5g/L,溶液温度21±10C,电流密度(1.3±0.05)A/dm2,时间(对LD31合金)30min,则10μm;60分钟,则可达18μm(电压18V),溶液用纯水配制。
(三)其他阳极氧化1、草酸阳极氧化对硫酸阳极氧化影响的大部分因素也适用于草酸阳极氧化,草酸阳极氧化可采用直流电、交流电或者交直流电迭加。
用交流电氧化比直流电在相同条件下获得膜层软、弹性较小;用直流电氧化易出现孔蚀,采用交流电氧化则可防止,随着交流成分的增加,膜的抗蚀性提高,但颜色加深,着色性比硫酸膜差。
电解液中游离草酸浓度为3%-10%,一般为3%-5%,在氧化过程中每A·h约消耗0.13-0.14g,同时每A·h有0.08-0.09g的铝溶于电解液生成草酸铝,需要消耗5倍于铝量的草酸。
溶液中的铝离子浓度控制在20g/L以下,当含30g/L铝时,溶液则失效。
草酸电解液对氯化物十分敏感,阳极氧化纯铝或铝合金时,氯化物的含量分别不应超过0.04-0.02g/L,溶液最好用纯水配制。
电解液温度升高,膜层减薄。
为得到厚的膜,则应提高溶液的pH值。
直流电阳极氧化用铅、石墨或不锈钢做阴极,其与阳极的面积比为(1:2)-(1:1)之间。
草酸是弱酸,溶解能力低,铝氧化时,必须冷却制品及电解液。
草酸膜层的厚度及颜色依合金成分而不同,纯铝的膜厚呈淡黄或银白色,合金则膜薄色深如黄色、黄铜色。
氧化后膜层经清洗,若不染色可用3.43×10的4次方Pa压力的蒸汽封孔30-60分钟。
2、铬酸阳极氧化铬酸阳极氧化工艺见表-4。
氧化过程中应经常进行浓度分析,适时添加铬酐。
电解的阴极材料可用铅、铁、不锈钢,最好的阳阴面积比为(5:1)-(10:1)。
当溶液中三价铬离子多时,可用电解的方法使其氧化成六价铬离子。
溶液中的硫酸盐含量超过0.5%,阳极氧化效果不好,硫酸根离子多时可加入氢氧化钡或者碳酸钡使其生成硫酸钡沉淀。
溶液中氯化物含量不应超过0.2g/L。
溶液中铬含量超过70g/L时就应稀释或更换溶液。
铬酸阳极氧化有电压周期变化的阳极氧化方法或恒电压阳极氧化法(快速铬酸法)两种。
3、硬质(厚膜)阳极氧化硬质阳极氧化是铝及铝合金表面生成厚而坚硬氧化膜的一种工艺方法。
硬质膜的最大厚度可达250μm ,纯铝上形成的膜层微硬度为12000-15000MPa,合金的一般为4000-6000MPa,与硬铬镀层的相差无几,它们在低符合时耐磨性极佳,硬质膜的孔隙率约为20%左右,比常规硫酸膜低。
某些硬质阳极氧化工艺见表-7。
表-7 硬质阳极氧化工艺4、瓷质阳极氧化瓷质阳极氧化铝及铝合金在草酸、柠檬酸和硼酸的钛盐、锆盐或钍盐溶液中阳极氧化,溶液中盐类金属的氢氧化物进入氧化膜孔隙中,从而使制品表面显示出与不透明而致密的搪瓷或具有特殊光泽的类似塑料外观的处理过程。
瓷质阳极氧化处理工艺流程与常规硫酸阳极氧化基本一致,不同的是瓷质阳极氧化是在高的直流电压(115-125V)和较高的溶液温度(50-60度)、电解液经常搅拌、经常调节pH值使之处于1.6-2范围内的条件进行。