注射成型氧化铝陶瓷工艺研究
95%氧化铝陶瓷产品生产基本工艺流程
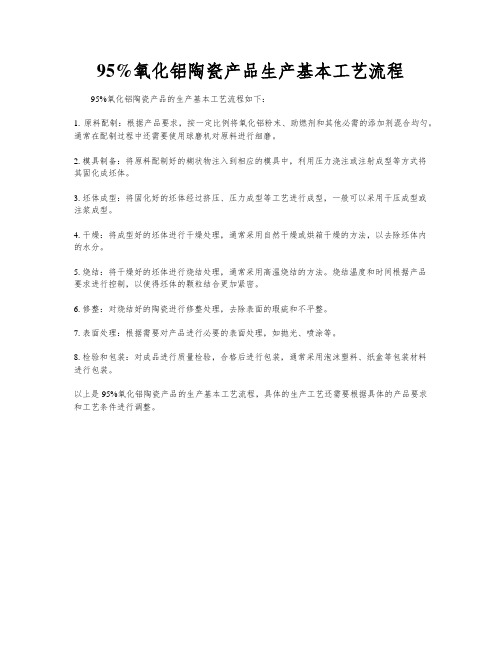
95%氧化铝陶瓷产品生产基本工艺流程
95%氧化铝陶瓷产品的生产基本工艺流程如下:
1. 原料配制:根据产品要求,按一定比例将氧化铝粉末、助燃剂和其他必需的添加剂混合均匀。
通常在配制过程中还需要使用球磨机对原料进行细磨。
2. 模具制备:将原料配制好的糊状物注入到相应的模具中,利用压力浇注或注射成型等方式将
其固化成坯体。
3. 坯体成型:将固化好的坯体经过挤压、压力成型等工艺进行成型,一般可以采用干压成型或
注浆成型。
4. 干燥:将成型好的坯体进行干燥处理,通常采用自然干燥或烘箱干燥的方法,以去除坯体内
的水分。
5. 烧结:将干燥好的坯体进行烧结处理,通常采用高温烧结的方法。
烧结温度和时间根据产品
要求进行控制,以使得坯体的颗粒结合更加紧密。
6. 修整:对烧结好的陶瓷进行修整处理,去除表面的瑕疵和不平整。
7. 表面处理:根据需要对产品进行必要的表面处理,如抛光、喷涂等。
8. 检验和包装:对成品进行质量检验,合格后进行包装,通常采用泡沫塑料、纸盒等包装材料
进行包装。
以上是95%氧化铝陶瓷产品的生产基本工艺流程,具体的生产工艺还需要根据具体的产品要求和工艺条件进行调整。
凝胶注模新工艺制备超轻质氧化铝陶瓷

凝胶注模新工艺制备超轻质氧化铝陶瓷
近年来,随着科技的发展,超轻质氧化铝陶瓷作为一种高性能陶瓷,已经在航空航天、军事等领域得到越发广泛的应用,而难以通过传统的注模法制备高性能的超轻质氧化铝陶瓷的技术制约了它的更大发展空间。
为此,立足于新型材料制备技术,我们提出了一种基于凝胶注模法制备超轻质氧化铝陶瓷的新技术,以缓解材料使用中的种种技术难题:
一、原料准备:按照新工艺制备超轻质氧化铝陶瓷,先将超轻质氧化铝经粉碎加工得到粉末状态,然后加入内衬机制硅凝胶中搅拌,待搅拌均匀后,再将添加好的凝胶倒入模具内,放置制备工艺环境中待固化;
二、凝胶成型:利用凝胶的高粘度,将其倒入模具中,经过固化,在模的内表面形成自然形状模版;
三、烧结后处理:将凝胶固化模型烘烤于高温烧结,烧结后形成实物模型,然后将其经过精加工处理完成最终步骤;
四、性能检测:经过精密加工处理后,可以通过机械性能检测、折射率测试和密度/硬度测试等……来检验超轻质氧化铝陶瓷的整体性能;
本新制备技术可以大大改善传统技术制备超轻质氧化铝陶瓷的缺陷,具有制备工艺简单、性能优异的特点,有助于更好的应用工艺,使超轻质氧化铝陶瓷取得更好的发展空间。
凝胶注模成型工艺制备高强度的氧化铝陶瓷

凝胶注模成型工艺制备高强度的氧化铝陶瓷学院:装备制造学院专业:无机非金属材料工程姓名:张大勇学号:1033020116摘要:本文以氧化铝陶瓷为例,研究探讨了凝胶注模成型工艺中制备低粘度、高固相含量浓悬浮体的关键技术;讨论分散剂因素对粘度的影响;不同固相含量对坯体的强度的影响。
关键词:凝胶注模;氧化铝;成型工艺1前言陶瓷材料成型工艺是制备复杂形状部件的关键环节,其对降低陶瓷零件生产成本、提高陶瓷材料性能及其可靠性起重要作用。
随着航天、航空、机械、化工等行业的发展,对陶瓷材料的性能要求越来越高。
凝胶注模成型技术是90年代初美国橡树岭国家重点实验室Mark A,Janney教授等人提出的[1]。
它首次将传统陶瓷工艺和聚合物化学有机结合起来,开创了在陶瓷成形工艺中利用高分子单体聚合进行成形的技术[2]。
与传统的工艺相比有其独特的优越性:1)可使用于复杂的部件成型2)坯体的强度高,生坯即可加工成一定得形状。
3)坯体比较均匀。
其工艺过程如图1所示:图1 凝胶注模成型工艺过程2实验2.1原料及反应体系的选择α- Al2O3粉提纯度为99.9%,平均粒径1.4µm,丙烯酰胺(AM)为有机单体,N-N亚甲基双丙烯酰胺(MBAM)为交联剂,过硫酸胺(APS)为引发剂;聚丙稀酸胺(PMAA-NH4)为分散剂;四甲基乙二胺(TEMED);分析纯氨水来调节pH。
本实验选择丙烯酰胺为有机单体,亚甲基双丙烯酰胺为交联剂,两者在水中搅拌后均可溶。
凝胶注模成型工艺要求单体在一定条件下形成交联大分子,形成聚合物的反应类型有聚合和缩聚两种形式,由于缩聚反应有小分子如水分子产生,而本实验要求原位聚合形成有一定形状和强度的固状坯体,要求尽量减少水份,因此采用聚合反应。
本实验选择引发剂APS和催化剂TEMED 的催化体系,可通过控制温度、APS与TEMED的量、分散剂等有效控制反应速度。
2.2反应步骤1) 将有机单体AM、交联剂MBAM 以AM:MBAM=20:1比例溶于水,再加入一定量分散剂PMAA-NH4 配置成溶液;2) 在溶液中加入高固相含量粉料,将其放置行星球磨机中球磨至浆料具备一定流动性;3) 加入引发剂过硫酸胺搅拌均匀再加催化剂四甲基乙二胺搅拌后注入模具中。
简述氧化铝陶瓷的生产工艺

简述氧化铝陶瓷的生产工艺氧化铝陶瓷是一种常见的陶瓷材料,其生产工艺主要包括选材、制备、成型、烧结和加工等环节。
首先,选材是氧化铝陶瓷生产的第一步。
氧化铝是一种常见的无机物,可以通过矿石提取或通过化学反应合成。
选材的关键是保证原料的纯度和稳定性,以确保最终产品的质量。
此外,还可以添加一些其他化学物质,如增强材料、稳定剂和颜料等,以提高氧化铝陶瓷的性能和外观。
其次,制备是指对原料进行预处理。
通常,原料会经过研磨和混合等处理,以使其颗粒尺寸均一,并达到所需的粒度。
可以使用球磨机、振动磨机或气流磨机等设备进行研磨,然后通过混合设备将不同的原料混合均匀,以确保最终产品的化学成分相对稳定。
接下来,成型是氧化铝陶瓷生产的关键步骤之一。
通常有多种成型方法可选择,如压制、注塑和注浆等。
其中,压制是最常用的一种方法,利用模具对原料进行压制,使其具有所需的形状和尺寸。
注塑和注浆是将原料放入注塑机或注浆机中,通过模具或挤出机将原料注射成型。
无论采用何种方法,都需要考虑原料的流动性和形状保持性,以确保成型的精度和一致性。
烧结是氧化铝陶瓷生产中的关键步骤之一。
烧结是通过高温处理,使成型体结合成坚固的陶瓷材料。
通常,高纯度的氧化铝陶瓷需要经过两次烧结过程:预烧和终烧。
预烧是在较低温度下使成型体变得致密,去除一部分残余物质和水分。
终烧是在更高温度下进行,以使陶瓷材料达到所需的密度和机械强度。
烧结条件的选择和控制对最终产品的性能和质量至关重要。
最后,加工是氧化铝陶瓷生产中的最后一步。
加工通常包括切割、抛光、镂空和修整等过程,以使最终产品达到所需的形状和表面精度。
这些加工过程可以通过机械加工、激光加工和化学加工等方式进行。
加工的目的是提高氧化铝陶瓷的装配性能和外观质量。
总结起来,氧化铝陶瓷的生产工艺包括选材、制备、成型、烧结和加工等环节。
通过精确的控制和合理的操作,可以生产出具有优良性能和高质量的氧化铝陶瓷产品。
同时,不断改进工艺参数和技术手段,可以进一步提高氧化铝陶瓷的生产效率和陶瓷材料的性能,满足不同领域和应用对高性能陶瓷的需求。
纤维素纳米纤维在氧化铝陶瓷注浆成型中的应用研究

纤维素纳米纤维在氧化铝陶瓷注浆成型中的应用研究
纤维素纳米纤维在氧化铝陶瓷注浆成型中的应用研究主要包括以下几个方面:
1. 纤维素纳米纤维作为增稠剂:纤维素纳米纤维具有很高的比表面积和极细的纤维直径,可以在注浆过程中作为增稠剂使用。
由于纤维素纳米纤维与注浆材料之间存在一定的黏附力,可以有效地增加注浆材料的黏度,提高其流变性能,从而改善注浆成型的可加工性。
2. 纤维素纳米纤维作为模板支撑剂:纤维素纳米纤维可以通过自组装形成具有高度有序结构的纤维网状结构,这种结构可用作模板支撑剂。
在注浆过程中,注浆材料可以在纤维网状结构上自发排列,形成高度有序的结构,从而得到具有良好力学性能和高度有序的氧化铝陶瓷制品。
3. 纤维素纳米纤维作为增强剂:纤维素纳米纤维可以在注浆材料中作为增强剂使用。
由于纤维素纳米纤维具有较高的机械强度和柔韧性,可以有效地增强注浆材料的力学性能。
此外,纤维素纳米纤维还可以提高氧化铝陶瓷的断裂韧性,抗裂性和耐磨性等性能。
4. 纤维素纳米纤维作为分散剂:纤维素纳米纤维可以通过表面修饰或化学修饰来改善其与注浆材料的相容性。
通过添加纤维素纳米纤维分散剂,可有效地提高注浆材料的分散性,减少颗粒聚集,从而得到均匀、致密的注浆浆料。
综上所述,纤维素纳米纤维在氧化铝陶瓷注浆成型中具有广泛的应用前景,并为氧化铝陶瓷的制备提供了新的思路和方法。
然而,目前相关研究还处于起步阶段,需要进一步深入研究优化纤维素纳米纤维的制备方法和性能调控,以实现其在氧化铝陶瓷制备中的商业化应用。
氧化铝陶瓷制作及强化工艺
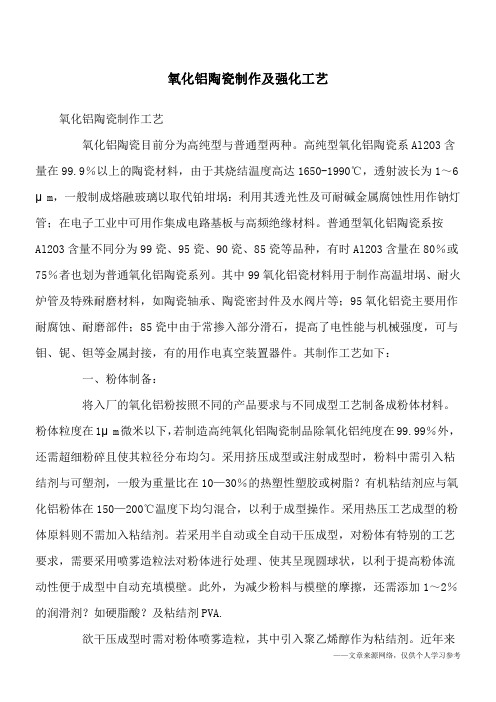
氧化铝陶瓷制作及强化工艺氧化铝陶瓷制作工艺氧化铝陶瓷目前分为高纯型与普通型两种。
高纯型氧化铝陶瓷系Al2O3含量在99.9%以上的陶瓷材料,由于其烧结温度高达1650-1990℃,透射波长为1~6μmAl2O380%或75%外,体原料则不需加入粘结剂。
若采用半自动或全自动干压成型,对粉体有特别的工艺要求,需要采用喷雾造粒法对粉体进行处理、使其呈现圆球状,以利于提高粉体流动性便于成型中自动充填模壁。
此外,为减少粉料与模壁的摩擦,还需添加1~2%的润滑剂?如硬脂酸?及粘结剂PVA.欲干压成型时需对粉体喷雾造粒,其中引入聚乙烯醇作为粘结剂。
近年来上海某研究所开发一种水溶性石蜡用作Al2O3喷雾造粒的粘结剂,在加热情况下有很好的流动性。
喷雾造粒后的粉体必须具备流动性好、密度松散,流动角摩擦温度小于30℃。
颗粒级配比理想等条件,以获得较大素坯密度。
二、成型方法:氧化铝陶瓷制品成型方法有干压、注浆、挤压、冷等静压、注射、流延、1mm,15~60μm、介于制备。
通常以水为熔剂介质,再加入解胶剂与粘结剂,充分研磨之后排气,然后倒注入石膏模内。
由于石膏模毛细管对水分的吸附,浆料遂固化在模内。
空心注浆时,在模壁吸附浆料达要求厚度时,还需将多余浆料倒出。
为减少坯体收缩量、应尽量使用高浓度浆料。
氧化铝陶瓷浆料中还需加入有机添加剂以使料浆颗粒表面形成双电层使料浆稳定悬浮不沉淀。
此外还需加入乙烯醇、甲基纤维素、海藻酸胺等粘结剂及聚丙烯胺、阿拉伯树胶等分散剂,目的均在于使浆料适宜注浆成型操作。
三、烧成技术:将颗粒状陶瓷坯体致密化并形成固体材料的技术方法叫烧结。
烧结即将坯体内颗粒间空洞排除,将少量气体及杂质有机物排除,使颗粒之间相互生长结合,中。
硬度较高,需用更硬的研磨抛光砖材料对其作精加工。
如SiC、B4C或金刚钻等。
通常采用由粗到细磨料逐级磨削,最终表面抛光。
一般可采用<1μm微米的Al2O3微粉或金刚钻膏进行研磨抛光。
此外激光加工及超声波加工研磨及抛光的方法亦可采用。
氧化铝陶瓷注凝成型的研究

氧化铝陶瓷注凝成型的研究作者:吴洋李文杰来源:《佛山陶瓷》2016年第06期摘要:本实验探究了氧化铝陶瓷注凝成型工艺,综合分析了分散剂和浆料的固相含量对氧化铝陶瓷浆料粘度的影响,实验证明:当分散剂的加入量为0.6%,浆料的固相含量为50%时,浆料适宜注浆,得到的陶瓷产品颗粒分布均匀,结构致密。
关键词:氧化铝;分散剂;固含量;注凝成型1 引言氧化铝陶瓷具有高硬度、耐腐蚀、耐磨损以及良好的机械性能而被广泛地运用到各行业中,但是传统的成型工艺如等静压成型、注浆成型在制造一些大尺寸、形状复杂的陶瓷制品时比较困难,生坯的强度低,不利于产品的后续加工。
热压铸成型虽然能够制备一些形状复杂的陶瓷类制品,但是这种成型工艺复杂,耗能也高,热压铸成型工艺中,要将石蜡等有机塑性剂与陶瓷粉料均匀混合,在排蜡的过程中,石蜡不完全燃烧、高温裂解的低碳低氢物质、反应不完全的碳等等造成了大量的空气污染,所需要能耗也巨大,这与国家制定的节能减排战略是相悖的。
因此,寻求新的成型工艺来制备高性能陶瓷势在必行。
注凝成型的出现[1-4]为解决这种问题提供了一种选择,该工艺是首先制备高浓度低粘度的浆料,之后注模,然后通过加入的引发剂和催化剂,控制一定的温度,引发有机单体聚合,使得浆料原位凝固成型,形成具有一定强度的三维网状结构的生坯,生坯经过脱模之后,干燥、排胶,然后烧结得到制品。
该技术创造性地将陶瓷工艺和聚合物有机化学结合在一起,开创了高分子聚合交联成型的先例。
其特点在于:1)工艺简单;2)素坯均匀性好,强度高易于加工;3)该工艺过程对模具无要求,坯体收缩小,适用于成型大尺寸,形状复杂的陶瓷制品;4)烧结后的陶瓷致密,均匀性好,性能优异,所加入的高分子在高温下热分解掉,不会残留杂质。
目前,这一工艺已运用于各种复杂陶瓷制品的研究工作,已开创出较多的陶瓷注凝成型体系,如丙烯酰胺体系,羟基甲基丙烯酰胺体系等等。
随着技术的不断完善,注凝成型[5-7]也会渐渐成为一种重要的陶瓷材料成型方法。
氧化铝陶瓷基片成型及加工工艺的研究——浓悬浮体的制备

图3 氧化铝悬浮液沉降体积 V与 p H值 的关系 从 图中可 以发现 , 料浆粘度随 p H值 的增 大在减小 , p H值约等于 9 时粘度 最小 , 随着 p 并 H值的进一步增大趋于缓慢增大 , 时料 浆处 于 此 比较均匀的分散状态 。 料浆的沉降体积随 p H值 的增大而减小 ,H值约 p 等于 9时最小 , 稳定性最好 。所 以, 料浆 粘度和沉降体积在 p H值 约为 90时最低 , . 即体系的分散性和稳定性很好 。 22球磨时间对料浆流动性 的影响 . 为 了提高料浆 的流动性 , 可借助机械球磨的方法 , 料浆的球磨 时间 是影响流动性 的一个主要因素。 球磨时 间对料浆粘度 的影响关系如图 4 所示( MA - N 4 P A- H 为分散剂其用量为 04 t 。 .w%)
1实 验 .
三
囊
胶冻成型技术路线如 图 1 所示 。 主要工艺 : 首先利用水 、 分散剂 、 有 机单体 、 交联 剂、 陶瓷粉体制 备浓悬浮体料 浆 ; 接着 加人引发剂 、 催化 剂、 除泡剂注模 并干燥切片 ; 最后烧结成型。 其中制备高 固相含量 , 分散 性和稳定性很好 的浓悬浮体料浆是浇注成型进 而得 到高性能氧化铝 陶 瓷基片的前提条件 。
图 l工 艺 流程 图
舶 5 60
1 原料与实验设备 . 1 本实验的主要 原料是 d A2 一 2 , 由 d A 块 粉碎 , 10 —I 0 AI 粉 0 —1 过 2 目筛 , 分得到 , 均粒径 2 m。实验设备主要包括 D 一 0 筛 平 T 10型光 电天 平 , M一1P行星式球磨机 , Q S 粘度计。 1 稳定料浆 的制备 . 2
科技信息
博士 ・ 专家论坛
萄化铝陶瓷基片成型及加工工 艺硇研究
- 1、下载文档前请自行甄别文档内容的完整性,平台不提供额外的编辑、内容补充、找答案等附加服务。
- 2、"仅部分预览"的文档,不可在线预览部分如存在完整性等问题,可反馈申请退款(可完整预览的文档不适用该条件!)。
- 3、如文档侵犯您的权益,请联系客服反馈,我们会尽快为您处理(人工客服工作时间:9:00-18:30)。
研究与开发 文章编号:1001—9643(2007)05—0014-05 注射成型氧化铝陶瓷工艺研究 雅菁,刘志锋,赵丹,周彩楼,辛颖,刘超 (天津城市建设学院, 天津 300384)
【摘要】:研究了氧化铝陶瓷注射成型工艺过程,包 括粘结剂的选择、粉末装载量的确定及热脱脂工艺的研究。 探讨了注射压力、注射温度和模具温度等注射成型工艺参 数对试样性能的影响,得到了一条优化的氯化铝注射成型 工艺路线。 【关键词】:氯化铝,注射成型,粘结利,睨脂
引言 陶瓷注射成型技术(Ceramics Injection Molding 简称CIM)类似于70年代发展起来的金属注射成型 (Metals Injection Molding简称MIM)技术,它们 均是粉末注射成型(Powders Injection Molding简称 PIM)技术的主要分支,均是在聚合物注射成型技术比较 成熟的基础上发展而来的,是当今国际上发展最快、应 用最广的陶瓷零部件精密制造技术l】 ]。其突出的优点包 括[3-4]:(1)成型过程机械化和自动化程度高;(2)可净近 成型各种复杂形状的陶瓷零部件,使烧结后的陶瓷产品无 需进行机加工或少加工,从而减少昂贵的陶瓷加工成本; (3)成型出的陶瓷产品具有极高的尺寸精度和表面光洁度。 陶瓷注射成型技术以其独特的优势已在高精度和高附加 值的新产品制造上显示出无比强大的生命力,解决丁,后 续机加工问题,成为精密陶瓷成型技术的一颗新星。 目前,氧化铝陶瓷以其独特的优势在高技术和尖端 工业,如做电子、核反应堆、磁流体发电、航天、人工 骨和人工关节等方面越来越得到广泛的应用。这些氧化 铝陶瓷和普通陶瓷在成分和制造工艺上都有着很大的差 别,特别是在成型技术方面,由于氧化铝陶瓷的硬度高, 难于切割加工,尤其对于形状复杂的氧化铝制品,如汽 车发动机中的增压器转子,骨骼、牙齿等生物陶瓷制品, 在成型烧结以后即为成品,无须再加工,而传统成型技 术(如干压、等静压等)后续机加工大,难以满足这一 苛刻要求。 陶瓷注射成型主要包括以下四个方面:配料及混炼、 注射成型、脱脂和烧结I4】。其中前三个是陶瓷注射成型工 艺所特有的。由于在陶瓷注射成型中陶瓷粉末细小且形 状不规则,其工艺参数的控制相比金属注射成型而言需 更为精细。除了烧结工序外,粘结剂、喂料混炼、注射 成型、脱脂等各道工序都与传统陶瓷粉末干压成型有着 很大的差异,研究了氧化铝陶瓷注射成型工艺过程及主
收稿日期 基金项目 作者蔺介
f4 f中国陶瓷l CHINA CERAMICS I 2007(43)第5期
要工艺参数的影响。 1 实验过程
1.1原料 氧化铝陶瓷粉(A1 O ,分析纯);液体石蜡(Pw, 化学纯);聚丙烯(PP,化学纯);硬脂酸(SA,化学纯)。 1.2实验过程 将称量好的PP加热到190℃左右,使其由白色粒 状变为无色的稠状物质;在加入SA,加热温度控制在 170℃左 待其溶解后冷却一段时间加入PW,继续加热, 温度控制在150。C左右,直至全部混合,呈白色粘稠状物 质。将A1,O,粉缓慢加入到上述粘结剂中,用搅拌机搅拌 均匀,每次加入粉末为整个总量的1/4左右;待充分混 合后,将混合料在烘箱中静置24h,同时保持一定的真空 度使混合料中的气体排出;充分陈腐后,将混合料在挤 出机中练泥造粒。最终将混合料制成长约3 5ram,直径 约2ram的条状,得到适合注射成型的粒状喂料。注射成 型在宁波海天集团生产的HTF86X2型注射成型机上完 成。采用热脱脂工艺对试样进行脱脂,最后将脱脂坯置 于硅钼棒高温电炉中,空气气氖中于1550 ̄C烧结成成品。 1.3测试与表征 用排水法测量样品的密度;喂料的差热一热重曲线 在LCT一2差热天平上完成;将试样切割成25ram×5ram X 2.5ram的试条,用三点弯曲法测抗弯强度。 2结果与讨论
2.1粘结剂的选取 在陶瓷注射成型中,粘结剂具有两个基本的功能: 首先,在注射成型阶段能够和粉末均匀混合,降低粉末 的粘度,使粉末具有良好的流动性,成为适合于注射成 型的喂料;其次,粘结剂能够在注射成型后和脱脂期间 起到维持坯体形状的作用,使产品在烧结前具有完整合 适的形状。陶瓷注射成型所用粘结剂的选择主要考虑以 下四点:(1)体系内的相容性;(2)注射悬浮体流变学 特性;(3)脱模性和生坯强度;(4)脱脂特性。根据这 些原则,粘结剂多选择热塑性多组元体系,即由流动性 好的低熔点组元和高分子聚合物组元组成。有机粘结剂 与陶瓷粉体混炼后的结合强度主要取决于热塑性高聚物, 脱脂特性亦可由耐热性好的高聚物调节,可塑性和润滑 剂则可改善体系流动性及脱模性能;表面活性剂具有综 合调节作用[5-7]。 目前,石蜡一聚烯烃粘结剂体系已广泛应用于科研
维普资讯 http://www.cqvip.com 2007年第5期 中国陶瓷 和生产实践。因为石蜡基粘结剂的流变性能好,注射工 艺范围宽。实验中选用石蜡即以软化温度点低、流动性 好的Pw作为主要填充物;高分子聚合物PP熔点较高, 可作为骨架材料以保证生坯具有足够的强度;以少量的 SA作为表面活性剂或润滑剂不仅可以在粘结剂和粉末 颗粒之间起桥梁作用,防止两相分离,保证混料的均匀, 而且可以在粉末颗粒之间、粉末颗粒与模壁之间起到润 滑的作用,从而达到预计的效果。 在陶瓷注射成型中聚合物粘结剂之间或是聚合物与 增塑剂之间的相容性都是必要的,若有机载体之间相容 性差,则不能有效的降低混合物的粘度,注射成型冷却 过程中有机物产生大量偏析以及粘结剂与模具分离,不 能获得组分均匀的成型坯体。 高分子物质共混的过程实际上是分子链问相互扩散 的过程,受到分子链问作用力的制约。内聚能密度(△ E/V)是分子链问作用力大小的量度,但由于高分子不 能汽化而无法直接测量内聚能密度,因而常用溶度参数d, 即内聚能密度的开方(△E/V) 来表示分子链问作用 力的大小,d值越接近,相容性越好,即△d越小,相容 性越好[Sl。 表1 粘结剂组分的溶度参数(单位:(J·cmI。) ) 粘结剂组分 l PP l PW l sA 鎏痊叁墼l垒l l : Q l 2: Q l 2:墨2 表l为所用粘结剂组分的溶度参数值,由表中数据 可知组元之间的溶度参数差为: PP与Pw之间溶度参数差为: △d.=8.10-7.80=0.30(J-C1T10) PP与SA之问溶度参数差为: △d =8.10-7.87=0.23(J·C1T1 ) Pw与SA之间溶度参数差为: △d,=7.87-7.80=0.07(J·C1TI ) : 根据相容性原则判断准则:△d<0.7相容性好,△ d>l不相容[81。可见,PP,Pw与SA之间相容性都非常好。 2.2喂料及粘结剂配方的确定 在A1 O 陶瓷注射成型过程中,为了确保粉末具有 良好的流动性,而且在脱脂期间能够维持坯体基本形状, 需在喂料里加入一定数量的粘结剂,通过实验发现粘结 剂含量一般在30wt%以上。表2给出了实验中典型的 A1 O 陶瓷注射成型用喂料的组分。 按照表2中的配方制备A1 O 陶瓷喂料,然后注射 样品(注射温度为l80℃、注射压力为ll0MPa),采用3.4 中的脱脂工艺进行热脱脂,再将脱脂坯烧结成成品。仅 从烧后样品外观看l 试样表面光滑平整;2 试样表面略 有气泡;而3 试样表面有少量开裂现象。 体积密度及强度测试结果(见表3)表明,烧后l 试样比2 、3 试样密度及强度值较高,其原因可能是l 试样中A1 O 含量较多,且粘结剂能够与A1 O 粉末均匀 混合,当粘结剂完全脱除后,坯体中A1,O 颗粒能够紧密 堆积,形成的结构缺陷少,故体积密度较大、强度值较高。 而在3 试样中,在粘结剂中作为主要填充物的石蜡较少, 故喂料的流动性较差,混料时A1 O 陶瓷颗粒分散得相对 不是很均匀,在一定程度上引起了缺陷的产生,使得试 样的密度和强度值较低。 2.3注射参数的选择 注射成型工艺也是整个工序的关键因素之一,如果 控制不当就会使产品形成很多缺陷,如裂纹、孔隙、焊缝、 分层、粉末和粘结剂分离等,而这些缺陷直到脱脂和烧 结后才能被发现。所以控制和优化注射温度、模具温度、 注射压力和保压时问等成型参数对减少生坯重量波动, 防止注射料中各组分的分离和偏析,提高产品成品率和 材料的利用率至关重要。 注射过程是指把计量室中预塑好的喂料熔体注入到 模具型腔里面去的过程。这是喂料熔体经过喷嘴、流道 和浇口向模腔流动的过程。从工艺流程上看可分为两个 阶段:注射阶段和保压阶段,这两个阶段虽都属于熔体 流动过程,但流动条件却有较大区别。 注射阶段是从螺杆推进熔体开始到熔体充满型腔为 止。此时,在螺杆头部对熔体所设定的压强(即注射压力) 和螺杆推进熔体的速度(即注射速度)是注射成型的关 键参数。 注射压力是指注射时料筒内前端熔料所受的最高 压力,而非注射系统油压的最高压力。注射压力与油压 的关系是反比于螺杆横截面积与射料缸面积之比。目前 注射压力尚无可用的计算公式,通常认为注射压力在 20 200MPa之间,要根据的具体的材料而定。显然,注 射压力过小会影响冲模过程的完成,引起欠注;增大压 力有利于冲模的流动过程,但是有可能使坏体内部的残 余应力过大,引起断裂或飞边。 表4为不同注射压力下A1,O 陶瓷的外观、体积密 度和强度值,其中注射温度为l80℃。当注射压力过小时, 试样虽已能成型,但较为松软;而压力过大时,内部会 出现气孔等缺陷;当注射压力达到140MPa的时候,试
表2 注射成型喂料组成 编号 氧化铝/wt% 粘结 ̄/wt% 粘结剂 聚丙烯/wt% 石蜡/wt ̄/o 硬脂酸/wco/0 1 70 30 20 79 1 2讦 60 40 20 79 1 3 60 40 67 22 11
中国陶瓷I CHINA CERAMICS I 2007(43)第5期I 15
维普资讯 http://www.cqvip.com