供应链成本管理的方法论意义【外文翻译】
成本控制外文文献(Costcontrol,foreignliterature)
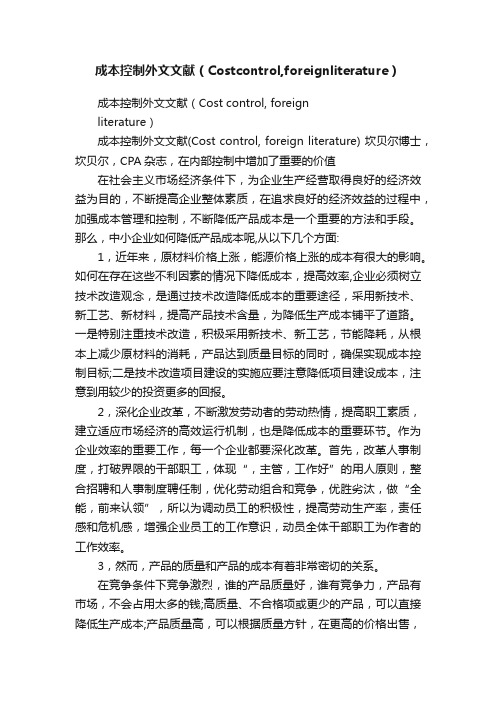
成本控制外文文献(Costcontrol,foreignliterature)成本控制外文文献(Cost control, foreignliterature)成本控制外文文献(Cost control, foreign literature) 坎贝尔博士,坎贝尔,CPA杂志,在内部控制中增加了重要的价值在社会主义市场经济条件下,为企业生产经营取得良好的经济效益为目的,不断提高企业整体素质,在追求良好的经济效益的过程中,加强成本管理和控制,不断降低产品成本是一个重要的方法和手段。
那么,中小企业如何降低产品成本呢,从以下几个方面:1,近年来,原材料价格上涨,能源价格上涨的成本有很大的影响。
如何在存在这些不利因素的情况下降低成本,提高效率,企业必须树立技术改造观念,是通过技术改造降低成本的重要途径,采用新技术、新工艺、新材料,提高产品技术含量,为降低生产成本铺平了道路。
一是特别注重技术改造,积极采用新技术、新工艺,节能降耗,从根本上减少原材料的消耗,产品达到质量目标的同时,确保实现成本控制目标;二是技术改造项目建设的实施应要注意降低项目建设成本,注意到用较少的投资更多的回报。
2,深化企业改革,不断激发劳动者的劳动热情,提高职工素质,建立适应市场经济的高效运行机制,也是降低成本的重要环节。
作为企业效率的重要工作,每一个企业都要深化改革。
首先,改革人事制度,打破界限的干部职工,体现“,主管,工作好”的用人原则,整合招聘和人事制度聘任制,优化劳动组合和竞争,优胜劣汰,做“全能,前来认领”,所以为调动员工的积极性,提高劳动生产率,责任感和危机感,增强企业员工的工作意识,动员全体干部职工为作者的工作效率。
3,然而,产品的质量和产品的成本有着非常密切的关系。
在竞争条件下竞争激烈,谁的产品质量好,谁有竞争力,产品有市场,不会占用太多的钱;高质量、不合格项或更少的产品,可以直接降低生产成本;产品质量高,可以根据质量方针,在更高的价格出售,在销售收入中的比重相对降低成本;高质量的产品,才能赢得更多的客户,增加销售,降低销售成本;产品质量高,实际上也节省了能源和原材料;产品质量高,可节省人工和管理费用,这肯定会降低成本。
供应链成本管理降低支出和提高利润

供应链成本管理降低支出和提高利润在当今竞争激烈的市场环境中,企业要想保持竞争力,就必须不断寻求降低成本、提高利润的方法。
供应链成本管理作为一种重要的管理手段,可以帮助企业降低支出、提高利润,提升整体竞争力。
本文将从供应链成本管理的概念、重要性、方法和实施步骤等方面进行探讨,帮助企业更好地理解和运用供应链成本管理,实现降低支出和提高利润的目标。
一、供应链成本管理的概念供应链成本管理是指企业在供应链中对各个环节的成本进行有效管理和控制,以实现成本最小化、效益最大化的管理活动。
供应链成本管理的范围涵盖了从原材料采购、生产制造、产品配送到售后服务等全过程,旨在通过优化供应链各环节的成本,提高资源利用效率,降低企业运营成本,从而提高企业的竞争力和盈利能力。
二、供应链成本管理的重要性1. 降低成本、提高利润:通过供应链成本管理,企业可以深入分析和优化供应链中的各个环节,找出成本高、效率低的环节,并采取相应的措施进行改进,从而降低企业的运营成本,提高利润水平。
2. 提高供应链效率:供应链成本管理可以帮助企业优化供应链的布局和流程,提高供应链的运作效率和灵活性,缩短交付周期,降低库存水平,提高客户满意度。
3. 优化资源配置:通过供应链成本管理,企业可以更好地协调内外部资源,优化资源配置,降低资源浪费,提高资源利用效率,实现成本最小化和效益最大化。
4. 增强市场竞争力:供应链成本管理可以帮助企业降低产品价格,提高产品质量,缩短交付周期,更好地满足客户需求,从而增强企业在市场上的竞争力,赢得更多市场份额。
三、供应链成本管理的方法1. 成本分析:对供应链中的各个环节进行成本分析,找出成本高、效率低的环节,确定改进的重点和方向。
2. 成本控制:通过制定合理的成本控制措施,对供应链中的成本进行有效管理和控制,确保成本在可控范围内。
3. 流程优化:优化供应链中的流程和环节,简化流程、减少环节,提高运作效率,降低成本。
4. 合作共赢:与供应链中的合作伙伴建立长期稳定的合作关系,共同优化供应链,降低整体成本,实现合作共赢。
成本管理外文文献及翻译
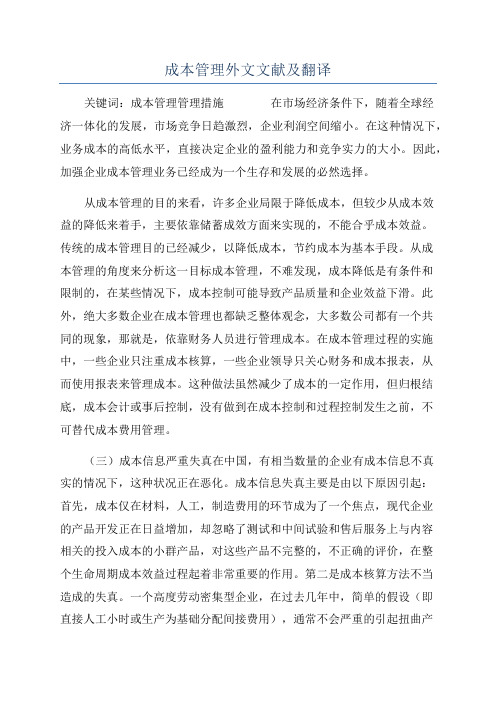
成本管理外文文献及翻译关键词:成本管理管理措施在市场经济条件下,随着全球经济一体化的发展,市场竞争日趋激烈,企业利润空间缩小。
在这种情况下,业务成本的高低水平,直接决定企业的盈利能力和竞争实力的大小。
因此,加强企业成本管理业务已经成为一个生存和发展的必然选择。
从成本管理的目的来看,许多企业局限于降低成本,但较少从成本效益的降低来着手,主要依靠储蓄成效方面来实现的,不能合乎成本效益。
传统的成本管理目的已经减少,以降低成本,节约成本为基本手段。
从成本管理的角度来分析这一目标成本管理,不难发现,成本降低是有条件和限制的,在某些情况下,成本控制可能导致产品质量和企业效益下滑。
此外,绝大多数企业在成本管理也都缺乏整体观念,大多数公司都有一个共同的现象,那就是,依靠财务人员进行管理成本。
在成本管理过程的实施中,一些企业只注重成本核算,一些企业领导只关心财务和成本报表,从而使用报表来管理成本。
这种做法虽然减少了成本的一定作用,但归根结底,成本会计或事后控制,没有做到在成本控制和过程控制发生之前,不可替代成本费用管理。
(三)成本信息严重失真在中国,有相当数量的企业有成本信息不真实的情况下,这种状况正在恶化。
成本信息失真主要是由以下原因引起:首先,成本仅在材料,人工,制造费用的环节成为了一个焦点,现代企业的产品开发正在日益增加,却忽略了测试和中间试验和售后服务上与内容相关的投入成本的小群产品,对这些产品不完整的,不正确的评价,在整个生命周期成本效益过程起着非常重要的作用。
第二是成本核算方法不当造成的失真。
一个高度劳动密集型企业,在过去几年中,简单的假设(即直接人工小时或生产为基础分配间接费用),通常不会严重的引起扭曲产品成本的核算。
但在现代制造业环境中,直接劳动成本所占的比例显著下降,而制造成本的比例大幅增加,因此,使用传统的成本计算方法会产生不合理的行为,利用传统的成本核算,在产品成本信息中将导致严重的扭曲,使企业错误的选择产品的方向。
供应链管理Supply Chain Management的定义与重要性

供应链管理SUPPLY CHAIN MANAGEMENT, SCMSCM seeks to synchronize a firm’s processes and those of its suppliers 供应链管理寻求试图使公司和其供应商的流程同步化 【Stone, 2008-6-20】 to match the flow of 物料、服务和信息with customer demand 客户需求. SCM has strategic implications 战略意义 because competitive priorities 竞争优先权【】Supply-Chain Management involves the coordination of key processes in the firm such as order placement, order fulfillment, and purchasing, which are supported by marketing, finance, engineering, information systems, operations, and logistics.Managing the flow of material is common to organizations in every segment of the economy: churches, governments, manufactures, wholesalers, retailers, and universities.This chapter looks at the supply chain management concept, which links one’s supplier’s suppliers and one’s customers’ customers. Also covered is logistics outsourcing or 3PL (third party logistics)(1) 供应链的重要特征Key attributes of supply-chain management(2) 供应链管理的壁垒Barriers to supply-chain management(3) 供应链管理和一体化supply-chain management and integration供应链管理:定义Definition of SCMSupply chain management, SCM 供应链管理 can be defined as “the systemic, strategic business functions within a particular company and across businesses in the supply chain 供应链, for the purpose of improving the long-term performance of the individual companies and the supply chain as whole 为了改进某个公司和整个供应链的长期绩效.”定义1:商业流程集成论供应链管理是集成从最终用户到最初供应商的商业流程,以向客户以及其他相关者提供产品、服务、信息,达到增值的目的。
供应链成本管理的方法论意义【外文翻译】

外文翻译外文题目Cost Management along the Supply Chain——Methodological Implications外文出处Research Methodologies in Supply Chain Management 外文作者Richard Chivaka原文:3 ResultsTables 2 to 4 summarize the cost management tools and practices applied along all three of the supply chains studied. The tools and practices are shown according to whether their emphasis is on intra-company or inter-company cost management.3.1 DiscussionThe results of the three case studies all show that cost management is being implemented (in varying degrees) along the supply chains studied. Tables 2 to 4 shows that (i) budgetary control and variance analysis are the common intra-company cost management tools in all three supply chains, (ii) target costing and continuous improvement are the most common inter-company cost management tools applied in all three supply chains, (iii) advanced management accounting tools are not widely applied and (iv) cost management along the three supply chains appears to be achieved largely through the application of practices rather than tools. This is contrary to expectations raised in the management accounting literature that suggests the use of advanced management accounting tools such as ABC, JIT, TQM and life cycle costing. However, an analysis of the results yields some interesting insights.First, there appears to be a link between the widespread use of practices along the three supply chains studied and the stage of development of these supply chains. As pointed out earlier, relationships among supply chain partners in the South African retail industry have evolved from arms-length towards more collaborative relationships. Inter-organizational settings along these supply chains are changing as relationships become closer and are aimed at improving the competitiveness of theentire supply chains. In the present study, such changes appear to be initially supported by practices such as information sharing through open book policy, oint product design, inter-company teams and sharing of cost savings. These changes create an environment that supports the application of tools that require a‘common language’ such as activity-based costing, so as to avoid incompatibility of accounting data from companies along these supply chains as a result of different accounting systems (Dekker & van Goor, 2000). Also, common terms applicable to inter-company processes need to be developed and understood by all key players along the supply chains. As such, the application of inter-company cost management tools across company boundaries may not be easily achievable during the early stages of supply chain development. Cost management tools may be more readily applied along the sup ply chain once the requisite changes have facilitated an ‘intimacy’ between supply chain participants. It appears that in this study, companies in the supply chains are focusing on the application of practices that draw them together as a possible precursor to the application of advanced management accounting tools on a wider scale. As argued by Goldbach (2002), the application of cost management tools and the involvement of the ‘actors’ along supply chains need to be embedded in the organizational setting of the supply chains. It appears that the supply chain participants are reconfiguring their inter-organizational settings through the deployment of collaborative practices, thereby creating a climate in which the adoption and application of most of the inter-organizational cost management tools can flourish.Second, an examination of some of the approaches applied along the supply chains studied reveals the application of cost management through tools whose characteristics mimic those of the advanced management accounting tools or at least some aspects thereof. Below are some examples of these approaches.Work-study & ABCGarment costs in supply chains 1 and 2 are managed by focusing on the activities performed. The work-study departments in these supply chains produce activity information used to refine the way the activities are performed, all as a way ofreducing garment costs. The target costing approach that is commonly applied across the supply chains studied requires the understanding of activities performed to facilitate the re-engineering of products where the target costs are below the actual costs. The activity analysis approach adopted to enable the management of garment costs is similar to ABC/M, in that activity information is obtained from the work-study departments and is then used to reduce costs through the elimination of non-value added activities and processes. The ABC/M approach involves the management of activities as the route towards improving the value received by the customer (Maccarrone, 1998). The labor cost of a garment is determined from the activities that must be performed, i.e. in terms of the time per activity, and the time is then converted into labor cost. An ABC system involves the measurement of time and resources spent on work processes and then the conversion of such time to cost data (Driver, 2001).Delivery scheduling & JITThe attributes of the delivery scheduling are similar to the JIT approach. JIT aims at synchronizing the operations of companies along the supply chain, where suppliers deliver inputs of the right quality, quantity and at the right time (Agrawal & Mehra, 1998; Drury, 2000). Its emphasis is on the reduction of non-value added costs by seeking to achieve 100% on-time delivery, along with other goals such as zero inventories, zero defects and zero breakdowns (Drury, 2000). In supply chain 3 for example, Supplier 3 has specific days and times for the delivery of inputs to Manufacturer 3. The manufacturer along supply chain 3 also knows the exact times at which to deliver to the retailer’s distribution center (each manufacturer has a 15 minute window within which to arrive at the distribution center to offload at a specific bay). In supply chain 2, the retailer and the manufacturer work on a delivery calendar that specifies the dates and times when garments will be delivered to the retailer’s stores.Quality focus & TQMThe quality focus practice commonly applied along all three supply chains has characteristics similar to TQM. The focus of TQM is the identification and reductionof quality-related costs (Agrawal & Mehra, 1998; Drury, 2000). Its emphasis is on preventive measures, hence the aim is to ‘design and build quality in’, rather than trying to ‘inspect it in’ (Drury, 2000: 901). TQM focuses on sati sfying the customer, striving for continuous improvement, involvement of all employees, active support and the involvement of top management, clear objectives, and continuous training focused on quality (Blocher et al., 2002). The quality initiatives along the supply chains are focused on preventative measures (testing of input quality) rather than rectification of quality problems. This approach is supported by the selection of key suppliers (especially in supply chains 1 and 3), who are also quality conscious and have the capability to produce good quality inputs and products. Manufacturers in these supply chains are required to source inputs only from suppliers that have been approved by the retailers on the basis of, among other criteria, quality of inputs. A lot of effort is spent in creating an awareness of the importance of quality among factory employees. In supply chains 1and 2, this is achieved through employee training, as well as by the strategic placement of large notices in the factories, encouraging employees to ‘do it right first time.’ In addition, the analysis of returns-to-manufacturers (RTMs) due to quality problems is done right down to the particular department where the garments were manufactured. Employees are thus made aware of quality-related problems and the concomitant costs. Therefore, the quality focus spans both the horizontal dimension (from suppliers of inputs right up to the retail shop) and the vertical dimension (from the shop floor employees to top management). The involvement of teamwork (both intra- and inter-company teams) also makes this approach very similar to TQM.Other approaches & Life cycle costingSome form of life cycle costing is being applied along the supply chains studied. Life cycle costing involves understanding and managing the total costs of a product incurred throughout its life cycle (Drury, 2000). The total cost of a product over its life cycle can be broken down into upstream costs (research & development and design), manufacturing costs (purchasing, direct manufacturing costs and indirect manufacturing costs), and downstream costs (marketing & distribution, and serviceand warranty costs such as recalls, service, product liability and customer support) (Blocher et al., 2002). Linkages between manufacturers and suppliers (through training & assistance and joint product design), and between manufacturers and retailers (through delivery scheduling and shared transport), assist in managing upstream and downstream costs, respectively. Also, one of the purposes of life cycle costing is to reduce the costs that end-use customers incur after they have bought the product. The lower the after-sales cost, the stronger the competitive advantage of a company. In supply chains 1 and 2, life cycle costing involves tests conducted on fabric to assess how the fabric reacts when (i) washed, either in cold or hot water, (ii) ironed, and (iii) bleached. A ‘care label’ is then produced to assist end-use customers with the best way of looking after their garments. In supply chain 3, life cycle costing takes the form of shelf-life tests that are used to prescribe ‘sell-by’ and ‘use-by’ dates, as well as refrigeration conditions, thus helping end-use customers to reduce costs that could be caused by waste. These quality-related approaches are particularly important in the retail industry, which is one of the industries where upstream and downstream costs account for a significant portion of total life cycle costs (Bloecher et al., 2002).4 FindingsThe application of management accounting tools appears to be preceded by the deployment of collaborative practices that draw together participants along the supply chain. These practices create the environment within which common process terms can be defined and understood. They also create the framework within which tools that require common language can be applied to support cost management. A closer examination of some of the approaches applied along the three supply chains studied shows the application of tools having characteristics similar to advanced management accounting tools. These approaches are activity analysis (through work-study) which is similar to ABC/M, quality focus which is similar to TQM, delivery scheduling which is similar to JIT, and RTMs analysis and quality focus which are similar to life cycle costing. It is the submission of this research that some practitioners are intuitively applying these advanced management accounting tools or parts thereof without referring to conventional terms used in the management accounting literature.Also, it is the submission of this research that if specific terms (e.g. ABC) are used to analyze the presence and hence the application of a tool, it is possible to conclude that such a tool is not being applied. However, if attention is given to the characteristics of the approaches that practitioners are using, and these characteristics are then compared with those of the tools known in the management accounting literature, a better conclusion is likely to be made.5 Contribution of ResearchThe major contributions of this research derive from the empirical research method adopted. First, the empirical research on the application of cost management was conducted by gathering data from three supply chains among three different participants along the supply chains, as opposed to gathering data from one stage of the supply chain only. Through multiple case studies and the application of the pattern of behavior approach, the research revealed that some practitioners are intuitively applying advanced management accounting tools or parts thereof to achieve cost management without using textbook definitions. Second, the case studies allowed the understanding of intimate, contextually sensitive knowledge of the manner in which supply chain participants are configuring their relationships through practices (such as open book policy, joint product design, training and assistance) as a precursor to the adoption and application of tools that require common language and a high level of intimacy. Third, case studies facilitated the observation of actual management practices that have an impact on cost management, hence they enabled a gain in insight into this important, emerging and yet ill-defined area from an exploratory perspective.6 ConclusionThe use of multiple case studies facilitates the understanding of the execution of cost management among supply chain partners from the perspective of characteristics of approaches applied by practitioners. Also, the way in which management accounting tools are applied to support cost management along the supply chains in developing countries should be interpreted in terms of the stage of evolution of the supply chains, as well as the practices deployed in the process of creating more collaborativerelationships. This research was exploratory in nature; hence more case studies need to be conducted to increase the extent to which findings can be generalized. Also, other case studies focusing on issues such as the impact of the use of power (i.e. its effects on the nature of co-operation achieved between supply chain participants), and how this affects the manner in which cost management is implemented need to be explored.Source: Richard Chivaka. Cost Management along the Supply Chain —Methodological Implications. Research Methodologies in Supply Chain Management, 2005,Part 3:P299-314译文:供应链成本管理的方法论意义3、研究成果表2和表4根据我们以上研究的三种供应链,总结了成本管理方法和实践应用。
供应链管理的概念内容及意义

供应链管理的概念内容及意义供应链管理的概念、内容及意义一、供应链管理的含义(一)供应链管理的含义和特征1.供应链管理的含义供应链管理(Supply Chain Management,SCM)是以提高企业个体和供应链整体的长期绩效为目标,对传统的商务活动进行总体的战略协调,对特定公司内部跨职能部门边界的运作和在供应链成员中跨公司边界的运作进行战术控制的过程。
供应链管理就是要整合供应商、制造部门、库存部门和配送商等供应链上的诸多环节,减少供应链的成本,促进物流和信息流的交换,以求在正确的时间和地点,生产和配送适当数量的正确产品,提高企业的总体效益。
供应链管理通过多级环节,提高整体效益。
每个环节都不是孤立存在的,这些环节之间存在着错综复杂的关系,形成网络系统。
同时这个系统也不是静止不变的,不但网络间传输的数据不断变化,而且网络的构成模式也在实时进行调整。
2.供应链管理的特征(1)以xx满意为最高目标,以市场需求的拉动为原动力;(2)企业之间关系更为紧密,共担风险,共享利益;(3)把供应链中所有节点企业作为一个整体进行管理;库存原材料在制品分销销售点最终制造采购分销零售用户供应商供应链管理的概念内容及意义图1-4 供应链管理的范围(4)对工作流程、实物流程和资金流程进行设计、执行、xx和不断改进;(5)利用信息系统优化供应链的运作;(6)缩短产品完成时间,是生产尽量贴近实时需求;(7)减少采购、库存、运输等环节的成本。
以上特征中,(1)(2)(3)是供应链管理的实质,(4)(5)是实施供应链管理的两种主要方法,而(6)(7)则是实施供应链管理的主要目标,即从时间和成本两个方面为产品增值,从而增强企业的竞争力。
二、供应链管理的内容作为供应链中各节点企业相关运营活动的协调平台,供应链管理应把重点放在以下几个方面:(一)供应链战略管理。
供应链管理本身属于企业战略层面的问题,因此,在选择和参与供应链时,必须从企业发展战略的高度考虑问题。
供应链管理的概念内容及意义
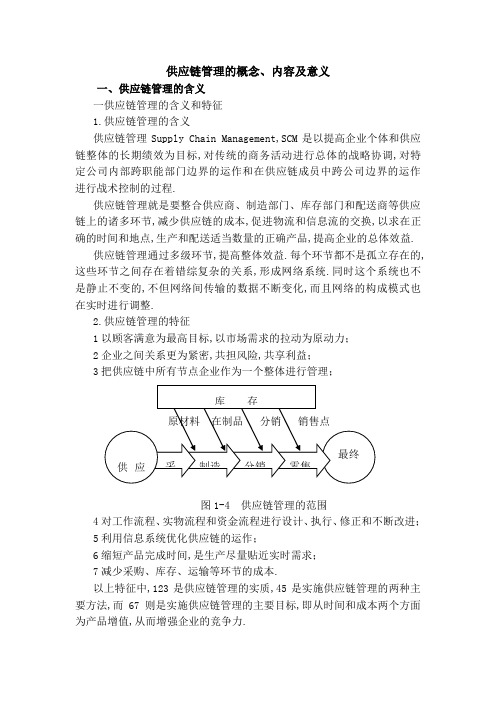
供应链管理的概念、内容及意义一、供应链管理的含义一供应链管理的含义和特征1.供应链管理的含义供应链管理Supply Chain Management,SCM是以提高企业个体和供应链整体的长期绩效为目标,对传统的商务活动进行总体的战略协调,对特定公司内部跨职能部门边界的运作和在供应链成员中跨公司边界的运作进行战术控制的过程.供应链管理就是要整合供应商、制造部门、库存部门和配送商等供应链上的诸多环节,减少供应链的成本,促进物流和信息流的交换,以求在正确的时间和地点,生产和配送适当数量的正确产品,提高企业的总体效益.供应链管理通过多级环节,提高整体效益.每个环节都不是孤立存在的,这些环节之间存在着错综复杂的关系,形成网络系统.同时这个系统也不是静止不变的,不但网络间传输的数据不断变化,而且网络的构成模式也在实时进行调整.2.供应链管理的特征1以顾客满意为最高目标,以市场需求的拉动为原动力;2企业之间关系更为紧密,共担风险,共享利益;3把供应链中所有节点企业作为一个整体进行管理;图1-4 供应链管理的范围4对工作流程、实物流程和资金流程进行设计、执行、修正和不断改进;5利用信息系统优化供应链的运作;6缩短产品完成时间,是生产尽量贴近实时需求;7减少采购、库存、运输等环节的成本.以上特征中,123是供应链管理的实质,45是实施供应链管理的两种主要方法,而67则是实施供应链管理的主要目标,即从时间和成本两个方面为产品增值,从而增强企业的竞争力.二、供应链管理的内容作为供应链中各节点企业相关运营活动的协调平台,供应链管理应把重点放在以下几个方面:一供应链战略管理.供应链管理本身属于企业战略层面的问题,因此,在选择和参与供应链时,必须从企业发展战略的高度考虑问题.它涉及企业经营思想,在企业经营思想指导下的企业文化发展战略、组织战略、技术开发与应用战略、绩效管理战略等,以及这些战略的具体实施.供应链运做方式、为参与供应链联盟而必需的信息支持系统、技术开发与应用以及绩效管理等都必须符合企业经营管理战略.二信息管理.信息以及对信息的处理质量和速度是企业能否在供应链中获益大小的关键,也是实现供应链整体效益的关键.因此,信息管理是供应链管理的重要方面之一.信息管理的基础是构建信息平台,实现供应链的信息共享,通过ERP和VMI等系统的应用,将供求信息及时、准确地传递到相关节点企业,从技术上实现与供应链其他成员的集成化和一体化.三客户管理.客户管理是供应链的起点.如前所述,供应链源于客户需求,同时也终于客户需求,因此供应链管理是以满足客户需求为核心来运作的.通过客户管理,详细地掌握客户信息,从而预先控制,在最大限度地节约资源的同时,为客户提供优质的服务.四库存管理.供应链管理就是利用先进的信息技术,收集供应链各方以及市场需求方面的信息,减少需求预测的误差,用实时、准确的信息控制物流,减少甚至取消库存实现库存的“虚拟化”,从而降低库存的持有风险.五关系管理.通过协调供应链各节点企业,改变传统的企业间进行交易时的“单向有利”意识,使节点企业在协调合作关系基础上进行交易,从而有效地降低供应链整体的交易成本,实现供应链的全局最优化,使供应链上的节点企业增加收益,进而达到双赢的效果.六风险管理.信息不对称、信息扭曲、市场不确定性以及其他政治、经济、法律等因素,导致供应链上的节点企业运作风险,必须采取一定的措施尽可能地规避这些风险.例如,通过提高信息透明度和共享性、优化合同模式、建立监督控制机制,在供应链节点企业间合作的各个方面、各个阶段,建立有效的激励机制,促使节点企业间的诚意合作.从供应链管理的具体运作看,供应链管理主要涉及以下四个领域:供应管理,生产计划,物流管理,需求管理.具体而言,包含以下内容:1.物料在供应链上的实体流动管理;2.战略性供应商和客户合作伙伴关系管理;3.供应链产品需求预测和计划;4.供应链的设计全球网络的节点规划与选址;图1-5 供应链管理涉及的领域5.企业内部与企业之间物料供应与需求管理;6.基于供应链管理的产品设计与制造管理、生产集成化计划、跟踪和设计;7.基于供应链的客户服务和物流运输、库存、包装等管理;8.企业间资金流管理汇率、成本等问题;9.基于Internet/Intranet的供应链交互信息管理.三、供应链管理的基本原则一以消费者为中心的原则.将消费者按照履约要求进行分类并努力调整业务运营以满足消费者的要求.二贸易伙伴之间密切合作、共享利益和共担风险的原则.供应链企业之间的关系是合作伙伴之间的关系,如果没有这种战略伙伴关系,供应链的一体化就难以实现.贸易伙伴之间应密切合作、共享利益和共担风险.三促进信息充分流动的原则.整合销售与运营计划,确保企业内部销售部门和运营部门之间,供应链合作伙伴之间对于客户需求的信息的实时沟通.四制定客户驱动的绩效指标.引导供应链上所有企业的行为并对每个企业的表现进行评价和跟踪.四、供应链管理的程序一分析市场竞争环境,识别市场机会分析市场竞争环境就是识别企业所棉对的市场特征,寻找市场机会.企业可以根据波特模型提供的原理和方法,通过市场调研等手段,对供应商、用户、竞争者进行深入研究;企业也可以通过建立市场信息采集监控系统,并开发对复杂信息的分析和决策技术.二分析顾客价值所谓顾客价值是指顾客从给定产品或服务中所期望得到的所有利益,包括产品价值、服务价值、人员价值和形象价值等.供应链管理的目标在于不断提高顾客价值,因此,营销人员必须从顾客价值的角度来定义产品或服务的具体特征,而顾客的需求是驱动整个供应链运作的源头.三确定竞争战略从顾客价值出发找到企业产品或服务定位之后,企业管理人员要确定相应的竞争战略.根据波特的竞争理论,企业获得竞争优势有三种基本战略形式:成本领先战略、差别化战略以及目标市场集中战略.四分析本企业的核心竞争力供应链管理注重的是企业核心竞争力,强调企业应专注于核心业务,建立核心竞争力,在供应链上明确定位,将非核心业务外包,从而使整个供应链具有竞争优势.五评估、选择合作伙伴供应链的建立过程实际上是一个合作伙伴的评估、筛选和甄别的过程.选择合适的对象企业作为供应链中的合作伙伴,是加强供应链管理的重要基础,如果企业选择合作伙伴不当,不仅会减少企业的利润,而且会使企业失去与其他企业合作的机会,抑制了企业竞争力的提高.评估、选择合作伙伴的方法很多,企业在实际具体运作过程中,可以灵活地选择一种或多种方法相结合.具体内容将在第四章中详细加以介绍.六供应链企业运作供应链企业运作的实质是以物流、服务流、信息流、资金流为媒介,实现供应链的不断增值.具体而言,就是要注重生产计划与控制、库存管理、物流管理与采购、信息技术支撑体系这四个方面的优化与建设.七绩效评估供应链节点企业必须建立一系列评估指标体系和度量方法,反映整个供应链运营绩效的评估指标主要有产销率指标、平均产销绝对偏差指标、产需率指标、供应链总运营成本指标、产品质量指标等.八反馈和学习信息反馈和学习对供应链节点企业非常重要.相互信任和学习,从失败中汲取经验教训,通过反馈的信息修正供应链并寻找新的市场机会成为每个节点企业的职责.因此,企业必须建立一定的信息反馈渠道,从根本上演变为自觉的学习型组织.五、实施供应链管理的意义供应链管理模式是顺应市场形势的必然结果,供应链管理能充分利用企业外部资源快速响应市场需求,同时又能避免自己投资带来的建设周期长、风险高等问题,赢得产品在成本、质量、市场响应、经营效率等各方面的优势,可以增强企业的竞争力.一供应链管理能提高企业间的合作效率现代社会,大部分产品需要各种企业的分工协作才能完成.譬如,波音747飞机的制造需要400万余个零部件,可这些零部件的绝大部分并不是由波音公司内部生产的,而是由65个国家的1500个大企业和15000个中小企业提供的.在这些合作生产的过程中,众多的供应商、生产商、分销商、零售商构成了供应链的冗长的、复杂的流通渠道,企业之间的合作效率极低.供应链管理的实质是跨越分隔顾客、厂家、供应商的有形或无形的屏障,把它们整合为一个紧密的整体,并对合作伙伴进行协调、优化管理,使企业之间形成良好的合作关系.二供应链管理可提高客户满意度供应链从客户开始,到客户结束.供应链是真正面向客户的管理.从前的生产是大批量生产,但随着客户越来越多个性化需求的出现,现在的生产要求满足客户的不同需求.供应链管理把客户作为个体来进行管理,并及时把客户的需求反应到生产上,能够做到对客户需求的快速响应.因而不仅满足了客户的需求,而且还挖掘客户潜在的需求.比如,供应链管理中的客户关系管理Customer Relationship Management,CRM,就可以根据客户的历史记录,分析客户的潜在需求,在客户想到之前把客户需求的产品生产出来.三供应链管理是企业新的利润源泉供应链管理思想与方法目前己在许多企业中得到了应用,并且取得了很大的成就.调查表明,通过实施供应链管理,企业可以降低供应链管理的总成本,提高准时交货率,缩短订单满足提前期,提高生产率,提高绩优企业资产运营业绩,降低库存等提高企业经济效益.。
简述供应链管理的意义

简述供应链管理的意义供应链管理是指为了实现企业最优化运作和利益最大化,对企业内外的供应商、制造商、分销商、零售商等各个环节进行协调和管理的一系列活动。
它在整个企业运作中起到重要的作用,对于企业的发展和竞争力具有决定性的影响。
以下将从多个方面解析供应链管理的意义。
供应链管理能够提高企业的运作效率。
通过对供应链中的各个环节进行协调和管理,可以减少生产和配送过程中的浪费,降低企业的运营成本。
例如,通过合理的库存管理和物流规划,可以减少库存积压和运输时间,提高产品的周转率和交付速度,从而缩短了整个供应链的周期,提高了企业的生产效率和运作效率。
供应链管理有助于提高产品质量和服务水平。
通过对供应链中的每个环节进行严格的质量控制和监管,可以确保产品的质量符合标准和客户的需求。
同时,供应链管理还可以优化企业的配送和售后服务,提高客户满意度和忠诚度。
例如,通过建立完善的售后服务体系,及时解决客户的问题和投诉,提高了企业的口碑和品牌形象。
供应链管理可以提高企业的竞争力。
在市场竞争日益激烈的背景下,企业需要通过不断提高自身的竞争力来获得更多的市场份额和利润。
供应链管理可以帮助企业优化供应商选择和合作关系,确保企业能够获得高质量的原材料和组件,降低采购成本。
同时,通过建立稳定的供应链网络和合理的分销渠道,可以更好地满足市场需求,提供更具竞争力的产品和服务。
供应链管理还可以提升企业的灵活性和应变能力。
在市场需求不断变化和供应链中出现异常情况时,企业需要能够及时做出调整和应对。
通过建立敏捷的供应链管理体系,企业可以更好地预测和应对市场需求的波动,通过灵活的生产和物流调度,快速响应市场变化,减少损失和风险。
供应链管理可以促进企业与供应商和客户之间的合作与沟通。
通过与供应商和客户建立紧密的合作关系,共享信息和资源,可以实现供应链中各个环节的优化和协同效应,提高整个供应链的效益。
同时,供应链管理还可以加强企业与供应商和客户之间的信任和合作,建立长期稳定的合作关系,共同推动供应链的持续改进和发展。
- 1、下载文档前请自行甄别文档内容的完整性,平台不提供额外的编辑、内容补充、找答案等附加服务。
- 2、"仅部分预览"的文档,不可在线预览部分如存在完整性等问题,可反馈申请退款(可完整预览的文档不适用该条件!)。
- 3、如文档侵犯您的权益,请联系客服反馈,我们会尽快为您处理(人工客服工作时间:9:00-18:30)。
供应链成本管理的方法论意义【外文翻译】本科毕业论文(设计)外文翻译外文题目 Cost Management along the Supply Chain——Methodological Implications外文出处 Research Methodologies in Supply Chain Management外文作者 Richard Chivaka原文:3 ResultsTables 2 to 4 summarize the cost management tools and practices applied along all three of the supply chains studied. The tools and practices are shown according to whether their emphasis is on intra-company or inter-company cost management. 3.1 Discussion The results of the three case studies all show that cost management is being implemented (in varying degrees) along the supply chains studied. Tables 2 to 4 shows that (i) budgetary control and variance analysis are the common intra-company cost management tools in all three supply chains, (ii) target costing and continuous improvement are the most common inter-company cost management tools applied in all three supply chains, (iii) advanced management accounting tools are not widely applied and (iv) cost management along the three supply chains appears to be achieved largely through the application of practices rather than tools. This is contrary to expectations raised in the managementaccounting literature that suggests the use of advanced management accounting tools such as ABC, JIT, TQM and life cycle costing. However, an analysis of the results yields some interesting insights. First, there appears to be a link between the widespread use of practices along the three supply chains studied and the stage of development of these supply chains. As pointed out earlier, relationships among supply chain partners in the South African retail industry have evolved from arms-length towards more collaborative1relationships. Inter-organizational settings along these supply chains are changing as relationships become closer and are aimed at improving the competitiveness of the entire supply chains. In the present study, such changes appear to be initially supported by practices such as information sharing through open book policy, oint product design, inter-company teams and sharing of cost savings. These changes create an environment that supports the application of toolsthat require a‘commonlanguage’ such as activity-based costing, so as to avoid incompatibility of accounting data from companies along these supply chains as a result of different accounting systems (Dekker & van Goor, 2000). Also, common terms applicable to inter-company processes need to be developed and understood by all key players along the supply chains. As such, the application of inter-company cost management tools across company boundaries may not be easily achievable during the early stagesof supply chain development. Cost management tools may be more readily applied along the supply chain once the requisite changes havefacilitate d an ‘intimacy’ between supply chain participants. It appears that in this study, companies in the supply chains are focusing on the application of practices that draw them together as a possible precursor to the application of advanced management accounting tools on a wider scale. As argued by Goldbach (2002), the application of cost management tools and the involvement of the ‘actors’ along supply chains need to be embedded in the organizational setting of the supply chains. It appears that the supply chain participants are reconfiguring their inter-organizational settings through the deployment of collaborative practices, thereby creating a climate in which theadoption and application of most of the inter-organizational cost management tools can flourish.Second, an examination of some of the approaches applied along the supply chains studied reveals the application of cost management through tools whose characteristics mimic those of the advanced management accounting tools or at least some aspects thereof. Below are some examples of these approaches. Work-study & ABCGarment costs in supply chains 1 and 2 are managed by focusing onthe activities2performed. The work-study departments in these supply chains produce activity information used to refine the way the activities are performed,all as a way of reducing garment costs. The target costing approach that is commonly applied across the supply chains studied requires the understanding of activities performed to facilitate the re-engineering of products where the target costs are below the actual costs. The activity analysis approach adopted to enable the management of garment costs is similar to ABC/M, in that activity information is obtained from the work-study departments and is then used to reduce costs through the elimination of non-value added activities and processes. The ABC/M approach involves the management of activities as the route towards improving the value received by the customer (Maccarrone, 1998). The labor cost of a garment is determined from the activities that must be performed, i.e. in terms of the time per activity, and the time is then converted into labor cost. An ABC system involves the measurement of time and resources spent on work processes and then the conversion of such time to cost data (Driver, 2001).Delivery scheduling & JITThe attributes of the delivery scheduling are similar to the JIT approach. JIT aims at synchronizing the operations of companies along the supply chain, where suppliers deliver inputs of the right quality, quantity and at the right time (Agrawal & Mehra, 1998; Drury, 2000). Its emphasis is on the reduction of non-value added costs by seeking to achieve 100% on-time delivery, along with other goals such as zero inventories, zero defects and zero breakdowns (Drury, 2000). In supply chain 3 for example, Supplier 3 has specific days and times for thedelivery of inputs to Manufacturer 3. The manufacturer along supply chain 3 also knows the exact times at which to deliver to theretailer’s distribution center (each manufacturer has a 15 minute window within which to arrive at the distribution center to offload at a specific bay). In supply chain 2, the retailer and the manufacturer work on a delivery calendar that specifies the dates and times when garments will be delivered to the retailer’s stores.Quality focus & TQM3The quality focus practice commonly applied along all three supply chains has characteristics similar to TQM. The focus of TQM is the identification and reduction of quality-related costs (Agrawal & Mehra, 1998; Drury, 2000). Its emphasis is on preventive measures, hence the aim is to ‘design and build quality in’, rather than trying to‘inspect it in’ (Drury, 2000: 901). TQM focuses on satisfying the customer,striving for continuous improvement, involvement of all employees, active support and the involvement of top management, clear objectives, and continuous training focused on quality (Blocher et al., 2002). The quality initiatives along the supply chains are focused on preventative measures (testing of input quality) rather than rectification of quality problems. This approach is supported by the selection of key suppliers (especially in supply chains 1 and 3), who are also quality conscious and have the capability to produce good quality inputs and products.Manufacturers in these supply chains are required to source inputs only from suppliers that have been approved by the retailers on the basis of, among other criteria, quality of inputs. A lot of effort is spent in creating an awareness of the importance of quality among factory employees. In supply chains 1and 2, this is achieved through employee training, as well as by the strategic placement of large notices in the factories, encouraging employees to ‘do it right first time.’ In addition, the analysis ofreturns-to-manufacturers (RTMs) due to quality problems is doneright down to the particular department where the garments were manufactured. Employees are thus made aware of quality-related problems and the concomitant costs. Therefore, the quality focus spans both the horizontal dimension (from suppliers of inputs right up to the retail shop) and the vertical dimension (from the shop floor employees to top management). The involvement of teamwork (both intra- and inter-company teams) also makes this approach very similar to TQM.Other approaches & Life cycle costingSome form of life cycle costing is being applied along the supply chains studied. Life cycle costing involves understanding and managing the total costs of a product incurred throughout its life cycle (Drury, 2000). The total cost of a product over its life cycle can be broken down into upstream costs (research & development and4design), manufacturing costs (purchasing, direct manufacturing costs and indirect manufacturing costs), and downstream costs (marketing & distribution, and service and warranty costs such as recalls, service, product liability and customer support) (Blocher et al., 2002). Linkages between manufacturers and suppliers (through training & assistance and joint product design), and between manufacturers and retailers (through delivery scheduling and shared transport), assist in managing upstream and downstream costs, respectively. Also, one of the purposes of life cycle costing is to reduce the costs that end-use customers incur after they have bought the product. The lower the after-sales cost, the stronger the competitive advantage of a company. In supply chains 1 and 2, life cycle costing involves tests conducted on fabric to assess how the fabric reacts when (i) washed, either in cold or hot water, (ii) ironed, and (iii) bleached. A ‘care label’ is then produced to assist end-use customerswith the best way of looking after their garments. In supply chain 3, life cycle costing takes the form of shelf-life tests that are used to prescribe ‘sell-by’ and ‘use-by’ dates,as well as refrigeration conditions, thus helping end-use customersto reduce costs that could be caused by waste. These quality-related approaches are particularly important in the retail industry, which is one of the industries where upstream and downstream costs account for a significant portion of total life cycle costs (Bloecher et al., 2002). 4 FindingsThe application of management accounting tools appears to be preceded by the deployment of collaborative practices that draw together participants along the supply chain. These practices create the environment within which common process terms can be defined and understood. They also create the framework within which tools that require common language can be applied to support cost management. A closer examination of some of the approaches applied along the three supply chains studied shows the application of tools having characteristics similar to advanced management accounting tools. These approaches are activity analysis (through work-study) which is similar to ABC/M, quality focus which is similar to TQM, delivery scheduling which is similar to JIT, and RTMs analysis and quality focus which are similar to life cycle costing. It is the submission of this researchthat some practitioners are5intuitively applying these advanced management accounting tools or parts thereof without referring to conventional terms used in the management accounting literature. Also, it is the submission of this research that if specific terms (e.g. ABC) are used to analyze the presence and hence the application of a tool, it is possible to conclude that such a tool is not being applied. However, if attention is given to the characteristics of the approaches that practitioners are using, and these characteristics are then compared with those of the tools known inthe management accounting literature, a better conclusion is likely to be made.5 Contribution of ResearchThe major contributions of this research derive from the empirical research method adopted. First, the empirical research on theapplication of cost management was conducted by gathering data from three supply chains among three different participants along the supply chains, as opposed to gathering data from one stage of the supply chain only. Through multiple case studies and the application of the pattern of behavior approach, the research revealed that some practitioners are intuitively applying advanced management accounting tools or parts thereof to achieve cost management without using textbook definitions. Second, the case studies allowed the understanding of intimate, contextually sensitive knowledge of the manner in which supply chain participants are configuring their relationships through practices (such as open book policy, joint product design, training and assistance) as a precursor to the adoption and application of tools that require common language and a high level of intimacy. Third, case studies facilitated the observation of actual management practices that have an impact on cost management, hence they enabled a gain in insight into this important, emerging and yet ill-defined area from an exploratory perspective.6 ConclusionThe use of multiple case studies facilitates the understanding of the execution of cost management among supply chain partners from the perspective of characteristics of approaches applied by practitioners. Also, the way in which management accounting tools are applied to support cost management along the supply chains in developing6countries should be interpreted in terms of the stage of evolution of the supply chains, as well as the practices deployed in the process of creating more collaborative relationships. This research was exploratory in nature; hence more case studies need to be conducted to increase the extent to which findings can be generalized. Also, other case studies focusing on issues such as the impact of the use of power (i.e. its effects on the nature of co-operation achieved between supply chain participants), and how this affects the manner in which cost management is implemented need to be explored.Source: Richard Chivaka. Cost Management along the Supply Chain —Methodological Implications. Research Methodologies in Supply ChainManagement, 2005,Part 3:P299-3147译文:供应链成本管理的方法论意义3、研究成果表2和表4根据我们以上研究的三种供应链,总结了成本管理方法和实践应用。