MRP自动重订货点
MRP-ERP订货点法

2.MRP与订货点法的三点区别
① 通过产品结构把所有物料的需求联系起来。考虑不同物料的需求之间的 相互匹配关系,从而使各种物料的库存在数量和时间上均趋于合理。
② 把所有物料按需求性质区分为独立需求项和非独立需求项。如果某项物 料的需求量不依赖于企业内其他物料的需求量而独立存在,则称为独 立需求项目;如果某项物料的需求量可由企业内其他物料的需求量来 确定,则称为非独立需求项目,即相关需求项目。独立需求项目的需 求量和需求时间通常由预测和客户订单等外在的因素来决定;而非独 立需求项目的需求量和需求时间则由MRP系统来定。
资金周转数
短缺件 成本 利润
上升
下降 下降 上升
50%-400%
60%-80% 7%-12% 5%-10%
21
Material Requirements Planning
Materials requirements planning (MRP) is a means for determining the number of parts, components, and materials needed to produce a product MRP provides time scheduling information specifying when each of the materials, parts, and components should be ordered or produced Dependent demand drives MRP MRP is a software system
用到什么) - 已有什么 = 还缺什么
© 2006 The McGraw-Hill Companies, Inc., All Rights Reserved.
MRP-逻辑

收入
异常消息
计划内
*
公差
*
计划外
公差 Tolerance
时间
需求 内部生产时间
+
物品收货时间进程表
+
延期时间
所需单据 : 生产订单、采购订单、固定计划订单 ,
这个计划运行将不会自动取代固定收货.
SAP AG 2001, A Business View of mySAP Financials, GBU FIN - 5
安全库存
安全库存: 设置在物料主数据(MRP2)
库存量
或者MRP部分
计划可用数量
安全库存
(计划不可用量)
时间
需求
SAP AG 2001, A Business View of mySAP Financials, GBU FIN - 14
收货
安全库存部分可用
安全库存部分可用:设置在MRP组
计划可用 可用数量
净需求计算概述
净需求量
批量计算 获取类型
排产 BOM展开
SAP AG 2001, A Business View of mySAP Financials, GBU FIN - 6
MRP: 净需求量
MRP 会对比供给和需求来满足短缺的空隙,仓库库存和相应的收据和问题之间比较。 在净需求计算,不同的是订货点计划,基础预测计划和MRP之间。在每个过程中,系统会自动计
SAP AG 2001, A Business View of mySAP Financials, GBU FIN - 11
计划如何运行每一种MRP类型
预测基本计划 (预测) (MRP 类型VV, 创建预测) 系统仅仅考虑预测需求(其他任何需求不考虑)。当库存可利用需求低于预测 需求时,需创建计划订单 可用库存 = 工厂库存 – 安全库存 + 收货 – 预测需求 定期分阶段计划 (时间计划) (MRP类型 R1, 计划周期, 创建预测) 物料计划是根据同一周期到货物料,但是不属于正常MRP运行 ,这些物料必须运行 一个单独。 可用库存=在计划周期内(工厂库存-安全库存+收货-预测需求) MRP 计划 (预测) (MRP Type PD,可选择性的创建预测) 系统检查每种需求来确定,是否这些需求能够被可用库存联合收货来覆盖 可用库存=工厂库存-安全库存+收货-全部 需求
订货点采购与MRP采购

第一节订货点采购一、订货点概述(一)订货点的概念订货点:仓库必须发出订货的警戒点。
订货点=实际最低库存量=理想最低库存量+安全存量理想最低库存量=购备时间×每日消耗量安全存量:即为防备购备时间与物资耗用情况变化时,确保不发生停工呆料现象而做的安全储备。
订货点法是一种传统的库存计划与控制方法,他的基本思想:根据过去的经验预测未来的需要,根据物料的需求情况来确定订货点和订货批量。
然而,在实际生产中,随着市场环境发生变化,需求常常是不稳定的、不均匀的,在这种情况下使用订货点法便暴露出一些明显的缺陷。
(二)订货点的基本假设1.对各种物料的需求是相互独立的。
(独立需求:对某种物料的需求与对其他产品或零部件的需求无关。
相关需求:对某些物料的需求取决于对其他物料的需求。
)2.物料的需求是稳定、连续的。
3.订货提前期是已知的、固定的。
(三)订货点法的缺陷1.盲目性:由于需求的不均匀以及对需求情况不了解,企业不得不保持一个较大数量的安全库存来应付这种需求。
这样盲目地维持一定量的库存会造成资金积压和浪费。
2.高库存与低服务水平:传统的订货点方法使得低库存与高服务水平两者不可兼得。
服务水平越高则库存越高,还常常造成零件积压与短缺共存的局面。
3.形成“块状”需求:在制造过程中形成的需求一般都是非均匀的:不需要的时候为零,一旦需要就是一批。
在产品的需求率为均匀的条件下,由于采用订货点方法,造成对零件和原材料的需求率不均匀,呈“块状”。
“块状”需求与“锯齿状”需求相比,平均库存水平几乎提高一倍,因而占用更多的资金。
订货点法之所以有这样的缺陷:是因为其没有真正的按照各种物料的真正需用时间来确定订货日期。
于是,人们便思考:怎样才能在需要的时间,按需要的数量得到真正需要的物料?从而消除盲目性,实现低库存与高服务水平(四)订货点法的优点1.它是至今能够用于独立需求物资进行物资资源配置的唯一方法;2.订货点技术操作简单,运行成本低;3.订货点技术特别适合于客户未来需求量连续而且稳定的情形。
mps与mrp的最大区

mps与mrp的最大区
所谓MPS,就是指主生产计划,主要是对成品一级的需求安排计划。
而MRP是指物料需求计划,针对主生产计划,根据BOM,展开所有材料的需求。
MRP一般是由于MPS引起的,比如你有一个部件A MRP type=M0(MPS部件),它下面一个子部件B MRP TYPE=PD ( MRP部件)。
系统跑MPS的时候,只跑A部件,然后算出
A的PL ORDER,然后产出对B的DEPENDENT REQUIREMENT,然后系统跑MRP(当然对B了),系统根据那个DEPENDENT REQUIREMENT,跑出对B的需求
MRP有三种:1、MPS/MRP/3、基本消费计划 MPS包含(M0、M1、M2、M3、M4) MRP包含(PD、P1、P2、P3、P4)基于消费计划包含(重订货点、基于预测计划、基于时间物料计划)补充一点:如果物料主数据维护为M0、M1、M2、M3、M4等MPS类型,那么用MD40,MD41,MD42,MDBS等事务码来运行;MRP类型物料用MD01,MD02,MD03,MD43,MDBT等事务码来运行。
1。
MRP与ERP确定订货批量的方法

紧迫系数
CR=Critical Ratio
需用日期-今日日期 CR=
剩余的计划提前期
CR值越小,优先级越高
• CR<0 已拖期 • CR=1 剩余时间恰好 • CR>1 剩余时间有余 • CR<1 剩余时间不够
最小单个工序平均时差
• 按固定时区需求量确定批量法
时区
123
净需求 35 10
计划订单 45
45 40 40
67 20 5 25
8 9 合计
10 30 150
40
150
确定订货批量的方法
• 最小单位成本法
时区
123
净需求 35 10
计划订单 45
45 40 60
6 7 8 9 合计
20 5 10 30 150
45
150
项目
可选特征
车轴
2种:标准车轴
大间隙车轴
挂钩
2种:机械式
液压式
动力输出装置
3种:A型
B型
无
散热器
2种:有
无
封闭驾驶室
2种:有
无
根据这些可选特征的组合数,这个企业所生产的农用拖拉机可共有::
3X3X2X2X2X2X2X2X3X2X2=6912种
构造模块化物料清单的步骤
1、划分产品类 如上述农用拖拉机构成一个产品类
17、利人为利已的根基,市场营销上老是为自己着想,而不顾及到他人,他人也不会顾及你。下午4时58分8秒下午4时58分16:58:0821.8.25
价值%
100 95
80
ABC分类
AB
MPS与MRP的区别与联系

MPS与MRP的区别和联系一、第一种解释MPS(主生产计划)MPS是产成品的计划表,描述一个特定的产成品的生产时间和生产数量,MPS是一个决定产成品生产排程及可承诺量/可销售签约量(ATP,Available To Promise)的程序。
依据MPS(主生产计划),MRP得以计算在该产成品需求之下,所有组件、零件乃至原材料的所需补充计算。
MPS不是销售预测,不代表需求。
MPS须考虑生产规划、预测、待交订单、关键材料、关键产能及管理目标和政策。
除了材料外,MPS也是其它制造资源的规划基础。
MRP(物料需求计划)MRP利用BOM(物料清单),将MPS运算结果中的产成品需求转换为半成品及原材料需求。
它利用库存状态如OH(在库量)及SR(在途量)等,以及材料主文件中的材料基本资料如LT及SS等,以及厂历,计算出何时需要多少何种材料。
MPS主要是围绕产成品展开生产计划表,MRP主要是依据材料展开采购工作。
根据公司的情况,大型的公司可以一周运行一次,先进行MPS,然后进行MRP,之间有一个时间差;对于小型企业,可以一天运行一次MPS及MRP,正规的MRP会考虑当前的所有变化,如库存、在途等,关键是要及时把变化信息录入ERP中:例如,前一次MRP分解后需要制造A产品100件,但因为某原因,实际只做了90件,就不做了,在ERP中要进行完工入库90件,然后把这个加工命令关闭。
在下一次运行MRP运算时,ERP系统会自动产生下一个制造10件A的任务。
因此,关键是数据的维护工作要及时,系统数据准确,ERP才会发挥作用。
1、MPS是MRP的直接目的,MPS体现的是净需求,MRP运算出来的作业计划和采购计划的目的就是完成MPS提出的任务,从而达到企业外部市场需求的目标2、MPS主要针对有独立需求计划而言,它是整个计划系统的调节器,在充分考虑企业粗能力和资源平衡的基础上平衡外部需求和企业供给能力.有些行业可以没有MPS,直接通过MRP来满足预测和订单的需要3、简单的说:MPS针对的是总装,MRP针对的是总装下的采购及零件4、如果从客户订单或预测过来的需求都需要计划部评估一下这个成品的交期和粗能力,在成品的评审没有完成之前下阶的材料都不允许产生相关需求,这个时候就对成品RUN MPS,当成品评审通过后再对它的一阶材料RUN MRP。
Mrp重订货点

Schneider Electric - IT/SAP
New ROP with safety stock = Demand in lead time + Safety stock
Safety stock
2
Consumption Based MRP Reorder Point Procedure
重订货点
Stock Level 库存水平
ROP
Order Quantity 订单数量
Reorder Level 重订货点
Safety Stock 安全库存
RLT
Replenishment Lead-time 补货提前期
Time 时间
Schneider Electric - IT/SAP
1
ReOrder Point重订货点
Fast mover – Daily or Weekly
F
Demand
M1
M2
M3
M4
Medium mover – Monthly
M
Demand
M1
M2
M3
M4
Rare mover – Quarterly or Yearly
R
Demand
M1
Schneider Electric - IT/SAP
M2
A item
Please rounded lot size quantity to packaging quantity 圆整到一个整包装的数量
Schneider Electric - IT/SAP 10
时间(上架, 质检等)(Current date (date of MRP execution) + purchasing department processing time + planned delivery time + goods receipt processing time = date the material will be available for use.)
MRP策略详解
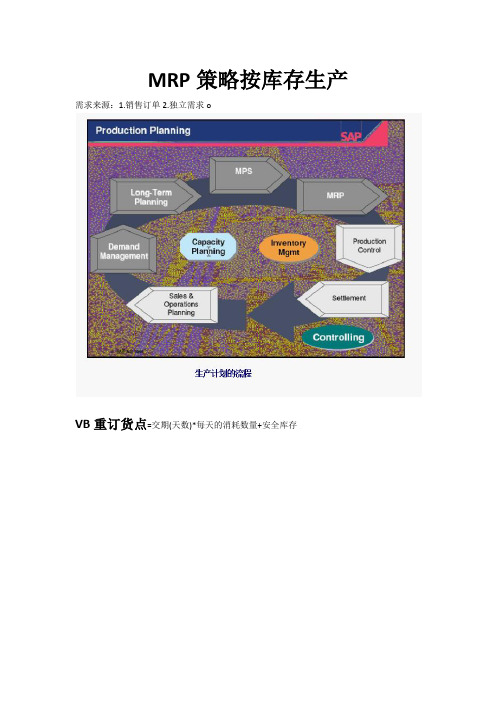
MRP策略按库存生产需求来源:1.销售订单2.独立需求oVB重订货点=交期(天数)*每天的消耗数量+安全库存策略:按库存生产(Make-to-stock)按订单生产(make-to-order) 按订单生产特殊类型(make-to-order-specific final assembly)按库存生产: 10 11 30 40 70 59按库存生产:理解为在没有销售订单的情况下去生产。
策略10纯的生产生产完全按计划独立需求生产跟销售订单没有关系,比如计划独立需求生产100个销售订单150个用策略10就生产100个不会生产150个策略组10设置在MRP3如下:步骤;10策略1.(净需求库存会参加运算)独立需求计划( FORCAST销售预测PIR DN DEMAND)(MD61)-运行MRP MPS 触发原材料采购或半成品成品的生产,产生计划订单,能否转成生产订单(是)-2.销售订单出货后冲销计划独立需求策略组11 MRP3设置如下步骤1.(毛需求库存不参加运算)2.成品入库后冲销计划独立需求3.综合MRP设置为2策略30 等于30+10MRP3设定:创建销售订单时在采购视图将KL改为KSL1.重要客户启用10(按批生产)(先做计划独立需求)不重要客户用30(有销售订单才做)2.综合MRP不用3.重要客人建立销售订单将采购KL改为KSL 已区分重要客人发货后独立需求减少策略30定义需求分类填1导致销售订单发货冲销不了独立需求设置销售订单读取策略方式设置为0的时候优先读取MRP组策略在读取MRP3里面策略策略40MRP3设定步骤40策略40与10区别,1. 40当销售订单下达后冲销独立需求,10当销售订单生产发货后在冲销计划独立需求2. 40如客户销售订单大于计划独立需求跑MRP会产生需求,10不考虑销售订单消耗模式1仅向后消耗消耗模式2先向后/在向前消耗消耗模式3仅超前消耗消耗模式2/4先超前/在滞后消耗消耗区间:绝对冲销时间综合MPR为空消耗模式:为1消耗模式:为3冲销比销售日期大的独立需求消耗模式:为2先冲销比销售日期大的独立需求,如不满足在往前找消耗模式:为4先冲销比销售日期小的独立需求,如不满足在往后找策略70(针对半成品或原材料)独立需求VSFB类型MRP3设定步骤:701.冲销模式在建成品生产订单或计划订单(在有相关预留或相关需求的情况下)冲销半成品计划独立需求2.综合MRP设为1针对半成品或原材料针对半成品或原材料做策略(针对半成品原材料做计划独立需求)物料可以转采购申请或生产订单3.成品建立销售订单或生产订单或计划订单对半成品产生相关需求或相关预留,跑MRP半成品的计划独立会冲销,策略591.同策略702.计划独立需求类型VSEB3.特殊采购类E+50虚无装配,策略设置,综合MRP设置为14.虚拟件子层设置为倒冲15.区别在于只针对虚拟料件,并且虚拟料件子层设反冲过程中虚拟料号运行MRP时出现例52无物料单被选择原来是BOM有效日期晚于计划订单有有效日期苦苦的想了一个下午按订单生产策略20(纯按单生产)MRP3设置策略组=策略定义策略策略=独立需求类型+客户需求类型独立需求类型=需求类需求类=计划标识+消耗标识+计划独立需求按单生产设置主物料MRP4 独立集中=1或是空白时下阶物料会分段显示设置为2时下阶物料不会分段显示MRP逻辑公式A*B-C=DA=主生产计划B=BOMC= 库存需求D=需求策略501.成品做计划独立需求2.半成品触发生产3.成品有销售订单后,会冲销成品销售预测4.在触发成品生产5.同策略40区别在于成品生产50为半成品触发生产计划订单类型为VP是不可以转生产订单的50策略设定测试步骤如下VP Plan order订单类型特点1.可以做产能分析2.不能被手工更改3.不能转成生产订单决定下阶物料是否可以生产取决于MRP4 独立/集中设定如下阶段物料独立/集中设置为2表示可以产生如独立集中设置为空或为1时表示不能生产策略74=70+50策略60设定步骤60策略82通过创建销售订单自动产生生产订单任意修改一个都有影响步骤82设定可配置物料策略26(用于变式物料)25根据可配置物料设定(跟策略20一样)(变式物料CS40 CS42 CS42)如果可配套物料的特殊配置非常受人欢迎,那么为这个产品变式创建一个单独的物料号以避免每次创建销售订单时不得不重新配置的麻烦是有好处的。
- 1、下载文档前请自行甄别文档内容的完整性,平台不提供额外的编辑、内容补充、找答案等附加服务。
- 2、"仅部分预览"的文档,不可在线预览部分如存在完整性等问题,可反馈申请退款(可完整预览的文档不适用该条件!)。
- 3、如文档侵犯您的权益,请联系客服反馈,我们会尽快为您处理(人工客服工作时间:9:00-18:30)。
重订货点法(Reorder Point)是物料需求计算的一种重要方式,与通常意义上的MRP方式不同,重订货点法属于基于消耗计算物料供给的方法。
其基本的指导思想是,补货元素的生成与物料需求不直接相关,而是以当前库存作为最重要的参照指标。
通过周期性的库存检查,每当库存水平低于预设的采购触发线(即重订货点)之后,系统就会自动生成对应的补货元素,将库存水平补充到重订货点水平之上。
而在这次补货完成之前,企业仍然可以使用当前剩余库存来满足日常需求。
基于重订货点法产生的补货,无法做到精确对应于需求元素,更无法适应精益生产理论,将库存水平降到最低。
但由于这种方法易于实现、易于理解、简单可靠,尤其适用于单位价值较低,且日常消耗频繁而稳定的物料。
然而,虽然这种方法实现起来很简单,不需要计划员在日常运行过程中做过多的分析与调整,但仍然不可避免地遇到这样的一个问题--重订货点到底设置在什么水平最合适?这绝对不是一个简单的问题,若想由计划部门提供一个可靠的重订货点水平往往非常困难。
重订货点设置得过低,则这种频繁消耗的物料稍微遇到需求波动就会面临断货的风险(尽管价值低,可一旦断货照样会中断整个供应链);而如果重订货点设置得过高,则由此带来的问题就是大量占用库存资金,导致没有必要的库存被存放在仓库里。
怎么办呢?其实对于每个实施了SAP系统的企业而言,设置重订货点无非就是以下两种方法:其一:手动重订货点(拍脑袋决定??)。
不管计划部门采取什么方法,总之最后敲定一个重订货点出来,直接将其分配给物料主数据。
此方法简单易行,大约有100%的企业采用这种方法进行重订货点的维护。
而这种重订货点维护方式不在本的探讨与分析范围内。
其二:自动重订货点。
顾名思义,把计算重订货点的工作交给系统来完成。
在维护物料主数据时,不维护重订货点,而是由系统自动推算之后,再自动将重订货点分配给相应的物料主数据。
此方法看上去也比较“简单易行”,大约有0%的企业采用这种方法进行重订货点的维护。
本文接下去所要描述的,就是所谓的自动重订货点法。
将会通过一个实际的测试案例,讲述自动重订货点法的运行步骤、原理、运算逻辑以及后台配置。
将会介绍自动重订货点的运算公式,并通过该公式推导重订货点的计算方法,看看SAP系统究竟是怎样计算出重订货点的合理值的。
除此之外,在进行自动重订货点计算的同时,SAP系统还在这里面附加了一个额外的功能,即自动安全库存。
在前面的中,已经探讨过安全库存的含义及其用途。
在一般情况下,一种物料的安全库存值也是由用户手动维护的,但SAP系统提供了自动计算最佳安全库存值的方法,这一方法及其运算公式将在推导重订货点的同时一并讲解。
在正式开始的案例测试之前,有以下几点需要特别说明:1)将要介绍的是自动重订货点以及自动安全库存的应用方法与运算逻辑,包括其公式构成与公式参数。
但将不会从纯数学的角度去推导公式的来源与其理论依据。
如果需要搞清楚计算公式是怎么来的,还需要查阅相应的学术文献。
2)出于简化测试、突出重点的需要,将采用最基本的趋势模型作为预测模型使用。
其中的平滑因子α和趋势因子β都直接取自默认值(0.2和0.1)3)将要介绍的功能包括了自动安全库存计算。
但大家一定要注意将这个功能与之前曾经专门探讨过的动态安全库存(Dynamic Safety Stock)功能区分开。
这两种功能完全基于不同的运算逻辑,且业务本质也有不同。
动态安全库存功能的计算依据是未来需求,其实质在于既定周期的需求保障,已经不同于传统的安全库存概念;而自动安全库存计算则完全在运行逻辑上等同于传统的安全库存概念,只不过安全库存值由系统自动算出而已。
且自动安全库存的计算依据为历史消耗,而非未来需求。
4)从功能上讲,自动重订货点计算与自动安全库存计算可以是两个完全独立的功能。
可以选择性地应用其中的任何一个,或者二者都用。
但在一般情况下,自动安全库存计算是自动重订货点计算的基础,重订货点是在安全库存的基础上推算出来的。
所以将这两个知识点合在一个系列里进行讲解。
但事实上,这两者究竟哪个自动、哪个手动,完全可以随意定制。
在前面的中,已经简要介绍了自动重订货点与自动安全库存在物料计划功能中的含义。
接下来,就通过具体测试案例对这个功能的应用进行分析。
第一步:在后台配置当中定义MRP类型“VM”。
其具体路径为(生产→MRP→主数据→检查MRP 类型),如下图所示:事实上,“VM”是SAP系统默认提供的,用于自动重订货点的MRP类型。
直接使用这个MRP类型,并不需要任何的配置工作。
但是为了从本质上理解这个MRP类型的特别之处,还是特意在后台配置中对这个MRP类型进行分析。
通过上图的展示,很容易就会发现这个MRP类型的本质特征:1)“MRP进程”(MRP procedure)字段:“VM”在这个字段上的值是“B”,这就从本质上决定了这是个基于重订货点的MRP类型。
其特点是系统在一般情况下不会依据需求元素产生供给元素,而是根据当前的库存水平来触发补货。
2)“预测标识符”(Forecast ind.)字段:“VM”在这个字段上的值是“+”,即“强制预测”。
这说明了凡是分配了MRP类型“VM”的物料,都必须同时激活预测功能。
因为预测功能的运行是自动重订货点计算的前提条件,因此不激活预测,重订货点功能就无从谈起了。
3)“安全库存”(Safety stock)字段:这个字段被选中,意味着系统将在运行预测程序的同时,自动为相应的物料计算最佳安全库存值。
4)“重订货点”(Reorder point)字段:这个字段被选中,意味着系统将在运行预测程序的同时,自动为相应的物料计算最佳重订货点。
通过这四个字段的选择,得出的结论有以下几点:其一:“自动重订货点”只是“重订货点”的一种罢了。
除了重订货点值由系统自动运算得出之外,其他功能特性与手动重订货点法没有任何区别。
其二:系统是通过预测(Forecast)功能来计算重订货点的。
这就意味着需要为物料维护预测视图、预测公式参数以及足量的历史数据。
而基于历史数据推算最佳重订货点与安全库存的方法,注定与基于计划独立需求(PIR)推算未来安全库存的动态安全库存法存在本质不同。
其三:标准的自动重订货点法,已经包含了自动安全库存运算功能。
但可以在上图界面中自定义是否分别激活这两种自动计算。
可以只算重订货点,也可以只算安全库存,可以两者都算,也可以两者都不算。
第二步:使用事务代码MM01,创建测试用物料主数据(物料号VMT01),并查看其MRP1视图,如下图所示:可以看到在上图中,将标准的MRP类型“VM”分配给了物料主数据。
同时没有给物料分配重订货点(空置“重订货点”字段)。
当使用手动重订货点法的时候,系统将会强制给物料分配重订货点。
但对于MRP类型“VM”而言,由于系统将会自动计算这个值,因此就可以空着“重订货点”字段不填了。
接下来,查看测试物料的MRP2视图,如下图所示:看到,该测试物料是一个自制件(不是外购件)。
针对这个自制件,在物料主数据上维护了它的“自制生产时间”字段,长度为3天(即3个工作日)。
这三个工作日将被作为该测试物料的补货提前期使用。
需要注意的是,如果使用自动重订货点或者自动安全库存计算,都必须为相应的物料在物料主数据中维护其补货提前期。
公式一:对于自制件而言:补货提前期= 未清期间(来自于计划边际码)+ 自制生产时间+ 收货处理时间公式二:对于外购件而言:补货提前期= 采购活动处理时间(来自于工厂参数)+ 交货时间+ 收货处理时间接下来,注意到在上图中,没有为相应的物料维护“安全库存”字段,这是因为已经在MRP类型中启用了自动安全库存计算。
同时,还为测试物料主数据维护了“服务级别”(Service level)字段,对应的值为“90%”。
所谓“服务级别”,指的是在多大概率上,希望需求数量可以直接被库存数量满足(而不需要通过生产订单、采购订单等后续方式)。
而这里维护的“90%”,就意味着对于测试物料而言,希望在90%的情况下,物料的库存数量大于等于需求数量。
而在另外10%的情况出现时,可以接受通过临时组织生产(冒着各种供应链中断风险)的方式来满足供货。
请注意,在自动安全库存计算功能中,必须为相应的物料维护“服务级别”字段。
接下来,查看物料主数据的“预测”视图,如下图所示:之前已经为物料主数据分配了MRP类型“VM”。
由于在这个MRP类型的后台配置中,“预测标识符”字段已经被维护为“+”,即“强制预测”。
因此只有为相应的物料主数据维护了“预测”视图之后,该物料主数据才能够保存。
在上图界面中,需要注意到以下字段:1)“预测模型”(Forecast model)字段:这个字段决定了相应的物料在运行预测的时候将采用哪一种预测模型。
在本测试案例中采用的是基本的趋势模型。
2)“期间标识符”(Period Indicator)字段:这个字段描述了在运行预测的时候,历史数据与预测数据将会基于怎样的区间而产生。
比如在上图中维护的字段值是“T”,这就意味着系统将以“天”为单位来运行预测程序。
所有的历史消耗数据将会基于“天”来读取,而所有的预测数据也将会诸天来生成。
本字段在自动安全库存的计算过程中起到了非常关键的作用。
3)“历史期间”(Hist. periods)字段:这个字段描述了系统每次运行预测程序时,将会读取多少个期间(之前已经定义了一天为一个期间)的历史数据。
在此维护的值为“10”。
4)“预测期间”(Forecast periods)字段:这个字段描述了系统每次运行预测程序时,将会产生多少个期间的预测值,同样在此维护“10”。
接下来,可以点击“消耗值”(Consumption vals)按钮,为测试物料维护历史消耗数据,如下图所示:第三步:使用事务代码CR01,创建工作中心VMTEST,该工作中心的单日能力为8小时。
第四步:使用事务代码CA01,为测试物料创建工艺路线,如下图所示:可以看到在唯一的工序中,维护的工序期间为100件/小时。
第五步:使用事务代码MD61,为测试物料维护计划独立需求。
第六步:使用事务代码MD02,为测试物料运行MRP。
第七步:使用事务代码MD04,查看测试物料的供需状况,如下图所示:看到,这个界面上什么也没有,既没有供给,也没有需求。
之前分配给该物料的计划独立需求并没有被MRP考虑在内。
这也和一般的重订货点计划思路完全相符。
在一般的重订货点模式下,物料的各类需求元素(安全库存除外)均不会参与净需求计划的运行。
第八步:使用事务代码MM02,为测试物料运行预测程序并观察其预测结果,如下图所示:可以看到,由于采用的预测模型是趋势模型,因此系统自然而然地为计算出了预测模型中的基准值与趋势值。
但这并不是所要探讨的重点。