连续铸造介绍(Continuous Casting)
连续铸造技术详解-精

单晶连 续铸造
1.溶液 2.冷却水 3.铸型 4.冷却水喷嘴 5.铸锭 6.气孔 7.电炉丝 8.加热铸型 9.液体膜 10.单晶铸锭
铝合金的连铸
铝合金的连铸
铝合金的连铸
铝合金的连铸
铜合金的连铸
金属间化合物的连铸
铸铁的连铸
10 9
8 7 65 4 3
2
1
1.引导杆 2.启动棒 3.石墨结晶器 4.水冷却器
Compact strip production
Inline strip production
漏斗形结晶器
塞棒
中间包座砖 中间包钢板
立
浸入式水口
弯
宽面平行铜板
式Hale Waihona Puke 垂直部分结晶
器
弧形部分,结晶 器中心R=5m
空心圆管坯的连铸
单晶连铸
普通连铸和单晶连铸凝固方式的比较
普通连 续铸造
连铸机种类
➢立式连铸 ➢立弯式连铸机 ➢弧形连铸机 ➢水平连铸机
立式连铸(垂直连铸)
立式连铸
立式连铸
在结晶器的下端插入引
锭,形成结晶器的底,
当浇入的金属液面达一
定高度后,开动拉锭装
置,使铸锭随引锭下降,
上面不断浇入金属,下
面连续拉出铸锭。
连续铸锭示意图 1-浇包 2-浇口杯 3-结晶器 4-铸锭 5-引锭
立式连铸
将铁水浇入内外结 晶器之间的间隙中 (间隙大小即铸管 的壁厚)结晶器上 下振动,从结晶器 下方,下断地拉出 管子。
连续铸管凝固示意图
1-内结晶器 2-未凝固层 3-凝固层 4-转动浇杯 5-外结晶器
连续铸管机示意图
1-内结晶器支架 2-转动 浇杯 3-内结晶器 4-浇 杯流槽 5-外结晶器 6- 承口铁芯 7-铁水包 8- 振动装置 9-铁管 10-重 锤 11-承口底盘 12-升 降盘 13-导轨 14-电机
连续铸造及其与轧制的衔接工艺

连续铸造及其与轧制的衔接工艺1. 引言连续铸造是一种现代化的铸造工艺,它与传统的间歇铸造相比具有更高的生产效率和质量控制能力。
随着工业技术的发展,连续铸造在轧制过程中的应用也越来越广泛。
本文将介绍连续铸造的基本原理和与轧制的衔接工艺。
2. 连续铸造的原理连续铸造是通过在连铸机上连续铸造金属坯料,将熔融金属倒入预先制备好的连续浇注铸模中,经过一系列冷却和凝固过程,最终形成所需的连续坯料。
连续铸造具有以下几个主要特点:•产量高:连续铸造可以实现连续、自动化生产,生产效率高于传统的间歇铸造。
•质量可控:由于冷却和凝固过程的控制,连续铸造可以获得均匀的结晶组织,从而提高材料的力学性能和物理性能。
•节省能源:连续铸造的过程中可以充分利用余热和余能,提高能源利用效率。
3. 轧制与连续铸造的衔接工艺在连续铸造生产的金属坯料经过冷却和凝固后,需要进行进一步的加工,其中轧制是最常用的一种加工方式。
轧制是利用辊轧机将金属坯料进行塑性变形,最终得到所需的板材、型材或管材。
轧制与连续铸造的衔接工艺主要包括以下几个步骤:3.1 金属坯料的预热在连续铸造后的金属坯料中,由于冷却和凝固过程的影响,金属坯料温度较低,不利于轧制操作。
因此,需要对金属坯料进行预热处理,将其温度提高到适合轧制的范围。
3.2 理化性能测试在进行轧制前,需要对金属坯料进行理化性能测试,以确保其符合轧制要求。
测试项目包括金属材料的化学成分、力学性能和物理性能等。
3.3 轧制机的调试轧制机是进行轧制操作的关键设备,调试工作包括辊轧机的调整和辊轧力的设定,以保证轧制过程中金属坯料的塑性变形符合要求。
3.4 轧制过程的控制轧制过程中,需要对金属坯料的温度、厚度、宽度等进行实时监控和控制。
一般采用自动控制系统,通过传感器和控制算法,对轧制参数进行调整,以实现所需的轧制结果。
3.5 轧制后的检验和修整轧制后的金属板材、型材或管材需要进行质量检验,包括外观质量、尺寸精度和力学性能等。
连续铸钢工艺教程
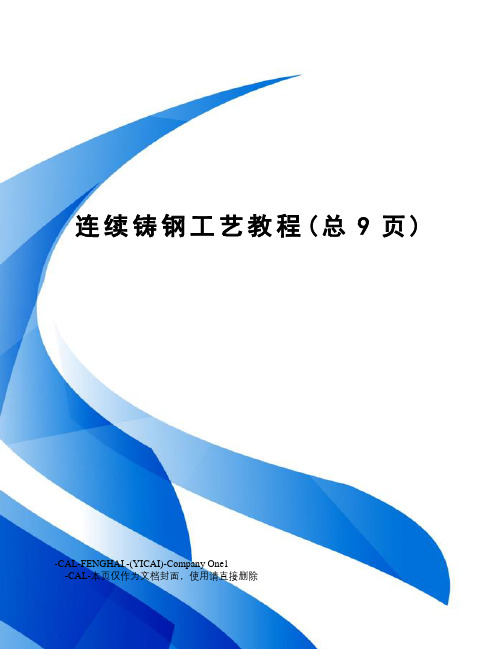
连续铸钢工艺教程(总9页) -CAL-FENGHAI.-(YICAI)-Company One1-CAL-本页仅作为文档封面,使用请直接删除连续铸钢工艺教程1.连铸工艺1.1连铸工艺介绍连铸全称连续铸钢,与模铸不同,它不是将高温钢水浇铸到一个个的钢锭模内,而是将高温钢水浇注到一个或几个用强制水冷、带有“活底”(叫引锭头)的铜模内(叫结晶器),钢水很快与“活底”凝结在一起,待钢水凝固成一定厚度的坯壳后,就从铜模的下端拉出“活底”,这样已凝固成一定厚度的铸坯就会连续不断地从水冷结晶器内被拉出来,,在二次冷却区继续喷水冷却,带有液芯的铸坯一边走一边凝固,直到完全凝固,待铸坯完全凝固后,用氧气切割或剪切机把铸坯切成一定尺寸的钢坯。
连铸是连接炼钢和轧钢的中间环节,是炼钢生产的重要组成部分,连铸生产的正常与否,不但会影响到炼钢生产任务的完成,还会影响到轧材的质量和成材率。
一台连铸机主要由大包回转台、中间包、中间包车、结晶器、结晶器振动装置、二次冷却装置、拉坯矫直装置、切割装置和出坯辊道等部分组成。
在连铸生产时通常用天车将钢包吊至大包回转台,然后大包转台将钢包旋至浇注位,经大包底部水口把钢水注入到中间包内,打开中间包塞棒后,钢水流入到下口用引锭杆堵塞并能上下振动的结晶器中,钢水沿结晶器周边冷凝成坯壳,当结晶器下端出口处坯壳有一定厚度时,带有液芯并和引锭杆连在一起的铸坯在拉矫装置的作用下,离开结晶器,沿着二冷段的支撑结构下移,与此同时铸坯被二次冷却装置进一步冷却并继续凝固,当引锭装置进入拉矫机后脱去引锭装置,铸坯在全部凝固或带有液芯的状态下被矫直,随后在水平位置被切割成定尺长度,经出坯辊道运送到规定地点,上述整个过程在实际生产中是连续进行的。
1.3连铸的主要设备1.3.1钢包回转台钢包回转台设置在电炉、精炼同一跨,它的本体是一个具有两个钢包支撑架的转臂,绕回转台中心回转,钢包回转台工作时,出钢跨一侧的天车将盛满钢水的钢包吊放到支撑架上,然后回转台旋转180o,将钢包转到连铸跨中间包上方的浇注位进行浇注,浇注完毕,再把空包转出的同时,又把另一个盛满钢水的钢包旋转到浇注位置,这样就可以快速更换钢包,实现多炉连浇。
第四章-连续铸造
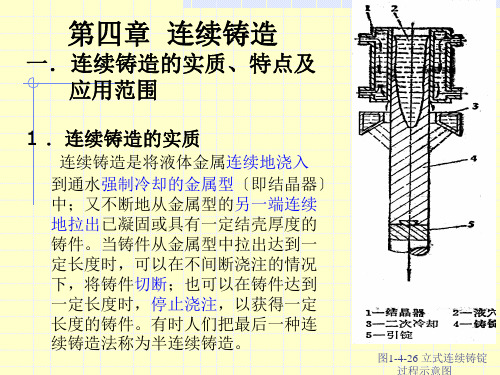
2 优缺点:
(1)铸件迅速冷却,其结晶细,组织较致密。连续浇注、 结晶的过程又会使铸件在整个长度上的组织均匀。 (2) 因无浇冒口,可节省金属消耗。 (3)生产工序简单;生产过程易于机械化,自动化,生产 效率高。 (4) 如把连续铸造获得的高温铸锭,立即进行轧制加工, 则可省去一般轧制前对铸锭的加热工序,故可大大地节省能 源,还可提高生产效率。 (5) 应用范围有一定局限性,只能生产断面不变的长铸 件。
2.1工艺过程 : 卧式连续铸 绽机上,结晶器轴线水平布置,在其型腔部 位是一石墨衬套。结晶器一端与保温炉相连,故液体金属可自 动地充填结晶器型腔。 铸锭的拔出是脉冲 式的,即拔出一定 长度后,稍停,再 拨,如此周而复地 进行。铸锭的拔出 速度由夹辊的转数 控制,当铸锭达到 一定长度时,飞锯 架以与铸锭相同的 速度往右移动,同 时飞锯进刀将铸锭 切断。 图1-4-27 卧式连续铸锭过程示意图
2.2 特点: 卧式连续铸锭厂房高度较低,机器均设在地面上,可 • 节省基建投资, 。 结构简单,易于维修, • 于液体金属可由保温炉直接进入结晶器,可防止产生 • 氧化、夹杂。 不足之处是所需车间面积较大。 •
2.3 应用: 这种方法常用于生产紫铜锭、铜合金锭、 铝合金锭及铸铁坯件等。铸锭的直径由几十毫米至500毫 米。也可用于生产中空厚壁管、板材及线材等。一台机器 的年产量可达数千吨。
第四章 连续铸造
一.连续铸造的实质、特点及 应用范围
1 .连续铸造的实质
连续铸造是将液体金属连续地浇入 到通水强制冷却的金属型〔即结晶器〕 中;又不断地从金属型的另一端连续 地拉出已凝固或具有一定结壳厚度的 铸件。当铸件从金属型中拉出达到一 定长度时,可以在不间断浇注的情况 下,将铸件切断;也可以在铸件达到 一定长度时,停止浇注,以获得一定 长度的铸件。有时人们把最后一种连 续铸造法称为半连续铸造。
连铸计算公式大全

连铸计算公式大全连铸(Continuous Casting)是一种金属加工工艺,用于生产连续长度的金属坯料。
在连铸过程中,液态金属被直接铸造成坯料,而不需要通过传统的浇铸过程。
连铸计算涉及到多个方面,包括熔炼过程、铸模设计、冷却和结晶过程等。
以下是一些可能涉及的连铸计算公式的示例:1. 铸坯截面积计算公式:A = L ×W其中:A -铸坯截面积L -铸坯长度W -铸坯宽度2. 铸坯体积计算公式:V = A ×H其中:V -铸坯体积A -铸坯截面积H -铸坯高度3. 结晶器截面积计算公式:A_mold = π×(D/2)²其中:A_mold -结晶器截面积D -结晶器直径4. 结晶器长度计算公式:L_mold = (8 ×V_mold) / (π×D_mold)其中:L_mold -结晶器长度V_mold -结晶器内腔体积D_mold -结晶器内腔直径5. 冷却水流量计算公式:Q = C ×A ×ΔT/Δt其中:Q -冷却水流量C -冷却水比热容A -冷却面积ΔT -冷却前后温度差Δt -时间间隔这些公式只是连铸计算中的一部分,实际生产中还需要考虑其他因素,如钢种、浇铸温度、浇铸速度等。
在实际应用中,需要根据具体生产情况选择合适的计算公式并进行相应参数的调整。
这只是连铸计算中的一小部分公式示例,实际的计算可能涉及到更多的参数和方程,具体取决于金属类型、连铸机型号、操作条件等因素。
在实际应用中,专业的冶金工程师通常会根据具体情况进行计算和优化。
连续浇铸法
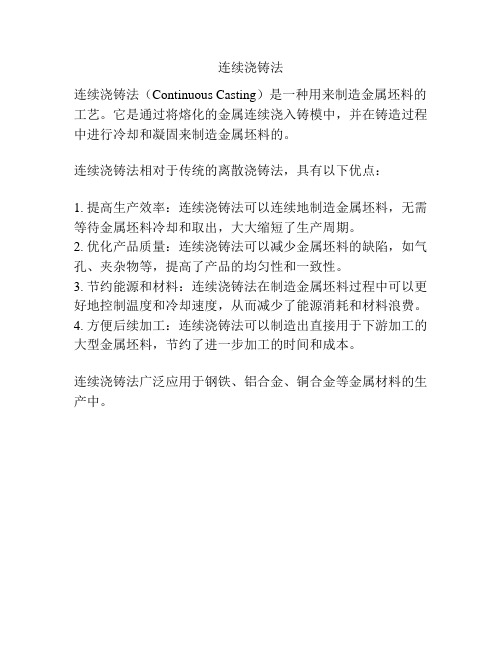
连续浇铸法
连续浇铸法(Continuous Casting)是一种用来制造金属坯料的工艺。
它是通过将熔化的金属连续浇入铸模中,并在铸造过程中进行冷却和凝固来制造金属坯料的。
连续浇铸法相对于传统的离散浇铸法,具有以下优点:
1. 提高生产效率:连续浇铸法可以连续地制造金属坯料,无需等待金属坯料冷却和取出,大大缩短了生产周期。
2. 优化产品质量:连续浇铸法可以减少金属坯料的缺陷,如气孔、夹杂物等,提高了产品的均匀性和一致性。
3. 节约能源和材料:连续浇铸法在制造金属坯料过程中可以更好地控制温度和冷却速度,从而减少了能源消耗和材料浪费。
4. 方便后续加工:连续浇铸法可以制造出直接用于下游加工的大型金属坯料,节约了进一步加工的时间和成本。
连续浇铸法广泛应用于钢铁、铝合金、铜合金等金属材料的生产中。
铸造机械 术语 第1部分:基本术语-最新国标
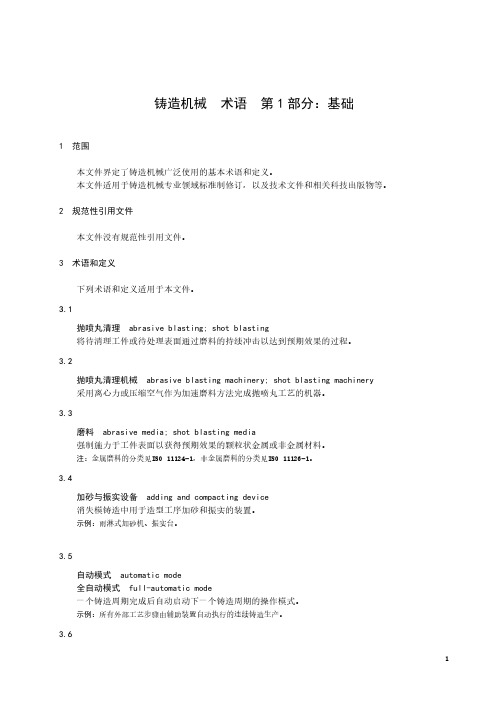
铸造机械术语第1部分:基础1范围本文件界定了铸造机械广泛使用的基本术语和定义。
本文件适用于铸造机械专业领域标准制修订,以及技术文件和相关科技出版物等。
2规范性引用文件本文件没有规范性引用文件。
3术语和定义下列术语和定义适用于本文件。
抛喷丸清理abrasive blasting;shot blasting将待清理工件或待处理表面通过磨料的持续冲击以达到预期效果的过程。
抛喷丸清理机械abrasive blasting machinery;shot blasting machinery采用离心力或压缩空气作为加速磨料方法完成抛喷丸工艺的机器。
磨料abrasive media;shot blasting media强制施力于工件表面以获得预期效果的颗粒状金属或非金属材料。
注:金属磨料的分类见ISO11124-1,非金属磨料的分类见ISO11126-1。
加砂与振实设备adding and compacting device消失模铸造中用于造型工序加砂和振实的装置。
示例:雨淋式加砂机、振实台。
自动模式automatic mode全自动模式full-automatic mode一个铸造周期完成后自动启动下一个铸造周期的操作模式。
示例:所有外部工艺步骤由辅助装置自动执行的连续铸造生产。
12间歇式混砂机batch sand mixer;batch sand mill用于分批次混制(搅拌、包覆、捏合)包括有粘结剂、水和附加物的型砂或芯砂的机器。
注:机器通常由装有刮板和/或辗轮,以及混/松砂转子的圆筒形容器组成。
粘结剂binder;bonding substance具有粘结性能,在铸造生产中主要用于配制型(芯)砂以及涂料、型芯胶粘剂等的材料。
注:铸造用粘结剂通常分为无机和有机两大类,也可分为粘土粘结剂和非粘土粘结剂。
配料burdening<熔炼>根据铸造用金属化学成分要求、炉料实际情况和熔炼过程中合金元素的变化,确定各种金属炉料配比的过程。
Chapter 14 Continuous casting of steel

From structure scheme of casting machine
From section of strand:
• It is a simple matter to differentiate between flat products, which are derived from slabs, and long products, which are derived from bloom and billets. • A width-to-thickness aspect ratio of 2.5/ 1 could be taken as the division between flat and long products.
连铸与模铸工艺流程对比
与模铸—初轧开坯工艺相比,连铸铸钢工艺具有如 下优点: (1)简化了铸坯生产的工艺流程,省去了模铸工艺 的脱模、整模、钢锭均热和开坯工序。流程基建投 资可节省40%,占地面积可减小30%,操作费用可 节省40%,耐火材料的消耗可减少15%。 (2)金属收得率高: 与模铸工艺生产钢锭的切头切尾损失10-20%相比, 金属收得率提高约8-14%(其中:板坯约10.5%, 大方坯约13%,小方坯约14%)。
14.3 Types and Anatomy of Continuous Casting Machines
14.3.1 Types of Casting Machines
按一般习惯,连铸机分类为: (1)按连铸机外形分类有:立式连铸机、立弯式连铸机、弧形 连铸机、超低头(椭圆形)连铸机、水平连铸机、轮式连铸 机等。 (2)按浇注铸坯断面分类有:方坯连铸机、板坯连铸机、圆坯 连铸机、异形坯连铸机、方、板坯兼用连铸机。 (3)按拉速分类有:高拉速连铸机和低拉速连铸机。 (4)按钢水静压头分类有:高头型连铸机(如立式、立弯式连 铸机)和低头连铸机(如弧形、椭圆形、水平连铸机)。
- 1、下载文档前请自行甄别文档内容的完整性,平台不提供额外的编辑、内容补充、找答案等附加服务。
- 2、"仅部分预览"的文档,不可在线预览部分如存在完整性等问题,可反馈申请退款(可完整预览的文档不适用该条件!)。
- 3、如文档侵犯您的权益,请联系客服反馈,我们会尽快为您处理(人工客服工作时间:9:00-18:30)。
A: Liquid metal. B: Solidified metal. C: Slag. D: Water-cooled copper plates. E: Refractory material.
Equipment and Process
• The steel is taken poured into water cooled vertical cooper moulds, which is 450 to 750 mm long. • Before starting the casting a dummy starter bar (引锭杆 ) is kept in the moulds bottom. • After starting the casting process as the metal level rises in the mould to a desirable height, the starter bar is withdrawn at a rate equal to the steel pouring rate.
Mold
• The working surface of the copper face is often plated镀 with chromium铬 or nickel to provide a harder working surface, and to avoid copper pickup on the surface of the cast strand • Friction between the shell and mold is reduced through the use of mold lubricants such as oils or powdered fluxes粉剂. • Mold oscillation(震荡)is necessary to minimize friction and sticking of the solidifying shell, and avoid shell tearing, and liquid steel breakouts, which can wreak havoc造成严重破坏 on equipment and machine downtime due to clean up and repairs. • Oscillation is achieved either hydraulically or via motor-driven cams or levers which support and reciprocate往复运动 (or oscillate) the mold.
Equipment and Process
• The skin formed in the mould is about 10 to 25 mm in thickness and is further solidified by intensive cooling with water spays as casting processes. • Feeds liquid steel continuously into a short, water-cooled vertical copper mold and, at the same time, continuously withdraws the frozen shell, including the liquid steel it contains.
As unbending occurs, the solid shell outer radius外径 is under tension拉力, while the inner radius is under compression. The resulting strain is dictated by the arc radius along with the mechanical properties of the cast steel grade. If the strain along the outer radius is excessive, cracks could occur, seriously affecting the quality of the steel. These strains are typically minimized by incorporating合并 a multi-point unbending process, in which the radii半径 become progressively larger in order to gradually straighten the product into the horizontal plane.
Continuous Cast Shapes
Bloom or Billet Rounds
Slab(variable thickness)
Beam blank
Dummy Bar(引锭杆)
• Functions: • to close off the base of the mould. • Metal is poured into the mould and withdrawn with the dummy bar once it solidifies.
Equipment and Process
1: Ladle. 2: Stopper. 3: Tundish浇铸盘. 4: Shroud保护罩. 5: Mold. 6: Roll support 轧辊支架. 7: Turning zone转折带. 8: Shroud. 9: Bath level炉浴面. 10: Meniscus弯液面. 11: Withdrawal unit 提取单元. 12: Slab.板坯
Bending and Straightening
Curved Section of MultiStraightener Strand Beam Blank Caster Withdrawal Units for prior to Unbending Strand Unbending
After straighten process
– Distribute liquid steel to the molds – Enhances oxide inclusion separation – Provides a continuous、constant and stable flow of liquid steel to the mold during ladle exchanges
Introduction
• Generally the starting point of any structural steel product is the ingot, which is subsequently rolled through number of mills before a final product. • Continuous casting has changed that scenario by directly casting billet(坯料), bloom(钢坯), and slab(板坯) without going through the rolling process and this process is fast and also economical.
The dummy bar should be corresponded to the casting path
Dummy Bar
Rigid type
Chain structure : more flexible to be corresponded to the casting path
Tundish
Mold
• Stucture:ope n-ended box structure, containing a water-cooled inner lining fabricated from a high purity copper alloy.
Mold
• Function:to establish a solid shell sufficient in strength to contain its liquid core.
Introduction
• Continuous casting is the process whereby molten metal is solidified into a "semifinished " billet, bloom, or slab for subsequent rolling in the finishing mills(精 轧机). • This process is used most frequently to cast steel. Aluminums and copper are also continuously cast.ters
Continuous Cast Shapes
Depending on the product end-use, various shapes are cast .In recent years, the melting/casting/rolling processes have been linked while casting a shape that substantially conforms to the finished product. The Near-NetShape cast section has most commonly been applied to Beams and Flat Rolled products, and results in a highly efficient operation.