2012 - 006 - 高速切削(刀具与机床)
高速切削刀具在数控加工中的应用
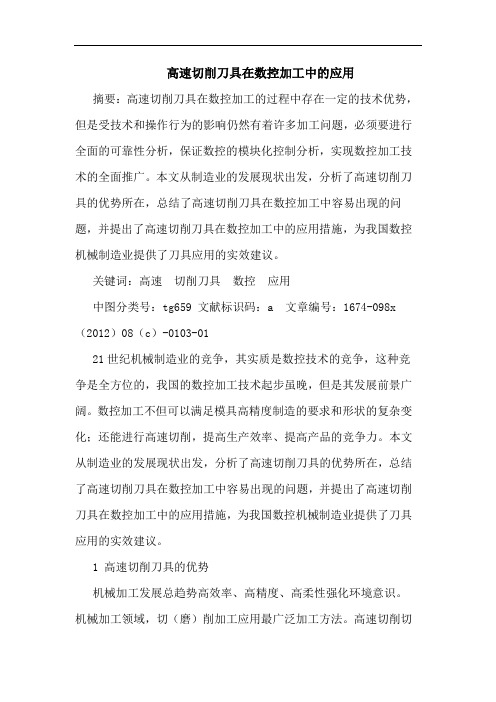
高速切削刀具在数控加工中的应用摘要:高速切削刀具在数控加工的过程中存在一定的技术优势,但是受技术和操作行为的影响仍然有着许多加工问题,必须要进行全面的可靠性分析,保证数控的模块化控制分析,实现数控加工技术的全面推广。
本文从制造业的发展现状出发,分析了高速切削刀具的优势所在,总结了高速切削刀具在数控加工中容易出现的问题,并提出了高速切削刀具在数控加工中的应用措施,为我国数控机械制造业提供了刀具应用的实效建议。
关键词:高速切削刀具数控应用中图分类号:tg659 文献标识码:a 文章编号:1674-098x (2012)08(c)-0103-0121世纪机械制造业的竞争,其实质是数控技术的竞争,这种竞争是全方位的,我国的数控加工技术起步虽晚,但是其发展前景广阔。
数控加工不但可以满足模具高精度制造的要求和形状的复杂变化;还能进行高速切削,提高生产效率、提高产品的竞争力。
本文从制造业的发展现状出发,分析了高速切削刀具的优势所在,总结了高速切削刀具在数控加工中容易出现的问题,并提出了高速切削刀具在数控加工中的应用措施,为我国数控机械制造业提供了刀具应用的实效建议。
1 高速切削刀具的优势机械加工发展总趋势高效率、高精度、高柔性强化环境意识。
机械加工领域,切(磨)削加工应用最广泛加工方法。
高速切削切削加工发展方向,已成为切削加工主流。
随着技术的发展,对工程材料提出了愈来愈高的要求,各种高强度、高硬度、耐腐蚀和耐高温的工程材料愈来愈多地被采用。
高速切削除了要求刀具材料具备普通刀具材料的一些基本性能之外,还突出要求刀具材料具备高的耐热性、抗热冲击性、良好的高温力学性能及高的可靠性。
而更为理想的刀具优势则要考虑到不同刀具的不同加工优势1。
例如:硬质合金刀具具有良好的抗拉强度和断裂韧性,但由于较低的硬度和较差的高温稳定性,使其在高速硬切削中的应用受到一定限制。
而如果进行了细晶粒和超细晶粒产品优化后,就可以使得其打磨加工的情况更为理想,获得更好地产品加工应用能力。
高速切削技术研究
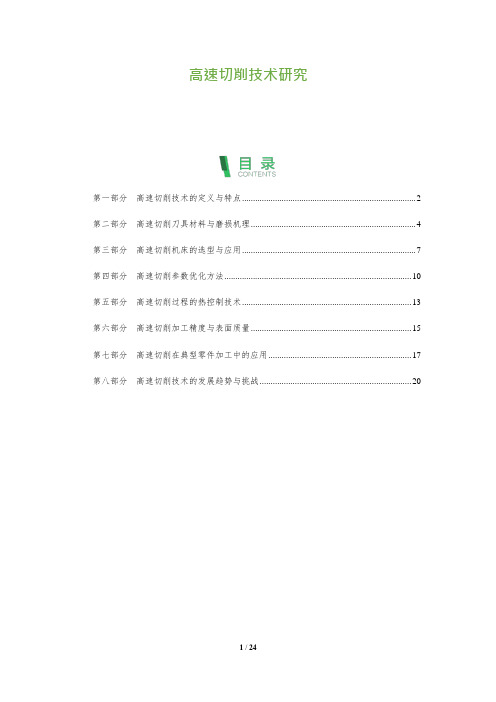
高速切削技术研究第一部分高速切削技术的定义与特点 (2)第二部分高速切削刀具材料与磨损机理 (4)第三部分高速切削机床的选型与应用 (7)第四部分高速切削参数优化方法 (10)第五部分高速切削过程的热控制技术 (13)第六部分高速切削加工精度与表面质量 (15)第七部分高速切削在典型零件加工中的应用 (17)第八部分高速切削技术的发展趋势与挑战 (20)第一部分高速切削技术的定义与特点高速切削技术是一种先进的制造工艺,它通过使用高转速的刀具和优化的切削参数来提高材料去除率、加工精度和表面质量。
该技术的核心在于实现高效率、高质量和高精度的加工过程。
在高速切削过程中,刀具以极高的速度旋转(通常超过每分钟数千转),同时进给速度也相应提高。
这种高速旋转产生的离心力有助于减小切削力和切削热,从而延长刀具寿命并减少工件的热变形。
此外,由于切削力的降低,高速切削还可以减少振动,进一步提高加工精度。
高速切削技术的优势主要体现在以下几个方面:1.高效率:与传统切削相比,高速切削可以显著提高材料去除率,缩短加工时间。
研究表明,高速切削可以提高生产效率达 30%至50%。
2.高精度:高速切削过程中的低切削力可以减少工件的振动,从而提高加工精度。
此外,由于切削热的影响较小,工件的热变形也得到了控制。
3.高质量表面:高速切削产生的切削热较低,这有助于减少工件的烧伤和裂纹,从而获得更好的表面质量。
4.刀具寿命延长:高速切削可以降低切削力,减少刀具磨损,从而延长刀具的使用寿命。
5.节能减排:高速切削技术可以实现更高的材料去除率,从而减少能源消耗和碳排放。
然而,高速切削技术也存在一些挑战,如刀具成本较高、对机床性能要求较高等。
因此,在实际应用中,需要根据具体加工需求和技术条件,合理选择切削参数和刀具,以确保高速切削技术的有效性和经济性。
总之,高速切削技术作为一种先进的制造工艺,具有高效率、高精度、高质量表面等优势,但在实际应用中需充分考虑其成本和设备要求。
高速切削加工技术
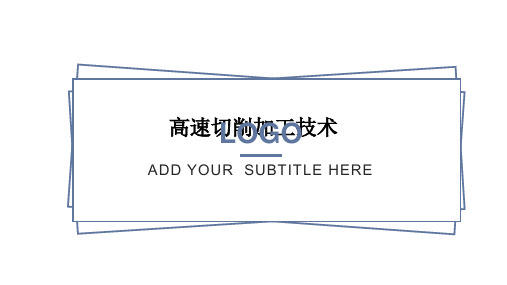
基本结构
进给机构 CNC控制 冷却系统
高速加工虽具有众多的优点,但由于技术复杂,且对于相关 技术要求较高,使其应用受到限制。
与高速加工密切相关的技术主要有:
○ 高速加工刀具与磨具制造技术; ○ 高速主轴单元制造技术; ○ 高速进给单元制造技术; ○ 高速加工在线检测与控制技术; ○ 其他:如高速加工毛坯制造技术,干切技术,高速加工的排屑技
术、安全防护技术等。
此外高速切削与磨削机理的研究,对于高速切削的发展也具 有重要意义。
高速切削 加工的关 键技术
高速主轴系统
高速主轴系统是高速切削技术最重要的关键技术之一。目前主 轴转速在15000-30000rpm的加工中心越来越普及,已经有转 速高达100000-150000rpm的加工中心。高速主轴由于转速 极高,主轴零件在离心力作用下产生振动和变形,高速运转摩 擦热和大功率内装电机产生的热会引起热变形和高温,所以必 须严格控制,为此对高速主轴提出如下性能要求:(1) 要求结 构紧凑、重量轻、惯性小、可避免振动和噪音和良好的起、停 性能;(2) 足够的刚性和高的回转精度;(3) 良好的热稳定性; (4) 大功率;(5) 先进的润滑和冷却系统;(6) 可靠的主轴监测 系统。
• 高速切削已成为当今制造业中一项快速发展的新技术,在工业发 达国家,高速切削正成为一种新的切削加工理念。
第 一 章 节 • 人们逐渐认识到高速切削是提高加工效率的关键技术。
高速切削的特点
随切削速度提高,单位时间内材料切除率增加,切削加工时间减 少,切削效率提高3~5倍。加工成本可降低20%-40%。
高速切削加工在国内的研究与应用
高速切削加工在国内的研究与 应用
20世纪90年代后,我们先后相继研究了模具高速切削加工技术与策 略、涂层刀具与PCBN刀具和陶瓷刀具等高速切削铸铁和钢的切削力、 刀具磨损寿命、加工表面粗糙度以及高速切削数据库技术等。
高速切削刀具在数控加工中的应用
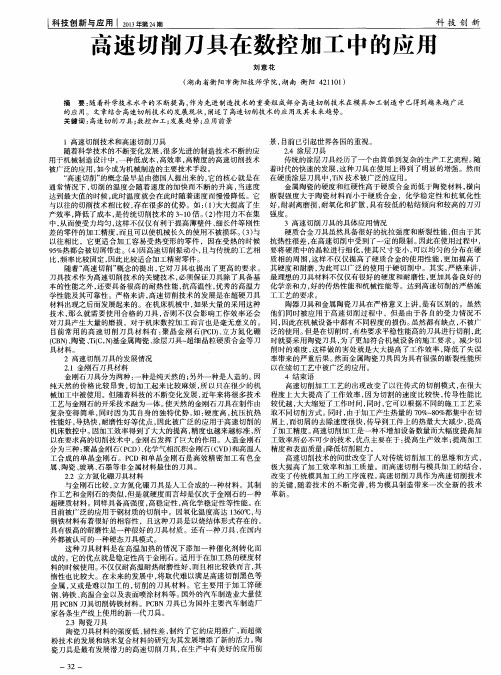
科 技 创 新
高速切 削刀具在数控加工中的应用
刘 ห้องสมุดไป่ตู้ 花
( 湖南省衡 阳市衡 阳技师 学院 , 湖南 衡 阳 4 2 1 1 0 1 )
摘 要: 随着科 学技 术 水平 的 不 断提 高 , 作 为先 进 制造 技 术 的 重要 组 成 部 分 高速 切 削技 术在 模 具加 工制 造 中 已得 到 越 来越 广 泛 的 应 用 。文章 结 合 高速 切 削技 术 的发 展 现状 , 阐述 了高速 切 削技 术 的应 用及 其 未 来趋 势 。 关键词: 高速 切 削a - g . - ; 数控 加 工 ; 发展 趋 势 ; 应 用 前景 景, 目前 已引 起世 界 各 国 的重 视 。 1高速 切削 技 术 和高 速 切削 刀具 随 着科 学技 术 的 不 断变 化 发展 , 很 多先 进 的制 造 技 术 不 断 的应 2 . 4涂 层 刀 具 用于机械制造设计 中, 一种低成本 , 高效率 , 高精度的高速切削技术 传统 的涂 层 刀 具经 历 了 一个 由简单 到 复 杂的 生 产工 艺 流程 。 随 被广 泛 的应 用 , 如 今 成为 机 械制 造 的 主要 技术 手 段 。 着时代的快速的发展 , 这种 刀具在使用上得到了明显 的增强。然而 “ 高 速 切 削” 的概 念最 早 是 由德 国人 提 出来 的 , 它 的核 心 就 是在 在 硬 质涂 层 刀 具 中 , T i N技 术 被广 泛 的应 用 。 金属 陶瓷 的硬 度 和红 硬 性 高于 硬 质 合金 而低 于 陶瓷 材 料 , 横向 通 常情 况 下 , 切 削 的温 度 会 随 着 速 度 的加 快 而 不 断 的升 高 , 当速 度 达到最大值 的时候 , 此时温度就会在此时随着速度而慢慢 降低 。它 断裂 强 度 大 于 陶 瓷 材料 而小 于硬 质 合 金 ,化 学 稳 定 性 和 抗 氧 化 性 与 以往 的切 削技 术相 比较 , 存 在很 多 的优 势 。如 : ( 1 ) 大大 提 高 了生 好 , 耐剥离磨损 , 耐氧化和扩散 , 具有较低 的粘结倾 向和较高的刀刃 产效 率 , 降 低 了成 本 , 是传 统 切 削技 术 的 3 ~ 1 0 倍。 ( 2 ) 作 用力 不 在集 强 度 。 3高 速 切 削刀 具 的具 体 应用 情 况 中, 从 而使 受 力均 匀 , 这样 不 仅 仅 有 利 于提 高 薄 壁件 、 细 长件 等 刚 性 差 的零 件 的 加工 精 度 , 而且 可 以使 机 械 长久 的 使用 不 被损 坏 。 ( 3 ) 与 硬 质合 金 刀具 虽 然具 备 很 好 的抗 拉 强 度 和断 裂 性 能 , 但 由 于其 以往相比 ,它更适合加工容易受热变形 的零件 ,因在受热的时候 抗热性很差, 在高速切削 中受到 了一定的限制 。 因此在使用过程 中, 9 5 %热都会被切 屑带走。( 4 ) 因高速切削振动小 , 且与传统的工艺相 要将硬质 中的晶粒进行细化 , 使其尺寸变小 , 可以均匀 的分布 在硬 质相的周围 , 这 样 不仅 仅 提 高 了硬 质合 金 的使 用 性 能 , 更 加 提 高 了 比, 频率 比较 固定 , 因此 比较适合加工精密零件 。 随着 “ 高 速切 削 ” 概 念 的提 出 , 它 对 刀具 也 提 出 了更 高 的要 求 。 其硬度和耐磨 , 为此可以广泛的使用于硬切削中。其实 , 严格来讲 , 更 加具 备 良好 的 刀具技术作为高速切削技术的关键技术 , 必须保证刀具除了具备基 最 理想 的刀具 材 料 不仅 仅有 很 好 的 硬度 和 耐 磨性 , 本 的性 能 之 外 , 还要 具 备很 高 的耐 热性 能 , 抗 高 温性 , 优 秀 的 高温 力 化学亲和力 , 好 的传热性能和机械性能等。达到高速切 削的严格施 学 性 能及 其 可靠 性 。严 格 来讲 , 高 速切 削 技 术 的发 展 是 在 超硬 刀 具 工 工艺 的要求 。 陶器刀具和金属陶瓷刀具在严格意义上讲 , 是有区别 的。虽然 材料出现之后而发展起来 的。在机床机械中, 如果大量的采用这种 技术 , 那 么 就需 要 使 用 合 格 的 刀具 , 否 则 不仅 会 影 响工 作 效 率 还 会 他们同时被应用 于高速切削过程中 ,但是 由于各 自的受力情况不 对 刀 具产 生 大 量 的磨 损 ,对 于 机床 数 控 加 工 而言 也 是 毫无 意 义 的 。 同, 因此在 机 械设 备 中都有 不 同程 度 的损 伤 。 虽然 都 有 缺点 , 不 被 广 目前 常用 的高速切 削刀具材料有 : 聚晶金刚石( P C D ) 、 立方氮化 硼 泛的使用 。 但是在切削时, 有些要求平稳性能高的刀具进行切削 , 此 ( C B N ) 、 陶瓷、 T i ( C, N ) 基 金属 陶瓷 、 涂层 刀 具 一 超 细 晶粒 硬 质 合 金 等 刀 时就要 采 用 陶 瓷刀 具 , 为 了更 加 符 合机 械 设 备 的施 工 要 求 。减 少 切 具材 料 。 削 时 的难 度 , 这 样 做 的害 处 就是 大 大 提 高 了工作 效率 , 降 低 了失 误 2 高速 切 削 刀具 的 发展 情 况 率 带 来 的严 重 后果 。 然 而金 属 陶瓷 刀 具 因为 具有 很 强 的断 裂性 能 所 2 . 1金 刚石 刀 具材 料 以在续 切 工 艺 中被 广泛 的应用 。 金 刚石 刀 具 分为 两种 : 一 种 是 纯天 然 的 ; 另 外一 种是 人 造 的 。 因 4 结 束语 纯 天 然 的价 格 比较 昂贵 , 切 加 工 起来 比较 麻 烦 , 所 以 只 在很 少 的 机 高速切削加工工艺的出现改变 了以往传式的切削模式 , 在很大 械加 工 中被使 用 。但 随 着科 技 的不 断变 化 发 展 , 近 年来 将 很 多 技术 程度上大大提高了工作效率 , 因为切割 的速度 比较快 , 传导性能 比 工艺与金刚石 的开采技术融为一体 。 使天然的金刚石刀具在制作由 较 优 越 , 大 大缩 短 了工 作 时 间 , 同时, 它可 以根 据不 同 的施 工 工艺 采 复杂变得 简单 , 同时因为其 自身 的独特优 势 , 如: 硬度高 , 抗 压抗 热 取不 同切 削方 式 。同时 , 由于加 工 产生 热 量 的 7 0 %~ 8 O %都 集 中在切 而切屑的去除速度很快 , 传导到工件上的热量大大减少 , 提高 性能好 , 导热快 , 耐磨性好等优点 , 因此被广泛的应用于高速切削的 屑上 , 机床数控 中。 因加工效率得到了大大的提高 , 精度也越来越标准 , 所 了加工精度 。 高速切削加工是一种不增加设备数量而大幅度提高加 优 点 主要 在 于 : 提 高生 产 效 率 ; 提 高 加 工 以在要 求 高 的切 削 技术 中 , 金 刚 石 发挥 了 巨大 的作 用 。人造 金 刚 石 工效 率 所必 不 可 少 的技 术 , 分 为 三种 : 聚 晶金 刚石 ( P C O) 、 化 学气 相 沉 积金 刚 石 ( C V O ) 和 高温 人 精 度 和 表 面质 量 ; 降低 切 削 阻力 。 工合成的单晶金 刚石 。P C D和单 晶金 刚石是高效精密加工有色金 高速切削技术 的问世改变了人对传统切削加工的思维 和方式 , 极 大提 高 了加 工 效率 和 加工 质 量 。而高 速 切 削 与模 具 加 工 的结 合 , 属、 陶瓷 、 玻璃 、 石 墨 等 非金 属 材料 最 佳 的刀 具 。 2 . 2立 方 氮化 硼 刀 具材 料 改 变 了传 统模 具 加 工 的工 序流 程 。 高 速 切 削刀 具作 为 高 速切 削 技术 与金 刚石 比较 , 立 方氮 化 硼 刀 具是 人 工 合 成 的一 种 材 料 。其 制 的 关 键 , 随 着 技 术 的 不断 完 善 , 将 为 模 具 制 造 带 来 一 次 全 新 的 技 术 作工艺和金刚石的类似 , 但是就硬度而言却是仅 次于金刚石的一种 革 新 。 超 硬 质材 料 。同样 具备 高 强度 , 高 稳 定性 , 高化 学稳 定 性 等性 能 。 在 目前 被广 泛 的 应用 于 钢材 质 的 切削 中。 因氧 化 温 度 高达 1 3 6 0  ̄, 与 钢铁 材料 有 着 很好 的相 容性 ,且这 种 刀 具是 以烧 结 体 形式 存 在 的 , 具有极高的耐磨性是一种很好的刀具材质。还有一种刀具 , 在 国内 外都被认可的一种硬态刀具模式 。 这种刀具材料是在高温加热的情况下添加一种催化剂转化而 成的。 它 的优点就是稳定性高于金刚石 。 适用于在加工热的硬度材 料的时候使用 。 不仅仅耐高温耐热耐磨性好, 而且相 比较铁而言, 其 惰性也 比较大 。在未来的发展 中, 将取代难 以满足高速切削黑色等 金属 , 又或 是 难 以加 工 的 , 切 削 的 刀具 材 料 。它 主 要 用 于 加 工 淬 硬
高速切削报告-国内外现状

2、超高速切削加工优势
极大地提高了机床的生产率
随着切削速度的大幅度提高,进给速度也相应提 高5-10倍。这样,单位时间内的材料切除率可大大增 加,可达到常规切削的3-6倍,甚至更高; 同时机床快速空程速度的大幅度提高,也大大减 少了非切削的空行程时间,从而极大地提高了机床的 生产率。
降低切削力
大多数情况下,垂直力比水平力大,这和理论分析的 结果相反;
峰值切削力只增加了33%-70%,而不是预计的500 %,而且使用的平均力还会减小; 在高速切削下,剪切角增大而导致剪切力减小。
超高速切削加工 与传统的切削加工相比发生了质变
1.3 高速切削逐渐成熟
在20世纪70年代中期,美国科学家罗伯特·金 (Robert I.king)和麦克唐纳(Mcdonaid.J)着手 验证和发展沃汉(Vaughan)的研究结论。
存在的问题
1)刚度低、惯量大,难以获得高进给速度和高加速度 (速度很难超过60m/min、加速度很难超过1.5 g)。
2)非线性严重,不易实现闭环控制。
3)传动误差较大,影响机械加工精度。
4)机械传动链结构复杂,特别是在重型机和多坐标机 床中这个问题尤为突出。
5)机械噪声大。
6)传动效率低,一般0.6。
主要结论:
1)高速切削方面
在超高速条件下,高强度材料可以切削,切削速度可高 达1220m/s;
高速钢刀具可在这一速度下切削高强度材料;
加工合金材料的脆性失效现象在高速下并没有发生; 高速下的实验结果和通常的加工曲线计算的结果不一样; 超高速切削可提高工件的表面质量; 高速切削的金属加工切除率可高达普通切削的240倍。
高速切削加工技术论文(2)
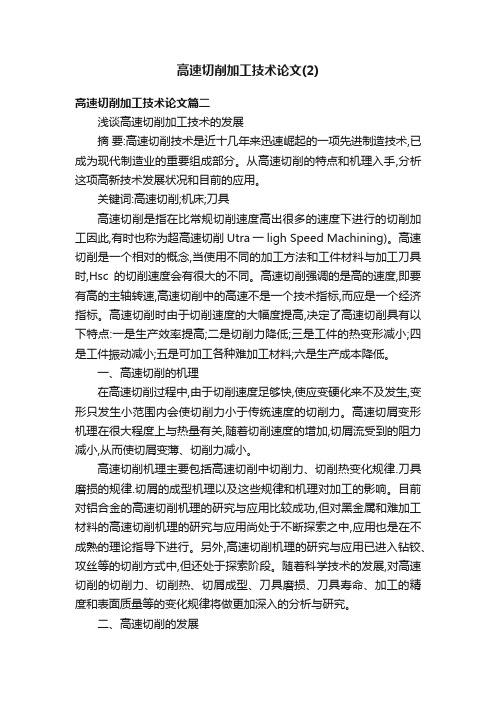
高速切削加工技术论文(2)高速切削加工技术论文篇二浅谈高速切削加工技术的发展摘要:高速切削技术是近十几年来迅速崛起的一项先进制造技术,已成为现代制造业的重要组成部分。
从高速切削的特点和机理入手,分析这项高新技术发展状况和目前的应用。
关键词:高速切削;机床;刀具高速切削是指在比常规切削速度高出很多的速度下进行的切削加工因此,有时也称为超高速切削Utra一ligh Speed Machining)。
高速切削是一个相对的概念,当使用不同的加工方法和工件材料与加工刀具时,Hsc的切削速度会有很大的不同。
高速切削强调的是高的速度,即要有高的主轴转速,高速切削中的高速不是一个技术指标,而应是一个经济指标。
高速切削时由于切削速度的大幅度提高,决定了高速切削具有以下特点:一是生产效率提高;二是切削力降低;三是工件的热变形减小;四是工件振动减小;五是可加工各种难加工材料;六是生产成本降低。
一、高速切削的机理在高速切削过程中,由于切削速度足够快,使应变硬化来不及发生,变形只发生小范围内会使切削力小于传统速度的切削力。
高速切屑变形机理在很大程度上与热量有关,随着切削速度的增加,切屑流受到的阻力减小,从而使切屑变薄、切削力减小。
高速切削机理主要包括高速切削中切削力、切削热变化规律.刀具磨损的规律.切屑的成型机理以及这些规律和机理对加工的影响。
目前对铝合金的高速切削机理的研究与应用比较成功,但对黑金属和难加工材料的高速切削机理的研究与应用尚处于不断探索之中,应用也是在不成熟的理论指导下进行。
另外,高速切削机理的研究与应用已进入钻铰、攻丝等的切削方式中,但还处于探索阶段。
随着科学技术的发展,对高速切削的切削力、切削热、切屑成型、刀具磨损、刀具寿命、加工的精度和表面质量等的变化规律将做更加深入的分析与研究。
二、高速切削的发展高速切削缘起自航空铝合金零件的加工。
在该领域,高速加工主要用于铣削高强度铝合金整体构件、薄壁类零件,切除其90%,的材料。
高速切削及其关键技术
高速切削及其关键技术摘要自20世纪30年代德国 Carl Salomon博士首次提出高速切削概念以来,经过50年代的机理与可行性研究,70年代的工艺技术研究,80年代全面系统的高速切削技术研究,到90年代初,高速切削技术开始进入实用化,到90年代后期,商品化高速切削机床大量涌现,21世纪初,高速切削技术在工业发达国家得到普遍应用,正成为切削加工的主流技术。
根据1992年国际生产工程研究会(CIRP)年会主题报告的定义,高速切削通常指切削速度超过传统切削速度5-10倍的切削加工。
因此,根据加工材料的不同和加工方式的不同,高速切削的切削速度范围也不同.高速切削包括高速铣削、高速车削、高速钻孔与高速车铣等,但绝大部分应用是高速铣削.目前,加工铝合金已达到2000-7500m/min;钛合金达150-1000m/min;纤维增强塑料为2000-9000m/min。
高速切削是一项系统技术,企业必须根据产品的材料和结构特点,购置合适的高速切削机床,选择合适的切削刀具,采用最佳的切削工艺,以达到理想的高速加工效果。
高速切削是一项先进的、正在发展的综合技术,必须将高性能的高速切削机床、与工件材料相适应的刀具和对于具体加工对象最佳的加工工艺技术相结合,充分发挥高速切削技术的优势。
高速切削技术已成为切削加工的主流和先进制造技术的一个重要发展方向。
高速切削较之常规切削是一种创新的加工工艺和加工理念。
本文分析了高速切削技术的特点,研究了高速切削的关键技术:机床技术、刀具技术和工艺技术,介绍了高速切削技术在航空航天和汽车制造等领域的发展及应用.关键词:高速切削 ;机床;刀具 ;切削工艺一.引言机械加工技术正朝着高效率、高精度、高柔性和绿色制造的方向发展。
在机械加工技术中,切削加工是应用最广泛的加工方法。
近年来,高速切削技术蓬勃发展,已成为切削加工的主流和先进制造技术的一个重要发展方向。
在数控机床出现以前,用于工件上下料、测量、换刀和调整机床等的辅助时间超过工件加工总工时的70%;以数控机床为基础的柔性制造技术的发展和应用,大大降低了工件加工的辅助时间,切削所占时间比例越来越大。
先进制造工艺--高速切削技术
第三讲1.高速切削技术高速切削的产生背景和发展史高速切削(HSM或HSC)通常指高主轴转速和高进给速度下的立铣,它是20世纪90年代迅速走向实际应用的先进加工技术,在航空航天制造业、模具加工业、汽车零件加工、以及精密零件加工等得到广泛的应用。
高速铣削技术既可用于铝合金、铜等易切削金属,也可用于淬火钢、钛合金、高温合金等难加工材料,以及碳纤维塑料等非金属材料。
例如,在铝合金等飞机零件加工中,曲面多且结构复杂,材料去除量达高达90%~95%,采用高速铣削可大大提高生产效率和加工精度;在模具加工中,高速铣削可加工淬火硬度大于HRC50的钢件,因此许多情况下可省去电火花加工和手工修磨,在热处理后采用高速铣削达到零件尺寸、形状和表面粗糙度要求。
高速切削概念始于1931年德国所罗门博士的研究成果:“当以适当高的切削速度(约为常规速度的5~10倍)加工时,切削刃上的温度会降低,因此有可能通过高速切削提高加工生产率”。
60多年来,人们一直在探索有效、适用、可靠的高速切削技术,但直到20世纪90年代该技术才逐渐在工业实际中推广应用。
高速切削最早在飞机制造业和模具制造l受到很大的重视。
为使飞机的零部件满足很高的可靠性要求,大部分重要零件都是在整块铝合金坯件卜铣削而成,既可减少焊缝,又可提高零件的强度和抗振性。
但常规铣削效率很低,从而导致了高的生产成本和长的交货时间。
高速切削是克服这方面问题的最好解决方案。
汽车工业中,模具制造是产品更新换代的关键。
新车型定型后,模具制造周期的长短直接影响到产品的上市时间,也关系到市场竞争的成败。
所以在80年代美国、欧洲和日本的政府都出巨资推动高速切削在模具制造中的应用研究,90年代初高速切削已进入工业化应用。
图16 高速切削在生产应用中的发展历程图17 采用高速切削后产品质量提高的历程a一硬质合金切钢 b一硬质合金切铸铁c—CBN切铸铁图16是德国宝马公司(BMW)采用高速切削的历程。
高速切削刀具在数控加工应用论文
高速切削刀具在数控加工中的应用[摘要]:随着科学技术水平的不断提高,作为先进制造技术的重要组成部分高速切削技术在模具加工制造中已得到越来越广泛的应用。
本文结合高速切削技术的发展现状,阐述了高速切削技术的应用及其未来趋势。
[关键词]:高速切削刀具数控加工应用中图分类号:tg659文献标识码:tg文章编号:1009-914x(2013)01- 0239-01一、高速切削技术和高速切削刀具目前,切削加工仍是机械制造行业应用广泛的一种加工方法。
其中,集高效、高精度和低成本于一身的高速切削加工技术已经成为机械制造领域的新秀和主要加工手段。
“高速切削”的概念首先是由德国的c.s~omom博士提出的,并于1931年4月发表了著名的切削速度与切削温度的理论。
该理论的核心是:在常规的切削速度范围内,切削温度随着切削速度的增大而提高,当到达某一速度极限后,切削温度随着切削速度的提高反而降低。
此后,高速切削技术的发展经历了以下4个阶段:高速切削的设想与理论探索阶段(193l—l971年),高速切削的应用探索阶段(1972-1978年),高速切削实用阶段(1979--1984年),高速切削成熟阶段(20世纪90年代至今)。
高速切削加工与常规的切削加工相比具有以下优点:第一,生产效率提高3~1o倍。
第二,切削力降低30%以上,尤其是径向切削分力大幅度减少,特别有利于提高薄壁件、细长件等刚性差的零件的加工精度。
第三,切削热95%被切屑带走,特别适合加工容易热变形的零件。
第四,高速切削时,机床的激振频率远离工艺系统的固有频率,工作平稳,振动较小,适合加工精密零件。
高速切削刀具是实现高速加工技术的关键。
刀具技术是实现高速切削加工的关键技术之一,不合适的刀具会使复杂、昂贵的机床或加工系统形同虚设,完全不起作用。
由于高速切削的切削速度快,而高速加工线速度主要受刀具限制,因为在目前机床所能达到的高速范围内,速度越高,刀具的磨损越快。
高速切削加工与刀具技术
刀具 的安全性等刀具技术 。 关键词 :高速切 削 刀具材料 刀柄 刀具的安全性
中 圈分 类 号 ;T 5 6 1 文 献 标 识 码 :A 文 章编 号 ; 17 -4 0 (0 7 4 3— 4 G0。 6 2 8 1 2 0 )0 - 3 0
1概 述
早在 2 世 纪 3 年 代 , 国切 削物 理学家 Cr O O 德 al S lmn根据 实验提 出 了高速切 削的概念 , a oo 他指 出 切 削速 度 与工件 的材料 有 关 ,每 一种 材料 都存在
高 刀具 硬度 和表 面光 洁度 ,刀 具制造 采 用涂 层技
术 。用 于高速 切 削 的涂层材 料 刀具可 按 加: 不 同 [
素的 产生 ,影 响加工 ,应如 何合 理选 定切 削参 数 及 与切 速 的运 转 下 刀 具 的 安全 保 障 3对
规高 5 l 倍以上的切削称为高速切削。 至 O
问题。
高速切削加工由于切削机理不同,因此具有 2 高速切削的刀具技术
维普资讯
机械 设计制造
《 电技术》2 0 机 07年第 4期
高速 切 削加 工 与刀 具技 术
林 明 山
( 州 职 业技 术学 院 机 械 与 自动化 工 程 系 ,福 建 漳 州 3 3 0 ) 漳 60 0
摘
要 :根据高速切削的特 点,高速切削的加工对刀具 的要求,介绍刀具材料 的选用、刀柄 的改进、刀具 的结构及
金 TC ( )等 。涂层硬 质合 金在 高速 加工 中应用 I N 最 为广泛 ,对 耐热 合金 、钛合 金 、高温 合金 、铸
好加工状态 ,从而保证了工件的加工精度 。⑤加
铁、纯钢 、铝合金及复合材料的高速切削加工耐
- 1、下载文档前请自行甄别文档内容的完整性,平台不提供额外的编辑、内容补充、找答案等附加服务。
- 2、"仅部分预览"的文档,不可在线预览部分如存在完整性等问题,可反馈申请退款(可完整预览的文档不适用该条件!)。
- 3、如文档侵犯您的权益,请联系客服反馈,我们会尽快为您处理(人工客服工作时间:9:00-18:30)。
20
D
高速切削加工刀具 – 刀具材料应具备的基本性能
(1)硬度和耐磨性。必须高于工件材料的硬度,一般在HRC60以上;
硬度越高,耐磨性越好。
(2)强度和韧性。要承受切削力、冲击和振动,防止刀具脆性断裂 和崩刃。 (3)耐热性。能承受高温,具备抗氧化能力。 (4)工艺性能和经济性。具备良好的锻造、热处理、焊接和磨削加
减小进给量 改变刀具主偏角以增加稳定性 选择韧性好的刀具材料
(4)剥落和裂纹 高速切削时温度很高,易产生平行于切削刃方向的热应力,而刀具离 开被加工件时热应力释放,刀具不断切入、切出,造成热应力疲劳。接触 疲劳与热应力疲劳都会引起裂纹,使刀具前、后刀面发生剥落。 (5)破损 刀具材料或切削用量选择不当,刀具经受不住强大应力(切削载荷或 热应力)作用,就可能突然破损
图 高速切削刀 具材料性能
D
高速切削加工刀具 – 刀具材料
金刚石:以PCD为主 立方氮化硼(PCBN) 陶瓷刀具:Al2O3基和Si3N4基两大类 TiC (N) 基硬质合金(金属陶瓷)
涂层刀具:刀体+涂层材料,CVD和PVD两种方法实现
D
高速切削加工刀具 – 刀具材料 表 普通刀具材料与超硬刀具材料性能与用途对比
b)涂层整体硬质合金刀具 (Vc=1200m/min,ap=5mm,ae=12mm) 图 机械疲劳裂纹及热裂纹(高速铣削7050铝合金)
D
高速切削加工刀具 – 磨损和破损
a)涂层整体硬质合金刀具 (Vc=1000m/min,ap=4mm,ae=10mm)
D
高速切削加工刀具 – 磨损和破损
b)可转位超细晶粒硬质合金刀具 (Vc=1200m/min,ap=3mm,ae=12mm) 图10 微崩刃(高速铣削7050铝合金)
D
高速切削加工刀具 – 磨损和破损
刀具损坏包括磨损和破损
连续切削刀具以磨损为主伴随微崩刃。 断续切削刀具是磨损伴随破损,有的以破损为主。
D
高速切削加工刀具 – 磨损和破损
a)YM30超细硬质合金刀具 (Vc=1200m/min,ap=3mm,ae=12mm)
D
高速切削加工刀具 – 磨损和破损
切削速度的提高而减小。这一特性使切削变形和切削力减小,加工表面
质量提高。
31
D
高速切削加工刀具 –PCB刀具应用实例
加工对象
硬度
加工方式
车削 镗孔 端铣 磨削 磨削 端铣 立铣
工艺参数
V=180m/mim f = 5.6mm/r V=50m/mim
加工效果
GCr15 HRC71 钢轧辊 YG15 HRA87 冷挤压模 A3热压板 凸轮轴 HRC60
28
D
高速切削加工刀具 – 聚晶金刚石 表 聚晶金刚石应用实例
加工对象 铝合金 共晶硅 铝合金 共晶硅
硬度
加工方式 端铣 车削
工艺参数
加工效果
HRC71
HRC71
铣削 车削 铣削 铣削
玻璃纤维 HRA87 强化塑料 热塑性醋 酸盐 高Si-Al 铸造件 铝合金
v=4000m/mim Ra0.8-0.4μm v=600m/mim 一次刃磨切削行程800km f = 0.1mm/r Ra0.8μm,刀具寿命为 硬质合金的50倍 v=2900m/mim 刀具寿命为硬质合金的80倍 vf=0.018mm/齿 Ra0.8μm v=500m/mim 刀具寿命为硬质合金的 150倍,Ra0.8-0.4μm v = 4500m/s 比硬质合金寿命提高380倍 vf=10mm/min Ra=0.8μm v=2200m/mim Ra=0.8μm
高速切削技术 第七讲
A B C D E
定义
理论基础
表面质量
刀具
机床
P2
D
高速切削加工刀具
P3
高速切削刀具特点
特点:“三高一专 ”,即高效率、高精度、高可靠性和专用化
以高强度铝合金做基体的HSC端面铣刀
带内部冷却的钻头
在基体上焊接刀片(材料 CBN,PCD)的HSC刀具
刀具损坏形态
(1)前刀面磨损 高速切削刀具的磨损区域与切削刃直接相连, 最大磨损部位位于切
热-力学磨损:磨粒和粘结磨损 热-化学磨损:扩散、溶解、氧化等 刀具磨损是多种磨损机理综合的结果。
图 涂层刀具高速切削 时不同切削温度下的磨 损机理作用简图
D
高速切削加工刀具 – 磨损和破损
(1) 刀具的磨损 粘结磨损:刀具与工件材料接触到原子间距离时所产生的结合现象。 在摩擦面的实际接触面积上,高压高温作用产生塑性变形,导致“冷焊”。 扩散磨损:两个化学上有一定亲和力的固体(碳和铁等)放在一起,在较高 温度时,碳原子会向铁中扩散。 溶解磨损:和扩散磨损相似,都是化学磨损,基于化学热力学的溶解理论。 氧化磨损:高速切削高温下,刀具材料中的一些元素与周围某些介质(空气 中的氧,切削液中的硫、氯)起化学反应,生成不同的氧化膜和粘附膜,有的 起保护作用,有的形成较软的化合物,使得刀具材料中的硬质相颗粒被粘走。 (2)刀具的破损:受冲击、机械疲劳和热疲劳等原因引起崩刃、剥落、裂纹 和脆断。
D
高速切削加工刀具 – 磨损和破损
刀具的磨损 前后刀面磨损形貌
图11 超细晶粒硬质合 金刀具铣削45#调质钢 (HRC35~40)前、后 刀面磨损V=300m/min
D
高速切削加工刀具 – 磨损和破损
图12
SG4陶瓷刀具铣削淬硬45#钢(HRC45~50)
前பைடு நூலகம்后刀面磨损,V=400m/min
图 JX-1陶瓷刀具加工 GH169边界磨损 V= 62.5m/min
图 JX-1陶瓷刀具加工 GH169前后刀面磨损V= 230m/min
D
高速切削加工刀具 – 磨损和破损
粘结
a)干切削时刀具前刀面的粘结
D
高速切削加工刀具 – 磨损和破损
粘结
b) 使用切削液时前刀面的粘结
图15 可转位刀片高速铣削7050铝合金时的粘结磨损(V=1200m/min)
D
高速切削加工刀具 – 磨损机理
HRA90 HRA93 HV10000 HV7500 0.3GPa 146.5 惰性小 2.8GPa 100-120 惰性小
抗弯强度 2.4GPa 导热系数 40-50
热稳定性 350℃
化学惰性 耐磨性 加工质量 低速加 加工对象 工一般 钢材、 铸铁
620 ℃
1000 ℃ 1400 ℃ 800 ℃ 600-800 ℃
32
D
高速切削加工刀具 –材料性能
硬度大小:PCD > PCBN>Al2O3基>Si3N4基>TiC(N)基硬质合金>WC基
超细晶粒硬质合金>高速钢HSS。
抗弯强度大小:HSS>WC基>TiC(N)基>Si3N4基>Al2O3基>PCD>PCBN。 断裂韧性大小:HSS>WC基>TiC(N)基>PCBN>PCD>Si3N4基>Al2O3基。 耐磨性:PCD>PCBN>Al2O3基>Si3N4基>TiC(N)基>WC基>HSS。
刀具材料种类
材料性能 硬度
合金 高速钢 硬质合金 陶瓷 工具钢 W18Cr4V YG6 Si3N4 HRC65 HRC66 3.2GPa 20-30 1.45GPa 0.8GPa 70-100 低 低 低 30-40 惰性大
天然 聚晶金刚石 金刚石 PCD
聚晶立方氮 化硼 PCBN HV4000 1.5GPa 40-100
磨材料时,其耐磨性为硬质合
金刀具的 50 倍,涂层硬质合金 刀具的 30 倍,陶瓷刀具的 25 倍。
硬度/HV
◆ PCBN切削性能
图
PCBN刀具高温硬度
高的热稳定性:热稳定性明显优于金刚石刀具
30
D
高速切削加工刀具 –立方氮化硼 1970年问世 良好的化学稳定性 1200-1300℃与铁系材料不发生化学反应;2000 ℃才与碳发生化学反
GCr15 HRC62 轴承内孔 Cr、Cu 铸铁 40Cr钢 HRC38
以车代磨,工效提高4-5倍 Ra0.8-0.4μm 工效较电火花加工提高30 倍,Ra0.8-0.4μm V = 800m/mim 以铣代磨,工效提高6-7倍 Vf = 100m/mim Ra1.6-0.8μm,平面度0.02 V= 80m/s 比单晶刚玉砂轮寿命提高 20倍,生产效率提高50% V= 65m/s 比棕刚玉砂轮耐用度提高 170倍,生产效率提高一倍 V = 800m/mim Ra0.8μm,平面度0.02 Vf = 0.1mm/齿 V = 850m/mim 以铣代磨,工效提高5-6倍 Ra0.8μm
钻削
v=360m/mim
以钻代镗, Ra=0.8μm
29
D
高速切削加工刀具 –立方氮化硼 1970年问世
5000 4000 3000 BN20 2000 1000 0 0 硬质合金 200 400 600 800 1000 温度/℃ 陶瓷 BN100
较高的硬度和耐磨性:
CBN 晶体结构与金刚石相似, 化学键类型相同,晶格常数相 近 。 CBN 粉 末 硬 度 HV8000 , PCBN硬度3000-5000。切削耐
工性能,性价比高。
21
D
高速切削加工刀具 – 刀具材料应具备的基本性能
(1)可靠性。节约换刀时间,保证安全。 (2)高的耐热性和抗热冲击性能。要求熔点高、氧化温度高等。 (3)良好的高温力学性能。高温强度、高温硬度和高温韧性。
(4)适应加工难加工材料和新型材料。难加工材料占40%。
22