发动机部件计算公式
机油泵吸油高度计算公式
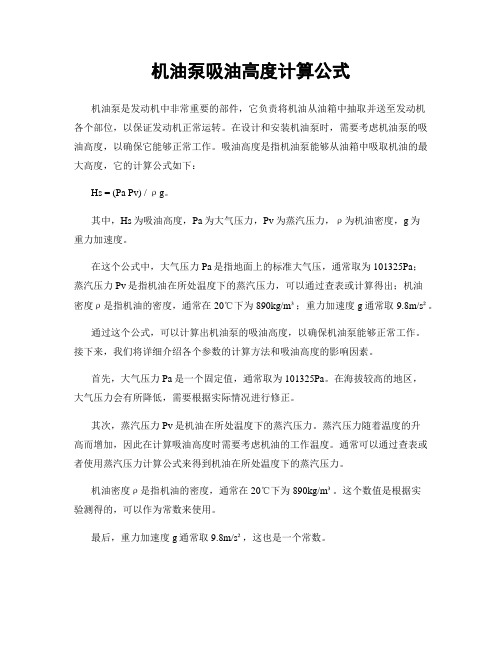
机油泵吸油高度计算公式机油泵是发动机中非常重要的部件,它负责将机油从油箱中抽取并送至发动机各个部位,以保证发动机正常运转。
在设计和安装机油泵时,需要考虑机油泵的吸油高度,以确保它能够正常工作。
吸油高度是指机油泵能够从油箱中吸取机油的最大高度,它的计算公式如下:Hs = (Pa Pv) / ρg。
其中,Hs为吸油高度,Pa为大气压力,Pv为蒸汽压力,ρ为机油密度,g为重力加速度。
在这个公式中,大气压力Pa是指地面上的标准大气压,通常取为101325Pa;蒸汽压力Pv是指机油在所处温度下的蒸汽压力,可以通过查表或计算得出;机油密度ρ是指机油的密度,通常在20℃下为890kg/m³;重力加速度g通常取9.8m/s²。
通过这个公式,可以计算出机油泵的吸油高度,以确保机油泵能够正常工作。
接下来,我们将详细介绍各个参数的计算方法和吸油高度的影响因素。
首先,大气压力Pa是一个固定值,通常取为101325Pa。
在海拔较高的地区,大气压力会有所降低,需要根据实际情况进行修正。
其次,蒸汽压力Pv是机油在所处温度下的蒸汽压力。
蒸汽压力随着温度的升高而增加,因此在计算吸油高度时需要考虑机油的工作温度。
通常可以通过查表或者使用蒸汽压力计算公式来得到机油在所处温度下的蒸汽压力。
机油密度ρ是指机油的密度,通常在20℃下为890kg/m³。
这个数值是根据实验测得的,可以作为常数来使用。
最后,重力加速度g通常取9.8m/s²,这也是一个常数。
通过以上公式和参数的计算,可以得到机油泵的吸油高度。
吸油高度的大小直接影响着机油泵的工作效果,如果吸油高度过大,机油泵可能无法正常工作,导致发动机缺油;如果吸油高度过小,机油泵可能会过度劳累,影响机油泵的使用寿命。
因此,在设计和安装机油泵时,需要根据实际情况计算吸油高度,并选择合适的机油泵。
除了上述公式外,还有一些其他因素会影响机油泵的吸油高度,例如管道的长度、管道的直径、管道的弯曲程度等。
活塞高度怎么计算公式

活塞高度怎么计算公式活塞是内燃机中的重要部件,它的高度对发动机的性能有很大影响。
因此,计算活塞高度是非常重要的。
活塞高度的计算公式可以帮助工程师们更好地设计发动机,提高其性能和效率。
活塞高度是指活塞顶部到活塞底部的距离,通常用来描述活塞的长度。
活塞高度的计算公式可以通过以下步骤来确定:步骤一,测量活塞的直径。
首先,需要测量活塞的直径。
活塞的直径是指活塞的宽度,通常是活塞顶部的最宽处的直径。
这个测量值将用于计算活塞高度。
步骤二,测量活塞的行程。
活塞的行程是指活塞在气缸内上下运动的距离。
通常是指从活塞顶部到活塞底部的距离。
这个值也将用于计算活塞高度。
步骤三,计算活塞高度。
活塞高度的计算公式为:活塞高度 = 行程 2 曲轴偏距活塞销高度。
其中,行程是指活塞在气缸内上下运动的距离,曲轴偏距是指曲轴中心线到活塞销中心线的距离,活塞销高度是指活塞销的高度。
通过这个公式,可以得到活塞的准确高度。
这个值将有助于工程师们更好地设计发动机,提高其性能和效率。
活塞高度的计算对于发动机设计和性能优化非常重要。
通过准确计算活塞高度,可以更好地了解发动机的工作原理,提高其性能和效率。
因此,活塞高度的计算公式是非常有用的工具,可以帮助工程师们更好地设计和优化发动机。
除了计算活塞高度,工程师们还需要考虑其他因素,如活塞材料、活塞环设计等。
这些因素都对发动机的性能和效率有很大影响。
因此,活塞高度的计算只是发动机设计中的一个方面,工程师们还需要综合考虑其他因素,才能设计出性能更好的发动机。
总之,活塞高度的计算公式是发动机设计中的重要工具,可以帮助工程师们更好地了解发动机的工作原理,提高其性能和效率。
通过准确计算活塞高度,可以更好地设计和优化发动机,为汽车工业的发展做出贡献。
发动机转子轴向力计算公式

发动机转子轴向力计算公式在工程学和机械设计中,发动机是一个非常重要的部件,它通过燃烧燃料来产生动力,驱动车辆或者机械设备。
在发动机的设计和运行过程中,轴向力是一个重要的参数,它影响着发动机的稳定性和工作效率。
因此,准确计算发动机转子轴向力是非常重要的。
发动机转子轴向力是指发动机转子在轴向方向上的受力情况,它是由发动机内部燃烧过程和机械运动所产生的。
在发动机设计和运行过程中,需要准确计算和控制轴向力,以确保发动机的稳定性和安全性。
为了计算发动机转子轴向力,可以使用以下公式:F = m a。
在这个公式中,F代表轴向力,m代表转子的质量,a代表转子的加速度。
通过这个公式,可以计算出发动机转子在轴向方向上的受力情况。
在实际应用中,需要考虑到转子的惯性、燃烧产生的气体压力和机械运动所产生的力等因素,以得到准确的轴向力值。
在实际工程中,计算发动机转子轴向力需要考虑到多种因素,包括转子的几何形状、材料特性、转速、燃烧压力、机械运动等。
因此,需要综合考虑这些因素,进行精确的计算和分析。
除了上述公式外,还可以使用其他方法来计算发动机转子轴向力。
例如,可以通过有限元分析来模拟发动机内部的燃烧过程和机械运动,以得到轴向力的准确数值。
此外,还可以通过实验方法来测量发动机转子的轴向力,以验证计算结果的准确性。
在实际工程中,准确计算发动机转子轴向力对于发动机的设计和性能优化非常重要。
通过准确的轴向力计算,可以优化发动机的结构设计,提高发动机的工作效率和稳定性,减少发动机的振动和噪音,延长发动机的使用寿命。
总之,发动机转子轴向力是影响发动机性能和稳定性的重要参数,准确计算和控制轴向力对于发动机的设计和运行非常重要。
通过合理的计算和分析,可以优化发动机的设计和性能,提高发动机的工作效率和稳定性,为工程实践提供重要的参考依据。
发动机部件计算公式

发动机部件计算公式发动机是汽车的核心部件,其性能直接影响到汽车的动力和燃油效率。
发动机由众多部件组成,如气缸、活塞、连杆、曲轴等。
在设计和制造发动机时,需要考虑各个部件之间的相互作用,以确保发动机的可靠性和性能。
1.气缸计算公式:气缸是发动机内燃过程的基本装置,其尺寸的选取对发动机的燃烧效率和动力特性有重要影响。
气缸计算公式包括气缸直径D和气缸行程S的选择。
气缸直径的选择与气缸的功率和转速有关,一般情况下,功率越大、转速越高,气缸直径就越大。
气缸行程的选择主要与发动机的转速在一定范围内有关。
行程较长有利于提高发动机的扭矩和低速性能,行程较短则有利于提高转速和高速性能。
计算公式如下:气缸直径(D)=(C/π)^(1/2)气缸行程(S)=2.2~2.5D其中C为发动机的歧管容积,π为圆周率。
2.活塞计算公式:活塞是发动机的运动部件,其结构和尺寸的设计直接影响到发动机的输出功率和燃油效率。
活塞计算公式主要包括活塞直径D、活塞行程H和活塞活塞冠高度的选择。
活塞直径的选择与发动机的功率、转速和气缸直径有关。
一般情况下,活塞直径与气缸直径之间取一个适当的比例,如1.3~1.6活塞行程的选择与发动机的功率和转速有关,一般情况下,行程较短有利于提高发动机的转速,行程较长有利于提高低速性能。
活塞冠高度的选择与发动机的燃烧室形状和燃油的喷射方式有关。
3.连杆计算公式:连杆是发动机的运动部件,其结构和尺寸的设计直接影响到发动机的输出功率和燃油效率。
连杆长度的选择与发动机的功率和转速有关,一般情况下,连杆长度与发动机的行程之间取一个适当的比例,如2.0~2.5连杆小头直径和连杆大头直径的选择与发动机的功率和气缸直径有关。
连杆角度和连杆挠曲的计算需要考虑到发动机的转速和挠曲的限制。
4.曲轴计算公式:曲轴是发动机的运动部件,其结构和尺寸的设计直接影响到发动机的输出功率和燃油效率。
曲轴主轴的直径和偏心量的选择与发动机的功率和转速有关。
发动机压缩比计算
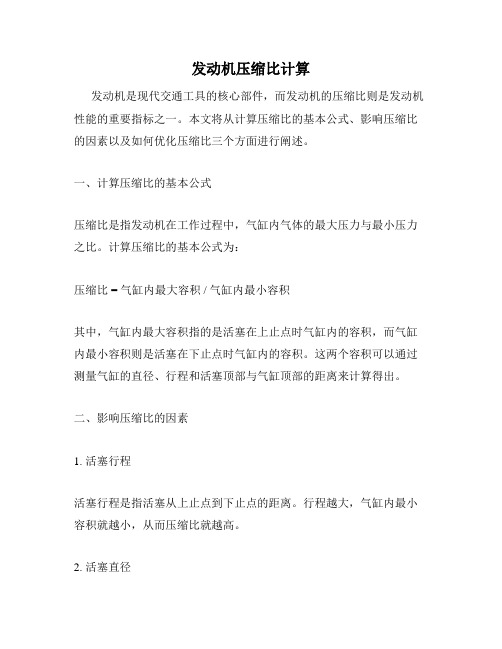
发动机压缩比计算发动机是现代交通工具的核心部件,而发动机的压缩比则是发动机性能的重要指标之一。
本文将从计算压缩比的基本公式、影响压缩比的因素以及如何优化压缩比三个方面进行阐述。
一、计算压缩比的基本公式压缩比是指发动机在工作过程中,气缸内气体的最大压力与最小压力之比。
计算压缩比的基本公式为:压缩比 = 气缸内最大容积 / 气缸内最小容积其中,气缸内最大容积指的是活塞在上止点时气缸内的容积,而气缸内最小容积则是活塞在下止点时气缸内的容积。
这两个容积可以通过测量气缸的直径、行程和活塞顶部与气缸顶部的距离来计算得出。
二、影响压缩比的因素1. 活塞行程活塞行程是指活塞从上止点到下止点的距离。
行程越大,气缸内最小容积就越小,从而压缩比就越高。
2. 活塞直径活塞直径是指活塞的直径大小。
直径越大,气缸内最大容积就越大,从而压缩比就越低。
3. 活塞顶部与气缸顶部的距离活塞顶部与气缸顶部的距离是指活塞在上止点时与气缸顶部的距离。
距离越小,气缸内最大容积就越小,从而压缩比就越高。
4. 气门开闭时间气门开闭时间是指气门开启和关闭的时间。
气门开启时间越长,气缸内的气体就越充分,从而压缩比就越高。
三、如何优化压缩比1. 改变活塞行程通过改变活塞行程,可以调整气缸内最小容积的大小,从而改变压缩比。
但是,改变行程需要重新设计发动机,成本较高。
2. 改变活塞直径通过改变活塞直径,可以调整气缸内最大容积的大小,从而改变压缩比。
但是,改变直径也需要重新设计发动机,成本较高。
3. 调整气门开闭时间通过调整气门开闭时间,可以让气缸内的气体更充分地进出,从而改变压缩比。
但是,调整气门开闭时间需要对发动机进行调整,成本较高。
综上所述,发动机的压缩比是影响发动机性能的重要指标之一。
通过计算压缩比的基本公式,我们可以了解到压缩比的计算方法。
同时,我们也可以通过改变活塞行程、直径和气门开闭时间等方式来优化压缩比,从而提高发动机的性能。
活塞速度公式

活塞速度公式活塞速度公式是在物理学和机械工程领域中一个挺重要的概念。
咱们先来说说啥是活塞速度。
想象一下汽车发动机里的活塞,它在气缸里上上下下地运动,这个运动的快慢就用活塞速度来描述。
活塞速度的快慢可关系到发动机的性能好坏呢。
活塞速度公式其实就是用来计算活塞在单位时间内移动的距离。
公式是:活塞速度 = 2 ×行程 ×转速 ÷ 60 。
这里面的“行程”就是活塞从一端到另一端移动的距离,“转速”就是活塞每分钟上下运动的次数。
我记得有一次去汽车修理厂,看到师傅们在检修发动机。
他们就特别关注活塞速度这个指标。
当时有一辆车总是动力不足,师傅们就通过测量和计算活塞速度,来判断是不是活塞运动出了问题。
他们拿着工具,仔细测量行程,然后查看发动机的转速数据,最后代入活塞速度公式进行计算。
我在旁边看着,心里那叫一个好奇。
这个公式在实际应用中用处可大啦。
比如说在设计新的发动机时,工程师们就得根据想要达到的性能指标,利用这个公式来确定活塞的行程和转速等参数。
要是活塞速度太快,可能会加剧磨损,影响发动机寿命;要是太慢呢,又发挥不出发动机的最大功率。
而且不仅仅是汽车发动机,像一些其他的机械设备,只要有类似活塞运动的部件,都可能会用到这个公式来进行分析和优化。
再比如说,在一些工业生产线上,某些机器的运转也涉及到类似的原理。
通过控制类似活塞运动的部件的速度,来保证生产的效率和质量。
总之,活塞速度公式虽然看起来简单,就那么几个参数,但是它背后蕴含的原理和应用可是非常广泛和重要的。
无论是在机械制造、工业生产,还是在我们日常生活中接触到的各种设备中,都有着不可或缺的作用。
希望通过我这一番不太专业但还算通俗的讲解,能让您对活塞速度公式有个初步的了解和认识。
活塞环外径尺寸计算公式

活塞环外径尺寸计算公式活塞环是内燃机中的重要部件,它的尺寸对发动机的性能和寿命有着重要的影响。
其中,活塞环的外径尺寸是一个关键参数,它直接影响着活塞环与气缸壁之间的密封性能和摩擦特性。
因此,合理计算活塞环外径尺寸是非常重要的。
在本文中,我们将介绍活塞环外径尺寸的计算公式及其影响因素。
活塞环外径尺寸计算公式的一般形式如下:D = B + 2H 0.02。
其中,D为活塞环的外径尺寸,B为气缸内径,H为活塞环的厚度。
这个公式是根据活塞环与气缸壁之间的密封原理和摩擦特性推导出来的。
下面我们将详细解释这个公式中各个参数的含义和影响因素。
首先是气缸内径B。
气缸内径是活塞环外径尺寸计算中最重要的参数之一。
它直接决定了活塞环与气缸壁之间的接触面积和密封性能。
一般来说,气缸内径越大,活塞环外径尺寸也会相应增大,以保证良好的密封性能。
同时,气缸内径的大小还会影响活塞环与气缸壁之间的摩擦特性,过大或过小的气缸内径都会导致摩擦增大或密封不良。
其次是活塞环的厚度H。
活塞环的厚度是活塞环外径尺寸计算中另一个重要的参数。
活塞环的厚度直接影响着活塞环的刚度和强度,从而影响活塞环与气缸壁之间的密封性能和摩擦特性。
一般来说,活塞环的厚度越大,活塞环外径尺寸也会相应增大,以保证活塞环的刚度和强度。
同时,活塞环的厚度还会影响活塞环与气缸壁之间的摩擦特性,过厚或过薄的活塞环都会导致摩擦增大或密封不良。
最后是0.02这个修正系数。
这个修正系数是根据实际使用情况和经验修正得到的。
一般来说,这个修正系数是一个负值,它是为了考虑到活塞环在高温、高压环境下的膨胀和变形。
通过这个修正系数,可以更准确地计算活塞环的外径尺寸,以保证活塞环在各种工况下都能保持良好的密封性能和摩擦特性。
通过以上分析,我们可以看到活塞环外径尺寸的计算公式是一个综合考虑了气缸内径、活塞环厚度和修正系数等多种因素的复杂公式。
在实际应用中,我们需要根据具体的发动机类型、工作条件和使用要求来确定这些参数的数值,以保证活塞环能够在各种工况下都能保持良好的密封性能和摩擦特性。
活塞平衡杆扭矩计算公式
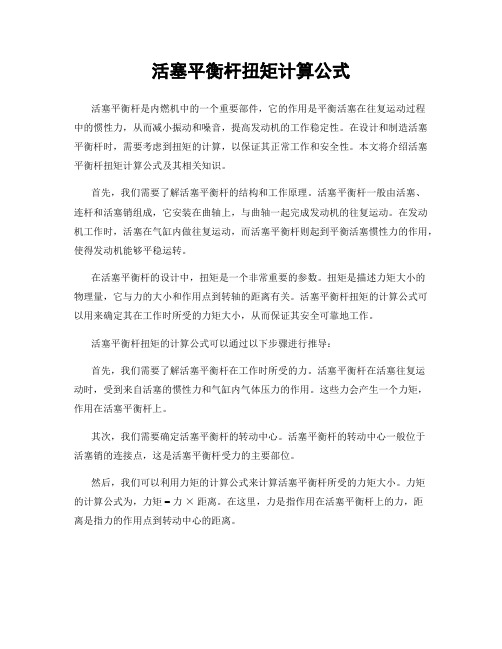
活塞平衡杆扭矩计算公式活塞平衡杆是内燃机中的一个重要部件,它的作用是平衡活塞在往复运动过程中的惯性力,从而减小振动和噪音,提高发动机的工作稳定性。
在设计和制造活塞平衡杆时,需要考虑到扭矩的计算,以保证其正常工作和安全性。
本文将介绍活塞平衡杆扭矩计算公式及其相关知识。
首先,我们需要了解活塞平衡杆的结构和工作原理。
活塞平衡杆一般由活塞、连杆和活塞销组成,它安装在曲轴上,与曲轴一起完成发动机的往复运动。
在发动机工作时,活塞在气缸内做往复运动,而活塞平衡杆则起到平衡活塞惯性力的作用,使得发动机能够平稳运转。
在活塞平衡杆的设计中,扭矩是一个非常重要的参数。
扭矩是描述力矩大小的物理量,它与力的大小和作用点到转轴的距离有关。
活塞平衡杆扭矩的计算公式可以用来确定其在工作时所受的力矩大小,从而保证其安全可靠地工作。
活塞平衡杆扭矩的计算公式可以通过以下步骤进行推导:首先,我们需要了解活塞平衡杆在工作时所受的力。
活塞平衡杆在活塞往复运动时,受到来自活塞的惯性力和气缸内气体压力的作用。
这些力会产生一个力矩,作用在活塞平衡杆上。
其次,我们需要确定活塞平衡杆的转动中心。
活塞平衡杆的转动中心一般位于活塞销的连接点,这是活塞平衡杆受力的主要部位。
然后,我们可以利用力矩的计算公式来计算活塞平衡杆所受的力矩大小。
力矩的计算公式为,力矩 = 力×距离。
在这里,力是指作用在活塞平衡杆上的力,距离是指力的作用点到转动中心的距离。
最后,我们可以将活塞平衡杆所受的力矩与其设计要求进行比较,以确定其是否满足工作条件。
如果所受力矩超过了设计要求,就需要重新设计活塞平衡杆的结构或材料,以保证其安全可靠地工作。
除了上述的计算公式外,活塞平衡杆扭矩的计算还需要考虑到一些其他因素,如活塞平衡杆的材料、工作温度、转速等。
这些因素都会对活塞平衡杆的扭矩产生影响,因此在实际工程中需要综合考虑这些因素,进行准确的扭矩计算。
在活塞平衡杆的设计和制造过程中,扭矩的计算是一个非常重要的环节。
- 1、下载文档前请自行甄别文档内容的完整性,平台不提供额外的编辑、内容补充、找答案等附加服务。
- 2、"仅部分预览"的文档,不可在线预览部分如存在完整性等问题,可反馈申请退款(可完整预览的文档不适用该条件!)。
- 3、如文档侵犯您的权益,请联系客服反馈,我们会尽快为您处理(人工客服工作时间:9:00-18:30)。
附录1 发动机部件计算公式1 基础知识1)空气、燃气的焓、熵公式见附录2。
2)气动函数()q λ、()πλ、τλ()、()f λ计算公式见附录3。
2 变循环发动机各部件的计算公式2.1 进气道2.1.1 已知:发动机飞行高度H 、飞行马赫数Ma 。
2.1.2 计算过程1)计算标准大气条件下环境压力0p (静压),环境温度0T (静温)。
当高度H km ≤11时:5.2553001.01325144.308288.15 6.5H p T H ⎧⎛⎫=⨯-⎪ ⎪⎨⎝⎭⎪=-⨯⎩ (2.1) 其中,高度H 的单位为km ,温度的单位为K ,压力的单位为bar 。
2)进气道进口的总温总压:2020 T T Ma p p Ma γγγγ*-*⎧-⎛⎫=+ ⎪⎪⎝⎭⎪⎨-⎪⎛⎫=+ ⎪⎪⎝⎭⎩10112112 (2.2) γ:气体绝热指数,纯空气=1.4γ,燃气=1.33γ。
3)计算进气道总压恢复系数:i 1.35i 1 1.01 1.00.075(1)H H H M M M σσ≤=⎧⎨>=--⎩:: (2.3) 4)计算进气道出口总温总压:iT T p p σ****⎧=⎨=⋅⎩1010(2.4) 2.2 压气机双涵道变循环发动机中三个压气机部件,分别是风扇、CDFS 和高压压气机,这三个压气机部件采用同一种计算法。
2.2.1 已知压气机进口总温T in *、总压P in *、压气机的压比函数值zz 、物理转速n 、压气机导叶角度α。
2.2.2 计算过程1)计算压气机换算转速:cor n = (2.5)其中,风扇:*,=288.15in d T ,CDFS :*,=428.56862609in d T ,高压压气机:*, 473.603961in d T =。
*in T 为压气机进口总温。
2)计算压气机增压比、效率和换算流量压气机的增压比c pr 、效率c η和换算流量c W 分别是其换算转速和压比函数值及导叶角α的函数。
(,,)(,,) (,,)c cor c cor ccor pr prc n zz n zz W W n zz αηηαα=⎧⎪=⎨⎪=⎩ (2.6) 压气机增压比、效率和换算流量的求法如下:(1) 附录4分别给出了风扇、CDFS,高压压气机的特性数据。
利用线性插值法计算出压气机的换算转速为cor n 、压比函数值为zz 时的特性图上的增压比,c map pr 、效率,c mapη和换算流量,c map W 。
(2) 将(1)求的特性图上的增压比,c map pr 、效率,c map η和换算流量,c map W 代入(2.7)修正后得到压气机的增压比、效率和换算流量:,,2,(1)(1)1100(1) 100(1) 100pr cpr c map w c W c map c c map k pr C pr k W C W k C ηηααηηα⎧=-++⎪⎪⎪=+⎨⎪⎪=+⎪⎩(2.7) pr w k k k η、、分别是增压比、效率和换算流量的修正系数。
风扇、CDFS 、高压压气机pr w k k k η、、这三个值均分别取1,1,0.01; CDFS 导叶角变化围:-535α≤≤,风扇和高压压气机的导叶角变化围:-515α≤≤ ;风扇: 2.3894=0.4950 1.0684pr W C C C η=⎧⎪⎨⎪=⎩,CDFS:0.30590.15001.0999pr W C C C η=⎧⎪=⎨⎪=⎩,高压压气机: 0.91190.38462 1.0719pr W C C C η=⎧⎪=⎨⎪=⎩。
3)计算压气机出口参数压气机出口总压:**out in c p p pr =⋅;计算进口熵:*()in in T ψψ=,进口焓:*()in in h h T =;压气机出口理想熵:,ln out ei in c Rpr Mψψ=+,这里1=M ,R 是气体常数; 由压气机出口理想熵*,()out ei T ψψ=out,ei ,计算压气机出口理想总温:*,out ei T ; 计算压气机出口理想焓:*,,()out ei out ei h h T =; 根据公式,out ei in c out inh h h h η-=-计算压气机出口焓out h ;由压气机出口焓*()out out h h T =求压气机出口总温:*out T ;计算压气机流量:**,ina c in dp W W p = (2.8) 其中,风扇:*,=1.01325in d p ,CDFS :*,= 3.5464in d p ,高压压气机:*, 4.8860in d p =;计算压气机功和功率:c out inc a cl h h N W l =-⎧⎨=⋅⎩ (2.9) 2.3 主燃烧室2.3.1 已知主燃烧室进口总温*3in T 、总压*3in p 、空气流量3a in W 、主燃烧室出口温度*4T 。
2.3.2 计算过程1)根据公式433b b u h h f H h ξ-=+求出主燃烧室出口油气比,其中,3h 和4h 分别主燃烧室进出口焓,燃烧效率=0.99b ξ,燃油热值=42900000u H ;2)燃油流量3f a b W W f =⋅;3)出口总压**43in b p p σ=,主燃烧室总压恢复系数=0.98b σ。
2.4 涡轮2.4.1 已知:涡轮进口总温*in T 、总压*in p 、涡轮的压比函数值zz 、物理转速n 、涡轮导叶角度α。
2.4.2 计算过程1)求涡轮换算转速cor n = (2.10)其中,高压涡轮:*,=1850in d T ,低压涡轮:*,= 1.5405e+003in d T 。
涡轮的增压比c pr 、效率c η和换算流量c W 分别是其换算转速和压比函数值及导叶角α的函数。
(,,)(,,) (,,)c cor c cor ccor pr prc n zz n zz W W n zz αηηαα=⎧⎪=⎨⎪=⎩ (2.11) 2)涡轮的增压比、效率和换算流量的求法如下:(1) 附录4分别给出了高压涡轮、低压涡轮的特性数据。
利用线性插值法计算出涡轮的换算转速为cor n 、压比函数值为zz 时的特性图上的增压比,c map pr 、效率,c map η和换算流量,c map W 。
(2) 将(1)求的特性图上的增压比,c map pr 、效率,c map η和换算流量,c map W 代入(2.12)修正后得到涡轮的增压比、效率和换算流量:,,2,(1)(1)1100(1) 100(1) 100pr cpr c map w c W c mapc c map k pr C pr k W C W k C ηηααηηα⎧=-++⎪⎪⎪=+⎨⎪⎪=+⎪⎩(2.12) pr w k k k η、、分别是涡轮增压比、效率和换算流量的修正系数。
高压涡轮、低压涡轮pr w k k k η、、这三个值均分别取1,1,0.01;高、低压涡轮导叶角变化围:-515α≤≤ ;高压涡轮: 1.534213.21211.0121pc W C C C η=⎧⎪=⎨⎪=⎩,低压涡轮:0.79020.38811.0061pr W C C C η=⎧⎪=⎨⎪=⎩。
3)根据涡轮换算流量计算涡轮流量:**,ing in dp W W p =c (2.13) 其中,高压涡轮:*,=28.7297in d p ,低压涡轮:*,=11.3371in d p 。
4)涡轮出口总压**/out in c p p pr =;5)涡轮出口总温*out T 根据下面公式(2.14)求出。
/**11/Cp Rout c in T pr T η-⎡⎤⎛⎫=--⎢⎥⎪⎝⎭⎣⎦c (2.14)其中:高压涡轮平均等压比热 1.2988e+003CP =,低压涡轮平均等压比热1.2745e+003CP =, R 为气体常数。
6)求涡轮进口焓*(,)in in b h h T f =,其中b f 为涡轮进口油气比;7)求涡轮出口焓*(,)out out b h h T f =;8)涡轮功和功率:T in out Tg T m l h h N W l η=-⎧⎪⎨=⋅⎪⎩ (2.15)其中,=0.99m η为涡轮机械效率.2.5 涵道2.5.1 已知涵道进口总温*in T 、总压*in p 、流量,a in W 、总压恢复系数duct σ。
2.5.2 计算过程****,,out in out in duct a out a in T T p p WW σ⎧=⎪=⎨⎪=⎩, 其中总压恢复系数0.98duct σ=。
2.6 前混合器,选择活门,副外涵道建模图1包含模式选择活门、副外涵道及CDFS 涵道,高压压气机等。
图1 变循环发动机局部简图图中数字序号表示发动机各截面参数定义的下脚标2.6.1 已知混合器两股参混气流参混前的总温、总压,副外涵、CDFS 涵道出口面积和CDFS 涵道出口流量。
2.6.2 计算过程在已经给定副外涵、CDFS 涵道出口面积的情况下, 1)CDFS涵道气流根据流量公式*125125125()g mW k A q λ=求出125()q λ和125λ,其中CDFS 涵道出口面积125= 608.4252A ,*125p 为CDFS 涵道出口总压,*125T 为CDFS 涵道出口总温,气动函数()q λ的定义及流量系数m k 的取值见附录3;2)由*125125125()p p πλ=⋅求出CDFS 涵道出口静压125p ;3)由前混合器静压平衡225125p p =和*225225225p p πλ=⋅(),求出225πλ()和225λ,*225p 为副外涵道出口总压;4)由流量公式*225225225()g mW k A q λ=计算出副外涵道出口的流量。
其中副外涵面积(选择活门面积)225=1.8395e+003A , *225T 为副外涵出口总温,m k 为流量系数见附录3;5)由下列公式(2.16)求出前混合器出口总温*15T 、总压*15p 、流量15g W 。
*15T 是由(2.16)的第二个公式求出的。
225125152252251251251515***225225225125125125151522512515()()()()g g g g g g g W W W W h W h W h p f A P f A p f A A W λλλ+=+=+=+*1515()m k A q λ⎧⎪⎪⎪⎨⎪⎪=⎪⎩(2.16) 其中:15225125A A A =+,15h 为前混合器出口焓,125h 为前混合器CDFS 涵道出口焓,225h 为前混合器副外涵出口焓,225g W 为前混合器副外涵出口流量,125g W 为前混合器CDFS 涵道出口流量,气动函数()f λ、()q λ的定义见附录3。