制动主缸设计计算共23页文档
(完整word版)制动系统设计
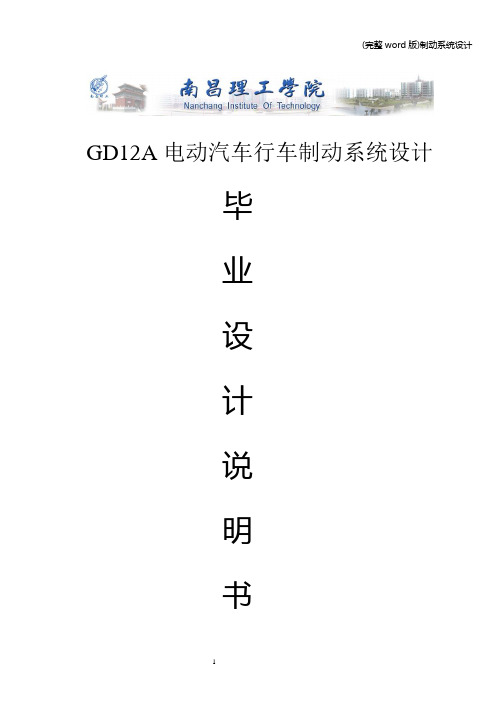
GD12A电动汽车行车制动系统设计毕业设计说明书姓名:俞翼鸿专业:汽车维修与检测班级:(2)指导老师: 邹章鸣南昌理工学院机械工程系1.。
目录摘要Troduction前言第一章绪论 (6)1。
1 制动系统设计的意义 (6)1。
2 制动系统研究现状 (6)1.3 本次制动系统应达到的目标 (6)1.4 本次制动系统设计要求 (6)第二章制动系统方案论证分析与选择 (7)2.1 制动器形式方案分析 (7)2。
1.1 鼓式制动器 (7)2。
1。
2 盘式制动器 (9)2。
2 制动驱动机构的结构形式选择 (10)2.2.1 简单制动系 (10)2。
2。
2 动力制动系 (10)2。
2。
3 伺服制动系 (11)2。
3 液压分路系统的形式的选择 (11)2.3.1 II型回路 (11)2.3.2 X型回/路 (12)2。
3。
3 其他类型回路 (12)2。
4 液压制动主缸的设计方案 (12)第三章制动系统设计计算 (15)3.1 制动系统主要参数数值 (15)3.1.1 相关主要技术参数 (15)3.1.2 同步附着系数的分析 (15)3.2 制动器有关计算 (16)3.2。
1 确定前后轴制动力矩分配系数β (16)3。
2。
2制动器制动力矩的确定 (16)3.2。
3 后轮制动器的结构参数与摩擦系数的选取 (17)3.2.4 前轮盘式制动器主要参数确定 (18)3。
3 制动器制动因数计算 (19)3.3.1 前轮盘式制动效能因数 (19)3.3。
2 后轮鼓式制动器效能因数 (19)3。
4 制动器主要零部件的结构设计 (20)第四章液压制动驱动机构的设计计算 (22)4。
1 后轮制动轮缸直径与工作容积的设计计算 (22)4.2 前轮盘式制动器液压驱动机构计算 (23)4.3 制动主缸与工作容积设计计算 (24)4.4 制动踏板力与踏板行程 (24)4.4。
1 制动踏板力 (24)4.4.2 制动踏板工作行程 (25)第五章制动性能分析 (26)5.1 制动性能评价指标 (26)5.2 制动距离S (26)5。
(完整版)气缸的设计计算1

4.1纵向气缸的设计计算与校核:由设计任务可以知道,要驱动的负载大小位140N,考虑到气缸未加载时实际所能输出的力,受气缸活塞和缸筒之间的摩擦、活塞杆与前气缸之间的摩擦力的影响,并考虑到机械爪的质量。
在研究气缸性能和确定气缸缸径时,常用到负载率β:由《液压与气压传动技术》表11-1:/β=200N 运动速度v=30mm/s,取β=0.7,所以实际液压缸的负载大小为:F=FD=1.27= =66.26mmF—气缸的输出拉力 N;P —气缸的工作压力Pa按照GB/T2348-1993标准进行圆整,取D=20 mm气缸缸径尺寸系列8 10 12 16 20 25 32 40 50 63 80 (90)100 (110)125 (140)160 (180)200 (220)250 320 400 500 630由d=0.3D 估取活塞杆直径 d=8mm缸筒长度S=L+B+30L为活塞行程;B为活塞厚度活塞厚度B=(0.6 1.0)D= 0.720=14mm由于气缸的行程L=50mm ,所以S=L+B+30=886 mm导向套滑动面长度A:一般导向套滑动面长度A,在D<80mm时,可取A=(0.6 1.0)D;在D>80mm 时, 可取A=(0.6 1.0)d。
所以A=25mm最小导向长度H:根据经验,当气缸的最大行程为L,缸筒直径为D,最小导向长度为:H代入数据即最小导向长度H + =80 mm活塞杆的长度l=L+B+A+80=800+56+25+40=961 mm由《液压气动技术手册》可查气缸筒的壁厚可根据薄避筒计算公式进行计算:式中—缸筒壁厚(m);D—缸筒内径(m);P—缸筒承受的最大工作压力(MPa);—缸筒材料的许用应力(MPa);实际缸筒壁厚的取值:对于一般用途气缸约取计算值的7倍;重型气缸约取计算值的20倍,再圆整到标准管材尺码。
参考《液压与气压传动》缸筒壁厚强度计算及校核,我们的缸体的材料选择45钢,=600 MPa, ==120 MPa n为安全系数一般取 n=5;缸筒材料的抗拉强度(Pa)P—缸筒承受的最大工作压力(MPa)。
制动主缸设计
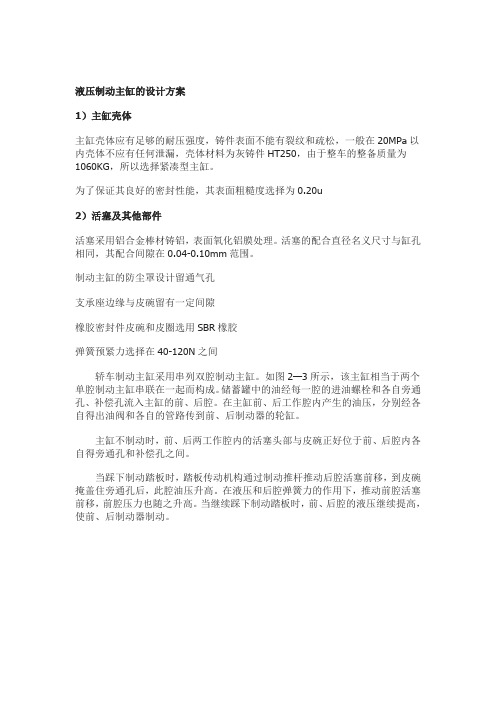
液压制动主缸的设计方案1)主缸壳体主缸壳体应有足够的耐压强度,铸件表面不能有裂纹和疏松,一般在20MPa以内壳体不应有任何泄漏,壳体材料为灰铸件HT250,由于整车的整备质量为1060KG,所以选择紧凑型主缸。
为了保证其良好的密封性能,其表面粗糙度选择为0.20u2)活塞及其他部件活塞采用铝合金棒材铸铝,表面氧化铝膜处理。
活塞的配合直径名义尺寸与缸孔相同,其配合间隙在0.04-0.10mm范围。
制动主缸的防尘罩设计留通气孔支承座边缘与皮碗留有一定间隙橡胶密封件皮碗和皮圈选用SBR橡胶弹簧预紧力选择在40-120N之间轿车制动主缸采用串列双腔制动主缸。
如图2—3所示,该主缸相当于两个单腔制动主缸串联在一起而构成。
储蓄罐中的油经每一腔的进油螺栓和各自旁通孔、补偿孔流入主缸的前、后腔。
在主缸前、后工作腔内产生的油压,分别经各自得出油阀和各自的管路传到前、后制动器的轮缸。
主缸不制动时,前、后两工作腔内的活塞头部与皮碗正好位于前、后腔内各自得旁通孔和补偿孔之间。
当踩下制动踏板时,踏板传动机构通过制动推杆推动后腔活塞前移,到皮碗掩盖住旁通孔后,此腔油压升高。
在液压和后腔弹簧力的作用下,推动前腔活塞前移,前腔压力也随之升高。
当继续踩下制动踏板时,前、后腔的液压继续提高,使前、后制动器制动。
图2—3 制动主缸工作原理图撤出踏板力后,制动踏板机构、主缸前、后腔活塞和轮缸活塞在各自的回位弹簧作用下回位,管路中的制动液在压力作用下推开回油阀流回主缸,于是解除制动。
若与前腔连接的制动管路损坏漏油时,则踩下制动踏板时,只有后腔中能建立液压,前腔中无压力。
此时在液压差作用下,前腔活塞迅速前移到活塞前端顶到主缸缸体上。
此后,后缸工作腔中的液压方能升高到制动所需的值。
若与后腔连接的制动管路损坏漏油时,则踩下制动踏板时,起先只有后缸活塞前移,而不能推动前缸活塞,因后缸工作腔中不能建立液压。
但在后腔活塞直接顶触前缸活塞时,前缸活塞前移,使前缸工作腔建立必要的液压而制动。
某车型制动系统设计计算书(后盘)分析解析
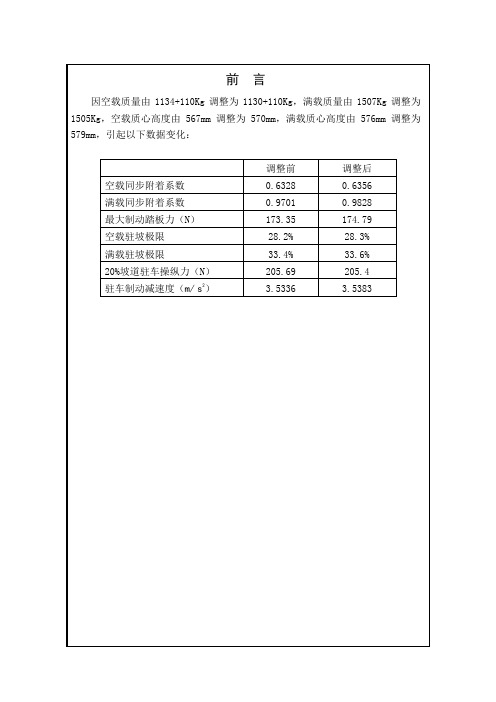
目录1 概述 (1)2 引用标准 (1)3 计算过程 (1)3.1整车参数 (1)3.2理想的前、后制动器制动力分配曲线 (1)3.3NA01制动系统性能校核 (3)3.3.1 NA01制动系统基本参数 (3)3.3.2 制动力分配曲线绘制及同步附着系数确定 (4)3.3.3 前、后轴利用附着系数曲线绘制 (5)3.3.4 空、满载制动距离校核 (7)3.3.5 真空助力器失效时制动减速度校核 (7)3.3.6 ESP系统失效制动减速度校核 (8)3.3.7 任一管路失效制动减速度校核 (8)3.3.8 制动踏板力校核 (8)3.3.9 制动主缸排量校核 (9)3.3.10 制动踏板行程校核 (9)3.3.11 驻车制动校核 (10)4 结论 (12)参考文献 (13)1 概述根据NA01乘用车设计开发目标,设计和开发NA01制动系统,要求尽量沿用M2零部件。
NA01制动系统共有三种配置:ESP+前盘后盘式制动器,ABS+前盘后鼓式制动器,比例阀+前盘后鼓式制动器,此三种配置需分别校核其法规要求符合性。
本计算书是根据整车室提供的NA01整车的设计参数(空载质量、满载质量、轴荷、轴距及质心高度),对经过局部改善(制动主缸直径由22.22mm 更改为20.64mm)的制动系统(ESP+前盘后盘式制动器)的适宜性进行校核计算,以选择合适的参数作为NA01制动系统的设计值。
2 引用标准GB 21670-2008 乘用车制动系统技术要求及试验方法。
GB 7258-2004 机动车运行安全技术条件 3 计算过程 3.1整车参数3.2 理想的前、后制动器制动力分配曲线制动时前、后车轮同时抱死,对附着条件的利用、制动时汽车方向稳定性均较为有利,此时的前、后轮制动器制动力1μF 和2μF 的关系曲线,常称为理想的前、后轮制动器制动力分配曲线。
在任何附着系数ϕ的路面上,前、后车轮同时抱死的条件是:前、后制动器制动力之和等于附着力,并且前、后轮制动器制动力分别等于各自的附着力,即:g F m F 21ϕμμ=+……………………………………(1) gg h L h L ϕϕμμ-+=1221F F (2)经计算得:221ϕϕμLh mg L L mg F g +=…………………………(3) 212ϕϕμLh mg L Lmg F g -= (4)式中:1μF 、2μF ——前、后轮制动器制动力,N ; ϕ——路面附着系数; m ——整车质量,kg ; hg ——汽车质心高度,m; L ——汽车轴距,m;1L ——质心至前轴中心线的距离,m;2L ——质心至后轴中心线的距离,m。
制动主缸DFMEA
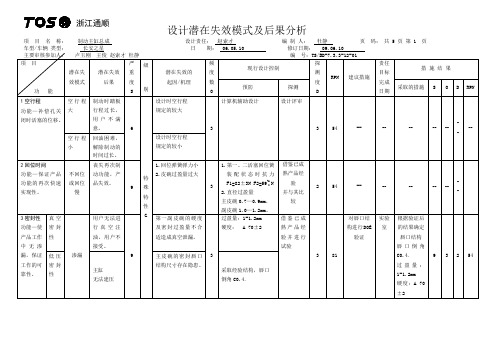
设计潜在失效模式及后果分析
项 目 名 称: 制动主缸总成 设计责任: 赵索才 编 制 人: 杜静 页 码: 共 5 页 第 1 页 车型/车辆 类型: 长安之星 日 期: 06.05.10 修订日期: 09.06.10
浙江通顺
设计潜在失效模式及后果分析
项 目 名 称: 制动主缸总成 设计责任: 赵索才 编 制 人: 杜静 页 码: 共 5 页 第 2 页 车型/车辆类型: 长安之星 日 期: 06.05.10 修订日期: 09.06.10
浙江通顺
设计潜在失效模式及后果分析
项 目 名 称: 制动主缸零部件 设计责任: 赵索才 编 制 人: 杜静 页 码: 共 5 页 第 3 页 车型/车辆类型: 长安之星 日 期: 06.05.10 修订日期: 09.06.10
浙江通顺
浙江通顺
设计潜在失效模式及后果分析
项目名称:制动主缸零部件设计责任:赵索才编制人:杜静页码:共5 页第 4 页车型/车辆类型:长安之星日期: 06.05.10 修订日期: 09.06.10
设计潜在失效模式及后果分析
项 目 名 称: 制动主缸零部件 设计责任: 赵索才 编 制 人: 杜静 页 码: 共 5 页 第 5 页 车型/车辆类型: 长安之星 日 期: 06.05.10 修订日期: 09.06.10
浙江通顺
设计潜在的失效模式及后果分析
(DFMEA)
产品名称:长安之星制动主缸
产品代号:0.02-2005.3B
浙江通顺科技集团有限公司
修订/日期:审核/日期:批准/日期:。
制动器的设计计算-15页文档资料

§3 制动器的设计计算3.1制动蹄摩擦面的压力分布规律从前面的分析可知,制动器摩擦材料的摩擦系数及所产生的摩擦力对制动器因数有很大影响。
掌握制动蹄摩擦面上的压力分布规律,有助于正确分析制动器因数。
在理论上对制动蹄摩擦面的压力分布规律作研究时,通常作如下一些假定:(1)制动鼓、蹄为绝对刚性;(2)在外力作用下,变形仅发生在摩擦衬片上;(3)压力与变形符合虎克定律。
1.对于绕支承销转动的制动蹄如图29所示,制动蹄在张开力P 作用下绕支承销θ∆点转动张开,设其转角为θ∆,则蹄片上某任意点A 的位移AB 为由于制动鼓刚性对制动蹄运动的限制,则其径向位移分量将受压缩,径向压缩为AC AC =AB COS β即 AC =A O 'θ∆COS β从图29中的几何关系可看到A O 'COS β=D O '=O O 'Sin ϕAC =O O 'Sin ϕθ∆⋅ 因为θ∆⋅'O O 为常量,单位压力和变形成正比,所以蹄片上任意一点压力可写成 q=q 0Sin ϕ (36)亦即,制动器蹄片上压力呈正弦分布,其最大压力作用在与O O '连线呈90°的径向线上。
2.浮式蹄在一般情况下,若浮式蹄的端部支承在斜支座面上,如图30所示,则由于蹄片端部将沿支承面作滚动或滑动,它具有两个自由度运动,而绕支承销转动的蹄片只有一个自由度的运动,因此,其压力分布状况和绕支承销转动的情况有所区别。
现分析浮式蹄上任意一点A 的运动情况。
今设定蹄片和支座面之间摩擦足够大,制动蹄在张开力作用下,蹄片将沿斜支座面上作滚动,设Q 为其蹄片端部圆弧面之圆心,则蹄片上任意一点A 的运动可以看成绕Q 作相对转动和跟随Q 作移动。
这样A 点位移由两部分合成:相对运动位移AB 和牵连运动位移BC ,它们各自径向位移分量之和为AD (见图30)。
AD =AB COS β+BC COS(ϕ-α)根据几何关系可得出AD =(θ∆·OQ +BC Sin α) Sin ϕ+BC COS αCOS ϕ式中θ∆为蹄片端部圆弧面绕其圆心的相对转角。
制动主缸毕业论文--汽车制动主缸的设计与优化
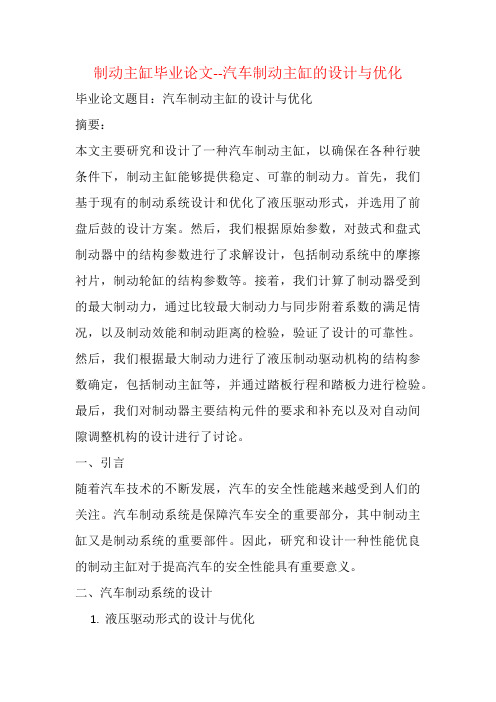
制动主缸毕业论文--汽车制动主缸的设计与优化毕业论文题目:汽车制动主缸的设计与优化摘要:本文主要研究和设计了一种汽车制动主缸,以确保在各种行驶条件下,制动主缸能够提供稳定、可靠的制动力。
首先,我们基于现有的制动系统设计和优化了液压驱动形式,并选用了前盘后鼓的设计方案。
然后,我们根据原始参数,对鼓式和盘式制动器中的结构参数进行了求解设计,包括制动系统中的摩擦衬片,制动轮缸的结构参数等。
接着,我们计算了制动器受到的最大制动力,通过比较最大制动力与同步附着系数的满足情况,以及制动效能和制动距离的检验,验证了设计的可靠性。
然后,我们根据最大制动力进行了液压制动驱动机构的结构参数确定,包括制动主缸等,并通过踏板行程和踏板力进行检验。
最后,我们对制动器主要结构元件的要求和补充以及对自动间隙调整机构的设计进行了讨论。
一、引言随着汽车技术的不断发展,汽车的安全性能越来越受到人们的关注。
汽车制动系统是保障汽车安全的重要部分,其中制动主缸又是制动系统的重要部件。
因此,研究和设计一种性能优良的制动主缸对于提高汽车的安全性能具有重要意义。
二、汽车制动系统的设计1.液压驱动形式的设计与优化液压驱动形式是制动系统的核心部分,其性能直接影响到制动的效能和稳定性。
我们采用前后式(Ⅱ式)双回路制动控制系统,以确保在任何一只车轮出现故障时,其他车轮仍能正常工作。
2.前盘后鼓的设计方案根据盘式和鼓式各自的性能特点,我们选用了前盘后鼓的设计方案。
这种设计方案可以充分发挥盘式制动器的高效性和稳定性,同时利用鼓式制动器在低速时的可靠性。
三、结构参数的设计与求解1.鼓式制动器的设计我们根据制动系统的原始参数,对鼓式制动器中的结构参数进行了求解设计,包括制动轮缸的结构参数等。
这些参数的确定需要考虑制动的效能、稳定性以及制造成本等多方面因素。
2.盘式制动器的设计同样地,我们对盘式制动器的结构参数也进行了求解设计,包括摩擦衬片的厚度、硬度等参数。
制动系统性能计算报告(正式)
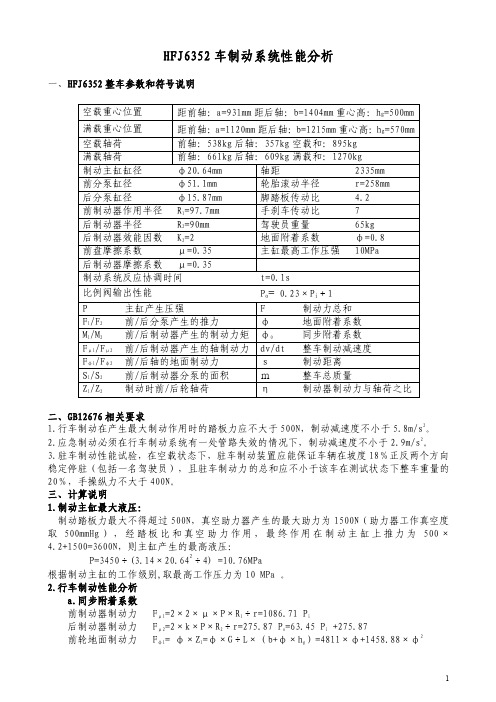
HFJ6352车制动系统性能分析一、HFJ6352整车参数和符号说明二、GB12676相关要求1.行车制动在产生最大制动作用时的踏板力应不大于500N,制动减速度不小于5.8m/s2。
2.应急制动必须在行车制动系统有一处管路失效的情况下,制动减速度不小于2.9m/s2。
3.驻车制动性能试验,在空载状态下,驻车制动装置应能保证车辆在坡度18%正反两个方向稳定停驻(包括一名驾驶员),且驻车制动力的总和应不小于该车在测试状态下整车重量的20%,手操纵力不大于400N。
三、计算说明1.制动主缸最大液压:制动踏板力最大不得超过500N,真空助力器产生的最大助力为1500N(助力器工作真空度取500mmHg),经踏板比和真空助力作用,最终作用在制动主缸上推力为500×4.2+1500=3600N,则主缸产生的最高液压:P=3450÷(3.14×20.642÷4) =10.76MPa根据制动主缸的工作级别,取最高工作压力为10 MPa 。
2.行车制动性能分析a.同步附着系数前制动器制动力 Fμ1=2×2×μ×P×R1÷r=1086.71 P i后制动器制动力 Fμ2=2×k×P×R2÷r=275.87 P o=63.45 P i +275.87前轮地面制动力 Fφ1= φ×Z1=φ×G÷L×(b+φ×h g)=4811×φ+1458.88×φ2后轮地面制动力 Fφ2= φ×Z2=φ×G÷L×(a-φ×h g)=2931.02φ-1458.88×φ2比例阀输出特性 P o= 0.23×P i+1同步抱死的条件: Fφ1= Fμ1Fφ2= Fμ2根据以上方程可求得空载同步附着系数φ0=1.5同理可求得:满载同步附着系数φ0=1.688不含比例阀时同步附着系数空载:φ0=(β×L-b)/ h g=0.92满载:φ0=(β×L-b)/ h g=1.14b.制动减速度分析(φ=0.8)地面附着系数为φ=0.8<φ0 ,制动开始时,前后制动器制动力Fμ1、Fμ2按β线上升。
- 1、下载文档前请自行甄别文档内容的完整性,平台不提供额外的编辑、内容补充、找答案等附加服务。
- 2、"仅部分预览"的文档,不可在线预览部分如存在完整性等问题,可反馈申请退款(可完整预览的文档不适用该条件!)。
- 3、如文档侵犯您的权益,请联系客服反馈,我们会尽快为您处理(人工客服工作时间:9:00-18:30)。
26、我们像鹰一样,生来就是自由的 ,但是 为了生 存,我 们不得 不为自 己编织 一个笼 子,然 后把自 己关在 里面。 ——博 莱索
ቤተ መጻሕፍቲ ባይዱ
•
27、法律如果不讲道理,即使延续时 间再长 ,也还 是没有 制约力 的。— —爱·科 克
•
28、好法律是由坏风俗创造出来的。 ——马 克罗维 乌斯
•
29、在一切能够接受法律支配的人类 的状态 中,哪 里没有 法律, 那里就 没有自 由。— —洛克
Thank you
•
30、风俗可以造就法律,也可以废除 法律。 ——塞·约翰逊
制动主缸设计计算
6、最大的骄傲于最大的自卑都表示心灵的最软弱无力。——斯宾诺莎 7、自知之明是最难得的知识。——西班牙 8、勇气通往天堂,怯懦通往地狱。——塞内加 9、有时候读书是一种巧妙地避开思考的方法。——赫尔普斯 10、阅读一切好书如同和过去最杰出的人谈话。——笛卡儿