双套筒石灰窑技术简介
双膛石灰窑非标出灰系统制作方法与相关技术
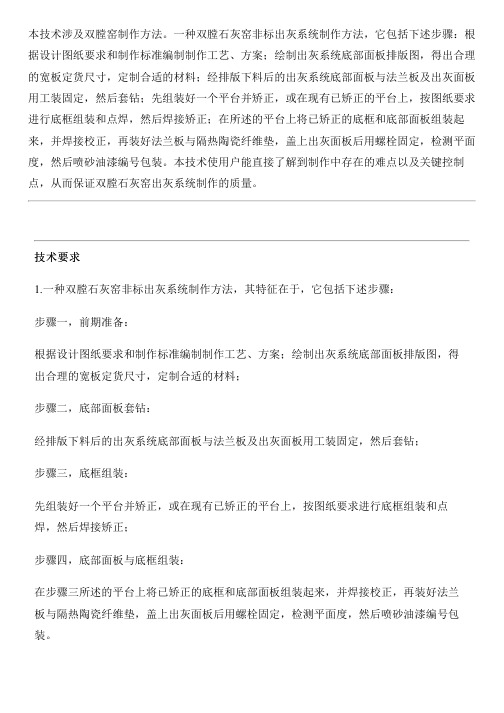
本技术涉及双膛窑制作方法。
一种双膛石灰窑非标出灰系统制作方法,它包括下述步骤:根据设计图纸要求和制作标准编制制作工艺、方案;绘制出灰系统底部面板排版图,得出合理的宽板定货尺寸,定制合适的材料;经排版下料后的出灰系统底部面板与法兰板及出灰面板用工装固定,然后套钻;先组装好一个平台并矫正,或在现有已矫正的平台上,按图纸要求进行底框组装和点焊,然后焊接矫正;在所述的平台上将已矫正的底框和底部面板组装起来,并焊接校正,再装好法兰板与隔热陶瓷纤维垫,盖上出灰面板后用螺栓固定,检测平面度,然后喷砂油漆编号包装。
本技术使用户能直接了解到制作中存在的难点以及关键控制点,从而保证双膛石灰窑出灰系统制作的质量。
技术要求1.一种双膛石灰窑非标出灰系统制作方法,其特征在于,它包括下述步骤:步骤一,前期准备:根据设计图纸要求和制作标准编制制作工艺、方案;绘制出灰系统底部面板排版图,得出合理的宽板定货尺寸,定制合适的材料;步骤二,底部面板套钻:经排版下料后的出灰系统底部面板与法兰板及出灰面板用工装固定,然后套钻;步骤三,底框组装:先组装好一个平台并矫正,或在现有已矫正的平台上,按图纸要求进行底框组装和点焊,然后焊接矫正;步骤四,底部面板与底框组装:在步骤三所述的平台上将已矫正的底框和底部面板组装起来,并焊接校正,再装好法兰板与隔热陶瓷纤维垫,盖上出灰面板后用螺栓固定,检测平面度,然后喷砂油漆编号包装。
2.根据权利要求1所述的双膛石灰窑非标出灰系统制作方法,其特征在于:所述步骤二包括下列步骤:2.1、电脑排版选择所需板宽及长度钢板,确定钢板数控下料尺寸,板宽及板长两边要预留至少5mm余量,测量对角线误差;2.2、采用等离子数控切割机下料,防止板材变形过大;2.3、用磨光机平整下料边缘切割处,将底部面板、法兰框及出灰面板矫平;2.4、在底部面板上放样划线,将已矫平的底部面板、法兰框及出灰面板用工装固定,然后套钻;2.5、将套钻后的底部面板、法兰框及出灰面板按顺序统一编号,方便组装时对应查找。
麦尔兹石灰窑介绍及市场前景分析
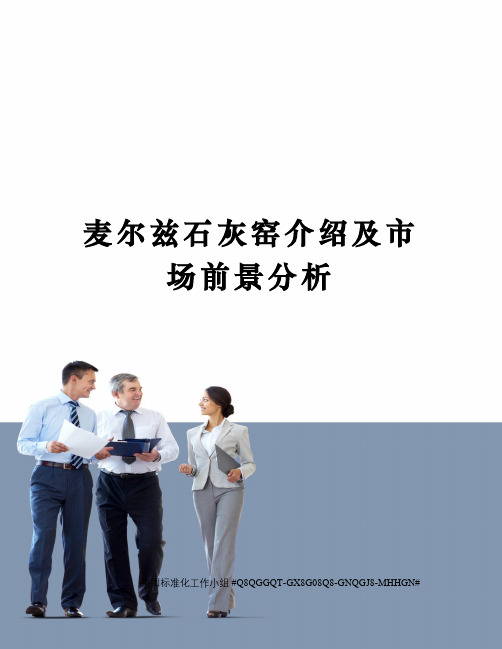
麦尔兹石灰窑介绍及市场前景分析集团标准化工作小组 #Q8QGGQT-GX8G08Q8-GNQGJ8-MHHGN#麦尔兹石灰窑介绍麦尔兹石灰窑又称并流蓄热式石灰窑,麦尔兹石灰窑是瑞士麦尔兹欧芬堡公司技术,麦尔兹欧芬堡公司是全球领先的提供石灰窑专利技术生产高质量石灰和白云石的工程公司,其在全球超过50 多个国家内设计和建造了500 多座石灰窑。
以下是其拥有专利技术的并流蓄热式双膛石灰窑的简单介绍:1.并流蓄热式麦尔兹双膛石灰竖窑⑴麦尔兹窑基本情况并流蓄热式麦尔兹双膛石灰竖窑,是由通道相连的两个窑筒组成的竖窑,其工作原理如下图所示:麦尔兹并流蓄热式双膛石灰窑有两个窑膛,两个窑膛交替轮流煅烧和预热矿石,在两个窑膛的煅烧带底部之间设有连接通道彼此连通,约每隔15 分钟换向一次以变换窑膛的工作状态。
在操作时,两个窑膛交替装入矿石,燃料分别由两个窑膛的上部送入,通过设在预热带底部的多支喷枪使燃料均匀地分布在整个窑膛的断面上,使原料矿石得到均匀的煅烧。
麦尔兹窑使用的是流体燃料,如煤气、油、煤粉等均可。
助燃空气用罗茨风机从竖窑的上部送入,助燃空气在与燃料混合前在预热带先被预热,然后煅烧火焰气流通过煅烧带与矿石并流,使矿石得到煅烧。
煅烧后的废气通过连接两个窑膛的通道沿着另一窑膛的预热带向窑顶排出。
由于长过程的并流煅烧,石灰质量非常好,且由于两个窑膛交替操作,废气直接预热矿石,热量得到充分的利用,所以单位热耗在各种窑型中最低。
为了适应并流蓄热式石灰窑对不同用户的要求,麦尔兹石灰窑所做的改进和技术发展包括:……麦尔兹并流蓄热式圆形窑的悬挂缸结构(尤其适用于产量在日产600 吨或以上的大型窑型);……用改进的专利上料技术来增加产量;……通过专门上料技术(三明治加料)获得更佳的石灰石利用率;……并流蓄热式石灰窑新获得专利的燃烧系统,可采用低热值的煤气或及固体和气体燃料(比如煤和热值约800-900 大卡的高炉煤气)的双燃料系统。
双梁窑、双膛窑、套筒窑比较
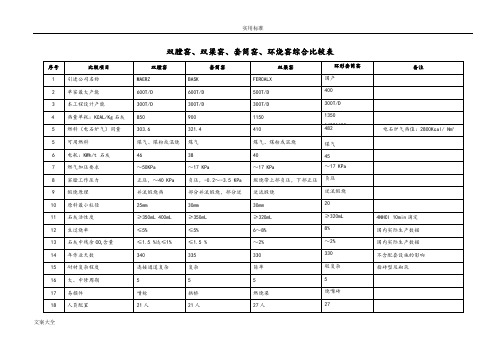
双膛窑、双梁窑、套筒窑、环烧窑综合比较表文案大全文案大全各种石灰窑技术特点1双膛式石灰竖窑窑型特点1.1双膛式石灰竖窑技术特点1)生产规模200~600t/d。
2)适用多种燃料:天然气、煤粉、发生炉煤气、电石炉尾气、兰炭气、焦炉煤气、转炉煤气、高炉煤气(热值≥800 kcal/m3)、混合煤气或煤粉与煤气的混合燃料。
3)热耗低,热能利用合理,在四大窑型中热消耗量最低,850 Kcal/Kg石灰。
双膛煅烧预热交替进行,能最大限度的回收废气预热。
交换完毕的废气温度低于120摄氏度。
4)煅烧方式为并流煅烧,同时换热方式为逆流换热,符合碳酸钙分解的化学反应机理。
5)自动化控制程度高,能根据设定产量设定和热值的检测值,自动控制整个热工系统的各个参数。
最大程度上减少人为的干预,产品质量稳定。
6)产品质量高:活性度大于350ml(4mol 10min HCL 滴定),生过烧率小于5%。
7)年生产率高:340天/年8)此窑型为行业公认的节能、环保、产品品质高的先进窑型1.2双膛式石灰竖窑窑体结构及工艺特点1)窑体共设置2个窑膛,下部通过专设的结构进行联通。
一个窑膛煅烧的同时,高温废气通过底部联通装置进入另一窑膛与石灰石换热。
2)经过一个周期(约12min),两个窑膛的工作制度将进行交换,其燃料(煤粉)及燃烧空气转换到将要煅烧的窑膛,废气抽出系统切换到蓄热窑膛。
3)在换向的时间段(约1min),石灰窑完成石灰石受料及出灰。
4)换向停窑期间:助燃风机及石灰冷却风机不停机,只是通过三通释放闸板进行释放。
5)两个窑膛呈圆形,自上而下分为预热带、煅烧带、冷却带三部分。
燃料喷枪下端以上为预热带,底部连接通道至喷枪下端面为煅烧带,连接通道下部至冷却风帽断面为石灰冷却带。
6)采用两窑膛煅烧换热交替进行是本窑型特有的技术。
高温废气与窑体整个高度范围内的石灰石进行充分热交换。
7)采用并流煅烧方式严格符合了石灰煅烧分解的要求。
即可以实现开始煅烧时温差大,煅烧结尾时温差小的要求。
双膛石灰窑构造
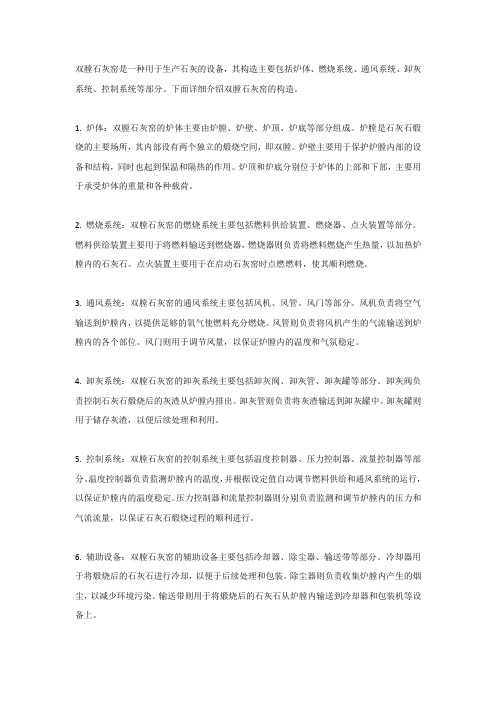
双膛石灰窑是一种用于生产石灰的设备,其构造主要包括炉体、燃烧系统、通风系统、卸灰系统、控制系统等部分。
下面详细介绍双膛石灰窑的构造。
1. 炉体:双膛石灰窑的炉体主要由炉膛、炉壁、炉顶、炉底等部分组成。
炉膛是石灰石煅烧的主要场所,其内部设有两个独立的煅烧空间,即双膛。
炉壁主要用于保护炉膛内部的设备和结构,同时也起到保温和隔热的作用。
炉顶和炉底分别位于炉体的上部和下部,主要用于承受炉体的重量和各种载荷。
2. 燃烧系统:双膛石灰窑的燃烧系统主要包括燃料供给装置、燃烧器、点火装置等部分。
燃料供给装置主要用于将燃料输送到燃烧器,燃烧器则负责将燃料燃烧产生热量,以加热炉膛内的石灰石。
点火装置主要用于在启动石灰窑时点燃燃料,使其顺利燃烧。
3. 通风系统:双膛石灰窑的通风系统主要包括风机、风管、风门等部分。
风机负责将空气输送到炉膛内,以提供足够的氧气使燃料充分燃烧。
风管则负责将风机产生的气流输送到炉膛内的各个部位。
风门则用于调节风量,以保证炉膛内的温度和气氛稳定。
4. 卸灰系统:双膛石灰窑的卸灰系统主要包括卸灰阀、卸灰管、卸灰罐等部分。
卸灰阀负责控制石灰石煅烧后的灰渣从炉膛内排出。
卸灰管则负责将灰渣输送到卸灰罐中。
卸灰罐则用于储存灰渣,以便后续处理和利用。
5. 控制系统:双膛石灰窑的控制系统主要包括温度控制器、压力控制器、流量控制器等部分。
温度控制器负责监测炉膛内的温度,并根据设定值自动调节燃料供给和通风系统的运行,以保证炉膛内的温度稳定。
压力控制器和流量控制器则分别负责监测和调节炉膛内的压力和气流流量,以保证石灰石煅烧过程的顺利进行。
6. 辅助设备:双膛石灰窑的辅助设备主要包括冷却器、除尘器、输送带等部分。
冷却器用于将煅烧后的石灰石进行冷却,以便于后续处理和包装。
除尘器则负责收集炉膛内产生的烟尘,以减少环境污染。
输送带则用于将煅烧后的石灰石从炉膛内输送到冷却器和包装机等设备上。
总之,双膛石灰窑的构造包括炉体、燃烧系统、通风系统、卸灰系统、控制系统等多个部分,各个部分之间相互配合,共同完成石灰石的煅烧过程。
套筒石灰竖窑工艺介绍

套筒石灰竖窑工艺介绍讲解人:刘林一、石灰窑的概况1、国内常见的石灰窑有:回转窑、竖窑、BASK套筒竖窑、麦尔兹窑(双膛细粒窑)等。
2、BASK套筒石灰竖窑几种石灰窑比较:(1).煅烧工艺合理:实现逆流和并流共存的煅烧工艺;(2).产品质量高:活性度达到350ml,一般炼钢对活性度的要求较高,化工行业(如电石)对活性度的要求不高,但对生/过烧率有要求;(3).环保安全,负压操作(窑内压力位-1000mm水柱,煤气压力位16KPa,可以在线检查);(4).节能,利用了换热器及二次循环空气;(5).对原料的粒度有要求(一般是30mm~80mm);(6).对原料的成分有要求(MgO的含量≤1.0),否则容易产生设备(换热器)的堵塞。
二、石灰窑的组成1、常见的套筒竖窑三大系统:(1).原料储运+筛分系统(2).竖窑本体焙烧(煅烧)系统(3).成品贮运+筛分系统2、三大系统的组成及工艺流程:(1).原料储运+筛分系统(2).竖窑本体焙烧(煅烧)系统a.套筒竖窑煅烧工艺及结构见下图工艺流程:石灰石原料经卷扬机上料小车(1)、漏斗及溜槽、密封闸门、旋转布料器及料钟(2),进入窑内装料槽(3)。
在窑顶入料口处设置密封闸门,以避免外界空气进入而影响套筒竖窑的负压操作。
窑内装石灰石的环形空间是由窑钢外壳(4)内部耐火墙和与其同心布置的上、下(5、6)内筒分割形成。
套筒竖窑有上、下两层烧嘴(7、8)并均匀错开布置,每层烧嘴有七个圆柱形燃烧室(9、10),每个燃烧室都有一个用耐火材料砌筑的从窑外壳到下内筒的过桥(16),高温气体从燃烧室内出来,经过过桥下面形成的空间进入料层。
两层烧嘴将套筒竖窑分成两个煅烧带,上煅烧带为逆流,下煅烧带为并流。
并流带下部为冷却带,在冷却带石灰将自身热量传递给冷却的空气,此处仍为逆流。
冷却石灰的空气由于废气风机作用向上抽,而石灰则在冷却带的底部通过液压推杆(11)及出灰装置(12)排出,排出的石灰进入到位于套筒竖窑底部的石灰料仓内(13),石灰料仓内的石灰通过振动给料机(14),经一定的时间间隔被排出。
双膛石灰窑介绍-文档资料
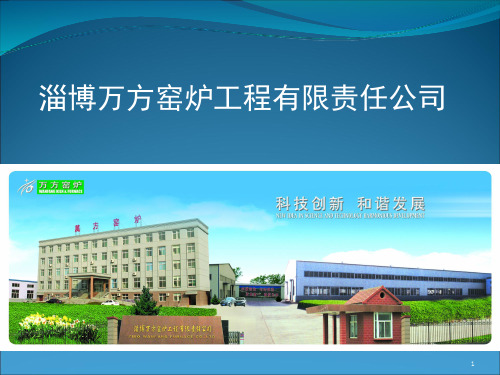
双膛蓄热高活性石灰竖窑简介
由于石灰石在煅烧初期分解需要吸收大量的热 量,随着物料的下移,石灰石逐步分解,石灰石需 要吸收的热量就逐渐降低,而在煅烧结尾阶段,为 了避免石灰的过烧,必须大幅度降低石灰的吸热率, 只有在这种条件下才能煅烧出高活性度的石灰。
11
双膛蓄热高活性石灰竖窑简介
双膛蓄热式高活性石灰竖窑就是基于以上煅烧 原理下一种理想的窑型。在煅烧膛初期,被物料加 热的助燃空气和燃料充分混合燃烧,达到高活性煅 烧需要的理想温度,随着物料的下移和燃烧的逐渐 结束,物料吸收的热量逐渐减少,燃料燃烧后的产 物和物料分解出的CO2经连接通道进入蓄热膛,体 现了并流蓄热的特点。
13双膛蓄热高活性石灰竖窑工作原理图中a和b烧带底部相互连通物料沿两个窑膛分别向下运行14双膛蓄热高活性石灰竖窑工作原理在窑膛a煅烧时助燃空气和燃料在窑膛a中与物料并流使最热的火焰与温度较低且吸收热量最大的物料接触相对温度较低的燃烧气体与逐步煅烧好的物料接触已达到均匀煅烧的条件且取得很高的热效率燃烧后的产物与物料分解出的co经过连接通道进入窑膛b15双膛蓄热高活性石灰竖窑工作原理此时窑膛b作为蓄热窑膛窑膛中的石灰石从废气中吸收热量同时使废气冷却到较低温度物料积蓄的热量在下一个周期时用于加热参加燃烧之前的助燃空气在这种情况下窑膛a为燃16双膛蓄热高活性石灰竖窑工作原理下一个周期窑膛a和窑膛b相互轮换即窑膛a成为蓄热窑膛窑膛b称为燃烧窑膛
14
双膛蓄热高活性石灰竖窑工作原理
此时窑膛B作为蓄热窑膛,窑膛中的石灰石从 废气中吸收热量,同时使废气冷却到较低温度, 物料积蓄的热量,在下一个周期时用于加热参加 燃烧之前的助燃空气,在这种情况下,窑膛A为燃 烧并流窑膛,窑膛B为蓄热窑膛。
15
双膛蓄热高活性石灰竖窑工作原理
麦尔兹石灰窑介绍及市场前景分析
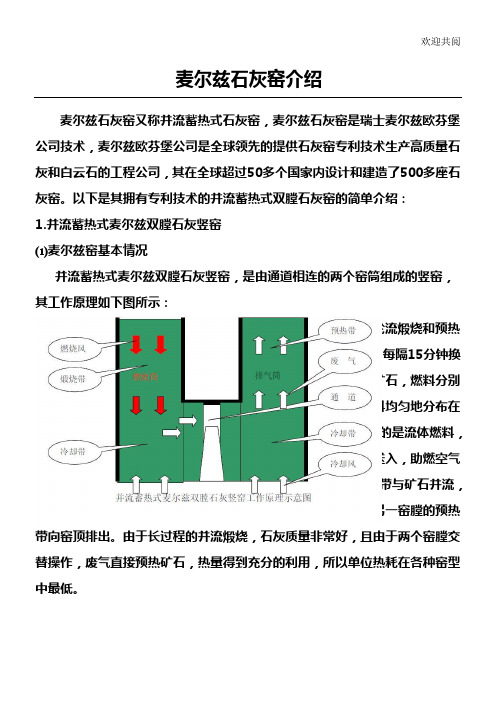
欢迎共阅麦尔兹石灰窑介绍麦尔兹石灰窑又称并流蓄热式石灰窑,麦尔兹石灰窑是瑞士麦尔兹欧芬堡公司技术,麦尔兹欧芬堡公司是全球领先的提供石灰窑专利技术生产高质量石灰和白云石的工程公司,其在全球超过50多个国家内设计和建造了500多座石1.麦尔兹并流蓄热式双膛石灰窑有两个窑膛,两个窑膛交替轮流煅烧和预热矿石,在两个窑膛的煅烧带底部之间设有连接通道彼此连通,约每隔向一次以变换窑膛的工作状态。
在操作时,两个窑膛交替装入矿石,燃料分别由两个窑膛的上部送入,通过设在预热带底部的多支喷枪使燃料均匀地分布在整个窑膛的断面上,使原料矿石得到均匀的煅烧。
麦尔兹窑使用的是流体燃料,如煤气、油、煤粉等均可。
助燃空气用罗茨风机从竖窑的上部送入,助燃空气在与燃料混合前在预热带先被预热,然后煅烧火焰气流通过煅烧带与矿石并流,使矿石得到煅烧。
煅烧后的废气通过连接两个窑膛的通道沿着另一窑膛的预热带向窑顶排出。
由于长过程的并流煅烧,石灰质量非常好,且由于两个窑膛交替操作,废气直接预热矿石,热量得到充分的利用,所以单位热耗在各种窑型中最低。
为了适应并流蓄热式石灰窑对不同用户的要求,麦尔兹石灰窑所做的改进和技术发展包括:……麦尔兹并流蓄热式圆形窑的悬挂缸结构(尤其适用于产量在日产600吨或以上的大型窑型);……用改进的专利上料技术来增加产量;年建-……由于两个窑身交替换向操作,废气直接预热矿石,热量得到充分利用,单位产品热耗最低,热回收率超过83%;其热损耗可以到800-890Kcal/kg(3350-3720kJ/kg);最低的热耗意味着最低的运行成本,比如一座日产600吨以煤粉为燃料的石灰窑,标准煤煤耗为每吨石灰产品114kg-120kg的煤。
简单计算一下:保守假设生产每吨石灰节省20kg的煤,以日产600吨的石灰总量,即每天节省600X20kg =12,000.-公斤的煤;……使用各类燃料之最大灵活性。
麦尔兹石灰窑的设计能接受可使用各种的气体,液体及固体燃料,详列如下:气体(天然气;丙烷,丁烷及石油气;焦炉煤气;转炉煤气;电弧炉煤气,电石炉气)液体(轻,中及重燃6。
意大利西姆公司双D石灰窑(双筒蓄能石灰窑)简介
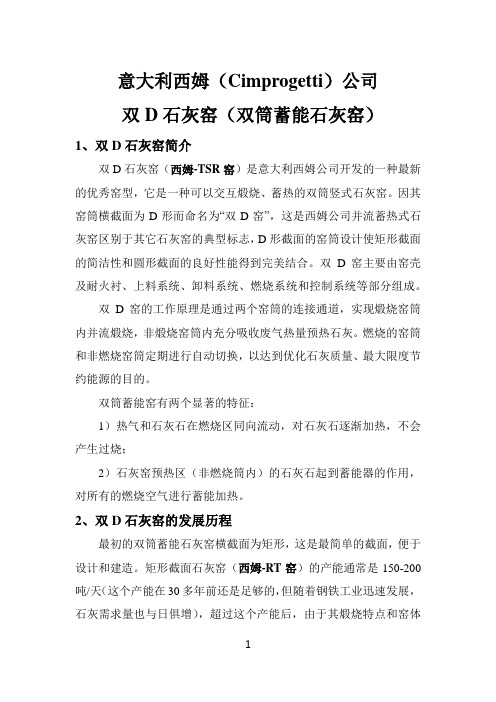
意大利西姆(Cimprogetti)公司双D石灰窑(双筒蓄能石灰窑)1、双D石灰窑简介双D石灰窑(西姆-TSR窑)是意大利西姆公司开发的一种最新的优秀窑型,它是一种可以交互煅烧、蓄热的双筒竖式石灰窑。
因其窑筒横截面为D形而命名为“双D窑”,这是西姆公司并流蓄热式石灰窑区别于其它石灰窑的典型标志,D形截面的窑筒设计使矩形截面的简洁性和圆形截面的良好性能得到完美结合。
双D窑主要由窑壳及耐火衬、上料系统、卸料系统、燃烧系统和控制系统等部分组成。
双D窑的工作原理是通过两个窑筒的连接通道,实现煅烧窑筒内并流煅烧,非煅烧窑筒内充分吸收废气热量预热石灰。
燃烧的窑筒和非燃烧窑筒定期进行自动切换,以达到优化石灰质量、最大限度节约能源的目的。
双筒蓄能窑有两个显著的特征:1)热气和石灰石在燃烧区同向流动,对石灰石逐渐加热,不会产生过烧;2)石灰窑预热区(非燃烧筒内)的石灰石起到蓄能器的作用,对所有的燃烧空气进行蓄能加热。
2、双D石灰窑的发展历程最初的双筒蓄能石灰窑横截面为矩形,这是最简单的截面,便于设计和建造。
矩形截面石灰窑(西姆-RT窑)的产能通常是150-200吨/天(这个产能在30多年前还是足够的,但随着钢铁工业迅速发展,石灰需求量也与日俱增),超过这个产能后,由于其煅烧特点和窑体结构,在窑体外部的四个角落就容易出现生烧。
双D石灰窑(西姆-TD 窑)正是在这样的背景下产生的,事实上它就是矩形截面窑的升级版,其目的就是为了消除矩形截面窑的缺陷。
双D窑面世后,其石灰产能达到了200-550吨/天。
西姆公司也因为双D窑的特殊性能,在全世界产生积极影响。
随后,面对当今世界石灰窑大型化的趋势,西姆公司迅速做出反应,设计开发了环形截面通道的新型双D窑(西姆-RD窑)。
新型双D窑代表了该领域的尖端水平,同时保留了双筒蓄能石灰窑成熟的特性(燃烧和冷却风单元、液压动力装置、自动化和控制系统逻辑等)。
窑体由2个圆柱状部分组成,上部窑筒直径较小,用于石灰石装料和燃烧,下部窑筒直径较大,用于石灰冷却和石灰卸料。
- 1、下载文档前请自行甄别文档内容的完整性,平台不提供额外的编辑、内容补充、找答案等附加服务。
- 2、"仅部分预览"的文档,不可在线预览部分如存在完整性等问题,可反馈申请退款(可完整预览的文档不适用该条件!)。
- 3、如文档侵犯您的权益,请联系客服反馈,我们会尽快为您处理(人工客服工作时间:9:00-18:30)。
双套筒石灰窑技术简介
发布时间: 2007-12-14 被阅览数: 1090 次
孙雪刚
双套筒窑采用了窑壳和内套筒的特殊结构,使并流煅烧过程在一个窑体内进行,且占地面积比双膛窑少,生产出来的石灰活性度较高,可达350ml以上,石灰中残余CO2含量小于1.5%,如原料条件好,石灰活性度还可提高,且产品的生烧和过烧现象较少。
双套筒窑使用的燃料范围宽,可使用发热值在1100kCal/Nm3以上的低热值煤气,且煤气压力仅为15kPa左右的常规压力。
整座窑采用循环气体、高温废气换热等方式循环利用热能,所以产品所需的热耗也较低,是一种节能型的石灰窑。
煅烧采用则同时采用了气流的并流和逆流原理,有效地解决了生、过烧问题,提高了石灰的活性。
并流煅烧方式的优点是:物料在煅烧带上部开始煅烧时,燃料在此处于正好混合开始燃烧,温度较高,煅烧效率较高,而在煅烧带下部,石灰煅烧过程基本完成,石灰在此处不再需要太多热量,而燃料的燃烧产物也基本将热量传递给了物料,温度降低,因此石灰活性度较高,可在350 ml以上,过、生烧率低于5%。
1、双套筒窑的特点:
(1)采用并流加热系统,在物料煅烧尾期,物料与烟气温差小,石灰不会造成生、过烧,且活性度高。
采用良好的换热系统,排烟温度低,单位热耗低。
(2)双套筒窑具有备工艺先进、烧成石灰品质好、能耗低、负压操作烟尘少、维护费用低和自动化程度高,窑体设备简单,操作方便。
且投资少,占地面积小。
(3)由于采用烟气回流喷射技术,有较长的并流燃烧带,产出石灰活性度高。
热耗较低。
2、双套筒窑工艺说明
料车自动上料到窑顶,通过溜槽进入旋转布料器,石灰石通过料盅,到上内套筒顶部分布器,进行二次布料,然后进入窑体。
料盅具有锁气的功能。
石灰石先经预热带,再到煅烧带、冷却带。
由于废气风机从窑顶抽气,石灰冷却空气从窑底自然吸入窑体,冷却石灰。
石灰在液压装置的驱动下,经出灰平台,进入窑底料仓。
窑底电振定期对窑底料仓进行清仓。
3、双套筒窑产品规格及基本参数(表一)
4、双套筒窑的性能表(表二)
表二:双套筒窑性能表
5、双套筒窑结构的先进性主要表现在三个方面:
其一,通过窑内四次物料的自动分布,使物料在窑内分布得更均匀,保证煅烧过程中热量始终均匀分布在物料上。
从结构上看,双套筒窑窑本体由窑外壳和内套筒组成,从上至下大致可分为四个区域:即石灰石预热带,上、下燃烧室之间逆流煅烧带,下燃烧室下部并流煅烧带和石灰冷却带,物料与气流就在内、外壳体之间流动。
在物料流动方向上,窑顶的横梁、上拱桥、下拱桥和出料门四部分结构,上下两两之间呈60°角(以500TPD 环型套筒窑为例)交错分布,实现了物料在向下流动的过程中的自动多次分布,保证了不同粒度的物料在窑体内均能均匀受热煅烧,煅烧出来的石灰质量稳定。
其二,在煅烧带形成并流煅烧过程,保证石灰石的充分煅烧,生产出高活性石灰产品。
双套筒窑利用从喷射管内喷出的高速流动热空气,在下燃烧室处产生低压区,使从下烧嘴进入的燃料和助燃空气与窑内的物料在下燃烧室下部同向流动并与之反应,形成并流煅烧带。
在并流煅烧区域内,石灰石原料充分与高温气体接触,反应生成石灰产品,故生产出来的石灰活性度较高。
在窑内形成循环气体,并通过控制循环气体的温度,使煅烧过程得到控制并充分利用热量。
环形套筒窑内的循环气体是指从下烧嘴进入的燃料和助燃空气,在下燃烧室下部的并流煅烧带与石灰石原料充分反应后,与从窑
底冷却带进入的冷却空气一起进入到双套筒窑下内套筒上段内,后经过上拱桥内的循环气体通道管流入喷射器,与喷射管内的热空气混合后一起再次喷射进入下燃烧室的这一部分气体。
循环气体的产生,在窑内形成了并流煅烧带,使双套筒窑能煅烧生产出高活性度的石灰。
同时循环气体也使窑内的热量得到了充分的利用,降低了石灰产品的热耗。
再次,人们通过控制循环气体在窑内的流量和气体温度,实现了对双套筒窑煅烧过程的控制,生产出来的石灰质量得到很好的控制,产品的生烧和过烧现象减少。
其三, 独立燃烧室位于拱桥下面,火焰在燃烧室内,不进入石灰料层,保证石灰石受热均匀。
同时,双套筒窑处于负压操作下的生产过程,很好的减少了因石灰窑工作给周边环境带来的污染,改善了操作人员的工作环境,也方便了操作人员对整座窑系统的设备工作状况的掌握,设备的检查、维护、维修工作也便利,操作人员能及时发现对石灰窑正常生产潜在的故障,保证了生产的石灰产品的质量。