Lean Production精益生产介绍
精益生产发展背景及流程

精益生产发展背景及流程精益生产(Lean Production)是一种高效的生产管理方法,它起源于日本丰田汽车公司的生产管理理念。
20世纪70年代,由于石油危机和全球经济危机,企业面临着严峻的竞争和资源压力,因此迫切需要一种能够提高生产效率的新方法。
精益生产的主要目标是消除浪费,提高生产效率,并同时提高产品质量。
其核心思想是在生产过程中最大限度地减少或消除非价值增加的活动,以便将资源集中用于创造价值。
精益生产采用各种工具和技术,如物理流程改善、人员能力培训、供应链管理和质量控制等,以实现生产过程的精益化。
精益生产的核心流程包括价值流分析、精益物流、快速返工和全员参与等。
首先,通过价值流分析,企业能够清楚地了解生产过程中的所有活动,并确定哪些活动是为客户创造价值的,哪些是浪费的。
然后,企业可以采取精益物流的方法,通过合理的物料流动和库存管理,消除生产过程中的浪费。
快速返工是指快速发现和解决生产过程中出现的问题,以确保产品的质量。
最后,全员参与是指企业鼓励员工在持续改进方面发挥积极作用,从而推动整个精益生产流程的不断改进。
精益生产方法的应用范围非常广泛,涉及各个行业和领域。
它不仅可以提高生产效率和质量,降低成本,还可以增强企业的竞争力和可持续发展能力。
许多企业在实施精益生产后,都取得了显著的成效,如减少生产周期、提高产品质量、降低库存水平和成本等。
总之,精益生产是一种有效提高生产效率和质量的管理方法。
它的发展背景是应对严峻的竞争和资源压力,以及推动企业的持续改进和可持续发展。
通过价值流分析、精益物流、快速返工和全员参与等核心流程,企业可以实现生产过程的精益化,从而提高竞争力和可持续发展能力。
精益生产(Lean Production)作为一种高效的生产管理方法,它的发展背景可以追溯到日本丰田汽车公司的生产管理理念。
20世纪70年代,由于石油危机和全球经济危机的冲击,企业面临着巨大的竞争和资源压力。
在这样的背景下,丰田汽车公司积极寻求一种能够增加生产效率、提高产品质量的方法,并希望采取一种能够在有限的资源条件下实现最佳效益的生产方式。
精益生产的概念及特点分析

精益生产的概念及特点分析引言精益生产是一种以节约资源、增加价值为中心的生产管理理念,起源于日本汽车业。
它通过最小化浪费和提高效率,实现了生产过程的优化和产品质量的提升。
本文将介绍精益生产的概念,并分析其特点。
一、精益生产的概念精益生产(Lean Production)是一种通过消除浪费、提高效率和灵活性的生产方式。
它最早由日本丰田汽车公司开发和实践,并得到广泛推广和应用。
精益生产的核心理念是尽量减少浪费,提高价值创造,从而实现成本降低和效率提高。
它通过减少库存、减少不必要的活动和流程、优化资源使用等方式,确保生产过程能够快速、高效地运转。
二、精益生产的特点1.去除浪费:精益生产强调去除各种形式的浪费,包括等待时间、过程中的缺陷、运输和库存的浪费等。
通过识别和消除浪费,企业能够大幅度提高生产效率和产品质量。
2.价值流分析:精益生产通过价值流分析,识别出创造价值的步骤和非价值增加的步骤,以便优化生产过程。
通过削减或优化非价值增加的步骤,企业能够实现资源的最大利用。
3.持续改进:精益生产强调持续改进的理念。
企业应该不断地寻求改进的机会,不断优化生产流程和提升产品质量。
通过持续改进,企业可以不断提高效率和竞争力。
4.员工参与:精益生产注重员工的参与和协作。
员工是企业的核心资产,他们的经验和智慧对于改进生产过程非常重要。
通过培养员工的参与意识和团队合作精神,企业可以更好地实现精益生产的目标。
5.质量优先:精益生产强调质量的重要性。
企业应该始终把质量放在第一位,追求卓越的产品质量。
通过不断提高产品质量,企业可以提升品牌形象、增加市场竞争力。
6.灵活性:精益生产注重灵活性和适应性。
企业应该具备快速响应市场需求的能力,同时灵活调整生产流程,以适应市场变化。
通过灵活性,企业可以更好地满足客户需求并获得竞争优势。
三、精益生产的实施步骤1.识别价值流:通过价值流分析,识别出创造价值的步骤和非价值增加的步骤。
2.消除浪费:排除所有不必要的活动和流程,减少浪费,提高效率。
精益生产基础知识

①.利用夹具或轨道限定动作路径; ②.抓握部的形状要便于抓握; ③.在可见的位置通过夹具轻松定位; ④.用轻便操作工具。
基本原则
要点
要素
动作经济原则
三、精益屋
课后作业: ECRS:发现一个可改善问题点; 动作经济原则:做一个工序的动作分析,并给出改善方案。
Thank You
*
三、精益屋
2.合并(combine)
合并就是将两个或两个以上的对象变成一个。如工序或工作的合并、工具的合并等。合并后可以有效地消除重复现象,能取得较大的效果。当工序之间的生产能力不平衡,出现人浮于事和忙闲不均时,就需要对这些工序进行调整和合并。有些相同的工作完全可以分散在不同的部门去进行,也可以考虑能否都合并在一道工序内。 例如,合并一些工序或动作,或将由多人于不同地点从事的不同操作,改为由一个人或一台设备来完成。
三、精益屋
1.减少动作数
2.双手同时进行
3.缩短动作距离
4.轻快动作
是否进行多余的搜索、选择、思考和预制
某只手是否处于空闲等待或拿住状态
是否用过大的动作进行作业
能否减少动素数
1.作业动作
①.取消不必要的动作; ②.减少眼的活动; ③.合并两个以上的动作。
①.双手同时开始,同时结束; ②双手反向、对称同时动作。
“简化”具体操作
简化包括将复杂的流程加以简化,也包括简化每道工序的内容: 减少各种繁琐的程序,减少各种复杂性。 使用最简单的动作来完成工作。 简化不必要的设计结构,使工艺更合理, 力求作业方法的简化。 运送路线、信息传递路线力求缩短。
三、精益屋
ECRS分析原则的适用性
2精益生产介绍

精益生産 的特點是消除一切浪費,追求精益求精和不斷 改善。去掉生産 環節中一切無用的東西,每個工人及其崗 位的安排原則是必須增值,撤除一切不增值的崗位。精簡 是它的核心,精簡産 品開發設計、生産、管理中一切不 産 生附加值的工作,旨在以最優品質、最低成本和最高效 率對市場需求作出最迅速的回應.
水平的1/10; 4 工廠佔用空間—最低可減至採用大量生産 方式下的1/2; 5 成品庫存最低可減至大量生産 方式下平均庫存水平的 1/4; 6 産 品質量—可大幅度提升;:
精益生産 方式是徹底地追求生産 的合理性、高效性,能夠靈 活 術,地其生基産本適原應理各和種諸需多求方的法高,質對量製産造業品具的有生積産極技的術意和義管。理精技益55
前置時間(Lead time) 爲 此要消除中間停滯,實現“零”停
精益生産 方式的優越性及其意義: 與大量生産 方式相比,日本所採用的精益生産 方式的優越
性主要表現在以下幾個方面: 1.所需人力資源--無論是在産 品開發、生産 系統,還是工
廠的
其他部門,與大量生産 方式下的工廠相比,最低能減至1/2; 2 新産 品開發周期—最低可減至l/2或2/3; 3 生産 過程的在製品庫存最低可減至大量生産 方式下一 般
精益生產的目標: Q:ty,品質; C:Cost,成本; D:Delivery,交貨期;
精益生產的目標就是實現短交期、低成本、高質量.
精益生產目標與企業現場管理目標是完全一致的.
其目標是精益求精,盡善盡美,永無止境的追求 七個零的終極目標。
“零浪費”爲 精益生産 終極目標,具體表現在PICQMDS 七個方面
爲 優化目標。
66
(2)對待庫存的態度不同 大批量生産 方式的庫存管理強調“庫存是必要的惡物”。 精益生産 方式的庫存管理強調“庫存是萬惡之源” 精益生産 方式將生産 中的一切庫存視爲“浪費”,同時 認爲 庫存掩蓋了生産 系統中的缺陷與問題。它一方面強 調供應對生産 的保證,另一方面強調對零庫存的要求,從 而不斷暴露生産 中基本環節的矛盾並加以改進,不斷降低 庫存以消滅庫存産 生的“浪費”。基於此,精益生産 提 出了“消滅一切浪費”的口號。追求零浪費的目標。 (3)業務控制觀不同 傳統的大批量生産 方式的用人制度基於雙方的“雇用”關 係,業務管理中強調達到個人工作高效的分工原則,並以 嚴格的業務稽核來促進與保證,同時稽核工作還防止個人 工作對企業産 生的負效應。 精益生産 源於日本,深受東方文化影響,在專業分工時強 調相互協作及業務流程的精簡(包括不必要的核實工作)
精益生产介绍.
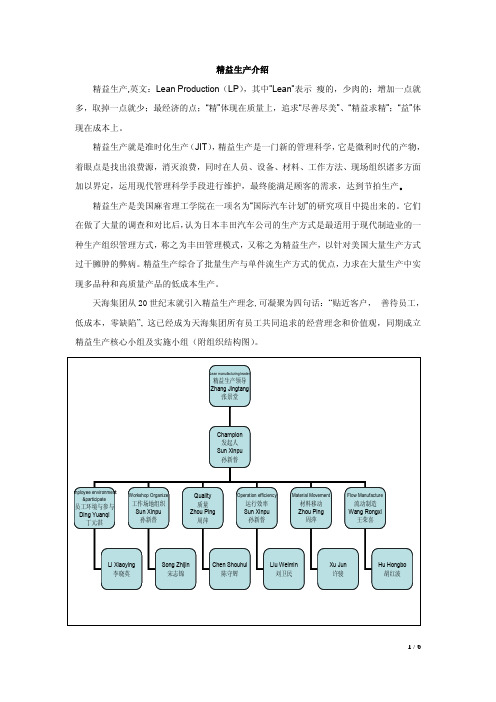
精益生产介绍精益生产,英文:Lean Production(LP),其中”Lean”表示瘦的,少肉的;增加一点就多,取掉一点就少;最经济的点;“精”体现在质量上,追求“尽善尽美”、“精益求精”;“益”体现在成本上。
精益生产就是准时化生产(JIT),精益生产是一门新的管理科学,它是微利时代的产物,着眼点是找出浪费源,消灭浪费,同时在人员、设备、材料、工作方法、现场组织诸多方面加以界定,运用现代管理科学手段进行维护,最终能满足顾客的需求,达到节拍生产。
精益生产是美国麻省理工学院在一项名为“国际汽车计划”的研究项目中提出来的。
它们在做了大量的调查和对比后,认为日本丰田汽车公司的生产方式是最适用于现代制造业的一种生产组织管理方式,称之为丰田管理模式,又称之为精益生产,以针对美国大量生产方式过干臃肿的弊病。
精益生产综合了批量生产与单件流生产方式的优点,力求在大量生产中实现多品种和高质量产品的低成本生产。
精益生产作为一种从环境到管理目标都全新的管理思想,在天海集团所有员工实际与实践努力中取得成功,是一套与企业环境、文化以及管理方法高度融合的管理体系。
精益生产的特点:(1)拉动式准时化生产(Just in time )精益生产是一种流畅制造,是按照顾客的需求节拍来平衡我们的生产节拍,所以如何来平衡我们的生产节拍是我们追求的目标,在一个以顾客为本的制造价值流中,如何快捷高效的满足顾客,我们首推Push 体系,Push 体系实际是一种推动式生产,那是根据顾客的需求,直接安排生产,每道工序完成直接进入下一道工序,中间没有库存,没有等待,最后入库发货的一种没有停顿的生产方式,但这是在生产品种较少,生产批量较大的情况下进行的,也就是说是一种卖方市场的一种产物,但随着市场竞争的加剧,微利时代的来临,没有任何一家公司敢宣称自己的市场是卖方市场,这就要求每生产一种产品要考虑是否顾客需要,生产多少由顾客决定,什么时间生产由顾客决定,JIT (准时化生产)就应运而生,所谓JIT 就是说:在顾客需要的时间,根据顾客需要的量,生产顾客需要的品种。
精益生产介绍

精益生产介绍精益生产(Lean Production)是一种旨在提高生产效率、降低生产成本、提升产品质量的生产管理方法。
精益生产起源于日本的丰田公司,旨在通过消除浪费、优化流程和提高员工参与度来实现生产的高效运作。
精益生产的核心理念是将价值观和原则贯穿到整个生产过程中。
它强调通过减少和消除各种浪费来提高生产效率。
浪费可以分为七种类型:超产、存储、运输、过程、等待、瑕疵和员工的潜力浪费。
通过减少或消除这些浪费,企业可以提高生产效率,降低成本,并最大限度地提供高质量的产品。
精益生产还强调优化流程。
它倡导通过精确分析工作流程,并使用工具和技术来改进和简化流程,以降低生产时间和成本。
常用的工具包括价值流图、时间研究和5S。
除了减少浪费和优化流程外,精益生产还着重关注员工的参与度。
它认为员工是企业最宝贵的资产,他们对于生产过程的改进和优化有着不可替代的作用。
因此,精益生产鼓励员工积极参与到生产管理中,提供他们所需的培训和支持,以便他们能够更好地发挥自己的潜力。
精益生产方法的实施可以带来众多的优势。
首先,它可以提高生产效率,减少浪费和降低成本,从而提高企业的竞争力。
其次,它可以优化流程,使生产过程更加紧密和高效,从而缩短交货时间,并满足客户对交付速度的要求。
最后,通过鼓励员工参与,精益生产可以激发员工的创造力和潜力,提高员工满意度和团队合作精神。
然而,精益生产的实施并非一蹴而就的过程,需要企业有明确的目标和长期的计划,并持之以恒地执行。
同时,要求公司高层对精益生产的理念和原则有深入的理解和支持,并打破传统的管理模式和思维定式。
总的来说,精益生产是一种提高生产效率、降低成本和提升产品质量的生产管理方法。
它通过减少浪费、优化流程和提高员工参与度来实现高效的生产运作。
精益生产方法的实施可以带来众多的优势,但需要企业有明确的目标和长期的计划,并打破传统的管理模式和思维定式。
精益生产是一种能够释放潜力、优化生产流程并实现持续改进的方法。
精益生产理论与实务

精益生产理论与实务精益生产理论(Lean Production)起源于日本丰田汽车公司,它是一种以消除浪费为核心的生产管理方法。
精益生产的目标是在不影响质量和交货期的前提下,最大限度地提高资源利用效率。
在精益生产实践中,企业通过最小化废品、减少库存、提高生产效率等手段来实现生产过程的最优化。
精益生产理论的核心是通过减少浪费来提高生产效率。
浪费是指任何与产品生产过程无关的活动或资源的消耗,比如库存积压、破损的产品、超时的生产等。
精益生产通过消除这些浪费,实现资源的最大化利用,从而提高生产效率并降低生产成本。
精益生产的实践需要从整个生产过程中寻找并改善各种形式的浪费。
例如,在生产产品的过程中,通过合理布局工作岗位和优化工作流程,减少人员的不必要移动和等待时间,提高生产效率。
此外,精益生产还倡导及时生产,以减少产品的库存积压。
另外,精益生产还鼓励企业与供应商建立长期合作关系,以实现产供需的紧密配合。
通过与供应商的密切合作,企业可以有效降低物料的库存,减少仓储成本,并及时获取原材料和零部件,在提高生产效率的同时确保产品质量。
精益生产理论的实践需要企业建立一个高效的管理体系。
管理层需要发掘并培养员工的潜力,使其参与到生产管理过程中,推动精益生产的实施。
同时,管理层还需要建立一套科学的绩效评估体系,以鼓励员工在精益生产实践中的积极表现。
总而言之,精益生产理论是一种以消除浪费为核心的生产管理方法。
通过消除各种形式的浪费,企业可以提高生产资源的利用效率,降低生产成本,从而提高竞争力。
精益生产的实践需要企业全员参与,建立高效的管理体系,与供应商建立长期合作关系。
只有这样,企业才能在激烈的市场竞争中立于不败之地。
精益生产理论(Lean Production)是一种以消除浪费为核心的生产管理方法,源自日本丰田汽车公司。
在全球范围内,精益生产已经被广泛应用于各行各业,从制造业到服务业,其效果显著。
精益生产理论的核心观念是通过最小化浪费来提高资源利用效率。
精选精益生产LEANPRODUCTION

减少库存的有力措施是变“批量生产、排队供应” 为单件流生产。单件流生产(1-Piece-Flow) 只有一个生产件在各道工序间流动,整个生产过程随单件流的进行而永远流动理想情况:相邻工序间没有在制品库存
同步——在不间断的连续生产流程中,必须 平衡生产单元内每一道工序,要求 完成每一项操作致相同的时间
计算如下:
(取4个工作台,尚有生产能力剩余)
规划精益生产单元的布置。 实际设计生产精益生产单元时,可以考虑设置两个铣、钻、磨加工区,每个加工区由两个工作台组成,每个工作台配备一个工人
上图是严格按照Tact Time为45秒,每小时生产80单位而设计的生产单元。包装、装配线1、铣/钻/磨等都有一定生产剩余,所以瓶颈是装配线2。如果要加大生产量,可把装配线2的工作适量的分配给包装、装配线1,或提高生产率,降低装配线2的生产时间来解决
步骤1:计算单件产品生产时间 (Tact Time)
步骤2:计算符合单件产品生产时间每小时的生产量
步骤3:计算每道工序的每小时的生产能力,以及每道工序所需工作台的数目
包装
(取一个工作台,尚有生产能力剩余)
装配线2:
(取4个工作台)
装配线1:
(取2个工作台,尚有生产能力剩余)
铣、钻、磨:这几道工序有长有短,必须平衡各道工序的劳动利用率。设置一个微型加工单元,把铣、钻、磨有机地结合起来,并且只要一个工人完成这三项操作。 完成这三道工序所需时间为170秒。每小时可完成21.2单位的产品。
消除停机时间 全面生产维修(TPM)是消除停机时间最有力的措施, 它包括例行维修、预测性维修、预防性维修和立即维修四种基本维修方式
例行维修——操作工和维修工每天所作的 维修活动,定 期对机器进行保养
- 1、下载文档前请自行甄别文档内容的完整性,平台不提供额外的编辑、内容补充、找答案等附加服务。
- 2、"仅部分预览"的文档,不可在线预览部分如存在完整性等问题,可反馈申请退款(可完整预览的文档不适用该条件!)。
- 3、如文档侵犯您的权益,请联系客服反馈,我们会尽快为您处理(人工客服工作时间:9:00-18:30)。
Copyright 2006 John Wiley & Sons, Inc.
15-10
Cells with Worker Routes
Copyright 2006 John Wiley & Sons, Inc.
15-11
Worker Routes Lengthen as Volume Decreases
waste, anything other than that which adds value to the product or service
Muda
Copyright 2006 John Wiley & Sons, Inc.
15-3
Waste in Operations
Copyright 2006 John Wiley & Sons, Inc.
Lecture Outline
Basic Elements of Lean Production Benefits of Lean Production Implementing Lean Production Lean Services
Copyright 2006 John Wiley & Sons, Inc.
Q = order quantity R = reorder point - demand during lead time
Copyright 2006 John Wiley & Sons, Inc.
15-16
Types of Kanban
Production kanban
Signal kanban
15-22
Small Lots
Require less space and capital investment Move processes closer together Make quality problems easier to detect Make processes more dependent on each other
15-2
Lean Production
Doing more with less inventory, fewer workers, less spaceBiblioteka Just-in-time (JIT)
smoothing the flow of material to arrive just as it is needed “JIT” and “Lean Production” are used interchangeably
N d L S C
= number of kanbans or containers = average demand over some time period = lead time to replenish an order = safety stock = container size
15-21
Copyright 2006 John Wiley & Sons, Inc.
Copyright 2006 John Wiley & Sons, Inc.
Determining Number of Kanbans: Example
d L S C = 150 bottles per hour = 30 minutes = 0.5 hours = 0.10(150 x 0.5) = 7.5 = 25 bottles
Cycle time
Takt time
Copyright 2006 John Wiley & Sons, Inc.
15-8
Standard Operating Routine for a Worker
Copyright 2006 John Wiley & Sons, Inc.
15-9
Cellular Layouts
External setup
Separate internal setup from external setup Convert internal setup to external setup Streamline all aspects of setup Perform setup activities in parallel or eliminate them entirely
Copyright 2006 John Wiley & Sons, Inc.
15-23
Inventory Hides Problems
Copyright 2006 John Wiley & Sons, Inc.
15-24
Less Inventory Exposes Problems
Copyright 2006 John Wiley & Sons, Inc.
15-17
Material kanban
Kanban square
Supplier kanban
Copyright 2006 John Wiley & Sons, Inc.
Copyright 2006 John Wiley & Sons, Inc.
15-18
Copyright 2006 John Wiley & Sons, Inc.
15-26
Move time
Waiting time
Setup time
Copyright 2006 John Wiley & Sons, Inc.
Quick Setups
Internal setup
SMED Principles
Can be performed only when a process is stopped Can be performed in advance
Copyright 2006 John Wiley & Sons, Inc.
15-14
Sample Kanban
Copyright 2006 John Wiley & Sons, Inc.
15-15
Origin of Kanban
a) Two-bin inventory system Bin 1 Kanban Bin 2 Reorder card Q-R R R b) Kanban inventory system
Copyright 2006 John Wiley & Sons, Inc.
15-7
Flexible Resources
Multifunctional workers
perform more than one job general-purpose machines perform several basic functions time required for the worker to complete one pass through the operations assigned paces production to customer demand
Copyright 2006 John Wiley & Sons, Inc.
15-12
Pull System
Material is pulled through the system when needed Reversal of traditional push system where material is pushed according to a schedule Forces cooperation Prevent over and underproduction While push systems rely on a predetermined schedule, pull systems rely on customer requests
15-19
Copyright 2006 John Wiley & Sons, Inc.
15-20
Determining Number of Kanbans
No. of Kanbans =
average demand during lead time + safety stock container size dL + S N = C where
15-4
Waste in Operations (cont.)
Copyright 2006 John Wiley & Sons, Inc.
15-5
Waste in Operations (cont.)
Copyright 2006 John Wiley & Sons, Inc.
15-6
Basic Elements
authorizes production of goods
Withdrawal kanban
authorizes movement of goods
a marked area designated to hold items