铝合金阳极处理
铝合金经硬质阳极氧化处理

六、 导线若干;
步骤如下——————
需要阳极的零件先要彻底除油(包括指纹、手汗、脏东西等等)例如用微温的洗衣粉88%的自来水,然后再一面用玻璃棒搅拌一面缓慢的加入体积为12%的浓硫酸,
!希望多提宝贵意见!!
针对专业人士的需求,作如下回复:
送电伊始,电流密度为0.5A/dm2,在25分钟内分5~8次逐渐把电流密度提高到2.5 A/dm2,最终电流密度依零件尺寸、表面积、材料具体成份、达到要求而定,一般在1~5 A/dm2为佳
最后用温热机器润滑油全部擦拭表面,使其封闭钝化,此法可保持永久的色泽不变。;
其实所谓阳极就是使铝件接通正极(阳极),通过酸性溶液的导电作用,使其表面产生一系列的反应,增加表面硬度、耐腐蚀度。并且改造表面物理结构,使其容易吸附染料。
以上均为本人多次实际操作过的方法,百试百灵!!今后弟兄们的铝质零件表面“毁容啦”就不再需要找喷漆工啦!
2、 电压一般为8~12V最终电压依零件尺寸、表面积、材料具体成份而定。
使用草酸为电解液的产品颜色依铝合金成分和阳极时各种条件有关,可承银白、黄铜色、黄褐色的氧化膜。建议使用12%(V/V)的硫酸溶液,价格低廉、溶液稳定,可得浅银灰、银白色氧化膜,不影响后期染色的成色,就算不染色也有不锈钢的质感!!!!!!
!!!!注意!!!!一定不要先放硫酸再放水,因为浓硫酸与水会产生高热,这样水会炸沸的!!!很危险!!!
溶液的量已能淹没过零件为准。估计需要数小时才会冷却至室温,溶液温度在10摄氏度以下时阳极硬度很高,超过20摄氏度效果不好,切记!!!
把不锈钢板焊上导线,或穿孔用不锈钢丝穿过使其导电,并串联起来。浸没溶液中并处于瓦盆两侧(贴着盆壁)接通直流电源的负极。
铝合金表面处理阳极工艺

工件表面,造成阳极氧化槽液的污染,也造成氧化膜成长不均,疏松, 质量大大下降。同时会影响后面的染色不均,染不上色等等问题。 2.脏污来源分析?
加工类型 加工方式 切削加工 粗磨 机械冷加 工 精磨、研磨、抛光 粘附的污垢 金属屑、粉粒(尘)、润滑冷却液 磨料粉尘、磨屑、润滑冷却液 磨料粉尘、油膏
2染色前处理原理
步骤 1.超音波染色处理 (5min)。 2.水洗(30s)。 3.重复(一阳重复1.2两次, 二阳重复一次)。 4.水洗(30s)。
染色前處理原理圖 表面活性物質
氧化膜層
染色
操作条件 1.温度40±2℃ 2.PH值5.2-5.5 3.染料浓度 BK420∶BK411=1∶1 (g/L) 4.PH稳定剂5ml/L 步骤 1.染色120-360s。 2.水洗30s。 3.检查色差。 4.水洗30s。 5.水洗30s。
铝及其合金在相应的电解液和特定的工艺条件下,由于 外加电流的作用下,在铝制品(阳极)上形成一层氧化膜的 过程.阳极氧化如果没有特别指明,通常是指硫酸阳极 氧化。 通电 1 水电解: H 2O H OH 2.阴极:
H 2e H 2
3.阳极: OH
2e O H
1.作用原理
在磷酸化抛后,会使工件表面残留一层黑
灰色的膜(铜、镍、锰、铁、硅等不溶于 磷酸的金属)之后用硝酸处理: 3A+8HNO3=3A(NO3)2+2NO+4H2O (A代表铜、镍、锰)加入铬酸处理。
Cr2O7 NO 6H 2NO3 3H2O 2Cr 6
若R=17,即为硬脂酸钠(肥皂),硬脂酸钠能溶 于水,是一种表面活性剂,对油脂溶解起促进 作用。 2.乳化作用:矿物油或其他不可皂化油是不能 用碱皂化的,但它们在表面活性剂的作用下能
铝合金阳极氧化处理

铝合金阳极氧化处理引言:铝合金是一种常用的金属材料,在工业生产和日常生活中都有广泛应用。
然而,铝合金表面容易受到氧化的影响,导致腐蚀和降低其使用寿命。
为了增加铝合金的抗腐蚀性和提高其表面硬度,人们常常采用阳极氧化处理的方法。
一、阳极氧化处理的原理和过程阳极氧化处理是利用电解原理,在铝合金表面形成一层氧化膜的过程。
具体来说,将铝合金制品作为阳极,放入含有硫酸等电解液中,通过外加电流使铝合金表面产生氧化反应,从而在表面形成一层氧化膜。
这层氧化膜具有良好的耐腐蚀性和硬度,可以有效保护铝合金。
阳极氧化处理一般包括以下步骤:1. 表面准备:将铝合金表面清洗干净,去除油污和杂质,保证表面光洁。
2. 预处理:将铝合金制品浸泡在酸性溶液中,例如硫酸溶液,进行脱脂和除氧化处理,以消除表面缺陷。
3. 阳极氧化:将铝合金制品作为阳极,放入电解槽中,与阴极(一般为铅)相连。
在电解液中施加直流电流,使铝合金表面发生氧化反应,形成氧化膜。
同时,电解液中的铝离子会与阴极上的氯离子发生反应,生成氯气和铝氧化物。
4. 封闭处理:将铝合金制品放入热水或其他封闭液中进行处理,使氧化膜进一步增强,提高其耐腐蚀性和硬度。
5. 清洗和干燥:将处理后的铝合金制品进行清洗,去除表面的残留物,然后进行干燥,以得到最终的产品。
二、阳极氧化处理的优势阳极氧化处理具有以下几个优势:1. 提高耐腐蚀性:通过阳极氧化处理,铝合金表面形成了一层致密的氧化膜,可以有效阻止氧、水和其他腐蚀性物质的侵蚀,提高铝合金的抗腐蚀性能。
2. 增加硬度:氧化膜具有较高的硬度,可以显著提高铝合金的表面硬度,增加其耐磨性和耐刮擦性。
3. 美观外观:阳极氧化处理可以使铝合金表面形成不同颜色的氧化膜,可以根据需要选择不同颜色的处理,使产品具有良好的外观效果。
4. 增加附着力:氧化膜与铝合金基体之间具有良好的结合力,可以增加其附着力,提高产品的耐用性。
5. 环保可持续:阳极氧化处理过程中不需要添加有害物质,电解液可以回收利用,具有较好的环保性能。
铝合金阳极氧化操作方法

铝合金阳极氧化操作方法
铝合金阳极氧化是一种常见的表面处理方法,可以提高铝合金的耐蚀性和硬度。
操作方法包括以下几个步骤:
1. 准备工件:将需要进行阳极氧化处理的铝合金工件清洗干净,去除油污和杂质。
2. 预处理:对工件进行预处理,包括去除氧化皮、清洗和除油等操作。
确保工件表面干净、平整。
3. 阳极氧化:将清洁的铝合金工件浸入含有酸性电解液的电解槽中,并连接阳极和阴极,通过施加电压使阳极氧化反应发生。
这一步骤会在工件表面形成一层氧化膜。
4. 封孔处理:在完成阳极氧化后,通常需要对工件进行封孔处理,以提高其耐腐蚀性能。
5. 清洗和干燥:将阳极氧化后的工件进行清洗和干燥,确保表面干净和无水渍。
6. 检验和包装:对阳极氧化后的工件进行检验,确保表面质量符合要求,然后进行包装。
需要注意的是,阳极氧化操作需要严格控制处理参数,包括电解液成分、温度、电压和处理时间等,以确保处理效果和工件质量。
另外,处理过程中要注意安全防护和环保要求。
铝合金的阳极化处理

铝合金的阳极化处理铝制品表面的自然氧化铝既软又薄,耐蚀性差,不能成为有效防护层更不适合着色。
人工制氧化膜主要是应用化学氧化和阳极氧化。
化学氧化就是铝制品在弱碱性或弱酸性溶液中,部分基体金属发生反应,使其表面的自然氧化膜增厚或产生其他一些钝化膜的处理过程,常用的化学氧化膜有铬酸膜和磷酸膜,它们既薄吸附性又好,可进行着色和封孔处理,表-1介绍了铝制品化学氧化工艺。
化学氧化膜与阳极氧化膜相比,膜薄得多,抗蚀性和硬度比较低,而且不易着色,着色后的耐光性差,所以金属铝着色与配色仅介绍阳极化处理。
一、阳极氧化处理的一般概念1、阳极氧化膜生成的一般原理以铝或铝合金制品为阳极置于电解质溶液中,利用电解作用,使其表面形成氧化铝薄膜的过程,称为铝及铝合金的阳极氧化处理。
其装置中阴极为在电解溶液中化学稳定性高的材料,如铅、不锈钢、铝等。
铝阳极氧化的原理实质上就是水电解的原理。
当电流通过时,在阴极上,放出氢气;在阳极上,析出的氧不仅是分子态的氧,还包括原子氧(O)和离子氧,通常在反应中以分子氧表示。
作为阳极的铝被其上析出的氧所氧化,形成无水的氧化铝膜,生成的氧并不是全部与铝作用,一部分以气态的形式析出。
2、阳极氧化电解溶液的选择阳极氧化膜生长的一个先决条件是,电解液对氧化膜应有溶解作用。
但这并非说在所有存在溶解作用的电解液中阳极氧化都能生成氧化膜或生成的氧化膜性质相同。
适用于阳极氧化处理的酸性电解液见表-2。
化。
按电解液分有:硫酸、草酸、铬酸、混合酸和以磺基有机酸为主溶液的自然着色阳极氧化。
按膜层性子分有:普通膜、硬质膜(厚膜)、瓷质膜、光亮修饰层、半导体作用的阻挡层等阳极氧化。
铝及铝合金常用阳极氧化方法和工艺条件见表-3。
其中以直流电硫酸阳极氧化法的应用最为普遍。
4、阳极氧化膜结构、性质阳极氧化膜由两层组成,多孔的厚的外层是在具有介电性质的致密的内层上成长起来的,后者称为阻挡层(也称活性层)。
用电子显微镜观察研究,膜层的纵横面几乎全都呈现与金属表面垂直的管状孔,它们贯穿膜外层直至氧化3、阳极氧化的种类阳极氧化按电流形式分为:直流电阳极氧化、交流电阳极氧化、脉冲电流阳极氧膜与金属界面的阻挡层。
铝合金阳极氧化及其表面处理

铝合金阳极氧化及其表面处理铝合金阳极氧化是铝合金材料常用的一种表面处理方法,它主要是通过利用阳极电位差,使氧原子和钙原子氧化成氧化物薄膜形成在铝合金表面,从而提供铝合金表面的耐腐蚀性能和外观美观度,使表面更具有耐磨性和防气孔能力。
当铝合金表面处理需要抗腐蚀、耐磨、抗气孔等性能时,阳极氧化可以满足要求。
铝合金阳极氧化的原理是利用分子氧的氧化还原反应,利用阳极电位差,氧原子和钙原子氧化成薄膜,形成在铝合金表面,起到保护作用。
所形成的氧化膜是稳定的,具有很强的抗腐蚀性和抗气孔性。
同时,铝合金阳极氧化的过程中,可以调整氧化膜厚度,改善表面光洁度和粗糙度,以满足表面性能要求。
铝合金阳极氧化工艺有多种,其中包括化学阳极氧化法、静电阳极氧化法和磁控溅射阳极氧化法等。
化学阳极氧化法是一种常用的阳极氧化处理方法,该方法主要是利用氧化剂和反应物的反应,使反应物在反应过程中形成自身的氧化膜,从而达到改善铝合金表面性能的目的。
但由于此方法操作过程复杂,需要在反应过程中控制反应条件,因此很少有工厂采用这种方法。
静电阳极氧化法是一种常用的处理技术,使用此方法可以在铝合金表面形成厚度比化学阳极氧化法薄的氧化膜,具有较高的耐磨性。
此外,由于反应速率相对较快,因此可以使用更低的温度来达到相同的效果。
磁控溅射阳极氧化法属于活性氧化方法,它是利用高速离子将氧化剂撞击在铝合金表面,氧化剂受到撞击时会被迅速氧化,从而形成一种厚度较薄的氧化膜,膜具有良好的抗冲击性和耐磨性,而且可以在普通条件下实现镀锌层效果,也可以改善表面摩擦性能。
除了铝合金阳极氧化之外,表面处理还可以采用其他技术,如络石抛光、热处理、激光处理、化学镀层和电镀等。
络石抛光,主要是利用磨削作用,在金属表面形成一定厚度的高光洁层,从而使金属表面更加平滑,并具有耐水性、耐酸碱性和耐腐蚀性。
热处理,是在一定温度、时间条件下,将金属表面热处理后,可以改变金属表面的光洁度、粗糙度和耐磨性,提高金属表面的耐腐蚀性和强度。
铝合金阳极处理工艺知识
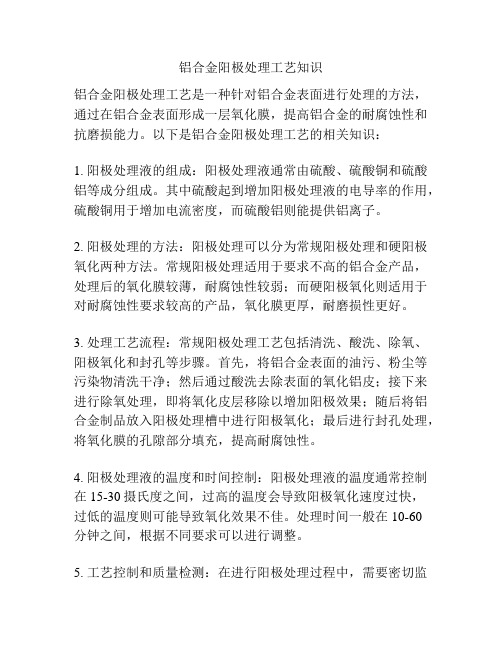
铝合金阳极处理工艺知识铝合金阳极处理工艺是一种针对铝合金表面进行处理的方法,通过在铝合金表面形成一层氧化膜,提高铝合金的耐腐蚀性和抗磨损能力。
以下是铝合金阳极处理工艺的相关知识:1. 阳极处理液的组成:阳极处理液通常由硫酸、硫酸铜和硫酸铝等成分组成。
其中硫酸起到增加阳极处理液的电导率的作用,硫酸铜用于增加电流密度,而硫酸铝则能提供铝离子。
2. 阳极处理的方法:阳极处理可以分为常规阳极处理和硬阳极氧化两种方法。
常规阳极处理适用于要求不高的铝合金产品,处理后的氧化膜较薄,耐腐蚀性较弱;而硬阳极氧化则适用于对耐腐蚀性要求较高的产品,氧化膜更厚,耐磨损性更好。
3. 处理工艺流程:常规阳极处理工艺包括清洗、酸洗、除氧、阳极氧化和封孔等步骤。
首先,将铝合金表面的油污、粉尘等污染物清洗干净;然后通过酸洗去除表面的氧化铝皮;接下来进行除氧处理,即将氧化皮层移除以增加阳极效果;随后将铝合金制品放入阳极处理槽中进行阳极氧化;最后进行封孔处理,将氧化膜的孔隙部分填充,提高耐腐蚀性。
4. 阳极处理液的温度和时间控制:阳极处理液的温度通常控制在15-30摄氏度之间,过高的温度会导致阳极氧化速度过快,过低的温度则可能导致氧化效果不佳。
处理时间一般在10-60分钟之间,根据不同要求可以进行调整。
5. 工艺控制和质量检测:在进行阳极处理过程中,需要密切监控和控制处理槽温度、电流密度等参数,保证处理效果的稳定性。
同时,需要对处理后的铝合金进行质量检测,如测量氧化膜的厚度、硬度和耐腐蚀性等指标。
铝合金阳极处理工艺是一项在铝合金加工中广泛应用的技术,通过对铝合金表面进行处理,能够提高其使用寿命和外观质量。
然而,在实际应用中,不同的合金材料和产品要求可能会有所不同,因此需要根据具体情况进行调整和优化处理工艺,以获得最佳的处理效果。
当进行铝合金阳极处理工艺时,还需要注意以下几个方面:6. 高质量铝合金材料的选择:选择合适的铝合金材料非常重要,因为不同的合金成分和含量会对阳极处理工艺产生影响。
铝合金件的阳极化处理

铝合金件的阳极化处理
铝合金件的阳极化处理是一种常见的表面处理方法,旨在提高铝合金件的耐腐蚀性、硬度和耐磨性。
阳极化处理的原理是在铝合金件表面形成一层氧化膜,该膜具有较高的硬度和耐腐蚀性。
该处理方法通常分为硫酸阳极氧化和硬质阳极氧化两种。
硫酸阳极氧化是一种常见的处理方法,其步骤包括清洗、脱脂、酸洗、阳极化和封孔。
清洗和脱脂的目的是去除铝合金件表面的油污和杂质;酸洗则是将铝合金件表面的氧化层去除,以便进行阳极化处理。
阳极化的过程中,铝合金件作为阳极,在硫酸溶液中通电,形成一层致密的氧化膜。
最后,通过封孔处理,防止氧化膜受到损坏。
硬质阳极氧化相对于硫酸阳极氧化而言,具有更高的硬度和更好的耐磨性。
其步骤与硫酸阳极氧化类似,但在阳极化过程中使用的电解液和电流密度不同。
硬质阳极氧化的电解液通常包括硫酸、氧化铝、磷酸和柠檬酸等,而电流密度则较硫酸阳极氧化更高。
总之,阳极化处理是一种有效的表面处理方法,可以显著提高铝合金件的性能和寿命。
不过,在进行阳极化处理时需要注意处理参数的选择,以确保处理效果的稳定和一致。
- 1 -。
- 1、下载文档前请自行甄别文档内容的完整性,平台不提供额外的编辑、内容补充、找答案等附加服务。
- 2、"仅部分预览"的文档,不可在线预览部分如存在完整性等问题,可反馈申请退款(可完整预览的文档不适用该条件!)。
- 3、如文档侵犯您的权益,请联系客服反馈,我们会尽快为您处理(人工客服工作时间:9:00-18:30)。
Alloy and Temper
Wrought Alloys. The alloy and temper of the product to be anodized will affect both the strength and the appearance of the part after it is anodized. V arious combinations of constituent elements cause each aluminum alloy to react differently to the process of anodizing; this is particularly evident between alloy series. As a result, each alloy or alloy series yields a different appearance, even if treated to identical anodizing processes. Also, each alloy exhibits its unique characteristics such as good formability, ease of machining, strength, response to anodizing, etc. Examples of some of these general characteristics follow:
The 2xxx Series alloys are high in copper, have relatively high strength, are hard, and have good machinability. As copper content increases, anodizing generally becomes more difficult. Anodizing conditions should be closely controlled. The anodic oxide on 2xxx alloys is usually softer and has lower corrosion resistance than on alloys with lower copper content. Special anodizing techniques may be used to obtain acceptable coatings.
The 3xxx Series have relatively high levels of manganese. These alloys are work-hardened (non-heat-treatable) and exhibit excellent formability characteristics. They anodize clear silver, grayish, or brownish depending on the production conditions.
The 4xxx Series alloys are high in silicon and generally are not anodized.
The 5xxx Series alloys are high purity aluminum with magnesium added. Alloys of this series are work-hardened (non-heat-treatable) and have good formability. Alloys 5252, 5457, and 5657 are low in iron and have good luster for chemically brightened finishes. These alloys are used largely in automotive and appliance trim applications. Alloy 5052, while higher in iron, chrome, and magnesium, is a high-strength alloy and is used in structural applications such as truck panels. Alloy 5005 is higher in iron and silicon than 5052. It is a good general-purpose architectural sheet and plate alloy. Alloy 5052 anodizes yellowish in thicker coatings, while 5005 anodizes clear silver, gray, or brownish.
The 6xxx Series offer good, general-purpose, heat-treatable alloys. Alloys of this series have excellent response to anodizing. For example, 6063 and 6463 are popular extrusion alloys having good strength and excellent anodizing characteristics. Principal alloying elements are magnesium and silicon; 6463 is low in iron and is used for bright finishes. Both have good luster and anodize clear silver. Alloy 6061 is higher in silicon, iron, copper, magnesium, and chrome than 6063. It is a high-strength structural alloy having excellent machinability, a favorite of machine shops, especially if the parts are to be hard anodized.
The 7xxx Series alloys are high in zinc. They are considered ultra-high-strength alloys and find wide use in the aircraft and aerospace industries. They anodize gray, blue-gray, and brown-black (mottled), depending on the alloy and the anodizing process.
Casting Alloys. Several aluminum casting alloys also can be anodized. Unfortunately, the characteristics that make good castings are not necessarily the best for anodizing. Alloys with the best casting characteristics are those containing up to 12-percent silicon. High-silicon alloys do not anodize well because silicon is not readily soluble in aluminum. Only the aluminum on the surface of the part anodizes, leaving areas with higher silicon unanodized and the entire part with a black or gray silicon powder.
Aluminum casting alloys containing relatively low amounts of silicon and iron and higher amounts of magnesium, chrome, and zinc tend to anodize well. Aluminum-magnesium alloys such as 514 and 535 anodize well. Aluminum-zinc alloys like 712, 713, and 771 also respond well to anodizing. Some higher silicon casting alloys, such as 356, can be anodized using special techniques and processes. It is best to check with an anodizing expert before specifying casting alloys for projects that call for anodized finishes.。