铸造工图,结构设计
合集下载
铸件的结构设计

(a)直角连接 (b)圆角连接 图6-35 转角处的热节
(a)直角连接 (b)圆角连接 图6-36 金属结晶的方向性
2.避免锐角连接
如图6-37(a)所示,锐角连接会由于 内角散热条件差而增大热节,容易产生缩 孔、缩松等铸造缺陷。若两壁间的夹角小 于90°,则应采取过渡形式,如图6-37(b) 所示。
(b)改进后
图6-31 内腔的两种结构
2.便于砂芯固定、排气和铸件清理
如图6-32(a)所示,轴承架铸件的内腔需要采用两个砂芯,其中较 大的砂芯呈悬臂状,需用型芯撑支撑固定;如图6-32(b)所示,将轴承 架铸件的内腔改为整体砂芯,则砂芯的稳定性大大提高,并有利于排气。
(a)改进前
(b)改进后
图6-32 轴承架铸件
铸件中垂直于分型面的不 加工表面最好有结构斜度,以 便于起模或者便于用砂垛代替 砂芯。如图6-34(a)所示的铸 件结构设计不合理,对铸件的 结构斜度进行改进后的合理设 计如图6-34(b)所示。
(a)改进前
(b)改进后
图6-34 结构斜度的设计
二、合金铸造性能对铸件结构的要求
(一)铸件壁厚设计合理
工程材料及成形工艺
铸件的结构设计
一、铸造工艺对铸件结构的要求
铸件的结构设计不应只考虑对其结构性能的影响,还应有利于提高 铸件的工艺水平。所以铸件结构应尽可能使制模、造型、造芯、合箱和 清理过程简单化,防止产生废品,并为实现机械化生产创造条件。铸件 外形力求简单,铸件内腔设计合理是铸造工艺对铸件结构的主要要求。
为保证金属液充满铸型,避免浇不足、冷隔等缺陷的产生,铸件应当有合理 的壁厚。每种铸造合金都有其适宜的壁厚,选择得当,既能保证铸件力学性能, 又能防止铸造缺陷的产生。几种常用铸件在砂型铸造时的最小壁厚如表6-7所示。
一铸造ppt课件

浇注温度低流动性差,易产生浇不到或冷隔。浇注温度过高,铸件晶粒粗大, 缩孔增大,易产生缩孔、裂纹和粘砂。
浇注温度由铸造合金`种类、铸件大小及形状确定。 形状复杂、薄壁灰铸铁件,浇注温度1400℃; 形状简单、厚壁灰铸铁件,浇注温度1300℃; 铸钢件浇注温度1500℃。
(2)浇注速度:
速度高流动性好,易冲砂;速度低,易于补缩,但易产生冷隔、夹砂、砂眼。 浇注速度由铸件大小、形状确定。
除了以上性能的要求外,还有溃散性、发气性、吸湿性等的性能要求。 • 型、芯砂的诸多性能,有时是相互矛盾的,如强度高、塑性好,透气性
就可能下降,因此应根据铸造合金的种类,铸件大小、批量、结构等, 具体决定型、芯砂的配比。 型砂种类:
面砂 填充砂 单一砂 型芯砂
型(芯)砂的制备过程 • 烘干---筛分---混砂(先干混后湿混)---松砂---停放(闷砂)。
1.1 砂型铸造
三、造型和制芯
(一)造型方法 手工造型和机器造型
1 手工造型:全部用手工或手动工具完成的造型工序。 (1)、整模造型的模样是整体的,分型面是平面,铸型型腔全部在
半个铸型内,其造型简单,铸件不会产生错型缺陷。适用于铸件最大截面 在一端,且为平面的铸件。
1.1 砂型铸造
(2)、分模造型是将模样沿最大截面处分成两半,型腔位于上、下两
个砂箱内,造型简单省工。常用于最大截面在中部的铸件。
1.1 砂型铸造
(4)、活块造型是在制模时将铸件上的妨碍起模的小凸台,肋条等这些 部分作成活动的(即活块)。起模时,先起出主体模样,然后再从侧面取出 活块。其造型费时,工人技术水平要求高。主要用于单件、小批生产带有突 出部分、难以起模的铸件。
1.1 砂型铸造
芯撑
(6)、铸件结构设计应考虑的其它问题
浇注温度由铸造合金`种类、铸件大小及形状确定。 形状复杂、薄壁灰铸铁件,浇注温度1400℃; 形状简单、厚壁灰铸铁件,浇注温度1300℃; 铸钢件浇注温度1500℃。
(2)浇注速度:
速度高流动性好,易冲砂;速度低,易于补缩,但易产生冷隔、夹砂、砂眼。 浇注速度由铸件大小、形状确定。
除了以上性能的要求外,还有溃散性、发气性、吸湿性等的性能要求。 • 型、芯砂的诸多性能,有时是相互矛盾的,如强度高、塑性好,透气性
就可能下降,因此应根据铸造合金的种类,铸件大小、批量、结构等, 具体决定型、芯砂的配比。 型砂种类:
面砂 填充砂 单一砂 型芯砂
型(芯)砂的制备过程 • 烘干---筛分---混砂(先干混后湿混)---松砂---停放(闷砂)。
1.1 砂型铸造
三、造型和制芯
(一)造型方法 手工造型和机器造型
1 手工造型:全部用手工或手动工具完成的造型工序。 (1)、整模造型的模样是整体的,分型面是平面,铸型型腔全部在
半个铸型内,其造型简单,铸件不会产生错型缺陷。适用于铸件最大截面 在一端,且为平面的铸件。
1.1 砂型铸造
(2)、分模造型是将模样沿最大截面处分成两半,型腔位于上、下两
个砂箱内,造型简单省工。常用于最大截面在中部的铸件。
1.1 砂型铸造
(4)、活块造型是在制模时将铸件上的妨碍起模的小凸台,肋条等这些 部分作成活动的(即活块)。起模时,先起出主体模样,然后再从侧面取出 活块。其造型费时,工人技术水平要求高。主要用于单件、小批生产带有突 出部分、难以起模的铸件。
1.1 砂型铸造
芯撑
(6)、铸件结构设计应考虑的其它问题
铸件的结构设计

过大的平面不利于金属液的填充,容易产生浇不到等缺陷, 在进行铸件的结构设计时,应尽量将水平面设计成倾斜形状。
避免大水平壁的结构
6、铸件结构应避免冷却收缩受阻和有利于减小变形
铸件在结构设计时,应尽量使其能自由收缩,以减小应力, 避免裂纹。如图所示的弯曲轮辐和奇数轮辐的设计,可使铸件 能较好地自由收缩。
拔模斜度在铸造工艺图上或 模型图上标出。它是对零件图 上没有结构斜度的立壁(垂直 于分型面的非加工面上),给 予的一个较小角度。
(二)铸件内腔的设计 1、 有利于砂芯的固定和排气
型芯的固定主要依靠芯头来保证,若采用图a的结构,则需要 两个型芯,而且其中大的型芯呈悬臂状态,装配时必须采用芯撑 作辅助支撑,若改成图b所示的形状,采用一个整体型芯来形成 铸件的空腔,则既可增加型芯的稳固性,又改善了型芯排气和清 理条件,显然后者的设计是合理的。
1、铸件应有合理的壁厚(铸件壁厚介于临界壁厚和最小壁
厚之间)
最小壁厚:在各种工艺条下,铸造合金能充满型腔的最小厚度。 主要取决于合金的种类、铸件的大小及形状等因素。 临界壁厚:各种铸造合金都存在一个临界壁厚,在砂型铸造条 件下,各种铸造合金临界壁厚约等于其最小壁厚的3倍。
缺陷:如果所设计铸件的壁厚小于允许的 “最小壁厚”,铸件就 易产生浇不足、冷隔等缺陷。在铸造厚壁铸件时,容易产生缩孔、 缩松、结晶组织粗大等缺陷,从而使铸件的力学性能下降。
铸件壁联结应尽量避免金属积聚
3)铸件壁与壁的连接 • 设计结构圆角(减小热节、内应力)
转角处形 成分界面,集 中许多杂质, 为铸件的薄弱 环节。
4、防止产生变形
某些壁厚均匀的细长铸件,较大面积的平板铸件,以及壁 厚不均匀的长形箱体都会由于应力而产生翘曲变形,应采用合 理的结构设计予以解决。
避免大水平壁的结构
6、铸件结构应避免冷却收缩受阻和有利于减小变形
铸件在结构设计时,应尽量使其能自由收缩,以减小应力, 避免裂纹。如图所示的弯曲轮辐和奇数轮辐的设计,可使铸件 能较好地自由收缩。
拔模斜度在铸造工艺图上或 模型图上标出。它是对零件图 上没有结构斜度的立壁(垂直 于分型面的非加工面上),给 予的一个较小角度。
(二)铸件内腔的设计 1、 有利于砂芯的固定和排气
型芯的固定主要依靠芯头来保证,若采用图a的结构,则需要 两个型芯,而且其中大的型芯呈悬臂状态,装配时必须采用芯撑 作辅助支撑,若改成图b所示的形状,采用一个整体型芯来形成 铸件的空腔,则既可增加型芯的稳固性,又改善了型芯排气和清 理条件,显然后者的设计是合理的。
1、铸件应有合理的壁厚(铸件壁厚介于临界壁厚和最小壁
厚之间)
最小壁厚:在各种工艺条下,铸造合金能充满型腔的最小厚度。 主要取决于合金的种类、铸件的大小及形状等因素。 临界壁厚:各种铸造合金都存在一个临界壁厚,在砂型铸造条 件下,各种铸造合金临界壁厚约等于其最小壁厚的3倍。
缺陷:如果所设计铸件的壁厚小于允许的 “最小壁厚”,铸件就 易产生浇不足、冷隔等缺陷。在铸造厚壁铸件时,容易产生缩孔、 缩松、结晶组织粗大等缺陷,从而使铸件的力学性能下降。
铸件壁联结应尽量避免金属积聚
3)铸件壁与壁的连接 • 设计结构圆角(减小热节、内应力)
转角处形 成分界面,集 中许多杂质, 为铸件的薄弱 环节。
4、防止产生变形
某些壁厚均匀的细长铸件,较大面积的平板铸件,以及壁 厚不均匀的长形箱体都会由于应力而产生翘曲变形,应采用合 理的结构设计予以解决。
结构工艺性
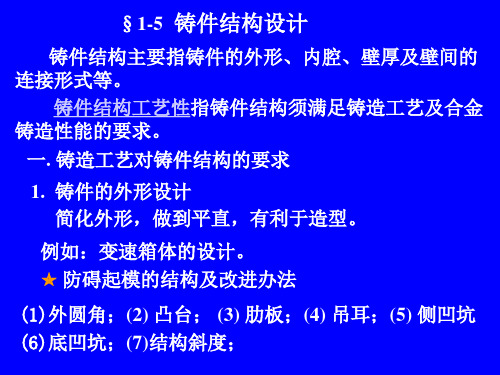
定、排气和简化铸件清理。
避免使用型芯
减少分型面和型芯的数量
便于铸件的清理
利于砂芯的固定
大型整体
分体铸后连接
正确采用大 型整体、分体铸 后连接、分体铸 后焊接或小件连 体铸造结构。
分体铸后焊接
二、合金铸造性能对铸件结构的要求 1. 铸件壁厚大小要合适
铸件壁厚大小主要与合金种类及铸件轮廓尺寸有关。 对于重载壁,切忌盲目增大壁厚,可用加强筋结构。
结构工艺性极差的箱体
改进后的箱体
将外部侧凹改成斜直表面
分型面设计成平面,可避免挖砂造型,方便模板制零件的非加工面上设置的,直接标注在零件 图上;起模斜度是在零件的加工面上放出的,在绘制铸造工艺 图或模样图时使用。
2. 铸件的内腔设计 应尽量避免或减少型芯的数量,并有利于型芯的固
§1-5 铸件结构设计
铸件结构主要指铸件的外形、内腔、壁厚及壁间的 连接形式等。
铸件结构工艺性指铸件结构须满足铸造工艺及合金 铸造性能的要求。
一. 铸造工艺对铸件结构的要求 1. 铸件的外形设计
简化外形,做到平直,有利于造型。
例如:变速箱体的设计。 防碍起模的结构及改进办法
(1)外圆角;(2) 凸台; (3) 肋板;(4) 吊耳;(5) 侧凹坑 (6)底凹坑;(7)结构斜度;
总结
收缩时,极易产生热应力。采用曲面或奇数轮辐,利用
铸件微量变形可减小内应力。
5. 避免大的水平面 大平面受高温金属液烘烤时间长,易形成夹砂缺陷;
金属液中气体、熔渣上浮滞留在上表面,使之产生气孔、 渣孔缺陷;而且大平面不利于金属液充填,易产生浇不 足和冷隔缺陷。
三.不同的铸造方法对铸件结构的要求 1.熔模铸件 (1)便于从压型中取出腊模; (2)孔、槽不应过小、过深; (3)尽量避免大平面。
避免使用型芯
减少分型面和型芯的数量
便于铸件的清理
利于砂芯的固定
大型整体
分体铸后连接
正确采用大 型整体、分体铸 后连接、分体铸 后焊接或小件连 体铸造结构。
分体铸后焊接
二、合金铸造性能对铸件结构的要求 1. 铸件壁厚大小要合适
铸件壁厚大小主要与合金种类及铸件轮廓尺寸有关。 对于重载壁,切忌盲目增大壁厚,可用加强筋结构。
结构工艺性极差的箱体
改进后的箱体
将外部侧凹改成斜直表面
分型面设计成平面,可避免挖砂造型,方便模板制零件的非加工面上设置的,直接标注在零件 图上;起模斜度是在零件的加工面上放出的,在绘制铸造工艺 图或模样图时使用。
2. 铸件的内腔设计 应尽量避免或减少型芯的数量,并有利于型芯的固
§1-5 铸件结构设计
铸件结构主要指铸件的外形、内腔、壁厚及壁间的 连接形式等。
铸件结构工艺性指铸件结构须满足铸造工艺及合金 铸造性能的要求。
一. 铸造工艺对铸件结构的要求 1. 铸件的外形设计
简化外形,做到平直,有利于造型。
例如:变速箱体的设计。 防碍起模的结构及改进办法
(1)外圆角;(2) 凸台; (3) 肋板;(4) 吊耳;(5) 侧凹坑 (6)底凹坑;(7)结构斜度;
总结
收缩时,极易产生热应力。采用曲面或奇数轮辐,利用
铸件微量变形可减小内应力。
5. 避免大的水平面 大平面受高温金属液烘烤时间长,易形成夹砂缺陷;
金属液中气体、熔渣上浮滞留在上表面,使之产生气孔、 渣孔缺陷;而且大平面不利于金属液充填,易产生浇不 足和冷隔缺陷。
三.不同的铸造方法对铸件结构的要求 1.熔模铸件 (1)便于从压型中取出腊模; (2)孔、槽不应过小、过深; (3)尽量避免大平面。
第5章铸件结构设计
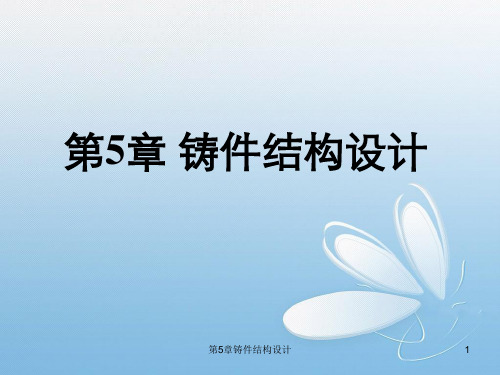
②在载荷的作用下,直角处的内侧产生应力集中,使内侧实际承受的应 力较平均应力大大增加(图2-53a);
③一些合金的结晶过程中,将形成垂直于铸件表面的柱状晶。若采用直 角联接,则因结晶的方向性,在转角的分角线上形成整齐的分界面(图 2-54a),在此分界面上集中了许多杂质,使转角处成为铸件的薄弱环节。
铸 造 铸件尺寸 方 (mm) 法
砂 <200×200 型 200×20~ 铸 500×500 造 >500×500
合金种类
铸钢 灰口铸铁 球墨铸铁 可锻铸铁 铝合金
8
5~6
6
5
3
10~12 6~10128 Nhomakorabea4
15~20
15第 ~52章0铸件结构15设~计20 10~12
6
铜合金 3~5 6~8 10~12
b>2a
R≥(1/6~1/3)(a+b)/2;R1≥R+(a+b)/2 C≈3(b-a)1/2,h≥(4~5)C
第5章铸件结构设计
22
4.减缓筋、辐收缩的阻碍
缺陷分析:铸件各部分冷却速度不同而收缩不一致,形成较大的 内应力。当此应力超过合金的强度极限时,铸件会产生裂纹。
• 实例分析:轮缘、轮辐、轮毂间若比例不当,
第5章铸件结构设计
3
第一节 铸件设计 的内容
一、铸件外形的设计
1 .避免外部侧凹、凸起; 2 .分型面应尽量为平直面; 3 .凸台、筋条的设计应便于起模。
下
中
中
下
上
上
第5章铸件结构设计
4
避免铸件的外形有侧凹。
第5章铸件结构设计
5
第5章铸件结构设计
6
结构斜度
③一些合金的结晶过程中,将形成垂直于铸件表面的柱状晶。若采用直 角联接,则因结晶的方向性,在转角的分角线上形成整齐的分界面(图 2-54a),在此分界面上集中了许多杂质,使转角处成为铸件的薄弱环节。
铸 造 铸件尺寸 方 (mm) 法
砂 <200×200 型 200×20~ 铸 500×500 造 >500×500
合金种类
铸钢 灰口铸铁 球墨铸铁 可锻铸铁 铝合金
8
5~6
6
5
3
10~12 6~10128 Nhomakorabea4
15~20
15第 ~52章0铸件结构15设~计20 10~12
6
铜合金 3~5 6~8 10~12
b>2a
R≥(1/6~1/3)(a+b)/2;R1≥R+(a+b)/2 C≈3(b-a)1/2,h≥(4~5)C
第5章铸件结构设计
22
4.减缓筋、辐收缩的阻碍
缺陷分析:铸件各部分冷却速度不同而收缩不一致,形成较大的 内应力。当此应力超过合金的强度极限时,铸件会产生裂纹。
• 实例分析:轮缘、轮辐、轮毂间若比例不当,
第5章铸件结构设计
3
第一节 铸件设计 的内容
一、铸件外形的设计
1 .避免外部侧凹、凸起; 2 .分型面应尽量为平直面; 3 .凸台、筋条的设计应便于起模。
下
中
中
下
上
上
第5章铸件结构设计
4
避免铸件的外形有侧凹。
第5章铸件结构设计
5
第5章铸件结构设计
6
结构斜度
铸件结构设计

铸件结构设计
铸件壁厚 力求均匀, 避免局部 过厚形成
避免铸造缺陷的合理结构
回到主页
热节的结
构 不合理 合理
成形工艺基础-铸件结构 设计
23
回到主页
铸件结构设计
铸件壁厚 力求均匀, 避免局部 过厚形成
避免铸造缺陷的合理结构
热节的结
构
不合理
合理
成形工艺基础-铸件结构 设计
24
铸件结构设计
避免铸造缺陷的合理结构
避免铸件产生 翘曲变形和大
的水平平面结
构
不合理
成形工艺基础-铸件结构 设计
合理
29
回到主页
铸件结构设计
避免铸造缺陷的合理结构
避免铸件产 生翘曲变形
和大的水平
平面结构 不合理 合理
成形工艺基础-铸件结构 设计
30
回到主页
铸件结构设计
避免铸造缺陷的合理结构
避免铸件产生 翘曲变形和大
的水平平面结
构 不合理
成形工艺基础-铸件结构 设计
40
回到主页
铸件结构设计
简化工艺过程的合理结构
不 合 理
铸件结构应有 利于型芯的固 定、排气和清 理
合 理
成形工艺基础-铸件结构 设计
41
铸件结构设计
结合铸造方法的合理结构 熔模铸造成形件的结构
回到主页
设计熔模铸造时应考虑 的问题:
•便于从压型中取出蜡模 和型芯 •孔、槽不宜过小或过深 •壁厚均匀、同时凝固、 避免分散的热节
合 理
成形工艺基础-铸件结构 设计
33
铸件结构设计
简化工艺过程的合理结构
不 合 理碍拔模的 局部凹陷结构
砂型铸件的结构设计

• • • •
1.蜡模的制造 制造压型要经过以下程序。 (1)压型制造 压型一般用钢、铜和铝经切削加工制成,这种压 型的使用寿命长,制出的蜡模精度高,但压型成 本高,生产准备时间长,主要用于大批量生产。 对于小批量生产,则可采用易熔合金(Sn、Pb、 Bi等组成的合金)、塑料或石膏直接向模样(母模) 上浇注而成。 • (2)蜡模的压制 • 料冷却凝固便可从压型中取出,然后修去分型面 上的毛刺,即得单个蜡模(图8—3(c))。 • (3)蜡模组装
• 2.合理设计铸件内腔 • (1)尽量不用或少用型芯 图9-5。 • 铸件的内腔也可以利用型腔内的砂垛(上箱 砂垛称吊砂)来形成。图9-6。
• (2)便于型芯固定、排气和铸件清理 图9-7所示轴承架。 • 对于因型芯头不足难以固定的铸件,在不影响使用的前 提下,可增加芯头数量,为此可设计出适当大小和数量的 工艺孔。如图9-8所示铸件,因底面没有型芯头,只好用 型芯撑固定;改为图9-8(b)后。铸件底面上增设两个工艺 孔,型芯为一整体,稳定性提高,下芯简便,易于排气和 清理。如果铸件上不允许有些工艺孔,可以用螺钉或柱塞 堵住.
• 3.脱蜡和造型 • (1)为了从型壳中取出蜡模以形成铸型空腔,还必 须进行脱蜡。 • (2)造型 为了提高型壳的强度,防止浇注时变形 或破裂,将脱蜡后的型壳置于铁箱中,周围用干砂 填紧,有时也叫填砂。 • 4.焙烧和浇注 • (1)焙烧 将型壳送入加热炉内,加热到800~ 1000℃进行焙烧,使其所含的残余挥发物得到进 一步排除。 • (2)浇注 为了提高液态合金的填充能力,防止浇 不足、冷隔等缺陷,要在焙烧后起热(600--700℃) 进行浇注。
• 图9-2所示为机床上一铸件。图9-2(a)在A-B截面两侧设计 成凹坑,造型时必须采用两个较大的外型芯才能取出模 样.若改为图9-2(b)所示结构,将凹坑扩展成通到底部的 凹槽则可省去外部型芯。显然,后一方案是比较合理的。
铸造工艺图及设计实例

xx年xx月xx日
铸造工艺图及设计实例
铸造工艺图概述铸造工艺图的设计原则及实例铸造设计的材料选择与处理铸造设计的结构优化与实例铸造工艺图的应用与发展
contents
目录
铸造工艺图概述
01
铸造工艺图是一种用图形方式表示铸造生产全过程的工艺方案,包括铸造方法、工艺参数、浇注位置、分型面、起模斜度、浇注系统、补缩系统、冷却系统、出渣和排气系统等。
满足使用性能要求
结构设计时应根据产品使用性能要求,合理确定结构形式和材料,同时考虑表面粗糙度、尺寸精度等参数。
确保力学性能
铸造件应具有相应的力学性能,如强度、刚度、耐磨性等,以满足使用过程中的各种应力条件。
铸造结构设计的基本原则
优化浇注系统
浇注系统是铸造过程中的重要环节,通过优化浇口、冒口、浇道等的设计,提高金属液的填充平稳性和补缩效果。
5G技术
铸造工艺图的设计将结合AI技术,实现智能设计、优化生产等功能。
AI技术
铸造工艺图的设计将更加注重绿色制造,采用更加环保的材料和工艺。
绿色制造
THANKS
感谢观看
确定铸造方法
设计铸造工艺方案
绘制铸造工艺图
根据铸件的大小、形状和材料等因素,选择合适的铸造方法,如砂型铸造、金属型铸造等。
根据铸造方法,制定详细的铸造工艺方案,包括造型、浇注系统、冷却系统、浇口和冒口等。
根据铸造工艺方案,绘制铸造工艺图,包括总装图、零件图、工艺尺寸和公差等。
缸体浇注系统
缸体浇注系统的设计是铸造工艺图的关键环节之一,需要合理规划浇口和冒口的数量、位置和尺寸,以保证充型完整和金属液的补缩。
03
铸造工艺图的应用范围
02
01
- 1、下载文档前请自行甄别文档内容的完整性,平台不提供额外的编辑、内容补充、找答案等附加服务。
- 2、"仅部分预览"的文档,不可在线预览部分如存在完整性等问题,可反馈申请退款(可完整预览的文档不适用该条件!)。
- 3、如文档侵犯您的权益,请联系客服反馈,我们会尽快为您处理(人工客服工作时间:9:00-18:30)。
返
回
(2) 厚薄壁间的连接应逐步过渡 铸件各部分的壁厚不可能完全均匀,设计时不同壁厚间 的连接应采用逐步过渡,避免壁厚突变,如下图示。
返
回
(3) 肋或壁的连接应避免交叉和锐角 如左下图所示和右图所示,主要目的是减少金属积聚, 防止铸造缺陷的产生。
返
回
3、 铸件应尽量避免有过大的水平面 铸件的大平面,易产生浇不到、冷隔等缺陷;平面型腔 的上表面,因受金属液长时间烘烤,易产生夹砂;大平面也 不利于气体和非金属夹杂物的排出。因此,应把铸件的大平 面设计成可以避免上述缺陷的倾斜结构,如下图所示。
四、浇、冒口系统
1. 浇注系统 1)浇注系统的组成及作用 2)浇注系统的常见类型 ① 封闭式浇注系统 ΣF直>ΣF横>ΣF内 ΣF直∶ΣF横∶ΣF内=1.15∶1.1∶1 ② 开放式浇注系统 ΣF直<ΣF横<ΣF内 ΣF直∶ΣF横:ΣF内=1∶2∶4
2. 冒口
冒口是在铸型中设置的一个储存金属液的空腔。 冒口
返
回
2、分型面应少而简单 铸件分型面的数量应尽量少,且尽量为平面,以利于减 少砂箱数量和造型工时,简化造型工艺,提高铸件尺寸精度。 如图所示。
改进前
改进后
返
回
3、 尽量或少用型芯和活块 型芯和活块会增加工艺的复杂性,增加工作量,提高 成本,并易产生缺陷,如下图所示。
返
回
4、应有结构斜度 凡垂直于分型面的非加工面都应有一定的倾斜度,即结 构斜度。如下图所示。结构斜度可使起模方便,延长模样寿 命,起模时不易损坏型腔表面,从而提高了铸件的尺寸精度, 此外,结构斜度还可使铸件美观。
第2节 特种铸造
三、压力铸造
将熔融的金属在高压下,快速压入金属铸型的型腔中,并在压 力下凝固,以得到铸件的一种铸造方法。 1、工艺特点: 高速高压。 多用于非铁合金(如铝、铜、镁等)精密铸件的批量生产。
2、工艺过程: 压力铸造
第2节 特种铸造
四、离心铸造
将熔融的金属浇入高速旋转的铸型中,使金属液在离心力的作 用下凝固成形,以得到铸件的一种铸造方法。 1、工艺特点: 组织紧密,铸件质量好。 用于生产空心铸件。
1、工艺特点:
一型多铸,铸件精度高,力学性能好,但成本高,主要用于大批 大量生产铜、铝、镁等非铁合金铸件。
2、工艺过程:
金属型铸造
第2节 特种铸造
二、熔模铸造
将蜡料制成模样,在上面涂以若干层耐火涂料制成型壳,然后 加热型壳,使模样熔化、流出,并焙烧成有一定强度的型壳,再经 浇注,去壳而得到铸件的一种铸造方法。 1、工艺特点: 以熔化模样为起模方式。铸件精度高,是少无切削加工的方法之 一。其设备简单,生产批量不受限制,主要用于大批、大量生产。 其缺点是工艺过程复杂,生产周期长。 2、工艺过程: 熔模铸造
返
回
第6节 特种铸造
第6节 特种铸造
引言:
1、概念:特种铸造是指砂型铸造以外的其他铸造方法。 2、特种铸造的特点: 铸件精度高,力学性能好;生产率高;工人 劳动条件好等。 3、常用的特种铸造方法:
金属型铸造 压力铸造 熔模铸造 壳型铸造 离心铸造
第6节 特种铸造
一、金属型铸造
将液态金属注入用金属制成的铸型中,以获得铸件的方法。
200×200500×500
>500500
为减轻铸件的重量,便于固定型芯可在壁厚处开窗口,如下 图所示。
返
回
2 、 铸件壁的连接应 逐步过渡
铸件壁的连接处容易 产生铸造缺陷,设计时, 应避免壁厚突变、尖角等, 防止产生金属积聚。
(1)圆角结构
如下图所示,a图为直 角连接,直角处金属积聚, 易产生缩孔、缩松;内侧 转角处容易产生应力集中, 从而导致裂纹。为防止这 些缺陷,必须采用b图的圆 角结构。圆角是铸件结构 的基本特征。
①
下 下
①
二、分型面的选择
1. 分型面应选在铸件的最大截面处。 2. 应尽量使铸件的全部或大部置于同一砂箱,以保证铸件
的尺寸精度。
上
① ②
中
下
① ②
3. 应尽量减少分型面的数量,并尽可能选择平面分型。
②
上 下 上 下 ②
上
下 上 下 ①
①
4. 为便于造型、下芯、合箱及检验铸件壁厚,应尽量使型
腔及主要型芯位于下箱。
2、工艺过程: 离心铸造
整模造型
刮板造型
假箱造型
挖砂造型铸造
熔模铸造
压力铸造
离心铸造
分模造型
工的依据。
返 回
一、浇注位置的选择
浇注时铸件在铸型中所处的空间位置。 1.铸件的重要加工面和受力面应朝下或位于侧面 2. 应将面积较大的薄壁部位置于铸型下部,或使其倾斜位置 3.铸件的大平面应朝下 4.为防止铸件产生缩孔、缩松的缺陷,应使铸件的厚大部位朝 上或侧放 ②
上 下 下 上
下
②
上
上 下
上
上
铸造工艺图与铸件图
铸件结构设计
铸造工艺图与铸件图
为保证铸件的质量,提高产生产率,降低成本,铸造生产需根据零 件的结构特点、技术要求、生产批量和生产条件等进行铸造工艺设计, 并绘制成图。 铸造工艺图是根据上述要求表示铸型分型面、浇冒口系统、浇注系 统、浇注位置、型芯结构尺寸、控制凝固措施(冷铁、保温衬板)等的 图样。它是按规定的工艺符号或文字、数字,将制造模样和铸型所需的 资料,用红蓝线条直接绘在铸件图上或另绘在工艺图样上,是进行生产 准备、指导铸件生产的基本工艺文件。 铸件图是指反映铸件实际形状、尺寸和技术要求的图样。它是根据铸造 工艺图绘制的,用图形、工艺符号和文字标注。其内容:包括切削余量、 工艺余量、不铸出的孔槽、铸件尺寸工差、加工基准、铸件金属等级、 热处理规范、铸件验收技术条件等。铸件图是铸造生产、技术检验、铸 件清理和成品检验的依据,也是设计、制造工艺装备和切削加
返
回
二、 铸造性能对铸件结构的要求 1、 铸件壁厚应力求均匀 铸件壁厚不均匀,会导致冷却不均匀,引起大的内应力,从而使铸件 产生变形和裂纹,还会因金属积聚产生缩孔,铸件壁厚只有选择适当,才 能保证铸件的力学性能。 铸件的最小壁厚主要取决于合金的种类、铸造方法和铸件尺寸。砂型 铸造的最小壁厚见下表。 为保证壁厚均匀和铸件的力学性能,设计结构时,应根据载荷性质和 大小,合理选择截面形状,并在脆弱处增设加强筋。 铸件尺寸 /mm <200×200 最小允许壁厚/mm 灰铸铁 5-6 6-10 15-20 铸钢 6-8 10-12 18-25 铝合金 3 4 5-7 铜合金 3-5 6-8 说明 1、 结构复杂以 及高强度灰铸件, 应取最大值 2、对于特大铸件, 还可以增林壁厚 的尺寸
明冒口 暗冒口
液态成形工艺设计实例
材料:HT200
②
收缩率:1.0 %
③
下
上
①
下 上
Ⅰ
上 下
Ⅱ
4
右 图是省 略浇注 系统的 支承台 零件图、 铸件图 和铸造 工艺图。
返
回
铸件的结构工艺性
铸件的结构工艺性是指所设计的零件在满足使用性能要求的前 提下,铸造成形的可行性和经济性及铸造成形的难易程度。铸件结 构工艺性是否合理直接影响着铸件质量、生产率以及成本。 一、 铸造工艺对铸件结构的要求 1、 铸件外形应力求简单 铸件外形尽可能采用平直轮廓,尽量少用非圆曲面,以便于制 模、造型和简化铸造生产的各个工序,如下图所示(图中A、B处是 曲面)。
返
回
4、铸件结构应有利于自由收缩 铸件收缩受阻是产生内应力、变形和裂纹的根本原因。 设计铸件结构时应尽量使其能自由收缩。如下图所示, a 图 中的轮辐由于内应力大,使轮辐或轮沿容易产生裂纹, b 图 和c图中的轮辐可借助轮辐的微量变形自行减小应力。
返
回
三、组合铸件的应用 对于大型或形状复杂的铸件,在不影响其精度、强度和 刚度的要求下,为使铸件结构简单合理,便于造型、浇注和 切削加工,可将其分成几个小铸件进行分铸,经机加工(或 粗加工)后,再用焊接或螺栓将其组合成整体。
三、工艺参数的确定
1.机械加工余量和铸孔
生产批量 大量生产 成批生产 单件、小批生产
2.起模斜度
最小铸出孔直径 灰口铸铁件 铸钢件 12~15 30~50 15~30 50 30~50
3.铸造圆角
圆角半径一般约为相交两壁平均厚度的1/3~1/2。 4.铸造收缩率 通常灰铸铁为0.7~1.0%,铸造碳钢为1.3~2.0%,铝硅 合金为0.8~1.2%,锡青铜为1.2~1.4%。 5 .型芯及芯头 型芯的功用是形成铸件的内腔、孔洞和形状复杂阻碍起模 部分的外形。 芯头的作用: 1)定位作用; 2)固定作用; 3)排气作用。