如何分析拉伸曲线
拉伸试验曲线的分析及控制

拉伸试验曲线的分析及控制拉伸试验是钢铁材料物理性能评价的重要手段之一。
本实验室在实际生产中使用较先进的ZWICK电子拉伸试验机。
但在实际生产中还是会出现由于试样夹持,试样打滑,参数设置等引起的试验机自动采集数据错误。
为了便于操作人员及时对异常情况做出判断和处理,确保拉伸试验数据的准确性。
本文针对以上问题,进行了研究和整理。
标签:拉伸曲线;试样夹持;试样打滑;参数设置;曲线异常1.引言近年来随着科技的发展进步,电子拉伸试验机已经得到认可。
ZWICK拉伸试验机实现了试验数据和试验曲线的同步性,它是通过不同传感器或测量装置,采集力值信号、应变信号、位移信号和时间。
利用软件对这些信息进行处理,绘制出力值和位移或力值和应变曲线,通过公式计算得出需要的力学性能指标。
并且在曲线上直观的表现出来[1]。
但是电子拉伸试验机也存在着弊端。
在试验过程中难免会出现异常状况,试验机无法自行进行判断。
因此在出现数据异常时,操作者必须清楚应该如何处理,才能确保数据的真确性。
2.试验机精度经过辽宁省计量院的鉴定,本实验室使用的ZWICK拉伸试验机符合《GB/T228》[2]的要求。
按照试验机鉴定计量要求,为了保证在2次试验机鉴定期间,试验机性能的稳定行,实验室自身建立了良好有序的期间核查程序,完成对拉伸试验机整体的运行及精度的控制。
从而排除试验机精度对试验结果的影响。
3.对拉伸试验出现的异常曲线分析及控制当出现拉伸试验结果异常时,首先要确认试验曲线,通过试验曲线判断出现异常结果的原因,从而判断出试验机出现了什么问题。
这样可以很快的对故障点予以修复。
以下对几种拉伸曲线异常情况进行分析。
3.1试样夹持不当造成拉伸曲线异常随着市场的需求不断变化,厚板及特厚板的产量越来越多。
因此检验室检验的圆拉伸试样数量增多了。
由于圆拉伸试验需要安装卡罐(图1,图2),试样与卡罐接触部位易存在间隙,间隙过大对试验曲线会有影响,不利于试验结果的采集,会出现位移增加力值没有改变的情况(图3)。
钢筋机械连接拉伸曲线
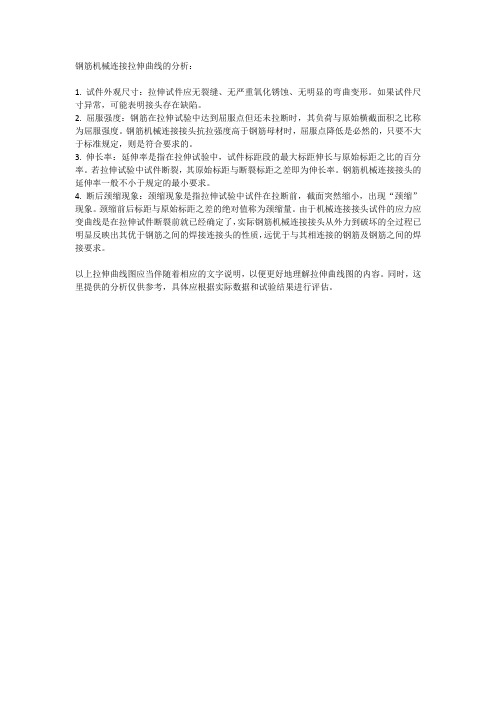
钢筋机械连接拉伸曲线的分析:
1. 试件外观尺寸:拉伸试件应无裂缝、无严重氧化锈蚀、无明显的弯曲变形。
如果试件尺寸异常,可能表明接头存在缺陷。
2. 屈服强度:钢筋在拉伸试验中达到屈服点但还未拉断时,其负荷与原始横截面积之比称为屈服强度。
钢筋机械连接接头抗拉强度高于钢筋母材时,屈服点降低是必然的,只要不大于标准规定,则是符合要求的。
3. 伸长率:延伸率是指在拉伸试验中,试件标距段的最大标距伸长与原始标距之比的百分率。
若拉伸试验中试件断裂,其原始标距与断裂标距之差即为伸长率。
钢筋机械连接接头的延伸率一般不小于规定的最小要求。
4. 断后颈缩现象:颈缩现象是指拉伸试验中试件在拉断前,截面突然缩小,出现“颈缩”现象。
颈缩前后标距与原始标距之差的绝对值称为颈缩量。
由于机械连接接头试件的应力应变曲线是在拉伸试件断裂前就已经确定了,实际钢筋机械连接接头从外力到破坏的全过程已明显反映出其优于钢筋之间的焊接连接头的性质,远优于与其相连接的钢筋及钢筋之间的焊接要求。
以上拉伸曲线图应当伴随着相应的文字说明,以便更好地理解拉伸曲线图的内容。
同时,这里提供的分析仅供参考,具体应根据实际数据和试验结果进行评估。
金属拉伸曲线课件
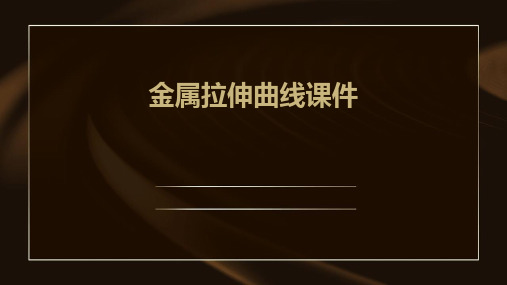
应用指导
金属拉伸曲线可以为实际工程应用提 供指导,例如在结构设计、选材等方 面提供依据。
通过对金属拉伸曲线的分析,可以优 化材料的加工工艺,提高产品的质量 和稳定性。
CHAPTER 02
金属拉伸曲线的形成原理
金属的晶体结构
晶体结构定义
金属的晶体结构是指金属内部原 子或分子的排列方式,决定了金
属的力学、物理和化学性质。
金属拉伸曲线课件
CONTENTS 目录
• 金属拉伸曲线的基本概念 • 金属拉伸曲线的形成原理 • 金属拉伸曲线的实验方法 • 金属拉伸曲线的应用实例 • 金属拉伸曲线的未来发展
CHAPTER 01
金属拉伸曲线的基本概念
金属拉伸曲线的定义
金属拉伸曲线
金属在拉伸过程中,应力与应变 之间的关系曲线。
常见晶体结构
常见的金属晶体结构有体心立方、 面心立方和密排六方等,不同的晶 体结构对金属的拉伸行为产生影响 。
晶体缺陷
在金属的晶体结构中,可能存在各 种缺陷,如空位、位错等,这些缺 陷会影响金属的塑性变形行为。
金属的塑性变形
塑性定义
金属的塑性是指金属在受到外力 作用时发生永久变形的特性。
塑性变形机制
金属制品的加工工艺优化
加工工艺参数优化
通过对金属拉伸曲线的分析,可以确定最佳的加工工艺参数,如拉伸速度、变 形程度等,以提高制品的质量和稳定性。
制品结构设计优化
根据金属拉伸曲线的变化规律,可以对制品的结构设计进行优化,以改善其受 力状况,提高制品的使用寿命。
新材料的研发与探索
新材料性能预测
通过模拟金属拉伸曲线,可以对新材料的基本性能进行预测,为新材料的研发提 供理论依据。
新材料探索与开发
拉伸曲线的四个阶段

拉伸曲线的四个阶段
拉伸曲线的四个阶段
拉伸曲线的四个阶段分别为:弹性阶段、屈服阶段、强化阶段、颈缩阶段
1、弹性阶段:随着荷载的增加,应变随应力成正比增
加。
如卸去荷载,试件将恢复原状,表现为弹性变
形,此阶段内可以测定材料的弹性模量E;
2、屈服阶段:超过弹性阶段后,载荷几乎不变,只是在
某一小范围内上下波动,试样的伸长量急剧地增加,
这种现象称为屈服。
如果略去这种荷载读数的微小
波动不计,这一阶段在拉伸图上可用水平线段来表
示。
塑性变形是突然开始且载荷数会突然下降,如
果全部卸除荷载试样将不会恢复原长表现为永久
形变。
而对于铝合金来说,弹性区域的结束点并非
伴随着载荷的突然下降或其他明显的变化从弹性
阶段到塑性阶段是一条平滑渐变的曲线;
3、强化阶段:经过屈服阶段后,曲线呈现上升趋势,
由于材料在塑性变形过程中不断强化,材料的抗变
形能力有增强了,这种现象称为应变硬化。
若在此
阶段卸载载荷到零时,变形并未完全消失,应力减
小至零时残留的应变称为塑性应变或残余应变;
4、颈缩阶段:试样伸长到一定程度后,荷载读数反而
逐渐降低。
(仅供参考)拉伸曲线、成形极限图介绍
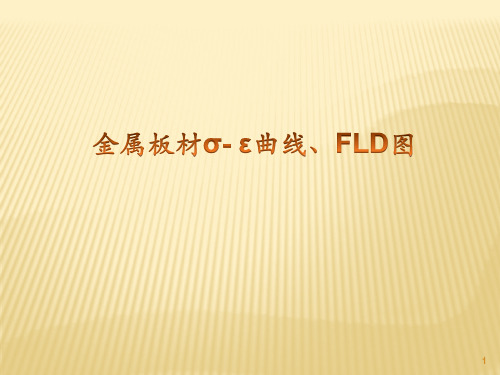
7
σ=F/S0
ReH
c
de
ReL
ε= △L/L0
第4阶段:屈服阶段(cde) 特点: (1)应力下降,应变增加; (2)Luders Band:在应力 达到c点时产生,试样表面沿 45 °度产生滑移带。 (3)c点:上屈服点
e点:屈服结束点 ce间最低点:下屈服点 (4)微观和Cottrell气团对位错 的定扎和反定扎有关。
注:屈服强度σs为下屈服应力;当屈服平台不明显时, σs=ReL
取σ0.2(变形量为0.2%时对应的应力)为屈服强度。
8
σ=F/S0
f
σb
e
ε= △L/L0
第5阶段:塑性变形加工硬化阶 段(ef) 特点: (1)试样在塑性变形下产生加 工硬化,应力不断上升,均匀塑 性变形阶段; (2)f点:应力应变曲线的最高 点;对应的应力为抗拉强度σb; (3)加工硬化阶段和位错密度 增加有关,位错在外力作用下发 生交割、增殖、塞积,要使位错 继续滑移,需进一步提高外力;
化达到平衡;
(2)不均匀塑性变形;
(3)力不再增加,试样最薄弱
的截面出现微孔,连接扩散成小
裂纹,裂纹扩展,形成缩颈,最 L m n ε= △L/L0 终断裂。
注:ok:最大力非比例伸长率; oL:最大力总伸长率; om:断后伸长率; on:断裂总伸长率。
11
12
成形极限图(FLD)或成形极限线(FLC)是评定金属板料 局部成形能力重要工具,在分析冲压成形的破裂问题时经 常使用。 FLD:冲压成形时,金属板料上缩颈或破裂区表面应变量称 为表面极限应变量。二维应变坐标系中,用不同应变路径 下表面极限应变量连成曲线或勾画出条带形区域称为冲压 成型时,成形极限曲线(Forming Limit Curve,缩写FLC), 极限应变量与极限曲线共同构成成形极限图(Forming Limit Diagram,缩写FLD) 。
拉伸试验曲线
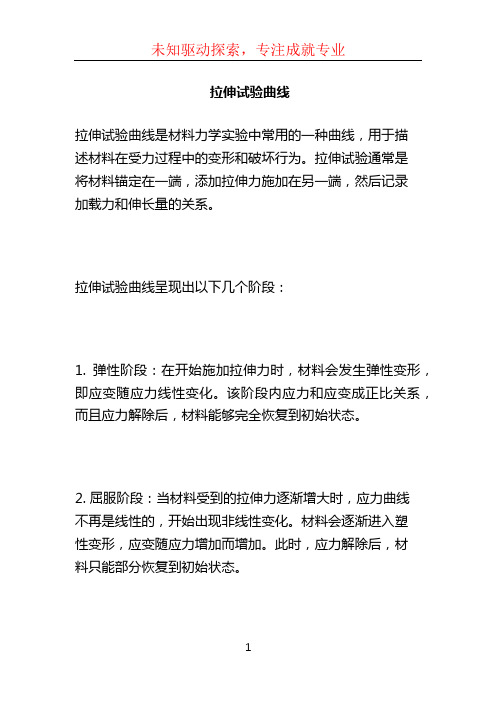
拉伸试验曲线可以通过加载力与伸长量的关系曲线图形来表示。该曲线可用于评估材料的强度、刚度、延性等力学性能,并分析材料的变形和破坏行为。
拉伸试验曲线是材料力学实验中常用的一种曲线,用于描述材料在受力过程中的变形和破坏行为。拉伸试验通常是将材料锚定在一端,添加拉伸力施加在另一端,然后记录加载力和伸长量的关系。
拉伸试验曲线呈现出以下几个阶段:
1. 弹性阶段:在开始施加拉伸力时,材料会发生弹性变形,即应变随应力线性变化。该阶段内应力和应变成正比关系,而且应力解除后,材料能够完全恢复到初始状态。
2. 屈服阶段:当材料受到的拉伸力逐渐增大时,应力曲线不再是线性的,开始出现非线性变化。材料会逐渐进入塑性变形,应变随应力增加而增加。此时,应力解除后,材料只能部分恢复到初始状态。
3. 极限阶段:当拉伸力进一步增加时,材料逐渐接近其极限强。在极限阶段,应力和应变之间关系较为复杂,材料可能发生局部变形和颈缩。
材料拉伸曲线

材料拉伸曲线
材料拉伸曲线是材料力学性能测试中的重要参数之一,它反映了材料在受力作
用下的变形和破坏过程。
通过对材料拉伸曲线的分析,可以了解材料的强度、韧性、塑性等性能,对材料的选择和设计具有重要的指导意义。
首先,材料拉伸曲线通常包括应力-应变曲线和载荷-变形曲线两种类型。
应力-
应变曲线是指在材料拉伸试验中,所施加的拉伸应力与试样的应变之间的关系曲线。
而载荷-变形曲线则是指在材料拉伸试验中,所施加的载荷与试样的变形之间的关
系曲线。
这两种曲线都可以反映材料在受力过程中的性能表现,但侧重点略有不同。
其次,材料拉伸曲线的特征包括线性阶段、屈服阶段、强化阶段和断裂阶段。
在拉伸试验开始时,材料会出现线性阶段,此时应力与应变成正比。
随着应力的增加,材料进入屈服阶段,此时材料开始出现塑性变形。
在经过屈服点后,材料进入强化阶段,此时应力与应变的关系变得更为陡峭。
最终,材料达到断裂点,发生破坏。
此外,材料拉伸曲线的形状与材料的性能密切相关。
比如,曲线的斜率可以反
映材料的弹性模量,屈服点可以反映材料的屈服强度,而强化阶段的斜率则可以反映材料的强化能力。
通过对这些特征的分析,可以全面了解材料的性能表现,为材料的应用提供重要的参考依据。
总之,材料拉伸曲线是材料力学性能测试中的重要参数,通过对其特征的分析,可以全面了解材料在受力过程中的性能表现,为材料的选择和设计提供重要的指导意义。
因此,在工程实践中,对材料拉伸曲线的研究具有重要的意义,可以为材料的应用提供科学的依据。
解读塑料拉力机的拉伸曲线及参数

解读塑料拉力机的拉伸曲线及参数
塑料拉力机是测量塑料制品的拉力等物理性能的,测试拉力性能后就会有一个拉伸曲线图,这个图需要我们去读懂,如果你什么都不知道,那么你肯定不知道上面的符号代表的是什么含义,因此在使用塑料拉力机前应该先了解如何读懂这些参数值。
塑料拉力机的拉伸曲线图:由试验机绘出的拉伸曲线,实际上是载荷-伸长曲线,如将载荷坐标值和伸长坐标值分别除以试样原截面积和试样标距,就可得到应力-应变曲线图。
图中op部分呈直线时,说明应力与应变成正比,其比值就是弹性模量,Pp表示呈正比时的最大载荷,p点应力表示比例极限σp.继续加载时,曲线偏离op,直到e点,这时如卸去载荷,试样仍然可以恢复到原始状态,若过e点试样便不能恢复原始状态。
e点应力为弹性极限σe.工程上由于很难测得真正的σe,常取试样残余伸长达到原始标距的0.01%时的应力为弹性极限,以σ0.01 表示。
继续加载荷,试样沿es曲线变形达到s点,此点应力为屈服点σS或残余伸长为0.2%的条件屈服强度σ0.2.过s 点继续增加载荷到拉断前的最大载荷b点,这时的载荷除以原始截面积即为强度极限σb.在b点以后,试样继续伸长,而横截面积减小,承载能力开始下降,直到k点断裂。
断裂瞬间的载荷与断裂处的截面的比值称断裂强度。
一般来说,塑料拉力机拉伸试验需要求取以下几项或七项的参数
1.试样拉伸至断裂过程中出现的最大力值(拉伸强度);
2.试样断裂时的力值(断裂强度);
3.屈服点对应的力值(屈服点拉伸应力);
4.试样拉伸到给定伸长率时的力值(定伸应力);
5.试样拉伸至给定应力时的伸长率(定应力伸长率);
6.屈服点对应的伸长率(屈服点伸长率);
7.试样断裂时的伸长率(扯断伸长率)。
- 1、下载文档前请自行甄别文档内容的完整性,平台不提供额外的编辑、内容补充、找答案等附加服务。
- 2、"仅部分预览"的文档,不可在线预览部分如存在完整性等问题,可反馈申请退款(可完整预览的文档不适用该条件!)。
- 3、如文档侵犯您的权益,请联系客服反馈,我们会尽快为您处理(人工客服工作时间:9:00-18:30)。
如何分析拉伸曲线?拉伸曲线分析篇
时间:2012-11-16 15:19:29 来源:越联作者:越联点击数:核心提示:拉伸试验的本质是对试样施加轴向拉力,测量试样在变形过程中直至断裂的各项力学性能。
试验材料的全面性能反映在拉伸曲线上。
拉力曲线如此重要,如何根据拉伸曲线分析材料的各项性能呢?现在就给大家分析下拉伸曲线。
拉伸试验的本质是对试样施加轴向拉力,测量试样在变形过程中直至断裂的各项力学性能。
试验材料的全面性能反映在拉伸曲线上。
拉力曲线如此重要,如何根据拉伸曲线分析材料的各项性能呢?现在就给大家分析下拉伸曲线。
典型的拉伸曲线图(低碳钢)
第 1 阶段:弹性变形阶段(oa)两个特点
a 从宏观看,力与伸长成直线关系,弹性伸长与力的大小和试样标距长短成正比,与材料弹性模量及试样横截面积成反比。
b 变形是完全可逆的。
加力时产生变形,卸力后变形完全恢复。
从微观上看,变形的可逆性与材料原子间作用力有直接关系,施加拉力时,在力的作用下,原子间的平衡力受到破坏,为达到新的平衡,原子的位置必须作新的调整即产生位移,使外力、斥力和引力三者平衡,外力去除后,原子依靠彼此间的作用力又回到平衡位置,使变形恢复,表现出弹性变形的可逆性,即在弹性范围保持力一段时间,卸力后仍沿原轨迹回复。
Oa 段变形机理与高温条件下变形机理不同,在高温保持力后会产生蠕变,卸力后表现出不可逆性。
由于在拉伸试验中无论在加力或卸力期间应力和应变都保持单值线性关系,因此试验材料的弹性模量是 oa 段的斜率,用公式求得:
E=σ/ε
oa 线段的 a 点是应力-应变呈直线关系的最高点,这点的应力叫理论比例极限,超过 a 点,应力-应变则不再呈直线关系,即不再符合虎克定律。
比例极限的定义在理论上很有意义,它是材料从弹性变形向塑性变形转变的,但很难准确地测定出来,因为从直线向曲线转变的分界点与变形测量仪器的分辨力直接相关,仪器的分辨力越高,对微小变形显示的能力越强,测出的分界点越低,这也是为什麽在最近两版国家标准中取消了这项性能的测定,而用规定塑性(非比例)延伸性能代替的原因。
第 2 阶段:滞弹性阶段(ab)
在此阶段,应力-应变出现了非直线关系,其特点是:当力加到 b 点时然后卸除力,应变仍可回到原点,但不是沿原曲线轨迹回到原点,在不同程度上滞后于应力回到原点,形成一个闭合环,加力和卸力所表现的特性仍为弹性行为,只不过有不同程度的滞后,因此称为滞弹性阶段,这个阶段的过程很短。
这个阶段也称理论弹性阶段,当超过 b 点时,就会产生微塑性应变,可以用加力和卸力形成的闭合环确定此点,当加卸力环第 1 此形成开环时所对应的点为 b 点。
第 3 阶段:微塑性应变阶段(bc)
是材料在加力过程中屈服前的微塑性变形部分,从微观结构角度讲,就是多晶体材料中处于应力集中的晶粒内部,低能量易动位错的运动。
塑性变形量很小,是不可回复的。
大小仍与仪器分辨力有关。
第 4 阶段:屈服阶段(cde)
这个阶段是金属材料的不连续屈服的阶段,也称间断屈服阶段,其现象是当力加至 c 点时,突然产生塑性变形,由于试样变形速度非常快,以致试验机夹头的拉伸速度跟不上试样的变形速度,试验力不能完全有效的施加于试样上,在曲线这个阶段上表现出力不同程度的下降,而试样塑性变形急剧增加,直至达到 e 点结束,当达到 c 点,在试样的外表面能观察到与试样轴线呈 45 度的明显的滑移带,这些带称为吕德斯带,开始是在局部位置产生,逐渐扩展至试样整个标距内,宏观上,一条吕德斯带包含大量滑移面,当作用在滑移面上的切应力达到临界值时,位错沿滑移方向运动。
在此期间,应力相对稳定,试样不产生应变硬化。
C 点是拉伸试验的一个重要的性能判据点,范围内的最低点也是重要的性能判 de 据点,分别称上屈服点和下屈服点。
e 点是屈服的结束点,所对应的应变是判定板材成型性能的重要指标。
第 5 阶段:塑性应变硬化阶段(ef)
屈服阶段结束后,试样在塑性变形下产生应变硬化,在 e 点应力不断上升,在这个阶段内试样的变形是均匀和连续的,应变硬化效应是由于位错密度增加而引起的,在此过程中,不同方向的滑移系产生交叉滑移,位错大量增殖,位错密度迅速增加,此时必须不断继续施加力,才能使位错继续滑移运动,直至 f 点。
f 点通常是应力-应变曲线的最高点(特殊材料除外),此点所对应的应力是重要的性能判据。
第 6 阶段:缩颈变形阶段(fg)
力施加至 f 点时,试验材材料的应变硬化与几何形状导致的软化达到平衡,此时力不再增加,试样最薄弱的截面中心部分开始出现微小空洞,然后扩展连接成小裂纹,试样的受力状态由两向变为三向受力状态。
裂纹扩展的同时,在试样表面可看到产生缩颈变形,
在拉伸曲线上,从 f 点到 g 点力是下降的,但是在试样缩颈处,由于截面积已变小,其真应力要大大高于工程应力。
试验达到 g 点试样完全断裂。
从以上典型的拉伸曲线上,可以测定金属材料如下性能:
1 上屈服强度:(c点)试样发生屈服而力首次下降前的最高应力
2 下屈服强度:(e 点)屈服期间的最低应力,要注意这里要排除初始瞬时效应最低应力点所对应的应力。
初始瞬时效应是表现于上屈服过后,力的突然降低的现象,其大小与试验机加力系统的柔度、试样的柔度、拉伸速度、试样屈服特性以及测力系统的惯性守恒各种因素有关。
3 抗拉强度:(f 点)在最大力点所对应的应力。
注意:新标准最大力的定义与GB/T228-87 不同,新标准规定:最大力是指屈服阶段之后的最大力,当材料无明显屈服时,是试验期间的最大力。
4 屈服点延伸率:(ae)对于呈现明显屈服现象的材料,从屈服开始至均匀硬化开始之间的延伸率。
要注意起点和终点的判定。
5 最大力总伸长率: F点处作一垂线, f 横座标原点与交点长度对应的伸长率(包括在此条件下的弹性伸长和塑性伸长率)。
6最大力非比例伸长率:f 点处作一平行于弹性段的直线,横座标原点与交点对应的伸长率。
7 断裂总伸长率:(g点)断裂时刻的试样总伸长率(包括弹性伸长和塑性伸长率),这里要注意的是断裂瞬间的判定,根据自动测试系统采样频率作合理测定。
当扣除断裂瞬间的弹性伸长率时,则是断后伸长率 A。
许多脆性材料在拉伸过程中不出现明显屈服现象,只有 3~4 阶段: oa-弹性变形阶段 ab-滞弹变形阶段 bf-应变硬化阶段(对淬火钢,到 f 断裂,对中强钢有缩颈)在此情况下,用规定条件强度表示屈服强度
8 规定塑性延伸强度 Rp:规定非比例延伸率对应的应力,即在代表伸长的横坐标上取规定的伸长量,平行于弹性线段作一直线。
在与曲线交点处作一水平线与力轴的交点力值所对应的应力为 Rp。
一般称平行线法,适用于弹性段为直线的拉伸曲线。
对于弹性段不是直线的拉伸曲线,上述方法无法用,此时要用滞后环法或逐步逼近法进行测定。
9 规定残余延伸强度 Rr:是对于拉伸过程中不出现明显屈服现象材料,用规定条件强度表示屈服强度另一性能,包括规定残余延伸强度 Rr 的测定和验证。
10 规定总延伸强度 Rt:规定总延伸率对应的应力,即在代表伸长的横坐标上取规定的伸长量,平行于力轴作一直线。
在与曲线交点处作一水平线与力轴的交点力值所对应的应力为 Rt。