氧化铝陶瓷制作工艺
氧化铝陶瓷制作工艺流程
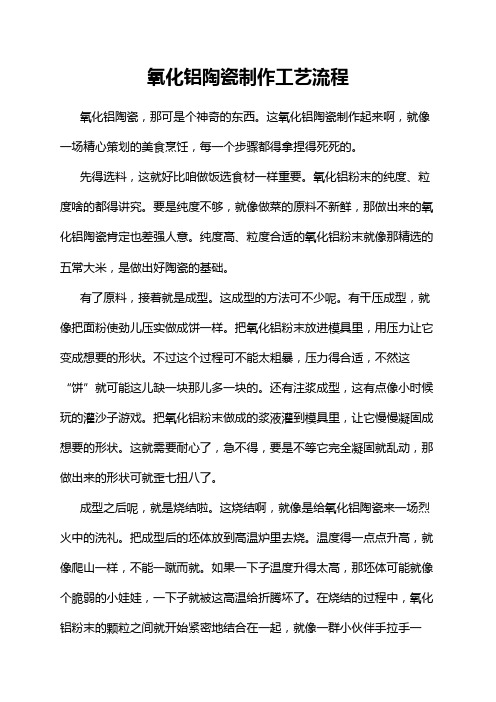
氧化铝陶瓷制作工艺流程氧化铝陶瓷,那可是个神奇的东西。
这氧化铝陶瓷制作起来啊,就像一场精心策划的美食烹饪,每一个步骤都得拿捏得死死的。
先得选料,这就好比咱做饭选食材一样重要。
氧化铝粉末的纯度、粒度啥的都得讲究。
要是纯度不够,就像做菜的原料不新鲜,那做出来的氧化铝陶瓷肯定也差强人意。
纯度高、粒度合适的氧化铝粉末就像那精选的五常大米,是做出好陶瓷的基础。
有了原料,接着就是成型。
这成型的方法可不少呢。
有干压成型,就像把面粉使劲儿压实做成饼一样。
把氧化铝粉末放进模具里,用压力让它变成想要的形状。
不过这个过程可不能太粗暴,压力得合适,不然这“饼”就可能这儿缺一块那儿多一块的。
还有注浆成型,这有点像小时候玩的灌沙子游戏。
把氧化铝粉末做成的浆液灌到模具里,让它慢慢凝固成想要的形状。
这就需要耐心了,急不得,要是不等它完全凝固就乱动,那做出来的形状可就歪七扭八了。
成型之后呢,就是烧结啦。
这烧结啊,就像是给氧化铝陶瓷来一场烈火中的洗礼。
把成型后的坯体放到高温炉里去烧。
温度得一点点升高,就像爬山一样,不能一蹴而就。
如果一下子温度升得太高,那坯体可能就像个脆弱的小娃娃,一下子就被这高温给折腾坏了。
在烧结的过程中,氧化铝粉末的颗粒之间就开始紧密地结合在一起,就像一群小伙伴手拉手一样,变得越来越结实。
在烧结的过程中,还得注意气氛的控制。
有时候需要还原气氛,有时候需要氧化气氛,这就好比不同的菜需要不同的火候和调料。
如果气氛不对,那做出来的氧化铝陶瓷可能颜色不对,性能也不好。
就像炒菜的时候盐放多了或者火候过了,菜就不好吃了。
烧结完了之后,还得进行加工。
这加工就包括研磨、抛光之类的。
研磨就像给氧化铝陶瓷做个美容,把表面不平整的地方磨掉。
抛光呢,就像是给它打一层光亮的蜡,让它看起来闪闪发亮。
这两个步骤就像女孩子化妆一样,经过这两道工序,氧化铝陶瓷就变得更加精致了。
从选料到最后的加工,氧化铝陶瓷的制作流程就像一场奇妙的旅程。
每一个环节都充满了挑战,也充满了乐趣。
氧化铝陶瓷干压工艺技术
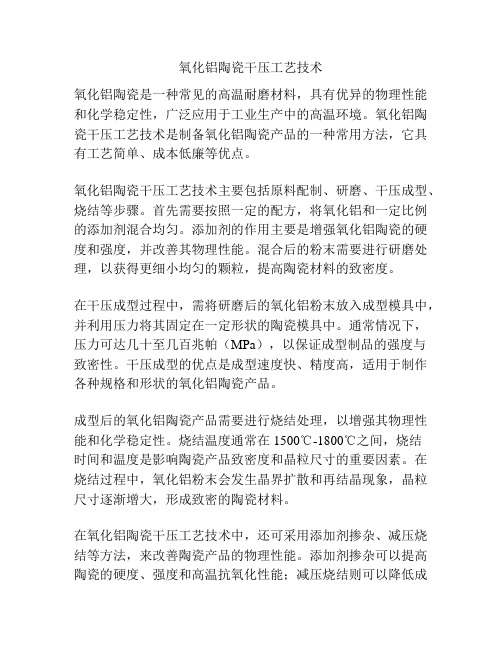
氧化铝陶瓷干压工艺技术氧化铝陶瓷是一种常见的高温耐磨材料,具有优异的物理性能和化学稳定性,广泛应用于工业生产中的高温环境。
氧化铝陶瓷干压工艺技术是制备氧化铝陶瓷产品的一种常用方法,它具有工艺简单、成本低廉等优点。
氧化铝陶瓷干压工艺技术主要包括原料配制、研磨、干压成型、烧结等步骤。
首先需要按照一定的配方,将氧化铝和一定比例的添加剂混合均匀。
添加剂的作用主要是增强氧化铝陶瓷的硬度和强度,并改善其物理性能。
混合后的粉末需要进行研磨处理,以获得更细小均匀的颗粒,提高陶瓷材料的致密度。
在干压成型过程中,需将研磨后的氧化铝粉末放入成型模具中,并利用压力将其固定在一定形状的陶瓷模具中。
通常情况下,压力可达几十至几百兆帕(MPa),以保证成型制品的强度与致密性。
干压成型的优点是成型速度快、精度高,适用于制作各种规格和形状的氧化铝陶瓷产品。
成型后的氧化铝陶瓷产品需要进行烧结处理,以增强其物理性能和化学稳定性。
烧结温度通常在1500℃-1800℃之间,烧结时间和温度是影响陶瓷产品致密度和晶粒尺寸的重要因素。
在烧结过程中,氧化铝粉末会发生晶界扩散和再结晶现象,晶粒尺寸逐渐增大,形成致密的陶瓷材料。
在氧化铝陶瓷干压工艺技术中,还可采用添加剂掺杂、减压烧结等方法,来改善陶瓷产品的物理性能。
添加剂掺杂可以提高陶瓷的硬度、强度和高温抗氧化性能;减压烧结则可以降低成型温度,并提高陶瓷材料的致密度和强度。
总之,氧化铝陶瓷干压工艺技术是一种制备氧化铝陶瓷产品的常用方法,具有工艺简单、成本低廉等优点。
通过适当的原料配制、研磨、干压成型和烧结处理,可以获得高致密度、高硬度、高强度和优异的物理性能的氧化铝陶瓷产品。
氧化铝陶瓷制作工艺简介

氧化铝陶瓷制作工艺简介氧化铝氧化铝陶瓷陶瓷目前分为高纯型与普通型两种。
高纯型氧化铝陶瓷系Al2O3含量在99.9%以上的陶瓷材料,9%以上的陶瓷材料,由于其烧结温度高达1650由于其烧结温度高达1650—1990℃,透射波长为1~6μm,一般制成熔融玻璃以取代铂坩埚:利用其透光性及可耐碱金属腐蚀性用作钠灯管;在电子工业中可用作集成电路基板与高频绝缘材料。
普通型氧化铝陶瓷系按Al2O3含量不同分为99瓷、同分为99瓷、95瓷、95瓷、95瓷、90瓷、85瓷等品种,90瓷、85瓷等品种,90瓷、85瓷等品种,有时Al2O3含量在80%或75%者有时Al2O3含量在80%或75%者也划为普通氧化铝陶瓷系列。
其中99氧化铝瓷材料用于制作高温坩埚、耐火炉管及特殊耐磨材料,如陶瓷轴承、陶瓷密封件及水阀片等;95氧化铝瓷主要用作耐腐蚀、耐磨部件;85瓷中由于常掺入部分滑石,提高了电性能与机械强度,可与、铌、钽等金属封接,有的用作电真空装置器件。
其制作工艺如下:用作电真空装置器件。
其制作工艺如下:一 粉体制备:粉体制备:将入厂的氧化铝粉按照不同的产品要求与不同成型工艺制备成粉体材料.粉体粒度在1μm微米以下,若制造高纯氧化铝陶瓷制品除氧化铝纯度在99.若制造高纯氧化铝陶瓷制品除氧化铝纯度在99.99%外,99%外,还需超细粉碎且使其粒径分布均匀。
采用挤压成型或注射成型时,采用挤压成型或注射成型时,粉料中需引入粘结剂与可塑剂,粉料中需引入粘结剂与可塑剂,粉料中需引入粘结剂与可塑剂,一般为重量一般为重量比在10—30%的热塑性塑胶或树脂有机粘结剂应与氧化铝粉体在150—200℃温度下均匀混合,以利于成型操作。
采用热压工艺成型的粉体原料则不需加入粘结剂。
采用热压工艺成型的粉体原料则不需加入粘结剂。
若采用若采用半自动或全自动干压成型,对粉体有特别的工艺要求,需要采用喷雾造粒法对粉体进行处理、使其呈现圆球状,使其呈现圆球状,以利于提高粉体流动性便于成型中自动充填模壁。
氧化铝陶瓷的制备及应用研究

氧化铝陶瓷的制备及应用研究氧化铝陶瓷是一种重要的陶瓷材料,具有许多优良的性质,比如高温稳定性、化学惰性、机械强度高等。
因此,在航空航天、化工、医疗、电子等领域都有广泛的应用。
本文将从氧化铝陶瓷的制备、性质和应用三个角度来阐述相关研究进展。
1.氧化铝陶瓷制备研究氧化铝陶瓷的制备有多种方法,包括焙烧法、注模成型、压制烧结法和激光烧结法等。
其中,焙烧法是一种常用的制备方法。
该方法首先将氧化铝粉末与有机混合物混合,在不同温度条件下煅烧,得到所需的陶瓷材料。
注模成型则是将氧化铝粉末与有机胶水混合,注入成型模具中制作成所需形状的陶瓷体。
压制烧结法则是将氧化铝粉末压制成形体后,在高温下烧结成陶瓷。
激光烧结法则是利用激光束对氧化铝粉末进行加热和压缩,形成陶瓷材料。
以上几种制备方法都有其优缺点。
焙烧法制备简单、成本低,但制备出的陶瓷材料中可能存在杂质,影响材料性能。
注模成型方法可以制作出形状复杂的陶瓷,但需要使用有机胶水作为粘合剂,可能影响材料的稳定性。
压制烧结法可以制备出高性能的氧化铝陶瓷,但加工难度较大、成本较高。
激光烧结法具有制备速度快、高温高压条件下制备的陶瓷具有均匀致密的优点,但设备成本高,生产成本也较高。
2.氧化铝陶瓷性质研究氧化铝陶瓷具有多种优良的性质,例如高机械强度、硬度、抗腐蚀性、化学稳定性、热稳定性等。
其中,氧化铝陶瓷的高机械强度和硬度使其成为制作切割工具、芯片基板等高性能材料的理想选择。
氧化铝陶瓷的化学稳定性和抗腐蚀性,使其成为能源、石油化工等领域中重要的结构材料。
氧化铝陶瓷的热稳定性则使其成为航空航天、电子等领域的重要材料。
同时,氧化铝陶瓷在生物医疗、环保等领域也有广泛的应用,如制备生物医疗器械、过滤器等。
3.氧化铝陶瓷应用研究氧化铝陶瓷在各个领域都有着广泛的应用。
在航空航天领域中,氧化铝陶瓷被应用于制造高温发动机、导弹隔热材料等。
在化工领域中,氧化铝陶瓷被应用于制作化工反应器、催化剂等。
氧化铝陶瓷制作工艺
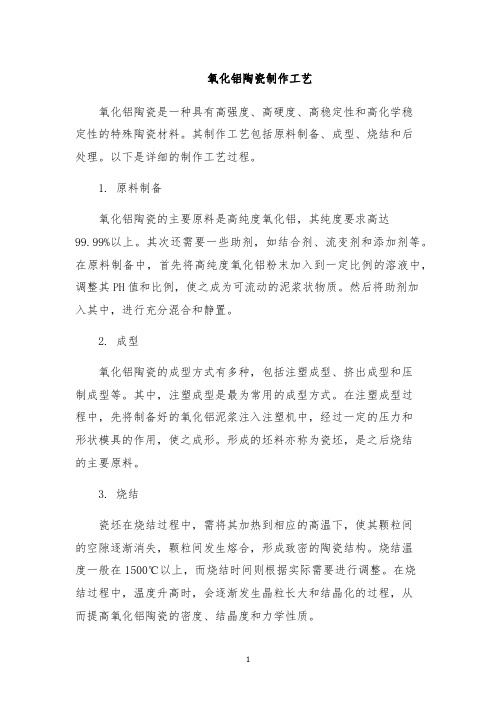
氧化铝陶瓷制作工艺氧化铝陶瓷是一种具有高强度、高硬度、高稳定性和高化学稳定性的特殊陶瓷材料。
其制作工艺包括原料制备、成型、烧结和后处理。
以下是详细的制作工艺过程。
1. 原料制备氧化铝陶瓷的主要原料是高纯度氧化铝,其纯度要求高达99.99%以上。
其次还需要一些助剂,如结合剂、流变剂和添加剂等。
在原料制备中,首先将高纯度氧化铝粉末加入到一定比例的溶液中,调整其PH值和比例,使之成为可流动的泥浆状物质。
然后将助剂加入其中,进行充分混合和静置。
2. 成型氧化铝陶瓷的成型方式有多种,包括注塑成型、挤出成型和压制成型等。
其中,注塑成型是最为常用的成型方式。
在注塑成型过程中,先将制备好的氧化铝泥浆注入注塑机中,经过一定的压力和形状模具的作用,使之成形。
形成的坯料亦称为瓷坯,是之后烧结的主要原料。
3. 烧结瓷坯在烧结过程中,需将其加热到相应的高温下,使其颗粒间的空隙逐渐消失,颗粒间发生熔合,形成致密的陶瓷结构。
烧结温度一般在1500℃以上,而烧结时间则根据实际需要进行调整。
在烧结过程中,温度升高时,会逐渐发生晶粒长大和结晶化的过程,从而提高氧化铝陶瓷的密度、结晶度和力学性质。
4. 后处理烧结后的氧化铝陶瓷需要进行后处理,以达到期望的性能和外观效果。
后处理包括去毛刺、打磨、抛光、阳极氧化等。
去毛刺是一项必要过程,可去除瓷坯表面的毛刺和毛发,使其表面更加光滑。
打磨和抛光则可将瓷坯表面的粗糙度和凹凸不平处处理,使之表面更加平滑细腻。
而阳极氧化则是为了提高氧化铝陶瓷的耐腐蚀性和色泽度。
总的来说,氧化铝陶瓷的制作工艺不仅要求原料的纯度和质量,还需要严格控制成型、烧结和后处理等各个环节的工艺参数。
只有如此,才能生产出高品质的氧化铝陶瓷产品。
氧化铝陶瓷制作工艺简介
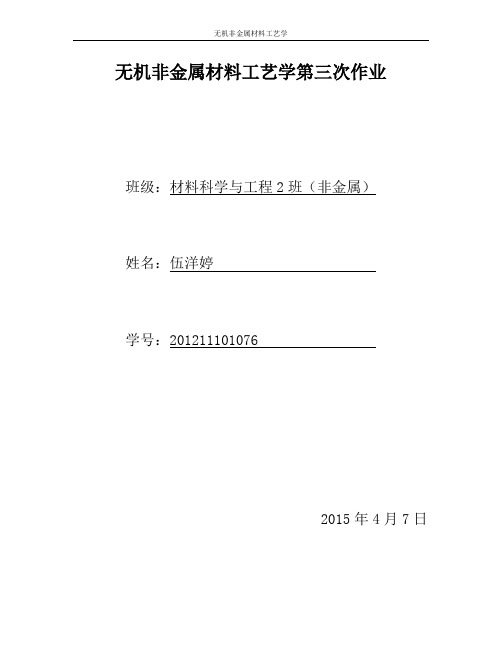
无机非金属材料工艺学无机非金属材料工艺学第三次作业班级:材料科学与工程2班(非金属)姓名:伍洋婷学号:2012111010762015年4月7日氧化铝陶瓷生产技术工艺简介氧化铝陶瓷的低温烧结技术氧化铝陶瓷是一种以Al2O3为主要原料,以刚玉(α—Al2O3)为主晶相的陶瓷材料。
一、通过提高Al2O3粉体的细度与活性降低瓷体烧结温度。
目前,制备超细活化易烧结Al2O3粉体的方法分为二大类,一类是机械法,另一类是化学法。
机械法是用机械外力作用使Al2O3粉体颗粒细化,常用的粉碎工艺有球磨粉碎、振磨粉碎、砂磨粉碎、气流粉碎等等。
通过机械粉碎方法来提高粉料的比表面积,尽管是有效的,但有一定限度,通常只能使粉料的平均粒径小至1μm左右或更细一点,而且有粒径分布范围较宽,容易带入杂质的缺点。
近年来,采用湿化学法制造超细高纯Al2O3粉体发展较快,其中较为成熟的是溶胶—凝胶法。
由于溶胶高度稳定,因而可将多种金属离子均匀、稳定地分布于胶体中,通过进一步脱水形成均匀的凝胶(无定形体),再经过合适的处理便可获得活性极高的超微粉混合氧化物或均一的固溶体。
目前此法大致有以下3种工艺流程。
(1)形成金属氧有机基络合物溶胶→水解并缩合成含羟基的三度空间高分子结构→溶胶蒸发脱水成凝胶→低温煅烧成活性氧化物粉料。
(2)含有不同金属离子的酸盐溶液和有机胶混合成溶液→溶胶蒸发脱水成凝胶→低温煅烧成粉体。
(3)含有不同金属离子的溶胶直接淬火、沉积或加热成凝胶→低温煅烧成粉体。
湿化学法制备的Al2O3粉体粒径可达到纳米级,粒径分布范围窄,化学纯度高,晶体缺陷多。
因此化学法粉体的表面能与活性比机械法粉体要高得多。
采用这种超细Al2O3粉体作原料不仅能明显降低氧化铝瓷的烧结温度(可降150℃—300℃),而且可以获得微晶高强的高铝瓷材料。
表二是日本住友化学有限公司生产的易烧结Al2O3粉料理化指标。
二、通过瓷料配方设计掺杂降低瓷体烧结温度氧化铝陶瓷的烧结温度主要由其化学组成中Al2O3的含量来决定,Al2O3含量越高,瓷料的烧结温度越高,除此之外,还与瓷料组成系统、各组成配比以及添加物种类有关。
浅析氧化铝陶瓷制作工艺
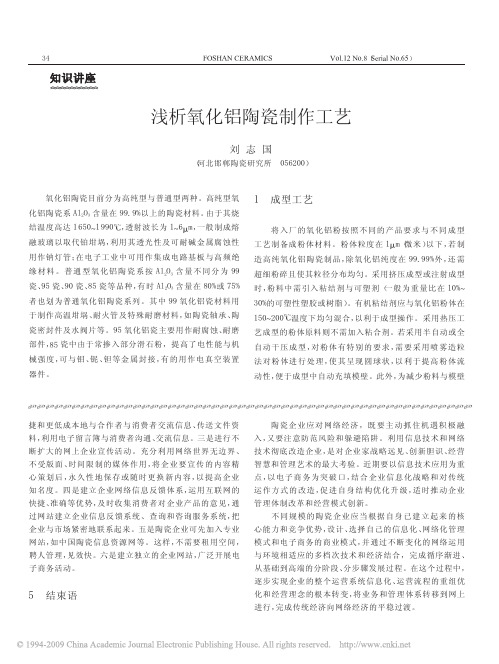
结提高 -"’!%"’ , 比一般热压烧结提高 &"’!&%’ 。因此, 目 前一些高附加值氧化铝陶瓷产品或国防军用的特殊零部 件, 如陶瓷轴 承 、 反射镜、 核燃料及枪管等制品, 常采用热 等静压烧成方法。 此外, 微波烧结、 电弧等离子体烧结、 自蔓延烧结技术 等亦在开发研究中。
有些氧化铝陶瓷材料在完成烧结后,尚需进行加工。 如可用作人工骨的制品要求表面有很高的光洁度, 如镜面 一样, 以增加润滑性。由于氧化铝陶瓷材料硬度较高, 需用 更硬的研磨抛光材料对其作精加工,如 567、 817 或金钢钻 等, 通常采用由粗到细磨料逐级磨削, 最终表面抛光。一般 可采用 9!0( 微米) 的 *+!,- 微粉或金刚钻膏进行研磨抛光。
()*。
干压成型时需对粉体喷雾造粒, 其中引入聚乙烯醇作 为粘结剂。近年来上海某研究所开发一种水溶性石蜡用作
*+!,- 喷雾造粒的粘结剂,在加热情况下有很好的流动性。
喷雾造粒 后 的 粉 体 必 须 具 备 流 动 性 好 、 密度松散、 流动角 摩擦温度小于 -"" 、 颗粒及 配 比 理 想 等 条 件 , 以获得较大 的素坯密度。
*00成型工艺
将入厂的氧化铝粉按照不同的产品要求与不同成型 微米) 以下, 若制 工艺制备成粉体材料。粉体粒度在 *!- ( 造高纯氧化铝陶瓷制品, 除氧化铝纯度在 ’’(’’) 外 , 还需 超细粉碎且使其粒径分布均匀。采用挤压成型或注射成型 时, 粉料中需引入粘结剂与可塑剂( 一般为重量比在 *,)! 。有机粘结剂应与氧化铝粉体在 &,)的可塑性塑胶或树脂) 以利于成型操作。采用热压工 *!,!$,,"温度下均匀混合, 艺成型的粉体原料则不需加入粘合剂。若采用半自动或全 自动干压 成 型 , 对粉体有特别的要求, 需要采用喷雾造粒 法对粉体 进 行 处 理 , 使其呈现圆球状, 以利于提高粉体流 动性, 便于成型中自动充填模壁。此外, 为减少粉料与模壁
氧化铝陶瓷

氧化铝陶瓷
氧化铝陶瓷是一种高性能陶瓷材料,也称为氧化铝陶瓷材料。
它是由高纯度氧化铝粉末通过压制、成型、烧结等工艺制成的一种非金属材料。
氧化铝陶瓷具有高硬度、高强度、高耐磨性、高耐腐蚀性、高耐高温性、绝缘性能好等优良的物理性能和化学性能。
因此,氧化铝陶瓷被广泛应用于航空航天、机械工业、电子电器、化学工业等领域。
氧化铝陶瓷的制备过程一般包括以下几个步骤:首先将高纯度氧化铝粉末与其他添加剂混合均匀,然后通过压制或注塑成型,最后进行高温烧结处理。
在烧结过程中,氧化铝粉末会逐渐结合成致密坚硬的结构,形成具有优良物理性能和化学性能的氧化铝陶瓷。
氧化铝陶瓷的应用领域非常广泛,例如在航空航天领域中,氧化铝陶瓷可以用于制造发动机涡轮叶片、航空仪器仪表、空气滤清器等;在机械工业中,氧化铝陶瓷可以用于制造轴承、轴瓦、机床刀具、磨料等;在电子电器领域中,氧化铝陶瓷可以用于制造电子器件、热敏电阻器、微波陶瓷等;在化学工业中,氧化铝陶瓷可以用于制造化学反应器、催化剂载体等。
- 1、下载文档前请自行甄别文档内容的完整性,平台不提供额外的编辑、内容补充、找答案等附加服务。
- 2、"仅部分预览"的文档,不可在线预览部分如存在完整性等问题,可反馈申请退款(可完整预览的文档不适用该条件!)。
- 3、如文档侵犯您的权益,请联系客服反馈,我们会尽快为您处理(人工客服工作时间:9:00-18:30)。
氧化铝陶瓷介绍来自:中国特种陶瓷网发布时间:2005-8-3 11:51:15氧化铝陶瓷制作工艺简介氧化铝陶瓷目前分为高纯型与普通型两种。
高纯型氧化铝陶瓷系Al2O3含量在99.9%以上的陶瓷材料,由于其烧结温度高达1650—1990℃,透射波长为1~6μm,一般制成熔融玻璃以取代铂坩埚:利用其透光性及可耐碱金属腐蚀性用作钠灯管;在电子工业中可用作集成电路基板与高频绝缘材料。
普通型氧化铝陶瓷系按Al2O3含量不同分为99瓷、95瓷、90瓷、85瓷等品种,有时Al2O3含量在80%或75%者也划为普通氧化铝陶瓷系列。
其中99氧化铝瓷材料用于制作高温坩埚、耐火炉管及特殊耐磨材料,如陶瓷轴承、陶瓷密封件及水阀片等;95氧化铝瓷主要用作耐腐蚀、耐磨部件;85瓷中由于常掺入部分滑石,提高了电性能与机械强度,可与钼、铌、钽等金属封接,有的用作电真空装置器件。
其制作工艺如下:一粉体制备:郑州玉发集团是中国最大的白刚玉生产商,和中科院上海硅酸盐研究所成立玉发新材料研究中心研究生产多品种α氧化铝。
专注白刚玉和煅烧α氧化铝近30年,因为专注所以专业,联系QQ2596686490,电话156390七七八八一。
将入厂的氧化铝粉按照不同的产品要求与不同成型工艺制备成粉体材料。
粉体粒度在1μm?微米?以下,若制造高纯氧化铝陶瓷制品除氧化铝纯度在99.99%外,还需超细粉碎且使其粒径分布均匀。
采用挤压成型或注射成型时,粉料中需引入粘结剂与可塑剂,?一般为重量比在10—30%的热塑性塑胶或树脂?有机粘结剂应与氧化铝粉体在150—200℃温度下均匀混合,以利于成型操作。
采用热压工艺成型的粉体原料则不需加入粘结剂。
若采用半自动或全自动干压成型,对粉体有特别的工艺要求,需要采用喷雾造粒法对粉体进行处理、使其呈现圆球状,以利于提高粉体流动性便于成型中自动充填模壁。
此外,为减少粉料与模壁的摩擦,还需添加1~2%的润滑剂?如硬脂酸?及粘结剂PVA。
欲干压成型时需对粉体喷雾造粒,其中引入聚乙烯醇作为粘结剂。
近年来上海某研究所开发一种水溶性石蜡用作Al2O3喷雾造粒的粘结剂,在加热情况下有很好的流动性。
喷雾造粒后的粉体必须具备流动性好、密度松散,流动角摩擦温度小于30℃。
颗粒级配比理想等条件,以获得较大素坯密度。
二成型方法:氧化铝陶瓷制品成型方法有干压、注浆、挤压、冷等静压、注射、流延、热压与热等静压成型等多种方法。
近几年来国内外又开发出压滤成型、直接凝固注模成型、凝胶注成型、离心注浆成型与固体自由成型等成型技术方法。
不同的产品形状、尺寸、复杂造型与精度的产品需要不同的成型方法。
摘其常用成型介绍:1干压成型:氧化铝陶瓷干压成型技术仅限于形状单纯且内壁厚度超过1mm,长度与直径之比不大于4∶1的物件。
成型方法有单轴向或双向。
压机有液压式、机械式两种,可呈半自动或全自动成型方式。
压机最大压力为200Mpa。
产量每分钟可达15~50件。
由于液压式压机冲程压力均匀,故在粉料充填有差异时压制件高度不同。
而机械式压机施加压力大小因粉体充填多少而变化,易导致烧结后尺寸收缩产生差异,影响产品质量。
因此干压过程中粉体颗粒均匀分布对模具充填非常重要。
充填量准确与否对制造的氧化铝陶瓷零件尺寸精度控制影响很大。
粉体颗粒以大于60μm、介于60~200目之间可获最大自由流动效果,取得最好压力成型效果。
2注浆成型法:注浆成型是氧化铝陶瓷使用最早的成型方法。
由于采用石膏模、成本低且易于成型大尺寸、外形复杂的部件。
注浆成型的关键是氧化铝浆料的制备。
通常以水为熔剂介质,再加入解胶剂与粘结剂,充分研磨之后排气,然后倒注入石膏模内。
由于石膏模毛细管对水分的吸附,浆料遂固化在模内。
空心注浆时,在模壁吸附浆料达要求厚度时,还需将多余浆料倒出。
为减少坯体收缩量、应尽量使用高浓度浆料。
氧化铝陶瓷浆料中还需加入有机添加剂以使料浆颗粒表面形成双电层使料浆稳定悬浮不沉淀。
此外还需加入乙烯醇、甲基纤维素、海藻酸胺等粘结剂及聚丙烯胺、阿拉伯树胶等分散剂,目的均在于使浆料适宜注浆成型操作。
三烧成技术:将颗粒状陶瓷坯体致密化并形成固体材料的技术方法叫烧结。
烧结即将坯体内颗粒间空洞排除,将少量气体及杂质有机物排除,使颗粒之间相互生长结合,形成新的物质的方法。
烧成使用的加热装置最广泛使用电炉。
除了常压烧结?即无压烧结?外,还有热压烧结及热等静压烧结等。
连续热压烧结虽然提高产量,但设备和模具费用太高,此外由于属轴向受热,制品长度受到限制。
热等静压烧成采用高温高压气体作压力传递介质,具有各向均匀受热之优点,很适合形状复杂制品的烧结。
由于结构均匀,材料性能比冷压烧结提高30~50%。
比一般热压烧结提高10~15%。
因此,目前一些高附加值氧化铝陶瓷产品或国防军工需用的特殊零部件、如陶瓷轴承、反射镜、核燃料及枪管等制品、场采用热等静压烧成方法。
此外,微波烧结法、电弧等离子烧结法、自蔓延烧结技术亦正在开发研究中。
四精加工与封装工序:有些氧化铝陶瓷材料在完成烧结后,尚需进行精加工。
如可用作人工骨的制品要求表面有很高的光洁度、如镜面一样,以增加润滑性。
由于氧化铝陶瓷材料硬度较高,需用更硬的研磨抛光砖材料对其作精加工。
如SiC、B4C或金刚钻等。
通常采用由粗到细磨料逐级磨削,最终表面抛光。
一般可采用<1μm?微米?的Al2O3微粉或金刚钻膏进行研磨抛光。
此外激光加工及超声波加工研磨及抛光的方法亦可采用。
有些氧化铝陶瓷零件需与其它材料作封装处理。
氧化铝陶瓷的低温烧结技术氧化铝陶瓷是一种以Al2O3为主要原料,以刚玉(α—Al2O3)为主晶相的陶瓷材料。
因其具有机械强度高、硬度大、高频介电损耗小、高温绝缘电阻高、耐化学腐蚀性和导热性良好等优良综合技术性能,以及原料来源广、价格相对便宜、加工制造技术较为成熟等优势,氧化铝陶瓷已被广泛应用于电子、电器、机械、化工、纺织、汽车、冶金和航空航天等行业,成为目前世界上用量最大的氧化物陶瓷材料。
然而,由于氧化铝熔点高达2050℃,导致氧化铝陶瓷的烧结温度普遍较高(参见表一中标准烧结温度),从而使得氧化铝陶瓷的制造需要使用高温发热体或高质量的燃料以及高级耐火材料作窑炉和窑具,这在一定程度上限制了它的生产和更广泛的应用。
因此,降低氧化铝陶瓷的烧结温度,降低能耗,缩短烧成周期,减少窑炉和窑具损耗,从而降低生产成本,一直是企业所关心和急需解决的重要课题。
目前,对氧化铝陶瓷低温烧结技术的研究工作已很广泛和深入,从75瓷到99瓷都有系统的研究,业已取得显著成效。
表一是已实现的各类氧化铝陶瓷低温烧结情况。
表中低温烧结氧化铝陶瓷的各项机电性能均达到了相应瓷种的国家标准,甚至中铝瓷在某些技术标准上超过高铝瓷的国标,如中科院上海硅酸盐研究所研制的1360℃烧成的85瓷,其抗弯强度超过99%Al2O3陶瓷的国标,各项电性能都优于95%Al2O3瓷的国标;Al2O3含量分别为90%和95%的低温烧结陶瓷,其机电性能都优于95瓷及99瓷的国标。
纵观当前各种氧化铝瓷的低温烧结技术,归纳起来,主要是从原料加工、配方设计和烧成工艺等三方面来采取措施,下面分别加以概述。
一、通过提高Al2O3粉体的细度与活性降低瓷体烧结温度。
与块状物相比,粉体具有很大的比表面积,这是外界对粉体做功的结果。
利用机械作用或化学作用来制备粉体时所消耗的机械能或化学能,部分将作为表面能而贮存在粉体中,此外,在粉体的制备过程中,又会引起粉粒表面及其内部出现各种晶格缺陷,使晶格活化。
由于这些原因,粉体具有较高的表面自由能。
粉体的这种表面能是其烧结的内在动力。
因此,Al2O3粉体的颗粒越细,活化程度越高,粉体就越容易烧结,烧结温度越低。
在氧化铝瓷低温烧结技术中,使用高活性易烧结Al2O3粉体作原料是重要的手段之一,因而粉体制备技术成为陶瓷低温烧结技术中一个基础环节。
目前,制备超细活化易烧结Al2O3粉体的方法分为二大类,一类是机械法,另一类是化学法。
机械法是用机械外力作用使Al2O3粉体颗粒细化,常用的粉碎工艺有球磨粉碎、振磨粉碎、砂磨粉碎、气流粉碎等等。
通过机械粉碎方法来提高粉料的比表面积,尽管是有效的,但有一定限度,通常只能使粉料的平均粒径小至1μm左右或更细一点,而且有粒径分布范围较宽,容易带入杂质的缺点。
近年来,采用湿化学法制造超细高纯Al2O3粉体发展较快,其中较为成熟的是溶胶—凝胶法。
由于溶胶高度稳定,因而可将多种金属离子均匀、稳定地分布于胶体中,通过进一步脱水形成均匀的凝胶(无定形体),再经过合适的处理便可获得活性极高的超微粉混合氧化物或均一的固溶体。
目前此法大致有以下3种工艺流程。
(1)形成金属氧有机基络合物溶胶→水解并缩合成含羟基的三度空间高分子结构→溶胶蒸发脱水成凝胶→低温煅烧成活性氧化物粉料。
(2)含有不同金属离子的酸盐溶液和有机胶混合成溶液→溶胶蒸发脱水成凝胶→低温煅烧成粉体。
(3)含有不同金属离子的溶胶直接淬火、沉积或加热成凝胶→低温煅烧成粉体。
湿化学法制备的Al2O3粉体粒径可达到纳米级,粒径分布范围窄,化学纯度高,晶体缺陷多。
因此化学法粉体的表面能与活性比机械法粉体要高得多。
采用这种超细Al2O3粉体作原料不仅能明显降低氧化铝瓷的烧结温度(可降150℃—300℃),而且可以获得微晶高强的高铝瓷材料。
表二是日本住友化学有限公司生产的易烧结Al2O3粉料理化指标。
此外,有专家推荐以下三种超细Al2O3粉体制备方法,仅供参考:(1)将(NH4)SO4Al2(SO4)3·2H2O与(MgCO3)4Mg(OH)2·5H2O混合、加热到1200℃分解,可获得含有MgO的纯度为99%、μm的α—Al2O3超细粉料。
(2)将无水二醋酸铝加热μm的α—Al2O3超细粉体。
(3)铁筒钢球,湿磨数百小时,浆料加热酸洗除铁,浮选,反复多次,可制—μm的α—Al2O3超细粉料。
二、通过瓷料配方设计掺杂降低瓷体烧结温度氧化铝陶瓷的烧结温度主要由其化学组成中Al2O3的含量来决定,Al2O3含量越高,瓷料的烧结温度越高,除此之外,还与瓷料组成系统、各组成配比以及添加物种类有关。
比如,在Al2O3含量相当时,CaO-Al2O3-SiO2系Al2O3瓷料比MgO-Al2O3-SiO2系瓷料的烧结温度低,对于我国目前大量生产的CaO-MgO-Al2O3-SiO2系统瓷料而言,少量的La2O3、Y2O3、Cr2O3、MnO、TiO2、ZrO2、Ta2O3等氧化物能进一步降低烧结温度、改善瓷体的微观组织结构和性能。
因此,在保证瓷体满足产品使用目的和技术要求的前提下,我们可以通过配方设计,选择合理的瓷料系统,加入适当的助烧添加剂,使氧化铝陶瓷的烧结温度尽可能降低。
目前配方设计中所加入的各种添加剂,根据其促进氧化铝陶瓷烧结的作用机理不同,可以将它们分为形成新相或固溶体的添加剂和生成液相的添加剂二大类。