石油化工管式工艺加热炉简介
加热炉学习

一、管式加热炉的结构及工作原理1.1 管式加热炉在炼油和石油化工中的重要性管式加热炉是一种火力加热设备,它利用燃料在炉膛内燃烧时产生的高温火焰与烟气作为热源,加热在炉管中高速流动的介质,使其达到工艺规定的温度,以供给介质在进行分馏、裂解或反应等加工过程中所需的热量,保证生产正常进行。
与其他加热方式相比,管式加热炉的主要优点是加热温度高(可达1273K),传热能力高和便于操作管理。
近60多年所来,管式炉的发展很快,已成为近代石化工业中必不可少的工艺设备之一,在生产和建设中具有十分重要的地位。
例如:一个年处理量为2.5Mt原油的常减压蒸馏装置,虽所用的加热炉的座数不多,但其提供的总热量却达70MW,如果炉子加热能力不够,就会限制整个装置处理能力的提高,甚至无法完成预定的任务。
管式加热炉消耗的燃料量相当可观,一般加工深度较浅的炼厂,约占其原油能力的3%~6%,中等深度的占4%~8%,较深的为8%~15%,其费用约占操作费用的60%~70%,因此,炉子热效率的高低与节约燃料降低成本有密切的关系。
此外,管式炉炉管结焦、炉管烧穿、炉衬烧塌等事故也常常是迫使装置停工检修的重要原因。
在生产中,希望生产装置能达到高处理量、高质量和低消耗以及长周期、安全运转,大量实践表明,管式炉的操作往往是关键之一。
管式炉的基建投资费用,一般约占炼油装置总投资的10%~20%,总设备费用的30%左右,在重整制氢和裂解等石油化工装置中,则占建设费用的25%左右,因此,加热炉设计选型的好坏,还直接影响装置经济的合理性。
1.2 管式加热炉的分类和主要工艺指标1.2.1管式加热炉的分类管式炉的类型很多,如按用途分有纯加热和加热-反应炉,前者如:常压炉、减压炉,原料在炉内只起到加热(包括汽化的作用);后者如:裂解炉、焦化炉,原料在炉内不仅被加热,同时还应保证有一定的停留时间进行裂解或焦化反应。
按炉内进行传热的主要方式分类,管式炉有:纯对流式、辐射-对流式和辐射式。
管式加热炉系统单元操作手册

文档编号:TSS_FURN.DOC管式加热炉单元仿真培训系统操作说明书北京东方仿真软件技术有限公司二〇〇六年十月目录一、工艺流程说明 (2)1、工艺流程简述 (2)2、本单元复杂控制方案说明 (3)3、设备一览 (3)二、本单元操作规程 (3)1、开车操作规程 (3)2、正常操作规程 (6)3、停车操作规程 (7)4、复杂控制系统和联锁系统 (8)5、仪表一览表 (9)三、事故设置一览 (12)四、流程仿真界面 (15)附:思考题 (17)一、工艺流程说明1、工艺流程简述本单元选择的是石油化工生产中最常用的管式加热炉。
管式加热炉是一种直接受热式加热设备,主要用于加热液体或气体化工原料,所用燃料通常有燃料油和燃料气。
管式加热炉的传热方式以辐射传热为主,管式加热炉通常由以下几部分构成:辐射室:通过火焰或高温烟气进行辐射传热的部分。
这部分直接受火焰冲刷,温度很高(600-1600℃),是热交换的主要场所(约占热负荷的70-80%)。
对流室:靠辐射室出来的烟气进行以对流传热为主的换热部分。
燃烧器:是使燃料雾化并混合空气,使之燃烧的产热设备,燃烧器可分为燃料油燃烧器,燃料气燃烧器和油一气联合燃烧器。
通风系统:将燃烧用空气引入燃烧器,并将烟气引出炉子,可分为自然通风方式和强制通风方式。
1.1、工艺物料系统某烃类化工原料在流量调节器FIC101的控制下先进入加热炉F-101的对流段,经对流的加热升温后,再进入F-101的辐射段,被加热至420℃后,送至下一工序,其炉出口温度由调节器TIC106通过调节燃料气流量或燃料油压力来控制。
采暖水在调节器FIC102控制下,经与F-101的烟气换热,回收余热后,返回采暖水系统。
2.2、燃料系统燃料气管网的燃料气在调节器PIC101的控制下进入燃料气罐V-105,燃料气在V-105中脱油脱水后,分两路送入加热炉,一路在PCV01控制下送入常明线;一路在TV106调节阀控制下送入油—气联合燃烧器。
粗苯管式炉工作原理

粗苯管式炉工作原理粗苯管式炉是一种常用的化工设备,主要用于石油化工行业中的精馏和分离过程。
它的工作原理是利用热交换的方式将原料加热至蒸发温度,然后通过冷凝器将蒸汽冷凝成液体。
粗苯管式炉的主要部件包括加热炉、蒸发器、冷凝器和分馏塔。
首先,原料通过进料管进入加热炉,经过加热炉内的加热管加热。
加热管中通有燃料或燃气,通过燃料燃烧释放出的热量加热管道壁,使管道壁温度升高,从而将原料加热。
加热后的原料进入蒸发器,蒸发器内设置有多根管子,这些管子周围通有加热介质,使管子内的原料蒸发。
蒸发过程中,原料中的易蒸发组分被蒸发出来,形成蒸汽。
蒸汽随后进入冷凝器。
冷凝器中的管子外部通有冷却介质,使管子内的蒸汽冷凝成液体。
蒸汽在冷凝器中传热给冷凝介质,使冷凝介质的温度升高。
而原料则从冷凝器中以液体形式排出。
通过冷凝的液体进入分馏塔,分馏塔内设置有多个塔板。
液体从上部进入分馏塔,沿着塔板逐渐下降,并与从下部进入的热蒸汽接触。
在分馏塔内,由于液体和蒸汽的接触,易蒸发组分会从液体中蒸发出来,向上升至更高的塔板。
而不易蒸发组分则倾向于留在液体中,向下沉降至更低的塔板。
经过多次蒸发和冷凝的过程,分馏塔最终可以将原料分离成不同组分。
粗苯管式炉的工作原理可以通过以上的描述得以解释。
通过加热炉的加热,原料被加热至蒸发温度,然后进入蒸发器蒸发,形成蒸汽。
蒸汽通过冷凝器冷凝成液体,然后进入分馏塔进行分离。
这一过程使得原料中的不同组分可以被有效地分离出来。
在实际应用中,粗苯管式炉可以根据需要进行多级加热和分离,以实现更高效的分离效果。
同时,炉内的加热介质和冷凝介质的选择也会影响炉的工作效果。
因此,在设计和操作粗苯管式炉时,需要综合考虑各种因素,并进行合理的优化。
粗苯管式炉是一种重要的化工设备,通过加热、蒸发、冷凝和分馏等过程,实现了原料的分离和提纯。
它的工作原理简单明了,但在实际应用中需要考虑多种因素,以达到预期的分离效果。
通过不断的优化和改进,粗苯管式炉在石油化工行业中发挥了重要作用。
管式炉概述
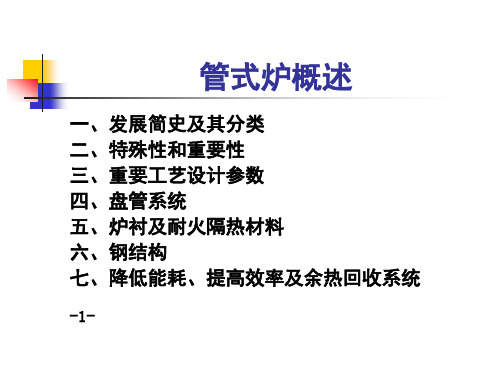
五、炉衬及耐火隔热材料
●炉衬结构—砖结构、衬里(浇注料、可塑料)、 陶瓷纤维结构、复合结构
●炉衬材料选择—热面温度、温度裕量、耐火隔热 材料的分类温度或等级温度、烟气的腐蚀性
●炉衬厚度计算
●炉墙外壁温度—SH/T3036规定:环境温度27℃, 无风条件下,外壁温度不高于80℃。
-10-
六、钢结构
-3-
二、特殊性和重要性
2.1特殊性 与石油化工装置中的其它设备相比,管式炉的特殊
性在于直接火焰加热,即是直接见火设备;与一 般工业炉相比,管式炉的盘管要承受高温、高压 和介质腐蚀;与锅炉相比,管式炉盘管内的介质 不是水和蒸汽,而是易燃、易爆、易裂解、易结 焦和腐蚀性较强的油和气。这些就是石油化工管 式炉的特殊性。
-4-
2.2重要性
管式炉在石油化工装置中的地位之所以重要,在于它是 主要的热能供应设备,同时也是节能的关键设备;其 基建投资占有相当高的比例;它是主要的污染源,也 就是解决环保问题的主要对象。
管式炉的燃料消耗占装置能耗的比例,管式炉投资占装 置投资的比例如下:
常减压 焦 化 连续重整 柴油加氢 制 氢 能耗比例 % 82~92 ~90 ~80 ~30 工程费 % 10~17 10~12 12~16 6~8 20~25
简化的热效率反平衡表达式 : η=(1-q1-q2-q3)×100%
η-加热炉热效率 q1 –排烟损失占总供热的比值,是排烟温度和过剩空气系
数的函数 q2 –不完全燃烧损失占总供热的比值 q3 –散热损失占总供热的比值
-14-
7.2.1降低排烟温度以减少排烟损失
⑴ 减小末端温差 ⑵ 将需要加热的低温介质引入对流室末端。 ⑶采用各种空气预热器以预热空气 ⑷采用烟气余热锅炉以发生蒸汽 ⑸除灰除垢,保证管式炉长期高热效率运转 7.2.2降低过剩空气系数以减少排烟损失 7.2.3减少不完全燃烧损失 7.2.4减少散热损失 -15-
管式加热炉炉管壁厚的设计计算

管式加热炉炉管壁厚的设计计算摘要本文介绍了石油化工管式加热炉炉管壁厚的切合实际的设计计算方法,举例说明了该计算方法,从而使复杂计算简单化。
〔关键词〕管式加热炉炉管壁厚设计计算管式加热炉是石油炼制、石油化工和化学、化纤工业中使用的工艺加热炉。
管式加热炉炉管一般都在高温、高压和腐蚀性介质中长期工作,所以除了应选择适宜的材质外,炉管壁厚的确定显得尤为重要。
一、炉管壁厚的计算方法:石油化工管式炉的操作条件各不相同,炉管壁温也有很大差别,在较低温度下操作的炉管,蠕变效果不存在或可忽略,管壁金属在弹性范围内工作;而在较高温度下操作的炉管(在裂解炉中,管壁温度可达680℃),管壁金属温度高到足以产生显著蠕变时,甚至在腐蚀或氧化不太严重时,炉管也会由于蠕变-断裂而失效。
因此,炉管壁厚计算应按下列三种情况进行:a.设计温度低于材料蠕变断裂温度下限时采用弹性设计。
b.设计温度高于材料蠕变断裂温度下限时采用断裂设计。
c.设计温度处于材料蠕变断裂温度下限附近时应分别按上述两种方法设计,取其较大值作为计算壁厚。
材料的蠕变断裂温度下限是指弹性许用应力和断裂许用应力曲线交点下的温度。
1.应力厚度和最小计算厚度①弹性设计:设计基础是当腐蚀裕量已经耗尽,接近设计寿命末期时,防止在最高压力下(接近p)由于破裂而损坏。
应力厚度Ss和最小计算厚度Sm按下两式计算:Ss=peDo/(2[σ]e+pe) 或 Ss=peDi/(2[σ]e-pe)Sm= Ss+C式中 Ss 应力厚度,mm;Sm 最小计算厚度,mm;P e 弹性设计压力,Mpa;Do 炉管内径,mm;[σ]e 弹性许用应力,Mpa;C 腐蚀裕量,mm。
②蠕变-断裂设计:设计基础是在设计寿命期间,防止由于蠕变-断裂而破坏。
Ss和Sm按下面两式计算:Ss=prDo/(2[σ]r+pr) 或 Ss=prDi/(2[σ]r-pr)Sm= Ss+fC式中 pr 蠕变-断裂设计压力,Mpa;[σ]e 蠕变-断裂许用应力,Mpa;f 腐蚀分数。
管式加热炉

第五章管式加热炉一、管式加热炉的工作原理管式加热炉一般由三个主要部分组成:辐射室、对流室及烟囱,图5-1是一典型的圆筒炉示意图。
炉底的油气联合燃烧器(火嘴)喷出高达几米的火焰,温度高达1000~1500℃、主要以辐射传热的方式,将大部分热量传给辐射室(又叫炉膛)炉管(也叫辐射管)内流动的油品。
烟气沿着辐射室上升到对流室,温度降到700~900℃。
以对流传热的方式继续将部分热量传给对流室炉管内流动着的油品,最后温度降至200~450℃的烟气从烟囱排人大气。
油品则先进入对流管再进入辐射管,不断吸收高温烟气传给的热量,逐步升高到所需要的温度。
辐射室是加热炉的核心部分,从火嘴喷出的燃料(油或气)在炉膛内燃烧,需要一定的空间才能燃烧完全,同时还要保证火焰不直接扑到炉管上,以防将炉管烧坏,所以辐射室的体积较大。
由于火焰温度很高(最高处可达1500~1800℃左右),又不允许冲刷炉管,所以热量主要以辐射方式传送。
在对流室内,烟气冲刷炉管,将热量传给管内油品,这种传热方式称为对流传热。
烟气冲刷炉管的速度越快,传热的能力越大,所以对流室窄而高些,排满炉管,且间距要尽量小。
有时为增加对流管的受热表面积,以提高传热效率,还常采用钉头管和翅片管。
在对流室还可以加几排蒸汽管,以充分利用蒸汽余热,产生过热蒸汽供生产上使用。
烟气离开对流室时还含有不少热量,有时可用空气预热器进行部分热量回收,使烟气温度降到200℃左右,再经烟囱排出,但这需要用鼓风机或引风机强制通风。
有时则利用烟囱的抽力直接将烟气排入大气。
由于抽力受烟气温度、大气温度变化的影响,要在烟道内加挡板进行控制,以保证炉膛内最合适的负压,一般要求负压为2~3mm水柱,这样既控制了辐射室的进风量,又使火焰不向火门外扑,确保操作安全。
二、管式加热炉的主要工艺指标1.加热炉热负荷。
每小时传给油品的总热量称为加热炉热负荷(千卡/小时),表明加热炉能力的大小,国内炼油厂所用的管式加热炉最大热负荷在4200万千卡/小时左右。
第四章管式加热炉
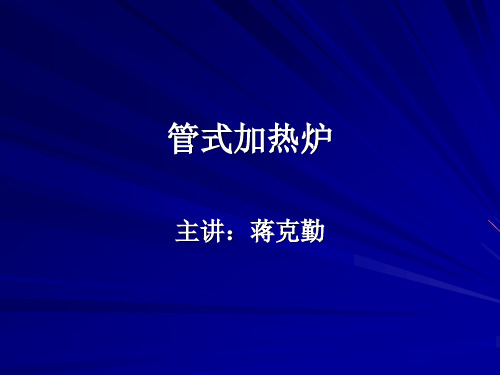
混 合 的 先 后 可 分 为
预混式 :结构复杂,对燃料要求高,易发生回火。 喷射式 :瓦斯-空气未经预先混合,而是由燃烧器
的不同通道分别进入炉内,然后借助扩 散作用使两者在炉中边混合、边燃烧(即 扩散燃烧)。 半预混式 一部分空气靠引射器吸入预先混合 (一次空气),其余部分则靠外部大气供 给,与燃料边烧边混合(二次空气)。
燃烧必须具备的条件:可燃物、空气、温度 燃料的化学组成:C、H、少量的S、N、O等元素
理 按化学反应的需氧量
论 C+O2=CO 2
燃烧1kg碳需用氧=2.67 kg
空 2H2+O2=2H2O 燃烧1kg氢需用氧=8 kg
气 S+O2=SO2
燃烧1kg硫需用氧=1 kg
量 燃烧1kg燃料由空气供给的理论用氧量为(kg)
管式加热炉的其他部件
一、炉管:是加热炉形成传热表面最重要的 组成部分。主要考虑耐热性、耐腐蚀性、 机械强度、炉管表面热强度。
二、回弯头:将炉管连成一个整体的部件, 分为可拆和不可拆两种。与炉管连接有膨 胀法和焊接法。
三、管件与管板:为防止炉管在炉内受热弯 曲变形而采用管架支持,用耐高温的合金 钢制造。
按燃烧所用空气的供给方式可分为
引射式(空气靠瓦斯本身吸入)和混合式 (空气靠鼓风机供给)
液体燃烧器(油嘴)
雾 机械雾化
化 方
低压空气雾化
法 高压水蒸气雾化(炼油厂常用)
高压水蒸气雾化燃烧器:
水蒸汽与燃料油在燃烧器内不进行混合, 二者由不同的孔道分别喷出。
水蒸汽与燃料油在火嘴内混合形成泡沫状 物质,再由小孔按适宜角度喷入空气流中。 (内混式水蒸气雾化燃烧器)
无焰燃烧炉,即把双面辐射与无焰火嘴相结 合的一种新型炉。
石油化工管式炉的基础知识

石油化工管式炉的基础知识管式加热炉是石油炼制、石油化工和化学、化纤工业使用的。
工业中使用的工艺加热炉,它具有其他工业炉所没有的若干特点。
1.工作原理石油化工管式炉是直接见火的加热设备,燃料在管式炉的辐射室内燃烧,释放出的热量主要通过辐射传热和对流传热传递给炉管,再经过传导传热和对流传热传热传递给管内的被加热介质,这就是管式炉的工作原理。
2.管式加热炉的特征是:(1)被加热物质的管内流动,故仅限于加热气体或液体。
而且,这些气体或液体通常都是易燃的烃类物质,同锅炉加热水或蒸汽相比,危险性大,操作条件要苛刻得多。
(2)加热方式为直接受火式。
(3)只烧液体或气体燃料。
(4)长周期连续运转,不间断操作。
3.管式加热炉的分类3.1 按功能分类;加热型管式炉和加热-反应型管式炉3.2 按炉型分类:圆筒炉、立式炉和大型箱式炉3.3 按工艺用途分类;加热炉和反应炉反应炉:炉管类被加热的物料在压力和催化剂作用下进行反应。
4.管式加热炉结构管式加热炉的一般结构:一般由辐射室、对流式、余热回流系统、燃烧器以及通风系统五部分组成。
4.1 辐射室辐射室是通过火焰或高温烟气进行辐射传热的部分。
这个部分直接受到火焰冲刷,温度最高,必须充分考虑说用材料的强度、耐热性能等。
这个部分是热交换的主要场所,全炉热负荷的70%-80%是由辐射室担负的,它是全炉最重要的部位。
烃蒸汽转化炉、乙烯裂解炉等,其反应和裂解过程全部都用辐射室来完成。
可以说,一个炉子是优是劣主要看它的辐射室性能如何。
4.2 对流室对流室是靠由辐射室出来的烟气进行对流换热的部分,但实际上它也是有一部分辐射热交换,而且有时辐射换热还占有破大的比例。
所谓对流室不过是指“对流传热起支配作用”的部位。
对流室内密布多排炉管,烟气比较大速度冲刷这些管子,进行有效的对流换热。
对流室一般担负全炉热负荷的20%~30%。
对流室吸热量的比例越大,全炉的热效率越高,但究竟占多少比例合适应根据管内流体同烟气的温度差和烟气通过对流管排的压力损失等,选择最经济合理的比值。
- 1、下载文档前请自行甄别文档内容的完整性,平台不提供额外的编辑、内容补充、找答案等附加服务。
- 2、"仅部分预览"的文档,不可在线预览部分如存在完整性等问题,可反馈申请退款(可完整预览的文档不适用该条件!)。
- 3、如文档侵犯您的权益,请联系客服反馈,我们会尽快为您处理(人工客服工作时间:9:00-18:30)。
石油化工管式工艺加热炉简介郑战利管式加热炉在一个有衬里的密闭体内设置有大量的相互连接的优质或合金无缝钢管,被加热介质在一连串的无缝钢管内以很高流速通过,燃料在密闭体内燃烧产生高温烟气,高温烟气通过辐射、对流和传导把热量传给被加热介质,把被加热介质加热到生产工艺规定的温度或完成一定的化学反应深度;这类设备统称为管式加热炉。
管式加热炉的范畴包含热水和蒸汽锅炉、热载体加热炉、油田水套炉、输油管道加热炉、炼油和石化生产装置的工艺加热炉等。
今天我们所讲的管式加热炉是炼油和石油化工生产装置的工艺加热炉,简称为石化工艺加热炉。
石化工艺加热炉的主要特点是1.被加热介质为易燃、易爆的液体或气体,且温度和压力较高。
操作条件苛刻。
安全运行要求高。
2.加热方式为明火加热。
3.长周期连续生产。
4.所用燃料为液体或气体燃料。
管式加热炉应满足的要求1.完成一定的传热任务,燃料耗量少、需要的传热面积小。
2.被加热介质不受局部过热。
3.在纯加热型管式加热炉中,被加热介质无分解或仅有极少量分解。
4. 在加热—反应型管式加热炉中,保证被加热介质的反应深度达到生产工艺要求,且炉管中结焦量最少。
5.安全、稳定、连续运行周期在3~5年。
6. 排烟中的有害物含量和噪声必须符合国家标准规定。
管式加热炉的主要操作参数1、有效热负荷:为各种被加热介质从体系入口状态到出口状态所吸收的能量之和,它等于供给能量与损失能量之差,Kw2、排烟损失热量:排出体系的烟气带走的热量。
Kw3、燃料不完全燃烧损失热量:由于燃烧设备及燃烧工况等原因造成燃料没有完全燃烧而未能释放出的反应热。
Kw4、散热损失热量:体系内所有设备及管线表面向周围环境中散失的热量。
Kw5、附属设备能耗:鼓风机、引风机、吹灰器、热载体循环泵等辅助设备所耗掉的能量,按供给这些设备的能量计算。
Kw6、燃料效率:有效吸能量占供给燃料燃烧放出热量的百分数,其数值可能大于l00%。
%7、全炉热效率:有效吸能量占供给炉子总热量(不含附属设备损失)的百分数。
%8、综合效率:是体系供给能量利用的有效程度在数量上的表示,它等于有效能量对供给能量的百分数。
%9、炉膛热强度:指单位时间内单位炉膛体积所传递的热量,单位为kw/m3。
10、炉管平均表面热强度:指单位时间内单位炉管表面积所传递的热量,单位为kw/m2。
11、排烟温度:烟气离开被加热介质加热段的最终温度。
℃12、排烟氧含量:烟气最终离开被加热介质加热段时中的氧含量。
V%13、炉膛Tp温度:烟气出辐射室时的温度。
℃14、燃烧过剩空气系数:燃料燃烧理论空气量与供风量的比值。
15、燃料耗量:单位时间内,加热炉消耗燃料总和(Kg/h或Nm3/h)。
16、质量流量:单位时间内,流过单位炉管内截面积的加热介质的质量(Kg/m2.h)。
17、全炉压力降:被加热介质流过炉管系统的压力损失。
MPa管式加热炉的结构简介石油化工工艺管式加热炉由辐射室、对流室、余热回收装置、燃烧器、供风系统和排烟系统等部分所组成(由炉管系统、钢结构、衬里、余热回收装置、燃烧器、供风系统和排烟系统等部分所组成)。
辐射室辐射室是加热炉辐射传热起支配作用的部分。
由于是火焰直接所在的场所,所以它是加热炉温度最高的部分,对其所用材料的成分、强度、厚度和机械的结构,需要仔细考虑,同时在功能上,全炉热负荷70~80%的热量是在辐射室被吸收。
在流体有反应转化和裂解的炉子上,反应和裂解等一般都全部在辐射室内完成。
所以说辐射室的好坏决定加热炉的好坏,并非过言。
对流室对流室是加热炉对流传热起支配作用的部分,对流室有排列很密的管束,这种结构使得烟气通过对流管的速度提高,得到有效的对流传热。
一般对流室吸收全炉热负荷的20~30%的热量。
对流室可设在辐射室上部;也可设在地面上,用烟道与炉本体连接,但在本质上机理一样。
在对流室可以采用钉头管或翅片管。
余热收回装置余热收回装置是指用来回收对流室出来的烟气,或者当没有对流室时直接从辐射室出来的烟气中热量的设备。
目前国内外各炼厂采用的余热回收措施大致有以下几种类型:1.从工艺流程与装置总体平衡考虑,冷进料–热油空气预热空气。
2.从改进和简化循环系统考虑有热载体循环–热油空气预热空气。
,包括开路与闭路热载体循环。
3.从增加附属回收设备考虑,有①钢管式;②玻璃管式;③回转式;④铸铁管式;⑤扰流子式;⑥热管式;⑦板式空气预热器等。
4.从与其他设备联合节能考虑,有①余热锅炉;②热电联产。
燃烧器燃烧器是加热炉的重要组成部分之一,技术性能的优劣以及是否与加热炉工艺要求、炉型结构、传热特点相匹配对加热炉的运行、能耗或环保都有着直接影响。
选用技术性能与加热炉工艺要求、炉型结构、传热特点相匹配的燃烧器对保证加热炉高效或“长、安、稳、满”运行有着重要意义。
通风装置通风装置的职能是把燃烧用空气引进的同时,把烟气向炉外排出,有自然通风和强制通风两种。
前者靠烟囱的通气力;后者用引风机,强力引出烟气。
一般炉内压力损失小时,多采用烟囱自然通风方式,烟囱安装在炉的上部,与加热炉成为一体,烟囱的高度,以克服炉内的压力损失,并保持充分的通风力为佳。
加热炉构造复杂,炉内压力损失大的加热炉或有废热回收装置的加热炉多采用安装引风机,强力通风方式。
炉管和弯头炉管和弯头是管式加热炉中最重要的部分,占管式加热炉总钢材量的40%,总投资的60%。
因为要耐压力,耐腐蚀,抵抗火焰的直接灼热,为了完成工艺任务和生产安全,根据下列标准设计炉管:⏹炉管的长度和总根数根据管式加热炉的热负荷、热效率和加热炉的构造来决定。
⏹管径和管程数,根据流量、允许压力损失、停留时间决定。
⏹壁厚由内部压力、热应力、静荷重、管壁温度、材料强度(包括高温蠕变性和脆性等)和腐蚀裕度等决定。
⏹材料由许用温度及高温强度(包括蠕变强度)、耐热性、腐蚀性和脆性等决定。
炉管温度低于500℃时使用碳钢炉管;炉管温度在500℃~700℃时使用低合金钢炉管(T9~T22);炉管温度在700℃~800℃时使用不锈钢炉管(304、316);炉管温度在800℃~900℃时使用309炉管;炉管温度超过900℃时使用高合金钢离心浇铸炉管(HK-40)。
⏹管式加热炉辐射炉管采用光管,对流室采用钉头管或翅片管。
⏹炉管与弯头连接方式有焊接和胀接两种。
采用焊接时,弯头为炉管压制成的急弯弯头,以180°的弯头为代表,铸造的不多。
采用胀接时,采用有堵头的铸造回弯头,卸下堵头,管内能够用机械清焦,缺点是较贵,材料和炉管相同。
如被加热油品较轻,炉管不易结焦或采用了在线清焦技术的加热炉可全部采用急弯弯头,如被加热油品较重,炉管易结焦,且没采用了在线清焦技术的加热炉可在辐射室部分采用铸造回弯头。
管支架和导架管支架承受炉内加热管的重量,并将其重量传给加热炉的框架。
管支架要具备的条件是:优越的抗氧化腐蚀性能和高的高温强度,以及随着加热管的温度变化,在结构上,管支架可以保持伸缩自由。
管支架的材料,在辐射室和对流室下部采用25Cr—12Ni钢或25Cr—20Ni钢。
在对流室上部采用密烘铸铁“HR”和5Cr合金钢。
采用高铬钢存在的问题是高温脆性,还有燃料中含钒硫所引起的腐蚀。
在这种场合支架应设计成具有可换性的构造,对高温脆性要用铁素体加以抑制,对钒的腐蚀可用浇注保护层处理。
一般在辐射室采用刀架形管支架,在对流室采用孔板形管支架,导管架仅起管子导向作用。
耐火材料耐火材料是加热炉的必需材料,大致分为定形的材料和非定形的材料两种。
a.定形耐火材料定形耐火材料就是重质耐火砖、轻质耐火砖和保温砖等,重质耐火砖以耐火性为主,用于燃烧器的燃烧道、温度较高加热炉辐射室迎火面衬里。
轻质耐火砖兼具有耐火性和保温性,多用于炉的侧壁和炉顶。
保温砖的耐热性很低,多用于炉底和侧壁的内衬里,用量不多。
非定形耐火材料b.b. 非定形耐火材料一般指由骨料和水泥用水和成,象混凝土那样施工的无定形耐火材料,简称为浇注料。
分为以耐火性为主,并具有一定的保温性的浇注料(重质浇注料)和保温型的浇注料(轻质),施工方法有注入、涂抹和喷抹三种。
对于管式加热炉,以耐火性为主,并具有一定的保温性可塑浇注料,用于炉顶、侧壁和炉底。
烟道和烟囱衬里及侧壁的内衬里,则采用保温性的可塑浇注料。
陶纤块、岩棉毡、陶纤喷涂也属于非定型耐火材料。
炉框架、侧壁和平台炉框架是承受加热炉全部荷重的钢结构,材料是普通碳钢,多用槽钢和工字钢。
侧板就是炉壁外表面的钢板,其作用是防雨、防尘,同时防止不必要的空气漏入炉内,按作用可以分为分担部分钢结构荷重和仅起覆盖作用两类。
平台和梯子是为操作和维修而设立,用于日常操作维修和检查。
主要炼油装置加热炉简介烟气阻断档板调节档板声波吹灰器三 焦化加热炉焦化加热炉由钢结构,耐火隔热衬里,辐射和对流炉管,燃烧器,烟气余热回收器,供风系统和烟气排放系统等主要部件组成. 是延迟焦化装置的核心设备,它为整个装置提供热量,其能耗占整个延迟焦化装置能耗的75%;也是影响延迟焦化装置操作的平稳性和生产周期的关键设备。
由于卧管立式加热炉具有结构简单,可以安装较多数量的燃烧器;水平炉管内介质流动状态稳定;沿炉管长度方向受热较均匀;便于炉管内清焦等优点,延迟焦化加热炉均为卧管立式加热炉。
石化工艺加热炉的发展过程在炼油工程上,采用管式加热炉开始于1910年~1911年间,在没有采用管式加热炉之前原油加工方式均为釜式蒸馏,小处理量、且为间歇生产。
管式加热炉的使用是炼油工业由小处理量、间歇生产转向大处理量、连续生产的标志。
初期的管式加热炉为如图-1所示的堆形炉。
传热面由一管束所组成。
管与管之间的联接件也置于炉中。
最低一排的受热强度达到56-78 kw/m2,而最上排管的受热强度就不超过9-11kw/m2,因此下排管常常被烧坏,而管间联接件也易松漏引起火灾。
但上排炉管的效率却又很低。
为了克服堆形管式加热炉存在的缺点,人们设计出了一种只装对流管的管式加热炉,如图-2所示。
当时的设想是既然堆形炉的最下排炉管直接受到高温燃气的辐射,表面热强度很高,因此用火墙把管子和燃烧室隔开,使炉管受不到火焰的辐射,那些炉管过热的问题就应该能解决。
但是实践的结果证明这种设想是不符合实际的,因为燃料燃烧生成的高温烟气在进入对流室之前,没有和一个吸热面进行热交换,烟气温度过高的问题没有得到解决,头几排管子仍有被烧坏的危险。
若减低火墙上烟道气的温度,则必须大量增加过剩空气,这就降低了炉子的热效率,并会引起炉管表面氧化的加剧。
这种炉子比堆形炉完善些,管子接头在对流室外安装,后来并采用了回弯头,减少了火灾的危险。
钢材消耗有所下降,但炉的热效率太低,因此在保护炉顶对流管的不受损坏以求降低炉管更换率,降低钢材消耗的同时,却带来了燃料消耗太大及炉管氧化这一后果。