第四章陶瓷成型技术
陶瓷成型工艺技术

陶瓷成型工艺技术陶瓷成型工艺技术是制造陶瓷产品的重要环节,它包括了整个制造过程中的成型、干燥和烧成等环节。
下面我们就来详细介绍一下陶瓷成型工艺技术。
陶瓷成型主要有手工成型和机械成型两种方式。
手工成型是传统的成型方式,通过手工操作将陶瓷泥料按照设计要求塑造成各种形状。
这种方式需要熟练的技术和经验,对工匠的要求较高。
而机械成型则是利用专门的设备进行成型,可以大大提高工作效率和产品的一致性。
无论是手工成型还是机械成型,首先需要制作成型工具。
手工成型时,工匠需要根据设计要求制作木模、泥模或者石模等成型工具。
而机械成型时,则需要根据产品的形状和尺寸设计制作专业的模具。
模具的制作需要考虑到产品的材料特性、成型工艺和产品的工艺要求。
在成型过程中,首先要准备好陶瓷泥料,根据工艺要求配置出适合的泥料浆料。
然后将泥料放入成型工具中,利用手工或者机械的力量逐步塑造成所需的形状。
这个过程需要注意控制泥料的水分含量和成型工具的力度,以确保成型的准确和一致性。
成型完成后,陶瓷制品需要经过干燥的过程。
干燥的目的是将陶瓷制品中的水分逐渐蒸发掉,使其成为干燥坚硬的瓷坯。
干燥过程需要控制好温度、湿度和通风等条件,以避免制品出现开裂和变形的问题。
最后一步就是烧成了。
烧成是将干燥的陶瓷制品置于高温条件下,使其经历化学和物理变化,最终形成坚硬、致密且具有特殊性能的陶瓷制品。
烧成过程需要控制好温度、时间和烧成环境,以确保制品的质量和性能。
总结起来,陶瓷成型工艺技术是制造陶瓷产品中的重要环节。
它包括了成型、干燥和烧成等过程,需要掌握深厚的技术和经验。
通过合理的成型工艺,能够制造出形状美观、质量优良的陶瓷制品,满足不同客户的需求。
陶瓷成型技术
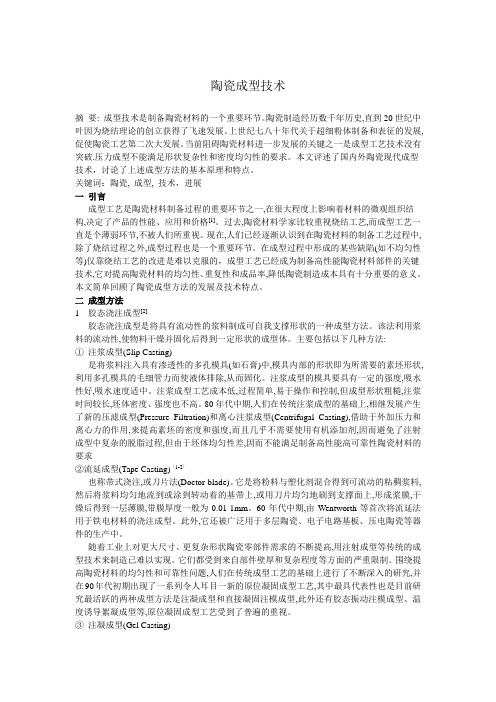
陶瓷成型技术摘要: 成型技术是制备陶瓷材料的一个重要环节。
陶瓷制造经历数千年历史,直到20世纪中叶因为烧结理论的创立获得了飞速发展。
上世纪七八十年代关于超细粉体制备和表征的发展,促使陶瓷工艺第二次大发展。
当前阻碍陶瓷材料进一步发展的关键之一是成型工艺技术没有突破.压力成型不能满足形状复杂性和密度均匀性的要求。
本文评述了国内外陶瓷现代成型技术,讨论了上述成型方法的基本原理和特点。
关键词:陶瓷, 成型, 技术,进展一引言成型工艺是陶瓷材料制备过程的重要环节之一,在很大程度上影响着材料的微观组织结构,决定了产品的性能、应用和价格[1]。
过去,陶瓷材料学家比较重视烧结工艺,而成型工艺一直是个薄弱环节,不被人们所重视。
现在,人们已经逐渐认识到在陶瓷材料的制备工艺过程中,除了烧结过程之外,成型过程也是一个重要环节。
在成型过程中形成的某些缺陷(如不均匀性等)仅靠烧结工艺的改进是难以克服的,成型工艺已经成为制备高性能陶瓷材料部件的关键技术,它对提高陶瓷材料的均匀性、重复性和成品率,降低陶瓷制造成本具有十分重要的意义。
本文简单回顾了陶瓷成型方法的发展及技术特点。
二成型方法1 胶态浇注成型[2]胶态浇注成型是将具有流动性的浆料制成可自我支撑形状的一种成型方法。
该法利用浆料的流动性,使物料干燥并固化后得到一定形状的成型体。
主要包括以下几种方法:①注浆成型(Slip Casting)是将浆料注入具有渗透性的多孔模具(如石膏)中,模具内部的形状即为所需要的素坯形状,利用多孔模具的毛细管力而使液体排除,从而固化。
注浆成型的模具要具有一定的强度,吸水性好,吸水速度适中。
注浆成型工艺成本低,过程简单,易于操作和控制,但成型形状粗糙,注浆时间较长,坯体密度、强度也不高。
80年代中期,人们在传统注浆成型的基础上,相继发展产生了新的压滤成型(Pressure Filtration)和离心注浆成型(Centrifugal Casting),借助于外加压力和离心力的作用,来提高素坯的密度和强度,而且几乎不需要使用有机添加剂,因而避免了注射成型中复杂的脱脂过程,但由于坯体均匀性差,因而不能满足制备高性能高可靠性陶瓷材料的要求②流延成型(Tape Casting)〔1-2〕也称带式浇注,或刀片法(Doctor-blade)。
陶瓷成型技术 ppt课件
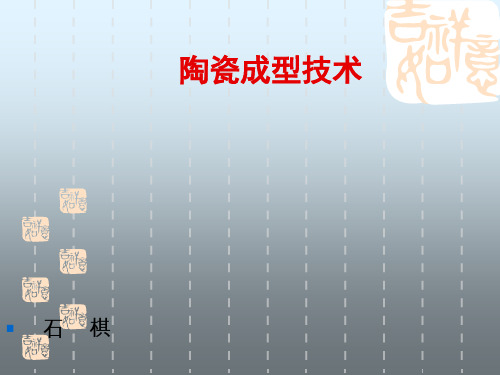
▪ 此外,流延成型技术还可以 用于造纸、塑料和涂料等行 业。
▪ 该工艺是由Glenn N. Howatt 于1947 年首次提出并于1952 年获得专利。
流延成形原理
陶瓷粉未 (烧结助剂)
溶剂 粘结剂
一次球磨 二次球磨
▪ 粉料成型 粉料含水量或其它溶剂≤8%
选择成型方法最基本的依据
➢ 产品的形状、大小和厚薄等。一般情况下,简单的回转 体宜用可塑法中的滚压法或旋压法;大件且薄壁产品可 用注浆法;板状和扁平状产品,宜用压制法。
➢ 坯料的工艺性能。可塑性能良好的坯料宜用可塑法;可 塑性能较差的坯料可选择注浆法或压制法。
工艺流程
▪ 单体AM:丙烯酰胺 ▪ 交联剂MBAM :亚甲基双丙烯酸胺 ▪ 分散剂:小、大分子电解质非电解质 ▪ 引发剂:过硫酸铵 ▪ 催化剂:四甲基乙二胺TEMED
链引发反应
▪ 初级自由基M·
单体自由基M·
链增长反应
单体
链终止反应
浆料成型的共同难点
▪ 高固相、低粘度浆料的分散与稳定悬浮。
凝胶铸模成型工艺特点
▪ 成形坯体强度高,可机械加工成形状复杂 的部件20MPa~40 MPa ;
▪ 有机物含量少,排胶较易; ▪ 净尺寸成型,表面光洁,可避免或减少烧
成后的加工; ▪ 陶瓷浆料具有很高的固相体积分数,一般
大于50vol%; ▪ 由于陶瓷颗粒原位凝固,成形坯体内部均
匀,缺陷少,保证烧结后材料Байду номын сангаас高可靠性。
➢ 产品的产量和质量要求。产量大宜用可塑法或压制法, 产量小可用注浆法;产品尺寸要求高时用压制法,产尺 寸规格要求不高时用注浆法或手工可塑成型。
陶瓷成型技术教案模板范文

课时:2课时年级:高中学科:工艺技术教学目标:1. 知识与技能:了解陶瓷成型技术的基本原理、常用方法和设备,掌握注浆成型、可塑成型、压制成型等基本技术。
2. 过程与方法:通过实践操作,培养学生动手能力和团队协作精神。
3. 情感态度与价值观:激发学生对陶瓷艺术的兴趣,培养学生对传统工艺的尊重和传承意识。
教学重点:1. 陶瓷成型技术的基本原理和常用方法。
2. 注浆成型、可塑成型、压制成型等基本技术的操作步骤。
教学难点:1. 陶瓷成型过程中材料的选择和配比。
2. 陶瓷成型过程中的质量控制。
教学准备:1. 教学课件2. 陶瓷原料、模具、工具等3. 实验室安全用品教学过程:第一课时一、导入新课1. 引导学生欣赏陶瓷艺术品,激发学生对陶瓷艺术的兴趣。
2. 提问:陶瓷是如何制作的?有哪些成型方法?二、讲授新课1. 介绍陶瓷成型技术的基本原理和常用方法。
2. 详细讲解注浆成型、可塑成型、压制成型等基本技术的操作步骤。
3. 分析陶瓷成型过程中的材料选择和配比,以及质量控制要点。
三、实践操作1. 学生分组,每组选择一种成型方法进行实践操作。
2. 教师巡回指导,纠正操作中的错误。
四、课堂小结1. 总结本节课所学内容。
2. 提出课后作业:收集陶瓷艺术品的图片或实物,了解其成型方法。
第二课时一、复习导入1. 复习上一节课所学内容。
2. 提问:陶瓷成型过程中有哪些注意事项?二、讲授新课1. 讲解陶瓷成型过程中的材料选择和配比。
2. 分析陶瓷成型过程中的质量控制要点。
三、实践操作1. 学生根据上一节课所学内容,继续完成实践操作。
2. 教师巡回指导,纠正操作中的错误。
四、课堂小结1. 总结本节课所学内容。
2. 提出课后作业:设计一款陶瓷作品,并尝试制作。
教学评价:1. 课堂表现:观察学生在实践操作中的表现,评价其动手能力和团队协作精神。
2. 作业完成情况:检查学生的课后作业,评价其对陶瓷成型技术的掌握程度。
3. 作品质量:评价学生的陶瓷作品,包括成型质量、造型创意等方面。
陶瓷成型技术

项目1:注浆成型技术
一、注浆成型 传统的定义:在石膏模的毛细管力作用下,含有一 定水分的粘土泥浆脱水硬化、成型的过程。 目前:将所有基于坯料具有一定液态流动性的成型 方法统归为注浆成型。 工艺特点: (1)适于成型各种产品,形状复杂、不规则、薄、 体积较大而且尺寸要求不严的器物,如花瓶、汤碗、 椭圆形盘、茶壶等。 (2)坯体结构均匀,但含水量大且不均匀,干燥 与烧成收缩大。
防止粉化的方法有: ①适当降低模型的干燥速度,使水分能够从模型四 周均匀地蒸发; ②采取提前合模的办法,夜间让模型整体干燥,因 模型湿不宜提前合模的,可在芯子上部盖塑料布, 以防止大量的水分从顶点蒸发; ③待模型的外吃浆面刮去一层,增加透气性,使水 分向外吃浆面蒸发。
5、延长石膏模型的使用寿命 1)石膏模型有一定的使用寿命,一般可塑成型用 模型的使用寿命约100-250次,注浆成型用模型只 有50-150次。其损坏原因主要有以下三方面:其 一是模型本身强度不高,易被碰裂或压裂;其二是 模型工作面被坯料中泥粒磨损而报废;其三是注桨 用模型由于模型与坯料桨中电解质起休化学反应造 成模型的毛细孔中与表面上产生硫酸钠析晶,而降 低吸水能力。
石膏模的寿命不但取决于合理的使用,还与制模的 石膏质量和操作工艺过程有关。如石膏粉炒温度过 高或过低,石膏粉颗粒粗大,浇注时加水过多,混 合不均匀,制备好的石膏粉放在潮湿的地方等情况 均会影响模型使用寿命。 2)为了延长石膏模的使用寿命,应正确掌握制造 模型的工艺操作和合理使用外,还可从提高石膏模 的机械强度入手。
各类产品尽管加工方法不同,但是坯体修整是必要 的,不可忽视的,否则就不能保证瓷器半成品质量。 在修坯中也要防止坯体产生缺陷,并修整那些能修 整的带缺陷的坯体。 修坯分为干修和湿修两种方式。 湿修:坯体的水分16~19%。 干修:坯体的水分 < 2%。
陶瓷材料成型方法

陶瓷材料成型方法
陶瓷材料的成型方法有多种,以下是三种主要的方法:
1. 可塑法成型:在外力作用下,使具有可塑性的坯料发生塑性变形而制成坯体的方法。
具体分为手工成形和机械成形两大类。
手工成形如雕塑、印坯、拉坯、手捏等,多用于艺术陶瓷的制造。
而机械成形如旋压和滚压成形,则多用于盘、碗、杯碟等制品的生产。
此外,还有其他陶瓷工业中采用的挤制、车坯、压制、轧膜等可塑成形方法。
2. 注浆法成型:利用多孔模型的吸水性,将泥浆注入其中而成形的方法。
这种成形方法适应性强,凡是形状复杂,不规则的薄壁、厚胎、体积较大且尺寸要求不严的制品都可用注浆法成型。
例如日用陶瓷中的花瓶、汤碗、椭圆形盘、茶壶手柄等都可采用注浆法成型。
3. 压制法成型:利用压力将置于模具内的粉料压紧至结构紧密,成为具有一定形状和尺寸的坯体的成形方法。
此外,还有其他的成型方法,如干压成型、等静压成型等,可以根据不同的需求选择合适的成型方法。
第四章 陶瓷工艺学 成型
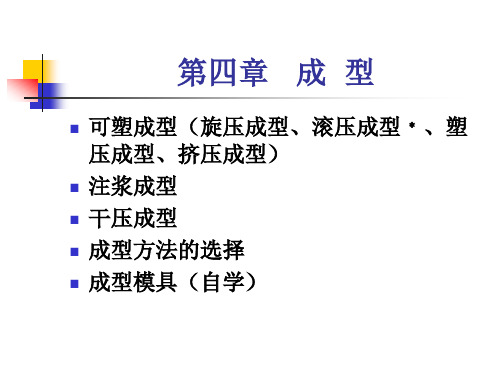
在生产实际中,可通过变更或调整泥料配 方的主粘土种类和配比,来调节泥料的流 变特性参数,使其屈服值与延展变形量满 足各种成形工艺方法的要求。
二、影响泥团可塑性的因素 粘土 矿物组成:蒙脱石>高岭石>伊利石
主轴转速(n1)和滚头转速(n2),转速比i= n1/ n2
为了在短时间内对泥料多次加压以及提高产量,主轴转速应 快些。但是,要使模型稳定旋转,尤其是对阳模滚压来说, 主轴转速不宜太快,否则易引起泥料飞离模型。对阴模滚压 来说,其主轴转速可比阳模滚压适当快些,过慢则易粘滚头。
无论阴模或阳模滚压,制品的口径大,滚头和主轴的转速均 应稍慢。反之,则可适当加快。
二、注浆过程(机理) 注浆成型基于石膏模吸收水分的特性,即借助石膏
模的毛细管力从泥浆中吸取水分,在该过程中,于模具 内面形成部分脱水的致密硬质塑性沉淀物层。该层的形 成过程称为坯料吸浆。
注浆成形过程可分为吸浆成坯和巩固脱模两个阶段
1. 吸浆成坯阶段
由于石膏模的吸水作用,先在靠近模型的工作面上形成一薄泥 层,随后泥层逐渐增厚达到所要求的坯体厚度。
小到大比较缓和、均匀,使坯体组织结构均匀;
滚压头与坯泥的接触面积较大,压力较大,受压时间较长,
坯体较致密,强度较高;
滚压成型靠滚压头与坯体相“碾”而使坯体表面光滑,无需
再加水赶光;所以滚压成型的坯体强度大,不易变形,表面质量 好
2.成型方法:阳模滚压及阴模滚压
3. 参数控制
泥料的性能:可塑性好、屈服值高些、延伸变形量大些、含
热滚和冷滚的工艺特点
冷滚的滚头可用聚四氟乙烯(塑料王)制成。塑料王具有良 好的物理化学性能,最高工作温度可达250℃,有突出的化 学稳定性,高温也不怕酸,与泥料摩擦系数小,不粘性和憎 水性强,表面光洁度高。用它制作滚头可在常温下成形而不 粘泥。阴模冷滚头材料还可用球墨铸铁,灰口铸铁。滚头结 构简单、不需加热装置,塑料王滚头还可由成形工人自己修 制,便于调整器型廓线和坯体厚薄。因而冷滚也成为我国的 陶瓷生产的一种主要成形手段。
陶瓷的成型技巧

陶瓷的成型技巧陶瓷是一种古老而又具有深厚文化底蕴的工艺品,而陶瓷制作的成型过程更是其制作工艺中的关键步骤之一。
陶瓷成型技巧在不同的时代和地域都有着不同的发展历史和特点,因此在这里我们将着重介绍陶瓷的成型技巧及其发展历史。
1. 手工成型技术手工成型技术是陶瓷成型技巧的最古老方法之一,它包括了传统的拉坯、减坯、轧坯、印坯等工艺。
拉坯是最为简单且常见的一种成型技术,制作陶瓷器皿的原理是将陶泥放在陶轮上旋转,然后利用手的力量来拉出器皿的形状。
减坯则是将原来的坯体逐渐削减至所需的形状和尺寸,这种方法主要用于制作对称的器皿。
轧坯是将陶泥放在桌上,然后用擀面棒慢慢擀成所需的形状,是古代常用的一种成型技术。
印坯则是用印模将图案和纹饰印在坯体上,制作器皿时只需根据印模的图案和纹饰进行成型。
2. 机械成型技术随着工业的发展,机械成型技术逐渐被引入到陶瓷制作的成型过程中。
其中最为常见的机械成型技术就是注塑成型技术和挤压成型技术。
注塑成型技术是将陶泥放入模具,然后利用注塑机将陶泥注入模具中,通过高压力使得陶泥充分填满模具的每一个角落,最终形成成型。
挤压成型技术则是将陶泥装入一个圆柱形模具中,然后用挤出机将陶泥挤压出所需的形状,这种技术特别适用于制作管状产品。
3. 旋转成型技术旋转成型技术也是陶瓷成型技巧中的一种重要方法,它主要通过旋转机械将坯体进行形状调整和成型,在这个过程中需要用手工来打磨和修饰坯体。
这种技术一般适用于制作较大型的器皿和雕塑作品,因为这种方法可以对坯体进行更多的细节处理。
4. 压坯成型技术压坯成型技术是通过压制模具来形成陶瓷成型的一种方式。
首先将陶泥放入特制的模具中,然后通过机械设备对模具进行压制,最终形成成型。
与传统的手工成型技术相比,这种方法可以大大提高生产效率并且可以做出大量相同尺寸的成型,因此在现代工业生产中非常常见。
5. 散坯成型技术散坯成型技术是一种将陶泥散放在模具内,然后用手工和机械设备来将散坯压实成型的技术。
- 1、下载文档前请自行甄别文档内容的完整性,平台不提供额外的编辑、内容补充、找答案等附加服务。
- 2、"仅部分预览"的文档,不可在线预览部分如存在完整性等问题,可反馈申请退款(可完整预览的文档不适用该条件!)。
- 3、如文档侵犯您的权益,请联系客服反馈,我们会尽快为您处理(人工客服工作时间:9:00-18:30)。
快速原型成型流程图
陶瓷成型方法
模压成型 冷等静压成型 注浆成型 原位凝固成型 快速原型成型 注射成型 薄膜和厚膜成型
模压成型
模压成型: 模压成型:通过模冲对装在钢模内的粉体 施加一定压力, 施加一定压力,压制成一定形状和尺寸的 压坯,卸压后,坯块从阴模中脱出。 压坯,卸压后,坯块从阴模中脱出。
一般会形成密度梯度分布(单向和双向压制) 一般会形成密度梯度分布(单向和双向压制)
快速原型成型技术
快速原型成型技术RP(Rapid Prototype)是20世 纪80年代出现的用于制造业的高新技术。它是集 CAD、CAM、机械电子工程、数控技术、激光技术、 化学技术、新材料科学为一体的新型制造技术,是 当前最先进的制造技术之一。 其本质是用积分制造三维实体。在成型过程中,先有 三维造型软件在计算机中做成部件的三维实体模型, 然后将其用软件“切割”出设定厚度(几个微米) 的系列片层;再将这些片层数据传递给成型机器, 通过材料逐层添加法制造出来,而不需要特殊模具、 工具或者人工干涉。
快速原型成型技术特点
陶瓷快速原型成型技术是陶瓷成型方式的一个革命 性突破,它具有的显著特征为: 1、它加工产品的造价几乎与批量无关,非常适合小 批量产品,尤其是单个产品; 2、它的生产周期比传统方法短得多; 3、几乎不受零件复杂性的限制; 4、制造成本与产品复杂性无关; 5、高度技术集成,可以实现设计制造一体化; 6、高度灵活性,仅需改变CAD模型、重新调整设置 参数即可生产不同形状的陶瓷部件。
冷等静压成型
利用高压泵把液体介质压入钢制的高压密封容器内, 利用高压泵把液体介质压入钢制的高压密封容器内,在弹性模套 内的粉料在各个方向上同时受到液体传递的均衡压力, 内的粉料在各个方向上同时受到液体传递的均衡压力,从而获得 密度分布均匀和强度较好的压坯。 密度分布均匀和强度较好的压坯。
分为干袋式和湿袋式
注浆成型分为普通注浆,压力注浆,真空注浆, 注浆成型分为普通注浆,压力注浆,真空注浆, 离心注浆等
原位凝固成型技术
陶瓷浆料原位凝固成型是20世纪90年代迅速发展起来的 胶态成型技术。其成型原理不同于依赖多孔模吸收浆料 的传统注浆成型,而是通过浆料内部的化学反映形成大 分子网络或者陶瓷颗粒网络结构,从而使注模后的陶瓷 浆料快速凝固为陶瓷坯体。
陶瓷成型工艺过程
工艺阶段 粉体 成型体 烧结体
特征 化学 形态 体堆性 均匀性 缺陷 晶粒 气孔 相态 化学特性 烧结尺寸形状 控制参数 化学计量 杂质 颗粒尺寸分布 团聚 形状和比表面 堆积性 流动性 密度 颗粒和有机物的分布 孔隙的尺寸和分布 裂纹 晶粒生长 尺寸和分布 致密化速度 气孔尺寸和分布 相态分布 相尺寸 晶界 偏析 炉内污染 烧结气氛影响 收缩率 烧结密度 尺寸精度
4 陶瓷成型技术
由粉体制造的陶瓷产品必须考虑的性能要求:
1材料特征性能 材料特征性能 2产品形状和尺寸 以及所要求的尺寸公差 产品形状和尺寸,以及所要求的尺寸公差 产品形状和尺寸 3产品的成本 产品的成本
其中第1项取决于材料的化学成分以及获得的显微结 构;而第2项则与生产设备和成型方法的选择及其可靠性 相关;而材料的化学成分和成型过程都会影响到产品的成 本. 工艺过程:为了获得规定要求的产品而进行的机械, 工具,方法,材料和人员的组合; 而工艺控制则是为此目的 建立和制备的标准而进行的一种有效的工艺过程控制.
原位凝固成型技术分类
凝胶成型(Gel Casting) 直接凝固成型(Direct coagulation casting ) 温度诱导絮凝成型(Temperature induced Temperature flocculation) 高分子凝胶注模成型(Polymer linking gel casting )
生产效率不高
500MPa
容易产生缺陷
200MPa
注浆成型
注浆成型:选择适当的反絮凝剂和悬浮液,将粉状原料制 成泥浆,浇注到多孔 多孔吸水性的模具 模具(一般常用石膏模)中, 多孔 模具 通过毛细管力或者外加压力使溶剂排出,浆料即干涸成 通过毛细管力或者外加压力使溶剂排出 一定形状的陶瓷坯体。 特点: 特点:注浆成型后的坯体结构均匀,但其含水量大,且 不均匀,干燥与烧成收缩也较大,不需专用设备,也不 拘于生产量的大小,投产容易上马快;但生产时间长, 手工操作多,占地面积大,模型用量大。
为了减少压制时的摩擦,改善压坯的密度和均匀性,减少模具的 磨损和脱模,粉料中一般加入1%以下的具有极性官能团的有机物 做润滑剂(油酸,石蜡或者硬脂酸盐)。 陶瓷坯体的压制压力一般为40----100兆帕。 模压成型只能成型形状简单和尺寸较小的陶瓷制品。(受 模压成型只能成型形状简单和尺寸较小的陶瓷制品。(受模具和 。( 压力的限制) )
湿袋式 定义 优点 缺点源自等静压压 力将预先成型的坯体放入可变形 的包套内,然后施加各向均匀 的压力,当压制过程完成时, 再将坯体的湿袋从容器内取出 成本相对低,成型不同形状制 品,灵活性大
干袋式
粉末批量填入柔性预先成型模具内, 然后施加等静压。由于干袋被固定 在设备中,当压制过程完成时,成 型制品退出 生产周期短,模具寿命长,便于大 规模工业化