MTC10使用手册
交通信息采集实验指导书10-27
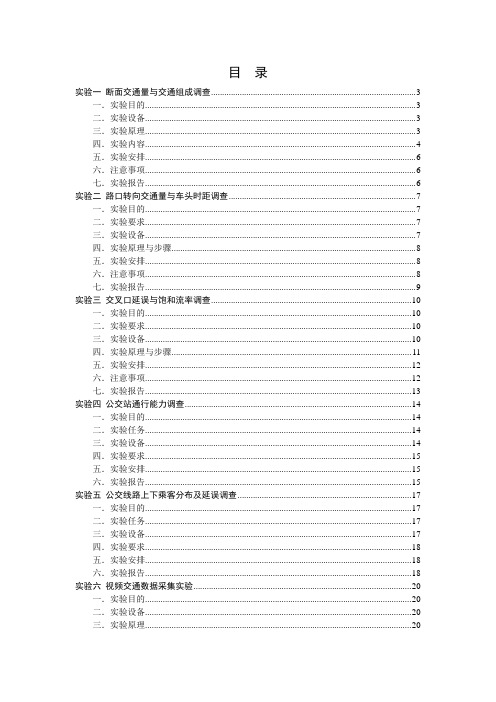
目录实验一断面交通量与交通组成调查 (3)一.实验目的 (3)二.实验设备 (3)三.实验原理 (3)四.实验内容 (4)五.实验安排 (6)六.注意事项 (6)七.实验报告 (6)实验二路口转向交通量与车头时距调查 (7)一.实验目的 (7)二.实验要求 (7)三.实验设备 (7)四.实验原理与步骤 (8)五.实验安排 (8)六.注意事项 (8)七.实验报告 (9)实验三交叉口延误与饱和流率调查 (10)一.实验目的 (10)二.实验要求 (10)三.实验设备 (10)四.实验原理与步骤 (11)五.实验安排 (12)六.注意事项 (12)七.实验报告 (13)实验四公交站通行能力调查 (14)一.实验目的 (14)二.实验任务 (14)三.实验设备 (14)四.实验要求 (15)五.实验安排 (15)六.实验报告 (15)实验五公交线路上下乘客分布及延误调查 (17)一.实验目的 (17)二.实验任务 (17)三.实验设备 (17)四.实验要求 (18)五.实验安排 (18)六.实验报告 (18)实验六视频交通数据采集实验 (20)一.实验目的 (20)二.实验设备 (20)三.实验原理 (20)四.实验流程 (21)五.实验安排 (21)六.注意事项 (21)七.实验报告 (21)实验七车速调查实验 (22)一.实验目的 (22)二.实验仪器设备 (22)三.实验原理 (22)四.实验要求 (23)五.实验流程 (24)六.人员安排 (27)七.实验思考 (27)实验一断面交通量与交通组成调查一.实验目的1. 掌握MC5600型气压管交通检测器、MMU51便携式交通流车辆分析仪的使用方法。
2. 掌握MMC5600型气压管检测器数据处理系统的使用方法。
3. 了解MC5600型气压管检测器、MMU51便携式交通流车辆分析仪的基本工作原理。
4. 了解MC5600型气压管检测器、MMU51便携式交通流车辆分析仪的特点及适用范围。
MTC加密读卡器操作手册

l 读卡器加密设置 注意:读卡器出厂原始密码为 FFFFFF,修改的新密码仅为数字,且务必记住新密码。
1.打开读卡器加密软件。 2.选择读卡器密码,在“6 位原始密码”信息框内填入:FFFFFF(出厂默认) ; 6 位新密码信息框内输入 新密码(限数字);确认新密码信息框内再次输入 6 位新密码确认。按确认就可以完成设置密码了。 如 下图 (@1CHANGE THE HOST PASSWORD Ok 有返回表示修改读卡器密码成功;)
②:8 位插座均为程式调式升级备用接口 (备用) ③:加密操作同上面读卡器加密操作一样(只需把
开关拨置 RS232 状态或连接发行器 RS232 接口即可对卡片进行加密操作 (须断电重启),前提是发行 器密码必须将密码改成与原读卡器密码一致。)
产品保修条款:
1、 保修期限:18 个月 2、 保修范围:非人为因素损坏。正常使用情况下,产品出现故障。
USB/电源复用接口:USB 供电、USB 转 RS232、USB 转 PS2 等接口。
C.外部开关操作及插座说明:
① RS232/PS2 切换开关 :当开关拨置 PS2, 断电重启此时 USB 接口输出为 PS2 数据格 式(模拟键盘);当开关拨置 RS232,断电重 启此时 USB 接口输出为 RS232 数据格式(模 拟串口);
红外信号扫描范
l 功能设置 产品外部结构
远距离读卡器
休眠中的远距
整机尺寸:248*330*55(mm)
金 金属后盖
万向调节器
金 金属防水箱
金属面盖
立杆尺寸:1500*60mm
采用两层防水结构设计全金属材料,内置金属防水箱安装线路板,防水等级达 IP67 级。金属表面烤漆, 户外使用不褪色;读卡器与立杆之间使用万向连接器连接,安装、调试极为方便;紧固件螺丝全部使 用 SUS304 材质。整机设计坚固耐用,防护等级高,大大降低了产品维护率。
Met One 010C 风速传感器用户手册说明书

MODEL010CWIND SPEED SENSOROPERATION MANUALMet One Instruments, IncCorporate Sales & Service: 1600 NW Washington Blvd. Grants Pass, OR 97526 Tel (541) 471-7111 Fax (541) 471-7116******************1.0 GENERAL INFORMATION1.1 The 010C Wind Speed Sensor uses a durable, three-cup anemometer assembly andsolid-optical link with a 40-slot chopper disk to produce a pulsed output whosefrequency is proportional to wind speed. An internal heater reduces moisture forextended bearing life. This sensor is usually used in conjunction with the 191 Cross arm Assembly. The sensor may be used with a translator module, or used directlywith a variety of data loggers.1.2 The Sensor Cable has a quick-connect connector with vinyl jacketed, shielded cable.Cable length is given in -XX feet on each cable part number. A 1953-XX cable isused with translators having terminal strip connections.Table 1-1Model 010C Wind Speed Sensor SpecificationsPerformance CharacteristicsMaximum Operating Range 0-60 meters/sec or 0-125 mphStarting Speed 0.27 meters/sec or 0.6 mphCalibrated Range 0-50 meters/sec or 0-100 mphAccuracy ±1% or 0.15 mphTemperature Range -50︒C to +85︒CResponse Distance constant less than 5 ft of flow**The distance traveled by the air after a sharp-edged gust has occurred for theanemometer rate to reach 63% of the new speed. Distant constant less than 15ft of flow with optional 010C-1 aluminum cupset.Electrical CharacteristicsPower Requirements 12 VDC at 10 mAOutput Signal 11-volt pulseOutput Impedance 100 ohms maximumHeater Power Requirement 12 VDC at 350 mAStandard Cable Length 300’ maximum (consult factory if longercable is to be used for special requirements) Physical CharacteristicsWeight 1.1 poundsFinish Anodized aluminumMounting Use with 191 CrossarmCabling 1953-XX Cable (XX is cable length in feet)Optional AccessoriesA. External heater and power supply for extreme low temperature operation.B. Ice Skirt for extreme icing environments.C. Aluminum cup assembly.2.0 INSTALLATION2.1 The 010C Wind Speed InstallationA. Mount the cup assembly and secure with the Allen head set screw, check to seethat the cup assembly rotates freely.B. Install the sensor in the end of the Model 191 Crossarm Assembly (the endwithout the bushing).C. Tighten the locking set screw. Do not over-tighten. Apply a small amount ofsilicone grease to set screws to prevent freezing in adverse environments.D. Connect the cable assembly to the keyed sensor receptacle and tape it to themounting arm.2.2 WiringA. The cable assembly contains five wires. Typical wiring hookup is shown inFigure 2-1.No Connection White/Brown ShieldElectrical ConnectorView looking at connector pins. (Pins are also identified on connector).2.3 Lightning ProtectionA. Weather sensors are sensitive to direct or nearby lightning strikes. A well-grounded metal rod or frame should be placed above the sensor installation. Inaddition, the shield on the signal cable leading to the translator must beconnected to a good earth ground at the translator end and the cable routeshould not be vulnerable to lightning.3.0 OPERATIONAL CHECK-OUT AND CALIBRATION3.1 010C Wind Speed Sensor Check-OutA. Spinning the anemometer cup assembly will produce a series of pulses (40pulses per revolution). To verify sensor output, monitor this signal with either thetranslator module, data logger, or an oscilloscope. (Refer to Frequency vs. WindSpeed Table 3-1). Spinning the hub of the wind speed transmitter without thecup assembly mounted and allowing it to coast to a stop will give a goodindication of threshold performance; a jerky or sudden stop indicates damage tobearings, bent drive shaft, or obstruction in the light chopper.B. Inspect the cup assembly for loose cup arms or other damage. The cupassembly cannot change calibration unless a mechanical part has come loose orhas been broken. If a cup arm is loose or broken the calibration of the sensormay be affected.C. If the sensor heater is used, check internal heater operation by sliding sensorcover down and touching the housing behind the printed circuit board. Thehousing should feel warmer than the adjoining metal parts. The sensor has abuilt-in heater that is designed to provide a raise in the internal temperature,providing a small amount of positive pressure. This heater requires as external12 V (@500ma) power supply.FREQUENCY vs WIND SPEED FOR 010 SENSORTABLE 3-1Transfer FunctionsMiles per hour: Meters per second:rpm = 16.767 * (V mph - 0.6) rpm = 37.522 * (V m/s - 0.27) V mph = (rpm / 16.767) + 0.6 V m/s = (rpm / 37.522) + 0.27 f Hz = (V mph - 0.6) / .08946 f Hz = (V m/s - 0.27) / 0.039976 V mph = V m/s * 0.44704 V m/s = V mph / 0.447044.0 MAINTENANCE AND TROUBLESHOOTING4.1 General Maintenance Schedule*6 – 12 Month Intervals:A. Inspect sensor for proper operation per Section 4.2.B. Replace wind speed sensor bearings in extremely adverse environments perSection 4.5.12 – 24 Month Intervals:A. Recommended complete factory overhaul of sensor.*Schedule is based on average to adverse environments.Table 4-1010C Wind Speed Sensor TroubleshootingSymptom Probable Cause Solution Refer toNo wind speed output Loss of supplyvoltage Check translator +12supply & connectingcablesFigure 2-1Faulty integratedamplifierReplace circuit board Section 4.5Faulty diodes,D1, D2Replace circuit board Section 4.5Faulty detector Replace detector Section 4.6No wind speed outputbelow 2-5 mphBad bearing(s) Replace bearing(s) Section 4.4Faulty detector Replace detector Section 4.6Wind speed signal drops ouas speed increasesFaulty detector Replace detector Section 4.64.2 010C Wind Speed Sensor: 6 – 12 Month Periodic ServiceA. At the crossarm assembly, disconnect the quick disconnect plug from the sensor(leave the cable secured to the crossarm) and remove the sensor from thecrossarm assembly.B. Loosen the set screw holding the cup assembly. Support the rotating hub of thesensor with one hand and pull the anemometer cup assembly free.C. Visually inspect the anemometer cups for cracks and breaks. Also, make surethat each arm is securely attached to the cup assembly hub.D. Slide the sensor cover down to expose the light-chopper disc assembly, lightsource, detector, and circuit board.E. Inspect the interior of the sensor for any signs of corrosion and/or dust buildup.F. Inspect the light-chopper for cracks, and make sure that all slots are free ofcorrosion.G. Inspect the signal-conditioning module for cracks and corrosion around solderedconnections.H. Rotate the sensor hub assembly to ensure that it turns freely and that the sensorbearings are not damaged. Make sure the light-chopper assembly is notcontacting the light source and detector.I. Apply a small amount of silicone lubricant. (Dow-Corning DC-33 or equivalent) tothe sensor O-ring seals; slide the cover up over the sensor and wipe off anyexcess lubricant.J. A moisture vent is located on the base of the sensor; make sure that this vent is clear.K. Re-install sensor according to installation procedure (Section 2.0); verify proper operation using procedures in Section 3.0.4.3 010C Wind Speed Sensor Maintenance (Refer to 010C Sensor Assembly Drawing)The following procedures require a relatively clean, dry work area, a source of 12VDC power at approximately 20 mA, and an oscilloscope (DC to 10 KHz minimumrange required.4.4 Sensor Bearing Replacement. (Refer to 010C Sensor Assembly Drawing)A. Remove sensor from tower and remove cup assembly (1). Refer to Section 4.2.B. Disassemble sensor and remove old bearings (6).1. Slide the sensor cover (16) down to expose the light-chopper discassembly (10), detector assembly (12) and circuit board (18).2. Loosen both special set screws on the shaft of the light chopper assembly(11).3. Support the light-chopper assembly (10) with one hand and slowly pullthe rotating hub/shaft assembly (2) out of the column (8).4. Remove the shield (4) and slinger (5) from the column (8).5. Remove the light-chopper assembly (10) from the sensor housing, beingcareful not to damage the slots located between the light-chopper holderand the lower bearing.6. Insert the lower end of the rotating hub/shaft assembly into the upperbearing, cock it slightly to one side and push out the lower bearing.7. Insert a right-angle type of tool, such as an Allen wrench, into the upperbearing; cock it slightly to one side and remove the bearing.8. Clean dirt from bearing bores, using a cotton swab and alcohol.C. Install the new bearings and assemble the sensor.1. Install new upper and lower bearings in the column (8). Bearings shouldslide easily into bearing bores.2. Install a slinger and shield (4, 5) on the column assembly. Use new partsif old ones are damaged or corroded.3. Insert the rotating hub shaft (2) into the column assembly (8), through theshield (4), slinger, and upper bearing, until it starts to protrude through thelower bearing.4. Support the light-chopper assembly (10) with one hand and slowly pushthe rotating hub shaft into it until the shaft almost touches the bottom.5. Tighten both special set screws on the light-chopper assembly; do notover tighten as the set screw tips will damage the shaft.6. Rotate the sensor hub assembly (2) to ensure that it turns freely and thatan endplay of about .005” exis ts.7. Hold sensor vertically and make sure that the light-chopper assembly (10)is not contacting the detector assembly (12).8. Apply small amount of silicone lubricant (Dow-Corning DC-33 orequivalent) to the sensor O-rings (9); slide the cover (16) up over thesensor and wipe off any excess lubricant.D. Replace cup assembly and re-install (refer to Section 2.0)4.5 1200-1 Circuit Board Assembly Replacement (Refer to 010C Assembly Schematic)A. Remove sensor from tower and remove cup assembly (refer to Section 4.2).B. Slide the sensor cover (16) down to expose the light-chopper disc assembly (10),detector assembly (12), and circuit board (18).C. Remove two screws (17) holding circuit board assembly (18) and lift circuit boardaway from sensor housing.D. Note color of wires and then unsolder wires to detector assembly from circuitboard and three wires from connector (19).E. Install new circuit board assembly by reversing above procedure.4.6 Detector Assembly Replacement Refer to 010C Assembly Schematic)NOTE: 010C sensors SN M10560 and later use 520253 photodetector. Oldersensors use 1074 photodetector assemblies.A. Remove sensor from tower and remove cup assembly. Refer to Section 4.2.B. Slide the sensor cover (16) down to expose the light-chopper disc assembly (10),detector assembly (12) and circuit board (18).C. Remove two screws (17) holding circuit board assembly (18) and lift circuit boardaway from sensor housing.D. Note color of wires and then unsolder wires to detector assembly from circuitboard (18).E. Remove two screws (20) holding detector assembly (12) and remove assembly.F. Install new detector assembly by reversing above procedures.4.7 010C Wind Speed Sensor Repair and Recalibration ServiceThe factory provides fast, economical service for the user. This repair andcalibration service includes disassembly and detailed inspection of all movingmechanical parts and electronic components.Service includes replacement of bearings, regardless of apparent condition, andfunctional test of sensor. Replacement of the following items is also included: O-rings, shield and slinger, shaft, set screws. Other components will be replaced as required. Only charges for additional materials will be added to the basic service charge.Table 4-2Replacement 010C Parts ListRef No.U Description Part No.1 Cup Assembly Lexan - 2672Aluminum – 2672-1 2 Hub/Shaft Assy. 26584 Shield 10095 Slinger 10106 Bearing 10559 O-ring 72012010 Chopper Wheel Assembly 220211 Set Screw 60125012 Photo Detector 520253*13 Heater Clamp 48010014 Heater 80508016 Sensor Cover 267517 PCBA Mounting Screws 60124018 PCBA 1200-120 Detector Assembly Mounting Screws 60127022 Standoff 86005023 Integrated Amplifier 62030024 Nut, Hex, Kep 4-40 60040025 Screw FH 82︒ 4-40 x 3/8 60133026 Screw FH 82︒ 4-40 x ¼ 601240NOTE: 010C sensors SN M10560 and later use the black 520253 photodetector. Earlier sensors use the white 1074 photodetector assemblies.。
Hurco TM10i 倾斜床纵轴铬转机说明书

TM10iThe small footprint, large work cube, chip management system, and affordable price tag of our slant-bed CNC lathes in theTM Series make small batch manufacturing profitable.i i True 30-degree slant-bed casting design promotes:-increased rigidity-larger turning capacity-efficient chip removali i Cast iron frame designed with Finite Element Analysis (FEA)i i Maintenance-free cartridge spindle with permanently greased bearingsi i Bi-directional hydraulic turret decreases tool index timei i Linear motion guideways on all axes:-less friction at higher speeds-easier and less expensive to replacei i Optional tailstock mounted on heavy-duty box ways with live centeri i Large 1.26-inch ball screws X/Z minimize frictioni i Distance between guide ways promotes rigidity-7.87 inches X-axis-12 inches Z-axisTMX8MYSii i More Y-axis travel thancompetitive modelsi i Sub-spindle with chiller i i Cast iron frame designed withFinite Element Analysis (FEA)i i True 30-degree slant-bed castingdesign promotes:-increased rigidity-larger turning capacityefficient chip removalThe TMXMY/S mill turn lathes are true slant-bed lathes with all-digital drives and motors and absolute encoders onall linear axes.i i Large ball screws to minimize friction(1.42-inches X/Z/W + 1.26 inches Y)i i Linear motion guideways on all axes:-less friction at higher speeds-easier and less expensive to replace i i Distance between guide wayspromotes rigidity-10 inches X-axis and Y-axis -18.5 inches Z-axis -11.4 inches WVMX6030i-50TOur signature line of VMX machining centers takes machining to the next level. These machines deliver high performance capabilities to any machining application.i i Solid cast iron framei i Generous Y-axis traveli i Wider table extends across the entire Y-axis, which provides the flexibility needed to produce a high mix of partsi i Table moves completely forwardin the work cube for easy operator accessi i Direct coupled ballscrewsi i Larger, heavy-duty roller ways on all three axesi i Ceramic hybrid spindle bearings with lifetime grease i i30-station electric swing-arm ATC (40-station available for 40T spindle) i i2 second tool-to-tool ATC time for 40T spindle (4 seconds for 50T)i i Yaskawa Sigma 5 drivesi i LED lighting shines brighter and saves energyi i MAX5 ergonomically designed console with two 19” LCD screensi i WinMax Mill Conversational and Industry Standard NC programming i iAdjustable height control armVMX60SRTiThe SR series of 5-axis CNC mills offers multiple advantages, starting with the machine's design configuration that utilizes a swivel head with either an A or C style rotary table.i i Direct drive, embedded, C-axis, rotary torque table-Provides additional 3.5 inches inZ-axis to support taller parts-Embedded rotary table designincreases working surface ofmachine table (66 x 26 inches) tosupport secondary operations andor 3-axis work-Unlimited angular movement:reduces cycle time-Stout table: supports heavier partsi i Solid one-piece cast iron frame optimized with both static and dynamic Finite Element Analysis (FEA) i i Yaskawa Sigma V Digital AC Servosi i2 or 4 passage rotary unions for hydraulics and/or airi i Angular encoders for rotary axesi i Pistol-style coolant and air gunsi i WinMax Mill Conversational andNC Programmingi i5-axis/5-sided software features – Tool Path Linearization, Tool Center Point Management, Transform Plane, 3-D Tool Compensation, Tool Vector Input & Retract, Shortest AngularTraversei i Robust control specifications (standard) – 2.7GHz Dual Core Processor, 4GB RAM Memory, 128GBSolid State Hard DriveVMX30UiThe integrated trunnion table design provides more clearance in Z-axis and the ability to machine heavier parts compared to 3-axis mills with trunnion table added.i i Solid one-piece cast iron frame optimized with both static and dynamic Finite Element Analysis (FEA) i i Yaskawa Sigma V Digital AC Servosi i2 or 4 passage rotary unions for hydraulics and/or airi i Electric, side-mounted, 40-Station swing-arm ATCi i Full Enclosure with wide front access doors and fully contained tool storage i i Dual LED work lightsi i Angular encoders for rotary axesi i Pistol-style coolant and air gunsi i WinMax Mill Conversational andNC Programming i i5-axis/5-sided software features – Tool Path Linearization, Tool Center Point Management, Transform Plane, 3-D Tool Compensation, Tool Vector nput & Retract, ShortestAngular Traversei i Ergonomically designed MAX5 console with twin 19” LCD screensi i Robust control specifications (standard) – 2.7GHz Dual Core Processor, 4GB RAM Memory, 128GB Solid State Hard Drivei i Z-axis regenerative brake –no counterbalanceHM1700RiThe Hurco HM1700Ri horizontal mill increases shop productivity with a rotary torque table added to the smart design of the HM1700i. The 8,000 rpm dual winding spindle is equipped for both high and low end torque operations. The large, front and side access doors provide maximum operator efficiency.With fast rapids, large work cube, a smart frame design andUltiMotion technology, complex production parts can bemachined efficiently and accuratelyi i67 x 51 x 35 in (1,700 x 1,300 x 900 mm) travelsi i67 x 36 in (1,700 x 914 mm) table,6,614 lbs (3,000 kg) capacityi i8,000 RPM spindlei i Brushless AC Servosi i WinMax Mill Conversational and Industry Standard NC programming i i Solid cast iron frame i i Heavy duty linear rails for X, Y, & Z-axis i i Double-nut pretensioned ball screws – twin ball screws on X-axisi i Two pallet systemi i LED lighting shines brighter and saves energyi i NEW MAX5 ergonomically designed dual-screen console with19” LCD screensVC500i5-Axis cantilever design supports a wide range of parts. Premium components and Expert Design. Full 110° in both positive and negative direction of the B-axis providessuperb undercutting ability.i i Integrated trunnion table designprovides more clearance in Z-axis and ability to machine heavier parts compared 3-axis mills with trunnion table addedi i Larger, heavy-duty linear guides on allthree axesi i Solid one-piece cast iron frameoptimized with both static anddynamic Finite Element Analysis (FEA)i i Yaskawa Sigma V Digital AC Servos i i 2 or 4 passage rotary unions forhydraulics and/or airi i Full Enclosure with wide front accessdoors and fully contained tool storagei iAngular encoders for rotary axesi i Pistol-style coolant and air guns i i WinMax Mill Conversational andNC Programmingi i 5-axis/5-sided software features – Tool PathLinearization, Tool Center Point Management, Transform Plane, 3-D Tool Compensation, Tool Vector Input & Retract, Shortest Angular Traversei i Ergonomically designed MAX5 console withtwin 19” LCD screensi i Robust control specifications (standard) –2.7GHz Dual Core Processor, 4GB RAM Memory, 128GB Solid State Hard Drivei i Z-axis regenerative brake –no counterbalanceBX60iHigh Speed Double Column Machine. The stability of the double-column, the ladder design of the Z-axis, and the overall weight of the machine (over 44,000 lbs.) provide exceptionalaccuracy and outstanding surface finish capabilities.i i Direct drive ballscrews i i High speed tool changer i i 18,000 RPM high speed spindle i i 47 hp (35 kW) peak spindlei i Integral motorized spindle equipped with ABEC-7 ceramic hybrid bearingsi i HSK 63 toolingi i Extremely rigid and thermally stabledouble-column designi i Generous Y-travel i i Easy access to tablei i Ladder design of bridge providesmaximum support to the head castingi i Close proximity of spindle to bridgecasting reduces overhangi i Brushless AC Servos i i Solid cast iron framei i Large front door opening. Large, hingedside doors i i Larger, heavy-duty roller ways on allthree axesi i 30-station electric swing-arm ATC i i Yaskawa Sigma 5 drivesi i LED lighting shines brighter and saves energy i i MAX5 ergonomically designed console withtwo 19” LCD screensi i WinMax Mill Conversational and IndustryStandard NC programmingHTL8-60iThese box way, gap bed lathes are user friend and makes it easy to load/unload bulky parts. The gap can be removed to accommodate even larger parts close to the headstock. The WinMax control that slidesalong a rail on the front of the machine allows for ease of use.i i Open bed design – easy to load/unload partsi i Gap can be removed to accommodatelarger parts close to the headstocki i Maintenance-free cartridge spindle withpermanently greased bearingsi i Standard tailstock mounted on heavy-duty box ways with live centeri i Hand wheels located below the controlallow manual operation of machinei i Bi-directional hydraulic 8 station turretdecreases tool index time-turret can be positioned anywhere along the saddle-slotted disc-type holds ¾” tool holders-1-¼” boring bar capacity -bi-directional operationi i Max 5 control is mounted on a set of linearrails that travel along the front of the machinei i Designed with both hardened andground ways-X-axis is solid way and Z-axis is box ways -Lined X-axis and Z-axisi i Large ball screws minimize friction -.98 inch X-axis -1.57 inches Z-axisi i Distance between guide ways promotesrigidity-8.4 inches X-axis -14 inches Z-axisVM30iThe VM series of 3-axis machining centers features a small footprint with a large work cube. No other mill packs as much productivity into such an efficiently designed package.i i Solid cast iron frame i i One-piece machine basei i 50 x 20 x 20 in (1,270 x 508 x 508 mm)travelsi i 52 x 20 in (1,321 x 508 mm) table,2,000 lbs (907 kg) capacityi i 10,000 RPM spindle i i 20 hp (15 kW) peak spindle i i CAT 40 tooling i i Brushless AC Servosi i Larger, heavy-duty linear rails on allthree axesi i Mounted to a machined shoulder forincreased rigidityi i Strategically spaced for increasedstrengthi i Wedge locked to a machined shoulder toreduce vibration instead of faster, cheaper face-milled processi i Electric, side-mounted, 20-station,swing-arm ATCi i 2.5 second tool-to-tool ATC timei i Wider table extends across the entire Y-axis,which provides the flexibility needed to produce a high mix of partsi i Table moves completely forward in the workcube for easy operator accessi i Yaskawa Sigma 5 drivesi i LED lighting shines brighter and saves energy i i MAX5 ergonomically designed console with19” LCD screeni i WinMax Mill Conversational and IndustryStandard NC programmingHurcoCompanies,Inc.|OneTechnologyWay|Indianapolis,IN46268|800.634.2416|**************|VM10i PLUSThe Hurco VM CNC vertical milling machines offer powerful machining with a compact footprint, and absolutely the best value on the market. The larger work cube provides impressive X travelwhile not demanding excessive floor space.i i Heavily Ribbed Fine-Grade Cast IronFrame Optimized with Finite Element Analysis (FEA)i i Wedge-locked Heavy duty Linear Rails forAll Three Axesi i Direct Drive Z axis with RegenerativeBrake – No Counterbalancei i Precision Ballscrewsi i Yaskawa Sigma V Digital AC Servos i i Fast 945 ipm Rapid Traverse Rates i i Electric Swing-arm 20 Station ATC –Random Accessi i 2.5 Second Tool-to-Tool ATC Time i i Full Enclosure with Wide Front Access andSide Access Doorsi i LED Work Lighti i Door Safety Interlocks / ANSI B11.23i i Flood Coolant System i i Spindle Thermal Chiller i i Rigid Tapi i Pistol-style Coolant and Air Guns i i Metal Telescopic Way Covers i i Automatic Central Lubrication System i i Power Cabinet Heat Exchanger i i Way Lube Separation System i i Modular One-Piece ITX Control RackHurcoCompanies,Inc.|OneTechnologyWay|Indianapolis,IN46268|800.634.2416|**************|VMX42DiThe Hurco VMX42Di CNC vertical milling machine is the industryworkhorse. These CNC machining centers are the perfectcombination of performance and flexibility.i i Heavily Ribbed Fine-Grade Cast IronFrame Optimized with Finite Element Analysis (FEA)i i Wedge-locked Heavy duty Linear Railswith roller bearings on X/Y/Z axesi i Direct Drive Servos on X/Y/Z Axes i i Double-Nut Pre-Tensioned BallscrewsAnchored at Both Endsi i New Max 5 control height adjustmentcapabilityi i Yaskawa Sigma V Digital AC Servos i i Fast 1,496 ipm Rapid Traverse Rates (X,Y)1,260 ipm on Zi i Full Enclosure with Wide Front Access andSwing-open Side Doorsi i Right and Left Side LED Work Lights i i 3-stack Signal Light i i Door Safety Interlocks i i Spindle Thermal Chiller Assembly i i Flood Coolant Ring and Washdown System i i Pistol-style Coolant and Air Guns i i Metal Telescopic Way Covers i i Lift-Up Chip Conveyori i Automatic Central Lubrication System i i Power Cabinet Heat Exchanger i i Way Lube Separation System i i Modular One-Piece ITX Control Rack。
MTC101-运动控制系统基础
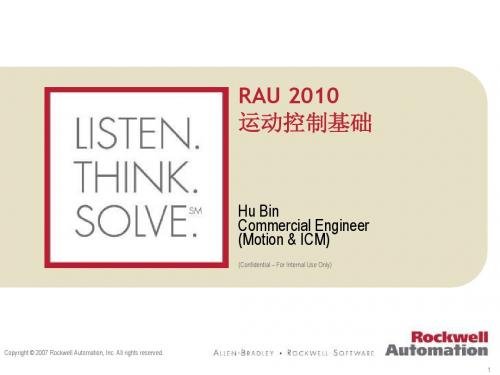
Motor with Position Motor Feedback Power Feedback
Motor Brake
Vertical Applicatio n
Gravity
Mechanical Brake Option
Mass
(Confidential – For Internal Use Only) Copyright 2007 Rockwell Automation, Inc. All rights reserved.
课程内容
1. 什么是运动控制系统 2. 运动控制产品 3. 设计和开发软件 4. 运动控制中的机电融合
(Confidential – For Internal Use Only) Copyright 2007 Rockwell Automation, Inc. All rights reserved.
Motor Power Position Feedback
Servo Drive Position Feedback To Motion Controller
(Confidential – For Internal Use Only) Copyright 2007 Rockwell Automation, Inc. All rights reserved. 10
伺服电机——抱闸的概念 伺服电机——抱闸的概念
伺服电机可以选择带有抱闸装 置。例如在垂直负载应用中, 为了防止在电机失电的情况下 自由落体状况的发生。 通常,在抱闸线圈通电的时候 ,弹簧压紧,抱闸处于打开状 态;而当电机失电,抱闸在弹 簧作用下关闭,防止轴的坠落 。 在其他需要的场合,也需要使 用抱闸电机。
Tye 100-240VAC (Single Phase) 100-240VAC (3-Phase)
MTC20使用手册

如左图所示,我们有 、 、 、 、 如左图所示,我们有10、11、12、13、 14、15、16秒七种时间间隔可选,选 秒七种时间间隔可选, 、 、 秒七种时间间隔可选 秒后, 择10秒后,按“Ent”键,进入下个界 秒后 键 面
Intersection Delay Site: 12 Int: 001 =Press Ent to start= 11:00:00
Intersection Delay Site: 12 Int: 002 Stopped 11:00:11 cars : 15 Rem 00:09
在每个统计周期结束的时候 MTC20会嘀嘀嘀响三声,这 会嘀嘀嘀响三声, 会嘀嘀嘀响三声 时我们输入停在进口道上的 车辆数。当我们再次按下#11 车辆数。当我们再次按下 号键时, 或#12号键时,数据就保存在 号键时 存储器里了。 存储器里了。
如 上 图 所 示 ,M T C 20 可 做 六 种 调 查 类 型 ITF=交叉口转向流量调查 SID=交叉口信号延误调查 S S D = 停 车 标 志 延误 调 查 SFR=交叉口饱和流率调查 SSP=车辆地点车速 R T S = 原 始 时 间 标 数 据 采集
如何做交叉口转向流量调查
1、设置地点代码 、
设备打开 出现以上界面 显示调查仪的类型
几秒钟之后, 几秒钟之后,被以上界面 替代 界面依次显示: 界面依次显示: 已存储的调查次数 已占用的存储空间百分比 当前的电池容量
再过几秒钟之后 出现主菜单界面
主菜单
我们来认识主菜单界面中各选项的含义 View Count Clear Setup Unload View memory, battery left and date / time.
如何做交叉口饱和流率调查
MTC产品说明书

在一支 MTC 型插入式多测点流量传感器上,配置 4 ~ 12 对高、低端感 压孔(视管径大小而不同)。在检测管中流量信号被平均后输出,其输出则代表 了多个测点的平均流速或流量。当管道内插入多支 MTC 流量传感器时,构成 矩阵分布的面测量方法,就可以准确测量流速分布不均匀的管道截面流量。
在流量测量过程中,流体的各相关参数经变送器转换为相对应的直流电流 信号(4-20 mA.DC),直接传送到DCS系统,运算并显示出管道的瞬时流量值。 或将变送器输出的直流电流信号传输到DZL-2智能流量信号转换仪运算显示出 管道的瞬时流量,并传送到DCS系统显示出瞬时流量。
MTC型 插入式多测点流量测量装置
产品说明书
量制陕字00000212号
西安中航流量技术研究所
1
MTC 型插入式多测点流量测量装置产品说明书
概述
在电力、冶金、石油、化工等诸多行业中有许多输送流体的工艺管道,准 确测量其流体的流量是操控设备自动、安全运行,实现节能降耗、提高生产效 率、保证产品质量的重要环节之一。很多大中型企业,尤其是电厂,设备庞大 且大管道繁多。管道布局受空间限制,大管道的交汇、分支、弯曲、变径等部 位,不能按最佳流态设计。由于阻力件形式繁杂,流量调节阀特性不佳、直管 段过短、流体温度混合不均、流速太低、管道振动、流体夹带大量粉尘及粒状 杂质等诸多因素的制约,造成管道流态复杂、流场紊乱。使得当前各类传统的 经典流量测量装置无法准确测量,不能满足自动测控要求。发明解决低速、管 道流场复杂多变、夹带粉粒杂质的流量测量的先进技术产品,并投放市场,是 我们的重要使命。
LIFT PRODUCTS INC. MOTO CART 操作手册说明书

Lift Products Inc.W226 N900 Eastmound Dr. Waukesha, WI 53186 Telephone: (262) 521-5720 Fax: (262) 521-5725Parts & Service: 877-543-8776MOTO CART PRODUCT SERVICE INFORMATIONINTRODUCTION (2)SAFETY FIRST (3)OPERATING THE MOTO CART (4)MODEL MC-10-S / MC-10-M /MC-10-L /MC2-HD20 /MC2-HD15 (EZ-GRIP CONTROLS) (4)ON-OFF KEY SWITCH (4)FORWARD/REVERSE (4)SPEED MODES (4)EMERGENCY STOPPING (4)BATTERY CONDITION (4)RUNNING (5)BRAKING SYSTEMS (5)CHARGING (6)BATTERIES (6)BATTERY LIFE (6)BATTERY LOAD TESTING (7)CIRCUIT BREAKER (7)MAINTENANCE (7)MAINTENANCE SCHEDULE (7)MAINTENANCE PROCEDURES (8)DIAGNOSTICS & TROUBLESHOOTING (9)PUSHING MANUALLY (11)SPECIFICATIONS (12)Welcome to the MOTO CART . . . a member of the Lift Products family of quality mobility products. We know you’ll be depending on it, so we have taken great care to make it completely reliable. This owner’s manual is designed to help you get the most out of your CART and includes very important safety and care information. Please read it thoroughly and keep it handy for reference. Thank you for choosing the MOTO CARTInformation in this manual is based upon specifications in effect at the time of publication. Lift Products reserves the right to make changes at any time without notice.Be sure to complete the Product Service Information box on the inside front cover. This will be your record of important information, which will help you if your MOTO CART ever requires service. When seeking repair parts while your MOTO CART is under warranty, a copy of your bill of sale may be requested to verify warranty status.FAILURE TO READ THIS OWNER’S MANUALWILL VOID THE WARRANTYIf there is anything in this manual that you do not completely understand or are unsure of,DO NOT OPERATE your MOT CART. Call Customer Service at:1-877-543-87762To prevent accidents which can cause injury to you, damage the MOTO CART or damage your cargo, observe the following rules:READ THE OWNERS'S MANUAL BEFORE OPERATING THE MOTO CART.1. Read and understand this owner’s/operator’s manual before operating the MOTO CART2. Read and understand all safety instructions provided with the MOTO CART.3. Only trained personnel should be allowed to use the MOTO CART. All persons using the CART must read this owner’s/operator’s manual.4. The MOTO CART has a maximum load capacity of 1500 pounds. Do not exceed the rated capacity for your model.MC2-HD20 2000MC2-HD15 1500MC-10-L 1500MC-10-M 1500MC-10-S 15005. Do not travel up or down inclines greater than 6°.6. Always turn the key switch off before loading or unloading the CART.7. Always take corners slowly and with caution to prevent the load from shifting.8. Do not travel sideways across inclines.9. Do not stop the MOTO CART on an incline. Always park, load and unload on a flat, level surface.10. Do not go up and down curbs. Only operate theCART on smooth surfaces.11. Always unplug the batteries before making anyadjustments or repairs to the MOTO CART. 12. Always load the CART evenly, distributingthe load to prevent tipping.13. Do not defeat any safety equipment on theCART.14. Do not use the MOTO CART to push or pullobjects or other carts.15. Do not operate the MOTO CART in wetenvironments.16. Do not expose the MOTO CART to hightemperatures. The CART is battery operated. Batteries may be severely damaged if exposed to high temperatures.17. Do not operate the MOTO CART with abroken wheel or broken or bent caster.18. Use extreme caution when operating theMOTO CART near doorways, in hallways and near stairwells. Reduce speeds in these areas.19. Do not manually release theelectromechanical brake on or near an incline. If you must release this brake, release the brake only when on a level surface and with the CART completely unloaded. Instructions for releasing the brake are in the section titled "Pushing Manually".20. Test the operation of the MOTO CART inan environment with sensitive electronic equipment prior to the use in that environment. The CART has not been tested with all manufacturers equipment and may react to, or cause a reaction in the electronic equipment.3We would like you to get the most out of your MOTO CART. When you use the CART for the first time, you must know how to properly operate and care for it to avoid unsafe situations. Please read this manual thoroughly and become familiar with all of the safety information provided.Be aware of your surroundings – drive slowly and cautiously. Avoid collisions which could cause damage to the CART or shift the load, damaging the goods, or injuring you or surrounding people.Anticipate and avoid unsafe situations. Be courteous of others and let your presence be known.Perform first time operation in an open area on a flat surface free of obstacles. Have someone familiar with the operation of the MOTO CART available to assist you.First time operators should read and understand all instructions and controls before attempting to operate the CART.On-Off Key SwitchThe on-off key switch is located on the side of the Roller Grip control unit. To turn the power on, fully insert the key into the key switch and turn the key clockwise. When the power is on, the status LED located on the top of the control unit will illuminate.Forward/ReverseThe Forward/Reverse direction of the Cart is controlled by the thumb-wheels located on either side of the Roller Grip control unit. Pushing either of the thumb-wheels forward (clockwise) will move the Cart forward. Pushing either of the thumb-wheels backward (counterclockwise) will move the Cart in reverse.Speed ModesThe Roller Grip control provides two speed modes, “Rabbit” (fast) or “Turtle” (slow). A “Rabbit/Turtle” rocker switch located on top of the unit allows selection of the desired speed mode. Depressing the back of the rocker switch (Turtle icon) selects the slow mode, while depressing the front of the switch (Rabbit icon) selects the fast mode.Always select the Turtle/Slow speed during training, in close quarters, or in circumstances in which you risk damage or injury if the Rabbit (fast) speed is selected.Emergency StoppingTo stop the Model MC-10M /MC-10-L/ MC-10-S/ MC2-HD15 /MC2-HD20 CART in an emergency, press in on the Emergency Stop Button. The Emergency Stop Button is the large red button covering most of the Roller-Grip control unit’s front. To restart the Cart, the key switch must be cycled (turned off and then back on).Battery ConditionThe Battery Gauge located on top of the Roller-Grip control unit indicates when the Cart’s batteries need to be recharged. If the Battery Gauge shows red, yellow and green, the batteries are charged. If the Battery Gauge shows just red and yellow, the batteries need to be charged as soon as possible. If the Battery Gauge shows just red (either steady or flashing slowly), the batteries need to be charged immediately. The Battery Gauge reading is more accurate after the power has been on for at least one4RunningThe Model MC-10-M/MC-10-L/MC-10-S/MC2HD-15/MC2-HD20 Cart is equipped with the ergonomically designed Roller-Grip control unit. To operate the Cart, follow the steps below:1. Turn the key switch clockwise to the Drive position. Select the desired speed mode using the “Rabbit/Turtle” switch2.Gently push either of the Roller-Grip thumb-wheels forward (clockwise). The CART will start to move and accelerate forward, away from you.3. To stop, release the control lever. The MOTO CART will gently slow down with the aid of dynamic regenerative braking.4. To go in reverse, gently push either of the Roller-Grip thumb-wheels backward (counter- clockwise). The CART will start to move and accelerate toward you. For safety, the maximum speed in reverse is normally set slower than the forward speed.Braking SystemsAll MOTO CARTS have two types of braking systems, dynamic regenerative braking and electro-mechanical braking.1. Dynamic Regenerative Braking - Dynamic regenerative braking automatically brings the CART to a smooth stop when the thumb-wheel is released. However, it does not lock the wheels in place.2. Electromechanical Braking - After the dynamic braking has brought the CART to a stop, the electromechanical brake will lock the drive wheels in place. The electromechanical brake is a parking brake and can be applied instantly by pressing the emergency stop switch (located on the front of the Model MC-10-M/MC-10-L/MC-10-S/MC2HD-15/MC2-HD20 Roller-Grip control unit). The center, or drive wheels, must be contacting the floor surface for the brake to hold.ChargingThe MOTO CART is equipped with two U-1 Absorbed Glass Mat (AGM) batteries, which require charging on a regular basis. An on-board charging system is integrated into the electronics of the CART to make charging easy.1. Position the MOTO CART close to an AC poweroutlet. The CART can be charged using any voltage between 100 and 240 volts AC 50/60 Hz.Model MC-10-M/MC-10-L/MC-10-S/MC2HD-15/MC2-HD20 is equipped with an on-board coil cord for charging (if required, use a plug adapter from the country in which the CART will be used).2. Turn the unit off and remove the key.3. Find the coil cord located just below the frame onthe control handle end of the CART.4. Plug the coil-cord directly into the power supplyoutlet. If needed, connect only an industrial grade grounded extension cord to the coil-cord and then to the AC power supply outlet. Make sure the plug is fully engaged into the supply outlet.5. Allow the unit to charge overnight – six to eighthours for a full charge. For optimum battery life, charge the CART whenever it is not in use – it cannot be over-charged.6. With the power on, the Battery Gauge shows thecharging status. If the Battery Gauge shows red, yellow and green, the batteries are nearly or fully charged. If the Battery Gauge shows red and yellow, or just red, charging needs to be continued.7. Unplug the cord from the power supply outlet(and if used, the extension cord from the unit) before attempting to turn the unit on.56Circuit BreakerA manually reset circuit breaker is located on one battery attached to the positive (+) terminal. The circuit breaker protects the wiring and batteries against damage in the event of a short circuit. If a breaker opens, reset it by pushing the tab down. If it opens again in a short time, there is a short circuit, which must be found and corrected.If any additional wiring is added to the CART, it must not bypass the break er.DO NOT DEFEAT THE BREAKER! DO NOT REMOVE OR BYPASS THE CIRCUIT BREAKER!DO NOT TAPE THE TAB DOWN!MAINTENANCE SCHEDULEYour MOTO CART will give you years of safeand dependable service in return for regularmaintenance and early attention to anydeveloping problems. We recommend thefollowing maintenance program.If you use your CART often, you may find it to your advantage to perform this maintenance more frequently.CAUTION: Disconnect the batteries beforePerforming any maintenance.Every Day or as Needed:1. Maintain the batteries’ charge.2. Clean debris from the wheels and drive unitassembly.Once Each Month:1. Check for loose connectors and any signs ofunusual wear.2. Grease caster wheel swivel assemblies. Use only industrial grade grease in the caster wheel swivel assemblies.Once Every Three Months:1. Clean your CART with a damp sponge.2. Check the wires for wear, fraying or cracking.3. Check the connectors for wear or cracking.4. Examine the tires and wheel assemblies for wear ordamage.NOTE: THIS MAINTENANCE IS BEST PERFORMED BY YOUR LOCAL AUTHORIZEDSERVICE CENTER.Cleaning Your MOTO CART:Turn the power OFF and disconnect the batteries before cleaning your CART. Use warm soapy water and a damp sponge to clean your MOTO CART. DO NOT pressure-wash or hose your CART off. Excessive water may damage electronic components.Do not use harsh or abrasive cleansers on the MOTO CART or its tires. These types of cleansers will damage the finish of your CART, and may cause premature tire wear. Clean your tires with a bristle brush dipped in warm water.7MAINTENANCE PROCEDURESLubrication:All wheel bearings are sealed and permanently lubricated. Spray silicone lubricants (or WD-40*) may be used on any other moving parts. Apply this lubricant whenever there is “stickiness” in the moving parts. *WD-40 is a registered trademark of the WD-40 Company and is Not affiliated with Electro Kinetic Technologies, LLC.Replacing the Batteries:Make sure that the brake is applied (brake handle down). Turn the power OFF and disconnect the batteries.Cut the wire ties holding the main cable and the charger cable to the drive system frame and disconnect the cables.Remove any load from cart. You may want a second person to help with dropping the drive system. Remove the hitch pin clips from the hitch pins and remove the hitch pins from the U brackets that attach the drive system to the cart.Some downward pressure on the platform maymake the pins easier to remove. The drivesystem frame should then drop away from the cart frame. Use caution, as the drive system is heavy.Raise the front of the cart and remove the twosuspension springs.Release the brake and roll the drive system out from under the cart.Undo the battery hold down straps and remove the batteries from the battery tray. Remove the circuit breaker and wires from the old batteries. Install the new batteries by following these steps inreverse order. Remember to re-apply the brake (push brake handle down).WARNING: Do not touch both the negativeand positive terminals of the batteries with a conductive material (e.g., metal) or sparks, burns, or explosion may result.8Your MOTO CART has been designed and built to be dependable and trouble free, but we know that there can be unexpected problems with any technical product. The following checklists will give you a “First Aid” approach to dealing with most problems. You can also call our Service Hotline: 877-543-8776.SYMPTOM POSSIBLE CAUSESOLUTION Key Switch turned to Off position.Turn Key Switch to Drive (right) position. Emergency Stop Switch has beenpressed.Recycle Key switch. Circuit breaker open.Reset circuit breaker. Unit Dead, BCI DarkPower connection interrupted.Check power cables to batteries. Obstruction in pathway of wheels. Check for obstruction. Unit Dead, BCIIlluminated Motor worn out.Contact Authorized Service Center. Battery charge low.Charge batteries. Unit Runs SlowWorn batteries.Charge batteries. Load test batteries. Charger power interrupted.Check wall outlet for continuous power. Loose connection in wiring.Check all exposed wire connections. Battery Weak orWon’t Take aCharge Charger burned out.Replace charger. Loose connection in wiring. Check all exposed wire connections. IntermittentRunning Worn motor brushes. Contact Authorized Service Center. Casters require lubrication. Lubricate casters.Hard to TurnWorn out caster bearings. Replace casters.9Moto Cart Model MC-10-M / MC-10-L / MC-10-S / MC2HD-15 & MC2-HD20 Carts equipped with Roller-Grip Hand Controls provide diagnostics information to assist technicians in troubleshooting drive system problems. The diagnostics information is obtained by observing the fault codes issued by the status LED located on the Roller-Grip control unit.During normal operation, with no faults present, the status LED is steadily on. If the controller detects a fault, the status LED displays a fault identification code. The number of flashes indicates the nature of the fault. The codes are listed in Table 1 below, along with possible causes of the fault indicated.Table 1 DIAGNOSTIC CODESNUMBER OFFLASHESPOSSIBLE CAUSE1 The battery needs charging or there is a bad connection to the battery. Check the connections to the battery. If the connections are good, try charging the battery.2 There is a bad connection to the motor. Check all connectionsbetween the motor and the control system.3 The motor has a short circuit to a battery connection. Contact yourservice agent.4 Not used.5 Not used.6 The controller is being inhibited from driving. This may be because theEmergency Stop Button was pressed. Turn the Key switch Off and On.7 A throttle fault is indicated. Make sure that the throttle is in the restposition before switching on the CART.8 A controller fault is indicated. Make sure that all connections aresecure. Contact your service agent.9 There is a bad connection to the parking brake. Check all connectionsbetween the parking brake and the controller.10 An excessive voltage has been applied to the controller. This is usually caused by a poor battery connection. Check the battery connections.RipplingUp & Down Throttle applied at power up. Release throttle lever.10PUSHING MANUALLYThe drive system on the MOTO CART can be disabled to allow you to push the unit Manually. To disable the drive system:1. On a level surface only, lift up on the brake handle located under the deck near the drive wheels to disable the Electromechanical Parking Brake.2. Turn the Key Switch to the Off position to disable the Dynamic Braking.AFTER PUSHING, RETURN THE BRAKE LEVER TO THE DOWN POSITIONTO PREVENT THE CART FROM ROLLING AND TO ENABLE DRIVING.WARNING:DO NOT RELEASE THE BRAKE ON OR NEAR AN INCLINED SURFACE.THE UNIT WILL NOT STOP ON ITS OWN WHEN THE BRAKING SYSTEM IS DISABLED.SEVERE INJURY MAY RESULT IF THE UNIT IS LEFT TO ROLL UNATTENDED. Array11• Spring-suspension and center wheeltransaxle drive system• Speed range, 0-3 MPH (0-4.8 km/hr)• Maintenance free permanent magnet motor • Non-marking tires• Variable speed control• Horn, key switch, emergency stop• Hi/Low speed switch• (2) 33AH, 12 volt, AGM maintenance free batteries• On board 100-240, 50/60 Hz, UL listed battery charger• Automatic dynamic braking & parking brake • Deck Height: 11.5” (290 mm)• Incline Rating: 6°Model MC-10-MUsable Platform Length: 48”Usable Platform Width: 24”Capacity: 1,500 lbs.Model MC-10-LUsable Platform Length: 60”Usable Platform Length: 24”Capacity: 1500 lbsModel MC-10-SUsable Platform Length: 41 ½”Usable Platform Width: 24”Capacity: 1500 lbsModel MC2-HD15Usable Platform Length: 48”Usable Platform Width: 36”Capacity: 1500 lbsModel: MC2-HD20Useable Platform Length: 48”Useable Platform Width: 36”Capacity: 2,000 lbs.1213Lift Products, Inc.W226 N900 Eastmound Dr. Waukesha, WI 53186 Telephone: (262) 521-5720 Fax: (262) 521-5725Parts & Service: 877-543-8776。
- 1、下载文档前请自行甄别文档内容的完整性,平台不提供额外的编辑、内容补充、找答案等附加服务。
- 2、"仅部分预览"的文档,不可在线预览部分如存在完整性等问题,可反馈申请退款(可完整预览的文档不适用该条件!)。
- 3、如文档侵犯您的权益,请联系客服反馈,我们会尽快为您处理(人工客服工作时间:9:00-18:30)。
在旅行时间及延误类型的调查上, 在旅行时间及延误类型的调查上, 我们在每经过一个预设站点就按 一下#1, 一下 ,然后根据延误类型操作 不同的按钮
3、开始调查 、
当我们记录了一辆车的类型和号牌后, 当我们记录了一辆车的类型和号牌后,直接按下一辆 车的车型,系统会自动存储上一辆车的号牌数据 车的车型,系统会自动存储上一辆车的号牌数据 自动存储
如何做车辆旅行时间及延误调查
1、设置路线代码 、
HVC ITF VLP MLH RTS Exit Travel Time and Delay survey TTD Route Code: 12 Press 1-10# key to add Site Code, press Enter to set. Exit
如 上 图 所 示 ,M T C 10 可 做 六 种 调 查 类 型。 HVC=路段24种车型调查 ITF =单方向路口6种车型转向调查 VLP=车辆区间旅行时间车牌照记录 TTD=单车旅行时间及延误调查 MLH=多车道车头时距或间距调查 RTS=原始时间标调查
如何做路段车型调查
1、设置地点代码 、
设备打开 出现以上界面 显示调查仪的类型
几秒钟之后, 几秒钟之后,被以上界面 替代 界面依次显示: 界面依次显示: 已存储的调查次数 已占用的存储空间百分比 当前的电池容量
再过几秒钟之后 出现主菜单界面
主菜单
我们来认识主菜单界面中各选项的含义 View Count Clear Setup Unload View memory, battery left and date / time.
如左图所示,开始调查后, 如左图所示,开始调查后,屏幕最后一 行显示当前时间和剩余时间。 行显示当前时间和剩余时间。调查仪会 在每个调查周期结束后自动存储数据。 自动存储数据 在每个调查周期结束后自动存储数据。
3、开始调查 、
本列进行左转车辆的调 本列进行左转车辆的调 左转 查,从上至下的六个按 钮可代表六种车型
License Plate Count Site:12 CL:-- -=Press Ent to start= 11:00:00
车辆牌照记录没有统计周期的概念, 车辆牌照记录没有统计周期的概念, 没有统计周期的概念 我们需要关注的除了车牌的位数外, 我们需要关注的除了车牌的位数外, 还有车辆的分型( ) 还有车辆的分型(CL)
本列进行右转车 本列进行右转车 右转 辆的调查, 辆的调查,从上 至下的六个按钮 可代表六种车型 本列可记录其他 本列可记录其他 (Other)其它 ) 特别车辆, 特别车辆,如公 交车、大货车、 交车、大货车、 自行车、行人等 自行车、行人等
本列进行直行车辆的调 本列进行直行车辆的调 直行 查,从上至下的六个按 钮可代表六种车型
3、开始调查 、
1-10号键用于输入号 号键用于输入号 牌,10号键代表 “0”值 号键代表 值 在号牌调 查中, 查中,可 区分四种 车型, 车型,分 别用C1、 别用 、 C2 、 C3 、 C4来表示 来表示
车牌号中多有字母,在调 车牌号中多有字母 在调 查中,我们用 我们用11号键代 查中 我们用 号键代 表“A”,用12号键代表 号键代表
确认后, 通过 Ent 确认后,会让 我们选择地点代码, 我们选择地点代码,如 上图所示, 上图所示,12 就是我 们此次调查的地点代码
2、选择统计周期 、
Site Code: 12 Interval Duration: 01 05 10 15 30 60 Minutes. Exit
如左图所示, 如左图所示,有1、5、15、30、60分 、 、 、 、 分 钟五个统计周期可选, 我们选择1分钟 分钟, 钟五个统计周期可选, 我们选择 分钟, 选定后按“Ent”键,再按“Ent”键 开 键 键 始调查
HVC ITF VLP TTD MLH RTS Exit Highway Vehicle Classification count Site Code: 12 Interval Duration: 01 05 10 15 30 60 Minutes. Exit
光标显示在HVC上,表 上 光标显示在 明我们要进行路段车型 的调查
Classification Count Site: 12 Int: 001 =Press Ent to start= 11:00:00
如左图所示,调查从 点开始 点开始, 如左图所示,调查从11点开始, Int 显示第几个调查周期
Classification Count Site: 12 Int: 001 Key #: 01 11:00:01 11:00:02 Rem 00:58
确认后, 通过 Ent 确认后,和之 前一样, 前一样,我们输入地点 代码
2、选择需要输入几位车辆牌照 、
Site Code: 12 Characters Number: 02 03 05 06 Press Enter to set Exit
如左图所示,可选择输入 、 、 、 如左图所示,可选择输入2、3、5、6 位数的车牌号码,我们选择输入6位的 位数的车牌号码,我们选择输入 位的 车牌号, 车牌号,选定后按“Ent”键,再按 键 “Ent”键开始调查 键开始调查
在三种主要延误 类型之外的其他 延误时, 延误时,车辆停 下来按#23,车 ,
辆重新启动按#24 辆重新启动按
Travel Time & Delay Route:12 Site No:001 Delay Type: SLD 11:00:03
Travel Time & Delay Route:12 Site No:001 Delay Type: -- -- -11:00:09
View: 显示调查次数、剩余空间、当前电量 : 显示调查次数、剩余空间、 和 时间日期 Count :开始新的调查或继续前一个调查
Clear: 清除存储器里的所有数据 : Setup : 设置时间日期、背光灯开关和 设置时间日期、 蜂鸣器开关。 蜂鸣器开关。
Unload :将数据下载到计算机里
如何开始新调查
Turning Flow Count Site: 12 Int: 001 =Press Ent to start= 11:00:00
如左图所示,调查从 点开始 点开始, 如左图所示,调查从11点开始, Int 显示第几个调查周期
Turning Flow Count Site: 12 Int: 001 Key #: 01 11:00:01 11:00:02 Rem 00:58
我们在每经过一 个预设站点都需 要按一下#1 要按一下 因信号灯延误时, 因信号灯延误时, 车辆停下来按
#17,车辆重新启 , 动按#18 动按
因交通堵塞延误 时,车辆停下来 按#21,车辆重新 ,
启动按#22 启动按
在公交停靠站停 靠引起的延误, 靠引起的延误, 车辆停下来按 #19,车辆重新 , 启动按#20 启动按
进入到主菜单界面后 选择光标移动到Count 选择光标移动到 进入调查界面
光标指向New Count 光标指向 开始一项新的调查
现在 我们可以选择需要调查 的类型
可以用来做那些调查
HVC ITF VLP TTD MLH RTS Exit Highway Vehicle Classification count
光标显示在 TTD 上,表 明我们要进行车辆旅行 时间及延误调查
确认后, 通过 Ent 确认后,和之 前不同的是, 前不同的是,这次我们 输入的是路线代码 路线代码, 输入的是路线代码,就 是我们行驶的路线
2、延误类型 、 我们可以用MTC-10 来调查以下三种主要的延误类型: 来调查以下三种主要的延误类型: 我们可以用 1)因信号灯引起的延误(SLD),操作时按 )因信号灯引起的延误( ),操作时按 ),操作时按#17、#18两个键 、 两个键 2)在公共汽车停靠站停靠所引起的延误(BSD), 操作时按 )在公共汽车停靠站停靠所引起的延误( ), 操作时按#19、#20两个键 、 两个键 3)因交通阻塞所引起的延误(TJD), 操作时按 )因交通阻塞所引起的延误( ), 操作时按#21、#22两个键 、 两个键 由于其他原因引起的延误( ),操作时按 由于其他原因引起的延误(OTD),操作时按 其他原因引起的延误 ),操作时按#23、#24两个键 、 两个键
MTC10手持式多功能调查仪 手持式多功能调查仪 操作说明
认识设备
滑动开光, 滑动开光,用于 开启或关闭设备 “Bak” 返回键 “Ent” 确认键
显示屏
电池充电端口
“Del” 删除键 “Tab” 用于移 动光标
24个数字键 个数字键
USB接口 接口
基本操作
…AOZER TECH… Hi-Pro MTC10 Traffic-Data Counter All Rights Reserved …STATUS… Counts Stored: 000 Memory Used: 000% Battery Left: 8.4V View Count Clear Setup Unload View memory, battery left and date / time.
确认后, 通过 Ent 确认后,会让 我们选择地点代码, 我们选择地点代码,如 上图所示, 上图所示,12 就是我 们此次调查的地点代码
2、选择统计周期 、
Site Code: 12 Interval Duration: 01 05 10 15 30 60 Minutes. Exit
如左图所示, 如左图所示,有1、5、15、30、60分 、 、 、 、 分 钟五个统计周期可选,我们选择1分钟 分钟, 钟五个统计周期可选,我们选择 分钟, 选定后按“Ent”键,再按“Ent”键 开 键 键 始调查