连接座注塑模模具设计说明书
连接座注塑模设计
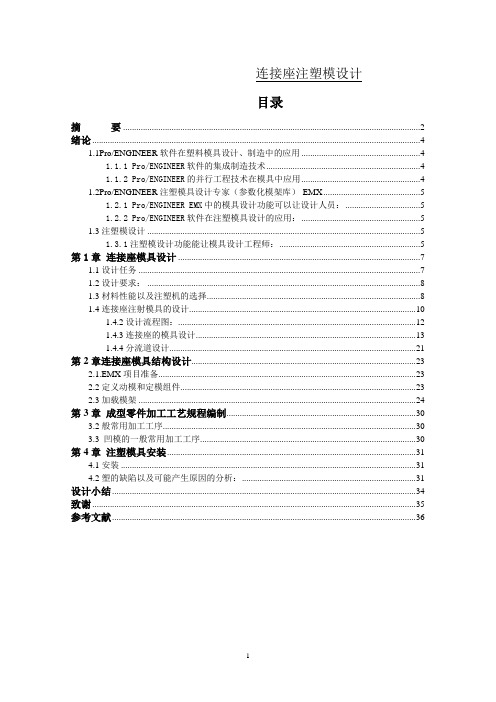
连接座注塑模设计目录摘要 (2)绪论 (4)1.1Pro/ENGINEER软件在塑料模具设计、制造中的应用 (4)1.1.1 Pro/ENGINEER软件的集成制造技术 (4)1.1.2 Pro/ENGINEER的并行工程技术在模具中应用 (4)1.2Pro/ENGINEER注塑模具设计专家(参数化模架库)-EMX (5)1.2.1 Pro/ENGINEER EMX中的模具设计功能可以让设计人员: (5)1.2.2 Pro/ENGINEER软件在注塑模具设计的应用: (5)1.3注塑模设计 (5)1.3.1注塑模设计功能能让模具设计工程师: (5)第1章连接座模具设计 (7)1.1设计任务 (7)1.2设计要求: (8)1.3材料性能以及注塑机的选择 (8)1.4连接座注射模具的设计 (10)1.4.2设计流程图: (12)1.4.3连接座的模具设计 (13)1.4.4分流道设计 (21)第2章连接座模具结构设计 (23)2.1.EMX项目准备 (23)2.2定义动模和定模组件 (23)2.3加载模架 (24)第3章成型零件加工工艺规程编制 (30)3.2般常用加工工序 (30)3.3 凹模的一般常用加工工序 (30)第4章注塑模具安装 (31)4.1安装 (31)4.2塑的缺陷以及可能产生原因的分析: (31)设计小结 (34)致谢 (35)参考文献 (36)摘要本设计题目为连接座注塑模设计,体现了典型连接座注塑模的设计要求、内容及方向,有一定的设计意义。
通过对该零件模具的设计,进一步加强了设计者弯注塑模设计的基础知识,为设计更复杂的注塑模做好了铺垫和吸取了更深刻的经验。
本设计运用注塑成型工艺及模具设计的基础知识,首先计算塑件的体积,为现在注塑机的选择座好准备,以确定注塑量,以便于选择注塑机型号;最后分析了注塑件的特征,确定模具的设计参数、设计要点及顶出装置的选取。
模具的设计应制造方便, 尽量做道使设计的模具制造容易、造价便宜。
注塑模具设计说明书
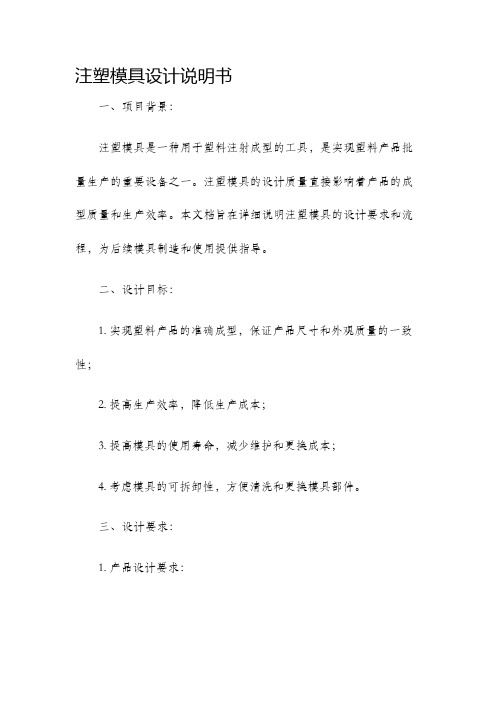
注塑模具设计说明书一、项目背景:注塑模具是一种用于塑料注射成型的工具,是实现塑料产品批量生产的重要设备之一。
注塑模具的设计质量直接影响着产品的成型质量和生产效率。
本文档旨在详细说明注塑模具的设计要求和流程,为后续模具制造和使用提供指导。
二、设计目标:1. 实现塑料产品的准确成型,保证产品尺寸和外观质量的一致性;2. 提高生产效率,降低生产成本;3. 提高模具的使用寿命,减少维护和更换成本;4. 考虑模具的可拆卸性,方便清洗和更换模具部件。
三、设计要求:1. 产品设计要求:a. 确定产品的尺寸和外观要求,提供详细的产品图纸和规格说明;b. 需要考虑产品的材料特性,如塑料的热胀冷缩性,流动性等;c. 确定产品的成型方式和注塑工艺参数。
2. 模具结构设计要求:a. 考虑产品的成型方式,确定模具的结构类型,如单腔模具、多腔模具等;b. 在满足产品尺寸和外观要求的基础上,尽量减小模具的尺寸和重量;c. 考虑模具的使用寿命,采用耐磨、耐腐蚀的材料,优化工艺和热处理;d. 考虑模具的冷却系统,保证注塑过程中材料的快速冷却和成型周期的缩短;e. 考虑模具的导向系统和定位系统,确保模具运动的准确性和稳定性;f. 考虑模具的拆卸性,方便清洗和更换模具部件。
3. 模具零件设计要求:a. 模具芯、模具腔、模具板等零件的尺寸要与产品尺寸要求一致;b. 避免尺寸过小、壁厚过薄等问题,确保零件的强度和刚性;c. 考虑零件的加工工艺,尽量减少加工难度和成本;d. 避免零件之间的干涉和碰撞,确保模具的正常运作;e. 采用标准化零件,方便制造和更换。
四、设计流程:1. 了解产品需求:与产品设计师沟通,收集产品图纸和规格说明;2. 制定模具设计方案:根据产品需求,确定模具的结构类型、尺寸和重量等;3. 进行模具设计:进行模具零件的设计,包括模具芯、模具腔、模具板等;4. 完善模具设计:考虑模具的冷却系统、导向系统、定位系统等;5. 优化模具设计:通过模拟和分析,优化模具结构和零件设计,提高模具的性能;6. 完成模具图纸:根据设计结果,绘制模具图纸,包括三维模型和二维工程图;7. 制造模具:将模具图纸提供给模具制造厂家,开始制造模具;8. 调试模具:完成模具制造后,进行模具调试和试模,保证模具的正常运行;9. 交付使用:完成模具调试后,交付给使用方,并提供模具的维护和保养指南。
6068家用插线板底座注塑模具设计说明书
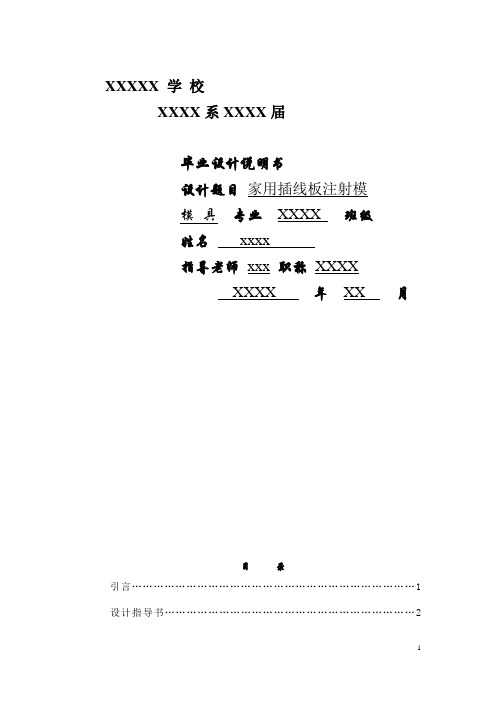
XXXXX 学校XXXX系XXXX届毕业设计说明书设计题目家用插线板注射模模具专业XXXX 班级姓名xxxx指导老师xxx职称XXXXXXXX 年XX 月目录引言 (1)设计指导书 (2)设计说明书 (4)一、毕业设计课题 (4)二、塑件及材料分析 (4)三、模具结构设计 (6)1、分型面 (6)2、型腔布局 (7)3、浇注系统设计 (7)4、排气系统设计 (8)5、成型零件设计 (9)6、脱模机构设计 (16)7、模温调节与冷却系统设计 (20)8、其它设计 (23)9、侧向抽芯机构 (26)10、装配图 (28)三、设计小结 (30)参考资料 (31)引言本说明书为我机械系XXXX届模具设计也制造专业毕业生毕业设计说明书,意在对我专业的学生在大学期间所学专业知识的综合考察、评估。
要在有限的时间内单独完成设计。
也是在走上工作岗位前的一次考察。
本设计说明书是本人完全根据《塑料模具技术手册》的要求形式及相关的工艺编写的。
说明书的内容包括:毕业设计要求,设计课题,设计过程,设计体会及参考文献等。
编写说明书时,力求符合设计步骤,详细说明了塑料注射模具设计的方法,以及各种参数的具体计算方法,如塑件的成型工艺,型腔及型芯的计算,塑料脱模机构的设计,调温系统的设计等。
由于本人才疏学浅,知识根底不牢,缺少经验,在模具结构设计计算和编写设计说明书的全工程中,得到张蓉老师以及其他机械、模具基础课的老师的细心指导,同时也得到同学的热情帮助和指点,在此谨以致谢。
敬请各位老师和同学批评指正,以促我在以后的工作中减少类似的错误,做出成绩,以报恩师的淳淳教诲和母校的培养。
设计者:XXXX XXXX年XX月XX日设计指导书1.设计前应明确的事项(1)明确制品的几何形状及使用要求。
对于形状复杂的制品,有时除看懂其图样外,还需参考产品模型或样品,考虑塑料的种类及制品的成型收缩率、透明度、尺寸公差、表面粗糙度、允许变形范围等范围,即充分了解制品的使用要求,因为这不仅是模具设计的主要依据,而且还是减少模具设计者与产品设计者已意见分歧的手段。
座注塑模设计说明书
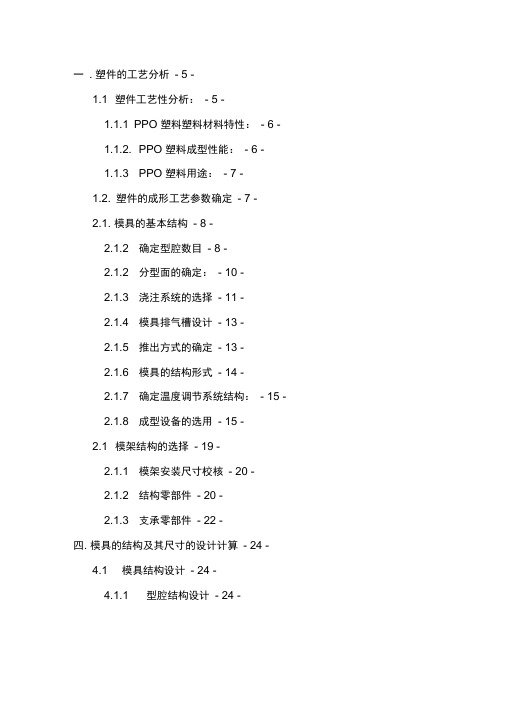
一. 塑件的工艺分析- 5 -1.1 塑件工艺性分析:- 5 -1.1.1 PPO 塑料塑料材料特性:- 6 -1.1.2. PPO 塑料成型性能:- 6 -1.1.3 PPO 塑料用途:- 7 -1.2. 塑件的成形工艺参数确定- 7 -2.1. 模具的基本结构- 8 -2.1.2 确定型腔数目- 8 -2.1.2 分型面的确定:- 10 -2.1.3 浇注系统的选择- 11 -2.1.4 模具排气槽设计- 13 -2.1.5 推出方式的确定- 13 -2.1.6 模具的结构形式- 14 -2.1.7 确定温度调节系统结构:- 15 -2.1.8 成型设备的选用- 15 -2.1 模架结构的选择- 19 -2.1.1 模架安装尺寸校核- 20 -2.1.2 结构零部件- 20 -2.1.3 支承零部件- 22 -四. 模具的结构及其尺寸的设计计算- 24 -4.1 模具结构设计- 24 -4.1.1 型腔结构设计- 24 -4.1.2 型心结构配合额- 24 -4.1.3 模具的导向机构- 25 -4.2 模具成形尺寸设计计算- 25 -4.2.2 型腔深度尺寸的计算- 29 -4.2.3 型芯径向尺寸- 29 -4.2.4 型芯高度尺寸- 30 -4.3 模具的加热、冷却系统的设计- 30 -五. 安装与调试- 31 -5.1 模具的安装试模- 31 -5.2 试模前的准备- 32 - 参考文献- 37 -、八、亠前言塑料是以高分子合成树脂为基本原料,加入一定量的添加剂而成,在一定的温度压力 F 塑制成具有一定结构形状,能在常温下保持其形状不变的材料。
一.塑料工业在国民经济中的地位。
塑料工业是世界上增长最快的工业之一,自从1909 年实现以纯粹化学合成方法生产塑料算起,塑料工业以有九十余年的历史。
1927 年聚氯乙烯塑料问世以来,随着高分子化学技术的发展,各种性能的塑料,特别是聚酰胺,聚甲醛,ABS,聚碳酸脂,聚砜,聚苯醚与氟塑料等工程塑料发展迅速,其速度超过了聚乙烯,聚丙烯,聚氯乙烯与聚苯乙烯等四种通用塑料,是塑料在工业产品与生活用品方面获得广泛的应用,以塑料代替金属的实例,比比皆是。
注塑模具设计说明书

注塑模具设计说明书一、引言注塑模具是一种用于制造塑料制品的重要工具。
它具有精密设计和制造的特点,直接影响到注塑成型工艺的质量和效率。
本文档旨在提供一个注塑模具设计的详细说明书,以帮助使用者了解并正确使用注塑模具。
二、设计原则1. 功能性设计:注塑模具设计的首要目标是确保塑料制品的质量和精度。
需要考虑到产品的形状、尺寸、结构等因素,确保模具能够精确地复制产品的形状。
2. 可靠性设计:模具在长时间运行过程中需具有足够的可靠性和稳定性。
设计时应考虑到材料的选择、结构的合理性、工艺性能等因素,以确保模具能够长时间稳定运行。
3. 高效性设计:注塑模具的设计还要考虑到生产效率的提高。
在保证产品质量的前提下,优化流程、减少工序、提高生产速度等都是设计中需要考虑的因素。
三、设计要点1. 产品参数分析:仔细研究产品的形状、尺寸、材料等参数,并根据不同产品的要求进行合理设计。
2. 模具结构设计:根据产品的特点设计合理的模具结构,包括模具的分型面、脱模方式、冷却系统等。
3. 材料选择:根据产品和模具的要求选择合适的材料,考虑材料的韧性、硬度、耐磨性等因素。
4. 流道系统设计:设计合理的流道系统,以保证熔融塑料流动均匀,避免短流、死角等问题,提高注塑成型过程的效率。
5. 冷却系统设计:优化冷却系统的设计,保证塑料在注塑过程中能够迅速冷却固化,提高生产效率并减少翘曲、变形等问题。
6. 模具表面处理:根据产品的表面要求进行合适的模具表面处理,包括抛光、喷涂等,以提高产品的表面质量。
7. 模具装配:模具设计时应考虑装配的便利性和准确性,保证模具能够容易安装和拆卸。
四、注意事项1. 安全操作:在使用注塑模具时,必须严格遵守相关的操作规程和安全要求,保证操作人员的人身安全。
2. 维护保养:定期对模具进行清洁和维护保养,保证模具的正常运行和寿命的延长。
3. 记录维护:对模具的使用情况进行记录,包括使用次数、维修情况等,以便及时调整维修周期和保养计划。
注塑模具设计说明书

数码相机盖模具设计说明书班级:10材料专业:材料成型及控制工程姓名:刘树飞学号:100118019指导老师:引言 (2)一.产品工艺性分析 (3)1.1设计产品概述 (3)1.2产品工艺性分析 (3)二、注塑机的选择 (3)1、塑件的质量、体积计算 (4)2、浇注系统凝料体积的初步估算 (4)3、注射容量与锁模力校核 (4)(1)注射容量校核 (4)(2)锁模力的校核 (4)4.利用UG软件,设置工件尺寸。
(4)三、分型设计 (5)四、标准模架的选用 (6)(1)先定系列。
(6)(2)看型芯固定方式是否需要加支撑板。
(6)(3)确定模板尺寸。
(6)(4)模架厚度 (6)五、模具滑块设计 (6)(1)抽芯距离和抽芯力的计算 (6)(2)斜导柱设计 (7)①斜导柱倾斜角的确定 (7)②斜导柱的直径计算 (7)③斜导柱长度的计算 (7)④滑块其他零部件设计 (7)六、导向与顶出机构设计 (8)(1)顶出机构设计 (8)①脱模力计算 (8)②推出零件尺寸计算 (8)③创建顶管 (8)④创建拉料杆 (8)(2)导向机构的设计 (8)①导柱的选取 (8)②复位杆的选取 (9)七、浇注系统设计 (9)1.浇注系统整体方案确定 (9)2.主流道设计 (9)3、分流道、浇口和冷料穴设计 (9)八、冷却系统设计 (10)1、冷却水道的尺寸计算 (11)(1)计算单位重量的塑料熔体在凝固时所放出的热量Q1(kJ/kg) (11)(2)求冷却水的体积流量qv(m³/min) (11)(3)查表使冷却水处于紊流状态,取d (11)九、画模具装配图 (12)引言虽然受到全球金融危机影响,但是我国模具整体实力还是得到进一步加强。
近两年来中国的模具制造技术水平又有了新的提高。
从模具产品进出口的地域来看,华东地区的江苏、浙江、上海、山东均位列中国进口和出口模具的十大省市之中。
长江三角地区在模具制造整体水平的数量和质量上均已在国内处于行业重要位置。
D30等径三通注塑模具设计

D30等径三通注塑模具设计D30等径三通注塑模具是一种常用的注塑模具,用于生产管道系统中的三通接头。
在设计这种模具时,需要考虑多个因素,例如模具的尺寸、结构、材料和制造工艺等。
下面是一个关于D30等径三通注塑模具的详细设计说明,总字数超过1200字。
一、模具尺寸设计1.模具整体尺寸:模具的整体尺寸应根据产品的要求确定,通常要考虑到投入产出比和设备的工作空间。
2.管道直径:D30等径三通的直径应根据具体要求确定,尺寸准确度要求较高,所以需要选择合适的工艺和设备。
二、模具结构设计1.模具结构类型:D30等径三通注塑模具结构一般为单模腔或多模腔结构,根据生产需求选择合适的结构类型。
2.模具芯型结构:对于三通注塑模具,通常需要使用可拆卸芯型结构以便于产品的脱模。
三、模具材料选择1.模具材料:选择合适的模具材料是保证模具质量和寿命的关键。
常见的模具材料有P20钢、718钢等。
四、模具制造工艺1.模具结构加工:根据模具设计图纸,分解各个部件,进行加工和装配。
2.模具表面处理:模具表面需要进行打磨和抛光,以确保模具零件的安装精度和表面光洁度。
3.注塑成型工艺:根据模具的设计要求,合理设置注塑机的工艺参数,如注塑温度、注射压力、注射速度等。
五、模具调试和试模1.模具调试:在注塑机上安装和调试模具,调整各个部位的位置和参数,确保模具能够正常运行。
2.试模验证:进行少量试模,检验产品的尺寸精度、外观质量和性能是否符合要求。
六、模具保养和维护1.模具保养:定期清洁和润滑模具,防止生锈和磨损。
2.模具维护:定期检查模具各个部位的磨损程度,及时更换磨损部件,延长模具使用寿命。
以上是关于D30等径三通注塑模具的设计说明,总字数超过1200字。
这种模具的设计需要考虑模具尺寸、结构、材料和制造工艺等多个方面,以确保模具能够满足产品的要求,且具有高精度和稳定性。
模具的设计和制造是一个复杂的过程,需要经验丰富的工程师和专业的制造设备来完成。
连接座注塑模模具设计说明书

*********学院课程设计说明书题目:连接座注塑模模具设计学院:机电工程学院专业:模具设计与制造班级: **********姓名: **********学号: **********指导老师: **********时间: ****年*月*日目录前言 (4)一、零件工艺性分析 (5)二、注塑模的结构确定 (6)三、模具设计的有关计算 (11)四、模具调节温度设计 (14)五、模具闭合高度的确定 (16)六、注塑机有关参数的校核 (16)七、绘制模具总装图 (17)总结 (18)参考文献 (18)引言注塑模具课程设计比较全面的训练,其意义在于为以后的设计工作打基础,培养学生在设计过程中严肃认真、刻苦钻研、一丝不苟、精益求精的态度,使其在设计思想、方法和技能等各方面均获得锻炼和提高。
经过一学期对塑料模具整体结构和细节的学习和了解,为了更进一步的了解模具制造和加工,利用所学模具知识设计一套简单的注塑模具,来巩固所学模具知识。
通过完成模具课程设计,综合应用和巩固模具设计课程以及相关课程的理论基础和专业知识,系统地掌握产品零件的成型工艺分析、模具结构设计的基本方法和步骤、非标准模具零件的设计等模具设计基本方法。
同时,学会准确运用技术标准和资料,培养了认真负责、踏实细致的工作作风和严谨的工作态度,强化了质量意识和时间观念,从而形成了从业的基本职业素质。
第二部分:模具设计实例一、零件工艺性分析工件为图1所示的落料冲孔件,材料为ABS,尺寸精度为4级,生产批量为大批量。
工艺性分析内容如下:技术要求:表面光亮无划伤痕迹1:塑件的原材料分析塑件的材料采用工程塑料ABS,属热塑性塑料,是由丙烯腈,丁二烯和苯乙烯组成的三不共聚物。
本身耐热性和溶性比HIPS佳,且具有光泽性。
由于丙烯腈的腈基极性较强,所以冲击强度,拉伸强度及塑料件的表面硬度均较HIPS佳。
综合物理-力学性能更是优良。
ABS树脂为浅黄色粒状或珠状树脂,熔融温度为217-237℃,热分解温度为250℃以上,无毒,无味,吸水率低,具有优良的综合物理-力学性能,优异的低温抗冲击性能,尺寸稳定性,电性能,耐磨性,抗化学药品性,染色性,成型加工和机械加工较好。
- 1、下载文档前请自行甄别文档内容的完整性,平台不提供额外的编辑、内容补充、找答案等附加服务。
- 2、"仅部分预览"的文档,不可在线预览部分如存在完整性等问题,可反馈申请退款(可完整预览的文档不适用该条件!)。
- 3、如文档侵犯您的权益,请联系客服反馈,我们会尽快为您处理(人工客服工作时间:9:00-18:30)。
课程设计说明书题 目 连接座注塑模模具设计 机电工程学院 模具设计与制造******************** ************** ^年 * 月 * 日目录前言 (4)一、 零件工艺性分析 (5)二、 注塑模的结构确定 (6)三、 模具设计的有关计算 (11)四、 模具调节温度设计 (14)五、 模具闭合高度的确定 (16)********* 学院学 院: 专 业: 班 级: 姓 名: 学 号: 指导老师: 时 间:六、注塑机有关参数的校核 (16)七、绘制模具总装图 (17)总结 (18)参考文献 (18)引言注塑模具课程设计比较全面的训练,其意义在于为以后的设计工作打基础,培养学生在设计过程中严肃认真、刻苦钻研、一丝不苟、精益求精的态度,使其在设计思想、方法和技能等各方面均获得锻炼和提高。
经过一学期对塑料模具整体结构和细节的学习和了解,为了更进一步的了解模具制造和加工,利用所学模具知识设计一套简单的注塑模具,来巩固所学模具知识。
通过完成模具课程设计,综合应用和巩固模具设计课程以及相关课程的理论基础和专业知识,系统地掌握产品零件的成型工艺分析、模具结构设计的基本方法和步骤、非标准模具零件的设计等模具设计基本方法。
同时,学会准确运用技术标准和资料,培养了认真负责、踏实细致的工作作风和严谨的工作态度,强化了质量意识和时间观念,从而形成了从业的基本职业素质。
第二部分:模具设计实例一、零件工艺性分析工件为图1所示的落料冲孔件,材料为ABS尺寸精度为4级,生产批量为大批量。
工艺性分析内容如下:技术要求:表面光亮无划伤痕迹1:塑件的原材料分析塑件的材料采用工程塑料ABS属热塑性塑料,是由丙烯腈,丁二烯和苯乙烯组成的三不共聚物。
本身耐热性和溶性比HIPS佳,且具有光泽性。
由于丙烯腈的腈基极性较强,所以冲击强度,拉伸强度及塑料件的表面硬度均较HIPS佳。
综合物理-力学性能更是优良。
ABS树脂为浅黄色粒状或珠状树脂,熔融温度为217-237 C ,热分解温度为250C以上,无毒,无味,吸水率低, 具有优良的综合物理-力学性能,优异的低温抗冲击性能,尺寸稳定性,电性能,耐磨性,抗化学药品性,染色性,成型加工和机械加工较好。
ABS树脂耐水,无机盐,碱和酸类,不溶于大部分酸类溶剂,而容易溶于醛酮, 脂和某些氯化氢中。
ABS树脂热变形温度较低,不透明,可燃,耐侯性较差,其成型性能较好,流动性好,成形收缩率较小(通常为0.3-0.8%),比热容较低,在料筒中塑化效率高,在模具中凝固较快,成型周期短,但吸水性较大,成形前必须充分干燥,可在柱塞式或螺杆式卧式注射机上成形。
2:塑件结构分析从零件图上分析,该零件总体形状为长方体,在宽度方向的一侧有一个凸台,零件壁厚均匀。
因此,设计时可采用单个分型面抽芯机构。
3:尺寸精度分析制件尺寸选用尺寸精度4级(GB/T14486-1993),零件的尺寸精度中等,对应的模具相关零件的尺寸加工可以得到保证。
从塑件的壁厚来看,壁厚较均匀,有利于制件的成型。
4:表面质量分析该零件的表面除要求没有缺陷、毛刺,内部不得有杂质外,没有特别的表面质量要求,故比较容易实现。
综上分析可以看出,注塑时在工艺参数控制得较好的情况下,零件的成型要求可以得到保证。
5:计算塑件的体积和重量计算塑件的体积:V =15285.6641mm计算塑件的重量:根据设计手册可查得工程塑料ABS的密度为P =1.03g/cm 3,故塑件的重量为:W =15140.0094 X 1.03g= 15594.21g 采用二模一件的模具结构,考虑其外形尺寸、注塑时所需压力和工厂现有设备等情况,初步选用注塑机为XS-ZY-125型。
额定注射量:125cm3;螺杆(柱塞)直径:42mm 注射压力:120MPa 注射行程:115mm 注射方式:螺杆式;合模力:900 KN;最大开模行程:300 mm模具最大厚度:300mm模具最小厚度:200mm6:塑件注塑工艺参数的确定查找附录H和参考工厂实际应用的情况,增强ABS的成型工艺参数可作如下选择。
试模时,可根据实际情况作适当调整。
注塑温度:包括料筒温度和喷嘴温度料筒温度:后段温度t1选用160C中段温度t 2选用170前段温度t3选用190C;注塑压力:选用100MPa(相当于注塑机表压35kgf );注塑时间:选用25s ;保压:选用72MPa(相当于注塑机表压25kgf );保压时间:选用4s ;冷却时间:选用20s 。
二、注塑模的结构设计:1:分型面选择制品在模具中的位置,直接影响到模具结构的复杂程度,模具分型面的确定,浇口的设置,制品尺寸精度和质量等。
因此,开始制定模具方案时,首先必须正确考虑制品在其中的位置;然后再考虑具体的生产条件(包括模具制造的),生产的批量所需的机械化和自动化程度等其他设计问题。
选择分型面的原则是:脱出塑件方便、模具结构简单、型腔排气顺利、确保塑件质量,无损塑件外观、设备利用合理。
所以,模具设计中,分型面的选择很关键,它决定了模具的结构。
应根据分型面选择原则和塑件的成型要求来选择分型面。
故选用下图所示的分型方式较为合理。
这样有利于成型后,塑件的脱模。
2:确定型腔的排列方式本塑件在注塑时采用一模一件,即模具需要一个型腔3:浇注系统设计①主流道设计:直浇口式主浇道呈截锥体,主浇道入口直径d应大于注射机喷嘴直径1伽左右。
主浇道入口的凹坑球面半径R应大于注射机喷嘴球头半径约2-3伽。
锥孔壁粗糙度Ra± 0.8,主流道锥角为2°-4 °过大的锥角会产生湍流或涡流,卷入空气。
根据设计手册查得XS-ZY-125型注塑机喷嘴的有关尺寸:喷嘴前端孔径:d o=© 4mm喷嘴前端球面半径:R o = 12mm根据模具主流道与喷嘴的关系R = R O + (1 〜2)mmd = d o + (0.5 〜1)mm取主流道球面半径R= 13mm;取主流道的小端直径d = © 4.5mm经换算得主流道大端直径D=8.5mm可在主流道出料端设计半径r=1.5mm的圆弧过渡。
②分流道设计:分流道的形状及尺寸,应根据塑件的体积、壁厚、形状的复杂程度、注射速率、分流道长度因素来确定。
本塑件的形状不算太复杂,熔料填充型腔比较容易。
根据型腔的排列方式可知分流道的长度较短,为了方便加工起见,选用截面形状为半圆形的分流道,查表5-3取R=4mm③:浇口的设计浇口是流道和型腔之间的连接部分,也是注塑模进料系统的最后部分,其基本作用是:1》使从流道来的熔融塑料以最快的速度进入并充满型腔。
2》型腔充满后,浇口能迅速冷却封闭,防止型腔内还未冷却的热料回流。
浇口的设计与塑件形状,断面尺寸,模具结构,注塑工艺条件(压力)及塑料性能等因素有关。
浇口截面要小,长度要短,因为只有这样才能满足增料流速度,快速冷却封闭,便于与塑件分离,以及浇口残痕最小等要求。
根据上面的要求,我采用侧浇口形式。
在侧浇口进入或连接型腔的部位,应用圆角以防劈裂。
故侧浇口初选尺寸为1mr K0.8mm< 1.2mm(t X L X h),试模时修正。
④:导柱的选择导柱的选择直形导柱和阶梯形导柱的前端都设计为锥形,便于导向。
两种导柱都可以在工作部分带有贮油槽。
带贮油槽的导柱可以贮存润滑油,延长润滑时间。
直形导柱用于塑件生产批量不大的模具,可以不用导套。
阶梯形导柱用于塑件大批量生产的模具,或导向精度要求高,必须采用导套的模具,装在模具另一侧的导套安装孔可以和导柱安装孔采用同一尺寸,一次加工而成,保证了严格的同轴,本模具采用有肩导柱I型导柱直径尺寸随模具分型面处模板外形尺寸而定,模板尺寸愈大,导柱间的中心距应愈大,所选导柱直径也应愈大。
除了导柱长度按模具具体结构确定外,导柱其余尺寸随导柱直径而定。
本模具导柱选用I型,直径为25mm选用d=25m m, L=100mm,L1=32n有肩导柱。
⑤:导套的选择导向孔可带导套,也可不带导套,带导套的导向孔用于生产批量大或导向精度高的模具。
无论带导套或不带导套的导向空,都不应该设计盲孔,盲孔会增加模具闭合时的阻力,并使模具不能紧密闭合。
带导套的模具应采用阶梯形导柱。
导套长度取决于含导套的模板厚度,其余尺寸随导套导向孔直径而定。
本模具选用d=25mm,L=40m带肩导套。
⑥:排气系统的设计塑料熔体注入模腔的同时,必须置换出型腔内空气和从物料中逸出的挥发性气体,排气系统是注塑模设计的重要组成部分。
排气不良有很多危害:①增加熔体充模流动的阻力,使型腔不能充满,会使塑件棱边不清②在制品上呈现明显可见的流动痕和熔合缝,其力学性能降低③滞留气体使塑件产生银纹,气孔,剥层等表面缺陷④型腔内气体受到压缩后产生瞬间局部高温,使塑件熔体分解变色,甚至炭化烧焦⑤由于排气不良,降低了充模速度,增长了注塑成型周期•常用的排气系统设计方法:①分型面排气②拼接裂缝③利用烧结块④冷料井⑤排气槽.对于小型模具可利用分型面排气,本模具的分型面位于塑料溶体流动的末端,易于排气。
4:推出机构设计该零件采用推件板推出机构①推杆位置、推杆形状尺寸及推杆数量等的确定推杆位置、推杆形状尺寸如图所示:由该模具结构确定推杆的数量为6②推杆安装固定及配合推杆直径d与推件板上的推杆孔采用H8/f7间隙配合,推件板进行淬火处理,硬度HRC>50推杆的材料为T8,且工作端配合部分的表面粗糙度Ra<0.8「m ;④推出机构导向设计5:成型零件结构设计①:凹模的结构设计本模具采用一模两件的结构形式,凹模拟采用整体式结构,分流道和浇口均设在凹模上②:凸模结构设计三、模具设计的有关计算:成型零件工作尺寸计算时采用平均尺寸、平均收缩率、平均制造公差和平均磨损量来进行计算。
查表得工程塑料(ABS的收缩率为Q=0.3%--0.8%,故平均收缩率为Qcp=(0.3+0.8)%/2=0.55%,模具制造公差取厶尸(1/4 〜1/5)△'800'004;-2000-00626 0 . -0.006;■280°.00634-0.0073_0.0030.006250 ;46^.007 ;推杆导套的结构形式及尺寸如图所示:0L8022①:型腔和型芯工作尺寸计算按平均收缩率计算模具成型零件工作尺寸 型腔径向尺寸 D m =[(1 S cp )D 一4新型芯径向尺寸 d m <(1 S cp )d 3『_z 4型腔深度尺寸 2 £H m <(1 S cp )H —3再0 z 3型芯高度尺寸 h m 二[(1 S cp )h 2 ]:z3中心距6Z L m <(1 S ep )L]子 2② :型芯尺寸的计算3 3 d m =[(1 • S cp )d ;化=[(1 0.0055) 8 二 0.004]0』.0。