MIM后处理工艺
徐州mim工艺流程
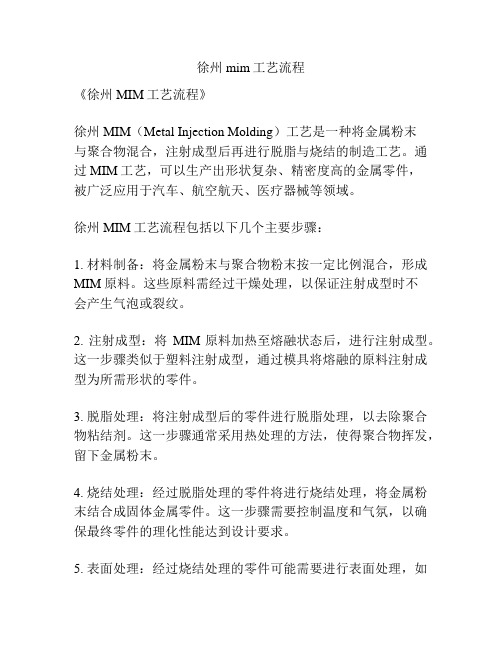
徐州mim工艺流程
《徐州MIM工艺流程》
徐州MIM(Metal Injection Molding)工艺是一种将金属粉末
与聚合物混合,注射成型后再进行脱脂与烧结的制造工艺。
通过MIM工艺,可以生产出形状复杂、精密度高的金属零件,
被广泛应用于汽车、航空航天、医疗器械等领域。
徐州MIM工艺流程包括以下几个主要步骤:
1. 材料制备:将金属粉末与聚合物粉末按一定比例混合,形成MIM原料。
这些原料需经过干燥处理,以保证注射成型时不
会产生气泡或裂纹。
2. 注射成型:将MIM原料加热至熔融状态后,进行注射成型。
这一步骤类似于塑料注射成型,通过模具将熔融的原料注射成型为所需形状的零件。
3. 脱脂处理:将注射成型后的零件进行脱脂处理,以去除聚合物粘结剂。
这一步骤通常采用热处理的方法,使得聚合物挥发,留下金属粉末。
4. 烧结处理:经过脱脂处理的零件将进行烧结处理,将金属粉末结合成固体金属零件。
这一步骤需要控制温度和气氛,以确保最终零件的理化性能达到设计要求。
5. 表面处理:经过烧结处理的零件可能需要进行表面处理,如
研磨、抛光、镀层等。
这些步骤可以提高零件的表面光洁度和耐腐蚀性能。
徐州MIM工艺流程通过将金属粉末与聚合物相结合,使得原本难以加工的复杂形状零件可以得以制造,同时还可以节约材料和减少后续加工工序。
随着技术的不断进步,MIM工艺将有望在更广泛的领域得到应用。
MIM工艺介绍
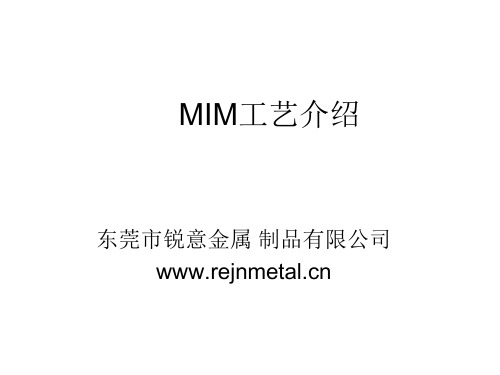
烧结技术
• 金属粉末注射成型技术(Metal Injection Molding,简称MIM)是近年来粉末 冶金学科和工业中发展最迅猛的领域,是现代先进的塑料注射成型技术和传 统粉末冶金技术相结合而形成的一项新型粉末冶金近净型成形技术。一、 MIM成型技术MIM基本丁艺过程是:将微细的金属或陶瓷粉末与有机黏结剂 均匀混合成为具有流变性的物质,采用先进的注射机注入具有零件形状的模 腔形成坯件,新技术脱除黏结剂并经烧结,使其高度质密成为制品,必要时 还可以进行后处理。i亥技术不仅具有常规粉末冶金技术生产效率高,产品一 致性好,少切削或无切削,经济高效的优点,而且克服r传统粉末冶金制品密 度低,材质不均匀,力学性能低,不易成型薄壁复杂件的缺点,特别适合大 批量、小型、复杂以及具有特殊要求的金属零部件的生产加工.该工艺技术在 20世纪8O年代中期实现产业化以来,已获得突飞猛进的发展,注射成型的产 品已遍及计算机信息产业、汽车摩托车产业、医疗卫生器械、家用电器、仪 器仪表、机械制造、化工、纺织、国防军工等领域。到目前为止,已有20多 个国家和地区的几百家公司从事该工艺技术的产品开发、研制与销售工作, 粉末注射成型工艺技术也因此成为新型制造业中开发最为活跃的前沿技术领 域,被誉为世界粉末冶金领域中的开拓性技术,代表着粉末冶金技术发展的 主方向。该工艺的主要特点如下:(1)可成型复杂结构的零件该工艺技术利用 注射机注射成型产品毛坯,保证物料充分充满模具型腔,也就保证了零件复 杂结构的实现。这一点是传统机械加工和常规粉末冶金工艺技术所无法比拟 的,是注射成型工艺发展的坚强基础。(2)注射成型制品
MIM简介
• MIM 简介 • 金属注射成形 • (Metal Injection Molding ,MIM) • • 是一种将金属粉末与其粘结剂的增塑混合料注射于模型中的成形方法。它是先将所选
mim工艺流程

mim工艺流程MIM工艺流程。
MIM(Metal Injection Molding)是一种将金属粉末与聚合物混合,然后通过模具成型和烧结工艺制作金属零件的先进制造技术。
MIM工艺流程包括原料混合、注射成型、脱模、烧结和后处理等环节,下面将详细介绍MIM工艺的具体流程。
首先,原料混合是MIM工艺的第一步。
在这一阶段,金属粉末和聚合物粉末按照一定的配方比例进行混合。
金属粉末通常是由不同种类的金属粉末混合而成,以获得所需的材料性能。
而聚合物粉末则用于提供成型时所需的流动性和可成型性。
混合后的原料需要经过干燥处理,以去除其中的水分和挥发性有机物,确保成型过程中不会产生气泡和缺陷。
接下来是注射成型阶段。
原料混合后,将其装入注射成型机中进行加热熔融,并注入模具中进行成型。
注射成型是MIM工艺中最关键的一步,模具的设计和注射参数的控制直接影响着成型零件的质量和成型周期。
在注射成型过程中,需要控制好温度、压力和流速等参数,以确保成型零件的尺寸精度和表面质量。
成型完成后,进行脱模处理。
脱模是指将成型后的零件从模具中取出的过程。
由于MIM工艺成型的零件通常具有复杂的结构和薄壁结构,因此脱模过程需要特别小心,以避免零件变形或损坏。
同时,还需要对脱模后的零件进行修整和去除支撑结构,以准备后续的烧结工艺。
随后是烧结阶段。
烧结是MIM工艺中最重要的一步,通过高温处理将成型后的零件中的聚合物烧尽,使金属粉末颗粒之间结合成型,最终得到密度高、性能优良的金属零件。
烧结温度和时间是影响零件密度和性能的关键因素,需要根据不同材料和零件的要求进行精确控制。
最后是后处理阶段。
烧结后的零件需要进行表面处理、机加工、热处理等工艺,以满足不同零件的要求。
例如,一些零件需要进行抛光或镀层处理,以提高表面光洁度和耐腐蚀性能;而一些零件还需要进行热处理,以改善材料的力学性能和耐磨性能。
总的来说,MIM工艺流程包括原料混合、注射成型、脱模、烧结和后处理等多个环节,每个环节都需要精心设计和严格控制,以确保最终生产出高质量的金属零件。
MIM金属注射成形工艺解析
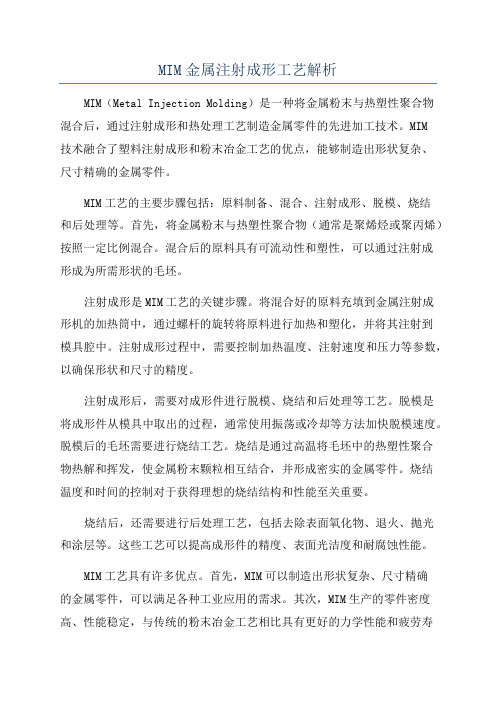
MIM金属注射成形工艺解析MIM(Metal Injection Molding)是一种将金属粉末与热塑性聚合物混合后,通过注射成形和热处理工艺制造金属零件的先进加工技术。
MIM技术融合了塑料注射成形和粉末冶金工艺的优点,能够制造出形状复杂、尺寸精确的金属零件。
MIM工艺的主要步骤包括:原料制备、混合、注射成形、脱模、烧结和后处理等。
首先,将金属粉末与热塑性聚合物(通常是聚烯烃或聚丙烯)按照一定比例混合。
混合后的原料具有可流动性和塑性,可以通过注射成形成为所需形状的毛坯。
注射成形是MIM工艺的关键步骤。
将混合好的原料充填到金属注射成形机的加热筒中,通过螺杆的旋转将原料进行加热和塑化,并将其注射到模具腔中。
注射成形过程中,需要控制加热温度、注射速度和压力等参数,以确保形状和尺寸的精度。
注射成形后,需要对成形件进行脱模、烧结和后处理等工艺。
脱模是将成形件从模具中取出的过程,通常使用振荡或冷却等方法加快脱模速度。
脱模后的毛坯需要进行烧结工艺。
烧结是通过高温将毛坯中的热塑性聚合物热解和挥发,使金属粉末颗粒相互结合,并形成密实的金属零件。
烧结温度和时间的控制对于获得理想的烧结结构和性能至关重要。
烧结后,还需要进行后处理工艺,包括去除表面氧化物、退火、抛光和涂层等。
这些工艺可以提高成形件的精度、表面光洁度和耐腐蚀性能。
MIM工艺具有许多优点。
首先,MIM可以制造出形状复杂、尺寸精确的金属零件,可以满足各种工业应用的需求。
其次,MIM生产的零件密度高、性能稳定,与传统的粉末冶金工艺相比具有更好的力学性能和疲劳寿命。
此外,MIM工艺还具有高效、节能的特点,能够减少生产过程中的材料浪费和能源消耗。
然而,MIM工艺仍然存在一些挑战。
首先,原料的成本较高,这对于大规模生产来说可能增加成本。
其次,MIM工艺对模具的要求较高,模具的制造成本较高。
此外,MIM的工艺周期较长,生产效率相对较低。
总之,MIM金属注射成形工艺是一种先进的金属加工技术,具有制造形状复杂、尺寸精确的金属零件的优势。
MIM工艺介绍及其应用

MIM工艺介绍及其应用MIM(Metal Injection Molding)工艺是一种将金属粉末与热塑性或热固性高分子混合,并通过注射成型和烧结工艺制造出复杂金属零件的技术。
MIM工艺结合了传统金属加工和塑料注射成型技术的优点,能够实现高精度、高复杂度的金属零件制造,并在很多行业得到广泛应用。
MIM工艺的制造过程主要包括以下几个步骤。
首先,将金属粉末与高分子材料混合,并制成类似塑料颗粒的混合物。
然后,将混合物注入金属注射成型机中,通过高压注射将其注射到预先设计好的模具中。
注射成型后,通过烧结工艺将混合物中的高分子材料去除,使金属粉末颗粒相互结合,形成致密的金属零件。
最后,对烧结后的零件进行精加工和表面处理,以实现最终的产品要求。
MIM工艺具有许多独特的优点,使其在各个领域得到广泛应用。
首先,MIM工艺可以制造出具有复杂形状和高精度的金属零件,可替代传统加工如铸造、机械加工等。
其次,MIM工艺可以生产不锈钢、合金、硬质合金等多种金属材料的零件,具有高强度和耐磨损性。
此外,MIM工艺还具有节约原材料、降低成本和提高生产效率的优势。
MIM工艺在汽车、电子、医疗器械、航空航天等行业中得到广泛应用。
在汽车行业,MIM工艺可用于制造发动机配件、承载结构件等关键零部件,提高汽车的性能和可靠性。
在电子行业,MIM工艺可用于制造手机壳、键盘、连接器等微小精密零件,提升产品的外观和功能。
在医疗器械领域,MIM工艺可应用于制造植入式医疗器械如人工关节、牙科支架等,提供定制化解决方案。
在航空航天领域,MIM工艺可用于制造航空发动机内部零部件,提高发动机的性能和可靠性。
总之,MIM工艺通过结合金属粉末和高分子材料,实现了复杂形状和高精度金属零件的制造,并在汽车、电子、医疗器械、航空航天等领域得到广泛应用。
随着材料科学和制造工艺的不断进步,MIM工艺将会在更多领域发挥重要作用,并为各行各业提供更多创新的解决方案。
MIM(Metal Injection Molding)工艺是一种先进的金属加工技术,通过将金属粉末与热塑性或热固性高分子混合,并通过注射成型和烧结工艺制造出具有复杂形状和高精度的金属零件。
mim工艺技术难点

mim工艺技术难点MIM(Metal Injection Molding)是一种金属注射成型技术,结合了传统注射成型和粉末冶金加工的优点,可以高效地制造复杂形状、高精度的金属零件。
然而,MIM工艺也面临着一些技术难点。
首先,粉末冶金工艺要求原料粉末必须具备一定的流动性和可压缩性。
对于MIM工艺来说,需要将金属粉末与有机增塑剂混合,形成可塑性的混合料。
但是,金属粉末和增塑剂具有不同的粒径和密度,会造成混合不均匀的现象。
因此,如何获得均匀的混合料成为一个难点。
其次,MIM工艺要求将混合料注射成型,在高温和高压力的情况下,混合料需要流动性好、易于填充模具中的复杂空腔。
然而,增塑剂的挥发会产生气泡,造成金属零件的内部质量问题。
此外,由于注射成型的过程需要用到大量的压力,容易导致模具的磨损和疲劳破裂,增加了工艺的难度。
另外,MIM工艺中的烧结过程也是一个技术难点。
烧结是将注射成型后的零件加热至金属粉末颗粒结合的工艺过程。
然而,不同金属粉末在烧结过程中具有不同的热膨胀系数和热导率,容易导致零件变形和内部应力累积。
同时,烧结过程中的温度控制也是一个关键技术,过低的温度无法完全烧结,而过高的温度可能导致零件脱硬。
最后,MIM工艺还需要进行后处理,包括去除增塑剂和表面处理。
增塑剂的去除需要进行热处理或化学溶解,但是过高的温度和化学剂会对零件的质量产生负面影响。
而表面处理则需要提供一种能够提高金属零件表面质量和抗腐蚀性能的方法。
综上所述,MIM工艺存在一些技术难点,包括混合料的均匀性、注射成型的气泡问题、模具的磨损和疲劳破裂、烧结过程中的变形和应力累积,以及后处理的负面影响等。
解决这些难点需要在材料选择、工艺参数优化、设备改进和技术创新等方面下功夫,以提高MIM工艺的稳定性和可控性,进一步推动其在制造业的应用。
mim工艺硬度

mim工艺硬度1. 简介MIM工艺(Metal Injection Molding)是一种将金属粉末与塑料注射成型工艺相结合的先进制造技术。
它将金属粉末与有机粘结剂混合,经过注射成型、脱脂和烧结等工艺步骤,最终得到具有金属特性的零件。
MIM工艺广泛应用于各个领域,例如汽车、电子、医疗等,并且在硬度方面也具有很高的要求。
2. MIM工艺的硬度测试方法2.1 维氏硬度测试维氏硬度测试是常用的测试方法之一,通过在测试材料表面施加标准压力,然后测量压痕的大小来评估材料的硬度。
对于MIM工艺制造的零件,维氏硬度测试通常是在烧结后进行的。
2.2 洛氏硬度测试洛氏硬度测试是另一种常用的硬度测试方法,它通过在测试材料表面施加标准压力,然后测量压痕的深度来评估材料的硬度。
与维氏硬度测试不同的是,洛氏硬度测试使用的钻头是圆锥形的。
2.3 布氏硬度测试布氏硬度测试也是一种常用的硬度测试方法,它通过在测试材料表面施加标准压力,然后测量压痕的大小来评估材料的硬度。
与维氏硬度测试不同的是,布氏硬度测试使用的压头是球形的。
3. MIM工艺硬度的影响因素3.1 材料成分MIM工艺硬度受到材料成分的影响。
不同的金属粉末和有机粘结剂的配比会导致不同的硬度结果。
例如,添加更多的金属粉末可能会增加材料的硬度。
3.2 烧结温度烧结温度是MIM工艺中一个重要的参数,它会直接影响到材料的硬度。
较高的烧结温度可以提高材料的硬度,但如果温度过高,可能会导致材料变形或烧结不完全。
3.3 烧结时间烧结时间也是影响MIM工艺硬度的因素之一。
适当的烧结时间可以使材料充分烧结,从而提高硬度。
然而,过长的烧结时间可能会导致材料的晶粒长大,从而降低硬度。
3.4 烧结气氛烧结气氛对MIM工艺硬度有一定的影响。
适当的烧结气氛可以减少材料的氧化,从而提高硬度。
常用的烧结气氛包括氢气、氮气等。
4. MIM工艺硬度的优化方法4.1 材料优化通过调整金属粉末和有机粘结剂的配比,可以优化MIM工艺硬度。
mim工艺——精选推荐
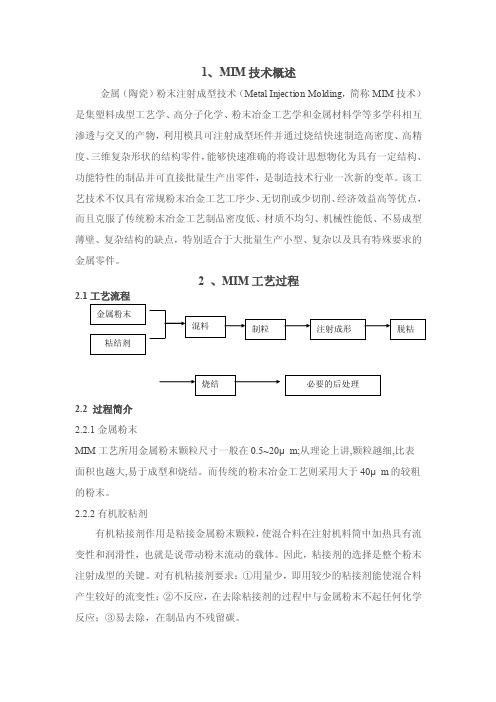
1、MIM 技术概述金属(陶瓷)粉末注射成型技术(Metal Injection Molding ,简称MIM 技术)是集塑料成型工艺学、高分子化学、粉末冶金工艺学和金属材料学等多学科相互渗透与交叉的产物,利用模具可注射成型坯件并通过烧结快速制造高密度、高精度、三维复杂形状的结构零件,能够快速准确的将设计思想物化为具有一定结构、功能特性的制品并可直接批量生产出零件,是制造技术行业一次新的变革。
该工艺技术不仅具有常规粉末冶金工艺工序少、无切削或少切削、经济效益高等优点,而且克服了传统粉末冶金工艺制品密度低、材质不均匀、机械性能低、不易成型薄壁、复杂结构的缺点,特别适合于大批量生产小型、复杂以及具有特殊要求的金属零件。
2 、MIM 工艺过程2.12.2 过程简介 2.2.1金属粉末MIM 工艺所用金属粉末颗粒尺寸一般在0.5~20μm;从理论上讲,颗粒越细,比表面积也越大,易于成型和烧结。
而传统的粉末冶金工艺则采用大于40μm 的较粗的粉末。
2.2.2有机胶粘剂有机粘接剂作用是粘接金属粉末颗粒,使混合料在注射机料筒中加热具有流变性和润滑性,也就是说带动粉末流动的载体。
因此,粘接剂的选择是整个粉末注射成型的关键。
对有机粘接剂要求:①用量少,即用较少的粘接剂能使混合料产生较好的流变性;②不反应,在去除粘接剂的过程中与金属粉末不起任何化学反应;③易去除,在制品内不残留碳。
2.2.3混练与制粒混练时把金属粉末与有机粘接剂均匀掺混在一起,将其流变性调整到适于注射成形状态的作用。
混合料的均匀程度直接影响其流动性,因而影响注射成型工艺参数乃至最终材料的密度及其它性能。
注射成形过程中产生的下角料、废品都可重新破碎、制粒,回收再用。
2.2.4注射成形本步工艺过程与塑料注射成型工艺过程在原理上是一致的,其设备条件也基本相同。
在注射成型过程中,混合料在注射机料筒内被加热成具有流变性的塑性物料,并在适当的注射压力下注入模具中,成型出毛坯。