陶瓷注射成型技术
【精品文章】一文了解陶瓷粉末注射成型

一文了解陶瓷粉末注射成型
精密陶瓷是近三十年材料科学领域中迅速发展起来的一大分支。
但陶瓷材料本身固有的高硬度、低韧性使其不能进行普通的变形加工,机械加工也很困难。
常规的粉末冶金工艺已不能满足要求,而注射成型工艺在很大程度上解决了这个问题。
陶瓷粉末注射成型(简称CIM)是近代粉末注射成型技术的一个分支,是从现代粉末注射成型技术中发展起来的一项新型成型技术,它具有一次性成型复杂形状制品、产品尺寸精度高、无需机械加工或只需微量加工、易于实现生产自动化和产品性能优异的特点,弥补了传统粉末冶金工艺的不足。
图1 陶瓷注射成型机及注射成型示意图
1. 陶瓷粉末注射成型的技术特点
从技术特点来说,陶瓷粉末注射成型和金属粉末注射成型类似,理论上任何形式的陶瓷粉末原料,如ZrO2、Al2O3、Si3N4等,都能利用CIM工艺制造形状复杂、精度高的产品。
CIM的基本工艺过程如图2所示。
图2 CIM的基本工艺过程[1]
综合国内外文献及研究生产现状和趋势,可以归纳出陶瓷粉末注射成型工艺的主要特点如下:
(1)可自由地直接制备几何形状复杂的制品。
(2)成形周期短,仅为浇注、热压成型时间的几十分之一至几百分之一,坯件的强度高,可自动化生产,生产过程中的管理和控制也很方便,适宜大批量生产。
Sialon陶瓷注射成型与脱脂工艺的研究的开题报告
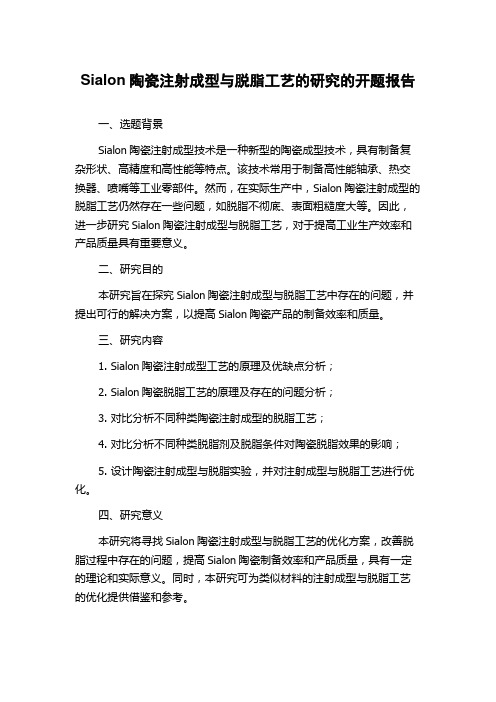
Sialon陶瓷注射成型与脱脂工艺的研究的开题报告
一、选题背景
Sialon陶瓷注射成型技术是一种新型的陶瓷成型技术,具有制备复杂形状、高精度和高性能等特点。
该技术常用于制备高性能轴承、热交换器、喷嘴等工业零部件。
然而,在实际生产中,Sialon陶瓷注射成型的脱脂工艺仍然存在一些问题,如脱脂不彻底、表面粗糙度大等。
因此,进一步研究Sialon陶瓷注射成型与脱脂工艺,对于提高工业生产效率和产品质量具有重要意义。
二、研究目的
本研究旨在探究Sialon陶瓷注射成型与脱脂工艺中存在的问题,并提出可行的解决方案,以提高Sialon陶瓷产品的制备效率和质量。
三、研究内容
1. Sialon陶瓷注射成型工艺的原理及优缺点分析;
2. Sialon陶瓷脱脂工艺的原理及存在的问题分析;
3. 对比分析不同种类陶瓷注射成型的脱脂工艺;
4. 对比分析不同种类脱脂剂及脱脂条件对陶瓷脱脂效果的影响;
5. 设计陶瓷注射成型与脱脂实验,并对注射成型与脱脂工艺进行优化。
四、研究意义
本研究将寻找Sialon陶瓷注射成型与脱脂工艺的优化方案,改善脱脂过程中存在的问题,提高Sialon陶瓷制备效率和产品质量,具有一定的理论和实际意义。
同时,本研究可为类似材料的注射成型与脱脂工艺的优化提供借鉴和参考。
陶瓷注射成型技术
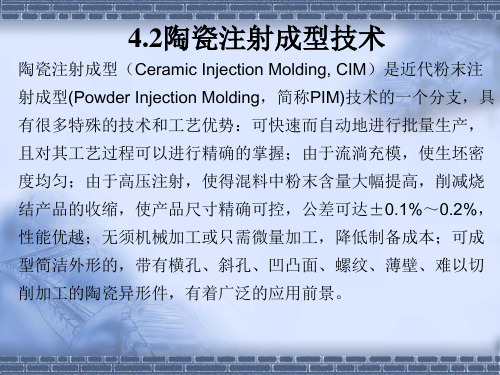
▪ 练泥时间:时间过短则练泥混合效果不好,时间过长则练泥混合效率不高
1) 粉末应专门配制,以求高的极限填充密度和低的成本; 2) 2) 粉末不结块团聚; 3) 3) 粉末外形主要为球形; 4) 4) 粉末间有足够的摩擦力以避开粘结剂脱出后坯件变
形或塌陷,在大多数情况下,自然坡度角应大于55°; 5) 5) 为利于快速烧结,应具有小的平均粒度,一般要
求小于1μm; 6) 6) 粉末本身致密,无内孔隙; 7) 7) 粉末的表面清洁,不会与粘结剂发生化学反应。
立式注射成型机
注射成型机构组成
▪ 可塑化机构(注射机构) ▪ 合模机构(包括模具) ▪ 油压机构 ▪ 电气掌握机构
注射成型模具
注射成型制备氧化锆坯体
注射成型制备氧化锆坯体
注射成型过程中缺陷的掌握
▪ 在注射成型过程中缺陷的掌握基本可从两个方面考 虑:一方面是成型温度、压力和时间三者关系设定; 另一方面是填充时喂料在模腔中的流淌。由于CIM 产品大多数是外形简洁、精度要求高的小尺寸零件, 混料在模腔的流淌就牵涉到模具设计问题,包括进 料口位置、流道的长度、排气孔的位置等,都需对 混料流淌性质、模腔内温度和残余应力分布等参数 有清楚了解。现行计算机充模过程动态模拟,正为 注射成型这一步供应理论指导。
孔洞缺陷
▪ 孔洞,指在生坯的横截面上可以发现的孔隙。 有的是一个近圆形的小孔,有的就进展为几 乎贯穿生坯坯体的中心通孔,这是常见的缺 陷.
陶瓷粉末注射成型技术

陶瓷粉末注射成型技术哎,你听说过陶瓷粉末注射成型技术吗?这玩意儿可真是高科技啊,我最近在研究这个,感觉自己都快成半个专家了。
你知道吗,这技术就是把陶瓷粉末和有机粘结剂混合在一起,然后注射到模具里成型。
听起来简单,但里面的门道可多了去了。
我记得有一次,我和老李在实验室里捣鼓这个,他一边搅拌着那些粉末,一边嘴里念叨着:“这玩意儿要是弄不好,可就全废了。
”我看着他那副认真的样子,忍不住笑出声来:“老李,你这架势,不知道的还以为你在炼丹呢!”他瞪了我一眼,说:“你小子别笑,这可比炼丹难多了。
”那天我们试了好几次,每次出来的成品都不太理想。
要么是密度不够,要么是表面有瑕疵。
老李急得直挠头,我看着他那副模样,心里也跟着着急。
后来我们决定换个思路,调整了一下粘结剂的比例,结果还真成了!看着那件完美的陶瓷制品从模具里取出来,我和老李都乐坏了,差点没抱在一起庆祝。
这技术虽然复杂,但做出来的东西可真是漂亮。
我记得有一次,我们用这技术做了一批陶瓷饰品,拿到市场上卖,结果一下子就被抢光了。
那些顾客都说,这东西既精致又耐用,比那些普通的陶瓷制品强多了。
我听了心里那个美啊,感觉自己这几个月的辛苦没白费。
不过,这技术也有它的局限性。
比如,对材料的要求特别高,稍微有点杂质就会影响成品的质量。
还有,成型后的脱脂和烧结过程也很关键,稍有不慎就可能前功尽弃。
所以,每次做实验的时候,我都特别小心,生怕出什么差错。
有一次,我和老李在实验室里忙活了一整天,结果还是没成功。
我累得瘫坐在椅子上,老李却还在那儿琢磨。
我看着他那副认真的样子,心里突然有种说不出的感动。
这老李,平时看着大大咧咧的,但做起事来还真是一丝不苟。
后来,我们终于找到了问题的关键,调整了一下工艺流程,结果一下子就成功了。
那天晚上,我和老李一起去喝了顿酒,庆祝我们的胜利。
酒桌上,老李拍着我的肩膀说:“小子,咱们这回可算是摸到门道了,以后可得好好干,别辜负了这门技术。
”我听了,心里暖洋洋的,感觉自己肩上的担子更重了。
陶瓷注射成型技术教学课件ppt
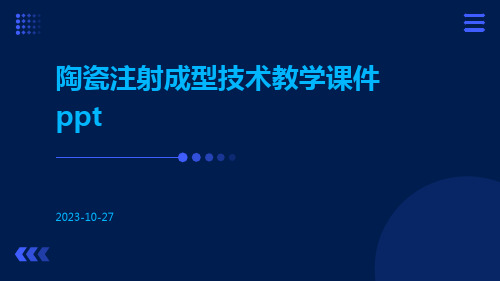
陶瓷注射成型技术的优缺点及与其他成型技术的比较 最新研究进展和未来发展趋势
02
陶瓷注射成型技术概述
陶瓷注射成型技术的定义
陶瓷注射成型技术是一种将陶瓷粉末、粘结剂、增塑剂等原 料混合,通过注射机注入模具,经干燥、烧结后获得致密陶 瓷成品的工艺方法。
陶瓷注射成型技术结合了塑料注射成型技术和传统陶瓷成型 技术的优点,具有成型复杂形状、高精度、高一致性等优势 。
注射机
将混合好的原料注射到模具中 ,形成所需形状的坯体。
模具
用于确定坯体的形状和尺寸, 通常由金属或陶瓷制成。
压机
用于将注射好的坯体进行压缩 ,以提高其密度和强度。
烧结设备
烧结炉
用于将坯体进行高温烧结,使其成为具有足够强 度的成品。
烧结助剂
为了促进烧结过程的进行,通常需要添加一些烧 结助剂。
冷却装置
高技术陶瓷领域
如电子、通讯、能源、环保等 领域的零部件制造。
精密陶瓷领域
如光学、机械、航空航天等领域 的零部件制造。
功能陶瓷领域
如压电、热敏、磁性等领域的电子 元器件制造。
03
陶瓷注射成型技术工艺流程
原料制备
原料储存
配料计算
保证原料的化学性质稳定,避免吸潮、氧化 等。
根据所需制备的陶瓷部件的尺寸和性能要求 ,计算所需原料的种类和数量。
球磨混合
干燥与除气
将原料加入球磨机中,加入适量的水或其他 溶剂,混合均匀,以保证原料的分散性。
通过干燥和除气处理,去除原料中的水分和 气泡,保证注射成型的质量。
模具设计
01
02
03
模具材料选择
根据陶瓷部件的形状和尺 寸要求,选择合适的模具 材料,如金属、塑料等。
陶瓷高压注浆成型工艺

陶瓷高压注浆成型工艺
陶瓷高压注浆成型工艺是一种将陶瓷粉末和粘合剂混合后,通过高压
注射机将混合物注入模具中进行成型的工艺。
具体工艺流程如下:
1.准备原料:将陶瓷粉末和粘合剂按一定比例混合。
2.注浆:将混合物倒入高压注射机中,通过高压将混合物注入模具中。
在注入过程中,需要控制注入速度和压力,以保证成型品的质量。
3.固化:注浆完成后,待陶瓷材料固化后,即可将成型品取出。
4.烧结:成型品经过固化后需要进行烧结,以使其获得更高的密度和
硬度。
5.加工处理:烧结后的陶瓷成型品需要进行加工处理,如磨光、抛光等,以使其表面光滑。
陶瓷高压注浆成型工艺具有成品的尺寸精度高、表面光滑、强度高、
耐磨性好等优点,广泛应用于电子、机械、化工等领域的制造。
金属、陶瓷粉末注射成型工艺简介

金属、陶瓷粉末注射成型工艺简介:金属、陶瓷粉末注射成型工艺技术是一种将粉末冶金工艺、粉末陶瓷工艺与塑料注射成型工艺相结合的新型制造工艺技术。
该工艺技术适合大批量生产小型、精密、复杂及具有特殊性能要求的金属陶瓷零件的制造。
该工艺的基本过程是:将微细的金属或陶瓷粉末与有机粘结剂均匀混合成为具有流变性的物料,采用先进的注射机注入具有零件形状的模腔形成坯件,新技术脱除粘结剂并经烧结,使其高度致密成为制品,必要时还可以进行后处理。
金属、陶瓷粉末注射成型工艺技术是近年来世界粉末冶金领域发展最快的高新技术。
该工艺技术的研究起始于70年代末,由于它适用性强、市场广阔,而且潜力巨大,所以一出现,便受到普遍重视,发展非常迅速。
美国、日本和西欧等发达国家率先形成产业规模。
1、粉末注射成型工艺特点:1)零部件几何形状的自由度高,制件各部分密度均匀、尺寸精度高,适于制造几何形状复杂、精密及具有特殊要求的小型零件(0.05g-200g);2)合金化灵活性好,对于过硬、过脆、难以切削的材料或原料铸造时有偏析或污染的零件,可降低制造成本;3)产品质量稳定、性能可靠,制品的相对密宽可达92-98%,可进行渗碳、淬火、回火等处理;4)加工零件的典型公差为±0.05mm;5)工艺流程短、生产效率高,易于实现大批量、规模化生产;2、粉末注射成型适用的材料:主要有Fe合金、Fe-Ni合金、不锈钢、Kovar合金、W合金、钛合金、Stellite Si-Fe合金、Hastelloy 合金、硬质合金、永磁合金及氧化铝、氮化硅、氧化锆等陶瓷材料。
3、粉末注射成型技术的应用领域:计算机及其辅助设施:如打印机零件、磁头、磁芯、撞针轴销、驱动零件;工具:如钻头、刀头、喷丸咀、枪钻、螺旋铣刀、冲头、套筒、扳手、电工工具、手工工具等;家用器具:如表壳、表链、电动牙刷、剪刀、风扇、高尔夫球头、珠宝链环、圆珠笔卡箍、照相机用等零件;医疗机械用零件:如牙矫形架、剪刀、镊子;军用零件:导弹尾翼、枪支零件、弹头、药型罩、引信用零件;电气用零件:微型马达、电子零件、传感器件;机械用零件:如松棉机、纺织机、卷边机、办公机械等;。
陶瓷的注射成型技术.

陶瓷的注射成型技朮随着现代陶瓷越来越多地被应用在先进热机组件上,注射成型以其适于大批量生产复杂形状陶瓷制品而倍受重视。
现代陶瓷在高温强度和耐磨性等方面具有优异的性能,但其硬度很大,采用机械加工成本极高,而采用注射成型技朮,由于坯体的成型形状接近制品的最终形状,使得这一问题得到了解决。
尽管许多工艺都可用来制造陶瓷,但对于高尺寸精度、复杂形状陶瓷制品的大批量生产,仅可通过粉浆浇注和注射成型来实现,而后者更快。
陶瓷的注射成型技朮有着诸多优点,用它制备复杂形状陶瓷组件,不仅产品尺寸精度高、表面条件好,而且省去了后加工操作,降低了生产成本,缩短了生产周期,还具有自动化程度高,适合于大规模生产的特点。
该工艺一般包括下列步骤:陶瓷粉的选取﹔粘结剂的选取﹔陶瓷粉与粘结剂的均匀混合﹔注射成型﹔脱脂(脱粘结剂)﹔烧结。
其中,脱脂是成功的关键。
1原料1.1陶瓷粉的选取陶瓷粉的特性如颗粒形貌、粒度分布、平均粒径、比表面以及表面自由能等对整个工艺的其它环节都有很大的影响﹝6~8﹞。
理想的陶瓷粉应该具有如下特点:(1)粒度分布宽,平均粒径小,适于快速烧结。
(2)以球形(或等轴)为主,填充密度高,有足够的粒间摩擦,以避免变形。
(3)表面洁净,无团聚。
(4)无毒害,低成本。
1.2粘结剂的选取粘结剂能使粉末填充成预期形状,它对整个工艺有重要的影响。
理想的粘结剂应具备下列特点:(1)在成型温度下纯粘结剂的粘度在0.1Pa.s以下,流动时不发生与粉体的分离,冷却后有足够的强度和硬度。
(2)为惰性物质,与粉体无反应。
(3)在成型和混合温度以上才分解,分解产物无毒性、腐蚀性且残余灰分少。
(4)膨胀系数低,由热膨胀或结晶引起的残余应力低。
(5)符合环保要求,价廉,安全﹔不吸湿,无易挥发组分,贮藏寿命长。
目前使用的大多数粘结剂可分为3类:蜡基或油基粘结剂、水基粘结剂和固体聚合物溶液。
表1列出了各类粘结剂的典型成分。
表1陶瓷注射成型用粘结剂的成分蜡基粘结剂通常含3、4种组分。
- 1、下载文档前请自行甄别文档内容的完整性,平台不提供额外的编辑、内容补充、找答案等附加服务。
- 2、"仅部分预览"的文档,不可在线预览部分如存在完整性等问题,可反馈申请退款(可完整预览的文档不适用该条件!)。
- 3、如文档侵犯您的权益,请联系客服反馈,我们会尽快为您处理(人工客服工作时间:9:00-18:30)。
热塑性
PW+PP+SA
热塑性
PW+SA
热塑性
CIM混料制备
▪ 混料是粉末和粘结剂的混合物。在整个注射成型的工艺中, 粉末和聚合物粘结剂混合物的制备是最重要的步骤之一。工 艺要求混料具有良好的均匀性、良好的流变特性,以及好的 脱脂特征。只有这三个方面都照顾到的粉末注射系统才是一 个成功的体系。
▪ 对选定的混合技术,起主要作用的是混合速率、温度和时间。 但如果混合速度和温度太低,无论多长时间混料也无法均匀, 因混料将在不均匀的水平上达到平衡,即存在一临界剪切状 态。
CIM中几种常见的粘结剂组成
近年来国际上各种陶瓷粉末注射成型中经常用到的较典型的粘结剂,从表
中可以看出,CIM中用粘结剂体系还主要属于热塑性多组分体系。
粉末组成
Si3N4
ZrO2 Al2O3 SiC/Si3N4
粘结剂组成
体系
PW+EVA+PP+PE+ 热塑性 SA
PW+PP+SA
PW+EVA+SA
混料练泥过程影响因素
▪ 粉末干燥:干燥的目的是为了去除粉末里的水分,否则由于水分包覆粉末, 降低了粉末同粘结剂之间的润湿性,使混合变得困难。另外掺入的水分会 在高温练泥过程中汽化,造成喂料中夹杂水汽,直接影响喂料的质量。一 般粉末要在200℃条件下干燥2小时。
▪ 粉末和粘结剂的粗混:粉末和粘结剂不能直接在练泥机上混合挤出,需先 在恒温加热皿中进行粗混,使其粘结成一体,并能剪切制粒。
注射成型粘结剂体系
▪ 注射成型中的粘结剂有两个基本的功能。首先在注 射成型阶段能够和粉末均匀混合,加热后能够使得 粉末具有良好的流动性;其次,粘结剂能够在注射 成型后和脱脂期间起到维持坯体形状的作用。可以 说,粘结剂是粉末注射成型技术中的核心和关键, 每次注射成型工艺的提高和突破都伴随着新粘结体 系的诞生。在CIM中,由于粉末粒度比金属粉末注 射成型中的细小,粉末本身的流动性差,粉末和粘 结剂混合后粉末之间的间隙极小,造成脱脂困难, 这就对粘结剂提出了更苛刻的要求。因此,作为陶 瓷注射成型粘结剂,必须具备以下条件:
▪ PIM的流变学问题主要就是混料粘度的评价表征问题。PIM 工艺涉及到的物料体系和状态,可能是纯粘性的,也可能是 粘弹性、粘塑性的,故变形的流动过程很复杂,可能既有瞬 时变形,也有对时间依存关系的变形(蠕变)。
CIM混料练泥机
练泥机的螺杆、料筒和料斗都采用镀铬不锈钢以增强耐磨性、 增加光洁度,防止异物的掺杂;料筒的长度要能够满足喂料 的预热,但不宜太长,以减少摩擦阻力并减少死料,增加原 料的利用率。
立式注射成型机
注射成型机构组成
▪ 可塑化机构(注射机构) ▪ 合模机构(包括模具) ▪ 油压机构 ▪ 电气控制机构
注射成型模具
注射成型制备氧化锆坯体
注射成型制备氧化锆坯体
注射成型过程中缺陷的控制
▪ 在注射成型过程中缺陷的控制基本可从两个方面考 虑:一方面是成型温度、压力和时间三者关系设定; 另一方面是填充时喂料在模腔中的流动。因为CIM 产品大多数是形状复杂、精度要求高的小尺寸零件, 混料在模腔的流动就牵涉到模具设计问题,包括进 料口位置、流道的长度、排气孔的位置等,都需对 混料流动性质、模腔内温度和残余应力分布等参数 有清楚了解。现行计算机充模过程动态模拟,正为 注射成型这一步提供理论指导。
▪ 练泥机转速:练泥时因螺杆转速太快而引起高的剪切力会导致喂料中陶瓷 粉末对挤出机料筒的磨损而引入杂质,转速太慢则不能产生适当的剪切力 而造成粘结剂粘度太低,使得混炼均匀变得很困难,从而引发后续的缺陷。 故需要将转速同喂料匹配,使喂料在粘度适当的条件下进行混炼。
▪ 练泥时间:时间过短则练泥混合效果不好,时间过长则练泥混合效率不高
▪ (3)物料流动分析对制品设计、模具设计有 十分重要的意义。
注射成型
▪ 注射成型的目的是获得所需形状的无缺陷、颗粒均 匀排布的CIM成型坯体。制备好的混料一般可在普 通塑料注射成型机上注射成型,也可以在专用粉末 注射机上注射成型。成型工艺参数一般包括注射温 度、注射压力、注射速度、保压压力、保压冷却时 间和模温等。工艺参数若控制不当则容易产生各种 缺陷。注射缺陷不能在后续工艺中消除,所以此过 程要严格控制,这对提高产品成品率和材料利用率 非常关键。
陶瓷注射成型技术
陶瓷部件的注射成型是利用塑性材料在压
力下的注射成型原理的一种成型原理。在
成型过程中需要将热塑性材料混合在一起。
陶瓷注射成型工艺主要有三个环节构成: 第一:热塑性材料与陶瓷粉体混合成热熔体,然后注射进入相对 冷的模具中。 第二:这种混合热熔体在模具中冷凝固化。 第三:成型后的坯体制品被顶出而脱模。
1) 粉末应专门配制,以求高的极限填充密度和低的成本; 2) 2) 粉末不结块团聚; 3) 3) 粉末形状主要为球形; 4) 4) 粉末间有足够的摩擦力以避免粘结剂脱出后坯件变
形或塌陷,在大多数情况下,自然坡度角应大于55°; 5) 5) 为利于快速烧结,应具有小的平均粒度,一般要
求小于1μm; 6) 6) 粉末本身致密,无内孔隙; 7) 7) 粉末的表面清洁,不会与粘结剂发生化学反应。
▪ 练泥温度: 必须选择合适的练泥温度,这是因为温度过低,喂料的粘度急 剧增大,导致喂料和挤出机之间的磨损而带入杂质,此外还可能导致在喂 料中夹入气体,带入注射成型生坯中产生孔隙。温度过高,会出现冒烟现 象,而且喂料表面易出现褶皱和小裂纹,因为温度太高会引起粘结剂中低 分子量成分的挥发,恶化粘结剂性能并导致粉末同粘结剂的分离。
陶瓷注射成型粘结剂必须具备的条件
(1)好的流动特性。对注射成型粘度要适中,粘度太高,粉料不能在粘 结剂中有效分散,不仅混练困难,而且很难得到混合均匀的坯料,容易产 生成型缺陷;粘度太低,会造成陶瓷粉体和粘结剂的分层。另外粘度不能 随温度的波动太大,否则会产生缺陷。 (2)粘结剂必须能很好地润湿粉体,并对粉体有效好的粘附作用。通常 为了改善粘结剂的润湿性能,要加入一些表面活性物质,减少混合物的粘 度,增加其流动性。同时,粘结剂通过润湿颗粒以产生毛细管力吸附颗粒, 保持坯体不变形。为了保证坯料的稳定性,粉体相对于粘结剂应是惰性的。 (3)粘结剂由多组份有机物组成。单一有机粘结剂很难满足流动性要求, 且多组份中的某一组份被脱脂移出后,形成开口气孔,有利于剩余的粘结 剂的排除。实践证明,多组份比单一组成粘结剂的脱脂速度要快得多缺陷 少得多。当然多组份粘结剂的有机聚合物之间是相容的。 (4)粘结剂具有较高的导热性和较低的热膨胀系数。这样不仅避免因热 应力而产生缺陷,且可以减少坯体所受热冲击,减少缺陷。 (5)此外,粘结剂还必须具有无毒害,无污染,不挥发,不吸潮,循环 加热性能不变化等。
孔洞缺陷
▪ 孔洞,指在生坯的横截面上可以发现的孔隙。 有的是一个近圆形的小孔,有的就发展为几 乎贯穿生坯坯体的中心通孔,这是常见的缺 陷.
▪ 注射成型样品不同部位产生的气孔的原因也 不一样,一般中部产生的气孔较小,原因可 能是喂料本身混合不充分并夹有气体、注射 温度太高造成粉末同粘结剂分离。相应可通 过调整喂料质量,降低模温和注射温度等措 施消除。而底部产生的气孔较大,有的甚至 是周身或半周身通孔。产生这样孔洞的原因 主要是注射时底部排气不充分而使样品夹入 气体。因为样品上部壁薄而底部壁厚,注射 过程中流动性喂料在注射压力下从上向下流 动冲模,当喂料流体到达底部时,空腔截面 面积突然变大,喂料会沿内侧经样品最底面 渐进冲模,这样一来最后被冲模的地方不是 空腔最底面,而是薄壁和厚壁的接合处。因 此模具上开在底面的排气孔并不能充分排气, 使得气体聚集,形成比较大的孔洞。
陶瓷粉末注射成型技术概况
▪ 粉末注射成型源于20世纪20年代的一种热压铸成型技术,当时已用于生 产汽车火花塞等产品。
▪ 20世纪50年代,用环氧树脂作粘结剂试制了大量的硬质合金、难熔金属、 陶瓷等,预示着此技术在应用中的地位。但因理论欠缺,加之制粉、成 型和烧结等技术存在一系列不足,离应用的距离还比较远。
各种粘结剂体系的优缺点比较
体系 主要组元 优点
缺点
热塑性 石蜡、聚乙 适用性好、流动性好、易 脱脂时间长、工 体系 烯、聚丙烯 于成型、粉末装载量高、 艺较复杂
注射过程易控制
热固性 环氧树脂、 注射坯的强度高、脱脂速 注射过程不易控
体系 苯酚树脂 度快
制、适用性差、
缺陷多
凝胶体 甲基纤维素、有机物少、脱脂速度快
每年垄断了全球数亿美元的市场 ▪ 美国已实现氧化锆理发推剪的生产和发动机中氮化硅零部件
的应用等 ▪ 在国内中南工业大学粉末冶金国家重点实验室开发出精密双
螺旋混练机陶瓷内衬和具有双螺纹的陶瓷喷嘴等 ;而华中科 技大学材料学院应用CIM技术成功开发出氧化锆氧传感器.
陶瓷粉末注射成型基本工艺流程图
注射成型技术对陶瓷粉末的要求
注射过程中的缺陷分析
▪ 注射成型过程中由于工艺参数控制不当,或 者是喂料本身缺陷,以及模具设计不合理等 因素,容易造成诸如欠注、断裂、孔洞、变 形、毛边等各种缺陷。结合具体过程,对常 见的注射缺陷进行分析,并加以控制,以提 高生产率和喂料的利用率。
欠注缺陷
▪ 就是指喂料在充模过程中不 能充满整个模腔,如图所示。 一般在刚开始注射时产生, 可能是由喂料温度或模具温 度过低、加料量不足、喂料 粘度过大等因素引起的。通 过增加预塑时间升高喂料温 度、升高模具温度、加大进 料量、升高注射温度降低喂 料粘度等措施可以消除此缺 陷。
断裂缺陷
▪ 断裂,如图所示。一般发生 在脱模中,往往是脆断。主 要是因为模具温度太低,或 者是保压和冷却时间过长, 使得坯体温度大幅下降,引 起的收缩太大使坯体紧紧箍 在下部凸模上,在模具顶出 机构的强烈冲击下,很容易 引起脆断。通过适当升高模 温以及减少保压和冷却时间, 在脱模过程中可以避免断裂。
▪ 到20世纪80年代,硬质合金、陶瓷领域基础研究的发展和突破,如超细 粉制备、先进陶瓷增韧理论和技术的发展,使该工艺制备的材料性能较 50年代有很大的提高,促使PIM成为比较成熟的复杂形状制品的制备成 型技术。