TPR注塑工艺知识
简述TPR塑料注塑成型加工前材料和工艺性能检测

简述TPR塑料注塑成型加工前材料和工艺性能检测TPR(热塑性橡胶)是一种具有橡胶弹性和塑料可加工性的材料,常用于注塑成型加工。
在进行TPR塑料注塑成型加工前,需要进行材料和工艺性能检测,以确保产品质量和生产效率。
本文将简述TPR塑料注塑成型加工前的材料和工艺性能检测。
一、TPR塑料的材料检测:1.外观检测:通过目视检查TPR塑料的颜色、表面光洁度、气泡、杂质等外观问题,确保材料质量。
2.密度检测:使用密度计对TPR塑料样品进行密度测量,了解其物理特性和杂质含量。
3.熔流率检测:通过熔流指数测试仪测量TPR塑料的熔流指数,评估其流动性和加工性能。
4.硬度检测:使用硬度计对TPR塑料进行硬度测量,了解其弹性和硬度特性。
5.拉伸强度和断裂伸长率检测:通过拉伸试验仪测量TPR塑料的拉伸强度和断裂伸长率,评估其机械性能和韧性。
6.热稳定性检测:通过热膨胀系数测试仪对TPR塑料进行热稳定性检测,了解其热性能和稳定性。
二、TPR塑料的工艺性能检测:1.熔融指数检测:通过熔融指数仪测试TPR塑料在不同温度和压力条件下的熔融指数,评估其熔融流动性。
2.热稳定性检测:使用热膨胀系数测试仪对TPR塑料进行热稳定性检测,了解其在高温下的热膨胀性。
3.压缩回弹率检测:通过压缩试验仪测量TPR塑料的压缩回弹率,评估其弹性恢复性能。
4.硬度检测:使用硬度计对TPR塑料的硬度进行测量,了解其硬度特性及变化。
5.热导率检测:使用热导率仪对TPR塑料的热导率进行测量,评估其热传导性能。
6.耐候性检测:通过模拟环境测试,如光老化试验、盐雾试验等评估TPR塑料的耐候性能。
综上所述,TPR塑料注塑成型加工前的材料和工艺性能检测对于确保产品质量和生产效率至关重要。
通过对TPR塑料的外观、密度、熔流率、硬度、拉伸强度、断裂伸长率、热稳定性等方面进行检测,可以评估其材料特性。
通过熔融指数、热稳定性、压缩回弹率、硬度、热导率、耐候性等方面的检测,可以评估其工艺性能。
tpr注塑加工工艺
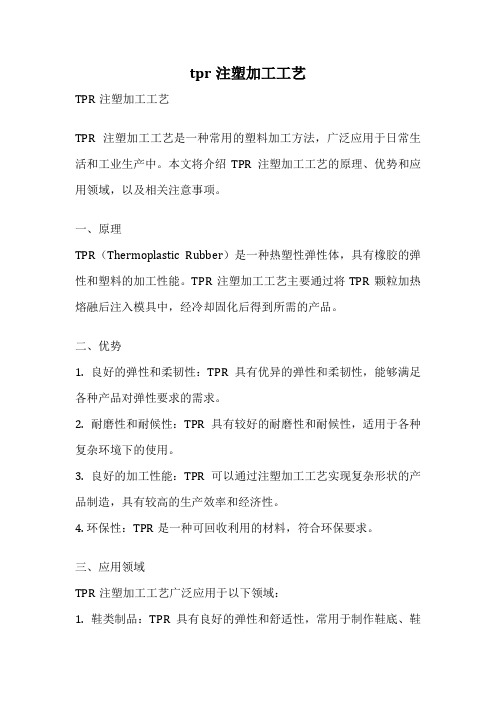
tpr注塑加工工艺TPR注塑加工工艺TPR注塑加工工艺是一种常用的塑料加工方法,广泛应用于日常生活和工业生产中。
本文将介绍TPR注塑加工工艺的原理、优势和应用领域,以及相关注意事项。
一、原理TPR(Thermoplastic Rubber)是一种热塑性弹性体,具有橡胶的弹性和塑料的加工性能。
TPR注塑加工工艺主要通过将TPR颗粒加热熔融后注入模具中,经冷却固化后得到所需的产品。
二、优势1. 良好的弹性和柔韧性:TPR具有优异的弹性和柔韧性,能够满足各种产品对弹性要求的需求。
2. 耐磨性和耐候性:TPR具有较好的耐磨性和耐候性,适用于各种复杂环境下的使用。
3. 良好的加工性能:TPR可以通过注塑加工工艺实现复杂形状的产品制造,具有较高的生产效率和经济性。
4. 环保性:TPR是一种可回收利用的材料,符合环保要求。
三、应用领域TPR注塑加工工艺广泛应用于以下领域:1. 鞋类制品:TPR具有良好的弹性和舒适性,常用于制作鞋底、鞋垫等部件。
2. 婴儿用品:TPR材料安全无毒,常用于制作奶嘴、安抚器等婴儿用品。
3. 家居用品:TPR材料具有良好的耐磨性和耐候性,常用于制作地垫、擦洗器等家居用品。
4. 医疗器械:TPR材料具有良好的弹性和柔韧性,常用于制作医疗器械的密封件、垫片等部件。
5. 工业制品:TPR材料具有较好的加工性能,常用于制作工业零部件、密封件等。
四、注意事项1. 原料选择:根据产品的要求选择合适的TPR原料,包括硬度、弹性等性能指标。
2. 模具设计:根据产品的形状和尺寸设计合适的模具,确保产品的精度和质量。
3. 加工参数控制:控制注塑机的温度、压力、注射速度等参数,以确保产品的一致性和稳定性。
4. 质量检验:对注塑成型的产品进行质量检验,包括外观、尺寸、物理性能等指标。
5. 设备维护:定期对注塑设备进行维护保养,延长设备寿命,确保生产的连续性和稳定性。
总结起来,TPR注塑加工工艺具有优异的弹性、柔韧性和加工性能,广泛应用于鞋类制品、婴儿用品、家居用品、医疗器械和工业制品等领域。
tpr注塑加工工艺
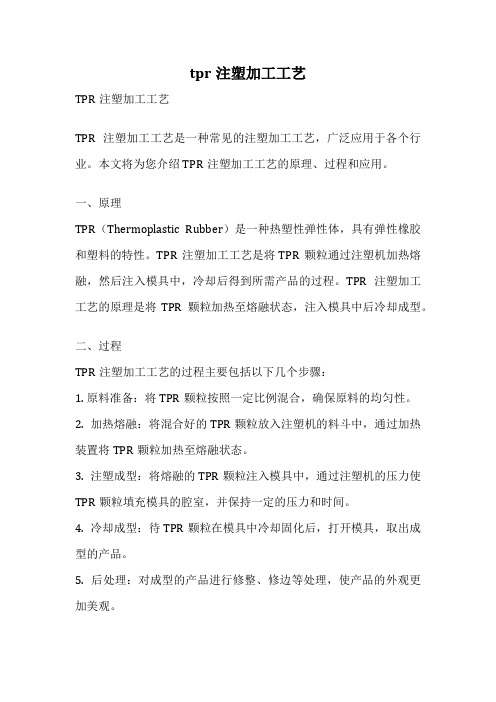
tpr注塑加工工艺TPR注塑加工工艺TPR注塑加工工艺是一种常见的注塑加工工艺,广泛应用于各个行业。
本文将为您介绍TPR注塑加工工艺的原理、过程和应用。
一、原理TPR(Thermoplastic Rubber)是一种热塑性弹性体,具有弹性橡胶和塑料的特性。
TPR注塑加工工艺是将TPR颗粒通过注塑机加热熔融,然后注入模具中,冷却后得到所需产品的过程。
TPR注塑加工工艺的原理是将TPR颗粒加热至熔融状态,注入模具中后冷却成型。
二、过程TPR注塑加工工艺的过程主要包括以下几个步骤:1. 原料准备:将TPR颗粒按照一定比例混合,确保原料的均匀性。
2. 加热熔融:将混合好的TPR颗粒放入注塑机的料斗中,通过加热装置将TPR颗粒加热至熔融状态。
3. 注塑成型:将熔融的TPR颗粒注入模具中,通过注塑机的压力使TPR颗粒填充模具的腔室,并保持一定的压力和时间。
4. 冷却成型:待TPR颗粒在模具中冷却固化后,打开模具,取出成型的产品。
5. 后处理:对成型的产品进行修整、修边等处理,使产品的外观更加美观。
三、应用TPR注塑加工工艺具有以下几个优点,因此在各个行业得到广泛应用:1. 灵活性:TPR注塑加工工艺可以制造出各种形状和尺寸的产品,满足不同行业的需求。
2. 耐用性:TPR材料具有较好的耐磨、耐油、耐腐蚀等性能,可以应用于需要耐用性的产品。
3. 弹性:TPR材料具有良好的弹性,可以应用于需要具备弹性的产品。
4. 色彩丰富:TPR材料可以通过添加颜料来调整颜色,可以制造出丰富多彩的产品。
TPR注塑加工工艺在各个行业有广泛的应用,例如汽车零部件、鞋类、玩具、家具等。
在汽车零部件领域,TPR注塑加工工艺可以制造出耐磨、耐油的密封件;在鞋类领域,TPR注塑加工工艺可以制造出具有良好弹性和舒适度的鞋底;在玩具领域,TPR注塑加工工艺可以制造出安全、环保的玩具产品。
TPR注塑加工工艺是一种常见且广泛应用的加工工艺。
通过掌握TPR注塑加工工艺的原理和过程,可以制造出各种形状、尺寸和颜色的产品,满足不同行业的需求。
TPE材料在注塑成型加工过程中需要注意的问题

TPE材料在注塑成型加工过程中需要注意的问题下面简述TPE成型加工需注意以下几点:1.机器选择(注塑成型)锁模能力以每平方英寸投射成型面积计应为1.5-3吨,可采用压缩比为2:1-3:1的通用螺杆,注射量应为机膛容量的25%-75%,通常在加工温度下最长的停留时间应为8-10分钟。
在注塑时注射喷嘴应使用一较小的锐孔,以有助于产生剪切加热。
2.主流道一般可采用带3C出模角的标准主流道设计,说到;软性SBS及SEBS材料不可用“Z”型拉针,倒扣指、反向锥形冷井和狭槽棒拉针皆是典型设计。
3.收缩率TPE材料的收缩率依配方而别,在0.5–2%范围内,熔胶流进模具反向的收缩率会较高,一般而言,SBS的收缩率要小一些,而SEBS的收缩率则会略大,密度较高的材料收缩率较密度低的材料收缩率要小,此外,加工条件如模温,熔胶温度,注速与产品厚度会影响产品收缩率。
4.干燥TPE一般不具备吸湿性,是无需干燥的,但对于二次注塑材料或基体中过多的水分会对粘接力产生不利的影响,为了尽可能地提高干燥效率和生产高质量的产品,工程塑料技术论坛强烈推荐采用去湿式干燥机或真空式干燥机。
典型的干燥条件是在温度为70-80摄氏度的条件下干燥2~3小时。
5.着色这里要注意,色母料载体应与所选择的TPE材料相容,对于SBS基材TPE来说以PS或EVA为底的色种较适当;而SEBS基材的TPE则以PE或PP为底的色种较适当,EVA为底的色种热稳定性较差,TPE不可采用以PVC为底的色种,为了使分散过程较易进行,色母料应该具有比基础TPE复合材料较低的粘度(较高的熔融流动指数)。
6.回收料对于很多采用两种材料的应用,添加回收料的方式不可取。
可以利用洁净的TPE回收料,其比例最高可达20%。
黑色材料可容纳较高比例的回收料。
天然产品、浅色或透明的复合材料可能呈现出污染或变色,除非妥善地加以控制。
停留时间过长或回收料掺混比例较高时,黄色、红色、蓝色和绿色的有机颜料较有可能被烧掉或褪色。
tpr注塑成型工艺参数
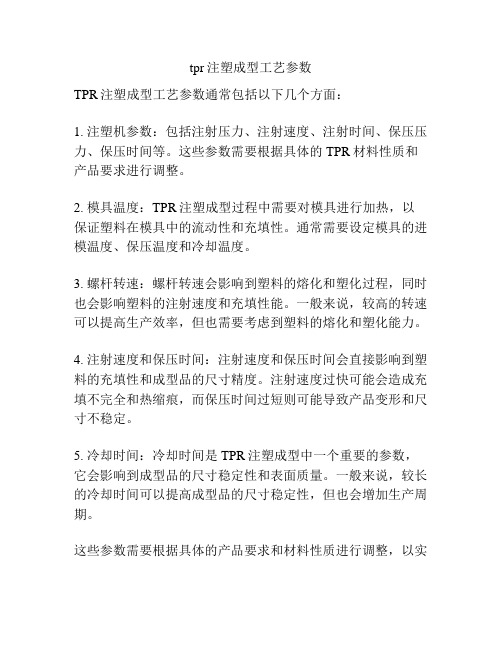
tpr注塑成型工艺参数
TPR注塑成型工艺参数通常包括以下几个方面:
1. 注塑机参数:包括注射压力、注射速度、注射时间、保压压力、保压时间等。
这些参数需要根据具体的TPR材料性质和产品要求进行调整。
2. 模具温度:TPR注塑成型过程中需要对模具进行加热,以保证塑料在模具中的流动性和充填性。
通常需要设定模具的进模温度、保压温度和冷却温度。
3. 螺杆转速:螺杆转速会影响到塑料的熔化和塑化过程,同时也会影响塑料的注射速度和充填性能。
一般来说,较高的转速可以提高生产效率,但也需要考虑到塑料的熔化和塑化能力。
4. 注射速度和保压时间:注射速度和保压时间会直接影响到塑料的充填性和成型品的尺寸精度。
注射速度过快可能会造成充填不完全和热缩痕,而保压时间过短则可能导致产品变形和尺寸不稳定。
5. 冷却时间:冷却时间是TPR注塑成型中一个重要的参数,它会影响到成型品的尺寸稳定性和表面质量。
一般来说,较长的冷却时间可以提高成型品的尺寸稳定性,但也会增加生产周期。
这些参数需要根据具体的产品要求和材料性质进行调整,以实
现最佳的注塑成型效果。
在调整参数时,还需考虑到注塑机的性能和工艺的可行性。
tpe包胶注塑工艺参数

tpe包胶注塑工艺参数(原创实用版)目录一、引言二、TPE 包胶注塑工艺概述1.TPE 包胶的定义2.TPE 包胶的加工方法三、TPE 包胶注塑工艺参数1.成型温度2.注塑压力3.注塑速度4.冷却时间5.模具设计四、不同基材的 TPE 包胶注塑工艺参数1.PP 材料的 TPE 包胶2.ABS 材料的 TPE 包胶3.PA 材料的 TPE 包胶五、TPE 包胶注塑工艺的难点及解决方案六、总结正文一、引言热塑性弹性体(Thermoplastic Elastomer,简称 TPE)是一种具有良好弹性和耐磨性的塑料材料。
在工业生产中,经常需要将 TPE 与其他硬质塑料进行包胶处理,以提高产品的耐磨性、抗老化性和美观性。
本文将详细介绍 TPE 包胶注塑工艺参数。
二、TPE 包胶注塑工艺概述1.TPE 包胶的定义TPE 包胶,顾名思义,就是将 TPE 软胶材料包胶到其他材料上。
这种工艺可以使产品具有更好的手感、抗老化性和耐磨性。
2.TPE 包胶的加工方法一般采用的加工方法有双色注塑机一次成型,或者用一般的注塑机,采用包胶模具,分二次注塑成型。
三、TPE 包胶注塑工艺参数1.成型温度TPE 材料的成型温度通常在 170-220℃之间,具体温度需根据所使用的 TPE 基料类型来确定。
对于包胶硬质塑料,如 PP、ABS、PA 等,其成型温度也有所不同,一般在 170-240℃之间。
2.注塑压力注塑压力的大小会影响到 TPE 包胶层的厚度和质量。
通常情况下,注塑压力越大,TPE 包胶层的厚度越大,但过大的压力可能会导致 TPE 材料过快地填充模具,影响产品的外观和质量。
3.注塑速度注塑速度的快慢会影响到 TPE 包胶层的均匀性和质量。
注塑速度过快,可能会导致 TPE 材料在模具内流动不均匀,进而影响产品的外观和质量;注塑速度过慢,可能会导致 TPE 材料在模具内填充不充分,影响产品的尺寸和性能。
4.冷却时间冷却时间的长短会影响到 TPE 包胶层的硬度和性能。
tpr注塑加工工艺

tpr注塑加工工艺TPR注塑加工工艺(Total Physical Response Injection Molding Process)是一种常用的塑料加工方法,广泛应用于工业生产中。
本文将介绍TPR注塑加工工艺的原理、应用以及其在制造业中的重要性。
一、原理TPR注塑加工工艺是通过将熔化的热塑性塑料注入模具中,经过冷却凝固后形成所需的产品。
其主要原理是将塑料颗粒加热至熔化状态,然后通过注射机将熔化的塑料注入模具中。
在模具中,塑料经过冷却后凝固成型,并通过模具的开合运动将成品取出。
TPR注塑加工工艺具有生产效率高、成本低、产品精度高等优点。
二、应用TPR注塑加工工艺广泛应用于制造业的各个领域,例如汽车零部件、家电外壳、电子产品等。
它可以制造出各种形状复杂、精度要求高的塑料制品。
同时,TPR注塑加工工艺还可以实现多色注塑、多材料注塑等特殊要求,满足不同客户的需求。
三、重要性TPR注塑加工工艺在制造业中具有重要的地位和作用。
首先,它可以大幅提高生产效率,实现批量生产,从而降低成本。
其次,TPR 注塑加工工艺可以制造出高精度的产品,保证产品的质量。
再次,它具有良好的产品一致性,可以保证每个产品的尺寸、外观等方面的一致性。
最后,TPR注塑加工工艺还可以实现自动化生产,提高生产线的自动化程度,减少人力投入。
四、TPR注塑加工工艺的发展趋势随着科技的进步和制造业的发展,TPR注塑加工工艺也在不断创新和发展。
目前,一些先进的注塑加工技术已经应用于TPR注塑加工工艺中,例如快速成型技术、微纳米注塑技术等。
这些新技术可以进一步提高生产效率、产品精度和质量,并满足不断变化的市场需求。
TPR注塑加工工艺是一种重要的塑料加工方法,广泛应用于制造业中。
它通过将熔化的塑料注入模具中,形成所需的产品。
TPR注塑加工工艺具有生产效率高、成本低、产品精度高等优点,对于提高制造业的竞争力具有重要意义。
随着科技的进步和市场需求的变化,TPR注塑加工工艺将不断创新和发展,为制造业带来更多的机遇和挑战。
trp的成型方式

trp的成型方式
TPR(热塑性橡胶材料)是一种新型的高分子材料,它是以热塑性弹性体为主要原料制成的。
成型方法主要有单独成型、吹塑成型、挤压成型、压延成型、浇注成型以及双色注塑或二次注塑成型方法 。
- 单独成型:将TPR颗粒直接放入模具中,加热至一定温度后使其熔化,然后冷却成型。
这种方法适用于形状简单、尺寸较小的制品。
- 吹塑成型:将TPR颗粒加入挤出机中加热熔化,然后通过挤出机口模连续挤出所需产品形状,再通过压缩空气将其吹成所需尺寸和形状。
这种方法适用于大型长条状制品。
- 挤压成型:将TPR颗粒加入挤出机中加热熔化,然后通过挤出机口模连续挤出所需产品形状,再通过冷却水槽使其冷却固化。
这种方法适用于管材、棒材等制品。
- 压延成型:将TPR颗粒加入挤出机中加热熔化,然后通过挤出机口模连续挤出所需产品形状,再通过辊筒将其压延成所需厚度和宽度。
这种方法适用于薄膜、片材等制品。
- 1、下载文档前请自行甄别文档内容的完整性,平台不提供额外的编辑、内容补充、找答案等附加服务。
- 2、"仅部分预览"的文档,不可在线预览部分如存在完整性等问题,可反馈申请退款(可完整预览的文档不适用该条件!)。
- 3、如文档侵犯您的权益,请联系客服反馈,我们会尽快为您处理(人工客服工作时间:9:00-18:30)。
TPR注塑工艺知识
根据材料的特性和供料情况,一般在成型前应对材料的外观和工艺性能进行检测。
供应的粒料往往含有不同程度的水分、熔剂及其它易挥发的低分子物,特别是具有吸湿倾向的TPR含水量总是超过加工所允许的限度。
因此,在加工前必须进行干燥处理,并测定含水量。
在高温下TPR的水分含量要求在5%以下,甚至2%~3%,因此常用真空干燥箱在75℃~90℃干燥2小时。
已经干燥的材料必须妥善密封保存,以防材料从空气中再吸湿而丧失干燥效果,为此采用干燥室料斗可连续地为注塑机提供干燥的热料,对简化作业、保持清洁、提高质量、增加注射速率均为有利。
干燥料斗的装料量一般取注塑机每小时用料量的2.5倍。
以SBC为基础的TPE在颜色上优于大多数其它TPR材料。
所以,它们只需要较少量的色母料就可达到某种特定的颜色效果,而且所产生的颜色比其它TPR更为纯净。
一般说来,色母料的粘度应该比TPR的粘度低,这是因为TPR的熔融指数比色母料高,这将有利于分散过程,使得颜色分布更加均匀。
对于以SBS为基础的TPE,推荐采用聚苯乙烯类载色剂。
对于以较硬的SEBS为基础的TPR,推荐采用聚丙烯(PP)载色剂。
对于以较软的SEBS为基础的TPR,可采用低密度聚乙烯或乙烯醋酸乙烯共聚物。
对于较软的品种,不推荐采用PP载色剂,因为复合材料的硬度将受到影响。
对于某些包胶注塑的应用,使用聚乙烯(PE)载色剂可能会对与基体的粘接力产生不利的影响。
新购进的注塑机初用之前,或者在生产中需要改变产品、更换原料、调换颜色或发现塑料中有分解现象时,都需要对注塑机机筒进行清洗或拆洗。
清洗机筒一般采用加热机筒清洗法。
清洗料一般用塑料原料(或塑料回收料)。
对于TPR材料,可用所加工的新料置换出过渡清洗料。
在加工注塑过程中,温度的设定是否准确是制品外观和性能好坏的关键。
下面是进行TPR加工注塑时温度设定的一些建议。
进料区域的温度应设定得相当低,以避免进料口堵塞并让夹带的空气逸出。
当使用色母料时为了改善混合状态,应将过渡区域的温度设定在色母料的熔点以上。
离注塑喷嘴最近区域的温度应该设定得接近于所需的熔体温度。
所以,经过测试,通常TPR产品在各个区域温度的设定范围分别是:料筒为160摄氏度到210摄氏度,喷嘴为180摄氏度到230摄氏度。
模具温度应该设定高与注塑区的冷凝温度,这将能避免水分对模具的污染以致制品表面出现的条纹。
较高的模具温度通常会导致较长的循环周期,但它能改进焊接线和制品的外观效果,所以,模具温度的范围应设计定在30到40之间。
在制品成型填充模具型腔的过程中,如果制品的填充性能不好,就会发生压力降低过大、填充时间过长、填充不满等等情况,从而使制品存在质量问题。
为了提高制品在成型时的填充性能,改善成型制品的质量,一般可以从下列几个方面来考虑:
1)改换科悦另一系列的产品;
2)改变浇口位置;
3)改变注射压力;
4)改变零件的几何形状。
通常将注射压力的控制分成为一次注射压力、二次注射压力(保压)或三次以上的注射压力的控制。
压力切换时机是否适当,对于防止模内压力过高、防止溢料或缺料等都是非常重要的。
模制品的比容取决于保压阶段浇口封闭时的熔料压力和温度。
如果每次从保压切换到制品冷却阶段的压力和温度一致,那么制品的比容就不会发生改变。
在恒定的模塑温度下,决定制品尺寸的最重要参数是保压压力,影响制品尺寸公差的最重要的变量是保压压力和温度。
例如:在充模结束后,保压压力立即降低,当表层形成一定厚度时,保压压力再上升,这样可以采用低合模力成型厚壁的大制品,消除塌坑和飞边。
保压压力及速度通常是塑料充填模腔时最高压力及速度的50%~65%,即保压压力比注射压力大约低
0.6~0.8MPa。
由于保压压力比注射压力低,在可观的保压时间内,油泵的负荷低,固油泵的使用寿命得以延长,同时油泵电机的耗电量也降低了。
采用预先调节好一定的计量,使得在注射行程的终点附近,螺杆端部仍残留有少量的熔体(缓冲量),根据模内的填充情况进一步施加注射压力(二次或三次注射压力),补充少许熔体。
这样,可以防止制品凹陷或调节制品的收缩率。
冷却时间主要取决于熔体温度、制品的壁厚和冷却效率。
此外,物料的硬度也是一个因素。
与很软的品种比较,较硬的品种在模具内将较快地凝固。
如果从两侧进行冷却,那么每0.100’ 壁厚所需的冷却时间通常将是大约10到15秒。
包胶方式的制品将需要较长的冷却时间,因为它们可以通过较小的表面积而有效地冷却。
每0.100’壁厚所需的冷却时间将是大约15到25秒。
1 塑料成型不完整
(1)进料调节不当,缺料或多料。
(2)注射压力太低,注射时间短,柱塞或螺杆退回太早。
(3)注射速度慢。
(4)料温过低。
2 溢料(飞边)
(1)注射压力过高或注射速度过快。
(2)加料量过大造成飞边。
(3)机筒、喷嘴温度太高或模具温度太高都会使塑料黏度下降,流动性增大,在流畅进模的情况下造成飞边。
3 银纹、气泡和气孔
(1)料温太高,造成分解。
(2)注射压力小,保压时间短,使熔料与型腔表面不密贴。
(3)注射速度太快,使熔融塑料受大剪切作用而分解,产生分解气;注射速度太慢,不能及时充满型腔造成制品表面密度不足产生银纹。
(4)料量不足、加料缓冲垫过大、料温太低或模温太低都会影响熔料的流动和成型压力,产生气泡。
(5)螺杆预塑时背压太低、转速太高,使螺杆退回太快,空气容易随料一起推向机筒前端。
4 烧焦暗纹
(1)机筒、喷嘴温度太高。
(2)注射压力或预塑背压太高。
(3)注射速度太快或注射周期太长。