S形曲线在伺服控制系统中的应用分析
S形曲线在伺服控制系统中的应用分析
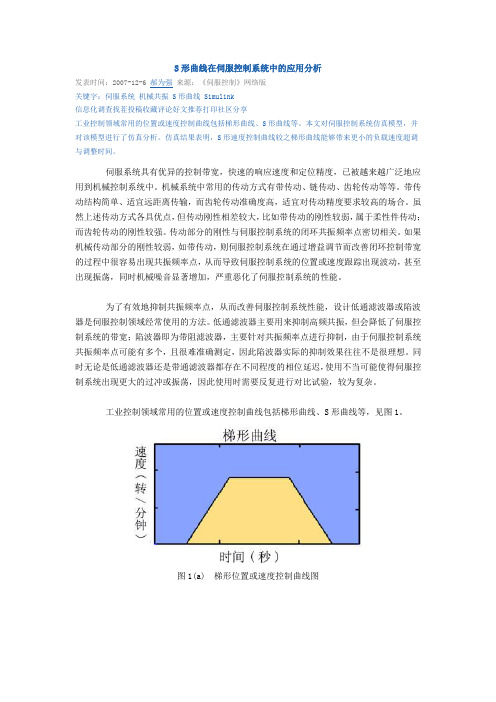
S形曲线在伺服控制系统中的应用分析发表时间:2007-12-6 郝为强来源:《伺服控制》网络版关键字:伺服系统机械共振 S形曲线 Simulink信息化调查找茬投稿收藏评论好文推荐打印社区分享工业控制领域常用的位置或速度控制曲线包括梯形曲线、S形曲线等。
本文对伺服控制系统仿真模型,并对该模型进行了仿真分析。
仿真结果表明,S形速度控制曲线较之梯形曲线能够带来更小的负载速度超调与调整时间。
伺服系统具有优异的控制带宽,快速的响应速度和定位精度,已被越来越广泛地应用到机械控制系统中。
机械系统中常用的传动方式有带传动、链传动、齿轮传动等等。
带传动结构简单、适宜远距离传输,而齿轮传动准确度高,适宜对传动精度要求较高的场合。
虽然上述传动方式各具优点,但传动刚性相差较大,比如带传动的刚性较弱,属于柔性件传动;而齿轮传动的刚性较强。
传动部分的刚性与伺服控制系统的闭环共振频率点密切相关。
如果机械传动部分的刚性较弱,如带传动,则伺服控制系统在通过增益调节而改善闭环控制带宽的过程中很容易出现共振频率点,从而导致伺服控制系统的位置或速度跟踪出现波动,甚至出现振荡,同时机械噪音显著增加,严重恶化了伺服控制系统的性能。
为了有效地抑制共振频率点,从而改善伺服控制系统性能,设计低通滤波器或陷波器是伺服控制领域经常使用的方法。
低通滤波器主要用来抑制高频共振,但会降低了伺服控制系统的带宽;陷波器即为带阻滤波器,主要针对共振频率点进行抑制,由于伺服控制系统共振频率点可能有多个,且很难准确测定,因此陷波器实际的抑制效果往往不是很理想。
同时无论是低通滤波器还是带通滤波器都存在不同程度的相位延迟,使用不当可能使得伺服控制系统出现更大的过冲或振荡,因此使用时需要反复进行对比试验,较为复杂。
工业控制领域常用的位置或速度控制曲线包括梯形曲线、S形曲线等,见图1。
图1(a) 梯形位置或速度控制曲线图图1(b) (S)形位置或速度控制曲线由于伺服电机的输出转矩与输出功率有一定的限制,但阶跃曲线需要伺服电机瞬时输出较大的转矩,易导致电机过载。
s形曲线在伺服控制系统中的应用分析(1)
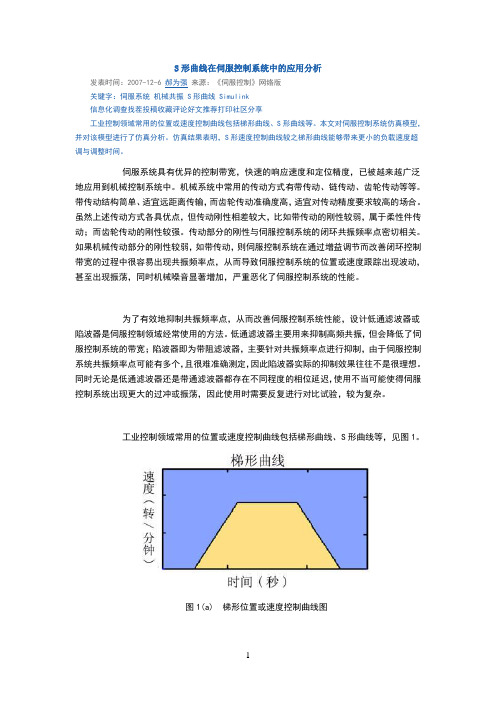
S形曲线在伺服控制系统中的应用分析发表时间:2007-12-6 郝为强来源:《伺服控制》网络版关键字:伺服系统机械共振 S形曲线 Simulink信息化调查找茬投稿收藏评论好文推荐打印社区分享工业控制领域常用的位置或速度控制曲线包括梯形曲线、S形曲线等。
本文对伺服控制系统仿真模型,并对该模型进行了仿真分析。
仿真结果表明,S形速度控制曲线较之梯形曲线能够带来更小的负载速度超调与调整时间。
伺服系统具有优异的控制带宽,快速的响应速度和定位精度,已被越来越广泛地应用到机械控制系统中。
机械系统中常用的传动方式有带传动、链传动、齿轮传动等等。
带传动结构简单、适宜远距离传输,而齿轮传动准确度高,适宜对传动精度要求较高的场合。
虽然上述传动方式各具优点,但传动刚性相差较大,比如带传动的刚性较弱,属于柔性件传动;而齿轮传动的刚性较强。
传动部分的刚性与伺服控制系统的闭环共振频率点密切相关。
如果机械传动部分的刚性较弱,如带传动,则伺服控制系统在通过增益调节而改善闭环控制带宽的过程中很容易出现共振频率点,从而导致伺服控制系统的位置或速度跟踪出现波动,甚至出现振荡,同时机械噪音显著增加,严重恶化了伺服控制系统的性能。
为了有效地抑制共振频率点,从而改善伺服控制系统性能,设计低通滤波器或陷波器是伺服控制领域经常使用的方法。
低通滤波器主要用来抑制高频共振,但会降低了伺服控制系统的带宽;陷波器即为带阻滤波器,主要针对共振频率点进行抑制,由于伺服控制系统共振频率点可能有多个,且很难准确测定,因此陷波器实际的抑制效果往往不是很理想。
同时无论是低通滤波器还是带通滤波器都存在不同程度的相位延迟,使用不当可能使得伺服控制系统出现更大的过冲或振荡,因此使用时需要反复进行对比试验,较为复杂。
工业控制领域常用的位置或速度控制曲线包括梯形曲线、S形曲线等,见图1。
图1(a) 梯形位置或速度控制曲线图图1(b) (S)形位置或速度控制曲线由于伺服电机的输出转矩与输出功率有一定的限制,但阶跃曲线需要伺服电机瞬时输出较大的转矩,易导致电机过载。
伺服s型曲线运动例子算法

伺服s型曲线运动例子算法伺服S型曲线运动是指在运动过程中加速度、速度和位置随时间的变化呈S型曲线的运动方式。
在实际应用中,伺服S型曲线运动常用于机械臂、汽车传动系统、航天器等需要平滑运动的场景。
下面将介绍一个基于三次样条插值的伺服S型曲线运动算法。
1. 确定运动时间首先,需要确定整个S型曲线运动的时间。
假设总运动时间为T,将其等分成n个时间间隔,每个时间间隔的长度为T/n。
这个值可以根据实际需求来确定。
2. 插值点的计算接下来,需要计算出每个时间间隔内的插值点。
在S型曲线运动中,需要考虑起始速度、终止速度以及最大速度这三个参数。
可以通过以下公式计算出每个时间间隔内的速度和位移:v = (2 * (x - x0) / T) - v0s = ((v0 + v) * T) / 2其中,x表示当前时间间隔的序号(从0开始),x0表示起始位置,v0表示起始速度,v表示终止速度,s表示当前时间间隔的位移。
3. 插值函数的构建根据上一步计算出的插值点,可以使用三次样条插值方法构建出S曲线的插值函数。
三次样条插值是一种常用的曲线插值方法,它可以保证曲线的平滑性和连续性。
可以使用如下公式来计算插值函数的系数:a0 = s0a1 = v0a2 = (3 * (s1 - s0) / (T ** 2)) - ((2 * v0 + v1) / T)a3 = (2 * (s0 - s1) / (T ** 3)) + ((v0 + v1) / (T ** 2))其中,s0和s1分别表示相邻两个时间间隔内的位移,v0和v1分别表示相邻两个时间间隔内的速度。
4. 运动控制通过插值函数,可以计算出任意时间点的位置。
在实际应用中,可以通过控制伺服系统的输出信号,调节位置来实现S型曲线运动。
需要注意的是,在实际应用中,还需要考虑到伺服系统的响应时间、传感器的精度等因素。
具体的实现细节可以根据实际需求来进行调整和优化。
以上就是一个基于三次样条插值的伺服S型曲线运动算法的简要介绍。
伺服s曲线加减速算法

伺服S曲线加减速算法
伺服S曲线加减速算法是一种常用的伺服控制算法,其主要目的是实现伺服系统的快速、准确、平稳的加减速控制。
具体来说,伺服S曲线加减速算法主要包括以下步骤:
1. 初始化:设定目标速度、加速度等参数,以及初始位置和速度等状态信息。
2. 计算当前位置:根据当前速度和加速度,利用运动学方程计算当前位置。
3. 计算加速度:根据目标速度和加速度,计算出当前需要的加速度。
4. 计算控制量:根据当前位置、目标速度和加速度,以及PID控制器的参数,计算出伺服电机的控制量,包括电机转速和电机转角等。
5. 调整控制量:根据实际反馈信号和误差信号,不断调整电机的控制量,以实现快速、准确、平稳的加减速控制。
6. 循环执行:不断重复上述步骤,直到达到目标位置或速度。
在实际应用中,伺服S曲线加减速算法可以通过单片机等控制器进行实现。
由于该算法能够快速准确地控制伺服电机的运动状态,因此在工业自动化、机器人控制等领域得到了广泛的应用。
g代码s曲线
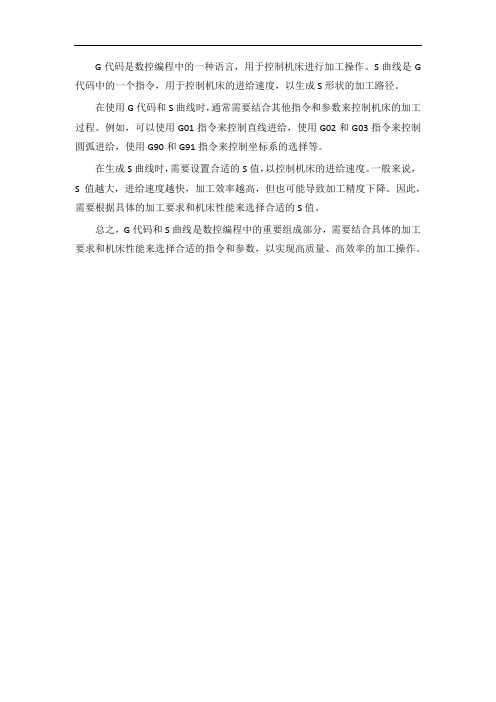
G代码是数控编程中的一种语言,用于控制机床进行加工操作。
S曲线是G 代码中的一个指令,用于控制机床的进给速度,以生成S形状的加工路径。
在使用G代码和S曲线时,通常需要结合其他指令和参数来控制机床的加工过程。
例如,可以使用G01指令来控制直线进给,使用G02和G03指令来控制圆弧进给,使用G90和G91指令来控制坐标系的选择等。
在生成S曲线时,需要设置合适的S值,以控制机床的进给速度。
一般来说,S值越大,进给速度越快,加工效率越高,但也可能导致加工精度下降。
因此,需要根据具体的加工要求和机床性能来选择合适的S值。
总之,G代码和S曲线是数控编程中的重要组成部分,需要结合具体的加工要求和机床性能来选择合适的指令和参数,以实现高质量、高效率的加工操作。
s型曲线加减速算法

s型曲线加减速算法
S型曲线加减速算法是一种常用于控制电机和伺服系统的运动控制算法,通过S型曲线实现平滑加减速运动。
具体算法描述如下:
1. 设置目标位置、初始位置和运动时间,以及加速度和减速度。
2. 计算总距离:总距离 = 目标位置 - 初始位置。
3. 计算加速时间:加速时间 = 速度 / 加速度。
4. 计算减速时间:减速时间 = 速度 / 减速度。
5. 计算匀速时间:匀速时间 = 运动时间 - 加速时间 - 减速时间。
6. 计算加速段距离:加速段距离 = 0.5 * 加速度 * 加速时间^2。
7. 计算减速段距离:减速段距离 = 0.5 * 减速度 * 减速时间^2。
8. 判断总距离是否大于加速段距离和减速段距离之和,如果是,则进入匀速运动阶段;如果不是,则重新计算加速时间和减速时间,并重新计算加速段距离和减速段距离。
9. 根据加速段距离、减速段距离和匀速时间计算匀速段距离。
10. 根据当前时间和加速段时间、减速段时间、匀速时间的比例,计算当前位置。
11. 根据当前位置和目标位置的关系,判断是否到达目标位置,如果是,则停止运动。
12. 根据当前位置和目标位置的关系,调整速度,实现匀速运动。
13. 返回第10步,进行下一步运动。
通过以上步骤的循环迭代,可以实现平滑的S型曲线加减速运动。
位置伺服控制器 精确位置控制与运动规划策略详解

位置伺服控制器精确位置控制与运动规划策略详解位置伺服控制器是一种用于工业自动化系统中的控制设备,主要用于实现精确的位置控制和运动规划。
本文将详细介绍位置伺服控制器的原理、特点以及常用的运动规划策略。
一、位置伺服控制器的原理和特点位置伺服控制器是基于反馈控制原理的一种设备,其核心是通过传感器实时采集执行机构位置的反馈信号,并与设定值进行比较,然后产生相应的控制信号,驱动执行机构实现精确的位置控制。
位置伺服控制器具有以下特点:1. 高精度:位置伺服控制器采用高精度的传感器进行位置反馈,可以实现微米级的位置控制精度。
2. 快速响应:位置伺服控制器的控制算法优化,使得其具有较快的响应速度,可以实现快速准确的位置调整。
3. 稳定性好:位置伺服控制器采用闭环控制的方式,具备良好的稳定性和抗干扰能力,可以适应复杂工作环境中的控制需求。
4. 灵活可扩展:位置伺服控制器通常具有多种输入输出接口,可以灵活扩展外部设备,满足不同应用场景的控制需求。
二、运动规划策略位置伺服控制器的运动规划策略是实现精确位置控制的关键。
下面介绍几种常用的运动规划策略:1. 梯形速度规划:梯形速度规划是一种简单且常用的运动规划策略,其原理是通过给定起始位置、目标位置和最大加速度,计算出一个速度-时间曲线,使得执行机构在一定时间内匀加速、匀速运动并减速到达目标位置。
2. S型速度规划:S型速度规划是一种更加平滑的运动规划策略,其原理是通过给定起始位置、目标位置、最大加速度和最大速度,计算出一个速度-时间曲线,使得执行机构在一定时间内匀加速、匀速运动并减速到达目标位置。
与梯形速度规划相比,S型速度规划的加速度更加平缓,运动过程更加平稳。
3. 末端轨迹规划:末端轨迹规划主要针对多轴联动的控制系统,通过给定起始位置、目标位置和运动时间,采用插值算法计算出多轴的位置和速度曲线,以实现多轴联动的精确控制。
本文主要介绍了位置伺服控制器的原理和特点,以及常用的运动规划策略。
三菱J4伺服基础课程精彩展示之速度控制

学员心得体会分享
知识体系建立完善
01
通过课程学习,我对伺服系统和速度控制有了更加全面和深入
的认识,建立了完善的知识体系。
实践操作能力提高
02
实验操作环节让我真正体验到了速度控制的实现过程,提高了
我的实践操作能力。
问题解决能力提升
03
课程中遇到的问题和挑战使我不断思考和探索,提升了我的问
题解决能力。
常见故障现象及原因分析
电机安装问题
检查电机安装是否牢固,联轴器是否对中。
电机内部故障
如轴承磨损、转子不平衡等,需专业维修。
常见故障现象及原因分析
控制器参数设置问题
检查速度环、电流环等参数设置是否合理。
编码器故障
检查编码器连接及信号是否正常。
故障诊断流程与技巧分享
观察故障现象,了解故障 发生时的操作环境和条件 。
按照检查清单,逐项排查 故障,缩小故障范围。
根据故障现象,分析可能 的原因,并列出检查清单 。
利用专业仪器和工具,对 疑似故障部位进行深入检 测和诊断。
预防性维护措施建议
保持电机及其周围环境的清 洁和干燥,防止灰尘和潮湿
对设备造成损害。
定期检查电机及其控制系统 的运行状态,及时发现并处
理潜在问题。
微分时间
调整速度调节器的微分时 间参数,以改善系统的动 态性能,减少超调和振荡 。
编码器反馈信号处理
编码器类型选择
编码器故障检测与处理
根据应用需求选择合适的编码器类型 ,如增量式编码器或绝对式编码器。
实时监测编码器的工作状态,对编码 器故障进行及时检测和处理,确保系 统稳定运行。
编码器信号处理
对编码器输出的信号进行解码、滤波 和倍频等处理,以提高速度和位置检 测精度。
- 1、下载文档前请自行甄别文档内容的完整性,平台不提供额外的编辑、内容补充、找答案等附加服务。
- 2、"仅部分预览"的文档,不可在线预览部分如存在完整性等问题,可反馈申请退款(可完整预览的文档不适用该条件!)。
- 3、如文档侵犯您的权益,请联系客服反馈,我们会尽快为您处理(人工客服工作时间:9:00-18:30)。
S形曲线在伺服控制系统中的应用分析
发表时间:2007-12-6郝为强来源:《伺服控制》网络版
关键字:伺服系统机械共振S形曲线Simulink
信息化调查找茬投稿收藏评论好文推荐打印社区分享
工业控制领域常用的位置或速度控制曲线包括梯形曲线、S形曲线等。
本文对伺服控制系统仿真模型,并对该模型进行了仿真分析。
仿真结果表明,S形速度控制曲线较之梯形曲线能够带来更小的负载速度超调与调整时间。
伺服系统具有优异的控制带宽,快速的响应速度和定位精度,已被越来越广泛地应用到
机械控制系统中。
机械系统中常用的传动方式有带传动、链传动、齿轮传动等等。
带传动结
构简单、适宜远距离传输,而齿轮传动准确度高,适宜对传动精度要求较高的场合。
虽然上
述传动方式各具优点,但传动刚性相差较大,比如带传动的刚性较弱,属于柔性件传动;而
齿轮传动的刚性较强。
传动部分的刚性与伺服控制系统的闭环共振频率点密切相关。
如果机
械传动部分的刚性较弱,如带传动,则伺服控制系统在通过增益调节而改善闭环控制带宽的
过程中很容易出现共振频率点,从而导致伺服控制系统的位置或速度跟踪出现波动,甚至出
现振荡,同时机械噪音显著增加,严重恶化了伺服控制系统的性能。
为了有效地抑制共振频率点,从而改善伺服控制系统性能,设计低通滤波器或陷波器是
伺服控制领域经常使用的方法。
低通滤波器主要用来抑制高频共振,但会降低了伺服控制系
统的带宽;陷波器即为带阻滤波器,主要针对共振频率点进行抑制,由于伺服控制系统共振
频率点可能有多个,且很难准确测定,因此陷波器实际的抑制效果往往不是很理想。
同时无
论是低通滤波器还是带通滤波器都存在不同程度的相位延迟,使用不当可能使得伺服控制系
统出现更大的过冲或振荡,因此使用时需要反复进行对比试验,较为复杂。
工业控制领域常用的位置或速度控制曲线包括梯形曲线、S形曲线等,见图1。
图1(a)梯形位置或速度控制曲线图
图1(b)(S)形位置或速度控制曲线
由于伺服电机的输出转矩与输出功率有一定的限制,但阶跃曲线需要伺服电机瞬时输出较大的转矩,易导致电机过载。
而梯形曲线具有一定的加减速斜率,且可通过斜率来限制伺服电机的输出转矩和输出功率,避免电机过载。
同时硬件设计简单方便,因此被工业控制领域广泛采用。
但梯形曲线也存在自身的弱点,从梯形曲线的频谱图中可见,其含有高次谐波分量,此时如果伺服控制系统闭环响应曲线存在共振频率点,则这些高次谐波分量会激励这些的共振频率点,从而导致位置或速度跟踪曲线出现过冲或振荡。
为了克服梯形曲线的上述缺点,工业控制领域逐渐开始使用S形位置或速度控制曲线。
S形曲线具有启动时需要伺服电机输出转矩小,加减速时高次谐波分量少等优点。
本文借助电机与负载耦合的常用模型,采用Simulink仿真软件对比分析了梯形曲线与S形曲线的控制性能,从而加深了对S形曲线的理解与认识。
伺服控制系统仿真模型
电机与负载的耦合模型见图2。
T表示电机电磁转矩、JM表示电机轴转动惯量、JL表示负载转动惯量、KS表示传动部分的扭转刚性、BML表示电机与负载间的粘滞阻尼系数。
该耦合模型忽略了机械传动部分的转动惯量,简化电机与负载间的耦合关系,用扭转刚性为Ks 的传动装置、粘滞阻尼系数为BML的摩擦环节等两个部分将电机与负载连接。
图2电机与负载的耦合模型
基于电机与负载的耦合模型,采用Simulink仿真软件对该耦合模型进行了分解,形成仿真示意图见图3。
梯形或S形速度控制曲线经过速度环PID调节后形成电流作用于电机定子绕组,形成电机电磁转矩。
由于电机与负载之间通过扭转刚性为Ks的传动装置、粘滞阻
尼系数为BML的摩擦环节耦合,因此实际作用在电机轴上的有效加减速力由电机电磁转矩T、电机与负载间由于存在瞬时速度差而形成的粘滞阻力、电机与负载间由于存在瞬时位置差而形成的扭转力三者合成。
作用在负载上的加速减力由粘滞阻力和扭转力两者合成。
对于电机轴而言,粘滞阻力和扭转力是阻力。
但对于负载,两者成为带动负载转动的动力。
由于伺服系统常在电机轴一侧装有编码器作为位置或速度反馈信号,而不是在负载一侧,因此Simulink仿真中将电机轴的速度接入了反馈回路,形成电机速度控制闭环。
图3电机与负载耦合模型的Simulink仿真示意图
Simulink仿真分析
在对伺服控制系统模型进行仿真分析时,使用的参数及对应数值如下:伺服电机转动惯量JM=80×10-6Kgm2、电机电磁转矩常数KT=1Nm/A、电机额定扭矩NR=4.5Nm、负载惯量
JL=8×10-4Kgm2(为电机轴转动惯量的10倍)、传动刚性KS=400Nm/rad、阻尼系数BML=0.01 Nms/rad。
仿真分析时,首先依据电机额定扭矩值设定控制曲线的加减速时间,防止电机过载。
其次在保证伺服控制系统负载速度响应带宽的前提下,尽量降低负载速度曲线的超调量,减小调整时间。
因此设定速度环PI调节器的比例系数P为3、积分时间常数Ti为100。
从伺服控制系统负载速度响应波特图(图4)中可见,负载速度响应带宽为173Hz(-3dB),相位-166°。
同时响应带宽内,存在共振频率点:频率114Hz,幅度13.2dB。
图4负载速度响应波特图
考虑到负载速度响应带宽内存在共振频率点,此时如果采用梯形速度控制曲线作为伺服控制系统的命令输入,则必然导致负载速度跟踪曲线出现较大超调量,较长的调整时间,见图5(a)所示。
但如果采用S形速度控制曲线,则会大幅降低负载速度跟踪曲线的超调量和调整时间,见图5(b)。
图5(a)梯形速度控制曲线下的负载跟踪速度曲线图5(b)S形速度控制曲线下的负载跟
踪速度曲线
图5中红色曲线表示速度控制曲线,蓝色曲线表示负载速度跟踪曲线。
从图5(a)中可见,在梯形速度控制曲线作用下的负载速度跟踪曲线最大超调量2.5%、调整时间约78ms(取△=0.005%);从图5(b)中可见,在S形速度控制曲线作用下的负载速度跟踪曲线最大超调量仅0.4%,调整时间更小。
通常伺服电机能够短时输出三倍额定转矩,用于加速负载而不出现过载。
在对上述两种
速度控制曲线输入进行仿真分析时,伺服电机的输出扭矩虽短时超过额定扭矩4.5Nm,但能够满足要求。
结语
仿真结果表明,S形速度控制曲线较之梯形曲线能够带来更小的负载速度超调与调整时间。
这就意味着在相同的速度超调要求下,S形速度控制曲线下能够进一步地缩短加减速时间,提高负载速度的控制带宽。
实际应用中的伺服控制系统结构较之本文的仿真模型要复杂的多,其机械传动部分可能包含多个传动环节。
由伺服调节器增益与控制算法、传动环节刚性、摩擦环节系数、电机与负载转动惯量等因素决定的共振频率点在伺服控制带宽内可能出现多个,且很难有效抑制。
因此使用S形位置或速度控制曲线是行之有效的控制方法,且必将更加广泛地应用于伺服控制系统中。