ASTM G31——金属的实验室浸泡腐蚀标准
耐碱试验标准(一)
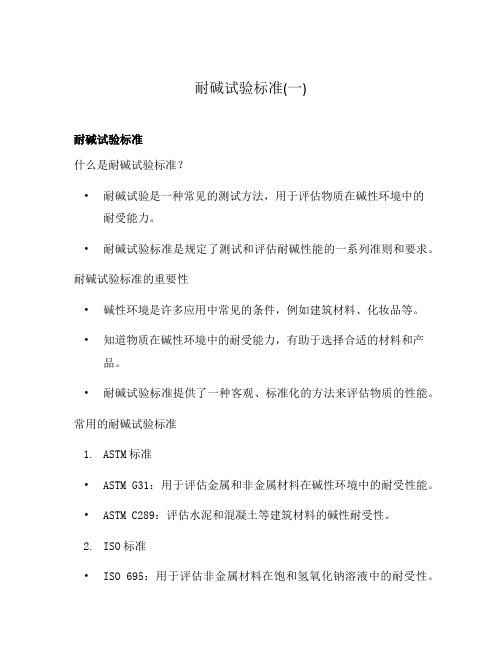
耐碱试验标准(一)耐碱试验标准什么是耐碱试验标准?•耐碱试验是一种常见的测试方法,用于评估物质在碱性环境中的耐受能力。
•耐碱试验标准是规定了测试和评估耐碱性能的一系列准则和要求。
耐碱试验标准的重要性•碱性环境是许多应用中常见的条件,例如建筑材料、化妆品等。
•知道物质在碱性环境中的耐受能力,有助于选择合适的材料和产品。
•耐碱试验标准提供了一种客观、标准化的方法来评估物质的性能。
常用的耐碱试验标准1.ASTM标准•ASTM G31:用于评估金属和非金属材料在碱性环境中的耐受性能。
•ASTM C289:评估水泥和混凝土等建筑材料的碱性耐受性。
2.ISO标准•ISO 695:用于评估非金属材料在饱和氢氧化钠溶液中的耐受性。
•ISO 2812-2:评估涂料和涂层在碱性环境中的耐受性。
3.国家标准•GB/T 2589:用于评估铅酸蓄电池在碱性条件下的耐受性。
•GB/T 17649:评估建筑材料在浓氢氧化钠溶液中的碱性耐受性。
如何进行耐碱试验1.准备样品•根据标准要求,制备符合规定的样品。
•样品的形态、尺寸和数量等应符合要求。
2.浸泡试验•将样品置于碱性溶液中浸泡一定时间。
•碱性溶液的浓度和温度应符合标准要求。
3.观察和评估•根据标准规定的方法和标准参考图表,观察样品的外观和性能变化。
•根据评估准则,对样品进行评分和评估。
耐碱试验标准的应用领域•建筑材料:评估砖块、水泥、玻璃等在碱性环境中的性能。
•化妆品:评估化妆品在碱性环境中的稳定性和耐受性。
•电子产品:评估电池、电路板等在碱性条件下的耐受性。
结论•耐碱试验标准是评估物质在碱性环境中耐受性能的重要参考。
•合适的耐碱试验标准可以提供可靠的数据,帮助选择适用的材料和产品。
以上是关于耐碱试验标准的简要介绍,通过遵循相关的标准和流程,我们可以更好地评估物质的耐受能力和适用性。
对于不同领域的应用,选择合适的耐碱试验标准是十分重要的。
astm g31 金属的实验室浸泡腐蚀标准

astm g31 金属的实验室浸泡腐蚀标准
ASTM G31是一组用于测试金属抗腐蚀性的标准试验方法。
这些测试方法可以用于评估材料的抗腐蚀能力,以确定其是否符合特定的使用要求。
ASTM G31标准分为以下两个部分:
第一部分是ASTM G31-72标准试验方法,用于测定锌铸件在腐蚀环境下的耐久性。
这项测试可用于评估锌铸件的使用寿命,并确定其是否符合特定的性能要求。
测试方法包括将锌铸件浸入腐蚀环境中,并根据时间和重量变化监测其耐久性。
第二部分是ASTM G31-72(2010)标准试验方法,用于测定镀层钢丝在腐蚀环境下的耐久性。
测试方法涉及在腐蚀环境中浸泡测试样品,并根据时间和重量变化监测其性能表现。
ASTM G31标准的实验室浸泡腐蚀试验可用于各种金属材料的测试。
结果可以帮助工程师和设计师了解材料的性能,并评估其在特定环境中的适用性。
它还可以为材料选择提供有用的数据,以确保选定的材料符合特定应用的要求。
总之,ASTM G31标准是测试金属抗腐蚀性能的重要标准。
使用这些测试方法,可以获取有用的数据,以帮助工程师和设计师选择符合特定应用要求的材料。
钛材耐腐蚀数据

钛材耐腐蚀数据钛材是一种具有优异耐腐蚀性能的金属材料,广泛应用于航空航天、化工、海洋工程等领域。
本文将详细介绍钛材的耐腐蚀数据,包括耐腐蚀性能测试方法、常见腐蚀介质下的腐蚀速率以及耐腐蚀性能评估标准等内容。
一、耐腐蚀性能测试方法1. 电化学测试法:电化学测试是评估钛材耐腐蚀性能的常用方法之一。
常见的电化学测试方法包括极化曲线法、交流阻抗法和电化学噪声法等。
通过测量钛材在不同电位下的电流密度和电化学参数,可以评估其耐腐蚀性能。
2. 加速腐蚀试验法:加速腐蚀试验是通过摹拟实际使用条件下的腐蚀环境,加快腐蚀速率以评估钛材的耐腐蚀性能。
常见的加速腐蚀试验方法包括盐雾试验、腐蚀热循环试验和腐蚀电流噪声法等。
二、常见腐蚀介质下的腐蚀速率1. 酸性介质下的腐蚀速率:钛材在酸性介质中具有较好的耐腐蚀性能。
以硫酸为例,钛材的腐蚀速率通常在0.1~0.5 mm/a范围内。
而在浓硝酸和盐酸等强酸介质中,钛材的腐蚀速率会进一步增加。
2. 碱性介质下的腐蚀速率:钛材在碱性介质中也具有一定的耐腐蚀性能。
以氢氧化钠为例,钛材的腐蚀速率通常在0.1~0.3 mm/a范围内。
但在浓氢氧化钠溶液中,钛材的腐蚀速率会显著增加。
3. 氯化物介质下的腐蚀速率:钛材对氯化物介质具有较好的耐腐蚀性能。
以氯化钠为例,钛材的腐蚀速率通常在0.1~0.3 mm/a范围内。
但在浓度较高的氯化钠溶液中,钛材的腐蚀速率会明显增加。
三、耐腐蚀性能评估标准1. ASTM标准:美国材料与试验协会(ASTM)制定了多个与钛材耐腐蚀性能评估相关的标准,如ASTM G31、ASTM G48和ASTM G61等。
这些标准包含了钛材的耐腐蚀性能测试方法、腐蚀速率评估和腐蚀性能等级划分等内容。
2. ISO标准:国际标准化组织(ISO)也制定了一些与钛材耐腐蚀性能评估相关的标准,如ISO 15510和ISO 18069等。
这些标准主要涵盖了钛材的化学成份要求、耐腐蚀性能测试方法和腐蚀性能等级划分等内容。
国外石化腐蚀标准与资料介绍
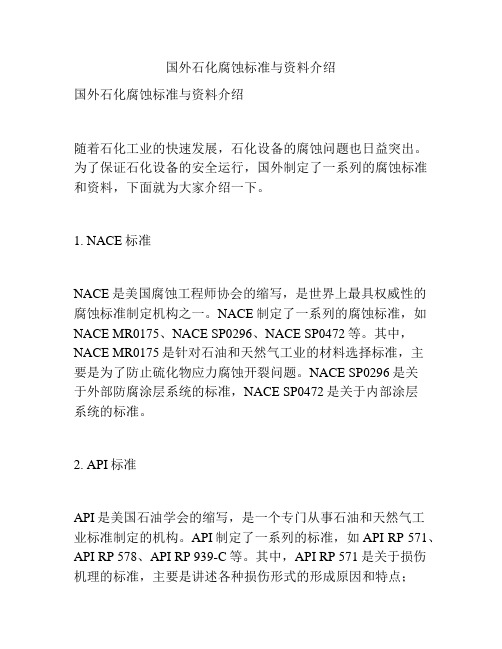
国外石化腐蚀标准与资料介绍国外石化腐蚀标准与资料介绍随着石化工业的快速发展,石化设备的腐蚀问题也日益突出。
为了保证石化设备的安全运行,国外制定了一系列的腐蚀标准和资料,下面就为大家介绍一下。
1. NACE标准NACE是美国腐蚀工程师协会的缩写,是世界上最具权威性的腐蚀标准制定机构之一。
NACE制定了一系列的腐蚀标准,如NACE MR0175、NACE SP0296、NACE SP0472等。
其中,NACE MR0175是针对石油和天然气工业的材料选择标准,主要是为了防止硫化物应力腐蚀开裂问题。
NACE SP0296是关于外部防腐涂层系统的标准,NACE SP0472是关于内部涂层系统的标准。
2. API标准API是美国石油学会的缩写,是一个专门从事石油和天然气工业标准制定的机构。
API制定了一系列的标准,如API RP 571、API RP 578、API RP 939-C等。
其中,API RP 571是关于损伤机理的标准,主要是讲述各种损伤形式的形成原因和特点;API RP 578是关于焊接人员资格认证的标准;API RP 939-C是关于材料选择和耐蚀性评估的标准。
3. ASTM标准ASTM是美国材料与试验协会的缩写,是一个从事材料和产品标准制定的机构。
ASTM制定了一系列的标准,如ASTM G1、ASTM G31、ASTM G48等。
其中,ASTM G1是关于化学分析和金相检查的标准;ASTM G31是关于电化学腐蚀测试方法的标准;ASTM G48是关于晶间腐蚀测试方法的标准。
4. ISO标准ISO是国际标准化组织的缩写,是一个从事国际标准制定的机构。
ISO制定了一系列的标准,如ISO 8501-1、ISO 8502-3、ISO 12944-5等。
其中,ISO 8501-1是关于表面清洁度等级的标准;ISO 8502-3是关于表面粗糙度测量方法的标准;ISO 12944-5是关于涂层系统设计和表面处理的标准。
astm g31 金属的实验室浸泡腐蚀标准

ASTM G31金属的实验室浸泡腐蚀标准引言ASTM G31是一项用于金属材料浸泡腐蚀实验的标准测试方法。
该方法可以评估金属在特定环境下的耐腐蚀性能,为金属材料的选型和工程设计提供参考。
本文将对ASTM G31标准进行全面、详细、完整且深入的探讨。
浸泡腐蚀实验概述浸泡腐蚀实验的目的•评估金属材料的耐腐蚀性能•确定金属在特定环境中的寿命•验证金属材料的性能是否符合设计要求实验参数浸泡腐蚀实验的参数包括: 1. 环境条件: - 温度 - 盐度 - pH值 - 氧化还原条件2.实验时间:–根据需求确定实验时间,通常为几天到几个月不等3.试样处理:–清洗–表面处理(去除氧化物、油污等)ASTM G31标准实验步骤实验装置设置合适的实验装置,包括: 1. 容器:用于装载试样和腐蚀介质 2. 温度控制装置:用于控制实验温度 3. 搅拌器:用于保持腐蚀介质的均匀性试样准备1.清洗试样:去除表面的污垢和油污2.表面处理:去除氧化物,保证试样表面光洁实验操作1.设置实验条件:包括温度、盐度、pH值等2.将试样放入容器中,并加入腐蚀介质3.开始实验计时4.定期观察试样的腐蚀情况,并记录数据5.根据实验要求确定实验终点6.取出试样,清洗并评估腐蚀情况7.分析实验数据,得出试样的腐蚀速率和寿命预估ASTM G31标准的参数和限制实验参数ASTM G31标准中对于实验参数的一些要求: 1. 温度范围:通常在常温至高温环境下进行实验 2. 盐度范围:根据特定应用需求设置 3. pH值范围:一般为酸性或碱性环境 4. 氧化还原条件:根据材料与介质的耦合效应设置实验结果ASTM G31标准对于实验结果的一些要求: 1. 腐蚀速率:根据实验数据计算得出,通常以mm/year作为单位 2. 寿命预估:根据腐蚀速率和实验时间推算材料的寿命3. 腐蚀形貌:通过观察试样表面得出,比如晶粒腐蚀、点蚀等实验限制ASTM G31标准的一些限制和注意事项: 1. 实验条件的选择应考虑实际工程和应用环境 2. 实验结果只能作为评估材料耐腐蚀性能的参考,并不代表实际使用寿命3. 对于复杂环境和特殊材料,可能需要进行额外的测试和分析 4. 实验过程需要严格控制,以避免意外或人为因素对实验结果的影响实验应用和意义ASTM G31标准适用于各种金属材料的腐蚀性能评估,具有以下应用和意义: 1. 材料选型:通过对不同金属材料的腐蚀性能测试,帮助工程师选择合适的材料 2. 制定工程设计规范:根据实验结果,制定相应的腐蚀防护措施 3. 增强产品质量控制:通过定期进行ASTM G31测试,保证产品的一致性和质量 4. 向用户提供技术支持:基于测试结果,提供金属材料的寿命预估和使用指导结论ASTM G31是一项用于金属材料浸泡腐蚀实验的标准测试方法。
astm 铜腐蚀率

astm 铜腐蚀率
ASTM(美国材料与试验协会)通常不提供特定的铜腐蚀率标准,但ASTM会发布一系列涉及金属和合金腐蚀测试的标准,这些标准可以用于评估不同材料的腐蚀性能。
铜腐蚀率通常用于测试液体或环境对金属的腐蚀程度。
一种常用的铜腐蚀率测试是ASTM G31标准,标题为"Standard Practice for Laboratory Immersion Corrosion Testing of Metals",通常用于评估金属在不同液体环境中的腐蚀性能。
ASTM G31标准提供了测试程序,可用于测量金属在特定液体中的腐蚀速率。
测试中通常会使用铜试片,将其与待测试材料暴露在一定的液体环境中,并测量一段时间后铜试片的腐蚀程度,以评估环境的腐蚀性。
另一个与铜腐蚀相关的ASTM标准是ASTM G1,标题为"Standard Practice for Preparing, Cleaning, and Evaluating Corrosion Test Specimens"。
该标准涵盖了制备和清洁腐蚀试样的程序,其中包括使用铜试片作为评估腐蚀性能的一部分。
请注意,ASTM标准通常需要购买或获取,因此如果需要详细的测试程序和规格,建议查阅相关ASTM标准文件或咨询ASTM的官方网站。
对于特定应用或要测试的具体情况,可能需要根据ASTM标准来设计和执行腐蚀测试。
化学液体对金属腐蚀的检测指标

化学液体对金属腐蚀的检测指标1、硫化氢应力腐蚀测试依据检测标准主要有:GB/T4157-2006《金属在硫化氢环境中抗特殊形式环境开裂实验室试验》SY/T 0599-2006《天然气地面设施抗硫化物应力开裂和抗应力腐蚀开裂的金属材料要求》NACE TM 0177-2016《金属在H2S环境中抗硫化物应力开裂和应力腐蚀》NACE MR 0175-2009《石油和天然气工业油、气生产中含硫化氢(H2S)环境下使用的材料耐裂化材料选择的一般原则》ISO 15156-1-2009《石油和天然气工业油、气生产中含硫化氢(H2S)环境下使用的材料耐裂化材料选择的一般原则》2、氢致开裂腐蚀试验依据检测标准主要有:GB/T 8650-2006管线钢和压力容器钢抗氢致开裂评定方法NACE TM 0284-2016管线钢和压力容器抗氢致开裂评定方法3、晶间腐蚀试验依据检测标准主要有:ASTM A763-93(R2009)不锈钢晶间腐蚀试验ASTM G28-02(2008) 煅制高镍铬轴承合金晶间腐蚀敏感性的检查用测试方法方法AGB/T21433-2008不锈钢压力容器晶间腐蚀敏感性检验GB/T 15260-1994镍基合金晶间腐蚀A法GB/T 26491-20115XXX系铝合金晶间腐蚀试验方法质量损失法GB/T 7998-2005铝合金晶间腐蚀测定方法ASTM G110-1992(2009)用浸入氯化钠+过氧化氢溶液的方法评定可热处理铝合金的晶间腐蚀ASTM G123-2000(2011)评定沸腾酸化氯化钠溶液中镍含量不同的不锈合金应力晶间腐蚀开裂4、盐雾腐蚀试验依据检测标准主要有:GB/T 10125人造气氛腐蚀试验盐雾试验GB/T 12967.3铝及铝合金阳极氧化膜检测方法第3部分:铜加速乙酸盐雾试验(CASS试验)GB/T 2423.18环境试验第2部分:试验方法试验Kb:盐雾,交变(氯化钠溶液)GB/T 1771色漆和清漆耐中性盐雾性能的测定GB/T 2423.17电工电子产品环境试验第2部分: 试验方法试验Ka:盐雾5、气体腐蚀试验依据检测标准主要有:GB/T 5170.11-2008 电工电子产品环境试验设备检验方法腐蚀气体试验设备GB/T2423.51-2000 电工电子产品(试验Ke)流动混合气体腐蚀试验方法IEC 60068-2-60-1995环境试验第2-60部分:试验试验Ke:流动混合气体腐蚀试验ISO 16750-4-2006电气和电子装备的环境条件和试验-气候环境EIA-364-65A-1997电连器进行混合气体腐蚀试验GB2423.51-2000电工电子产品环境试验ASTM B845-97(2008)混合流动气体腐蚀测试6、模拟工矿腐蚀依据检测标准主要有:GB/T 25147-2010 工业设备化学清洗中金属腐蚀率及腐蚀总量的测试方法重量法JB/T 7901-2001 金属材料实验室均匀腐蚀全浸试验方法ASTM G111-1997(2013)标准导则腐蚀试验在高温和高压环境,或者两者7、点腐蚀试验依据检测标准主要有:GB/T 17897-2016 金属和合金的腐蚀不锈钢三氯化铁点腐蚀试验方法JIS G 0578-2000不锈钢的氯化铁腐蚀试验方法点腐蚀预防MH/T 6102-2014 化学处理致飞机金属晶间腐蚀和端面晶粒点蚀的试验方法ASTM G48 method A 不锈钢点蚀电位测量方法8、氢剥离试验依据检测标准主要有:ASTM G146-2001(2013)高压高温精炼氢设备用双金属不锈合金/钢板剥离性评定规程9、沸腾氯化镁应力腐蚀开裂试验依据检测标准主要有:ASTM G 36-2006不锈钢在沸腾氯化镁溶液中应力腐蚀试验方法GB/T 17898-1999 不锈钢在沸腾氯化镁溶液中应力腐蚀试验方法YB/T 5362-2006 不锈钢在沸腾氯化镁溶液中应力腐蚀试验方法GB/T 15970.5-1995 金属和合金的腐蚀应力腐蚀试验第5部分:C型环试样的制备和应用GB/T 15970.3-1995金属和合金的腐蚀应力腐蚀试验第3部分:U型弯曲试样的制备和应用10、黄铜耐脱锌腐蚀试验依据检测标准主要有:GB/T 10119黄铜耐脱锌腐蚀性能的测定ISO 6509 铜合金锌脱锌性的测定 - 金属和合金的腐蚀第1部分:试验方法AS 2345 澳大利亚铜合金脱锌性11、醋酸盐雾腐蚀试验依据检测标准主要有:GB/T 10125-2012 人造气氛腐蚀试验盐雾试验ISO 9227-2012 人造气氛腐蚀试验盐雾试验JIS Z2371-2015 盐雾试验方法ASTM G85-2011 改性盐雾(雾)测试规程AS 2331.3.2-2001 金属及其相关镀层的试验方法第3.2部分:腐蚀性及其相关属性试验 .醋酸盐喷雾试验12、涂层浸渍腐蚀试验依据检测标准主要有:ASTM D 870-2009 水浸渍法测试涂层的耐水性能的标准实施规程ISO 21809-3-2016 石油和天然气工业--管道输送系统中使用的地下或水下管道的外部涂层--第3部分:安装接头涂层SY/T 0315-2013 钢质管道单层熔结环氧粉末外涂层技术规范13、全浸腐蚀试验依据检测标准主要有:JB/T 6073-1992 金属覆盖层实验室全浸腐蚀试验ASTM G31-2012a 金属的实验室浸渍腐蚀试验HB 5194-1981 周期浸润腐蚀试验方法GB 10124-1988 金属材料实验室均匀腐蚀全浸试验方法JB/T 7901-1999 金属材料实验室均匀腐蚀全浸试验方法14、电腐蚀试验依据检测标准主要有:GB/T 15748-2013 船用金属材料电偶腐蚀试验方法NACE TM0175-2009附录B 油田设备用抗硫化应力裂纹的金属材料。
周期性浸泡腐蚀试验标准及相关设备分析

周期性浸泡腐蚀试验标准及相关设备分析魏艳娟;陈利钦;顾佳伟【摘要】Based on the complexity of the product transportation and the use environment, the simulation of single environmental factors can’t meet the requirements of product testing. Solution immersion corrosion test is a common environmental test. At present, in addition to the single solution immersion, the periodic immersion corrosion test is gradually carried out. In this regard, GB, TB, ISO, PSA, ASTM and other related standards are given the requirements and test methods. On these basis, in order to meet the requirements, the corresponding test device has gradually begun to develop and application. In this paper, based on the different standards and present equipment, the periodic immersion corrosion test is analyzed and discussed, obtaining the applicable scope and test conditions of each standards and putting forward the prospect of developing universal equipment according to the generality of the principle, providing reference for the selection of immersion corrosion test standards and the development of test equipments.%基于产品运输、使用环境的复杂性,单一环境因素模拟已不能满足产品测试需求。
- 1、下载文档前请自行甄别文档内容的完整性,平台不提供额外的编辑、内容补充、找答案等附加服务。
- 2、"仅部分预览"的文档,不可在线预览部分如存在完整性等问题,可反馈申请退款(可完整预览的文档不适用该条件!)。
- 3、如文档侵犯您的权益,请联系客服反馈,我们会尽快为您处理(人工客服工作时间:9:00-18:30)。
Designation:G31–72(Reapproved2004)Standard Practice forLaboratory Immersion Corrosion Testing of Metals1This standard is issued under thefixed designation G31;the number immediately following the designation indicates the year of original adoption or,in the case of revision,the year of last revision.A number in parentheses indicates the year of last reapproval.A superscript epsilon(e)indicates an editorial change since the last revision or reapproval.1.Scope1.1This practice2describes accepted procedures for and factors that influence laboratory immersion corrosion tests, particularly mass loss tests.These factors include specimen preparation,apparatus,test conditions,methods of cleaning specimens,evaluation of results,and calculation and reporting of corrosion rates.This practice also emphasizes the impor-tance of recording all pertinent data and provides a checklist for reporting test data.Other ASTM procedures for laboratory corrosion tests are tabulated in the Appendix.(Warning—In many cases the corrosion product on the reactive metals titanium and zirconium is a hard and tightly bonded oxide that defies removal by chemical or ordinary mechanical means.In many such cases,corrosion rates are established by mass gain rather than mass loss.)1.2The values stated in SI units are to be regarded as the standard.The values given in parentheses are for information only.1.3This standard does not purport to address all of the safety concerns,if any,associated with its use.It is the responsibility of the user of this standard to establish appro-priate safety and health practices and determine the applica-bility of regulatory limitations prior to use.2.Referenced Documents2.1ASTM Standards:3A262Practices for Detecting Susceptibility to Intergranu-lar Attack in Austenitic Stainless SteelsE8Test Methods for Tension Testing of Metallic Materials G1Practice for Preparing,Cleaning,and Evaluating Cor-rosion Test SpecimensG4Guide for Conducting Corrosion Coupon Tests in Field ApplicationsG16Guide for Applying Statistics to Analysis of Corrosion DataG46Guide for Examination and Evaluation of Pitting Corrosion3.Significance and Use3.1Corrosion testing by its very nature precludes complete standardization.This practice,rather than a standardized pro-cedure,is presented as a guide so that some of the pitfalls of such testing may be avoided.3.2Experience has shown that all metals and alloys do not respond alike to the many factors that affect corrosion and that “accelerated”corrosion tests give indicative results only,or may even be entirely misleading.It is impractical to propose an inflexible standard laboratory corrosion testing procedure for general use,except for material qualification tests where standardization is obviously required.3.3In designing any corrosion test,consideration must be given to the various factors discussed in this practice,because these factors have been found to affect greatly the results obtained.4.Interferences4.1The methods and procedures described herein represent the best current practices for conducting laboratory corrosion tests as developed by corrosion specialists in the process industries.For proper interpretation of the results obtained,the specific influence of certain variables must be considered. These include:4.1.1Metal specimens immersed in a specific hot liquid may not corrode at the same rate or in the same manner as in equipment where the metal acts as a heat transfer medium in heating or cooling the liquid.If the influence of heat transfer effects is specifically of interest,specialized procedures(in which the corrosion specimen serves as a heat transfer agent) must be employed(1).44.1.2In laboratory tests,the velocity of the environment relative to the specimens will normally be determined by convection currents or the effects induced by aeration or boiling or both.If the specific effects of high velocity are to be studied,special techniques must be employed to transfer the1This practice is under the jurisdiction of ASTM Committee G01on Corrosion of Metals and is the direct responsibility of Subcommittee G01.05on Laboratory Corrosion Tests.Current edition approved May1,2004.Published May2004.Originally approved st previous edition approved in1998as G31–72(1998).2This practice is based upon NACE Standard TM-01-69,“Test Method-Laboratory Corrosion Testing of Metals for the Process Industries,”with modifica-tions to relate more directly to Practices G1and G31and Guide G4.3For referenced ASTM standards,visit the ASTM website,,or contact ASTM Customer Service at service@.For Annual Book of ASTMStandards volume information,refer to the standard’s Document Summary page on the ASTM website.4The boldface numbers in parentheses refer to the list of references at the end of this practice.1Copyright©ASTM International,100Barr Harbor Drive,PO Box C700,West Conshohocken,PA19428-2959,United States.environment through tubular specimens or to move it rapidly past the plane face of a corrosion coupon(2).Alternatively,the coupon may be rotated through the environment,although it is then difficult to evaluate the velocity quantitatively because of the stirring effects incurred.4.1.3The behavior of certain metals and alloys may be profoundly influenced by the presence of dissolved oxygen.If this is a factor to be considered in a specific test,the solution should be completely aerated or deaerated in accordance with 8.7.4.1.4In some cases,the rate of corrosion may be governed by other minor constituents in the solution,in which case they will have to be continually or intermittently replenished by changing the solution in the test.4.1.5Corrosion products may have undesirable effects on a chemical product.The amount of possible contamination can be estimated from the loss in mass of the specimen,with proper application of the expected relationships among(1)the area of corroding surface,(2)the mass of the chemical product handled,and(3)the duration of contact of a unit of mass of the chemical product with the corroding surface.4.1.6Corrosion products from the coupon may influence the corrosion rate of the metal itself or of different metals exposed at the same time.For example,the accumulation of cupric ions in the testing of copper alloys in intermediate strengths of sulfuric acid will accelerate the corrosion of copper alloys,as compared to the rates that would be obtained if the corrosion products were continually removed.Cupric ions may also exhibit a passivating effect upon stainless steel coupons ex-posed at the same time.In practice,only alloys of the same general type should be exposed in the testing apparatus.4.1.7Coupon corrosion testing is predominantly designed to investigate general corrosion.There are a number of other special types of phenomena of which one must be aware in the design and interpretation of corrosion tests.4.1.7.1Galvanic corrosion may be investigated by special devices which couple one coupon to another in electrical contact.The behavior of the specimens in this galvanic couple are compared with that of insulated specimens exposed on the same holder and the galvanic effects noted.It should be observed,however,that galvanic corrosion can be greatly affected by the area ratios of the respective metals,the distance between the metals and the resistivity of the electrolyte.The coupling of corrosion coupons then yields only qualitative results,as a particular coupon reflects only the relationship between these two metals at the particular area ratio involved.4.1.7.2Crevice corrosion or concentration cell corrosion may occur where the metal surface is partially blocked from the corroding liquid as under a spacer or supporting hook.It is necessary to evaluate this localized corrosion separately from the overall mass loss.4.1.7.3Selective corrosion at the grain boundaries(for example,intergranular corrosion of sensitized austenitic stain-less steels)will not be readily observable in mass loss measurements unless the attack is severe enough to cause grain dropping,and often requires microscopic examination of the coupons after exposure.4.1.7.4Dealloying or“parting”corrosion is a condition in which one constituent is selectively removed from an alloy,as in the dezincification of brass or the graphitization of cast iron. Close attention and a more sophisticated evaluation than a simple mass loss measurement are required to detect this phenomenon.4.1.7.5Certain metals and alloys are subject to a highly localized type of attack called pitting corrosion.This cannot be evaluated by mass loss alone.The reporting of nonuniform corrosion is discussed below.It should be appreciated that pitting is a statistical phenomenon and that the incidence of pitting may be directly related to the area of metal exposed.For example,a small coupon is not as prone to exhibit pitting as a large one and it is possible to miss the phenomenon altogether in the corrosion testing of certain alloys,such as the AISI Type 300series stainless steels in chloride contaminated environ-ments.4.1.7.6All metals and alloys are subject to stress-corrosion cracking under some circumstances.This cracking occurs under conditions of applied or residual tensile stress,and it may or may not be visible to the unaided eye or upon casual inspection.A metallographic examination may confirm the presence of stress-corrosion cracking.It is imperative to note that this usually occurs with no significant loss in mass of the test coupon,although certain refractory metals are an exception to these observations.Generally,if cracking is observed on the coupon,it can be taken as positive indication of susceptibility, whereas failure to effect this phenomenon simply means that it did not occur under the duration and specific conditions of the test.Separate and special techniques are employed for the specific evaluation of the susceptibility of metals and alloys to stress corrosion cracking(see Ref.(3)).5.Apparatus5.1A versatile and convenient apparatus should be used, consisting of a kettle orflask of suitable size(usually500to 5000mL),a reflux condenser with atmospheric seal,a sparger for controlling atmosphere or aeration,a thermowell and temperature-regulating device,a heating device(mantle,hot plate,or bath),and a specimen support system.If agitation is required,the apparatus can be modified to accept a suitable stirring mechanism,such as a magnetic stirrer.A typical resin flask setup for this type test is shown in Fig.1.5.2The suggested components can be modified,simplified, or made more sophisticated tofit the needs of a particular investigation.The suggested apparatus is basic and the appa-ratus is limited only by the judgment and ingenuity of the investigator.5.2.1A glass reaction kettle can be used where the configu-ration and size of the specimen will permit entry through the narrow kettle neck(for example,45/50ground-glass joint).For solutions corrosive to glass,suitable metallic or plastic kettles may be employed.5.2.2In some cases a wide-mouth jar with a suitable closure is sufficient when simple immersion tests at ambient tempera-tures are to be investigated.5.2.3Open-beaker tests should not be used because of evaporation andcontamination.5.2.4In more complex tests,provisions might be needed for continuous flow or replenishment of the corrosive liquid,while simultaneously maintaining a controlled atmosphere.6.Sampling6.1The bulk sampling of products is outside the scope of this practice.7.Test Specimen7.1In laboratory tests,uniform corrosion rates of duplicate specimens are usually within 610%under the same test conditions.Occasional exceptions,in which a large difference is observed,can occur under conditions of borderline passivityof metals or alloys that depend on a passive film for their resistance to corrosion.Therefore,at least duplicate specimens should normally be exposed in each test.7.2If the effects of corrosion are to be determined by changes in mechanical properties,untested duplicate speci-mens should be preserved in a noncorrosive environment at the same temperature as the test environment for comparison with the corroded specimens.The mechanical property commonly used for comparison is the tensile strength.Measurement of percent elongation is a useful index of embrittlement.The procedures for determining these values are shown in detail in Test Methods E 8.7.3The size and shape of specimens will vary with the purpose of the test,nature of the materials,and apparatus used.A large surface-to-mass ratio and a small ratio of edge area to total area are desirable.These ratios can be achieved through the use of square or circular specimens of minimum thickness.Masking may also be used to achieve the desired area ratios but may cause crevice corrosion problems.Circular specimens should preferably be cut from sheet and not bar stock,to minimize the exposed end grain.Special coupons (for example,sections of welded tubing)may be employed for specific purposes.7.3.1A circular specimen of about 38-mm (1.5-in.)diam-eter is a convenient shape for laboratory corrosion tests.With a thickness of approximately 3mm (0.125-in.)and an 8-mm (5⁄16-in.)or 11-mm (7⁄16-in.)diameter hole for mounting,these specimens will readily pass through a 45/50ground-glass joint of a distillation kettle.The total surface area of a circular specimen is given by the following equation:A 5p /2~D 22d 2!1t p D 1t p d(1)where:t =thickness,D =diameter of the specimen,and d =diameter of the mounting hole.7.3.1.1If the hole is completely covered by the mounting support,the last term (t p d )in the equation is omitted.7.3.2Strip coupons 50by 25by 1.6or 3mm (2by 1by 1⁄16or 1⁄8in.)may be preferred as corrosion specimens,particularly if interface or liquid line effects are to be studied by the laboratory tests (see Fig.1),but the evaluation of such specific effects are beyond the scope of this practice.7.3.3All specimens should be measured carefully to permit accurate calculation of the exposed areas.A geometric area calculation accurate to 61%is usually adequate.7.4More uniform results may be expected if a substantial layer of metal is removed from the specimens to eliminate variations in condition of the original metallic surface.This can be done by chemical treatment (pickling),electrolytic removal,or by grinding with a coarse abrasive paper or cloth such as No.50,using care not to work harden the surface (see section 5.7).At least 0.0025mm (0.0001in.)or 0.0155to 0.0233mg/mm 2(10to 15mg/in.2)should be removed.(If clad alloy specimens are to be used,special attention must be given to ensure that excessive metal is not removed.)After final preparation of the specimen surface,the specimens should be stored in a desic-cator until exposure,if they are not used immediately.In special cases (for example,for aluminum and certain copper alloys),a minimum of 24h storage in a desiccator is recom-mended.The choice of a specific treatment must be considered on the basis of the alloy to be tested and the reasons for testing.A commercial surface may sometimes yield the most signifi-cant results.Too much surface preparation may remove segre-gated elements,surface contamination,and so forth,and therefore not be representative.7.5Exposure of sheared edges should be avoided unless the purpose of the test is to study effects of the shearing operation.It may be desirable to test a surface representative of the material and metallurgical conditions used in practice.N OTE 1—The flask can be used as a versatile and convenient apparatus to conduct simple immersion tests.Configuration of top to flask is such that more sophisticated apparatus can be added as required by the specific test being conducted.A =thermowell,B =resin flask,C =specimens hung on supporting device,D =air inlet,E =heating mantle,F =liquid inter-face,G =opening in flask for additional apparatus that may be required,and H =reflux condenser.FIG.1Typical Resin Flask7.6The specimen can be stamped with an appropriate identifying mark.If metallic contamination of the stamped area may influence the corrosion behavior,chemical cleaning must be employed to remove any traces of foreign particles from the surface of the coupon(for example,by immersion of stainless steel coupons in dilute nitric acid following stamping with steel dies).7.6.1The stamp,besides identifying the specimen,intro-duces stresses and cold work in the specimen that could be responsible for localized corrosion or stress-corrosion crack-ing,or both.7.6.2Stress-corrosion cracking at the identifying mark is a positive indication of susceptibility to such corrosion.How-ever,the absence of cracking should not be interpreted as indicating resistance(see4.1.7.6).7.7Final surface treatment of the specimens should include finishing with No.120abrasive paper or cloth or the equiva-lent,unless the surface is to be used in the millfinished condition.This resurfacing may cause some surface work hardening,to an extent which will be determined by the vigor of the surfacing operation,but is not ordinarily significant.The surfacefinish to be encountered in service may be more appropriate for some testing.7.7.1Coupons of different alloy compositions should never be ground on the same cloth.7.7.2Wet grinding should be used on alloys which work harden quickly,such as the austenitic stainless steels.7.8The specimens should befinally degreased by scrubbing with bleach-free scouring powder,followed by thorough rins-ing in water and in a suitable solvent(such as acetone, methanol,or a mixture of50%methanol and50%ether),and air dried.For relatively soft metals(such as aluminum, magnesium,and copper),scrubbing with abrasive powder is not always needed and can mar the surface of the specimen. Proper ultrasonic procedures are an acceptable alternate.The use of towels for drying may introduce an error through contamination of the specimens with grease or lint.7.9The dried specimens should be weighed on an analytical balance to an accuracy of at least60.5mg.If cleaning deposits (for example,scouring powder)remain or lack of complete dryness is suspected,then recleaning and drying is performed until a constant mass is attained.7.10The method of specimen preparation should be de-scribed when reporting test results,to facilitate interpretation of data by other persons.7.11The use of welded specimens is sometimes desirable, because some welds may be cathodic or anodic to the parent metal and may affect the corrosion rate.7.11.1The heat-affected zone is also of importance but should be studied separately,because welds on coupons do not faithfully reproduce heat input or size effects of full-size weldments.7.11.2Corrosion of a welded coupon is best reported by description and thickness measurements rather than a millime-tre per year(mils per year)rate,because the attack is normally localized and not representative of the entire surface.7.11.3A complete discussion of corrosion testing of welded coupons or the effect of heat treatment on the corrosion resistance of a metal is not within the scope of this practice.8.Test Conditions8.1Selection of the conditions for a laboratory corrosion test will be determined by the purpose of the test.8.1.1If the test is to be a guide for the selection of a material for a particular purpose,the limits of the controlling factors in service must be determined.These factors include oxygen concentration,temperature,rate offlow,pH value,composi-tion,and other important characteristics of the solution.8.2An effort should be made to duplicate all pertinent service conditions in the corrosion test.8.3It is important that test conditions be controlled through-out the test in order to ensure reproducible results.8.4The spread in corrosion rate values for duplicate speci-mens in a given test probably should not exceed610%of the average when the attack is uniform.8.5Composition of Solution:8.5.1Test solutions should be prepared accurately from chemicals conforming to the Specifications of the Committee on Analytical Reagents of the American Chemical Society5and distilled water,except in those cases where naturally occurring solutions or those taken directly from some plant process are used.8.5.2The composition of the test solutions should be controlled to the fullest extent possible and should be described as completely and as accurately as possible when the results are reported.8.5.2.1Minor constituents should not be overlooked be-cause they often affect corrosion rates.8.5.2.2Chemical content should be reported as percentage by weight of the solutions.Molarity and normality are also helpful in defining the concentration of chemicals in some test solutions.8.5.3If problems are suspected,the composition of the test solutions should be checked by analysis at the end of the test to determine the extent of change in composition,such as might result from evaporation or depletion.8.5.4Evaporation losses may be controlled by a constant level device or by frequent addition of appropriate solution to maintain the original volume within61%.Preferably,the use of a reflux condenser ordinarily precludes the necessity of adding to the original kettle charge.8.5.5In some cases,composition of the test solution may change as a result of catalytic decomposition or by reaction with the test coupons.These changes should be determined if possible.Where required,the exhausted constituents should be added or a fresh solution provided during the course of the test.8.5.6When possible,only one type of metal should be exposed in a given test(see4.1.6).5Reagent Chemicals,American Chemical Society Specifications,American Chemical Society,Washington,DC.For suggestions on the testing of reagents not listed by the American Chemical Society,see Analar Standards for Laboratory Chemicals,BDH Ltd.,Poole,Dorset,U.K.,and the United States Pharmacopeia and National Formulary,U.S.Pharmacopeial Convention,Inc.(USPC),Rockville,MD.8.6Temperature of Solution :8.6.1Temperature of the corroding solution should be controlled within 61°C (61.8°F)and must be stated in the report of test results.8.6.2If no specific temperature,such as boiling point,is required or if a temperature range is to be investigated,the selected temperatures used in the test,and their respective duration,must be reported.8.6.3For tests at ambient temperature,the tests should be conducted at the highest temperature anticipated for stagnant storage in summer months.This temperature may be as high as from 40to 45°C (104to 113°F)in some areas.The variation in temperature should be reported also (for example,4062°C).8.7Aeration of Solution :8.7.1Unless specified,the solution should not be aerated.Most tests related to process equipment should be run with the natural atmosphere inherent in the process,such as the vapors of the boiling liquid.8.7.2If aeration is employed,the specimen should not be located in the direct air stream from the sparger.Extraneous effects can be encountered if the air stream impinges on the specimens.8.7.3If exclusion of dissolved oxygen is necessary,specific techniques are required,such as prior heating of the solution and sparging with an inert gas (usually nitrogen).A liquid atmospheric seal is required on the test vessel to prevent further contamination.8.7.4If oxygen saturation of the test solution is desired,this can best be achieved by sparging with oxygen.For other degrees of aeration,the solution should be sparaged with air or synthetic mixtures of air or oxygen with an inert gas.Oxygen saturation is a function of the partial pressure of oxygen in the gas.8.8Solution Velocity :8.8.1The effect of velocity is not usually determined in normal laboratory tests,although specific tests have been designed for this purpose.8.8.2Tests at the boiling point should be conducted with the minimum possible heat input,and boiling chips should be used to avoid excessive turbulence and bubble impingement.8.8.3In tests below the boiling point,thermal convection generally is the only source of liquid velocity.8.8.4In test solutions with high viscosity,supplemental controlled stirring with a magnetic stirrer is recommended.8.9Volume of Test Solution :8.9.1The volume of the test solution should be large enough to avoid any appreciable change in its corrosivity during the test,either through exhaustion of corrosive constituents or by accumulation of corrosion products that might affect further corrosion.8.9.2Two examplesof a minimum “solution volume-tospecimen area”ratio are 0.20mL/mm 2(125mL/in.2)of specimen surface (Practice A 262),and 0.40mL/mm 2(250mL/in.2).8.9.3When the test objective is to determine the effect of a metal or alloy on the characteristics of the test solution (for example,to determine the effects of metals on dyes),it is desirable to reproduce the ratio of solution volume to exposedmetal surface that exists in practice.The actual time of contact of the metal with the solution must also be taken into account.Any necessary distortion of the test conditions must be considered when interpreting the results.8.10Method of Supporting Specimens :8.10.1The supporting device and container should not be affected by or cause contamination of the test solution.8.10.2The method of supporting specimens will vary with the apparatus used for conducting the test,but should be designed to insulate the specimens from each other physically and electrically and to insulate the specimens from any metallic container or supporting device used within the apparatus.8.10.3Shape and form of the specimen support should assure free contact of the specimen with the corroding solution,the liquid line,or the vapor phase as shown in Fig.1.If clad alloys are exposed,special procedures will be required to ensure that only the cladding is exposed,unless the purpose is to test the ability of the cladding to protect cut edges in the test solution.8.10.4Some common supports are glass or ceramic rods,glass saddles,glass hooks,fluorocarbon plastic strings,and various insulated or coated metallic supports.8.11Duration of Test :8.11.1Although duration of any test will be determined by the nature and purpose of the test,an excellent procedure for evaluating the effect of time on corrosion of the metal and also on the corrosiveness of the environment in laboratory tests has been presented by Wachter and Treseder (4).This technique is called the “planned interval test,”and the procedure and evaluation of results are given in Table 1.Other procedures that require the removal of solid corrosion products between exposure periods will not measure accurately the normal changes of corrosion with time.8.11.2Materials that experience severe corrosion generally do not ordinarily need lengthy tests to obtain accurate corro-sion rates.However,there are cases where this assumption is not valid.For example,lead exposed to sulfuric acid corrodes at an extremely high rate at first,while building a protective film;then the rates decrease considerably so that further corrosion is negligible.The phenomenon of forming a protec-tive film is observed with many corrosion-resistant materials.Therefore,short tests on such materials would indicate a high corrosion rate and be completely misleading.8.11.3Short-time tests also can give misleading results on alloys that form passive films,such as stainless steels.With borderline conditions,a prolonged test may be needed to permit breakdown of the passive film and subsequent more rapid attack.Consequently,tests run for long periods are considerably more realistic than those conducted for short durations.This statement must be qualified by stating that corrosion should not proceed to the point where the original specimen size or the exposed area is drastically reduced or where the metal is perforated.8.11.4If anticipated corrosion rates are moderate or low,the following equation gives the suggested test duration:Hours 52000/~corrosion rate in mpy !(2)。