加工参数计算公式
加工中心常用计算公式

CNC常用计算公式一、三角函数计算1.tanθ=b/aθ=tan-1b/a2.Sinθ=b/c Cos=a/c二、切削速度的计算Vc=(π*D*S)/1000Vc:线速度(m/min) π:圆周率(3.14159) D:刀具直径(mm) S:转速(rpm)例题. 使用Φ25的铣刀Vc为(m/min)25 求S=?rpmVc=πds/100025=π*25*S/1000S=1000*25/ π*25S=320rpm三、进给量(F值)的计算F=S*Z*FzF:进给量(mm/min) S:转速(rpm) Z:刃数Fz:(实际每刃进给)例题.一标准2刃立铣刀以2000rpm)速度切削工件,求进给量(F 值)为多少?(Fz=0.25mm)F=S*Z*FzF=2000*2*0.25F=1000(mm/min)四、残料高的计算Scallop=(ae*ae)/8RScallop:残料高(mm) ae:XY pitch(mm) R刀具半径(mm) 例题. Φ20R10精修2枚刃,预残料高0.002mm,求Pitch为多少?mmScallop=ae2/8R0.002=ae2/8*10ae=0.4mm五、逃料孔的计算Φ=√2R2X、Y=D/4Φ:逃料孔直径(mm) R刀具半径(mm) D:刀具直径(mm) 例题. 已知一模穴须逃角加工(如图),所用铣刀为ψ10;请问逃角孔最小为多少?圆心坐标多少?Φ=√2R2Φ=√2*52Φ=7.1(mm)X、Y=D/4X、Y=10/4X、Y=2.5 mm圆心坐标为(2.5,-2.5)六、取料量的计算Q=(ae*ap*F)/1000Q:取料量(cm3/min)ae:XY pitch(mm) ap:Z pitch(mm)例题. 已知一模仁须cavity等高加工,Φ35R5的刀XY pitch是刀具的60%,每层切1.5mm,进给量为2000mm/min,求此刀具的取料量为多少?Q=(ae*ap*F)/1000Q=35*0.6*1.5*2000/1000Q=63 cm3/min七、每刃进给量的计算Fz=hm * √(D/ap )Fz:实施每刃进给量hm:理论每刃进给量 ap:Z pitch(mm)D:刀片直径(mm)例题 (前提depo XY pitch是刀具的60%)depoΦ35R5的刀,切削NAK80材料hm为0.15mm,Z轴切深1.5mm,求每刃进给量为多少?Fz=hm * √(D/ap )Fz=0.2*√10/1.5Fz=0.5mm冲模刀口加工方法刀口加工深度=板厚-刀口高+钻尖(0.3D)D表示刀径钻头钻孔时间公式T(min)=L(min)/N(rpm)*f(mm/rev)=πDL/1000vfL:钻孔全长N:回转数f:进刀量系数D:钻头直径v:切削速度如图孔深l钻头孔全长L则L=l+D/3T=L/Nf=πDL/1000vf系数表f直径mm进刀mm/rev1.6~3.2 0.025~0.0753.2~6.4 0.05~0.156.4~12.8 0.10~0.2512.8~25 0.175~0.37525以上0.376~0.6251英寸=25.4mm=8分25.4/牙数=牙距管牙计算公式例如25.4/18=1.414牙距为5/16丝攻马力(枪钻)W=Md*N/97.410W:所要动力(KW)Md:扭矩(kg-cm)N:回转数(r.p.m)扭矩计算公式如下:Md=1/20*f*ps*f为进给量mm/rev系数r为钻头半径赛(mm)α:切削抵抗比值ps.在小进给时,一般钢为500kg/m㎡;一般铸铁为300kg/m㎡;。
加工中心切削转速和进给速度计算方法及公式
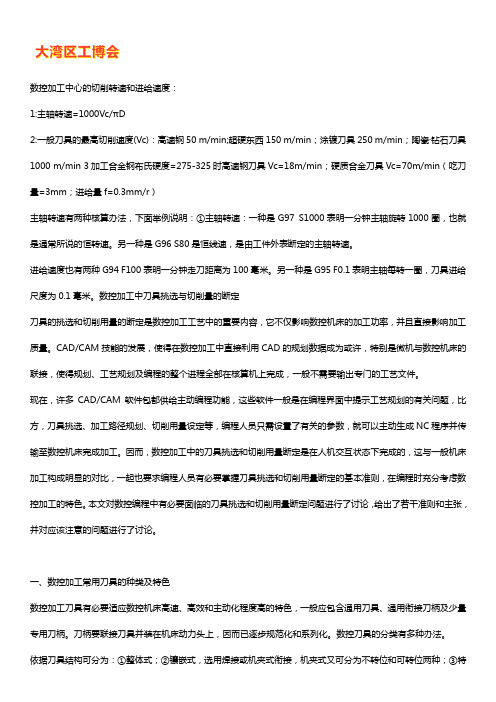
数控加工中心的切削转速和进给速度:1:主轴转速=1000Vc/πD2:一般刀具的最高切削速度(Vc):高速钢50 m/min;超硬东西150 m/min;涂镀刀具250 m/min;陶瓷·钻石刀具1000 m/min 3加工合金钢布氏硬度=275-325时高速钢刀具Vc=18m/min;硬质合金刀具Vc=70m/min(吃刀量=3mm;进给量f=0.3mm/r)主轴转速有两种核算办法,下面举例说明:①主轴转速:一种是G97 S1000表明一分钟主轴旋转1000圈,也就是通常所说的恒转速。
另一种是G96 S80是恒线速,是由工件外表断定的主轴转速。
进给速度也有两种G94 F100表明一分钟走刀距离为100毫米。
另一种是G95 F0.1表明主轴每转一圈,刀具进给尺度为0.1毫米。
数控加工中刀具挑选与切削量的断定刀具的挑选和切削用量的断定是数控加工工艺中的重要内容,它不仅影响数控机床的加工功率,并且直接影响加工质量。
CAD/CAM技能的发展,使得在数控加工中直接利用CAD的规划数据成为或许,特别是微机与数控机床的联接,使得规划、工艺规划及编程的整个进程全部在核算机上完成,一般不需要输出专门的工艺文件。
现在,许多CAD/CAM软件包都供给主动编程功能,这些软件一般是在编程界面中提示工艺规划的有关问题,比方,刀具挑选、加工路径规划、切削用量设定等,编程人员只需设置了有关的参数,就可以主动生成NC程序并传输至数控机床完成加工。
因而,数控加工中的刀具挑选和切削用量断定是在人机交互状态下完成的,这与一般机床加工构成明显的对比,一起也要求编程人员有必要掌握刀具挑选和切削用量断定的基本准则,在编程时充分考虑数控加工的特色。
本文对数控编程中有必要面临的刀具挑选和切削用量断定问题进行了讨论,给出了若干准则和主张,并对应该注意的问题进行了讨论。
一、数控加工常用刀具的种类及特色数控加工刀具有必要适应数控机床高速、高效和主动化程度高的特色,一般应包含通用刀具、通用衔接刀柄及少量专用刀柄。
车床每转进给计算公式(一)

车床每转进给计算公式(一)
车床每转进给
概述
车床每转进给是机床加工过程中一个重要的参数,表示车削工具
在车床上每转动一周所移动的距离。
它是计算和控制车削过程中切削
速度和进给速度的关键参数。
计算公式
车床每转进给可以用以下公式来计算:
车床每转进给(mm/r)= 主轴进给速度(mm/min)/ 主轴转速
(r/min)
其中,主轴进给速度指的是车削工具在车床上每分钟移动的距离,主轴转速则是指主轴每分钟旋转的圈数。
示例
示例1:
假设主轴进给速度为200 mm/min,主轴转速为100 r/min,那么
根据上述公式,可以计算得到
车床每转进给 = 200 mm/min / 100 r/min = 2 mm/r
这意味着车削工具在车床上每转动一周,将移动2毫米的距离。
示例2:
如果主轴进给速度为500 mm/min,主轴转速为250 r/min,那么
车床每转进给 = 500 mm/min / 250 r/min = 2 mm/r
同样地,车削工具在车床上每转动一周,仍然移动2毫米的距离。
结论
通过计算和控制车床每转进给,可以有效地控制车削过程中的切
削速度和进给速度。
根据实际加工需求,合理调整主轴进给速度和主
轴转速,可以获得更高的加工效率和加工质量。
综上所述,车床每转进给作为机床加工过程中的关键参数,其计
算公式可以帮助我们准确地确定车削过程中切削速度和进给速度的关系。
切削速度和进给速度公式
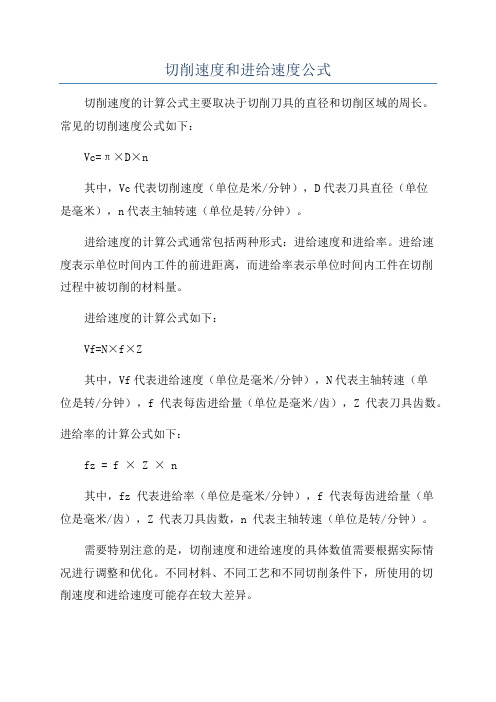
切削速度和进给速度公式切削速度的计算公式主要取决于切削刀具的直径和切削区域的周长。
常见的切削速度公式如下:Vc=π×D×n其中,Vc代表切削速度(单位是米/分钟),D代表刀具直径(单位是毫米),n代表主轴转速(单位是转/分钟)。
进给速度的计算公式通常包括两种形式:进给速度和进给率。
进给速度表示单位时间内工件的前进距离,而进给率表示单位时间内工件在切削过程中被切削的材料量。
进给速度的计算公式如下:Vf=N×f×Z其中,Vf代表进给速度(单位是毫米/分钟),N代表主轴转速(单位是转/分钟),f代表每齿进给量(单位是毫米/齿),Z代表刀具齿数。
进给率的计算公式如下:fz = f × Z × n其中,fz 代表进给率(单位是毫米/分钟),f 代表每齿进给量(单位是毫米/齿),Z 代表刀具齿数,n 代表主轴转速(单位是转/分钟)。
需要特别注意的是,切削速度和进给速度的具体数值需要根据实际情况进行调整和优化。
不同材料、不同工艺和不同切削条件下,所使用的切削速度和进给速度可能存在较大差异。
在实际应用中,切削速度和进给速度的选择通常需要考虑以下几个因素:1.材料硬度:通常情况下,硬度较高的材料需要使用较低的切削速度和进给速度,以避免刀具过快磨损。
2.切削刀具:不同切削刀具的切削速度和进给速度存在一定差异,需根据刀具特性进行选择。
3.机床性能:机床的主轴转速和进给速度对切削速度和进给速度的选择也有一定的限制。
4.切削过程:对于不同的切削过程(如粗加工、精加工等),切削速度和进给速度的选择也存在差异。
总之,切削速度和进给速度是工业加工过程中重要的参数,其选择需要综合考虑材料、刀具、机床和加工要求等方面的因素,并根据实际情况进行调整和优化。
机械加工时间定额的计算公式和方法
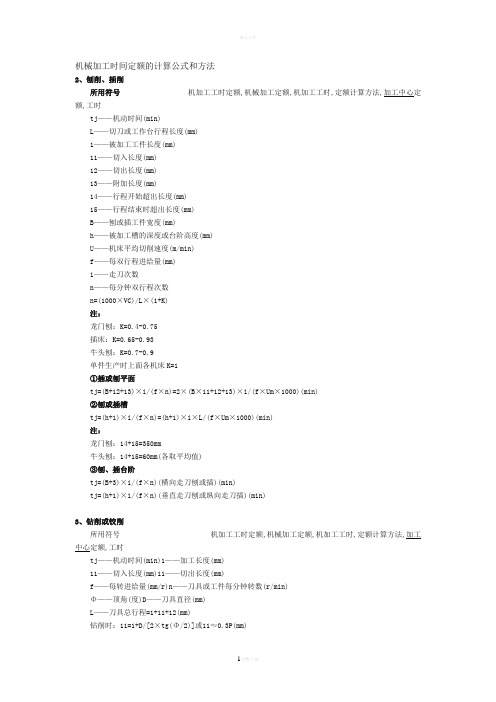
机械加工时间定额的计算公式和方法2、刨削、插削所用符号机加工工时定额,机械加工定额,机加工工时,定额计算方法,加工中心定额,工时tj——机动时间(min)L——切刀或工作台行程长度(mm)1——被加工工件长度(mm)11——切入长度(mm)12——切出长度(mm)13——附加长度(mm)14——行程开始超出长度(mm)15——行程结束时超出长度(mm)B——刨或插工件宽度(mm)h——被加工槽的深度或台阶高度(mm)U——机床平均切削速度(m/min)f——每双行程进给量(mm)i——走刀次数n——每分钟双行程次数n=(1000×VC)/L×(1+K)注:龙门刨:K=0.4-0.75插床:K=0.65-0.93牛头刨:K=0.7-0.9单件生产时上面各机床K=1①插或刨平面tj=(B+12+13)×i/(f×n)=2×(B×11+12+13)×i/(f×Um×1000)(min)②刨或插槽tj=(h+1)×i/(f×n)=(h+1)×i×L/(f×Um×1000)(min)注:龙门刨:14+15=350mm牛头刨:14+15=60mm(各取平均值)③刨、插台阶tj=(B+3)×i/(f×n)(横向走刀刨或插)(min)tj=(h+1)×i/(f×n)(垂直走刀刨或纵向走刀插)(min)3、钻削或铰削所用符号机加工工时定额,机械加工定额,机加工工时,定额计算方法,加工中心定额,工时tj——机动时间(min)1——加工长度(mm)11——切入长度(mm)11——切出长度(mm)f——每转进给量(mm/r)n——刀具或工件每分钟转数(r/min)Φ——顶角(度)D——刀具直径(mm)L——刀具总行程=1+11+12(mm)钻削时:11=1+D/[2×tg(Φ/2)]或11≈0.3P(mm)①一般情况tj=L/f×n(min)②钻盲孔、铰盲孔tj=(1+11)/(f×n)(min)③钻通孔、铰通孔tj=(1+11+12)/(f×n)(min)4、齿轮加工所用符号tj——机动时间(min)B——齿轮宽度(mm)m——齿轮模数(mm)Z——齿轮齿数B——螺旋角(度)h——全齿高(mm)f——每转进给量(mm/r)vf——进给速度(mm/r)g——铣刀线数n——铣刀每分钟转数(r/min)i——走刀次数11——切入长度(mm)12——切出长度(mm)D0——铣刀直径(mm)d——工件节圆直径(mm)f1——工件每转径向进给量(mm)f2——每双行程圆周进给量(mm)t——每齿加工时间(min)nz——加工每齿双行程次数n分——每分钟双行程次数①用齿轮铣刀铣削圆柱齿轮1)铣直齿轮tj=(B+11+12)×Z×i/vf(min)注:(11+12)=d0/(3~4)(mm)2)铣螺旋齿轮机加工工时定额,机械加工定额,机加工工时,定额计算方法,加工中心定额,工时tj=(B/cosβ+11+12)×Z×i/vf(min)注:(11+12)=d0/(3~4)(mm)②用齿轮滚刀滚削圆柱齿轮(1)滚切直齿轮tj=(B+11+12)×Z/(g×f×n)(min)注:(11+12)=d0/(3~4)(2)滚切螺旋齿轮tj=(B/cosβ+11+12)×Z/(g×f×n)(min)注:(11+12)=d0/(3~4)③用模数铣刀铣蜗轮tj=(h+11)×Z/f(min)④用蜗轮滚刀径向滚切蜗轮tj=3×m×Z/(g×n×f)(min)⑤用指状铣刀成形铣齿轮tj=(B+0.5d0+12)/(f×n)=(B+0.5d0+12)/vf(min)注:12=2—5(mm)⑥插圆柱齿轮tj=h/(f1×n)+π×d×i/(f2×n)(min)⑦刨齿机刨圆锥齿轮tj=t×Z×i注:式中,t=nZ/n分(min)n分=1000×Vc/2×LL——刀具行程长度(mm)⑧磨齿tj=Z[L/n0(i/f1+212/f2+213/f)+iτ1+2i2τ2+2i3τ3]将上式查表简化并取平均值为下式tj=Z[L/n0×3.18+0.33](min)式中,L=1+2[h(D-h)+10]1/2——砂轮行程长度(mm)n0——每分钟范成次数D——砂轮直径(mm)h——全齿高i1、i2、i3——粗、半精、精行程次数f1、f2、f3——粗、半精、精每次范成纵向进给量5、铣削机加工工时定额,机械加工定额,机加工工时,定额计算方法,加工中心定额,工时所用符号tj——机动时间(min)L=1+11+12工作台行程长度(mm)1——加工长度(mm)11——切入长度(mm)12——切出长度(mm)Vf——工作台每分钟进给量(mm/min)n——铣刀每分钟转数(r/min)B——铣削宽度(mm)i——走刀次数d0——铣刀直径(mm)D——铣削圆周表面直径(mm)αp——切削深度(mm)β——螺旋角或斜角(度)①圆柱铣刀、圆盘铣刀铣平面、面铣刀铣平面tj=(1+11+12)×i/Vf(min)注:(11+12)=d0/(3~4)(mm)②铣圆周表面tj=D×π×i/vf(min)③铣两端为闭口的键槽tj=(1-d0)×i/vf(min)④铣一端为闭口键槽tj=(1+11)×i/vf(min)⑤铣两端为开口的槽tj=(1+11+12)×i/vf(min)注:11=d0/2+(0.5-1)(mm)12=1-2(mm)⑥铣半圆键槽tj=(1+11)/vf(min)注:1=h——键槽深度(mm)11=0.5-1(mm)⑦按轮廓铣tj=(1+11+12)×i/vf(min)注:1——铣削轮廓长度(mm)11=αp+(0.5-2)12=0-3(mm)⑧铣齿条机加工工时定额,机械加工定额,机加工工时,定额计算方法,加工中心定额,工时1)铣直齿条tj=(B+11+12)×i/vf(min)2)铣斜齿条tj=(B/cosβ+11+12)×i/vf(min)注:以上两式中11+12=d0/(3~4)(mm)⑨铣螺纹1)铣短螺纹tj=L/V周(min)注:式中,L=7πd/6(mm)V周——圆周进给速度(mm/min)d——螺纹外径(mm)2)铣长螺纹tj=d×π×L×g×i/(V周×P)(min)注:式中,L——螺纹长度(mm)g——螺纹头数(mm)p——螺纹升程(度)3)外螺纹旋风铣削tj=L×i/(nW×p)(min)4)内螺纹旋风铣削tj=L×i/(nW×p)(min)注:上两式式中L——被加工螺纹长度(mm)i——走刀次数nW=fZ×n/(d×π)——工件转数P——螺纹升程(mm)fZ——每齿(刀头)的圆周进给量(mm/z)n——铣刀转数(r/min)d——螺纹外(mm)6、用板牙或丝锥加工螺纹tj=[(1+11+12)/p×n+(1+11+12)/p×n1]×i=2×(1+2p)×i/(p×n)(mm)式中,tj——机动时间(mm)1——加工长度(mm)11——切入长度(mm)12——切出长度(mm)p——螺距(mm)n——刀具或工件转数(r/min)n1——刀具或工件返回转数(r/min)7、拉削t1——H/(1000×VC)(min)式中,H——机床调整的冲程长度(mm)8、磨削机加工工时定额,机械加工定额,机加工工时,定额计算方法,加工中心定额,工时所用符号tj——机动时间(min)h——每面加工余量(mm)B——磨轮宽度(mm)f纵——纵向进给量(mm/r)ft——磨削深度进给量(mm)n——工件每分钟转数(r/min)A——切入次数K——光整消除火花修正系数=1.3τ——光整时间(min)L——工件磨削长度(mm)11——工件磨削表面长度(mm)b——工件磨面宽度(mm)VW——工作台往复速度(m/min)fB——磨削宽度进给量(mm)Z——同时加工工件数①外、内圆磨削1)纵向进给磨削tj=2×L×h×K/(n×f纵×ft)(min)2)切入法磨削tj=[h×A/ft+τ]×K=(0.25×A/0.005+0.15)×1.3(min)②平面磨削1)周磨tj=2×L×b×h×K/(1000×VW×FB×ft×Z)(min)注:L=11+20(mm)fB=平均15(mm)ft=0.003-0.085(mm)VW=5-20(m/min)2)端磨tj=h×i/(f双×n双)(min)注:f双——双行程轴向进给量(mm)n双——每分钟双行程数(双程/min)3)无心磨tj=L×i/(0.95×Vf)(min)式中,Vf——轴向进给速度(mm/min)L=1+B(单件)L=n工×1+B(多件连续进给)(mm) 1——工件长度(mm)nZ——连续磨削工件数欢迎您的下载,资料仅供参考!致力为企业和个人提供合同协议,策划案计划书,学习资料等等打造全网一站式需求。
加工参数计算公式

加工参数计算公式
加工参数计算公式是指在机械加工中,根据工件的特性和加工要求,计算出加工参数的公式。
主要包括以下内容:
1. 切削速度计算公式:切削速度=π×直径×转速÷60,其中π取3.14。
2. 进给速度计算公式:进给速度=每齿进给×齿数×转速,其中每齿进给指每个齿槽切削时的进给量,齿数指刀具上的齿数。
3. 切削深度计算公式:切削深度=每齿进给×齿数,其中每齿进给和齿数同上。
4. 切削力计算公式:切削力=切削力系数×主轴转矩÷刀具半径,其中切削力系数是由材料、切削参数等因素确定的常数。
5. 主轴转矩计算公式:主轴转矩=刀具力×刀具半径,其中刀具力由切削力计算公式得出。
6. 切削功率计算公式:切削功率=切削力×切削速度,其中切削力由切削力计算公式得出,切削速度同上。
通过以上公式计算出加工参数,可以保证机械加工过程中的效率和质量,提高生产效益。
- 1 -。
注塑计算公式范文
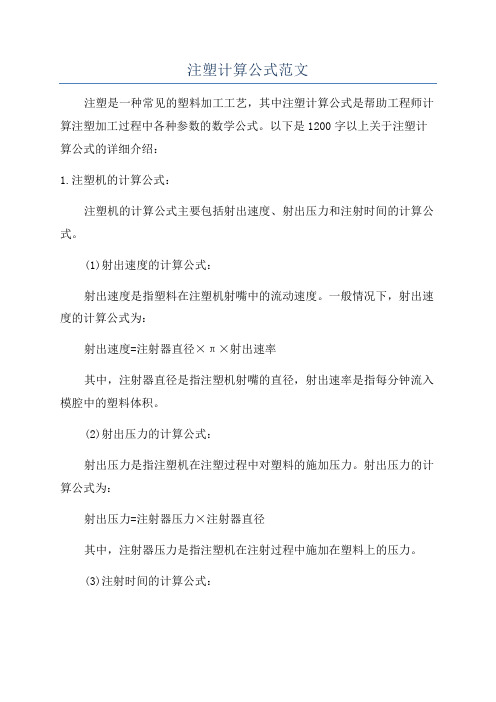
注塑计算公式范文注塑是一种常见的塑料加工工艺,其中注塑计算公式是帮助工程师计算注塑加工过程中各种参数的数学公式。
以下是1200字以上关于注塑计算公式的详细介绍:1.注塑机的计算公式:注塑机的计算公式主要包括射出速度、射出压力和注射时间的计算公式。
(1)射出速度的计算公式:射出速度是指塑料在注塑机射嘴中的流动速度。
一般情况下,射出速度的计算公式为:射出速度=注射器直径×π×射出速率其中,注射器直径是指注塑机射嘴的直径,射出速率是指每分钟流入模腔中的塑料体积。
(2)射出压力的计算公式:射出压力是指注塑机在注塑过程中对塑料的施加压力。
射出压力的计算公式为:射出压力=注射器压力×注射器直径其中,注射器压力是指注塑机在注射过程中施加在塑料上的压力。
(3)注射时间的计算公式:注射时间是指注塑机注射塑料的时间,也就是注射器的运转周期。
注射时间的计算公式为:注射时间=注射器容积/注射速度其中,注射器容积是指注塑机射嘴的容积,注射速度是指塑料从注射器流入模具的速度。
2.模具的计算公式:模具在注塑加工过程中起到了至关重要的作用,模具的计算公式主要包括模具尺寸、模腔容积和模具开合力的计算公式。
(1)模具尺寸的计算公式:模具尺寸是指模具的长度、宽度和高度。
模具尺寸的计算公式由产品设计要求和模具样品的尺寸决定。
(2)模腔容积的计算公式:模腔容积是指模具中可以容纳的塑料体积。
模腔容积的计算公式为:模腔容积=产品体积+塑料收缩率×产品体积其中,产品体积是指注塑产品的体积,塑料收缩率是指塑料在冷却过程中的体积收缩比例。
(3)模具开合力的计算公式:模具开合力是指模具在注塑加工过程中需要施加的开合力量。
模具开合力的计算公式为:模具开合力=施力面积×施力压力其中,施力面积是指模具中需要施加开合力的面积,施力压力是指每平方米需要施加在模具上的压力。
3.注塑产品的计算公式:注塑产品的计算公式主要包括产品尺寸、产品质量和产品收缩率的计算公式。
数控车床倒角计算公式
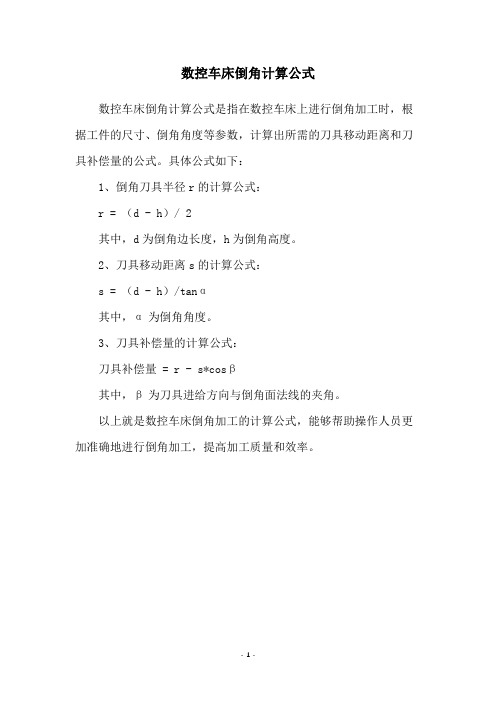
数控车床倒角计算公式
数控车床倒角计算公式是指在数控车床上进行倒角加工时,根据工件的尺寸、倒角角度等参数,计算出所需的刀具移动距离和刀具补偿量的公式。
具体公式如下:
1、倒角刀具半径r的计算公式:
r = (d - h)/ 2
其中,d为倒角边长度,h为倒角高度。
2、刀具移动距离s的计算公式:
s = (d - h)/tanα
其中,α为倒角角度。
3、刀具补偿量的计算公式:
刀具补偿量 = r - s*cosβ
其中,β为刀具进给方向与倒角面法线的夹角。
以上就是数控车床倒角加工的计算公式,能够帮助操作人员更加准确地进行倒角加工,提高加工质量和效率。
- 1 -。