陶瓷的施釉
釉料制备及施釉

2.池炉
• 图3-6-6为良种不同池炉的结构示意图。 • ??????????????????
池炉与坩埚相比,具有以下特 点:
• (1) 熔块料与火焰直接相接触,受 气氛影响。 • (2) 产量高,劳动条件好,易实现 自动化。 • (3) 结构简单,维修费用低 • (4) 熔块料中易挥发组分有损失, 但仍呢感保证熔块质量。
2浇釉法
• 浇釉是将胚体放在旋转的机轮上,釉浆 浇在胚体中央,借离心力使得浆体均匀 散开。或使釉浆流过半球浇釉器表面在 流向胚体。此发适用于盘碟或者单面层 瓷砖或胚体强度较差的胚体。
3喷釉发
• 利用喷枪或喷雾器将釉浆成雾滴使之附 在胚体上。胚与枪的距离、喷釉压力、 釉浆密度决定釉层厚度,此发适用与大 型,薄壁或形状复杂的生胚。可多次喷 釉以增加厚度,近年来卫生陶瓷生产线 上采用自动喷釉,并设计出静电喷釉, 使之操作时损失大为减少。
1.
熔块的配制原则
• ( 1 )( SiO2+B2O3 ):( R2O+RO ) = ( 1 : 1 ) — (3:1)。此外必须考虑PbO、B2O3和碱金属氧 化物在高温时的挥发。 • ( 2 )在熔块中碱金属氧化物与碱土金属氧化 物之比小于1:1 • (3)熔块中的酸性成分须含SiO2 , 但如果加 入B2O3,则SiO3与B2O3之比宜大于或等于2:1。 • (4)熔块中Al2O3不宜超过0.2mol(釉式),
二、釉熔体的粘度、润湿性和 表面张力
在成熟温度下,釉的粘度过小,则流动性过大,容 易造成流釉、堆釉及干缺陷;釉的粘度过大,则流 动性差,易引起橘釉、针眼、釉面不光滑,光泽不 好等缺陷。 釉的表面张力对釉的外观质量影响很大。表面张力 过大,阻碍气体的排除和熔体的均化,在高温时对 坯的湿润性不好,容易造成缩釉缺陷;表面张力过 小,则易造成“流釉”(当釉的粘度也很小时,情 况更严重),并使釉面小气孔破裂时形成针孔难以 弥合,形成缺陷。
陶瓷工序流程
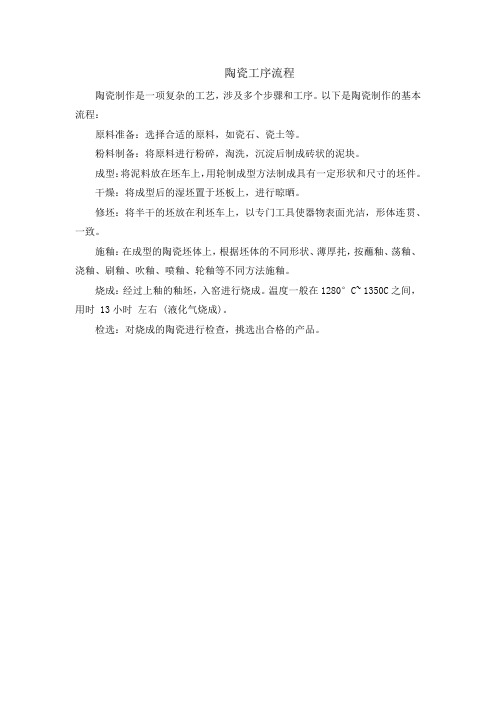
陶瓷工序流程
陶瓷制作是一项复杂的工艺,涉及多个步骤和工序。
以下是陶瓷制作的基本流程:
原料准备:选择合适的原料,如瓷石、瓷土等。
粉料制备:将原料进行粉碎,淘洗,沉淀后制成砖状的泥块。
成型:将泥料放在坯车上,用轮制成型方法制成具有一定形状和尺寸的坯件。
干燥:将成型后的湿坯置于坯板上,进行晾晒。
修坯:将半干的坯放在利坯车上,以专门工具使器物表面光洁,形体连贯、一致。
施釉:在成型的陶瓷坯体上,根据坯体的不同形状、薄厚扥,按蘸釉、荡釉、浇釉、刷釉、吹釉、喷釉、轮釉等不同方法施釉。
烧成:经过上釉的釉坯,入窑进行烧成。
温度一般在1280°C~ 1350C之间,用时 13小时左右 (液化气烧成)。
检选:对烧成的陶瓷进行检查,挑选出合格的产品。
陶瓷釉生产工艺
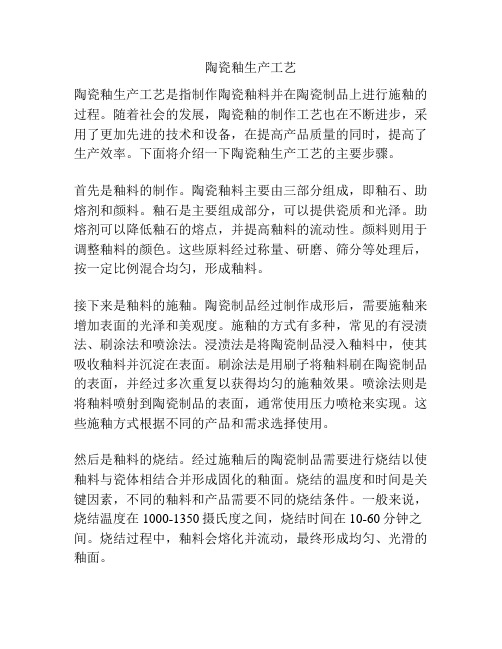
陶瓷釉生产工艺陶瓷釉生产工艺是指制作陶瓷釉料并在陶瓷制品上进行施釉的过程。
随着社会的发展,陶瓷釉的制作工艺也在不断进步,采用了更加先进的技术和设备,在提高产品质量的同时,提高了生产效率。
下面将介绍一下陶瓷釉生产工艺的主要步骤。
首先是釉料的制作。
陶瓷釉料主要由三部分组成,即釉石、助熔剂和颜料。
釉石是主要组成部分,可以提供瓷质和光泽。
助熔剂可以降低釉石的熔点,并提高釉料的流动性。
颜料则用于调整釉料的颜色。
这些原料经过称量、研磨、筛分等处理后,按一定比例混合均匀,形成釉料。
接下来是釉料的施釉。
陶瓷制品经过制作成形后,需要施釉来增加表面的光泽和美观度。
施釉的方式有多种,常见的有浸渍法、刷涂法和喷涂法。
浸渍法是将陶瓷制品浸入釉料中,使其吸收釉料并沉淀在表面。
刷涂法是用刷子将釉料刷在陶瓷制品的表面,并经过多次重复以获得均匀的施釉效果。
喷涂法则是将釉料喷射到陶瓷制品的表面,通常使用压力喷枪来实现。
这些施釉方式根据不同的产品和需求选择使用。
然后是釉料的烧结。
经过施釉后的陶瓷制品需要进行烧结以使釉料与瓷体相结合并形成固化的釉面。
烧结的温度和时间是关键因素,不同的釉料和产品需要不同的烧结条件。
一般来说,烧结温度在1000-1350摄氏度之间,烧结时间在10-60分钟之间。
烧结过程中,釉料会熔化并流动,最终形成均匀、光滑的釉面。
最后是釉面的修整和装饰。
烧结后的陶瓷制品表面可能会出现一些不良现象,如釉面不均匀、气泡、色差等,需要进行修整。
修整包括打磨、刮磨、抛光等操作,以获得平滑、光亮的釉面。
修整后,还可以进行一些装饰工艺,如描绘花纹、涂饰颜色等,以增加产品的艺术价值。
陶瓷釉生产工艺是一个复杂而精细的过程,需要严格控制各个环节的参数和条件。
只有保证原料的质量,合理的配比和处理手法,良好的施釉和烧结工艺,才能生产出优质的陶瓷制品。
随着科技的发展,陶瓷釉生产工艺将不断改进,以满足人们对于美的追求。
陶瓷马桶施釉工艺流程

陶瓷马桶施釉工艺流程英文回答:Ceramic toilet glazing is a crucial process in the production of high-quality toilets. It involves applying a layer of glaze to the surface of the ceramic toilet to enhance its appearance, durability, and resistance to stains and scratches. The glazing process typically consists of several steps, including preparation, application, drying, and firing.The first step in the glazing process is the preparation of the ceramic surface. This involves cleaning the toilet thoroughly to remove any dirt, dust, or grease that may be present. It is important to ensure that the surface is completely clean and dry before applying the glaze.Once the surface preparation is complete, the glaze can be applied. The glaze is a mixture of various minerals andchemicals that give the toilet its desired color, texture, and finish. It is usually applied using a spray gun or a brush, depending on the size and shape of the toilet. The glaze should be applied evenly and smoothly to ensure a consistent and attractive finish.After the glaze is applied, the toilet needs to be dried. This can be done naturally by air-drying or by using specialized drying equipment. The drying process is essential to remove any excess moisture from the glaze and allow it to harden properly. It is important to ensure that the drying process is carried out in a controlled environment to avoid any damage or defects in the glaze.Once the glaze is dry, the toilet is ready for firing. Firing is the process of subjecting the glazed toilet to high temperatures in a kiln. This process helps to fuse the glaze to the ceramic surface, making it more durable and resistant to wear and tear. The firing temperature and duration may vary depending on the type of glaze and the desired final result. It is important to closely monitor the firing process to ensure that the glaze does notoverfire or underfire, which can result in poor quality or defective toilets.After the firing process, the ceramic toilet is carefully inspected for any defects or imperfections. Any necessary touch-ups or repairs are carried out at this stage to ensure that the final product meets the quality standards. Once the inspection and repairs are complete, the glazed toilet is ready for packaging and distribution.Overall, the glazing process is a crucial step in the production of ceramic toilets. It requires careful attention to detail and expertise to ensure that the glaze is applied correctly and the final product is of high quality. The glazing process plays a significant role in enhancing the aesthetics and durability of the ceramic toilet, making it an essential part of the manufacturing process.中文回答:陶瓷马桶的施釉工艺是生产高质量马桶的关键步骤之一。
宋代瓷器施釉特点_概述说明以及解释

宋代瓷器施釉特点概述说明以及解释1. 引言1.1 概述宋代是中国瓷器发展的一个重要时期,也是中国瓷器工艺取得巅峰成就的时期之一。
在宋代,瓷器施釉技术得到了进一步的发展和创新,形成了自己独特的特点。
本文将对宋代瓷器施釉的特点进行概述、说明和解释。
1.2 文章结构本文由引言、正文和结论三部分组成。
引言部分将介绍文章的概述、结构和目的;正文部分将详细探讨宋代瓷器施釉的起源与发展、工艺特点以及色彩和纹饰特点;结论部分则总结宋代瓷器施釉的特点,并探讨其对后世影响和未来研究方向。
1.3 目的本次文章旨在全面了解并阐述宋代瓷器施釉的特点,通过对其起源与发展、工艺特点以及色彩和纹饰特点等内容进行概述和解释,加深人们对该历史阶段瓷器施釉工艺过程和表现形式的认识。
同时,通过分析其影响与意义以及未来研究方向,展示宋代瓷器施釉对中国陶瓷文化发展的重要贡献,并为后续相关领域的学术研究提供参考和借鉴。
2. 正文:2.1 宋代瓷器施釉的起源和发展宋代是中国古代陶瓷制造史上一个重要的时期,也是中国瓷器工艺发展的高峰时期之一。
在宋代,瓷器釉料的制作和施釉技术得到了极大的进步和创新。
施釉这一环节对于瓷器的成品质量和外观效果有着至关重要的影响。
宋代初期,瓷器施釉主要使用的是白色透明釉料,称为清釉。
这种透明清亮的釉料能够更好地展现出瓷器胎体的质感和纹理。
随着技术的推动和需求的变化,底色不再单一使用白色,而开始使用其他颜色进行装饰。
2.2 宋代瓷器施釉的工艺特点宋代瓷器施釉工艺相对于以前古代陶瓷来说有了更大幅度的提升,并在技术上有了很大突破。
首先,在原料选择方面,搭配科学合理并加入适量助剂可以改善釉料质量,增强其附着力和抗腐蚀性。
其次,施釉的过程变得更加注重细节控制,提高了对釉料的涂抹均匀性和厚度控制。
最后,在烧制方面,掌握了适宜的温度和时间,使得施釉后的瓷器既能保持坚固耐用,同时也呈现出美观绮丽的效果。
2.3 宋代瓷器施釉的色彩和纹饰特点宋代瓷器在施釉工艺方面突出表现在色彩和纹饰上。
上釉的五种基本方法

上釉的五种基本方法
上釉是一项非常重要的陶瓷工艺,能够使陶瓷表面变得光滑、耐磨、易清洁,同时还能赋予陶瓷更多的装饰性和艺术性。
下面我们来介绍一下上釉的五种基本方法:
1. 涂刷法:这是最常见的上釉方法,也是最简单的方法之一。
将釉料涂刷在陶瓷表面,并用刷子均匀涂开,然后送入窑中烧制即可。
2. 浸泡法:这种方法适用于形状规则的陶瓷制品,比如碗、盘、瓶等。
将陶瓷制品放入釉料中浸泡一段时间,使釉料充分渗透到制品表面,然后取出晾干,送入窑中烧制。
3. 喷涂法:这种方法适用于形状复杂的陶瓷制品,比如花瓶、雕塑等。
将釉料放入喷枪中,通过喷枪将釉料均匀地喷洒在制品表面,然后送入窑中烧制。
4. 滴落法:这种方法适用于需要在陶瓷表面形成图案的制品,比如陶瓷花瓶、陶瓷画等。
将釉料滴在制品表面,通过流动和滴落形成不同的图案,然后送入窑中烧制。
5. 雕刻法:这种方法适用于需要在陶瓷表面雕刻出图案或文字的制品,比如陶瓷印章、陶瓷餐具等。
将釉料涂在制品表面,然后用特制的雕刻工具在釉面上进行雕刻和刻画,最后送入窑中烧制。
以上就是上釉的五种基本方法,不同的方法适用于不同的陶瓷制品和不同的要求,我们可以根据需求选择合适的方法来进行上釉。
陶瓷工艺品介绍(3篇)

第1篇一、陶瓷工艺品的历史陶瓷工艺品起源于我国新石器时代,距今已有7000多年的历史。
最早的陶瓷制品为黑陶,主要分布在黄河流域。
随着时代的发展,陶瓷工艺逐渐成熟,出现了彩陶、青瓷、白瓷、釉瓷等不同类型的陶瓷制品。
宋代是陶瓷工艺的鼎盛时期,出现了汝窑、定窑、哥窑、官窑等著名的瓷窑。
明清时期,陶瓷工艺品进一步发展,形成了丰富多彩的艺术风格。
二、陶瓷工艺品的种类1. 黑陶:黑陶是我国最早的陶瓷制品,具有独特的艺术风格。
黑陶制品色泽深沉,质地坚硬,具有较强的耐腐蚀性。
2. 彩陶:彩陶是我国新石器时代晚期的代表性陶瓷制品。
彩陶制品以红、黄、黑、白等颜色为底色,绘有各种图案,具有极高的艺术价值。
3. 青瓷:青瓷是我国古代瓷器的一种,以其釉色青翠、造型优美而著称。
青瓷制品在宋代达到鼎盛,有汝窑、定窑、哥窑、官窑等著名瓷窑。
4. 白瓷:白瓷是我国古代瓷器的一种,以其胎质洁白、釉色纯净而著称。
白瓷制品在唐代开始兴起,宋代达到鼎盛。
5. 釉瓷:釉瓷是我国古代瓷器的一种,以其釉色丰富、装饰手法多样而著称。
釉瓷制品在唐代开始兴起,明清时期达到鼎盛。
6. 釉上彩瓷:釉上彩瓷是在瓷器上绘制图案,然后进行高温烧制而成。
釉上彩瓷制品具有色彩鲜艳、图案丰富等特点。
7. 釉下彩瓷:釉下彩瓷是在瓷器上绘制图案,然后进行低温烧制,图案在釉下显现。
釉下彩瓷制品具有图案清晰、色泽稳定等特点。
8. 紫砂壶:紫砂壶是我国传统的茶具,以江苏宜兴的紫砂泥为原料,具有透气性好、保温性能强等特点。
三、陶瓷工艺品的制作工艺1. 拉坯:拉坯是陶瓷制作的基础工艺,通过手工旋转陶轮,使泥料形成所需的形状。
2. 修坯:修坯是在拉坯的基础上,对陶瓷制品进行精细加工,使其表面光滑、线条流畅。
3. 洗泥:洗泥是将陶土中的杂质去除,提高陶土的纯度。
4. 配釉:配釉是调制釉料的过程,釉料的质量直接影响陶瓷制品的色泽和质感。
5. 施釉:施釉是将釉料均匀涂抹在陶瓷制品表面,使制品表面光滑、色泽均匀。
陶瓷工艺学第九章粘结修坯与施釉

干法修坯和湿法修坯
(1)干法修坯
坯体含水率6%~10%或者更低时修坯 工具:各种形状的修坯刀、0#、1#、 刚玉砂布或60~80 目的铜筛网和泡沫塑料、抹布、帚子等蘸水。
切削
打磨
抹水
特点:坯体强度高,坯体不易变形, 操作难度大, 粉尘大。
(2)湿法修坯
使坯体带正电荷,釉料随着压缩空气向坯体移
动,达到施釉的目的。
特点:釉层分布均匀,生产效率高产量 大,釉浆浪费少。设备复杂,维持困难,劳
动安全保护要求严格。
3. 干法施釉 近年来在墙地砖生产中采用的一种新工
艺。随着干法制釉工艺的发展这种施釉方法
有着广阔的前景。
(1)流化床施釉 (2)釉纸施釉
(3)干法静电施釉
特点:节约釉料,省工、省时、节能无污染, 只适合光滑釉面装饰选择范围窄,干 釉层强度低。技术不成熟。
3.4 撒干釉
通过撒干釉,结合釉浆施釉法,实现多 层次、不同部位、不同粗细、不同熔化温度 不同颜色的釉料施于一块墙地砖上,得到斑 晶状多色装饰或大理石、花岗岩等仿石效果。
(1)几种常用的撒干釉工艺流程
(相对密度1.25~1.7的釉浆)附着于坯体表面。 方法:浸釉、浇釉、荡釉、涂刷釉、喷釉、 甩釉等 。
1.1 浸釉法(蘸釉) 日用陶瓷 、高压电瓷等。
1.2 浇釉(淋釉)
(1)手工浇釉 (2)机轮浇釉 (3)钟罩式浇釉 弧形釉幕 (4)鸭嘴式浇釉 直线釉幕
(大件坯体) (日用陶瓷) (墙地砖) (墙地砖)
第九章 粘结、修坯与施釉源自第一节 粘接与修坯 第二节 施釉
第一节 粘接与修坯
1.坯体粘接
1.1 粘接方法
(1)干法粘接 坯体含水率在3%以下进行的粘接。 特点:对操作工人技术要求较高,粘接件 不易变形。
- 1、下载文档前请自行甄别文档内容的完整性,平台不提供额外的编辑、内容补充、找答案等附加服务。
- 2、"仅部分预览"的文档,不可在线预览部分如存在完整性等问题,可反馈申请退款(可完整预览的文档不适用该条件!)。
- 3、如文档侵犯您的权益,请联系客服反馈,我们会尽快为您处理(人工客服工作时间:9:00-18:30)。
陶瓷的施釉一、釉的概念釉是熔融在陶瓷制品表面上一层很薄很均匀的接近玻璃的物质。
二、施釉的概念施釉是将深度一定的釉浆,即悬浮在水中的釉料,利用压缩空气喷到生坯表面上。
生坯很快地吸收湿釉中的水分并形成一定的较硬的表面。
在烧成后的制品表面就形成300到400微米厚度的釉层。
三、施釉步骤1、制釉(分为白釉和色釉两类进行说明)(1)白釉高档的豪华卫生陶瓷产品,已经有了使用锡的氧化物的釉面配方;中低档产品釉的配方中使用了硅酸锆。
使用专用的预混原料,锡熔块釉只需与水混合并加入到原料中。
粒度一般控制在10微以下,颗粒占65%~75%。
当烧到“70~1230℃时,就玻化而形成白釉,几乎可以不考虑缩釉。
这是所用的釉面配方之一。
第二种配方,锆乳浊釉。
要将釉料球磨至粒度在10微米以下的颗粒占到75%~85%,才能在1150~1230C温度范围内烧成时,形成比较好的釉面。
乳浊剂费用较低,但准备费用较高,更重要的是,因为颗粒细小,有约3%的产品易发生缩釉缺陷。
这就需要有较好的生产条件。
若其中90%~100%的产品可以卖到标准价格,使用硅酸锆则比较经济合理:若需重烧,考虑到一般重烧损失及费用,就不够经济了。
而第三种釉可以在原料消耗和生产工艺之间达成折衷。
它需要球磨几个小时,使70%~80%的颗粒小于10微米。
考虑产品的外观要求,上述原料都必须经过充分的烧成,而且要达到同样质量。
由于每种成分都经过严格测试,在产品经过窑炉烧成后,就能够获得理想的釉面。
釉浆必须至少一个月测试一次,即将釉浆喷到两个经过标准干燥的、未经烧成的测试片表面。
然后在实验室的窑炉中烧成,这种窑炉可以使其中一个试样升温到1250℃,另一个(放在窑炉尾部区域)则升温到1150℃,分开进行测试烧成。
烧成膨胀率也必须一个月测试一次,并与坯体进行比较。
(2)色釉彩色制品价格较高,而且也比白色制品畅销。
但由有色原料制备色釉要比制备白釉贵得多。
因此在喷釉时,应严格控制釉层的厚度,这就需要有一个灵敏度高的控制系统。
作为着色剂的原料,在使用前应测试其溶解度,可溶性着色剂或许会流动并造成产品变异,已配好的釉料,通常是由专门的厂家提供的。
但在购买前都应进行测试,即在实验室内测试其玻化温度及气氛制度。
购买干燥的、已混合好的基釉,然后加入着色剂和水,球磨到着色剂完全分散开。
测试、调节、再测试、贮存,加入粘结剂,最后使用。
这是通常的使用过程。
在经过烧成测试之后,与标准釉试板(样本)和标准花饰板在下述灯光条件下进行对比:(1)日光下或者模拟日光照明下;(2)明亮的日光灯和减弱的日光灯照明下;(3)钨丝灯照明下:(4)荧光灯照明下。
白釉和色釉都必须通过检测。
检测最好是在装备有各种类型灯的暗室中进行。
在一种灯照下,看上去很相似的色釉,在另一种灯照下,就可能有很大的不同。
例如一种白色的釉,在明亮的日光灯下,看上去比标准样本明亮。
然而在昏暗的灯光下看时,则没有标准样本白亮。
这是因为它没有标准样本那样好的反光度。
为了实现标准的喷釉工作条件,施釉必须调节到20~25℃的标准温度.釉浆粘度过大时,可以通过加入水来降低,或者在加入粘结剂时带入水分。
返回使用的釉浆,必须经过重新混合、重新过筛、重新测试和重新调节等环节。
即使这样,它也只能仅仅作为喷枪控制下,满足釉浆性能的浆料而加入进去。
当条件较好时,在560mm洗面器上,在50秒时间内施釉两次,并且每次厚度正好合适,没有产生一个干燥的、带有釉屑的表面,或者湿釉(否则就会滴到或落到别的制品上)。
一般认为比较好的工作状态是:泥浆密度为1.8kg/1;粘结剂含量为0.7%;干坯温度均匀,通常在20~25℃。
(干坯温度高时,吸釉快;反之,吸釉慢)。
2、施釉操作途径(分为人工施釉、机械手施釉以及静电施釉三类说明)(1)人工施釉在搅拌条件下施加一定压力(2Pa)把釉浆从管道中压入手提喷枪内,利用喷枪巾压力为4Pa的压缩空气,将釉浆压出,并喷射到生坯上。
在施釉时,釉浆会失去部分水分。
干的坯体会很快地吸收刚喷射到表面上的釉浆内的水分。
一个普通工人每天能够对300件产品施白釉两次;或者对200件较厚重的产品施色釉。
还包括完成清洗制品、清除产品上局部的余釉等工作。
施釉后的产品,被装上坯车送往窑炉烧成。
喷釉时小心以防止釉浆回溅。
通过改变颜色釉的厚度,可以达到“质朴”的效果,如颇受欢迎的棕色、蓝色和墨绿色等色釉。
其他色彩,也可以通过以下的途径得到:如在洗面器的内部喷一层灰白的色釉,而在外面喷一种与制品形状相符的深色釉,两种颜色的交接线经过仔细研究,看上去比同一种色调更加引人注目。
这个方法也很容易做到。
灰白色的盆子受到大众欢迎的原因是它对肥皂泡沫的显露没有深色的明显。
生产商的鉴别标志,可以通过丝网印刷到刚上釉的表面上。
印前坯体表面必须先磨平滑。
做标记的位置目前已发展到在有限位置做标记。
(2)机械手施釉施釉机械手是靠模仿人手施釉的动作而工作的,但生产速度比一个熟练的施釉工快20%。
一般产量为:每班次500个洗面器;或者400个坐便器。
一个人可以同时在两台机器上装坯和卸下制品,更换颜色及改变图案,都可以很快地进行。
然而,实际上在使用中并没有降低废品率,这是将机械手与一个好的喷釉工相对照得出的结论。
而且对许多卫生陶瓷厂家而言,它的单位成本也较高,(3)静电施釉静电施釉装置可以安装在施釉线(运输机)旁边,对运输机上的生坯施釉。
一般的静电施釉装置共装有9个喷枪,可进行雾化喷釉,其喷出的雾粒比一般喷釉要小,速度也低,其中有一部分雾粒喷到生坯表面外,但大多数则在磁场作用下被生坯吸引到表面形成釉层。
电压一般控制在100,000V。
静电施釉的主要优点在于:釉浆利用率高,而且生产效率也比前两种方法高得多。
它可以每班喷釉2000件生坯。
从简单坐便器到洗面器等一系列产品,都可以使用这种方法施釉。
3、施釉方式(1)浸釉①粗陶浸釉将釉浆倒人大木桶搅拌均匀,手持陶坯,在釉浆中滚动,蘸上釉浆。
②瓷器浸釉唐代,德化的瓶和烛台等瓷器采用浸釉方法。
从宋代以后一直沿用浸釉法。
施釉前,坯体要保持清洁,防止灰尘等侵人,釉浆浓度要渊匀,经常搅拌,使釉浆保持浮悬状态。
浸釉时,用手持坯体浸入釉浆中,使釉料吸附在坯体的表面上。
这种方法适用于碗、杯、盘、汤匙等平体制品施内外釉.罐、瓶等制品施外表釉。
小件瓷雕制品亦采用浸釉法,雕塑品异形处、凹形部位,积存的釉水要及时处理,用口吹或用毛笔刷干。
20世纪80年代,手持浸釉改用手架吊着坯件浸釉。
9O年代中后期,又改用机械浸釉。
(2)浇釉浇釉,俗称淋釉,始于宋代,用手工操作,用于陶器的缸、瓮等大件产品。
把坯体倒置放正于架上,手艺熟练的操作者两人合作,一人掌缸,一人泼釉,也有两人同时在同一起点反向浇釉浆。
上浇内釉要及时把缸坯旋转一周,倒出剩釉,擦掉口沿釉流。
新中国成立后,大型瓷雕也用浇釉法。
浇釉时,凹处先擦上水,然后把釉浆浇上,凹处的积釉用嘴风吹平,或用笔刷平。
壶、罐、瓶、碗上内釉采用搪釉法,将釉浆舀入坯体内,用手将坯体左右上下旋转,使坯体内膛壁均匀吸附釉浆,然后将多余釉浆倒出。
50年代中后期,搪釉法改为机轮上釉,把坯件放到旋转的机轮上二,把釉浆倒入坯件中心,借机轮旋转的离心力把釉浆均匀洒到坯体上,多余釉浆溅飞于坯外。
旋釉工效比手工快,釉层厚薄一致,光滑平整,适用于碟、盘、碗类产品。
20世纪80年代,自动流水生产线采用自动上釉法。
(3)刷釉宋代,德化就有刷釉法。
新中国成立后,沿用刷釉法。
一般是用毛刷或毛笔蘸釉浆涂在坯件上。
同一器物施几种不同的釉,厚釉层刷平,缺釉处补釉,均采用刷釉。
(4)喷釉20世纪60年代使用手工喷釉,即用手提喷雾器,装上釉浆喷施。
大多用于大型器物、雕塑品、薄胎瓷或对陶瓷制品有特殊要求的产品。
20世纪80年代引进机械喷釉技术,喷枪连接空气压缩机风管,把釉浆均匀喷到坯体上。
主要用于大批量生产釉面砖、大件雕塑品、二次烧成产品等。
四、施釉的注意事项1、容重的控制施釉前应进行釉浆的测定和调制,釉浆的容重调制到1.70—1.74g/cm³较为合适。
容重过大的釉浆含水分低,流动性差,在外界条件(指喷釉气压、温度、细度)相同的情况下,喷出的釉雾化粒度细而稀少,在同样的操作时间内,坯体所形成的釉层就薄,易造成釉薄、波纹,而且新喷的釉层与坯体的附着能力差,在搬运、装窑过程中易蹭釉。
而容重过小的釉浆,含水分高,流动性太大,釉浆很容易喷出,往往形成釉雾粒度大,在相同的操作方法下,坯体接受到的水分过大,着釉部位很容易出现水分饱和,釉面出现水光。
特别是涂色釉产品要求釉层厚,如果容重过小,极易形成滚釉或薄釉,影响产品的釉面质量。
2、粘度的调制陶瓷施釉前将釉浆的粘度调制到0.8—1.2Pa/s,深色釉粘度要求稍大(1.0—1.4Pa/s)。
在卫生陶瓷喷釉时,粘度太大的釉浆容易造成不出枪,雾化差的釉浆会使釉面出现波纹或不平整,在干燥过程中易发生龟裂,粘度大的釉浆与坯体形成釉层时,釉浆内的空气很难逸出,容易形成闭针孔。
而釉浆粘度太小,喷釉时釉浆很容易出枪,坯体的吸水能力接受不了这种水分的持续快速渗入,当水分喷出速度大于垭体的吸水速度时,釉面出现水分。
这时再接着喷釉,在来不及渗入水分和空气的压力下造成坯釉脱节,失水后形成气泡,干燥后附着能力差,烧后易出现针孔、滚釉等缺陷。
3、气压的控制正常喷釉的气压控制在3—4.5MPa。
若喷釉气压偏低,釉浆雾化程度差,釉面容易造成釉薄和波纹等缺陷;若喷釉气压偏高,喷出釉量小,雾化强,已经粘附在坯体上的釉层在压力的作用下容易遭到破坏。
由于釉浆在坯体上的保水性差,干燥时间内所喷的釉容易出现釉分层,附着能力差。
除此之外,施釉前对精坯进行干燥、吹灰、擦水等工序也不可忽视,目的是对沾的浮灰、油迹、苍蝇屎的湿垭体进行处理。
沾有浮灰、油迹的坯体部分釉层吸附不好,在烧后有剥落的可能。
由于坯体具有一定的气孔率,过湿的坯体釉层难于吸附,但过热的坯体,气孔率过大,在喷釉过程中坯体吸水太快。
由于陶瓷施釉工艺不好控制,很容易影响釉面质量,所以在陶瓷产品(家居饰品、陶瓷茶具、陶瓷花瓶等)施釉时要特别的注意。