压铸模具材料选择和热处理要求
压铸件设计规范详解

压铸件设计规范详解压铸件是指利用压铸工艺将熔融金属注入模具中,经过凝固和冷却后得到的零件。
由于该工艺具有生产效率高、成本低、制造精度高等优点,被广泛应用于汽车、航空航天、电子等领域。
为了保证压铸件质量和安全性,需要遵循一系列的设计规范。
下面将详细介绍压铸件设计规范。
一、材料选择1.铝合金:常用的有A380、A383、A360等。
根据使用条件和要求,选择合适的铝合金材料,确保压铸件具有良好的强度和塑性。
2.压铸型腔材料:常用的有铜合金、热处理工具钢等。
要选择适当的材料,以耐高温和磨损。
二、模具设计1.模具设计必须满足压铸件的要求,保证铸件的尺寸精度和表面质量。
2.模腔设计要考虑到铸件收缩率、冷却速度等因素,以避免产生缺陷和变形。
3.合理安排模具冷却系统,保证压铸件内部和表面的冷却均匀。
三、尺寸设计1.压铸件的尺寸设计应符合产品技术要求和工艺要求,确保功能和安装的需要。
2.避免设计尺寸太小或太薄,以免产生破裂和变形。
3.设计保证良好的表面质量,避免设计中出现接触不良、挤压不足等问题。
四、壁厚设计1.壁厚不应过薄,以免影响产品的强度和刚性。
2.避免壁厚过大,以减少成本和缩短冷却时间。
3.边缘和角部应注意壁厚过渡,避免产生应力集中。
五、设计角度和半径1.设计时应根据铝合金的流动性选择合适的角度和半径。
2.避免设计尖锐角度和太小的半径,以免产生气孔和挤压不足。
3.设计角度和半径应保持一定的一致性,避免因设计不当导致铸件变形和收缩不均匀。
六、设计放射状构件1.当压铸件具有放射状构件时,要合理设计放射状梁的位置和数量,以充分利用材料,并减少成本。
2.注意放射状构件的设计不应影响整体结构的强度。
七、设计排气系统1.设计时要考虑到铸件内部的气孔、气泡等气体排出问题。
2.合理安排和设计排气道,以保证良好的注模效果和铸件质量。
八、设计孔和螺纹1.设计孔和螺纹时应遵循标准规范,确保质量和安装的可靠性。
2.孔和螺纹的位置和尺寸应符合产品要求,保证压铸件的功能和使用要求。
压铸模具标准
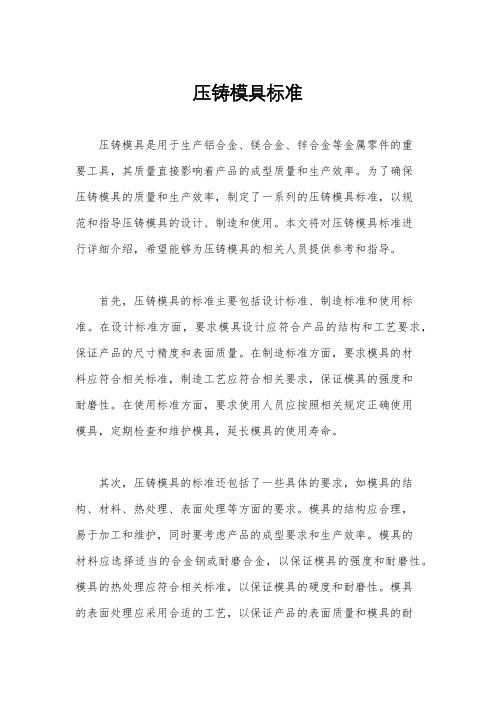
压铸模具标准压铸模具是用于生产铝合金、镁合金、锌合金等金属零件的重要工具,其质量直接影响着产品的成型质量和生产效率。
为了确保压铸模具的质量和生产效率,制定了一系列的压铸模具标准,以规范和指导压铸模具的设计、制造和使用。
本文将对压铸模具标准进行详细介绍,希望能够为压铸模具的相关人员提供参考和指导。
首先,压铸模具的标准主要包括设计标准、制造标准和使用标准。
在设计标准方面,要求模具设计应符合产品的结构和工艺要求,保证产品的尺寸精度和表面质量。
在制造标准方面,要求模具的材料应符合相关标准,制造工艺应符合相关要求,保证模具的强度和耐磨性。
在使用标准方面,要求使用人员应按照相关规定正确使用模具,定期检查和维护模具,延长模具的使用寿命。
其次,压铸模具的标准还包括了一些具体的要求,如模具的结构、材料、热处理、表面处理等方面的要求。
模具的结构应合理,易于加工和维护,同时要考虑产品的成型要求和生产效率。
模具的材料应选择适当的合金钢或耐磨合金,以保证模具的强度和耐磨性。
模具的热处理应符合相关标准,以保证模具的硬度和耐磨性。
模具的表面处理应采用合适的工艺,以保证产品的表面质量和模具的耐蚀性。
最后,压铸模具的标准还包括了一些检验和测试的要求,如模具的出厂检验、使用前检验、定期检验等。
模具的出厂检验应包括模具的尺寸检验、材料检验、热处理检验等,以保证模具的质量。
使用前检验应包括模具的装配检验、润滑检验、保养检验等,以保证模具的正常使用。
定期检验应包括模具的尺寸检验、磨损检验、裂纹检验等,以保证模具的使用寿命。
总之,压铸模具标准是保证压铸模具质量和生产效率的重要依据,对压铸模具的设计、制造和使用都有着重要的指导作用。
压铸模具的相关人员应严格按照相关标准执行,以保证产品质量和生产效率,推动压铸模具行业的健康发展。
希望本文所介绍的压铸模具标准能够为相关人员提供参考和指导,推动我国压铸模具行业的发展。
压铸工艺流程中的模具设计要点

压铸工艺流程中的模具设计要点压铸是一种常用的金属加工工艺,通过将熔融金属注入模具中,并在固化后取出成型件。
模具设计是整个压铸工艺中的关键环节,决定了成型件的质量和生产效率。
本文将从模具结构设计、材料选择和加工工艺三个方面讨论压铸工艺流程中的模具设计要点。
一、模具结构设计要点1. 合理选择模具结构模具结构的设计应根据产品的形状、尺寸和压铸工艺要求进行合理选择。
一般常见的模具结构包括单腔、多腔、合模和分模等。
对于形状复杂的产品,可以采用多腔结构来提高生产效率。
对于尺寸较大的产品,可以考虑采用合模结构来减少模具成本。
2. 考虑产品的冷却和顶针装置在模具设计中,需要考虑产品的冷却和顶针装置。
冷却系统的设计应能够有效地排除熔融金属的热量,以确保成型件的质量。
顶针装置的设计应满足产品的要求,并保证顶针在压铸过程中的精确位置。
3. 设计合理的浇口和溢流槽浇口和溢流槽是模具设计中的重要组成部分。
设计浇口时应考虑熔融金属的流动性和冷却速度,并确保浇口与产品的结合处处于合适的位置。
溢流槽的设计应考虑金属液体的顺利流动,以避免产生气体和杂质。
二、材料选择要点1. 选择耐磨耐热的材料模具在压铸过程中需要承受高温和高压的作用,因此材料的选择至关重要。
一般采用耐磨耐热的工具钢或合金钢作为模具材料,以保证模具的使用寿命和成型件的质量。
此外,还应考虑材料的加工性能和可靠性。
2. 考虑材料的强度和刚性模具的结构设计需要兼顾材料的强度和刚性。
材料的强度直接影响到模具的承载能力,而刚性则影响到模具的稳定性和精度。
因此,在模具设计中应根据产品的要求选择合适的材料,并进行合理的加工和热处理,以提高模具的性能。
三、加工工艺要点1. 精确计算和控制成型参数在压铸工艺中,成型参数的精确计算和控制是保证成型件质量和加工效率的关键。
成型参数包括注射速度、压力、温度和冷却时间等。
合理选择和控制这些参数,可以避免产生缺陷和变形,提高成型件的精度和表面质量。
铝压铸模具材料
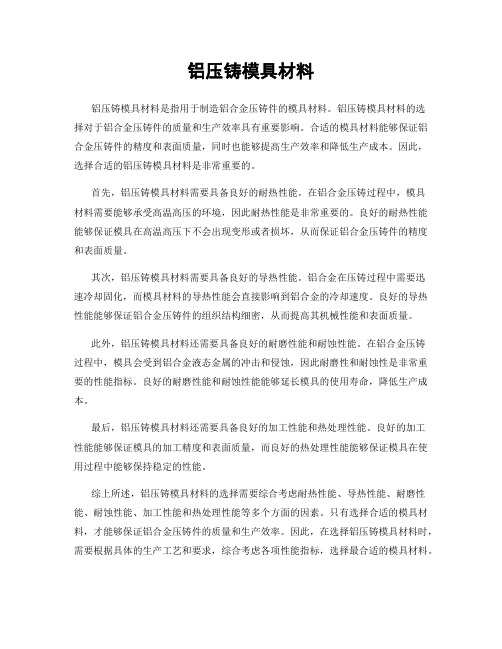
铝压铸模具材料铝压铸模具材料是指用于制造铝合金压铸件的模具材料。
铝压铸模具材料的选择对于铝合金压铸件的质量和生产效率具有重要影响。
合适的模具材料能够保证铝合金压铸件的精度和表面质量,同时也能够提高生产效率和降低生产成本。
因此,选择合适的铝压铸模具材料是非常重要的。
首先,铝压铸模具材料需要具备良好的耐热性能。
在铝合金压铸过程中,模具材料需要能够承受高温高压的环境,因此耐热性能是非常重要的。
良好的耐热性能能够保证模具在高温高压下不会出现变形或者损坏,从而保证铝合金压铸件的精度和表面质量。
其次,铝压铸模具材料需要具备良好的导热性能。
铝合金在压铸过程中需要迅速冷却固化,而模具材料的导热性能会直接影响到铝合金的冷却速度。
良好的导热性能能够保证铝合金压铸件的组织结构细密,从而提高其机械性能和表面质量。
此外,铝压铸模具材料还需要具备良好的耐磨性能和耐蚀性能。
在铝合金压铸过程中,模具会受到铝合金液态金属的冲击和侵蚀,因此耐磨性和耐蚀性是非常重要的性能指标。
良好的耐磨性能和耐蚀性能能够延长模具的使用寿命,降低生产成本。
最后,铝压铸模具材料还需要具备良好的加工性能和热处理性能。
良好的加工性能能够保证模具的加工精度和表面质量,而良好的热处理性能能够保证模具在使用过程中能够保持稳定的性能。
综上所述,铝压铸模具材料的选择需要综合考虑耐热性能、导热性能、耐磨性能、耐蚀性能、加工性能和热处理性能等多个方面的因素。
只有选择合适的模具材料,才能够保证铝合金压铸件的质量和生产效率。
因此,在选择铝压铸模具材料时,需要根据具体的生产工艺和要求,综合考虑各项性能指标,选择最合适的模具材料。
压铸模具的技术要求文档

压铸模具的技术要求文档压铸模具是现代工业生产中常用的一种模具,用于制造各种金属制品。
压铸模具的技术要求非常高,对模具的设计、制造、使用等方面都有相应的要求。
本文将从几个方面详细介绍压铸模具的技术要求。
一、设计要求1.模具结构设计要合理,要考虑到产品的结构特点、工艺要求等因素,并保证在模具使用中有较高的稳定性和精度。
2.模腔的设计要充分考虑充型性、冷却性、顶出性等要素,确保产品成型质量稳定。
3.模具的开口方式、进料方式等设计要符合产品要求,并能保证模具的安全操作。
二、材料要求1.模具材料应具有良好的刚性、韧性和耐磨性,能够承受较大的冲击负荷和高温环境,如工具钢、合金钢等。
2.模具的热处理要求良好,能够使模具硬度均匀、稳定,延长使用寿命。
三、制造要求1.模具加工要求高精度、高质量,要保证模具的尺寸精度和表面质量。
2.维修和保养要定期进行,及时处理模具的磨损、损伤等问题,确保模具的正常使用和寿命。
四、使用要求1.模具的操作人员要具备一定的技能和经验,严格按照操作规程进行操作,保证操作的安全和准确性。
2.模具的使用环境要保持清洁、干燥,避免灰尘、水汽等对模具的损坏。
3.模具的顶出装置、冷却装置等要保持良好的工作状态,及时进行维修和更换。
五、质量控制要求1.模具的尺寸精度、表面质量等要进行严格的检测和控制,保证产品的准确性和一致性。
2.定期对模具进行检测和维修,及时发现并解决模具的问题,防止因模具问题引起的产品质量问题。
总结:压铸模具的技术要求非常高,对模具的设计、制造、使用等方面都有严格要求。
只有合理的设计,良好的材料和制造工艺,正确的使用和维护,才能保证模具的高质量和长寿命,从而保证产品的质量和生产效率。
因此,在实际应用中,需要充分重视压铸模具的技术要求,综合考虑各方面因素,确保模具的高效稳定运行。
一体化压铸模具钢热处理

一体化压铸模具钢热处理一、预热处理预热处理是压铸模具钢热处理的第一步,其目的是消除材料的内应力,提高材料的稳定性,预防热处理过程中产生变形和裂纹。
预热处理通常包括以下步骤:1. 退火:退火是一种将钢加热到一定温度,保温一段时间,然后缓慢冷却的过程。
退火可以消除内应力,改善材料的塑性和韧性,提高材料的可加工性。
2. 回火:回火是将钢加热到一定温度,保温一段时间,然后快速冷却的过程。
回火可以消除加工过程中产生的内应力,提高材料的硬度和耐磨性。
二、表面处理表面处理是压铸模具钢热处理的第二步,其目的是提高模具表面的硬度和耐磨性,增加模具的使用寿命。
表面处理通常包括以下方法:1. 渗碳:渗碳是将钢在渗碳介质中加热,使碳原子渗入钢的表面,形成一层高碳层,从而提高表面的硬度和耐磨性。
2. 氮化:氮化是将钢在氮化介质中加热,使氮原子渗入钢的表面,形成一层高氮层,从而提高表面的硬度和耐磨性。
3. 镀铬:镀铬是在钢表面电镀一层铬层,以提高表面的硬度和耐磨性。
镀铬层具有很高的硬度和耐腐蚀性,可以显著提高模具的使用寿命。
三、最终热处理最终热处理是压铸模具钢热处理的最后一步,其目的是进一步提高模具的整体硬度和耐磨性,优化模具的性能。
最终热处理通常包括以下步骤:1. 高温回火:高温回火是将钢加热到一定温度,保温一段时间,然后缓慢冷却的过程。
高温回火可以消除内应力,提高材料的稳定性和韧性,优化模具的性能。
2. 淬火:淬火是将钢加热到一定温度,保温一段时间,然后快速冷却的过程。
淬火可以显著提高模具的硬度和耐磨性,优化模具的性能。
淬火过程中应控制好淬火温度和时间,以避免产生裂纹和变形。
3. 回火:淬火后的模具需要进行回火处理,以消除淬火过程中产生的内应力,稳定材料的组织和性能,优化模具的性能。
回火温度和时间应根据材料和要求的不同而有所区别。
热处理材料的性能及使用
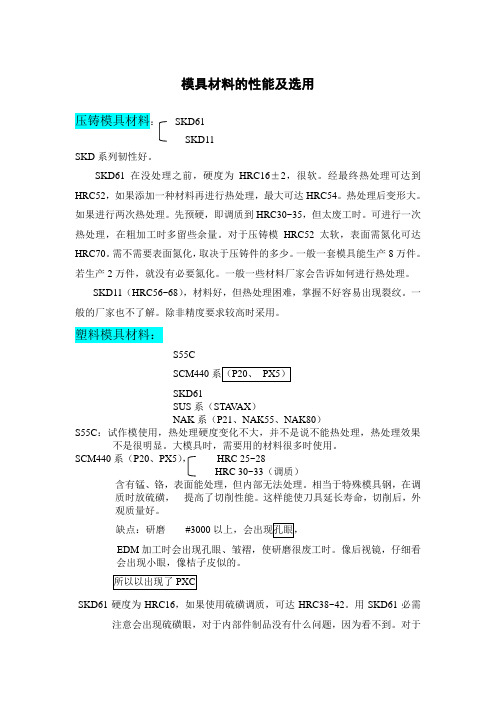
模具材料的性能及选用压铸模具材料:SKD61SKD11SKD系列韧性好。
SKD61在没处理之前,硬度为HRC16±2,很软。
经最终热处理可达到HRC52,如果添加一种材料再进行热处理,最大可达HRC54。
热处理后变形大。
如果进行两次热处理。
先预硬,即调质到HRC30~35,但太废工时。
可进行一次热处理,在粗加工时多留些余量。
对于压铸模HRC52太软,表面需氮化可达HRC70。
需不需要表面氮化,取决于压铸件的多少。
一般一套模具能生产8万件。
若生产2万件,就没有必要氮化。
一般一些材料厂家会告诉如何进行热处理。
SKD11(HRC56~68),材料好,但热处理困难,掌握不好容易出现裂纹。
一般的厂家也不了解。
除非精度要求较高时采用。
塑料模具材料:S55CSCM440SKD61SUS系(STA V AX)NAK系(P21、NAK55、NAK80)S55C:试作模使用,热处理硬度变化不大,并不是说不能热处理,热处理效果不是很明显。
大模具时,需要用的材料很多时使用。
SCM440系(P20、PX5),HRC 25~28HRC 30~33(调质)含有锰、铬,表面能处理,但内部无法处理。
相当于特殊模具钢,在调质时放硫磺,提高了切削性能。
这样能使刀具延长寿命,切削后,外观质量好。
缺点:研磨#3000EDM加工时会出现孔眼、皱褶,使研磨很废工时。
像后视镜,仔细看会出现小眼,像桔子皮似的。
SKD61硬度为HRC16,如果使用硫磺调质,可达HRC38~42。
用SKD61必需注意会出现硫磺眼,对于内部件制品没有什么问题,因为看不到。
对于HRC40 HRC40 HRC33HRC33硬度为HRC38~42的材料,已经含有硫磺,所以再热处理也不会有很大的改善,可表面氮化,但韧性很好。
HRC45、HRC52,适用于冲压模具,加工方式为线切割或铣削。
STA V AX 系(SUS 系),不锈钢,分HRC15、HRC33、HRC52HRC15,很少有卖的。
项目16压铸材料选择与技术要求

模具所有活动部件,应保证位置准确,动作可靠,不得有歪
01
斜和卡滞的现象。相对固定的零件之间不允许窜动。
浇道转接处应光滑连接,镶拼处应紧密,未注脱模斜度不小
02
于5°,表面粗糙度Ra不大于0.4μm。
滑块运动应平稳,合模后滑块与楔紧块应压紧,接触面积不
03
小于3/4,开模后定位准确可靠。
合模后分型面应紧密贴
6~7级 6~7级
≤0.05m
表面粗糙度:
压铸模结构零件的表面粗糙度直接影响到各机构的正常 工作和模具使用寿命。成型零件的表面粗糙度以及加工 后遗留的加工痕迹及方向,直接影响到铸件表面质量, 脱模的难易,甚至是导致成型零件表面产生裂纹的起源。 表面粗糙也是产生金属粘附的原因之一。
各种结构件工作部位推荐的表面粗糙度
套板两平面的平行度 镶块相对两侧面和分型面对其底面的平行度
套板内镶块孔的轴线与分型面的端面圆跳动 圆形镶块的轴线对其端面的圆跳动
镶块的分型面、滑块的密封面、组合拼块的组合面等表面的平面度
选用精度
5~6级 5~6级 6~7级 圆孔6级,非圆孔7~8级
5~6级 5~6级 6~7级 7~8级 7~8级
5级 5级
处理,氮化层深度为0.08~0.15mm,硬度≥600HV。
压铸模材料的热处理要求:
压铸模成型部位(动、定模镶块、型芯等)及浇注系统使用的热模 钢必须进行热处理,为保证热处理质量,避免出现畸变、开裂、脱 碳、氧化和腐蚀等疵病,可在盐浴炉,保护气氛炉装箱保护加热或 在真空炉中进行热处理。尤其是在高压气冷真空炉中淬火,质量最 好。
单击添加副标题
项目16压铸材料 选择与技术要求
项目实施
单击此处添加文本具体内容,简明扼要地阐述你的观点
- 1、下载文档前请自行甄别文档内容的完整性,平台不提供额外的编辑、内容补充、找答案等附加服务。
- 2、"仅部分预览"的文档,不可在线预览部分如存在完整性等问题,可反馈申请退款(可完整预览的文档不适用该条件!)。
- 3、如文档侵犯您的权益,请联系客服反馈,我们会尽快为您处理(人工客服工作时间:9:00-18:30)。
压铸模具材料选择和热处理要求
压铸模的使用寿命与压铸模的材质密切相关。
压铸模零、部件主要分为与金属液接触的零部件、滑动配合零部件和模架结构零件。
压铸模型腔与浇道等部件在金属的压力铸造生产过程中,直接与高温、高压、高速的金属液相接触。
一方面受到金属液的直接冲刷、磨损、高温氧化和各种腐蚀。
另一方面由于生产的高效率,模具温度的升高和降低非常剧烈,并形成周期性的变化。
因此,压铸模的工作环境十分恶劣。
所以,在选择压铸模的制造材料时就应当予以注意。
①具有良好的可锻性和切削性。
②高温下具有较高的红硬性、高温强度、抗回火稳定性和冲击韧度。
③具有良好的导热性和抗疲劳性。
④具有足够的高温抗氧化性。
⑤热膨胀系数小。
⑥具有高的耐磨性和耐蚀性。
⑦具有良好的淬透性和较小的热处理变形率。
压铸模成型零件(动、定模镶块、型忒等)及浇注系统零件使用的热作模具钢必须进行热处理。
为保证热处理质量,避免出现畸变、开裂、脱碳、氧化和腐蚀等疵病,可在盐浴炉,保护气氛炉装箱保护加热或在真空炉中进行热处理。
尤其是在高压气冷真空炉中淬火,质量最好。
淬火前应进行一次除应力退火处理,以消除加工时残留的应力,减少淬火时的变形程度及开裂危险。
淬火加热宜采用两次预热,然后加热到规定温度,保温一段时间,然后油淬或气淬。