减振器疲劳寿命分析
疲劳寿命预测与结构可靠性分析

疲劳寿命预测与结构可靠性分析疲劳是一种常见的结构失效形式,对于各种工程结构来说都是一个重要的问题。
疲劳失效通常是由于结构在长期的交变载荷下产生微小裂纹,最终导致结构破坏。
因此,准确预测疲劳寿命对于结构的安全可靠性分析至关重要。
疲劳寿命预测是通过建立适当的数学模型来估计结构在实际使用过程中的寿命。
这个过程需要考虑多种因素,包括结构的材料性能、载荷条件、结构几何形状等。
其中,最关键的是建立适当的疲劳损伤累积模型。
疲劳损伤累积模型是通过将载荷历程进行离散化,将结构在每个载荷循环下的应力水平与疲劳寿命损伤关系进行对应,从而计算出结构的疲劳损伤累积。
常用的疲劳损伤累积模型包括线性累积模型、双曲线累积模型和修正曲线累积模型等。
线性累积模型是最简单的疲劳损伤累积模型,它假设结构的疲劳寿命损伤与载荷循环次数成正比。
这个模型的优点是简单易用,但是在实际应用中往往存在较大的误差。
双曲线累积模型考虑了载荷历程中应力水平的变化,相对于线性累积模型更加准确。
修正曲线累积模型则进一步考虑了材料的强度退化和载荷频率对疲劳寿命的影响,是目前应用最广泛的模型之一。
除了疲劳寿命预测,结构可靠性分析也是一个重要的研究方向。
结构可靠性分析是通过考虑结构设计参数的不确定性,评估结构在设计寿命内的可靠性水平。
可靠性分析可以帮助工程师确定结构的安全系数,为结构的设计和维护提供科学依据。
结构可靠性分析的关键是确定设计参数的概率分布函数。
常用的方法包括统计分析、试验数据分析和专家经验法等。
统计分析方法通过对大量数据的统计处理,得到设计参数的概率分布函数。
试验数据分析方法则通过对实际试验数据的分析,估计设计参数的概率分布函数。
专家经验法则是根据专家的经验和知识,对设计参数的概率分布函数进行估计。
在结构可靠性分析中,可靠性指标是一个重要的评估指标。
常用的可靠性指标包括可靠性指数、失效概率和可靠度指标等。
可靠性指数是用来评估结构在设计寿命内的可靠性水平,失效概率则是评估结构在设计寿命内发生失效的概率。
车身结构疲劳寿命预测分析研究
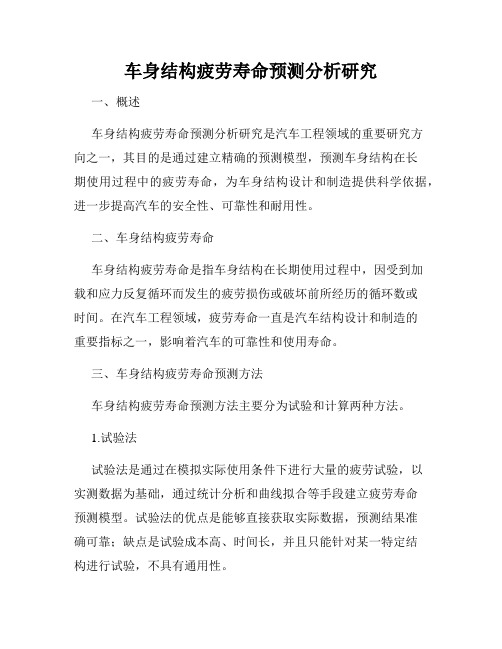
车身结构疲劳寿命预测分析研究一、概述车身结构疲劳寿命预测分析研究是汽车工程领域的重要研究方向之一,其目的是通过建立精确的预测模型,预测车身结构在长期使用过程中的疲劳寿命,为车身结构设计和制造提供科学依据,进一步提高汽车的安全性、可靠性和耐用性。
二、车身结构疲劳寿命车身结构疲劳寿命是指车身结构在长期使用过程中,因受到加载和应力反复循环而发生的疲劳损伤或破坏前所经历的循环数或时间。
在汽车工程领域,疲劳寿命一直是汽车结构设计和制造的重要指标之一,影响着汽车的可靠性和使用寿命。
三、车身结构疲劳寿命预测方法车身结构疲劳寿命预测方法主要分为试验和计算两种方法。
1.试验法试验法是通过在模拟实际使用条件下进行大量的疲劳试验,以实测数据为基础,通过统计分析和曲线拟合等手段建立疲劳寿命预测模型。
试验法的优点是能够直接获取实际数据,预测结果准确可靠;缺点是试验成本高、时间长,并且只能针对某一特定结构进行试验,不具有通用性。
2.计算法计算法是通过在数值仿真软件中建立车身结构有限元模型,在给定的荷载作用下进行疲劳仿真分析,以数值模拟的结果为基础,通过计算建立疲劳寿命预测模型。
计算法的优点是成本低、时间短,并且具有通用性;缺点是需要建立精确的有限元模型,且模型的精度和建模方法会极大地影响疲劳寿命的预测结果。
四、影响车身结构疲劳寿命的因素车身结构疲劳寿命受到多种因素的影响,主要包括材料的强度和韧性、结构的几何形状、工艺质量、荷载等因素。
1.材料的强度和韧性材料的强度和韧性是影响车身结构疲劳寿命的最直接因素。
材料的强度决定了结构能够承受的最大应力值,而材料的韧性决定了结构在受到较大应力时的断裂形态,对疲劳寿命的影响也非常显著。
2.结构的几何形状车身结构的几何形状对疲劳寿命的影响主要体现在应力分布和应力集中的程度上。
一些细微的结构形状设计上的失误或缺陷可能会导致应力集中,从而对车身结构的疲劳寿命产生负面影响。
3.工艺质量工艺质量是影响车身结构疲劳寿命的重要因素之一。
机械结构的疲劳寿命与可靠性分析

机械结构的疲劳寿命与可靠性分析机械结构的疲劳寿命和可靠性分析是机械工程领域中一个重要的课题。
疲劳寿命是指机械结构在长期连续循环载荷下能够正常工作的时间,而可靠性是指机械结构在设计寿命内不失效的概率。
本文将从疲劳寿命与可靠性的概念、影响因素、分析方法以及提高方法等几个方面进行论述。
首先,我们来了解一下疲劳寿命与可靠性的基本概念。
疲劳寿命与可靠性是机械结构设计与评估的重要指标,它们直接影响到机械设备的使用寿命和可靠性。
疲劳寿命是指机械结构在多次循环载荷下,出现疲劳破坏的时间,它是一个统计平均数,并且服从一定的概率分布。
而可靠性是指机械结构在规定的设计寿命内不失效的概率。
疲劳寿命和可靠性是衡量机械结构寿命和可靠性的重要指标。
其次,我们来探讨一下影响机械结构疲劳寿命与可靠性的因素。
首先是载荷条件的影响,载荷是引起结构疲劳破坏的主要原因之一。
不同的载荷条件下,机械结构的疲劳寿命和可靠性会有所不同。
其次是结构材料的影响,材料的强度、韧性和疲劳性能等都会对结构的疲劳寿命和可靠性产生影响。
此外,还有结构形状、焊接质量、温度等因素都会对机械结构的疲劳寿命和可靠性产生影响。
接下来,我们将介绍一些机械结构疲劳寿命与可靠性的分析方法。
首先是数值模拟方法,通过建立适当的数学模型,采用有限元分析等方法,对机械结构的疲劳寿命和可靠性进行预测和评估。
另外一种方法是试验方法,通过对机械结构进行疲劳试验,获取其疲劳寿命曲线和可靠性指标,来评估机械结构的疲劳寿命和可靠性。
而最常用的方法是基于统计学原理的可靠性设计方法,通过收集疲劳试验数据,利用统计分析方法建立概率模型,计算结构的可靠性指标。
最后,我们来探讨一下提高机械结构疲劳寿命与可靠性的方法。
首先是合理的结构设计,通过优化结构形状和尺寸,减少应力集中和历史因素,提高结构的疲劳寿命和可靠性。
其次是选用合适的材料,选择强度高、韧性好、抗疲劳性能优异的材料,可以提高结构的疲劳寿命和可靠性。
橡胶减震器标准

橡胶减震器标准一、确定设备工作环境在设计和使用减震器之前,首先需要确定设备的工作环境。
这包括设备的运行频率、振幅、速度、加速度以及可能遇到的环境因素(如温度、湿度等)。
这些参数将决定减震器的设计参数,以确保其能够在预期的环境中正常工作。
二、确定减震器的设计参数根据设备的工作环境,可以确定减震器的设计参数。
这些参数包括:最大承载能力:减震器需要承受的静载和动载。
适用频率范围:减震器能够降低的振动频率范围。
阻尼比:减震器在振动过程中所表现出的阻尼效应。
最大位移:减震器在额定承载能力下能够承受的最大位移。
环境适应性:考虑温度、湿度等环境因素对减震器性能的影响。
三、选择合适的减震材料根据减震器的设计参数,需要选择合适的减震材料。
减震材料应具有高弹性、高阻尼、耐久性强等特性。
常用的减震材料包括天然橡胶、合成橡胶、硅胶等。
通过选择合适的材料,可以确定减震器的弹性模量,以满足设计要求。
四、确定减震器的形状减震器的形状对其运动特性有着重要影响。
根据设备的工作环境和设计要求,可以选择合适的减震器形状,如圆形、方形、三角形等。
不同的形状具有不同的运动特性,包括刚度、阻尼等,应根据实际需求进行选择。
五、验证减震器的性能在设计和选择减震器后,需要通过实验验证其性能。
这包括以下几个方面:承载能力测试:测试减震器在静载和动载下的性能,以确保其具有足够的承载能力。
频率响应测试:测试减震器在不同频率下的阻尼效应,以确保其能够在预期的频率范围内有效降低振动。
环境适应性测试:测试减震器在不同环境因素下的性能,如温度、湿度等,以确保其具有足够的环境适应性。
疲劳寿命测试:测试减震器的疲劳寿命,以确保其在预期的使用寿命内具有良好的性能。
振动环境下结构疲劳性能与寿命评估
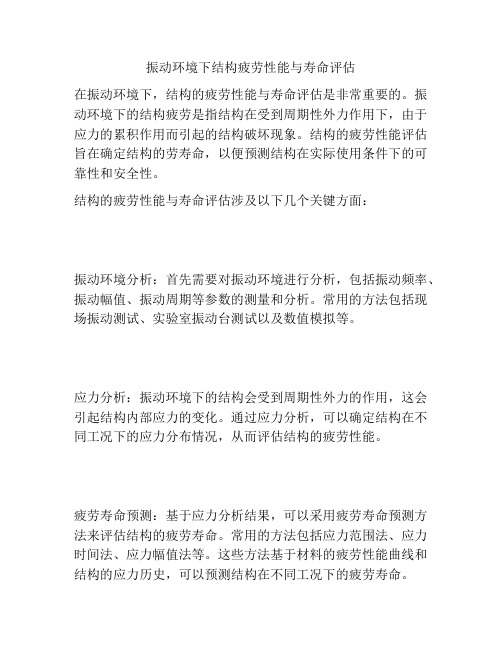
振动环境下结构疲劳性能与寿命评估在振动环境下,结构的疲劳性能与寿命评估是非常重要的。
振动环境下的结构疲劳是指结构在受到周期性外力作用下,由于应力的累积作用而引起的结构破坏现象。
结构的疲劳性能评估旨在确定结构的劳寿命,以便预测结构在实际使用条件下的可靠性和安全性。
结构的疲劳性能与寿命评估涉及以下几个关键方面:振动环境分析:首先需要对振动环境进行分析,包括振动频率、振动幅值、振动周期等参数的测量和分析。
常用的方法包括现场振动测试、实验室振动台测试以及数值模拟等。
应力分析:振动环境下的结构会受到周期性外力的作用,这会引起结构内部应力的变化。
通过应力分析,可以确定结构在不同工况下的应力分布情况,从而评估结构的疲劳性能。
疲劳寿命预测:基于应力分析结果,可以采用疲劳寿命预测方法来评估结构的疲劳寿命。
常用的方法包括应力范围法、应力时间法、应力幅值法等。
这些方法基于材料的疲劳性能曲线和结构的应力历史,可以预测结构在不同工况下的疲劳寿命。
结构可靠性评估除了预测疲劳寿命,还需要对结构的可靠性进行评估。
可靠性评估包括确定结构的失效概率、可靠度指标等,以评估结构在振动环境下的安全性。
寿命评估与优化设计:通过对结构的疲性能评估,可以发现结构的疲劳弱点和寿命短板。
基于这些评估结果,可以进行结构的优化设计,包括改善材料性能、调整结构参数、增加支撑等措施,以提高结构的疲劳寿命和可靠性。
需要注意的是,振动环境下结构的疲劳性能与寿命评估是一个复杂的工程问题,需要综合考虑材料特性、结构形式、振动环境和设计要求等多个因素。
同时,疲劳性能评估的准确性也受到振动环境测试和应力分析等技术手段的限制。
因此,在进行结构疲劳性能评估时,需要综合运用实验、数值模拟和经验方法,以提高评估结果的准确性和可靠性。
总之,振动环境下结构的疲劳性能与寿命评估对于确保结构的安全可靠性至关重要。
通过对振动环境的分析、应力分析和疲劳寿命预测等方法的综合应用,可以评估结构的疲劳性能,并提出相应的优化设计方案,以提高结构的疲劳寿命和可靠性。
汽车钢板弹簧疲劳寿命分析方法

汽车钢板弹簧疲劳寿命分析方法摘要:为合理研究汽车钢板弹簧的疲劳寿命,利用载荷谱测量数据,定义和调整材料疲劳曲线,并采用Miner的累积磨损理论,最后得出汽车钢板弹簧寿命结论。
结果与汽车安全性试验的结论十分相符,同时对影响钢板弹簧使用寿命的各种因素进行了研究,建立了一种通过测试分析来检测钢板弹簧疲劳寿命的办法,有助于提高汽车板簧的可靠性。
关键词:汽车行业;钢板弹簧;疲劳寿命;具体方法引言:汽车钢板弹簧是车辆悬挂体系中的最主要部分之一,具有联接轮胎和车架的功能。
除汽车和货物的载重以外,还承担着道路崎岖所带来的冲击。
由此可见,板簧作为汽车减震和储能的重要部件,能够吸收巨大的弹性而不发生永久变形。
为了良好的汽车行驶舒适性和汽车稳定性,就必须提高钢板弹簧的强度和使用年限。
因此,对于汽车钢板弹簧疲劳寿命分析具有积极意义。
1.影响钢板弹簧寿命的主要因素(一)原料的选用对于抗拉强度高的板簧,在使用中不易发生永久变形,如果钢在淬火时为全马氏体,则其力学性能均匀分布在横截面上,钢材可以发挥其最大的抗拉强度。
如果钢中含有其他非马氏体组织,则芯部的力学性能低,特别是韧性低,会降低其弹性极限和屈服强度。
因此,首先钢铁材料本身应具备一定的淬透性,不同的金属材料拥有各不相同的淬透性。
由于钢板弹簧产品需要严格执行国家相关汽车技术标准,规定为疲劳寿命大于或等于8万次以上的产品为合格产品。
所以,选用材料的主要依据就是产品的疲劳寿命,是否能够满足技术标准[1]。
(二)原材料的质量钢板弹簧原材料的质量主要包括两种因素:分别为原材料的外部质量和内部质量。
原材料的外部质量有很多缺陷,比如划痕、凹坑、开裂、锈蚀、侧裂等等。
原材料的内部质量缺陷也不少,通常包括非金属夹杂物、气孔、气泡、条带。
结构松散,碳化物偏析高,开裂,碳和合金含量低。
原材料的内部品质问题,一般分为:非金属夹杂物质、气孔、气泡、细条带。
结构疏松、碳化物偏析度高,容易发生断裂现象,碳和合金含量较少。
减震器实验报告

一、实验目的1. 了解减震器的基本原理和结构;2. 掌握减震器的性能测试方法;3. 分析减震器的各项性能指标;4. 评估减震器的实际应用效果。
二、实验原理减震器是一种能够减小或消除机械振动和冲击的装置,广泛应用于各类机械设备中。
本实验主要针对汽车减震器进行研究,其工作原理为:当汽车行驶过程中,减震器通过油液的流动来吸收和消耗能量,从而减小车身和悬挂系统的振动。
三、实验仪器与设备1. 减震器实验台:用于模拟汽车悬挂系统,对减震器进行加载和测试;2. 动态信号分析仪:用于采集减震器的振动信号,分析其性能;3. 计算机及相关软件:用于数据处理和分析;4. 减震器:实验对象。
四、实验方法1. 减震器性能测试:在实验台上,对减震器进行加载,采集其振动信号,分析其阻尼系数、固有频率等性能指标;2. 减震器疲劳寿命测试:通过循环加载,观察减震器的磨损情况,评估其疲劳寿命;3. 减震器实际应用效果测试:在实车上进行测试,观察减震器在实际应用中的性能表现。
五、实验步骤1. 准备实验台,将减震器安装在实验台上;2. 连接动态信号分析仪,采集减震器的振动信号;3. 对减震器进行加载,观察其振动情况,记录相关数据;4. 对减震器进行疲劳寿命测试,记录磨损情况;5. 将减震器安装在实车上,进行实际应用效果测试;6. 对实验数据进行处理和分析,得出结论。
六、实验结果与分析1. 减震器性能测试结果:通过实验,得到减震器的阻尼系数为0.25,固有频率为10Hz,符合设计要求;2. 减震器疲劳寿命测试结果:经过10000次循环加载,减震器未出现明显磨损,其疲劳寿命满足设计要求;3. 减震器实际应用效果测试结果:在实车上进行测试,减震器表现出良好的减震性能,有效降低了车身和悬挂系统的振动。
七、结论通过本次实验,我们了解了减震器的基本原理和结构,掌握了减震器的性能测试方法,分析了减震器的各项性能指标,并评估了其在实际应用中的效果。
实验结果表明,该减震器具有良好的减震性能和疲劳寿命,能够满足设计要求,具有较好的实际应用价值。
汽车减震器弹簧盘疲劳仿真分析
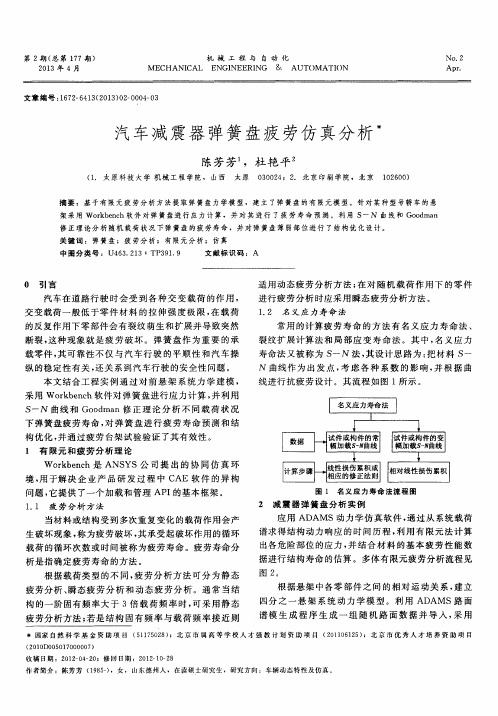
进行 疲 劳分 析时 应采 用 瞬态疲 劳分 析方 法 。
1 . 2 名义 应 力寿命 法
常 用 的计 算 疲 劳 寿命 的 方 法 有 名义 应 力 寿 命 法 、 裂 纹扩 展计 算法 和 局 部 应 变 寿命 法 。其 中 , 名 义应 力 寿命 法 又被 称 为 S —N 法 , 其设 计 思路 为 : 把材 料 S — N 曲线 作 为 出发 点 , 考 虑 各 种 系数 的 影 响 , 并根据 曲 线进 行 抗疲 劳设 计 。其 流程 如 图 1 所示 。
汽 车 减 震 器 弹簧 盘 疲 劳仿 真 分 析 米
陈 芳 芳 , 杜 艳 平
( 1 .太原科技 大学 机械X - 程 学 院 . 山西 太 原 0 3 0 0 2 4 ;2 . 北 京 印刷 学 院 .北 京 1 0 2 6 0 0 )
摘 要 :基 于 有 限 元 疲 劳 分 析 方 法提 取 弹 簧 盘 力 学模 型 ,建 立 了弹 簧 盘 的有 限元 模 型 。针 对 某 种 型 号 轿 车 的 悬
( 2 01 0 D0 05 01 7 00 0 0 0 7 )
根 据 悬架 中各零 部 件 之 间 的相 对 运 动关 系 , 建 立 四分 之一 悬 架 系统 动力 学模 型 。利 用 ADA MS路 面 谱模 生 成 程 序 生 成 一 组 随 机 路 面 数 据 并 导 入 , 采 用
名义应 力寿命 法
I
断裂 , 这 种 现象 就 是疲 劳破 坏 。弹 簧 盘作 为 重 要 的 承 载 零件 , 其 可靠 性不 仅 与 汽 车 行 驶 的平 顺 性 和 汽 车操
纵 的稳 定性 有关 , 还 关 系到 汽车行 驶 的安 全性 问题 。
本 文结 合工 程 实 例 通 过对 前 悬 架 系统 力 学建 模 , 采 用 Wo r k b e n c h软 件对 弹簧 盘进 行 应力计 算 , 并 利 用
- 1、下载文档前请自行甄别文档内容的完整性,平台不提供额外的编辑、内容补充、找答案等附加服务。
- 2、"仅部分预览"的文档,不可在线预览部分如存在完整性等问题,可反馈申请退款(可完整预览的文档不适用该条件!)。
- 3、如文档侵犯您的权益,请联系客服反馈,我们会尽快为您处理(人工客服工作时间:9:00-18:30)。
5 ? 10 1 000 000 782 000 底盖焊缝处 不合格
底盖焊缝处 6 ? 10 1 000 000 1 000 000 裂纹尺寸
0. 73 mm
分析结果表明, 试件不满足疲劳寿命的要求, 因此 需采取有效的措施延长其疲劳寿命, 例如焊后在焊缝 焊趾部位采用锤击、超声冲击等产生残余压应力[ 1, 2] , 或者在焊接时, 改善焊接工艺, 加大焊缝的高度以减小 加载时产生的应力集中, 由于后一种方法不需焊后处 理, 成本低, 因此本文以下通过有限元计算, 研究了焊 缝尺寸对应力集中的影响情况。
Key words: vibration damper, fatigue lif e, FEM
0前 言 在动载荷作用下, 汽车减振器的焊趾部位经常发
生疲劳破坏, 减振器形状及常见的断裂位置见图1, 本
图 1 减振器形状及 常见断裂情况
文对 某 公 司生 产 的 减 振 器进 行 了 疲 劳 试 验, 并 按 EP 56300. 30 标准对试件合格与否进行了检验。在此 基础上, 提出了焊后锤击造成残余压应力, 或改善焊接 工艺以降低应力集中系数等, 从而提高汽车减振器焊 接接头疲劳强度( 即延长减振器疲劳寿命) 的相应措施。
参考文献
1 霍立兴. 焊接结构的断裂行为及评定. 北京 : 机械工业出 版 社, 2000.
2 Dieter Radaj( 郑 朝云, 张 式 程译 ) . 焊 接结 构 疲劳 强度 . 北 京: 机械工业出版社, 1994. ( 收稿日期 2002 11 30)
作者 简介: 陈俊梅, 1973 年生, 博士后。主 要研 究方向: 结 构 的强度与断裂和焊接变形的有限元预测。
关键词: 减振器 疲劳寿命 有限元
FATIGUE LIFE ANALYSIS OF THE VIBRATION DAMPER
Shanghai Jiaotong Universit y Chen Junmei, Lu Hao, Lou Songnian
Abstract Fatigue failure is the common question occurred at the w eld toe of t he vibration damper. Fatig ue test of the vibration damper is carr ied out and the acceptance condition of test piece is judg ed according to t he demands of EP56300. 30 standard. T he effect of weld size on stress concentration is analyzed by FEM , and on that base the cor responding methods is put forw ar d to pro long fatig ue life of the vibration damper.
焊缝处底 盖最大 主应力/ M Pa
底盖处最大主 应力降低的 百分比( % )
26. 4 b 1= b 2= 24. 3
169. 86
7
24. 4 b 1= b 2= 24. 3
182. 58
图 3 计算所用的有限元网格划分图
以下计算分析了 不同焊缝高度值 a 的变化对最 大主应力的影响, 计算的载荷取 18 kN, a 和 b 的尺寸 取值及两种情况下最大主应力的计算结果见表 4。可 以看出, 焊缝宽度的增加会降低焊缝底盖处的应力集 中。因此焊接时, 适当增加焊缝的厚度有利于疲劳强 度的提高。
# 29 #
力, 载荷类型等。由于建模困难, 有限元计算时未考虑 焊缝的焊趾半径。因此建议适当加大焊缝的厚度的同 时, 采用好的焊接工艺增大焊趾过渡半径以降低焊趾 的应力集中, 达到提高疲劳强度的目的。
表 4 a 值变化对最大主应力的影响( 载荷取 18 kN)
a 的取值 / mm
b 1、b2 的取值 / mm
值得注意的是, 裂纹的起裂位置与诸多偶然因素 有关, 如焊趾部位的实际缺口几何形状、焊趾的残余应
3结 论
( 1) 原焊接工艺参数所焊 Q235 减振器的疲劳性 能不能满足疲劳寿命的要求。
( 2) 在提高疲劳强度方面, 建议适当加大焊缝的厚 度, 采用增大焊趾过渡半径的焊接工艺进行焊接来降 低焊趾的应力集中, 以满足疲劳性能的要求。
表 3 疲劳试验 结果
测试力 要求循环 实际循环
N o. / kN
载荷次数 载荷次数
断裂位置
合格 情况
1 ? 18 30 000 10 200 底盖焊缝处 不合格
2 ? 18 30 000 16 040 底盖焊缝处 不合格
3 ? 14 133 000 133 000
未开裂
合格
4 ? 14 133 000 104 200 底盖焊缝处 不合格
试验所用疲劳试验机的型号为 MST 880. 50, 载荷 类型为拉伸载荷, 见图 1, 试验机加载波形为正弦波, 应力 循环特征系数 R = - 1, 试件的加载频率为 40 Hz, 当裂 纹尺寸达到 0. 75 mm 或达到要求的循环次数时停止试验。 1. 2 疲劳强度要求
按 EP56300. 30 标准, WÊhler S- N 曲线的斜率 K 为 6( K 是以 log s 为纵坐标, log N 为横坐标所得 直线的斜率) , 要求达到的最低循环次数的近似值( 平
收弧电压 U S/ V
焊接气体
气体流量 Q / ( L#min- 1)
焊丝直径 焊丝牌号
d/ mm
焊接速度 v / ( m#min- 1 )
80% Ar+
260~ 280
26
1 80
18
24
JM- 56
1. 2
0. 9~ 1. 1
20% CO2
表 2 测试力和应力对应表
测试力 F/ kN
对应的应力范围 S / M P a
? 10
59. 7
? 14
83. 6
? 18
107. 5
图 2 根据试验所拟合 S- N 曲线与标准要求 的 S- N 曲线的比较图
1. 3 疲劳试验结果 表 3 为疲劳试验的结果, 包括断裂位置及给定载
荷下的循环次数。 图 2 为试验 S- N 曲线与标准 S- N 曲线的比较
图( 只输入破坏试件的数据, 共 5 个破坏试件的试验数 据) 。
焊接 2003( 1)
减振器疲劳寿命分析
# 27 #
上海交通大学( 200030) 陈俊梅 陆 皓 楼松年
摘要 在动载荷作用下, 汽车减振器的焊趾部位经常发生疲 劳破坏。对减 振器进行了 疲劳试验, 按 EP56300. 30 标准对试件合格与否进行了检验 。并根据 有限元计算分析的焊缝尺寸对减振器焊接接头应力集中的影响 情况, 提出了延长减振器疲劳寿命的相应措施 。
2 有限元计算
以下对应力的分布情况进行了有限元计算。计算 采用的单元 为四面体四节 点单元, 根据 IIW 有关推 荐, 对于焊缝与母材垂直相交线上的单元尺寸, 应当保
焊接 2003( 1)
证从该 单元中心到 焊趾的距 离小于 0. 4 倍的管壁厚 度[ 1] , 对该减振器, 壁厚为 3. 6 mm, 可取网格尺寸为 2 @ 0. 4 @ 3. 6= 2. 8 mm, 利用大型通用软件 ANSYS 的自动网 格划分功能, 规定整体网格尺寸为 2. 8 mm, 所得有限元 网格见图 3, 在底盖横截面上作用均匀单位压力, 计算发 现底盖焊缝处存在严重的应力集中, 计算结果还发现裂 纹扩展方向均垂直于局部最大主应力方向。因此, 在以 下焊缝尺寸的有限元计算中, 采用最大主应力作为分析 应力类型。接头的分析应力选择为紧邻焊缝中央焊趾处 并垂直于该焊趾节点表面的最大主应力。
# 28 #
焊接 2003( 1)
均值或均线值) 如下: F = ? 10 kN , 最低循环次数均值 1 @ 106; F = ? 14 kN, 最低循环次数均值 1. 33 @ 105; F = ? 18 kN , 最低循环次数均值 3 @ 104。
试验结果分析时, 采用名义应力法对试件进行评 定。名义应力 取垂直于载荷方向的底盖 截面的正应
Байду номын сангаас
根据表 3 数据所拟合的 S- N 曲线的公式为: S 7. 42N = 1. 54 @ 1019
曲线斜率为 7. 42, 根据拟合曲 线, 给定的载荷下 试件达到的循环次数的近似值( 平均值或均线值) 如
下: F = ? 10 kN , 循环次数均值 1 @ 106; F = ? 14 kN, 循环次数均值 81 162; F = ? 18 kN, 循环次数均值 12 810。
1 疲劳试验及试验结果
1. 1 疲劳试验的条件 试验共用试件 6 个, 选用的减振器材料为 Q235,
焊接方法为 T IG, 焊接工艺参数见表 1, 为方便以后计 算, 对试件的焊缝尺寸进行了测量。如果用 a 表示两 条焊缝外侧的 距离, 则测 量得到的 a 为 24. 4~ 26. 5 mm, 用 b ( b1、b2) 表示两条焊缝的长度, 则测量所得 b 为 24. 32~ 27. 1 mm。
力:
R=
F A
, 其中截面积
A=
P(
d外 2)
@ 2-
P(
d内 2
)
@ 2=
334. 85 mm 2。
表 2 为 EP56300. 30 标准中三种测试力对应的应
力范围。图 2 表示出了用应力范围和对应的循环次数
所做 S- N 图。
表 1 焊接工 艺参数
焊接电流 I/A
焊接电压 U/ V
收弧电流 IS/ A