4 金属塑性成形中的摩擦
金属塑性成形中的摩擦

三、边界摩擦 1.边界摩擦:介于干摩擦与流体摩擦之间的摩擦 边界摩擦: 边界摩擦 状态。 状态。 2.机理 机理 当坯料与工、模具间存在润滑物质时, 当坯料与工、模具间存在润滑物质时,随着 接触表面上压力的增加,坯料表面的部分“凸峰” 接触表面上压力的增加,坯料表面的部分“凸峰” 被压平,润滑剂或形成一层薄膜残留在接触面间, 被压平,润滑剂或形成一层薄膜残留在接触面间, 或被挤入附近“凹谷” 或被挤入附近“凹谷”,这时在挤去润滑剂的部 分出现金属间的接触,即发生粘着现象。 分出现金属间的接触,即发生粘着现象。 这时的摩擦力就是剪断表面粘着部分的剪切 抗力与边界膜分子间抗剪力之和。 抗力与边界膜分子间抗剪力之和。 在生产中,这三种摩擦状态不是截然分开的, 在生产中,这三种摩擦状态不是截然分开的,常 常会出现混摩擦状态。 常会出现混摩擦状态。
8.3 摩擦系数及其影响因素 一、摩擦系数 金属塑性成形中的摩擦系数, 金属塑性成形中的摩擦系数,通常是指工具与坯料接 触表面上的平均摩擦系数。 触表面上的平均摩擦系数。 根据库仑定律,摩擦系数可表达如下: 根据库仑定律,摩擦系数可表达如下:
T τ µ= = N σN 式中
或
τ = µσ N
τ − − 接触表面上的剪应力( 摩擦应力) 接触表面上的剪应力( 摩擦应力) σ N − 接触表面上的正压应力
二、流体摩擦 1.流体摩擦:被加工金属与工模具之间被润滑油 流体摩擦: 流体摩擦 膜所隔开时的摩擦。 膜所隔开时的摩擦。 2.机理 机理 润滑油膜将两摩擦面完全隔开, 润滑油膜将两摩擦面完全隔开,使得两摩擦面在 相互运动中不产生直接接触, 相互运动中不产生直接接触,摩擦发生在流体内 部分子之间。摩擦力的大小取决于流体的粘度、 部分子之间。摩擦力的大小取决于流体的粘度、 速度梯度等因素,因而流体摩擦的摩擦系数很小。 速度梯度等因素,因而流体摩擦的摩擦系数很小。
金属塑性加工的摩擦与润滑

=m·k 式中,m为摩擦因子
§4.4 摩擦系数及其影响因素
摩擦系数随金属性质、工艺条件、表面状态、单位压力及 所采用润滑剂的种类与性能等而不同。其主要影响因素有:
1 .金属的种类和化学成分 2.工具材料及其表面状态 3. 接触面上的单位压力 4 .变形温度 5.变形速度 6 .润滑剂
3. 圆环镦粗法
此法较简单,不需测定压力,也不 需制备许多压头和试件。可测定各 种温度、速度条件下的摩擦系数, 应用广泛。但由于圆环试件在镦粗 时会出现鼓形。环孔出现椭圆形等, 引起测量上的误差,影响结果的精 确性。
塑性加工常用摩擦系数 ➢热锻时的摩擦系数
材料 45 钢
锻铝
坯料温度 (℃) 1000 1200
§4.5 测定摩擦系数的方法
➢ 夹钳轧制法 ➢ 楔形件压缩法 ➢ 圆环镦粗法
1. 夹钳 h
k
简单易做,也比较精确,可用来测定冷、热态下的摩擦系数。
2. 楔形件压缩法
(L'c L"c ) 2
(L'c L"c )
与轧制过程及一般的平锤下镦粗相似,应用较方便,主要困难是在 于较难准确的确定中立面的位置及精确的测定有关数据。
的乳液为什么具有良好的润滑作用?
四. 润滑剂中的添加剂 润滑油中的添加剂,一般应易溶于机油,热稳定性要好, 且应具有良好的物理化学性能。 常用的添加剂有油性剂、极压剂、抗磨剂和防锈剂等。
五. 润滑方法的改进 1.流体润滑 2.表面处理 (1)表面磷化处理 (2)表面氧化处理 (3)表面镀层
作业
1.金属塑性加工的接触摩擦有哪些主要特点?对加工过 程有何影响和作用?
金属塑性成形原理---第四章 金属塑性成形中的摩擦_

4.6 塑性成形中的润滑
润滑是减少摩擦对塑性成形过程不良影响的最有效 措施。润滑的目的是:
1. 降低接触面间的摩擦力; 2. 提高模具寿命; 3. 提高产品质量; 4. 降低变形抗力; 5. 提高金属充满模膛的能力
一·塑性成形中对对润滑剂的要求 1. 良好的耐压性能 2. 良好的耐热性能 3. 冷却模具 4. 无腐蚀作用 5. 无毒 6. 使用、清理方便、来源丰富、价格便宜
金属塑性成形原理---第四章 中摩擦的分类和机理
一·塑性成形中摩擦的分类 干摩擦、边界摩擦、流体摩擦
二 摩擦机理
1 .表面凹凸学说 2 .分子吸附学说 3 .粘着理论
4.3 描述接触表面上摩擦力的数学表达式
一.库伦摩擦条件
不考虑接触面上的粘贴现象,以为摩擦符合库伦 定律,即摩擦力与接触面上的正压力成正比,其数 学表达式为
二·塑性成形中常用的润滑剂
三·润滑剂中的添加剂
四·塑性成形时的润滑方法
拉拔时流体强制润滑
4.7不同塑性成形条件下的摩擦系数
见课本157页表
金属质点向中心方向流动,该面以外的金属
质点向外流动,变形后使圆环内径缩小,外 径扩大,而且,分流面半径 Rn 随摩擦系数 的增大而增大。
摩擦系数很小或为零时对金属 流动的影像动态图
摩擦系数大于某临界值时对金属 流动的影像动态图
在圆环镦粗试验之前,必须根据
圆环原始尺寸和变形后可能达到 的尺寸,利用圆环镦粗变形理论 公式(求中性层位置),绘制出 镦粗后圆环高度 h 和内径 di 与 接触面摩擦因子 m 的关系曲线, 即为理论校准曲线。
❖在热塑性变形时常采用该模型
4.4 影响摩擦系数的主要因素
一.金属的种类和化学成分
4金属塑形加工中的摩擦与润滑
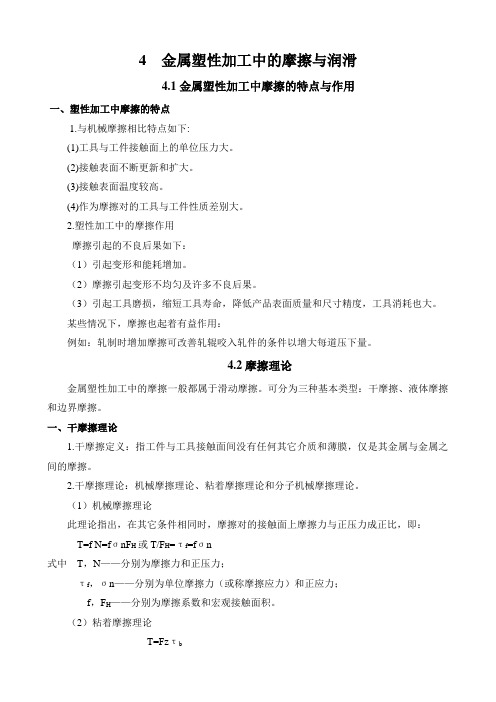
4 金属塑性加工中的摩擦与润滑4.1金属塑性加工中摩擦的特点与作用一、塑性加工中摩擦的特点1.与机械摩擦相比特点如下:(1)工具与工件接触面上的单位压力大。
(2)接触表面不断更新和扩大。
(3)接触表面温度较高。
(4)作为摩擦对的工具与工件性质差别大。
2.塑性加工中的摩擦作用摩擦引起的不良后果如下:(1)引起变形和能耗增加。
(2)摩擦引起变形不均匀及许多不良后果。
(3)引起工具磨损,缩短工具寿命,降低产品表面质量和尺寸精度,工具消耗也大。
某些情况下,摩擦也起着有益作用:例如:轧制时增加摩擦可改善轧辊咬入轧件的条件以增大每道压下量。
4.2摩擦理论金属塑性加工中的摩擦一般都属于滑动摩擦。
可分为三种基本类型:干摩擦、液体摩擦和边界摩擦。
一、干摩擦理论1.干摩擦定义:指工件与工具接触面间没有任何其它介质和薄膜,仅是其金属与金属之间的摩擦。
2.干摩擦理论:机械摩擦理论、粘着摩擦理论和分子机械摩擦理论。
(1)机械摩擦理论此理论指出,在其它条件相同时,摩擦对的接触面上摩擦力与正压力成正比,即:T=f N=fσnF H或T/F H=τf=fσn式中T,N——分别为摩擦力和正压力;τf,σn——分别为单位摩擦力(或称摩擦应力)和正应力;f,F H——分别为摩擦系数和宏观接触面积。
(2)粘着摩擦理论T=Fzτ b式中Fz——粘着点处的实际剪切面积;τb——较软金属的剪切强度。
(3)分子—机械摩擦理论此理论认为摩擦是即要克服摩擦对的分子相互作用力,又要克服机械变形阻力的混合过程,即T=αFzβN或f=αFz/N+β式中α,β——分别是与表面分子特性和机械特性有关的参数。
二、液体摩擦理论1.液体摩擦定义:工具与工件的接触面间被润滑油完全隔开,两表面的相对滑动阻力只与液体的性质和速度梯度有关,而与接触面状态无关时,这种摩擦称为液体摩擦。
2.液体动压润滑理论(1)液体摩擦定律各流层因相对运动而产生的摩擦力称为内摩擦力。
此内摩擦力Tt 与层间接触面积S及相对速度dv成正比,而与层间距离dz成反比,即Tt=ηs dvdz或τt=TtS=ηdvdz式中τt,η——分别为层间切应力和液体粘度;dvdz——流速梯度。
圆环压缩法测定金属塑性成形的摩擦系数实验报告·

圆环压缩法测定金属塑性成形的摩擦系数实验报告一、实验目的(1)了解金属塑性成形中的摩擦特点和影响; (2)熟悉摩擦对于金属流动影响的一般规律;(3)掌握用圆环法测定金属成形中摩擦系数的原理和方法。
二、概述金属塑性成形过程中,工具与变形金属接触面上存在相对运动或有相对运动的趋势时,其接触表面之间必然产生摩擦。
塑性成形中的摩擦与机械传动中的摩擦相比,接触压力较高,会产生新的接触面,并且大多是在较高的温度下产生的。
金属塑性成形时,摩擦在少数情况下会起到积极的作用,可以利用摩擦阻力来控制金属流动的方向。
但在大多数情况下摩擦是十分有害的,主要表现在改变了变形金属的应力状态,增大了变形抗力;引起不均匀变形,产生附加应力和残余应力;降低模具的寿命等。
为了减轻摩擦引起的种种不良影响,常采用润滑剂来降低摩擦。
因此对金属塑性成形过程中的摩擦和润滑机理的深入了解能大大提高生产效益和产品质量。
金属材料体积成形与金属板料面积成形的摩擦机理有差别。
圆环压缩法是20世纪60年代提出的一种利用圆环镦粗时的变形来测定摩擦系数的方法,可用于确定金属材料体积成形中锻造成形时的摩擦系数和评定润滑剂的润滑效果。
该方法是把一定尺寸的圆环试样(如0::20:10:7D d H =)放在平砧上镦粗。
由于试样和砧面间接触摩擦系数的不同,圆环的内、外径在压缩过程中将有不同的变化。
在任何摩擦情况下,外径总是增大的,而内径则随摩擦系数μ而变化,或增大或缩小。
当接触面上的摩擦系数很小时,圆环上每一金属质点均沿径向作辐射状向外流动,变形后的圆环内外径均扩大,如图6-1(a)所示。
当接触面上的摩擦系数增大到某一临界值后,靠近内径处的金属质点向内流动的阻力小于向外流动的阻力,从而改变了流动方向,这时在圆环中出现一个半径为n R 的分流面,该面以内的金属质点向中心方向流动,该面以外的金属质点向外流动,变形后的圆环内径缩小,外径扩大,如图6-1(b)所示。
图6-1 圆环压缩时的金属流动用上限法或应力分析法可以求出分流面半径n R 、摩擦系数μ和圆环尺寸的理论关系式。
金属塑性成形时的摩擦系数测量技术

此方法 的优点 ,是板 材试件 的变形状 态及 摩擦状态 与实 际拉深状况的非常接 近 ,能够分别 测量出板材在不 同拉 深状
态 下 的摩 擦 系数 。
22 基 于板材拉延 的摩 擦系数测量方法 。 李 东升等提 出了一 种基于板材拉延成 型的摩擦系数测量 方 法( 图 5所示嘲 。 如 ) 首先 , 将试件放到合适位置后 , 用夹 头和 动夹头将试件 的两端夹 紧 , 左右布置 的凸模 、 凹模将试件 中部
系数 测 量 技 术 的发 展 趋 势 。
关键词 : }成形 ; 塑l 生 摩擦 系数 ; 测量技术
中 图 分 类 号 : G3 1 T 0 文献 标 识 码 : A
文章编号: 6 2 5 5 2 1 1 — 0 5 0 1 7 — 4 X( 0 0)2 0 0 — 4
摩擦在金属塑性成形过程 中 , 起着举足轻重 的作用 。 塑性
响成形 件的表面光洁度 ,而且会在制造过 程中使 零件产生局 部 减薄 、 断裂 、 皱等现象【 起 l 】 。塑性成形过 程从 宏观看 , 随着材 料 与模具表 面接触 面的增大 , 接触压力逐 渐增 大 , 氧化 膜在大
压 力 下 破 裂 , 致 金 属 向 外 表 面 裸 露 的 面 积增 大 , 于 新 旧表 导 由
3 . 位移传 感器
8 . 工控机
5电桥箱 .
7 . MD采集卡
1 几 种典 型 的摩擦 系数测 量 系统
摩擦 系数测量 系统 , 是使 用传感 器 、 配套仪 器和模 具等 ,
将塑性成形过程 中与摩擦 系数相关 的参数 ,用 MD转 换器把 采集到 的模拟信号 转换 成数字信号 , 通过放 大器 放大后 , 入 输
第四章金属塑性成形中的摩擦和润滑2013

缩短制品的寿命
当残余应力和制品实际应力叠加,超过该零件的 许用应力时,零件将产生塑性变形或破坏。 降低金属的塑性、冲击韧性及抗疲劳强度。
46
残余应力会降低金属的耐蚀性 例如:将冲压的黄铜制品置于潮湿的 气氛中,易产生裂纹,这种现象称为黄 铜的季裂。
47
问题讨论
产生畸变 (变形)
假设某圆柱体,心部受 拉应力,力图缩短,表 面受压,力图伸长。
拔长
27
要求较高的拔长生产效率时,坯料 的送料要小,这时轴向延伸较大。即 当送进量l小于坯料宽度a(l < a) 时,坯料轴向伸长得多。
不要求长度方向有较大的伸长时, 坯料的送料要大,这时轴向延伸较小 。即当送进量l大于坯料宽度a(l > a )时,坯料宽度增加的多。
28
金 属 塑 性 成 形 原 理 第 四 章 金 属 塑 性 成 形 中 的 摩 擦
10
摩擦学的定义
• 摩擦学是研究作相对运动的相互作用 表面及其有关的理论和实践的一门科 学技术。
机床导轨
11
• 定义中二个主要的部分:
1. 相对运动 2. 相互作用表面
机床导轨
12
摩擦学涉及的学科
• 摩擦学是一门交叉、边缘学科
– 摩擦学主要涉及学科:
• 物理学
• 化学 • 机械工程 • 材料学 • 力学
该圆柱体存在 残余应力,但 未变形。
切削前
某圆柱体切削后的变形。
48
49
减小或消除残余应力的方法
残余应力是附加应力的变化而来,其根本原因就是物体产 生了不均匀的变形。 减小材料在加工和处理过程中所产生的不均匀变形。 对加工件进行热处理。 去应力退火 人工时效 自然时效 进行机械处理。 使工件再产生一些表面变形,使残余应力得到一定的 释放和松弛。 如木锤敲打表面或喷丸加工。 表面层中具有残余拉应力的板材,经表面辗压后,其残 50 余应力大为缩小。
摩擦

2、 边界摩擦
起部分被压平,润滑剂被压入凹坑中,被封存在里面,如图18-8b。大多数塑性 成形的摩擦属于边界摩擦。 3、流体摩擦 两表面的微观凸凹部分不直接接触,完全被润滑剂隔开的润滑
叫流体润滑,该状态下的摩擦叫流体摩擦,如图18-8c。 流体摩擦与干摩擦和边界摩擦有着本质的区别,其摩擦特征与所加润滑剂的
N
(18-1)
实际上摩擦切应力不能随 N 的增大而无限地增大,当 max K 时接触面将 产生塑性流动。此时 N 的极限值为材料真实应力应变曲线上的屈服应力 Y 。根 据Mises屈服准则, K 1 ~ 1 )Y (
2 3
故由式(18-1)可确定摩擦系数的
极限值为 0.5 ~ 0.577
但是在塑性成形中也常常应用摩擦的有益作用。 例如,模锻中利用飞边槽桥部的摩擦力来保证模膛充满,滚锻和轧 制时依靠足够的摩擦使坯料被咬入轧辊。
二、塑性成形中的摩擦分类及机理
(一)塑性成形中的摩擦分类
根据塑性成形中坯料与工具表面之间的润滑状态的不同,摩擦可分为三类, 即干摩擦、边界摩擦和流体摩擦,由此还可以派生出混合型摩擦。 1、干摩擦 通常所说的干摩擦是指不加任何润滑剂的摩擦。 接触表面之间存在很薄的润滑膜,凸凹不平的坯料表面凸
mK
(18-3)
式中,m 称为摩擦因子,上式与式(18-2)相比,当 m 1 时,两条件一致。式(18-3)适合 于摩擦系数低于最大值的三向应力显著的塑性成形过程,如挤压、变形量大的镦粗、模锻等。
四、影响摩擦系数的主要因素Байду номын сангаас
1. 金属的种类和化学成分 2. 工具表面状态 材料的硬度、强度越高,摩擦系数就越小。
1.
分子吸附学说
- 1、下载文档前请自行甄别文档内容的完整性,平台不提供额外的编辑、内容补充、找答案等附加服务。
- 2、"仅部分预览"的文档,不可在线预览部分如存在完整性等问题,可反馈申请退款(可完整预览的文档不适用该条件!)。
- 3、如文档侵犯您的权益,请联系客服反馈,我们会尽快为您处理(人工客服工作时间:9:00-18:30)。
金属塑性成形原理
第三节 计算摩擦力的数ຫໍສະໝຸດ 表达式在计算金属塑性加工时的摩擦力时,常用以下三种条件: 一、 库伦摩擦条件 (滑动摩擦)
不考虑接触面上的粘合,认为摩擦符合库伦定律。 适合正压力不太大、变形量较小的的冷成形工序。不考虑接触表面的粘合 现象,认为单位面积上的摩擦力与接触面上的正应力成正比,即
坦光滑,都有不同程度的微观凸峰和凹坑,当微观粗糙的两表面接触时,一 个表面的凸峰可能会陷入另一表面的凹坑,产生机械咬合, 2. 分子吸附学说
对于非常光滑的接触面,认为摩擦是接触面上分子相互吸引的结果。接触 面越光滑,接触面积就越大,分子吸引力就越强,则摩擦力就越大。该学说 解释了凸凹学说无法解释的表面越光滑,摩擦力不降反升的现象。 3. 粘着理论
,变形也不均匀,产生不同的几个区域,形成鼓形。 而残余应力会使制品的尺寸和形状发生变化,缩短制品的使用寿命。
由于变形体内各部位的不均匀变形受 到变形体整体性限制,各部位不能独立地 改变自己的尺寸而不对相邻部分发生影响 ,这种应力被称为附加应力。
例如,利用凸肚轧辊轧制等厚矩形坯料 时,矩形坯料边缘部分变形程度小,中间部 分的变形程度大。
无论是机械传动、还是金属塑性成形,都存在有相对运动或有运 动趋势的两接触表面的摩擦。
分别称为动摩擦和静摩擦。 机械传动中主要为动摩擦,塑性成形中有动摩擦和静摩擦。 金属塑性成形中又分为内摩擦和外摩擦: 内摩擦是金属内晶界面或晶内滑移面产生的的摩擦; 外摩擦指变形金属与工具间接接触面上产生的摩擦。 这里研究的摩擦是指外摩擦。单位接触面上的摩擦力称为摩擦 切应力,其方向与质点运动方向相反,阻碍金属质点的流动。
金属塑性成形原理
一、金属塑性成形中摩擦的特点
与机械传动摩擦相比,塑性成形的摩擦有如下特点:
1、伴随着变形金属的塑性流动 塑性成形的摩擦接触面因金属的塑性流动,接触状态不断变化,接触面上
各处塑性流动不同,有滑动、粘着,有快、慢,接触面上各点摩擦不同。而 机械传动的摩擦的表面均处于弹性变形。 2、接触面单位压力高
流体摩擦与干摩擦和边界摩擦有着本质的区别,其摩擦 特征与所加润滑剂的性质和相对速度有关,而与接触表面 的状态无关。
金属塑性成形原理
二、摩擦机理
塑性成形过程中的摩擦是非常复杂的,目前关于摩擦机理(即摩擦产生 的原因)有三种学说,现代摩擦理论认为是三者的结合。(焊合-剪切理论)
1. 表面凹凸学说 认为摩擦是由接触面上凹凸形状引起的。经过机械加工的表面并非绝对平
但有时在成形过程中,摩擦是有益的。例如,模锻中利用飞边槽桥部的 摩擦力来保证模膛充满,滚锻和轧制时依靠足够的摩擦使坯料被咬入轧辊。
开式模锻的金属流动
轧制
金属塑性成形原理
第二节 金属塑性成形中摩擦的分类及机理
一、塑性成形中摩擦的分类
根据塑性成形中坯料与工具表面之间的润滑状态的不同 ,摩擦可分为三类,即干摩擦、边界摩擦和流体摩擦,由 此还可以派生出混合型摩擦。 1. 干摩擦 通常指不加任何润滑剂的摩擦。 2. 边界摩擦 接触表面之间存在很薄的润滑膜,凸凹不平的 坯料表面凸起部分被压平,润滑剂被压入凹坑中,被封存 在里面。大多数塑性成形的摩擦属于边界摩擦。 3. 流体摩擦 两表面的微观凸凹部分不直接接触,完全被润 滑剂隔开的润滑叫流体润滑,该状态下的摩擦叫流体摩擦。
小得多。而塑性变形过程中,由于发生塑性变形,接触面上的凸起部分被压平 ,因而实际面积接近名义接触面积,使摩擦力增大。 4、不断产生新的摩擦面
在塑性成形过程中,原来非接触面在变形过程中可能成为新的接触摩擦面 ,从而产生粘合力,使摩擦力增大。因此,要不断给新的接触面添加润滑剂。 5、经常在高温下进行
金属塑性变形往往通过热压力加工 。钢材热塑性加工温度一般为800- 1200℃,这时,接触表面会产生金属氧化、模具软化、润滑剂分解等复杂的物 理化学变化。 6、摩擦副性质差别大
无摩擦条件下: p 3 s
摩擦条件下: 1 3 s p 3 1 s
因而摩擦力使变形抗力增大,增大能量消耗,一 般情况下,摩擦的加大可使负荷增加30%
金属塑性成形原理
2. 引起不均匀变形,产生附加应力和残余应力 如挤压杆件时,由于挤压筒壁摩擦力的影响,使坯料边缘处的流动比中间
慢,造成边缘受拉伸而中间受压缩的附加应力。 如圆柱体镦粗时,由于接触面摩擦的影响,使变形体内部应力不均匀分布
金属塑性成形原理
第四章 金属塑性成形中的摩擦
金属塑性成形原理
内容提纲
一、金属塑性成形中摩擦的特点和影响 二、塑性成形中摩擦的分类及机理 三、描述接触表面上摩擦力的数学表达式 四、影响摩擦系数的主要因素 五、测定外摩擦系数的方法 六、塑性成形中的润滑 七、不同塑性成形下的摩擦系数
金属塑性成形原理
第一节 金属塑性成形中摩擦的特点和影响
塑性成形时的摩擦接触面上压力很高,热塑性时达500MPa,钢冷挤压和冷 轧时高达2500~3000MPa。接触面压力愈高,润滑剂易挤出和失效,降低了润 滑效果。(一般的机械传动,接触面的压强仅为20~40MPa)
金属塑性成形原理
3、实际接触面积大 一般机械传动过程中,由于接触面凹凸不平,故实际接触面比名义接触面
但矩形坯料为一整体,虽各部分变形量 不同,但纵向伸长量趋于相等。故中间部分 将给边缘部分施以拉应力,反之边缘部分给 中间部分施以压应力。
金属塑性成形原理
金属塑性成形原理
3. 降低模具寿命
摩擦使模具接触面磨损增加、摩擦产生的热使模具材料软化、磨损 导致的内应力增大。
为减少摩擦对塑性成形的不利影响,常采用润滑,即在工具和变形金属 的接触面上涂敷润滑剂。
工具无塑性变形、组织不发生变化;工件较大塑性变形。二者性质与作用差 异大,变形摩擦特殊。
金属塑性成形原理
二、摩擦对塑性成形过程的影响
在多数情况下,摩擦对塑性成形是有害的,具体表现如下:
1. 改变应力状态,增大变形抗力 例如单向压缩时,若工具与坯料无摩擦存在,则坯料受单向应力状态;
若存在摩擦时,则变成三向应力状态,且使端面压应力增加才能屈服,因 而变形抗力增加。