FPGA毕业设计论文英文
毕业设计(论文)-基于fpga的sdram控制器的实现(软件部分)[管理资料]
![毕业设计(论文)-基于fpga的sdram控制器的实现(软件部分)[管理资料]](https://img.taocdn.com/s3/m/0426a5c767ec102de3bd8968.png)
毕业设计(论文)机械与电气工程学院电气工程及其自动化专业毕业设计(论文)题目基于FPGA的SDRAM控制器的实现(软件部分)学生姓名班级电气工程及其自动化学号指导教师完成日期2012 年 6 月 6 日基于FPGA的SDRAM控制器的实现(软件部分)The realization of SDRAM controller based on FPGA (software)总计毕业设计(论文) 41 页表格 6 个插图 21 幅摘要文中介绍了FPGA的开发流程、硬件开发语言及其开发环境QuartusII和SDRAM的结构特点和工作原理,根据SDRAM的工作原理、控制时序和指令特点,设计一种基于FPGA的SDRAM控制器的方案。
SDRAM控制器的设计主要由主控制模块、信号产生模块、数据路径模块和参数模块组成。
本设计解决SDRAM控制复杂、不方便的问题,并用Verilog给予仿真结果。
仿真结果表明使用该方法设计实现的控制器能够使系统方便,可靠的对SDRAM进行操作。
关键字:SDRAM控制器FPGA 控制模块软件仿真AbstractThis paper introduces the development process and FPGA hardware development language and the development environment of SDRAM QuartusII and structural characteristics and working principle, according to the working principle of SDRAM, sequence control and instruction characteristics, a scheme based on FPGA SDRAM controller is designed. SDRAM controller design mainly by the master control module, signal module, data path module and parameter module composition. This design solved a problem about the controlling complexity of SDRAM controller, and gives the simulation results by using Verilog. The simulation results show that using this method to design the controller can realize the system is convenient, reliable operation of SDRAM.Key words: SDRAM controller FPGA Control module Software simulation目录摘要 (I)Abstract (II)第一章绪论 (1)课题背景 (1)课题研究的意义 (1)第二章FPGA与Quartus II软件简介 (2)FPGA简介 (2)FPGA背景 (2)FGPA结构原理 (2)Quartus II软件简介 (3)硬件描述语言Verilog (4)FPGA开发过程 (5)第三章SDRAM的技术介绍 (6) (6)SDRAM简介 (6)SRAM和DRAM (6)SDRAM发展过程 (7)SDRAM工作原理和基本操作 (8)SDRAM存储的工作原理 (9)SDRAM 的引脚信号 (9)SDRAM基本命令 (10)SDRAM初始化 (10)SDRAM读、写操作 (11)终止操作 (12)第四章 SDRAM控制器设计 (12)SDRAM控制器 (13)主控制模块 (14)信号产生模块 (16)参数模块 (18)数据通路模块 (19)第五章SDRAM的读、写仿真 (19)SDRAM控制器时序仿真 (20)Quartus II (20)读仿真时序 (20)写仿真时序 (21)仿真结果分析 (22)结论 (24)参考文献 (25)致谢 (26)附录 (27)第一章绪论课题背景伴随着电子信息技术的飞速发展和其在通讯、工业、商业、医疗等方面的广泛应用,人们对信息的需求逐渐向着更快、更多、更准确发展。
fpga毕业设计
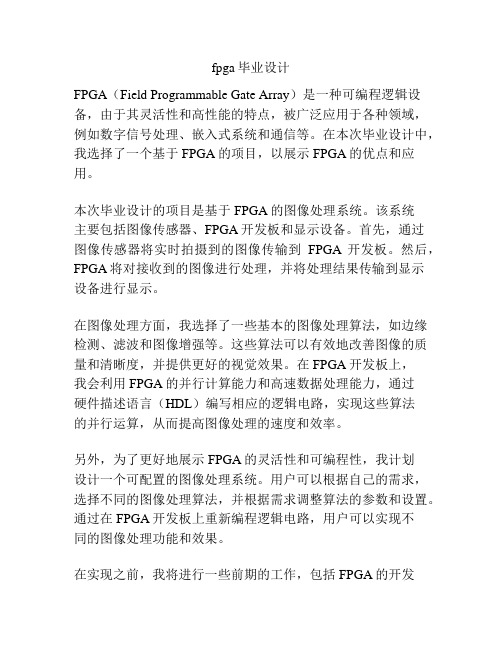
fpga毕业设计FPGA(Field Programmable Gate Array)是一种可编程逻辑设备,由于其灵活性和高性能的特点,被广泛应用于各种领域,例如数字信号处理、嵌入式系统和通信等。
在本次毕业设计中,我选择了一个基于FPGA的项目,以展示FPGA的优点和应用。
本次毕业设计的项目是基于FPGA的图像处理系统。
该系统主要包括图像传感器、FPGA开发板和显示设备。
首先,通过图像传感器将实时拍摄到的图像传输到FPGA开发板。
然后,FPGA将对接收到的图像进行处理,并将处理结果传输到显示设备进行显示。
在图像处理方面,我选择了一些基本的图像处理算法,如边缘检测、滤波和图像增强等。
这些算法可以有效地改善图像的质量和清晰度,并提供更好的视觉效果。
在FPGA开发板上,我会利用FPGA的并行计算能力和高速数据处理能力,通过硬件描述语言(HDL)编写相应的逻辑电路,实现这些算法的并行运算,从而提高图像处理的速度和效率。
另外,为了更好地展示FPGA的灵活性和可编程性,我计划设计一个可配置的图像处理系统。
用户可以根据自己的需求,选择不同的图像处理算法,并根据需求调整算法的参数和设置。
通过在FPGA开发板上重新编程逻辑电路,用户可以实现不同的图像处理功能和效果。
在实现之前,我将进行一些前期的工作,包括FPGA的开发环境搭建、相关的图像处理算法的研究和实验验证。
同时,我也会参考相关的文献和资料,了解已有的图像处理算法在FPGA上的实现方法和性能表现,以便更好地设计和优化系统。
总的来说,本次毕业设计的目标是基于FPGA的图像处理系统的设计和实现,通过利用FPGA的优点和特性,提高图像处理的速度和效率,并实现用户可配置的图像处理功能。
通过该项目,我将掌握FPGA的开发和应用技术,以及图像处理算法的实现和优化方法,为以后的研究和工作打下坚实的基础。
同时,通过展示该项目的成果,也能够展示FPGA的广阔应用前景和潜力。
一篇关于FPGA的英文文献及翻译
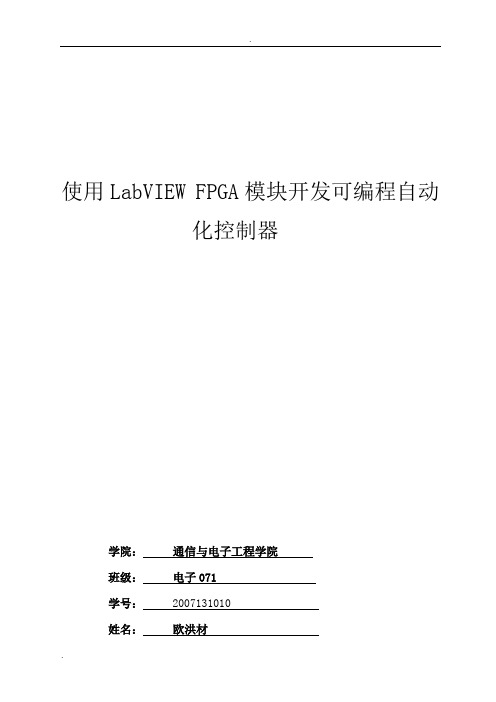
使用LabVIEW FPGA模块开发可编程自动化控制器学院:通信与电子工程学院班级:电子071学号: 2007131010姓名:欧洪材Building Programmable Automation Controllers with LabVIEWFPGAOverviewProgrammable Automation Controllers (PACs) are gaining acceptance within the industrial control market as the ideal solution for applications that require highly integrated analog and digital I/O, floating-point processing, and seamless connectivity to multiple processing nodes. National Instruments offers a variety of PAC solutions powered by one common software development environment, NI LabVIEW. With LabVIEW, you can build custom I/O interfaces for industrial applications using add-on software, such as the NI LabVIEW FPGA Module.With the LabVIEW FPGA Module and reconfigurable I/O (RIO) hardware, National Instruments delivers an intuitive, accessible solution for incorporating the flexibility and customizability of FPGA technology into industrial PAC systems. You can define the logic embedded in FPGA chips across the family of RIO hardware targets without knowing low-level hardware description languages (HDLs) or board-level hardware design details, as well as quickly define hardware for ultrahigh-speed control, customized timing and synchronization, low-level signal processing, and custom I/O with analog, digital, and counters within a single device. You also can integrate your custom NI RIO hardware with image acquisition and analysis, motion control, and industrial protocols, such as CAN and RS232, to rapidly prototype and implement a complete PAC system.Table of Contents1.Introduction2.NI RIO Hardware for PACs3.Building PACs with LabVIEW and the LabVIEW FPGA Module4.FPGA Development Flowing NI SoftMotion to Create Custom Motion Controllers6.Applications7.ConclusionIntroductionYou can use graphical programming in LabVIEW and the LabVIEW FPGA Module to configure the FPGA (field-programmable gate array) on NI RIO devices. RIO technology, the merging of LabVIEW graphical programming with FPGAs on NI RIOhardware, provides a flexible platform for creating sophisticated measurement and control systems that you could previously create only with custom-designed hardware.An FPGA is a chip that consists of many unconfigured logic gates. Unlike the fixed, vendor-defined functionality of an ASIC (application-specific integrated circuit) chip, you can configure and reconfigure the logic on FPGAs for your specific application. FPGAs are used in applications where either the cost of developing and fabricating an ASIC is prohibitive, or the hardware must be reconfigured after being placed into service. The flexible,software-programmable architecture of FPGAs offer benefits such ashigh-performance execution of custom algorithms, precise timing and synchronization, rapid decision making, and simultaneous execution of parallel tasks. Today, FPGAs appear in such devices as instruments, consumer electronics, automobiles, aircraft, copy machines, and application-specific computer hardware. While FPGAs are often used in industrial control products, FPGA functionality has not previously been made accessible to industrial control engineers. Defining FPGAs has historically required expertise using HDL programming or complex design tools used more by hardware design engineers than by controlengineers.Within the test-fixture the tx output of the transmitter module is loop ed back to the rx input of the receiver module.This allows the transmitter module to be used as test signal generator for the receiver module.Data can be written in parallel format to the transmitter module and looped back in serial format to the rx input of the receiver module,and data received can finally be read out in paral lel format from the receiver module.In order to automate the testing of the UART a s much as possible,tree independent Verilog tasks were written as follows.The Ve rilog task“write_to_transmitter”holds all necessary statements required to generate a s ingle parallel data write sequence to the transmitter module.Data that are writt en to the transmitter upon execution of the“write_to_transmitter”task,get la tched internal to the test-fixture for later analysis.The Verilog task“read_ou t_receiver”holds all necessary statements required to generate a single paral lel data read out sequence from the receiver module.Data that are read out of the receiver upon execution of the“read_out_receiver”task,get latched internalto the test-fixture for later analysis.The Verilog task“compare_data”holds a ll necessary statements required to compare the previous data written to the tran smitter module,to the corresponding and most recent data received and read out f rom the receive r module.If any discrepancy occurs,the“compare_data”task fl ags for an error by writing out the data values that were written to the transmitte r module,as well as the corresponding data values that were received by and read o ut from the receiver module.The simulation is immediately stopped by the“compa re_data”task if any discrepancy occurs.Besides the tree above mentioned Verilo g tasks,the test-fixture holds the statements to generate the mclkx16,the master reset signals as well as the“tx to rx”loop back feature.The statements are c onsidered trivial,and will not be illustrated here,but can be referred to within the test-fixture itself.The core of the test-fixture is a behavioral level“for loop”that executes the tree above mentioned Verilog tasks in order to write all possible data combinations to the transmitter and verify that same data gets prop erly received by the receiver.The for loop is showed below in figure21.Next to port definitions comes port directions.Directions are specified as in put,output or inout(bidirectional),and can be referred to in table1.Next to the specification of port directions comes declaration of internal signals.Inter nal signals in Verilog are declared as“wire”or“reg”data types.Signals of the“wire”type are used for continuos assignments,also called combinatorial s tatements.Signals of the“reg”type are used for assignments within the Verilog“always”block,often use for sequential logic assignments,but not necessari ly.For further explanation see aVerilog reference book.Data types of the internal signals of the module can be referred to in table3.We have now passed by all nec essary declarations,and are now ready to look at the actual ing hardware description language allows us to describe the function of the transm itter in a more behavioral manner,rather than focus on it’s actual implementation at gate level In software programming language, functions and procedures breaks larger programs into more readable,manageable and certa inly maintainable pieces.The Verilog language provides functions and tasks as co nstructs,analogous to software functions and procedures.A Verilog function andtask are used as the equivalent to multiple lines of Verilog code,where certain i nputs or signals affects certain outputs or variables.The use of functions and ta sks usually takes place where multiple lines of code are repeatedly used in a desi gn,and hence makes the design easier to read and certainly maintain.A Verilog fu nction can have multiple inputs,but always have only one output,while the Veril og task can have both multiple inputs,and multiple outputs and even in some cases,non of each.Below is shown the Verilog task,that hold all necessary sequential statements,to describe the transmitter in the“shift”modeWith the LabVIEW FPGA Module and NI RIO hardware, you now can use LabVIEW, a high-level graphical development environment designed specifically for measurement and control applications, to create PACs that have the customization, flexibility, and high-performance of FPGAs. Because the LabVIEW FPGA Module configures custom circuitry in hardware, your system can process and generate synchronized analog and digital signals rapidly and deterministically. Figure 1 illustrates many of the NI RIO devices that you can configure using the LabVIEW FPGA Module.Figure 1. LabVIEW FPGA VI Block Diagram and RIO Hardware PlatformsNI RIO Hardware for PACsHistorically, programming FPGAs has been limited to engineers who have in-depth knowledge of VHDL or other low-level design tools, which require overcoming a very steep learning curve. With the LabVIEW FPGA Module, NI has opened FPGA technology to a broader set of engineers who can now define FPGA logic using LabVIEW graphical development. Measurement and control engineers can focus primarily on their test and control application, where their expertise lies, rather than the low-level semantics of transferring logic into the cells of the chip. The LabVIEW FPGA Module model works because of the tight integration between the LabVIEW FPGA Module and the commercial off-the-shelf (COTS) hardware architecture of the FPGA and surrounding I/O components.National Instruments PACs provide modular, off-the-shelf platforms for your industrial control applications. With the implementation of RIO technology on PCI, PXI, and Compact Vision System platforms and the introduction of RIO-based CompactRIO, engineers now have the benefits of a COTS platform with thehigh-performance, flexibility, and customization benefits of FPGAs at their disposal to build PACs. National Instruments PCI and PXI R Series plug-in devices provide analog and digital data acquisition and control for high-performance, user-configurable timing and synchronization, as well as onboard decision making on a single device. Using these off-the-shelf devices, you can extend your NI PXI or PCI industrial control system to include high-speed discrete and analog control, custom sensor interfaces, and precise timing and control.NI CompactRIO, a platform centered on RIO technology, provides a small, industrially rugged, modular PAC platform that gives you high-performance I/O and unprecedented flexibility in system timing. You can use NI CompactRIO to build an embedded system for applications such as in-vehicle data acquisition, mobile NVH testing, and embedded machine control systems. The rugged NICompactRIO system is industrially rated and certified, and it is designed for greater than 50 g of shock at a temperature range of -40 to 70 °C.NI Compact Vision System is a rugged machine vision package that withstands the harsh environments common in robotics, automated test, and industrial inspection systems. NI CVS-145x devices offer unprecedented I/O capabilities and network connectivity for distributed machine vision applications.NI CVS-145x systems use IEEE 1394 (FireWire) technology, compatible with more than 40 cameras with a wide range of functionality, performance, and price. NI CVS-1455 and NI CVS-1456 devices contain configurable FPGAs so you can implement custom counters, timing, or motor control in your machine vision application.Building PACs with LabVIEW and the LabVIEW FPGA ModuleWith LabVIEW and the LabVIEW FPGA Module, you add significant flexibility and customization to your industrial control hardware. Because many PACs are already programmed using LabVIEW, programming FPGAs with LabVIEW is easy because it uses the same LabVIEW development environment. When you target the FPGA on an NI RIO device, LabVIEW displays only the functions that can be implemented in the FPGA, further easing the use of LabVIEW to program FPGAs. The LabVIEW FPGA Module Functions palette includes typical LabVIEW structures and functions, such as While Loops, For Loops, Case Structures, and Sequence Structures as well as a dedicated set of LabVIEW FPGA-specific functions for math, signal generation and analysis, linear and nonlinear control, comparison logic, array and cluster manipulation, occurrences, analog and digital I/O, and timing. You can use a combination of these functions to define logic and embed intelligence onto your NI RIO device.Figure 2 shows an FPGA application that implements a PID control algorithm on the NI RIO hardware and a host application on a Windows machine or an RT target that communicates with the NI RIO hardware. This application reads from analog input 0 (AI0), performs the PID calculation, and outputs the resulting data on analog output 0 (AO0). While the FPGA clock runs at 40 MHz the loop in this example runs much slower because each component takes longer than one-clock cycle to execute. Analog control loops can run on an FPGA at a rate of about 200 kHz. You can specify the clock rate at compile time. This example shows only one PID loop; however, creating additional functionality on the NI RIO device is merely a matter of adding another While Loop. Unlike traditional PC processors, FPGAs are parallel processors. Adding additional loops to your application does not affect the performance of your PID loop.Figure 2. PID Control Using an Embedded LabVIEW FPGA VI with Corresponding LabVIEW HostVI.FPGA Development FlowAfter you create the LabVIEW FPGA VI, you compile the code to run on the NI RIO hardware. Depending on the complexity of your code and the specifications of your development system, compile time for an FPGA VI can range from minutes to several hours. To maximize development productivity, with the R Series RIO devices you can use a bit-accurate emulation mode so you can verify the logic of your design before initiating the compile process. When you target the FPGA Device Emulator, LabVIEW accesses I/O from the device and executes the VI logic on the Windows development computer. In this mode, you can use the same debugging tools available in LabVIEW for Windows, such as execution highlighting, probes, and breakpoints.Once the LabVIEW FPGA code is compiled, you create a LabVIEW host VI to integrate your NI RIO hardware into the rest of your PAC system. Figure 3 illustrates the development process for creating an FPGA application. The host VI uses controls and indicators on the FPGA VI front panel to transfer databetween the FPGA on the RIO device and the host processing engine. These front panel objects are represented as data registers within the FPGA. The host computer can be either a PC or PXI controller running Windows or a PC, PXI controller, Compact Vision System, or CompactRIO controller running a real-time operating system (RTOS). In the above example, we exchange the set point, PID gains, loop rate, AI0, and AO0 data with the LabVIEW host VI.Figure 3. LabVIEW FPGA Development FlowThe NI RIO device driver includes a set of functions to develop a communication interface to the FPGA. The first step in building a host VI is to open a reference to the FPGA VI and RIO device. The Open FPGA VI Reference function, as seen in Figure 2, also downloads and runs the compiled FPGA code during execution. After opening the reference, you read and write to the control and indicator registers on the FPGA using the Read/Write Control function. Once you wire the FPGA reference into this function, you can simply select which controls and indicators you want to read and write to. You can enclose the FPGA Read/Write function within a While Loop to continuously read and write to the FPGA. Finally, the last function within the LabVIEW host VI in Figure 2 is the Close FPGA VI Reference function. The Close FPGA VI Reference function stops the FPGA VI and closes the reference to the device. Now you can download other compiled FPGA VIs to the device to change or modify its functionality.The LabVIEW host VI can also be used to perform floating-point calculations, data logging, networking, and any calculations that do not fit within the FPGA fabric. For added determinism and reliability, you can run your host application on an RTOS with the LabVIEW Real-Time Module. LabVIEW Real-Time systems provide deterministic processing engines for functions performed synchronously or asynchronously to the FPGA. For example, floating-point arithmetic, including FFTs, PID calculations, and custom control algorithms, are often performed in the LabVIEW Real-Time environment. Relevant data can be stored on a LabVIEW Real-Time system or transferred to a Windows host computer for off-line analysis, data logging, or user interface displays. The architecture for this configuration is shown in Figure 4. Each NI PAC platform that offers RIO hardware can run LabVIEW Real-Time VIs.Figure 4. Complete PAC Architecture Using LabVIEW FPGA, LabVIEW Real-Time and Host PC Within each R Series and CompactRIO device, there is flash memory available to store a compiled LabVIEW FPGA VI and run the application immediately upon power up of the device. In this configuration, as long as the FPGA has power, it runs the FPGA VI, even if the host computer crashes or is powered down. This is ideal for programming safety power down and power up sequences when unexpected events occur.Using NI SoftMotion to Create Custom Motion ControllersThe NI SoftMotion Development Module for LabVIEW provides VIs and functions to help you build custom motion controllers as part of NI PAC hardware platforms that can include NI RIO devices, DAQ devices, and Compact FieldPoint. NI SoftMotion provides all of the functions that typically reside on a motion controller DSP. With it, you can handle path planning, trajectory generation, and position and velocity loop control in the NI LabVIEW environment and then deploy the code on LabVIEW Real-Time or LabVIEW FPGA-based target hardware.NI SoftMotion includes functions for trajectory generator and spline engine and examples with complete source code for supervisory control, position, and velocity control loop using the PID algorithm. Supervisory control and the trajectory generator run on a LabVIEW Real-Time target and run at millisecond loop rates. The spline engine and the control loop can run either on a LabVIEW Real-Time target at millisecond loop rates or on a LabVIEW FPGA target at microsecond loop rates.ApplicationsBecause the LabVIEW FPGA Module can configure low-level hardware design of FPGAs and use the FPGAs within in a modular system, it is ideal for industrial control applications requiring custom hardware. These custom applications can include a custom mix of analog, digital, and counter/timer I/O, analog control up to 125 kHz, digital control up to 20 MHz, and interfacing to custom digital protocols for the following:Batch control∙Discrete control∙Motion control∙In-vehicle data acquisition∙Machine condition monitoring∙Rapid control prototyping (RCP)∙Industrial control and acquisition∙Distributed data acquisition and control∙Mobile/portable noise, vibration, and harshness (NVH) analysis ConclusionThe LabVIEW FPGA Module brings the flexibility, performance, and customization of FPGAs to PAC platforms. Using NI RIO devices and LabVIEW graphical programming, you can build flexible and custom hardware using the COTS hardware often required in industrial control applications. Because you are using LabVIEW, a programming language already used in many industrial control applications, to define your NI RIO hardware, there is no need to learn VHDL or other low-level hardware design tools to create custom hardware. Using the LabVIEW FPGA Module and NI RIO hardware as part of your NI PAC adds significant flexibility and functionality for applications requiring ultrahigh-speed control, interfaces to custom digital protocols, or a custom I/O mix of analog, digital, and counters.使用LabVIEW FPGA(现场可编程门阵列)模块开发可编程自动化控制器综述工业控制上的应用要求高度集成的模拟和数字输入输出、浮点运算和多重处理节点的无缝连接。
一篇关于FPGA的英文文献及翻译
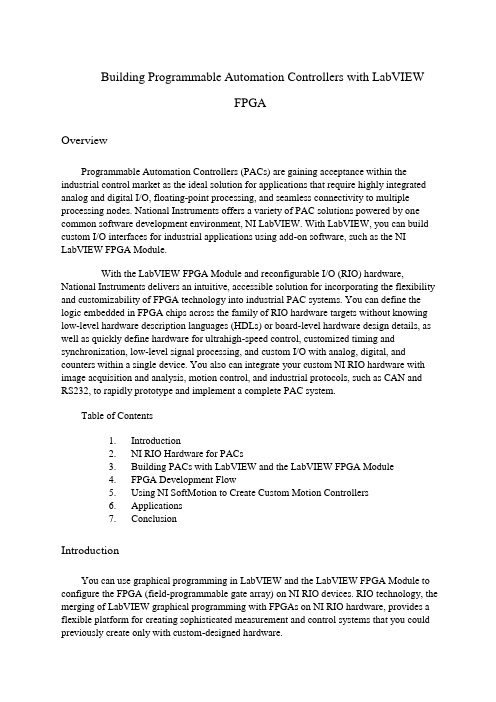
Building Programmable Automation Controllers with LabVIEWFPGAOverviewProgrammable Automation Controllers (PACs) are gaining acceptance within the industrial control market as the ideal solution for applications that require highly integrated analog and digital I/O, floating-point processing, and seamless connectivity to multiple processing nodes. National Instruments offers a variety of PAC solutions powered by one common software development environment, NI LabVIEW. With LabVIEW, you can build custom I/O interfaces for industrial applications using add-on software, such as the NI LabVIEW FPGA Module.With the LabVIEW FPGA Module and reconfigurable I/O (RIO) hardware, National Instruments delivers an intuitive, accessible solution for incorporating the flexibility and customizability of FPGA technology into industrial PAC systems. You can define the logic embedded in FPGA chips across the family of RIO hardware targets without knowing low-level hardware description languages (HDLs) or board-level hardware design details, as well as quickly define hardware for ultrahigh-speed control, customized timing and synchronization, low-level signal processing, and custom I/O with analog, digital, and counters within a single device. You also can integrate your custom NI RIO hardware with image acquisition and analysis, motion control, and industrial protocols, such as CAN and RS232, to rapidly prototype and implement a complete PAC system.Table of Contents1.Introduction2.NI RIO Hardware for PACs3.Building PACs with LabVIEW and the LabVIEW FPGA Module4.FPGA Development Flowing NI SoftMotion to Create Custom Motion Controllers6.Applications7.ConclusionIntroductionYou can use graphical programming in LabVIEW and the LabVIEW FPGA Module to configure the FPGA (field-programmable gate array) on NI RIO devices. RIO technology, the merging of LabVIEW graphical programming with FPGAs on NI RIO hardware, provides a flexible platform for creating sophisticated measurement and control systems that you could previously create only with custom-designed hardware.An FPGA is a chip that consists of many unconfigured logic gates. Unlike the fixed, vendor-defined functionality of an ASIC (application-specific integrated circuit) chip, you can configure and reconfigure the logic on FPGAs for your specific application. FPGAs are used in applications where either the cost of developing and fabricating an ASIC is prohibitive, or the hardware must be reconfigured after being placed into service. The flexible,software-programmable architecture of FPGAs offer benefits such as high-performance execution of custom algorithms, precise timing and synchronization, rapid decision making, and simultaneous execution of parallel tasks. Today, FPGAs appear in such devices as instruments, consumer electronics, automobiles, aircraft, copy machines, andapplication-specific computer hardware. While FPGAs are often used in industrial control products, FPGA functionality has not previously been made accessible to industrial control engineers. Defining FPGAs has historically required expertise using HDL programming or complex design tools used more by hardware design engineers than by control engineers.With the LabVIEW FPGA Module and NI RIO hardware, you now can use LabVIEW, a high-level graphical development environment designed specifically for measurement and control applications, to create PACs that have the customization, flexibility, andhigh-performance of FPGAs. Because the LabVIEW FPGA Module configures custom circuitry in hardware, your system can process and generate synchronized analog and digital signals rapidly and deterministically. Figure 1 illustrates many of the NI RIO devices that you can configure using the LabVIEW FPGA Module.Figure 1. LabVIEW FPGA VI Block Diagram and RIO Hardware PlatformsNI RIO Hardware for PACsHistorically, programming FPGAs has been limited to engineers who have in-depth knowledge of VHDL or other low-level design tools, which require overcoming a very steep learning curve. With the LabVIEW FPGA Module, NI has opened FPGA technology to a broader set of engineers who can now define FPGA logic using LabVIEW graphical development. Measurement and control engineers can focus primarily on their test and control application, where their expertise lies, rather than the low-level semantics of transferring logic into the cells of the chip. The LabVIEW FPGA Module model works because of the tightintegration between the LabVIEW FPGA Module and the commercial off-the-shelf (COTS) hardware architecture of the FPGA and surrounding I/O components.National Instruments PACs provide modular, off-the-shelf platforms for your industrial control applications. With the implementation of RIO technology on PCI, PXI, and Compact Vision System platforms and the introduction of RIO-based CompactRIO, engineers now have the benefits of a COTS platform with the high-performance, flexibility, and customization benefits of FPGAs at their disposal to build PACs. National Instruments PCI and PXI R Series plug-in devices provide analog and digital data acquisition and control for high-performance, user-configurable timing and synchronization, as well as onboard decision making on a single device. Using these off-the-shelf devices, you can extend your NI PXI or PCI industrial control system to include high-speed discrete and analog control, custom sensor interfaces, and precise timing and control.NI CompactRIO, a platform centered on RIO technology, provides a small, industrially rugged, modular PAC platform that gives you high-performance I/O and unprecedented flexibility in system timing. You can use NI CompactRIO to build an embedded system for applications such as in-vehicle data acquisition, mobile NVH testing, and embedded machine control systems. The rugged NI CompactRIO system is industrially rated and certified, and it is designed for greater than 50 g of shock at a temperature range of -40 to 70 °C.NI Compact Vision System is a rugged machine vision package that withstands the harsh environments common in robotics, automated test, and industrial inspection systems. NICVS-145x devices offer unprecedented I/O capabilities and network connectivity for distributed machine vision applications.NI CVS-145x systems use IEEE 1394 (FireWire) technology, compatible with more than 40 cameras with a wide range of functionality, performance, and price. NI CVS-1455 and NI CVS-1456 devices contain configurable FPGAs so you can implement custom counters, timing, or motor control in your machine vision application.Building PACs with LabVIEW and the LabVIEW FPGA Module With LabVIEW and the LabVIEW FPGA Module, you add significant flexibility and customization to your industrial control hardware. Because many PACs are already programmed using LabVIEW, programming FPGAs with LabVIEW is easy because it uses the same LabVIEW development environment. When you target the FPGA on an NI RIO device, LabVIEW displays only the functions that can be implemented in the FPGA, further easing the use of LabVIEW to program FPGAs. The LabVIEW FPGA Module Functions palette includes typical LabVIEW structures and functions, such as While Loops, For Loops, Case Structures, and Sequence Structures as well as a dedicated set of LabVIEWFPGA-specific functions for math, signal generation and analysis, linear and nonlinear control, comparison logic, array and cluster manipulation, occurrences, analog and digital I/O, and timing. You can use a combination of these functions to define logic and embed intelligence onto your NI RIO device.Figure 2 shows an FPGA application that implements a PID control algorithm on the NI RIO hardware and a host application on a Windows machine or an RT target that communicates with the NI RIO hardware. This application reads from analog input 0 (AI0), performs the PID calculation, and outputs the resulting data on analog output 0 (AO0). While the FPGA clock runs at 40 MHz the loop in this example runs much slower because each component takes longer than one-clock cycle to execute. Analog control loops can run on an FPGA at a rate of about 200 kHz. You can specify the clock rate at compile time. This example shows only one PID loop; however, creating additional functionality on the NI RIO device is merely a matter of adding another While Loop. Unlike traditional PC processors, FPGAs are parallel processors. Adding additional loops to your application does not affect the performance of your PID loop.Figure 2. PID Control Using an Embedded LabVIEW FPGA VI with Corresponding LabVIEW HostVI.FPGA Development FlowAfter you create the LabVIEW FPGA VI, you compile the code to run on the NI RIO hardware. Depending on the complexity of your code and the specifications of your development system, compile time for an FPGA VI can range from minutes to several hours.To maximize development productivity, with the R Series RIO devices you can use abit-accurate emulation mode so you can verify the logic of your design before initiating the compile process. When you target the FPGA Device Emulator, LabVIEW accesses I/O from the device and executes the VI logic on the Windows development computer. In this mode, you can use the same debugging tools available in LabVIEW for Windows, such as execution highlighting, probes, and breakpoints.Once the LabVIEW FPGA code is compiled, you create a LabVIEW host VI to integrate your NI RIO hardware into the rest of your PAC system. Figure 3 illustrates the development process for creating an FPGA application. The host VI uses controls and indicators on the FPGA VI front panel to transfer data between the FPGA on the RIO device and the host processing engine. These front panel objects are represented as data registers within the FPGA. The host computer can be either a PC or PXI controller running Windows or a PC, PXI controller, Compact Vision System, or CompactRIO controller running a real-time operating system (RTOS). In the above example, we exchange the set point, PID gains, loop rate, AI0, and AO0 data with the LabVIEW host VI.Figure 3. LabVIEW FPGA Development FlowThe NI RIO device driver includes a set of functions to develop a communication interface to the FPGA. The first step in building a host VI is to open a reference to the FPGA VI and RIO device. The Open FPGA VI Reference function, as seen in Figure 2, also downloads and runs the compiled FPGA code during execution. After opening the reference, you read and write to the control and indicator registers on the FPGA using the Read/Write Control function. Once you wire the FPGA reference into this function, you can simply select which controls and indicators you want to read and write to. You can enclose the FPGA Read/Write function within a While Loop to continuously read and write to the FPGA. Finally, the last function within the LabVIEW host VI in Figure 2 is the Close FPGA VI Reference function. The Close FPGA VI Reference function stops the FPGA VI and closes the reference to the device. Now you can download other compiled FPGA VIs to the device to change or modify its functionality.The LabVIEW host VI can also be used to perform floating-point calculations, data logging, networking, and any calculations that do not fit within the FPGA fabric. For added determinism and reliability, you can run your host application on an RTOS with the LabVIEW Real-Time Module. LabVIEW Real-Time systems provide deterministicprocessing engines for functions performed synchronously or asynchronously to the FPGA. For example, floating-point arithmetic, including FFTs, PID calculations, and custom control algorithms, are often performed in the LabVIEW Real-Time environment. Relevant data can be stored on a LabVIEW Real-Time system or transferred to a Windows host computer for off-line analysis, data logging, or user interface displays. The architecture for this configuration is shown in Figure 4. Each NI PAC platform that offers RIO hardware can run LabVIEW Real-Time VIs.Figure 4. Complete PAC Architecture Using LabVIEW FPGA, LabVIEW Real-Time and Host PC Within each R Series and CompactRIO device, there is flash memory available to store a compiled LabVIEW FPGA VI and run the application immediately upon power up of the device. In this configuration, as long as the FPGA has power, it runs the FPGA VI, even if the host computer crashes or is powered down. This is ideal for programming safety power down and power up sequences when unexpected events occur.Using NI SoftMotion to Create Custom Motion ControllersThe NI SoftMotion Development Module for LabVIEW provides VIs and functions to help you build custom motion controllers as part of NI PAC hardware platforms that can include NI RIO devices, DAQ devices, and Compact FieldPoint. NI SoftMotion provides all of the functions that typically reside on a motion controller DSP. With it, you can handle path planning, trajectory generation, and position and velocity loop control in the NI LabVIEW environment and then deploy the code on LabVIEW Real-Time or LabVIEW FPGA-based target hardware.NI SoftMotion includes functions for trajectory generator and spline engine and examples with complete source code for supervisory control, position, and velocity control loop using the PID algorithm. Supervisory control and the trajectory generator run on a LabVIEW Real-Time target and run at millisecond loop rates. The spline engine and the control loop can run either on a LabVIEW Real-Time target at millisecond loop rates or on a LabVIEW FPGA target at microsecond loop rates.ApplicationsBecause the LabVIEW FPGA Module can configure low-level hardware design of FPGAs and use the FPGAs within in a modular system, it is ideal for industrial controlapplications requiring custom hardware. These custom applications can include a custom mix of analog, digital, and counter/timer I/O, analog control up to 125 kHz, digital control up to 20 MHz, and interfacing to custom digital protocols for the following:•Batch control•Discrete control•Motion control•In-vehicle data acquisition•Machine condition monitoring•Rapid control prototyping (RCP)•Industrial control and acquisition•Distributed data acquisition and control•Mobile/portable noise, vibration, and harshness (NVH) analysis ConclusionThe LabVIEW FPGA Module brings the flexibility, performance, and customization of FPGAs to PAC platforms. Using NI RIO devices and LabVIEW graphical programming, you can build flexible and custom hardware using the COTS hardware often required in industrial control applications. Because you are using LabVIEW, a programming language already used in many industrial control applications, to define your NI RIO hardware, there is no need to learn VHDL or other low-level hardware design tools to create custom hardware. Using the LabVIEW FPGA Module and NI RIO hardware as part of your NI PAC adds significant flexibility and functionality for applications requiring ultrahigh-speed control, interfaces to custom digital protocols, or a custom I/O mix of analog, digital, and counters.使用LabVIEW FPGA(现场可编程门阵列)模块开发可编程自动化控制器综述工业控制上的应用要求高度集成的模拟和数字输入输出、浮点运算和多重处理节点的无缝连接。
fpga毕业论文

fpga毕业论文FPGA技术在计算机和电子领域中得到越来越广泛的应用。
本文主要介绍了FPGA在数字信号处理中的应用。
文章首先介绍了FPGA的基本原理和结构,然后详细阐述了FPGA在数字信号处理中的应用,包括数字滤波器、均衡器、FFT等。
最后,文章对FPGA在数字信号处理中的应用进行了总结和展望。
一、FPGA概述FPGA(Field Programmable Gate Array)是一种可编程逻辑器件,其硬件结构由可编程逻辑单元(LUT)、寄存器和互连资源组成,可以进行不同电路结构的编程和再编程。
FPGA 拥有很多优点,例如高度的可定制性、可重构性、高速性、大规模集成度、低功耗和低成本等,因此在数字电子、通信、图像处理、网络交换机、音视频处理、科学计算等领域中得到广泛应用。
二、FPGA在数字信号处理中的应用数字信号处理(Digital Signal Processing,DSP)是数字电子学的一个重要领域,用于处理数字信号。
FPGA在数字信号处理中的应用包括数字滤波器、均衡器、FFT、数字信号合成器、数字调制解调等,下面分别进行详细介绍。
(一)数字滤波器数字滤波器是一种数字信号处理器件,用于对数字信号进行滤波处理,滤除或增强特定频率的信号。
数字滤波器可以基于FPGA硬件平台进行设计和实现。
常见的数字滤波器包括低通滤波器、高通滤波器、带通滤波器和带阻滤波器等。
FPGA 实现数字滤波器具有高速处理、低延迟、低功耗、高精度和灵活性等优点。
(二)均衡器均衡器是用于抵消信号失真的一种电路装置,主要用于数字通信和音频处理。
FPGA可以实现各种类型的均衡器,如时域均衡器、频域均衡器、自适应均衡器等。
这些均衡器主要用于信道均衡、接收机均衡和发射机预失真等领域,能够提高系统的信号质量和稳定性。
(三)FFTFFT(Fast Fourier Transform,快速傅里叶变换)是一种数字信号处理算法,用于将时间域信号转换为频域信号。
基于FPGA的全数字锁相环设计(毕业设计)
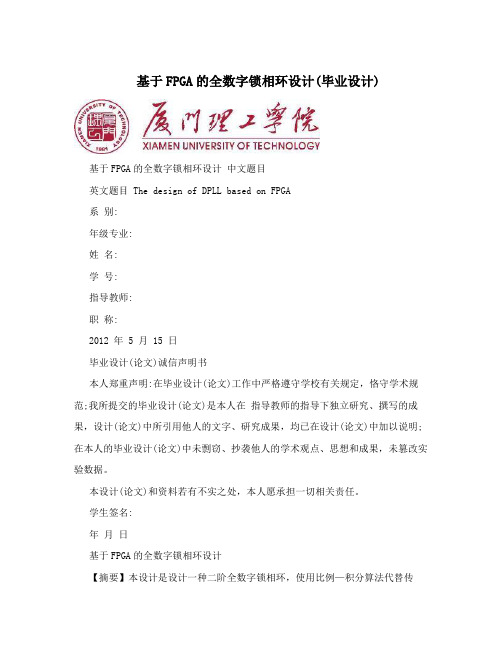
基于FPGA的全数字锁相环设计(毕业设计)基于FPGA的全数字锁相环设计中文题目英文题目 The design of DPLL based on FPGA系别:年级专业:姓名:学号:指导教师:职称:2012 年 5 月 15 日毕业设计(论文)诚信声明书本人郑重声明:在毕业设计(论文)工作中严格遵守学校有关规定,恪守学术规范;我所提交的毕业设计(论文)是本人在指导教师的指导下独立研究、撰写的成果,设计(论文)中所引用他人的文字、研究成果,均已在设计(论文)中加以说明;在本人的毕业设计(论文)中未剽窃、抄袭他人的学术观点、思想和成果,未篡改实验数据。
本设计(论文)和资料若有不实之处,本人愿承担一切相关责任。
学生签名:年月日基于FPGA的全数字锁相环设计【摘要】本设计是设计一种二阶全数字锁相环,使用比例—积分算法代替传统锁相环路系统中的环路滤波,并使用相位累加器实现数控振荡器的功能。
在实际工程中所应用的锁相环无论其功能和结构有何差别,其基本结构应该都由三个基本部件(鉴相器、环路滤波器和压/数控振荡器)构成。
本设计的主要任务就是沿用此基本结构,在具体实现上采用了全新的控制和实现方法来设计这三大模块。
该锁相环由FPGA实现,采用Quartua II和Modelsim SE作为软件开发环境,其灵活性、速度优化和资源控制都能够更好的体现。
设计调试好此系统后,需进行后期的锁相环数据分析,记录分析的数据主要包括:分析锁相环系统的稳定性;分析系统的跟踪误差;通过调节比例和积分系数以调节系统稳定性和锁相速度,做好分析图表。
【关键词】全数字锁相环(ADPLL),比例积分,FPGA ,环路滤波The design of DPLL based on FPGAAbstract:The design is to design a second-order digital phase locked loop, using theproportional - integral algorithm instead of the traditional PLL loop filter and digitally controlled oscillator function of the phase accumulator. In practical engineering application of phase-locked loop, regardless of theirfunction and structure of the difference between the basic structure should consistsof three basic components(phase detector, loop filter and voltage / numerically controlled oscillator) .The main task of this design is to adopt the basicstructure of the concrete realization of a new control and methods to design these three modules.The phase-locked loop implemented by the FPGA, used Quartua II and Modelsim SE as a software development environment,its flexibility, speed optimization and control of resources to better reflect. Design and debug this system, the need for late phase-locked loop data analysis .Recording and analyzing data including :Analysis of phase-locked loopsystem stability; analysis of the tracking error; to adjust the system stability and phase-locked speed by adjusting the proportionaland integral coefficients, good analysis chart.Key Words:ADPLL,Proportional integral,FPGA,Loop filter.目录第一章绪论 ..................................................................... ...................................... 7 1.1 课题背景及意义 ..................................................................... .................. 7 1.2 国内外相关研究状况 ..................................................................... ........... 8 1.3 FPGA技术与Verilog HDL语言简介.. (8)第二章软件方案选择论证.................................................................................... 9 2.1 鉴相器(DPD)程序设计实现方案 (10)2.2 环路滤波器(DLF)的程序设计的实现方案 (10)2.3 数字振荡器(DCO)的程序设计的实现方案 (11)2.4 FPGA程序设计实现方案 ..................................................................... ... 11 2.5 软件设计系统时钟的选择 ..................................................................... .. 11第三章锁相环系统介绍 ..................................................................... ................ 12 3.1 锁相环系统的分类及性质 ......................................................................123.1.1 模拟锁相环 ..................................................................... .. (12)3.1.2 数字锁相环 ..................................................................... .. (12)3.2 锁相环的性质 ..................................................................... .. (13)3.2.1 带宽 ..................................................................... .. (13)3.2.2 线性 ..................................................................... .......................... 13 3.3 锁相环的工作原理与结构 ......................................................................133.3.1 鉴相器(PD).................................................................... .. (14).................................................................... ... 15 3.3.2 环路滤波器(LF)3.3.3 压控振荡器(DCO) .................................................................. .. 153.3.4 环路相位模型 ..................................................................... .. (16)3.3.5 环路的动态方程 ..................................................................... . (17)第四章锁相环系统的软件设计及仿真 .............................................................. 18 4.1 系统软件设计要求 ..................................................................... ........... 18 4.2 数字鉴相器(DPD)的软件设计及仿真 (18)4.3 数字环路滤波器(DLF)的软件设计与仿真 (20)4.4 数控振荡器(DCO)的软件设计与仿真 (21)4.5 锁相环系统软件设计中遇到的问题及解决方法 (24)第五章锁相环系统的硬件环境及调试 (25)5.1 锁相环系统的硬件环境:Altera DE2开发板的介绍 (25)5.2 锁相环系统的载入DE2开发析调试 (25)5.3 锁相环系统硬件调试所遇到的问题及解决方法 (25)第六章锁相环系统相关参数的分析确定及数据的测试分析 (27)6.1 锁相环系统相关参数的分析确定 (27)6.1.1 锁相环系统比例参数PG、积分参数IG的确定 (27)6.1.2 锁相环系统比例和积分计数限幅参数、控制参数N限幅参数的确定 ................................................................. (27)6.3 数字锁相环系统数据的测试分析 (28)6.3.1 锁相环系统的稳定性分析 (28)6.3.2 锁相环系统跟踪误差的分析 (32)6.3.3 调节比例积分系数来分析系统的稳定性和锁相速度 ..................34总结 ..................................................................... (38)致谢 ..................................................................... (39)参考文献 ..................................................................... . (40)第一章绪论1.1 课题背景及意义锁相环路(PLL)是一个能使输出锁相信号频率跟踪输入被锁信号频率的闭环控制系统。
fpga毕业设计

fpga毕业设计FPGA毕业设计(700字):FPGA(Field-Programmable Gate Array)是一种可现场编程门阵列的集成电路。
它具有高度灵活性和可编程性,能够根据设计的需求自主配置和重构电路结构。
毕业设计是大学生在学术生涯中非常重要的一环,要求学生能够独立完成一个完整的项目。
基于FPGA的毕业设计项目可以提供学生丰富的经验和实践机会。
FPGA毕业设计可以选择在几个方面展开,例如通信、图像处理、数字信号处理等。
在通信方面,可以设计一个基于FPGA的软硬件通信系统,通过FPGA板上的芯片实现无线通信,实现数据传输和接收功能。
在图像处理方面,可以将图像数据传输到FPGA中,并利用FPGA的并行计算能力进行图像滤波、边缘检测等处理,最后将处理后的图像输出。
在数字信号处理方面,可以利用FPGA的高速计算能力进行音频、视频信号的采集和处理,实现数字滤波、频谱分析等功能。
毕业设计不仅仅是一个技术实验,还需要学生进行系统设计和工程管理。
学生需要从需求分析开始,设计系统结构和软硬件接口。
然后需要选择合适的开发工具和编程语言进行开发,以及选择合适的FPGA板进行硬件布局和连接。
学生还需要编写设计文档和用户手册,以及进行测试和优化。
通过毕业设计,学生可以了解到一个完整的项目周期,提高综合分析和解决问题的能力。
除了技术和实践能力的提高,FPGA毕业设计还可以为学生的就业提供一定的帮助。
FPGA技术在通信、图像处理、数字信号处理等领域有广泛的应用,而且市场需求也很大。
通过完成一个FPGA毕业设计项目,学生可以有机会接触到一些企业或研究机构,得到实际项目的经验。
这对于学生在求职过程中是非常有竞争力的。
总之,FPGA毕业设计是学生在大学期间重要的一环。
通过FPGA毕业设计,学生可以提高技术、实践和项目管理能力,为将来的就业和研究奠定良好的基础。
希望每位学生都能够积极参与到毕业设计中,充分发挥自己的才能和潜力。
毕业设计(论文)-基于fpga的电路设置[管理资料]
![毕业设计(论文)-基于fpga的电路设置[管理资料]](https://img.taocdn.com/s3/m/e964cc9527d3240c8547ef07.png)
摘要FPGA(Field-Programmable Gate Array),即现场可编程门阵列,它是在PAL、GAL、CPLD等可编程器件的基础上进一步发展的产物。
它是作为专用集成电路(ASIC)领域中的一种半定制电路而出现的,既解决了定制电路的不足,又克服了原有可编程器件门电路数有限的缺点。
目前以硬件描述语言(Verilog 或VHDL)所完成的电路设计,可以经过简单的综合与布局,快速的烧录至FPGA 上进行测试,是现代IC 设计验证的技术主流。
这些可编辑元件可以被用来实现一些基本的逻辑门电路(比如AND、OR、XOR、NOT)或者更复杂一些的组合功能比如解码器或数学方程式。
在大多数的FPGA里面,这些可编辑的元件里也包含记忆元件例如触发器(Flip-flop)或者其他更加完整的记忆块。
系统设计师可以根据需要通过可编辑的连接把FPGA内部的逻辑块连接起来,一个出厂后的成品FPGA的逻辑块的连接可以按照设计者而改变,所以FPGA可以完成所需要的逻辑功能。
本文设计的实验板目的就是验证所设计的电路的逻辑功能。
实验板以EP1C6Q240C8为主,配以存储器、数据配置、复位、实时时钟、I/O口分配、扩展接口、独立按键及LED、液晶显示、数码管显示、蜂鸣器和电源等功能电路。
而其中的独立按键及LED、液晶显示、数码管显示、蜂鸣器就是验证时的直接展现。
关键字:FPGA,硬件原理图,测验ABSTRACTFPGA(Field-Programmable Gate Array),It is based on the further development of the product of PAL、GAL、CPLD etc.. It is in the field of application-specific integrated circuit (ASIC)for a half customize the circuit, it solves the shortage, and custom circuit overcomes original programmable gate device limited number of faults. Now completed the above circuit design by the Hardware description language, can pass by the simple integrated and layout, rapid replication to test on FPGA, it is the mainstream of modern IC design verification. These can edit component can be used to achieve some basic logic gate(such as AND、OR、XOR、NOT ) or, more complex combination of some functions such as decoder or mathematical equations. In most of the FPGA, these can edit component also includes memory devices such as flip-flop or other more complete memory block. According to the system designer, through the FPGA links can edit the internal logic pieces together. One of the products of the factory, logical block of FPGA can be changed according to the designer, so the FPGA can complete the required logic functions.The purpose of this experimental plate is to verify that the logic function of circuit. The primary device is EP1C6Q240C8 on this experimental plate, use with the circuit of memory, Data configuration, reset, real-time clock, I/O port, expand interface, independent buttons and LED, LCD display, digital display, buzzers and power etc.. And that the independent buttons and LED, LCD display, digital display show directly of the checkoutKey Words: FPGA, Hardware diagram, quiz目录第1章绪论 (1)设计背景 (1)设计目的和意义 (2)论文的结构安排 (2)第2章 FPGA开发板原理图分析 (3)FPGA电路 (4)存储电路 (6)Flash存储器 (6)SRSM存储器 (7)SDRAM存储器 (8)配置电路 (9)复位电路 (11)时钟电路 (12)FPGA I/O口分配电路 (13)扩展接口电路 (13)外扩I/O口PACK2 (18)外设PACK接口电路 (18)FPGA扩展接口电路 (19)验证功能电路 (17)按键及LED电路 (17)蜂鸣器电路 (18)七段数码管显示电路 (18)液晶显示电路 (19)实时时钟电路 (19)电源电路 (24)系统电源电路 (24)FPGA电源电路 (25)第3章实验板的测验 (28)读取按键信号 (28)第4章结论 (27)参考文献 (28)致谢 (29)第1章绪论设计背景半导体技术一直遵循著名的摩尔定律持续地发展,回顾半导体的发展历史,当一种技术具有可编程特性时,它就会处于支配的地位。
- 1、下载文档前请自行甄别文档内容的完整性,平台不提供额外的编辑、内容补充、找答案等附加服务。
- 2、"仅部分预览"的文档,不可在线预览部分如存在完整性等问题,可反馈申请退款(可完整预览的文档不适用该条件!)。
- 3、如文档侵犯您的权益,请联系客服反馈,我们会尽快为您处理(人工客服工作时间:9:00-18:30)。
[1] Using FPGA technology towards the design of an adaptive fault tolerant frameworkErdogan, Sevki (University of Hawaii); Gersting, Judith L.; Shaneyfelt, Ted; Duke, Eugene L. Source: Conference Proceedings - IEEE International Conference on Systems, Man and Cybernetics, v 4, IEEE Systems, Man and Cybernetics Society, Proceedings - 2005 International Conference on Systems, Man and Cybernetics, 2005, p 3823-3827ISSN: 1062-922X CODEN: PICYE3Conference: IEEE Systems, Man and Cybernetics Society, Proceedings - 2005 International Conference on Systems, Man and Cybernetics, Oct 10-12 2005, Waikoloa, HI, United States Sponsor: IEEE Systems, Man and Cybernetics Society Publisher: Institute of Electrical and Electronics Engineers Inc.Abstract: In this paper we propose architecture for a Reconfigurable, Adaptive, Fault-Tolerant (RAFT) framework for application in real time systems with require multiple levels of redundancy and protection. Typical application environments include distributed processing, fault-tolerant computation, and mission and safety-critical systems. The framework uses Field Programmable Gate Array (FPGA) technologies with on the fly partial programmability achieving reconfiguration of a system component when the existing components fail or to provide extra reliability as required in the specification. The framework proposes the use an array of FPGA devices to implement a system that, after detecting an error caused by a fault, can adaptively reconfigure itself to achieve fault tolerance. The FPGAs that are becoming widely available at a low cost are exploited by defining a system model that allows the system user to define various levels of reliability choices, providing a monitoring layer for the system engineer. ? 2005 IEEE. (21 refs.)[2]METHOD FOR PROTECTING COMPUTER THROUGH REAL-TIME MONITORING BY PROTECTING EXECUTION FILE, AND COMPUTER AND SYSTEM PROTECTED BY THE SAMEPatent number: KR20040083409Publication date: 2004-10-01Inventor: AHN MU GYEONGApplicant: SAFEI CO LTDClassification:- international: G06F11/30; G06F11/30; (IPC1-7): G06F11/30- european:Application number: KR20040072633 20040910Priority number(s): KR20040072633 20040910View INPADOC patent familyView forward citationsReport a data error hereAbstract of KR20040083409PURPOSE: A method for protecting a computer through real-time monitoring, and the computer and a system protected by the same are provided to safely protect the computer by monitoring an interrupt or an event related to file handling and enable a user to perform setting conveniently. CONSTITUTION: A setting list(50) stores permission for changing an executable file. A detecting module(10) detects/intercepts occurrence of the interrupt or the event related to the file handling. An analysis module(20) checks the permission by comparing the interrupt or the event detected from the detecting module with the setting list after checking that the interrupt or the event is a request for changing the executable file by analyzing the interrupt or the event. A processing module(30) disuses or returns the interrupt or the event depending on an analysis result of the analysis module.[3] Method and system for protecting computer system from malicious software operationPatent number: US2004225877Publication date: 2004-11-11Inventor: HUANG ZEZHEN (US)Applicant:Classification:- International: G06F1/00; G06F11/30; G06F1/00; G06F11/30; (IPC1-7): G06F11/30 - European:Application number: US20040792506 20040303Priority number(s): US20040792506 20040303; US20030469113P 20030509View INPADOC patent familyView forward citationsAlso published as:CN1550950 (A)Report a data error hereAbstract of US2004225877A method and system for protecting a computer system from malicious software operations in real-time is disclosed. The security system combines system and user activity information to derive a user initiation attribute indicating whether or not a system operation is initiated by a computer user, and stop secrete malicious software operations that are not initiated by a computer user. The security system incorporates a plurality of attributes to support flexible security policy design, warn about potentially damaging operations by Trojan programs, and dynamically create security policies to allow trusted programs to perform trusted operations.[4]PREBOOT PROTECTION, IDENTIFICATION AND SECURITY OF A COMPUTER SYSTEMPatent number: WO0233522Publication date: 2002-04-25Inventor: TELLO JOSE ALBERTOApplicant: CODEX TECHNOLOGIES INC (CA)Classification:- international: G06F1/00; G06F21/00; G06F1/00; G06F21/00; (IPC1-7): G06F1/00; G06F9/445- european: G06F21/00N5A2D; G06F21/00N1C; G06F21/00N1V; G06F21/00N3P2 Application number: WO2000IB01659 20001017Priority number(s): WO2000IB01659 20001017; US199******** 19990104View INPADOC patent familyView forward citationsAlso published as:US6463537 (B1)Cited documents:WO0048063US5835597WO9613002US5610981WO9839701Report a data error hereAbstract of WO0233522A "personalized" computer with a unique digital signature which will not boot up or recognize any data storage or communication peripheral devices without a matching "personalized" smart card containing a complementary encrypted digital signature. A modified BIOS (Basic Input Output System) replaces the standard BIOS of a motherboard and allows a security engine microprocessor to take over preboot control of the computer from the motherboard CPU (Central Procesisng Unit), configures and operates the encryption-based security system, and enables or disables selected data storage devices and other user selectable peripherals upon start up and shut down of the computer. The enabling or disabling of peripheral devices involves the use of special enabling/disabling circuits. A modified DDL (Device Driver Layer), loaded in the hard drive of the computer as part of the resident O/S (Operating System) of the computer, and memory buffer circuits allows a real time encryption system to be in place for any communication or data storage device. A data encryption engine in the security engine microprocessor allows encryption and decryption of all data stored indata storage devices. Upon power up, reset or interrupt of the computer, the microprocessor looks for, and if present, reads from the smart card in the smart card reader which is logically connected to the security engine microprocessor. This invention can also be used to allow identification and authentication of the computer and its user in networks.[5]Temporarily authorizing the use of a computer programme protected by an electronic cartridgePatent number: GB2302968Publication date: 1997-02-05Inventor: ANTONINI PIERREApplicant: ANTONINI PIERRE (FR)Classification:- international: G06F21/00; G06F21/00; (IPC1-7): G06F1/00- european: G06F21/00N7P5HApplication number: GB199******** 19960701Priority number(s): FR199******** 19950705View INPADOC patent familyView forward citationsAlso published as:US5898778 (A1)FR2736448 (A1)DE19626972 (A1)Report a data error hereAbstract of GB2302968Use of a programme protected by an electronic cartridge in a computer system is authorised for a period limited by a number of hours or a date. So as to extend the use of a protected programme contained in the memory (103) of the computer system (100-106), the user needs to enter by means of the keyboard (105) into this system a password so as to reset the electronic cartridge (107). This electronic cartridge (107) preferably comprises a memory (108), a first counter (110), a second counter (112), a monostable element (113), an adder (114), a real time clock (109) and a cabled logic network (111). This device is connected to the outside of the computer system (100-106) by means of a connector. For renting software, this invention is able to control the use of these programmes.[6] System for computer software protectionPatent number: US5666411Publication date: 1997-09-09Inventor: MCCARTY JOHNNIE C (US)Applicant:Classification:- international: G06F1/00; G06F9/38; G06F21/00; G06F1/00; G06F9/38; G06F21/00; (IPC1-7): H04L9/00- european: G06F21/00N7P5H; G06F9/38S4L; G06F21/00N1C1Application number: US199******** 19940113Priority number(s): US199******** 19940113View INPADOC patent familyView forward citationsReport a data error hereAbstract of US5666411This system protects proprietary software from disclosure and unauthorized use, enforces license limits on number of users of the software, and prevents corruption of protected software by computer viruses. Software protected under this system may execute only on computer systems which incorporate a microprocessor capable of deciphering enciphered instructions in real time. Program files are first enciphered under control of a distribution cipher key. Prior to first use of software, program files must be customized on the user computer system. This customization procedure re-enciphers the programs, so that they are enciphered under a second cipher key. Customized programs may not execute on a computer system other than one constructed with a processor chip which incorporates a crypto microprocessor. The crypto microprocessor is capable of performing this re-encipherment, and of executing both enciphered and unenciphered programs. The customization program runs on user's computer system and normally accesses a remote Exchange database system by means of a modem to accomplish its task. Variations of customization process provide for storage of enciphered software on either a single system, a network server, or a site license repository system.[7]METHOD AND DEVICE FOR PROTECTION OF COMPUTER SYSTEM FROM ILLEGAL DISTRIBUTIONPatent number: BG48653Publication date: 1991-04-15Inventor: KOLEV VLADIMIR N (BG); MARDIROSJAN GARO KH (BG) Applicant: TS LAB KOSM IZSLEDV ANIJAClassification:- international: G06F5/00; G06F5/00; (IPC1-7): G06F5/00- european:Application number: BG198******** 19890712Priority number(s): BG198******** 19890712View INPADOC patent familyView forward citationsReport a data error hereAbstract of BG48653The invention is designed for the production and use of computer systems and their software. It provides complete protection against undesirable unauthorised copying and reproduction. The method of current real time of the computer system serves to establish a protection code combination for the software product currently used by it. The unit consists of a power supply unit (1), a quartz crystal standart (2), a real time register (3), a real time coder (4), a protection code register (5) and an interface package (6)[8]DEVICE FOR PROTECTING INFORMATION BY USING USB SECURITY MODULE ON BASIS OF PC AND CODE CHIPPatent number: KR20010048160Publication date: 2001-06-15Inventor: CHO JIN HO (KR); CHOI KWANG YUN (KR); HAN SEUNG JO (KR) Applicant: CHO JIN HO (KR); CHOI KWANG YUN (KR); HAN SEUNG JO (KR); SOFTPROTEC CO LTD (KR)Classification:- international: H04L9/00; H04L9/00; (IPC1-7): H04L9/00- european:Application number: KR199******** 19991125Priority number(s): KR199******** 19991125View INPADOC patent familyView forward citationsReport a data error hereAbstract of KR2001004816PURPOSE: A device for protecting information by using a USB security module on basis of a PC and a code chip is provided to prevent illegal copy and modification of the software or data by the illegal users on the basis of the PC and to protect the important data and information. CONSTITUTION: The device for protecting information by using a USB(Universal Serial Bus) security module on basis of a PC and a code chip includes a USB controller(10) and a code chip(100). The USB controller(10) is composed of a USB core(11) and an MCU(12). The serial data by the outer input by using the USB port are sent in the USB core(11) and are in/output serially after buffering. If all the input data are the module information request order languages, the module information is read from a PROM(103) of the code chip(100) and is output to the input step of the USB core(11) or the 17 bites are output to the input step of a buffer(101) in the code chip(100) or the 16 bites input from thebuffer(101) are input and output to the input step of the USB core(11) in the MCU(12). The code chip(100) is composed of the buffer(101), a KSE96 block(110), a controlling portion(130), a mode checker(102), a scrambler, the PROM(103) and an RSA calculating portion(140).[9] Security method for protecting a system, e.g. a computer or online system against unauthorized access, whereby a computer is used with a chip card reader, with an additional varying control question used for access authenticationPatent number: DE10218945Publication date: 2003-11-13Inventor: SCHWENK JOERG (DE); SAAR EV A (DE)Applicant: DEUTSCHE TELEKOM AG (DE)Classification:- international: G06F21/00; G07F7/10; G06F21/00; G07F7/10; (IPC1-7): G06F17/60 - european: G06F21/00N5A2D; G07F7/10D6K; G07F7/10D6PApplication number: DE20021018945 20020422Priority number(s): DE20021018945 20020422View INPADOC patent familyView forward citationsReport a data error hereAbstract of DE10218945Method for securing a system against unauthorized access, whereby an input device is used to input a value that is compared with a stored input code in order to provide access to a system. Following input of the code, e.g. a PIN, a further control question is asked via a system output unit, e.g. the monitor. The question includes information for providing the answer and the user must input the correct answer before access is granted. The invention also relates to a system for implementing the method that comprises a computer with a chip card reader. The information displayed in the additional control question changes each time an identification chip card is inserted in the reader.[10]Computer chip heat protection apparatusPatent number: US6496118Publication date: 2002-12-17Inventor: SMITH WARREN L (US)Applicant:Classification:- international: H01L23/34; H01L23/467; H01L23/34; (IPC1-7): G08B17/00- european: H01L23/34; H01L23/467Application number: US20010953001 20010911Priority number(s): US20010953001 20010911View INPADOC patent familyView forward citationsReport a data error hereAbstract of US6496118A heat protection apparatus includes a heat sink adapted for mounting to a computer chip for dissipating heat generated thereby, the heat sink having a base defining a channel peripherally thereabout. A cooling fan is mounted to the heat sink for dispersing the dissipated heat. The apparatus includes a logic circuit capable of evaluating resistance input data and capable of energizing an alarm upon a programmed condition. The apparatus includes a temperature sensitive polymeric tape spanning between a pair of conductors connected to the circuit. The conductors and polymeric tape are mounted in the channel. The circuit energizes the alarm if the resistance data indicates a temperature greater than a predetermined critical temperature parameter or if the data indicates a temperature rate of rise greater than a critical rate of rise parameter. The alarm may be audible or provide a visual indicator to a computer display.[11] Protection device for portable computersPatent number: US2005039502Publication date: 2005-02-24Inventor: A VGANIM MAIR (IL)Applicant:Classification:- international: G06F1/00; G06F21/00; G06F1/00; G06F21/00; (IPC1-7): E05B73/00 - european: G06F21/00N5A2D; G06F21/00N1Z; G06F21/00N5A2BApplication number: US20040497635 20040602Priority number(s): IL20010146897 20011204; WO2002IL00965 20021202View INPADOC patent familyView forward citationsAlso published as:WO03048907 (A3)WO03048907 (A2)AU2002365735 (A1)Report a data error hereAbstract of US2005039502A protection device (16) particularly for portable computers (10) having a Universal Serial Bus (USB) socket (12) and a standardized dedicated slot (14) formed in vicinityof the socket (12). A key or the like operable mechanism (18) is provided for rotatinga T-shaped tip member (20) which is adapted to be inserted into and locked by the slot(14). Plug (22) may be either a "demo" or part of an active device, which functions to enable/disable the operation of the computer. The device (16) may further be provided with arresting means in the form of a cable (24), which can be tied to an immovable object such as table leg (26) for protecting the computer (10) against theft.[12] Electronic system and corresponding method for protecting an access gate of a computerPatent number: EP1429226Publication date: 2004-06-16Inventor: NICCOLINI MARCELLO (IT)Applicant: INFOTRONIC SPA (IT)Classification:- international: G06F21/00; G06F21/00; (IPC1-7): G06F1/00- european: G06F21/00N1V3Application number: EP20020425770 20021213Priority number(s): EP20020425770 20021213View INPADOC patent familyView forward citationsView document in the European RegisterCited documents:EP1248179WO9743716US6009527Report a data error hereAbstract of EP1429226The invention relates to a system and a method for protected access to an input/output gate (2) of an electronic processor equipped with conventional microprocessor units, volatile and mass memory units, at least one display unit, and an operating system (4) arranged to handle the several processor units, said access gate (2) being a USB gate allowing connenction at fast receptacle to predetermined peripheral units (3) of the electronic processor that are entitled to accede to be plugged in. The method comprises the following steps: detecting, through the operating system (4), the type of any unit coupled to said USB gate (2); comparing the detected type with a stored list of the predetermined units (3) entitled to accede; disabling the USB gate (2) if the comparison gives negative result.[13]APPARATUS FOR PROTECTING COMPUTER USING FUNCTIONAL CHARACTERPatent number: WO03072451Publication date: 2003-09-04Inventor: LEE IN JA (KR)Applicant: LEE IN JA (KR)Classification:- international: B65D41/26; B65D51/24; B65D81/36; B65D41/02; B65D51/24; B65D81/00; (IPC1-7): B65D41/26- european: B65D41/26; B65D51/24L; B65D81/36D2Application number: WO2002KR00432 20020313Priority number(s): KR20020005975U 20020228View INPADOC patent familyView forward citationsAlso published as:AU2002239122 (A1)Cited documents:KR890016287UKR880016247UReport a data error hereAbstract of WO03072451The present invention relates to a apparatus for protecting computer for notifying the outside of each of operation state of virus inspection using the character apparatus connected to the computer. The present invention includes computer for generating and transmitting the USB code value corresponding to registry value inspected from each of operation state of vaccine engine, and character apparatus for inquiring and outputting the voice data corresponding to the USB code value received from the computer. Hence, the present invention has an effect on not only hearing the information to virus inspection through the voice irrespective of the time as it always surveys the vaccine engine, but also presenting a fine view around the computer and increasing the effective value of the character by forming the character apparatus as the character including a doll.[14] Multiple protecting system to protect personal computer data from burglary utilized flash memory drivePatent number: US2003079140Publication date: 2003-04-24Inventor: URA YOSUKE (JP)Applicant:Classification:- international: G06F21/00; G06F21/00; (IPC1-7): H04L9/00- european: G06F21/00N1D1; G06F21/00N1V3Application number: US20010002501 20011024Priority number(s): US20010002501 20011024View INPADOC patent familyView forward citationsReport a data error hereAbstract of US2003079140This invention provides the system to protect the data stored in personal computer from burglary. This invention features providing method to protect the data stored in personal computer from easy burglary by combining several types of protecting method in the system that data is input and output inserting flash memory drive into USB port on personal computer.[15]Secure general purpose input/output pins for protecting computer system resourcesPatent number: US6138240Publication date: 2000-10-24Inventor: TRAN ROBIN T (US); SIMONICH CHRISTOPHER E (US) Applicant: COMPAQ COMPUTER CORP (US)Classification:- international: G06F21/00; G06F21/00; (IPC1-7): G06F11/00- european: G06F21/00N1VApplication number: US199******** 19980619Priority number(s): US199******** 19980619View INPADOC patent familyView forward citationsReport a data error hereAbstract of US6138240A security device and methodology that prevents unauthorized access to general purpose I/O pins in a computer system. In a system according to the invention, secure general purpose I/O pins are utilized as enable signals for data transfer devices such as Universal Serial Port (USB) ports. In one embodiment of the invention, access to the secure general purpose I/O pins is governed by an administrator password that is protected by a memory slot in a security device. When an administrator (or other authorized user) desires access to the general purpose I/O register that controls the secure general purpose I/O pins, the administrator enters the administrator password. If the password is correct, the relevant slot of the security device is unlocked, thereby permitting completion of write cycles to the secure general purpose I/O register. If a write cycle to the secure general purpose I/O register is attempted while the relevantslot in the security device is locked, the write cycle is ignored. Control and monitoring of various system resources in a secure manner is thereby permitted via use of the secure general purpose I/O pins.[16] SECRECY-PROTECTING COMPUTER AND PROGRAMPatent number: JP2006338136Publication date: 2006-12-14Inventor: KANEUCHI HIDEApplicant: MITSUBISHI ELECTRIC INF TECHClassification:- international: G06F21/24; H04L9/32; G06F21/00; H04L9/32;- european:Application number: JP20050159474 20050531Priority number(s): JP20050159474 20050531View INPADOC patent familyView forward citationsReport a data error hereAbstract of JP2006338136PROBLEM TO BE SOLVED: To provide a secrecy-protecting computer which prevents a file from being operated in a computer except the computer from which the file is taken away.SOLUTION: When a file is closed by a filter driver provided between an I/O manager and a device driver, plain-sentence data 100 to be stored are encrypted, and the file is stored in a form of mixed data 130 which include the encrypted data and a MAC address 120 unique to the computer. When the file is opened, the encrypted data included in the mixed data are decrypted only when the MAC address included in the mixed data 130 accords with a MAC address 130 unique to the computer which opens the file.[17] ACCESS PROTECTION FOR A COMPUTER BY MEANS OF A PORTABLE STORAGE MEDIUMPatent number: WO2006074490Publication date: 2006-07-13Inventor: FUCHS HJALMAR DOUGLAS (ZA)Applicant: FUCHS HJALMAR DOUGLAS (ZA)Classification:- international: G06F21/20; G06F21/20;- european:Application number: WO2005ZA00176 20051130Priority number(s): ZA20040009657 20041130View INPADOC patent familyView forward citationsCited documents:WO03079163US6401205DE19508288NL9101506FR2783943Report a data error hereAbstract of WO2006074490This Invention relates to a memory device such as a memory stick with a unique identifier or ID to be used in conduction with an electronic device such as a Personal Computer as to enable a user to gain access or operate or control devices or services associated with the electronic device for example a PC or Laptop. The systems software running or operational on the electronic device and/or memory device will search and read a unique identifier on the memory device such as a serial number or code. Should the serial number or code not be Read operation of the electronic device is seized.[18]METHOD AND SYSTEM FOR PROTECTING AGAINST COMPUTER VIRUSESPatent number: WO2005008417Publication date: 2005-01-27Inventor: KWAN TONY (AU)Applicant: COMPUTER ASS THINK INC (US); KWAN TONY (AU) Classification:- international: G06F21/00; G06F21/00; (IPC1-7): G06F- european: G06F21/00N3P; G06F21/00N3V6; H04L29/06C6HApplication number: WO2004US22216 20040709Priority number(s): US20030486754P 20030711View INPADOC patent familyView forward citationsView document in the European RegisterAlso published as:WO2005008417 (A3)EP1644859 (A3)EP1644859 (A2)EP1644859 (A0)Cited documents:US5956408US6049671US2003084322US5948104US2003065926more >>Report a data error hereAbstract of WO2005008417A method for delivering an update to at least one user including creating an electronic communication including an update and a unique signature identifying, the electronic communication as including the update and sending the electronic communication to the user..[19] Systems, methods, and computer program products for privacy protection Patent number: US2003130893Publication date: 2003-07-10Inventor: FARMER BENNIE L (US)Applicant: TELANON INC (US)Classification:- international: (IPC1-7): G06F17/60- european: G06F21/00N9A2P1Application number: US20020291196 20021108Priority number(s): US20020291196 20021108; US20000638177 20000811; US20010337827P 20011108View INPADOC patent familyView forward citationsReport a data error hereAbstract of US2003130893A systems and method of transmitting or communicating unique data from a unique user through a communications and/or computer network to a third party, wherein the third party has no method of determining the personal-identifying information (PII) of the unique user upon receiving the data. The invention provides privacy protection and location for communication of data, voice orOther information via a communications network, for providing various services related to telemetric communications and other location-based services.[20]Method and apparatus for establishing computer configuration protection passwords for protecting computer configurationsPatent number: US6470454Publication date: 2002-10-22Inventor: CHALLENER DA VID CARROLL (US); ATKINS BARRY DOUGLAS (US); ARNOLD TODD W (US)Applicant: IBM (US)Classification:- international: G06F21/00; G06F21/00; (IPC1-7): G06F11/30; H04L9/00; H04L12/14- european: G06F21/00N5A2Application number: US199******** 19980331Priority number(s): US199******** 19980331View INPADOC patent familyView forward citationsReport a data error hereAbstract of US6470454A method and apparatus is provided for facilitating the generation and use of computer system configuration passwords which can be utilized in an enterprise or organization to allow authorized users having knowledge of the password associated with a particular data processing system to make and change configuration decisions, but which prevents unauthorized users from making and changing such configuration decisions. In the preferred embodiment, a unique identifier (such as a serial number) and an enterprise secret key are supplied to a one-way cryptographic hash function in order to generate the configuration passwords which are unique to each data processing system of the plurality of data processing system of the enterprise or organization.。